Steam turbine
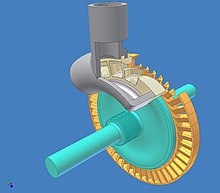
A steam turbine is an engine that uses a turbine to convert energy from water vapor . It consists of a rapidly rotating shaft equipped with turbine blades against which water vapor flows.
Designations
Standardized designations
According to DIN , the following designations are to be distinguished:
- Steam turbine: It is the pure power machine with the rotating components,
- Steam turbine set: In addition to the steam turbine, it consists of the connected machines , possibly also a gearbox ,
- Steam turbine system: This is understood to mean the entirety of the steam turbine, machine , condenser and connected pipelines .
Other names
- According to the flow direction: axial turbine and radial turbine
- After the procedure: Action turbine (dismantling of the enthalpy drop to the guide vanes ) and reaction turbine (dismantling of the enthalpy drop on the vanes and the rotor blades )
- After the vapor state: hot steam - , wet steam turbine and high-pressure , medium-pressure and low-pressure turbine
- After the steam supply: live steam, exhaust steam and storage steam turbine
- After steam removal: condensation , extraction condensation and back pressure turbine
development
The steam turbine uses the total enthalpy (= sum of different forms of energy) of the steam. Depending on the division of the enthalpy gradient between the stator and impeller, one speaks of either action or reaction turbines. The principle of the reaction turbine was described by Heron of Alexandria as early as the 1st century , in the form of the Heron's ball , which was already known to ancient Egyptian priests. This early steam turbine was a gimmick and was never put to any further use. In 1551 the Ottoman-Turkish polymath Taqi ad-Din first described a steam turbine as a drive for a rotisserie spit. In 1629 the Italian engineer Giovanni Branca was the first to come up with the idea of using hot steam to drive the blades of a turbine wheel in the West , but he did not put the idea into practice.
The first usable steam turbines were developed by the Swede Carl Gustav Patrik de Laval (1883) (principle of action) and the Englishman Charles Parsons (1884) (principle of reaction). Both original machines are in the Deutsches Museum in Munich . Parsons was also the first to install a steam turbine on a ship, the Turbinia . The advantage of the reaction turbine is, among other things, that the same blade profiles can be used for running and guide rows if the degree of reaction is selected accordingly. A disadvantage is the large number of steps and the resulting length of the runner. As a compromise between the compact design of the Laval turbine and the better efficiency of the Parsons turbine, Charles Gordon Curtis in the USA, Auguste Rateau in France and Heinrich Zoelly in Switzerland each developed multi-stage action turbines at the turn of the century.
Before the First World War, the Swedish brothers Birger and Frederik Ljungström developed a counter-rotating type of radial turbine in back pressure operation, which could be used very flexibly with outputs of up to 30 megawatts and the possibility of operation in a district heating network or on a condenser . In principle, however, the greatest output of this type is also around 30 megawatts; therefore, Ljungström turbines are no longer being built these days.
function
On the one hand, a liquid is evaporated. The steam drives a turbine at its high speed. The vapor then condenses and is pumped back into the circuit as a liquid and small volume. There is a large pressure difference between the evaporator and the condenser which drives the steam flow in the turbine.
The red line in the diagram shows the limit of the states of aggregation: to the left of it is liquid water (x = 0), to the right of it is pure steam (x = 1), in between "wet steam".
The idealized (loss-free) steam power process of a superheated steam turbine is represented as follows (in the steam turbine itself, the state changes from 5 = steam turbine inlet to 6 = steam turbine outlet take place):
- 1 - 2 : Friction-free and adiabatic pressure increase of the working medium water to the pressure prevailing in the steam generator ,
- 2 - 3 : heating the water to the evaporation temperature associated with the pressure ,
- 3 - 4 : Conversion of liquid water into steam at constant pressure (x = 0 -> 1),
- 4 - 5 : Further heating and superheating of the steam at constant pressure,
- 5 - 6 : Friction-free and adiabatic expansion of the steam with constant entropy in the steam turbine with simultaneous formation of the first water droplets,
- 6 - 1 : Isobaric condensation of the wet vapor in the condenser (x -> 0).
The area enclosed by the shown cycle represents the technically usable work related to the amount of steam flowing through.
