Gas power plant

( Ahrensfelde gas turbine power plant : left: air filter, middle: common exhaust gas cleaning )
A gas power plant is a power plant , which as a primary energy source , the chemical energy from the combustion of a fuel gas used. Natural gas is by far the most frequently used, along with biogas , wood gas , coal gas , dome gases and the like. a. Fuel gas. If the term gas power plant is used without further details, it is usually natural gas. In the case of other fuel gases, the type is usually listed in the name (biogas power plant, furnace gas power plant, etc.).
The fuel gas can be converted into electricity with different types of thermal power plants : In addition to classic steam power plants or heat engines ( gas turbines or gas engines ) with natural gas combustion, gas and steam combined power plants are mainly used today. The designation as gas power plant for fuel cell power plants is unusual , although these also convert a fuel gas, mostly hydrogen, which can also be obtained from natural gas by reforming .
Fuel gases
(from GE Jenbacher for power generation of wood gas in the thermal power station transmitting )
As a rule, the gas that is burned is natural gas . Other fuel gases are used less frequently:
- Biogas , Kompogas from the fermentation of biomass (see biogas plant )
- Gas from biomass gasification , especially wood gas (see e.g. Biomass Integrated Gasification Combined Cycle , wood gasification )
- Coal gas from coal gasification (see e.g. IGCC )
- Blast furnace gases from industrial processes ( furnace gas , blast furnace gas , refinery gas , etc.)
- Landfill gas from landfill sites
- Mine gas from (closed) coal mines
- Hydrogen , renewable energy gas
- Liquefied gases
Compared to solid fuels (and to a limited extent also liquid fuels ), most fuel gases for use in power plants have considerable technical advantages: The fuel supply systems (intermediate storage, processing, conveying, etc.) are much simpler in structure. Since most gases burn very “cleanly” (low in pollutants) due to their constituents, exhaust gas cleaning is greatly simplified. There is also no ash from the incineration . Thanks to all of these properties, fuel gases - unlike solid fuels - are also suitable as fuel for internal combustion engines. In connection with the greenhouse effect, it is also advantageous that many fuel gases have a high H / C ratio (hydrogen to carbon ratio) and therefore less climate-damaging carbon dioxide is produced during combustion .
The technologies for fuel gases mentioned below in the section Gas - fired power plant designs are very similar to those for liquid fuels . Older gas-fired power plants, in particular, are therefore often “dual”, so that both gas and liquid fuels (diesel, heating oil, etc.) can be used as required. In other words, the power plant is then wholly or partly operated as an oil power plant.
Types of gas power plants
Various types of thermal power plants can be used as technology for converting the chemical energy stored in the fuel gas into thermal , mechanical and ultimately electrical energy :
Gas turbine and engine power plants


In gas-fired power plants of this type, the energy of the fuel gas is converted directly into mechanical drive energy in an internal combustion engine and then converted into electrical energy ("electricity") by means of a coupled generator .
The machines used are mostly gas turbines ; alternatively, depending on the type of application and size, gas engines (internal combustion) or Stirling engines (external combustion) can also be used. While engines are mainly used as smaller (emergency) power generators or as compact combined heat and power units for decentralized electricity and heat supply, larger gas turbine power plants are used as industrial power plants and in public power supply (the latter is only used as a peak load power plant due to the disadvantages mentioned below ).
Gas power plants of this type are characterized by their simple structure, high power density , high flexibility with short start times (approx. 15 minutes to full load) and high load gradients as well as low specific investment costs (costs per kilowatt). By dispensing with the steam process, many systems and plant components are no longer necessary; the system essentially only consists of the machine with its combustion air and exhaust system as well as the fuel supply and the electrical network connection (see diagram). In such systems, a machine house is often dispensed with; the machine is only given a simple weather protection hood, which also acts as sound insulation. Thanks to the high availability and automation of such machines, there is no need for constant operating and maintenance personnel on site. Operation is largely fully automatic, operation can be carried out remotely, and there is usually no on-site control room .
The main disadvantage of internal combustion engines lies in their low level of efficiency , which in the simple process (“simple cycle”, i.e. only open cycle without a downstream steam process) is usually only a maximum of 30%. Since the high-quality and expensive fuel is only poorly used, larger gas turbine and engine power plants are almost only used as "peaker" (peak load power plants) in most countries today. Due to the disadvantages, combined cycle power plants (see below) became increasingly popular in the 1990s. Older power plants from the time before were mostly either converted to combined cycle power plants or only kept ready for operation as a quick-start reserve. Only in countries that have large natural gas reserves and where gas prices are correspondingly low are gas turbine and engine power plants still used today at medium and sometimes even base loads. Special cases are power plants that use special gases such as biogas, mine gas, landfill gas and the like. incinerate (see below section fuel gases ).
