Traction motor
As traction motors , including traction motors , which are motors designated with which a wheel of a tractive vehicle is driven. This applies above all to the electric motor for driving rail vehicles or locomotives and railcars . Since the establishment of electronic frequency converters at the end of the 20th century, three-phase asynchronous machines have mainly been used as traction motors , regardless of the design of the traction current system . The mechanical power transmission to the associated wheel sets, the so-called drive, is closely linked to the design of the traction motor.
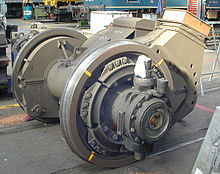
history

Electric
In the early days of electric railways , the type of traction motor was very closely linked to the traction current system used and the demands on power control. At initially low speeds and low powers, the main differences in the traction motors were initially in the electrical operating mode.
The first electric trains used DC motors , which were ideally suited for suburban trains and trams , but were rather unsuitable for long-distance railways because the losses in the overhead lines increase sharply due to the high currents and with increasing distances between the feeder and the vehicle. Single-phase alternating current with 16 2/3 or other low frequencies with which the much more complicated single-phase series motors could be operated were more suitable here . The locomotives must also be equipped with a transformer , but far fewer losses occurred in the energy supply over a greater distance than with direct current. Some locomotives were also equipped with repulsion engines, but they were not suitable for high speeds.
Independently of the two systems mentioned above, electrifications with three-phase alternating current also emerged . The three-phase asynchronous machines used were difficult and often only to be regulated in rough steps, but the implementation of an electrical regenerative brake was very easy to implement, so that these systems were often used for mountain railways . A major disadvantage of three-phase railways was the complex overhead contact line, which required two contact wires lying next to each other.
In the mid-thirties, the Deutsche Reichsbahn carried out the first successful tests with a 20 kV network at a frequency of 50 Hz. In Europe there are countries that use 50 Hz, in Germany, with the exception of the Rübelandbahn , 16.7 Hz is still used today. Card .
In the 50 Hz network, the traction units are equipped with shaft current motors , also known as mixed current motors , which were initially supplied with voltage by mercury vapor rectifiers and later by thyristor control . This type of construction was used more and more for direct current railways together with chopper controls .
The development of power electronics and computer controls allowed the use of converter- fed three-phase asynchronous machines with squirrel cage rotors regardless of the traction current system used. The very simple and robust traction motors replaced all other motor types mentioned above. Since around 2010, brushless motors with permanent magnets have also been used as traction motors.
Mechanically
While the DC motors offered the possibility from the beginning to build traction motors that could be accommodated directly in the underframe near the axle to be driven, most traction motors powered by AC were so large that they had to be accommodated in the locomotive body and the drive was similar to that of the Steam locomotives had to be done via drive and coupling rods . Only the progressive refinement of the construction made it possible to build AC motors that were so small that they could also be accommodated near the axes to be driven.
Types of currents
DC motor

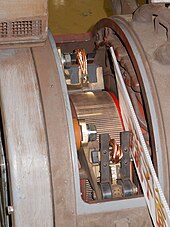
The direct current series motor has a high starting torque and is therefore ideally suited for driving vehicles. The comparatively low wheel speeds required also make it easier to use when there are commutation problems that occur more frequently at higher speeds. The terminal voltage of the traction motor corresponds mostly of the vehicle supplied voltage , which is why by direct injection or direct drive motor is spoken, because the contact line voltage without conversion is fed directly to the engine. The term should not be confused with that of the direct drive , which is used for drives without a gearbox .
The regulation of the voltage and thus the power of the traction motor was carried out by connecting starting resistors , which are short-circuited with increasing driving speed . The motors can be switched in different groups. The approach takes place in a series connection of all traction motors, with increasing speed traction motor groups are connected in parallel until all traction motors are connected in parallel with the voltage supplied to the vehicle at the highest driving level. Further speed levels are possible through field weakening . Although the tractive effort of the traction vehicle can be very finely regulated with the appropriate graduation of the control, the vehicles have only very few economical driving levels in which no energy is converted into heat in the series resistors.