The process itself is very simplistic, in practice, further steps such as the come intermediate superheating of steam at 5 - 6 and the multiple stages pre-heating of the water at 1-2 , and between 2 - 3 with tapped steam from various stages of the steam turbine added. Both serve to increase performance and efficiency. - Likewise, in practice, the adiabatic relaxation is not frictionless, so that the change of state 5 - 6 does not run vertically, but somewhat "obliquely" from 5 to the bottom right.
See cycle process , picture "Example: Steam power plant (legal process)". The reheating at constant pressure shifts the expansion in the steam turbine to the right. The relaxation should end near the red line "x = 1" so that the low-pressure blades of the turbine are exposed to the dry steam possible with few drops of liquid.
technology
The steam is provided in the steam generator with natural gas , crude oil , coal (fossil energy), biomass , solar energy or nuclear energy and fed to the turbine via pipes . There the enthalpy difference of the steam is used up to the temperature and pressure specified by the condenser . This type of machine is therefore also called a "condensation turbine" .
Today's steam turbines have an output of up to 1,600 megawatts due to the division of the steam volume into separate partial turbines with a common shaft . The technically possible limit power of this type is estimated at 4000 MW.
In power plants, the steam turbines are coupled to a synchronous turbo generator that generates electricity. Its speed depends on the frequency of the electrical power grid to be fed, which is 50 Hz (3000 or 1500 revolutions / min) or 60 Hz (3600 or 1800 revolutions / min) depending on the country.
In large conventional power plants, hot steam turbines with speeds of 3000 or 3600 revolutions per minute are usually used. The currently largest steam turbine for a coal-fired power plant is in Maasvlakte (Maasvlakte Power Plant 3, owner: e.on ) and delivers 1,100 MW. It consists of a high pressure, a medium pressure and 3 low pressure turbines, built by the former Alstom Power.
Nuclear power plants, on the other hand, are operated with saturated steam turbines at half the network speed of 1500 or 1800 revolutions per minute. This is also where the highest power plant outputs, often over 1000 MW, are achieved. The most powerful steam turbines (1755 MW) were built for the two units of the Chinese Taishan nuclear power plant . The turbines of most nuclear power plants consist of one high pressure and two or three low pressure parts in separate housings with a total of two or three condensers.
The longest blade lengths of the low-pressure parts are around 1400 mm (at 3000 revolutions per minute) or 2200 mm (at 1500 revolutions per minute). In operation, the blade tips can reach speeds of up to 500 meters per second, which is roughly 1.5 times the speed of sound in the air. The associated centripetal acceleration of the blade tip in this operating state is 4000 m / s². The resulting centrifugal force acting on one blade corresponds to the mass of a fully fueled Airbus 380 (approx. 550 t) and acts on each of the approx. 50 moving blades of the low-pressure output stage. Not only the blades themselves have to withstand these forces, but also the blade roots, which in turn transfer the forces into the rotor shaft. Such loads are mastered by martensitic steels; Using special materials such as titanium alloys , attempts are made to lower the relaxation end further in order to extract more work from the steam.

A side effect that is difficult to control arises when operating low-pressure steam turbines. The steam pressure drops well below 1 bar . The steam reaches the corresponding speed of sound between certain sections of the blades of the last stages . So that the water droplets previously created during the expansion can not erode the blades of the turbine and its pipes when entering the condenser , the steam flows through the centrifugal separator , where the droplets are removed by centrifugal force . In the turbine there is a radial pressure gradient due to the strongly decreasing density and thus unequal flow speeds above the blade height.
The limits of the turbine performance are given by the achievable blade lengths, which are determined by flow problems rather than the achievable strength of the blade material.
Application area steam power plants

The most far-reaching area of application of steam turbines today is in the generation of electricity in power plants for fossil fuels or in nuclear power plants . With outputs of up to 1755 MW (installed in the Chinese Taishan nuclear power plant ), these steam turbines are the largest of their kind. In addition, steam turbines are used in solar thermal power plants.
When generating electricity, however, there are special framework conditions to be observed: The mains frequency in Europe is 50 Hz, which makes a speed of 3000 / min for a two-pole machine and 1500 / min for a four-pole machine absolutely necessary. This requirement must be adhered to down to one revolution in order not to lose synchronicity with the network. For this reason, very special requirements are placed on the regulation. From a technical point of view, the lower speed is more favorable - nevertheless, many power plants work with 3000 rpm, since the natural frequency of many turbine shafts is in the 1200-1400 rpm range and therefore too close to the operating speed.