Gas-fired steam power plants

Gas power plants of this type are conventional steam power plants whose steam generator (boiler) is fired with a fuel gas via gas burners .
In terms of their structure and functionality, such gas power plants are similar to other fired steam power plants: The steam generated in the boiler is used to generate electricity by means of a steam turbine . A cooling system ( cooling tower or similar) dissipates the inevitable waste heat to the environment. Compared to steam power plants that are fired with solid fuels , many systems are much simpler, starting with the fuel supply. In a gas-fired power plant, there is no ash or slag from combustion. Also, the exhaust gas purification is greatly simplified in combustion gases: A dusting of carbon black or fly ash is not required for clean combustion. In the case of low-sulfur fuel gases, flue gas desulphurisation can also be dispensed with. A denitrification (or catalytically non-catalytic) may be used in the combustion and the steam generator are integrated. The chimney can therefore often be placed directly on top of the tower boiler without the need for flue gas cleaning.
The disadvantage of this type of construction, similar to the above with internal combustion engines, is primarily the relatively poor efficiency. Compared to internal combustion engines, a further complication is that a gas-fired steam power plant is considerably more expensive to build and is not quite as flexible with regard to start times (approx. 1 hour to full load) and load gradients. The fact that such gas-fired power plants were built in large numbers up until the 1980s was mainly due to the fact that gas was still relatively inexpensive at that time and that the gas turbines and engines available on the market were still relatively small. With the development of more powerful gas turbines, gas-fired steam power plants were increasingly replaced by GT and combined cycle power plants (see below) from the 1990s. Older gas-fired steam power plants that are still in operation today, are almost exclusively as a peak-load power plant or a thermal power station in cogeneration used.
Combined power plants

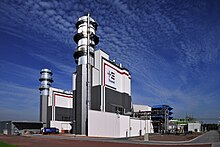
(in front the waste heat boiler , in the background machine houses with gas and steam turbines )
In a combined cycle power plant, an internal combustion engine (gas turbine or, more rarely, gas engine) is combined with a steam power plant (consisting of a steam boiler and a steam turbine with a cooling system); this combines the advantages of the two types mentioned above and mitigates the disadvantages to some extent. The machine makes the power plant flexible and quick to use, and through the combination of gas and steam processes, combined power plants achieve the highest level of efficiency of all thermal power plants (up to approx. 60%). The main disadvantage of this type are the high fuel and operating costs, which mean that combined cycle power plants are only used in the base load in exceptional cases.
In the case of combined cycle power plants, a distinction must be made between two subspecies according to the proportion of gas and steam processes:
- Combined gas and steam power plants (CCGT power plants) have been the common design since the 1990s. Here the steam boiler is a waste heat steam generator that only uses the waste heat from the internal combustion engine. At most, the steam generator has a relatively small additional firing. The internal combustion engine supplies about 2/3, the steam turbine about 1/3 of the total output of the power plant.
- Combined gas blocks are predominantly older systems, some of which have been retrofitted from a pure steam power plant to a combined power plant. Combination blocks consist of a conventional steam power plant, the fired steam generator of which is equipped with an upstream gas turbine (VGT) for preheating the air or feed water. Both the gas turbine and the boiler can be operated with gas as fuel. The VGT makes the power plant more flexible and improves efficiency, but is smaller in terms of output than the steam turbine.
Application
Systems that burn gas are comparatively simple in construction compared to solid fuel systems and have a high power density, which results in relatively low construction costs. However, since fuel gases are usually very high-quality and therefore expensive fuels, gas-fired power plants have high operating costs. The relationship between construction and operating costs means that gas power plants are mostly used for load control in the medium and peak load range. In the base load range, gas-fired power plants are usually economical at best as combined heat and power plants.
As a result of the development of more powerful gas turbines, falling costs and improved efficiencies, there was a “boom” of combined cycle power plants in many industrialized nations from the 1990s. As a result, for example, the use of gas to generate electricity in Germany doubled between 1990 and 2012 (see picture).
Because of the short start-up time and quick controllability, gas-fired power plants are being promoted as a flexible alternative for regulating fluctuations in electricity production, which are increasingly occurring due to the growing feed-in of volatile electricity from wind and solar energy . Politicians and associations are therefore calling for and predicting a further expansion of gas power plant capacities as a reserve to secure the energy transition. In this way, the period should be bridged until sufficient storage power plants are available. However, the operators complain that in particular the elimination of the midday peak due to the increasing feed-in from photovoltaic systems greatly reduces the profitability of gas power plants, so that there is currently no incentive to build new gas power plants. In addition, due to their relatively high operating costs and the resulting position in the merit order , gas-fired power plants are disproportionately affected by the current overcapacities on the electricity market and the resulting low electricity prices on the exchange. Some operators have therefore announced the closure of gas-fired power plants that have become uneconomical.