Active control of the speed via steam valves would be much too slow for this requirement, which is why passive control via the load was preferred. The turbine speed is specified via the network frequency.
The shafts of power plant turbines can be up to 60 m long and weigh several 100 tons including the turbine set . Because of the high for this size of machine speeds caused this tremendous forces that in a worst-case accident can lead to a rupture of the turbine. For this reason, turbines in nuclear power plants are always set up in such a way that debris flying off cannot hit the nuclear reactor . Conventional power plants are also built in such a way that such debris can never be thrown away in the direction of the control center .
Starting up a power plant turbine from the cold state can take up to a week. Starting up too quickly could lead to its jamming due to the rapid and uneven thermal expansion of the shaft in relation to the housing . The turbine is therefore slowly preheated to up to 300 ° C with constant rotation at low speed. The shaft is driven by an electric or hydraulic slewing gear at around 60 / min to prevent sagging and axial scraping in the bearing of the shaft. If the turbine is at operating temperature, it usually takes between 12 and 60 minutes to run up to operating speed.
A special feature are the power plant blocks for the traction current of the Deutsche Bahn , because for a two-pole machine not 3000, but only 1000 / min are required. Often these turbo sets are therefore not connected to one another directly, but rather through a gearbox so that only the generator is operated at a lower speed.
The steam turbine is still used in particularly efficient power plants because it can be combined with gas turbines : The exhaust gases from the gas turbines heat the steam generator, and the steam produced in the steam generator drives a steam turbine. This type of power plant is called combined cycle power plant ( gas and steam combined cycle power plant ).
Other uses
Steam turbines were already being used in ocean-going ships at the beginning of the 20th century, because only they could meet the demand for ever higher ship speeds due to their efficiency. During the Second World War, the larger combat ships and aircraft carriers were mostly powered by steam turbines and achieved outputs of up to 150,000 hp (110 MW). After the price of oil for firing steam boilers continued to rise in the mid-1970s, hardly any steam turbines were installed in ships. Instead, preference was given to the more expensive but more economical diesel engines and gas turbines .
Today, steam turbines are only used for actual power generation on nuclear-powered ships. Especially in the field of military technology, the vibration-free and low-noise operation is rated as a great advantage.
Turbines are also used to drive compressors and pumps in the high output range (> 1 megawatt).
Steam turbines are also used in large combined heat and power plants .
Steam turbines were also used experimentally to drive locomotives ( steam turbine locomotive ).
Illustrations of historical turbines
Older steam turbine with housing covers pulled apart; exhibited in the Rheinisches Industriemuseum Zinkhütte Alternberg in Oberhausen
Machine set with steam turbine (right), directly connected to three-phase generator (left). Year of construction 1910; Speed 2,000 / min electrical power 250 kW .
Low-pressure rotor of a ship's steam turbine for driving a tanker. Year of construction 1977, output 23,500 kW, speed of the low pressure rotor 4,100 / min, manufacturer AEG Location: Technical University Hamburg-Harburg
Runner of a Ljungströmturbine from the heating plant Tiefstack the HEW . Manufacturer: MAN 1938 Location: Technical University Hamburg-Harburg
Decommissioned low-pressure turbine rotor from the Unterweser nuclear power plant
Disused low-pressure turbine rotor Grafenrheinfeld nuclear power plant
Disused twin-flow steam turbine in front of the visitor center of the Gundremmingen nuclear power plant
Disused low-pressure rotor from the Philippsburg nuclear power plant in the Speyer Technology Museum
Low-pressure rotor from Block D of the Schwandorf / Dachelhofen lignite power station , in operation from 1972 to 1997, exhibited in Wackersdorf
Steam turbine construction
There has been a strong process of concentration in steam turbine construction in recent decades. The remaining turbine builders are u. a .:
- Ansaldo , Genoa
- Alstom Power Systems , Levallois-Perret ( sold to GE Power Systems in 2015 )
- BHEL , New Delhi
- Doosan Škoda Power (until 2009 Škoda ), Pilsen
- Dresser-Rand , Houston , Texas
- GE Power Systems, Atlanta
- Hitachi Power Europe
- Power Machines , St. Petersburg
- M + M Turbinen-Technik GmbH, Bad Salzuflen
- MAN Energy Solutions SE , Augsburg
- Mitsubishi Heavy Industries
- Siemens Energy Oil & Gas Steam Turbine Units , Görlitz
- Siemens Sector Energy including Mülheim an der Ruhr , Görlitz , Nuremberg , Brno
- Siemens Turbomachinery Equipment (until 2007 Kühnle, Kopp & Kausch ), Frankenthal
- SPILLING Energiesysteme , Hamburg
- TGM Turbinas , Sertãozinho ( São Paulo )
- Tuga , Tehran
- TurboAtom (until 1980 Kharkiv Turbine Works ), specializing in steam turbines for nuclear power plants, Kharkiv
literature
- Stefan from the Wiesche, Franz Joos: Handbook of Steam Turbines: Basics, Construction, Operation, Springer Vieweg, Wiesbaden, 2018, ISBN 978-3-658-20629-1
- STEAG AG Essen (Ed.): Electricity from hard coal, state of power plant technology, Springer, 1988, ISBN 3-540-50134-7 , steam turbines pp. 148–191.
- Wilh. H. Eyermann: The steam turbine, a teaching and manual for designers and students, R. Oldenburg, 1906.
- Adolf J. Schwab: Electrical energy systems - generation, transport, transmission and distribution of electrical energy, Springer, Berlin 2006, ISBN 3-540-29664-6 .
The "old masters":
- Aurel Stodola: Steam and gas turbines, 6th edition. Springer, Berlin 1924.
- G. wing: The steam turbines, JA Barth, Leipzig 1931.
- C. Zietemann: Calculation and construction of steam turbines, 2nd edition, Springer, Berlin / Göttingen / Heidelberg 1952.
- C. Pfleiderer: Steam turbines, Wissenschaftl. Publishing house, Hanover 1949.
Very detailed basic work - THE classic of turbomachinery, today in 2 volumes (also as an e-book with a different ISBN):
- Walter Traupel: Thermische Turbomaschinen, 4th edition, Springer Verlag, Berlin / Heidelberg 2001.
- Volume 1: Thermodynamic fluidic calculation, ISBN 3-540-67376-8 .
- Volume 2: Changed operating conditions, regulation, mechanical problems, temperature problems, ISBN 3-540-67377-6 .
- Fritz Dietzel: steam turbines. Calculation, construction, partial load and operating behavior, condensation , 3rd, completely revised edition, Hanser, 1980, ISBN 3-446-12915-4 .
- Fritz Dietzel: Turbines, Pumps and Compressors, Vogel-Verlag, Würzburg 1980, ISBN 3-8023-0130-7 .
- Hans-Walter Roemer: Steam turbines - introduction to construction and operation, Girardet-Verlag, Essen 1972, ISBN 3-7736-0095-X .
- Otto Martin: Steam and gas turbines, De Gruyter-Verlag, 1971, ISBN 3-11-114067-9 .
Newer plants deal with all flow machines together:
- Carl Pfleiderer, Hartwig Petermann: Fluid Machines , 6th Edition, Springer, Berlin / Heidelberg 1991, ISBN 3-662-10102-5 .
- Willi Bohl, Wolfgang Elmendorf: Turbomachines 1: Structure and mode of operation, (= Kamprath series ), Vogel Business Media Verlag, 2012, ISBN 978-3-8343-3288-2 .
- Willi Bohl, Wolfgang Elmendorf: Fluid machines 2: Calculation and construction, (= Kamprath series ), Vogel Business Media Verlag, 2012, ISBN 978-3-8343-3293-6 .
- Herbert Sigloch: Turbo machines . Basics and Applications, 5th edition, Hanser Fachbuchverlag, 2013, ISBN 978-3-446-43242-0 .
- Klaus Menny: Turbo machines . Hydraulic and thermal power and working machines, 5th edition, Vieweg & Teubner, 2006, ISBN 3-519-46317-2 .
as well as issues of Siemens Power Journal , ABB Technik , trade journal BWK. Fuel - heat - power , VDI-Verlag
See also
Web links
Individual evidence
- ↑ Aurel Stodola (ed.): The steam turbines . Springer, 1910, p. 1 ( online [accessed June 9, 2014]).
- ↑ Steam turbine , on energie-lexikon.info
- ↑ DT 1 aerodynamics. abayfor, archived from the original on September 28, 2007 ; accessed on March 23, 2015 (English).