In order to counteract this, the Energy Industry Act was revised to the effect that gas-fired power plants that are classified as "systemically relevant" by the Federal Network Agency must be kept operational by the operator against payment of compensation. With the increase in certificate prices following the revision of the EU emissions trading to 22 euros / ton (as of January 2019), gas-fired power plants have become more competitive again. At this price level, individual efficient combined cycle power plants were already ahead of hard coal power plants in the merit order. From around 35 euros / ton, a general shift in the merit order towards gas-fired power plants is expected. At a price level of around 45 to 55 euros / ton, gas power plants could displace both hard coal and lignite power plants from the electricity mix.
In the summer of 2019 there was a switch from coal to natural gas in Germany due to increased certificate costs in European emissions trading and lower gas prices, with gas-fired power plants forcing coal-fired power plants out of the market. As a result, electricity generation from gas-fired power plants rose by around 50%, while electricity generation from hard coal power plants fell by around 50% and more than a third less electricity was produced from lignite power plants. In parallel to this economically induced shift in the production sequence of various types of power plants, electricity exports abroad decreased. According to preliminary data from the AG Energiebilanzen, electricity generation from coal fell by around 57 TWh over the year as a whole, while gas electricity generation rose by around 9 TWh.
Greenhouse gas emissions
In direct operation, gas-fired power plants cause lower emissions than coal-fired power plants . However, since natural gas consists largely of methane , which is a powerful greenhouse gas , natural gas losses during extraction and transport must also be included in the greenhouse balance of gas-fired power plants. Depending on the origin of the natural gas, the greenhouse balance varies, especially since there is still uncertainty in science about methane losses in the supply chains. In particular, there are great differences in research about gas losses in shale gas extraction , which is usually based on hydraulic fracturing .
If the natural gas comes from conventional production, the greenhouse gas emissions from combined cycle power plants are 420 to 480 g CO 2 -eq / kWh (carbon dioxide equivalent), the median is 450 g CO 2 -eq / kWh. Gas turbine power plants show significantly higher values with 570 to 750 g CO 2 -eq / kWh and a median of 670 g CO 2 -eq / kWh.
When using shale gas, however, the emission values differ greatly depending on the methane losses determined. While some studies do not see a big difference to conventionally extracted natural gas, others come to the conclusion that the gas losses during extraction can be significantly higher than with conventional extraction, which means that the climate balance is significantly worse. Viewed over a period of 100 years, the greenhouse gas emissions from gas-fired power plants are therefore at the same level as those from coal-fired power plants; over 20 years even higher by at least 20% to over 100%.
Basically, gas-fired power plants do not have the potential to reduce greenhouse gas emissions to a level that would be sufficient to avoid dangerous climate change . This goal can only be achieved with renewable energies or nuclear energy , as this requires emission reductions of 80% by 2050, which gas-fired power plants cannot achieve in principle. On the other hand, a limited reduction in emissions compared to coal-fired power plants is possible, with both a positive and a negative effect being achieved depending on various variables such as efficiency or gas losses. Should the switch to gas as a bridging technology delay the expansion of climate-friendly alternatives, there is a risk that global warming will even increase.
literature
- Christof Lechner (Ed.): Stationary gas turbines . Springer, 2009, ISBN 978-3-540-92788-4 , especially Chapter 3: GT power plants .
- Wolfgang Ströbele, Wolfgang Pfaffenberger: Energy industry: Introduction to theory and politics . Ed .: Michael Heuterkes. Oldenbourg, 2010, ISBN 978-3-486-58199-7 .
- Panos Konstantin: Practical book energy industry: Energy conversion, transport and procurement in the liberalized market . Springer, 2009, ISBN 978-3-540-78591-0 .
- Karl Schröder (Ed.): Large steam power plants, planning, execution and construction . in 2 volumes. Springer, 1962.
Web links
- Gas power plant . Auf: We reap what we sow . DIALOGIK - non-profit society for communication and cooperation research, Stuttgart.
Individual evidence
- ↑ Karl Schröder (Ed.): Large steam power plants, planning, execution and construction . in 2 volumes. Springer, 1962.
- ↑ a b c Christof Lechner (Ed.): Stationary gas turbines . Springer, 2009, ISBN 978-3-540-92788-4 , especially Chapter 3: GT power plants .
- ^ Franz-Josef Sehr : Fire in the landfill gas power plant Beselich . In: fire protection - Deutsche Feuerwehrzeitung 8/1991 . W. Kohlhammer, Stuttgart 1991, p. 397-399 . ISSN 0006-9094 . ZDB -ID & key = zdb 240087-x .
- ^ Fritz Brandt: Fuels and combustion calculation (= FDBR reference book series . Volume 1 ). Vulkan, 1999, ISBN 3-8027-5801-3 .
- ^ Wolfgang Ströbele, Wolfgang Pfaffenberger: Energy industry: Introduction to theory and politics . Ed .: Michael Heuterkes. Oldenbourg, 2010, ISBN 978-3-486-58199-7 , pp. 220 f .
- ↑ gas power plant. We reap what we sow (DIALOGIK gGmbH), accessed on November 14, 2013 .
- ↑ Electricity generation - gas power plant. Schwarzwald energy, accessed on November 14, 2013 .
- ↑ Uwe Milles, Peter Horenburg: Electricity from gas and coal . Ed .: FIZ Karlsruhe (= BINE basisEnergie . Volume 17 ). BINE Information Service, February 2011, ISSN 1438-3802 ( online as PDF ).
- ↑ Working group for economical and environmentally friendly energy consumption (ed.): Decentralized power generation with natural gas in single-family houses . Materials for the international conference in Essen. Kaiserslautern November 23, 2005. http://asue.de/cms/upload/inhalte/blockheizkraftwerke/broschuere/tagungsband_essen_sum_03.pdf ( Memento from December 3, 2013 in the Internet Archive )
- ↑ The electricity-generating heating (SeH). (No longer available online.) Erdgas.ch (Association of the Swiss Gas Industry), archived from the original on October 10, 2013 ; Retrieved November 14, 2013 .
- ↑ Electricity generation with natural gas. (No longer available online.) GRAVAG Erdgas AG, archived from the original on January 8, 2014 ; Retrieved November 14, 2013 .
- ^ Michael G. Feist (Stadtwerke Hannover): Efficient electricity from natural gas . In: Mediaplanet News . No. 5/2010 , June 2010. Efficient electricity from natural gas ( Memento from December 3, 2013 in the Internet Archive ); accessed on November 7, 2019
- ↑ Data on the environment. Federal Environment Agency, accessed on November 14, 2013 .
- ↑ Christina Steinlein: The greatest challenges of the energy transition: gas power plants as a new bridging technology. FOCUS Online, May 27, 2012, accessed on November 14, 2013 .
- ^ Association of Swiss Electricity Companies (VSE), Association of the Swiss Gas Industry (VSG): VSE and VSG for generating electricity with natural gas . Press release. December 23, 2011. VSE and VSG for generating electricity with natural gas ( Memento from December 3, 2013 in the Internet Archive ); accessed on November 7, 2019
- ↑ Christoph Hugi, Jürg Füssler, Markus Sommerhalder (Switzerland. Federal Office for Energy, Switzerland. Federal Office for the Environment, Swisselectric Research, Ernst Basler + Partner): Framework conditions for gas power plants in Europe. Research program in the energy industry . Federal Office for Energy , 2006.
- ↑ Andreas Wildhagen: Natural gas: gas power plants become a burden. WirtschaftsWoche (Online), August 14, 2012, accessed on November 14, 2013 .
- ↑ The electricity companies should get billions . In: Die Zeit , November 26, 2013. Retrieved December 4, 2013.
- ↑ Karsten Wiedemann: Gas power plants: The load of peak power. BIZZ energy today, January 7, 2013, accessed on November 14, 2013 .
- ↑ § 13c Energy Industry Act (EnWG)
- ↑ System relevance decides: energy companies want to switch off old power plants. Handelsblatt (online), October 10, 2013, accessed on November 25, 2013 .
- ↑ The high CO₂ price begins to take effect . In: Klimareporter , January 11, 2018. Retrieved January 12, 2018.
- ↑ Solar, wind and gas energy are increasingly displacing coal power from the market . In: Spiegel Online , August 28, 2019. Retrieved August 29, 2019.
- ↑ Gross electricity generation in Germany by energy source . AG energy balances. Retrieved January 7, 2020.
- ↑ a b Patrick R. O'Donoughue et al .: Life Cycle Greenhouse Gas Emissions of Electricity Generated from Conventionally Produced Natural Gas. Systematic Review and Harmonization . In: Journal of Industrial Ecology . tape 18 , no. 1 , 2014, p. 125-144 , doi : 10.1111 / jiec.12084 .
- ^ Robert W. Howarth et al .: Methane and the greenhouse-gas footprint of natural gas from shale formations . In: Climatic Change . tape 106 , 2011, pp. 679-690 , doi : 10.1007 / s10584-011-0061-5 .
- ↑ Xiaochun Zhang et al .: Climate benefits of natural gas as a bridge fuel and potential delay of near-zero energy systems . In: Applied Energy . tape 167 , 2016, p. 317-322 , doi : 10.1016 / j.apenergy.2015.10.016 .