DC motors were mostly chosen for trams , suburban trains, and subways . Given the limited length of the route, these systems can be operated with a few hundred volts, so that power can also be supplied via a power rail . For long-distance railways, the highest possible contact line voltage was chosen to avoid transmission losses due to high currents, but this is unfavorable for engine construction. The maximum possible terminal voltage on a full-line motor is around 1500 V. This voltage results in a commutator with a reasonable diameter that fits into a motor that can still be built into the vehicle. For this reason, only the overhead line voltages 1.5 kV and 3 kV prevailed for long-distance traffic . At 3 kV, two 1500 V motors are connected in series to halve the voltage per motor. Nonetheless, direct current transmission over long distances turned out to be economically expensive.
AC motor
Just like the DC series motor, the single-phase AC series motor has a high starting torque. The use of the AC motor specially developed for railway companies makes it possible to reduce the financial outlay for power transmission by transferring high voltages. However, this on the condition that a correspondingly large transformer and high-voltage tap changer were carried on the locomotive (in contrast to the direct current drive) in order to reduce the voltages, which ultimately amount to 15 kV to 25 kV, to motor-compatible levels.
Initially, it turned out to be problematic to use the common industrial frequency of 50 Hz. In the large motors, this frequency generated undesirably high induction voltages in the winding coils, which were currently in the "neutral zone", which led to strong spark formation and wear on the commutators and brushes. Experiments showed that the problem could be better controlled at low frequencies. This led to an agreement in the German-speaking countries around 1912 on an AC contact line voltage of 15 kV at a frequency of a third of the 50 Hz value, i.e. 16 2/3 Hz. Later other countries such as Sweden and Norway also adopted this successful operating system. Nevertheless, systems with higher voltages and frequencies were also able to spread around the world, especially the 25 kV 50 Hz system.
Since around 1990, single-phase AC motors have been losing importance as traction motors, since the availability of rail-mounted electronic converters and control technology has made it possible to use more economical three-phase AC motors.
Three-phase motor
The three-phase asynchronous motor offers a number of advantages due to its very simple design, in which, above all, there is no power transmission to the rotating armature. That is why the first AC traction drives were made around 1900 with three-phase motors. There were two main drawbacks here: On the one hand, the three-phase motor can only be operated at certain speeds , which are determined by the frequency of the three-phase current and the number of poles in the motor winding. Switchable motors only allow rough speed control in a maximum of six stages. The other point was historically the complex catenary, which had to be either three-pole or two-pole (when the rails were added as the third pole). From a technical and operational point of view, the routing of cables over switches and crossings is particularly complicated.
Nevertheless, the three-phase system was used extensively on the Italian State Railways from 1904 to 1976.
During the First World War, the Hungarian engineer Kálmán Kandó, who also designed the first three-phase locomotives for Italy, developed a system for converting the nationwide 50 Hz system into three-phase current using a rotating phase converter directly on the locomotives. After extensive experiments, the line from Budapest to Hegyeshalom was electrified with 15 kV and a frequency of 50 Hz from 1932 to 1935 .
Similar locomotives were built in Germany and France. The E 244 31 built for the Höllentalbahn test operation remained a one-off, but the French CC 14000, which had a rotating frequency converter , was built in 20 copies and remained in operation until 1981. However, the mechanical components proved to be too heavy and the controls too complicated compared to other systems, especially compared to the rectifier locomotives developed in the 1950s .
Since the 1990s, however, it has been possible to generate three-phase current for the motor drive with any frequency from the direct or single-phase alternating current of the contact line using modern converters and control technology on the traction vehicle itself . This enables the use of simple, robust and powerful three-phase motors with stepless speed control.
Differentiation according to the type of storage
Differentiation according to the power transmission
- Westinghouse spring drive
- Buchli drive
- Spring cup drive
- Rubber ring segment drive
- Cardan rubber ring spring drive
- Conical ring spring drive
Mechanical construction variants
The heat lost when the drive motor is operated must be dissipated. This is done either with fan wheels attached directly to the motor shaft ( self-ventilated ) or with special drive motor fans that are arranged outside the drive motor and have their own drive. Self-ventilated motors are used in light railcars, separately ventilated motors are used in locomotives and other vehicles with high drive powers.
The drive motor forms the drive together with the power transmission to the wheelset . This results in different designs of the traction motors:
- Direct drive - the rotor is arranged on the wheelset shaft , the stator is either also arranged on the axle shaft ( axle motor ) or housed in the spring-loaded chassis , which only allows a two-pole design of the drive motor. Both variants were previously used in the USA, but also on the London Underground .
- Tatzlagermotor - traction motor is partially supported on the axle, high wheel / rail forces due to the lack of suspension between traction motor and axle
- Levitation motor - traction motor is partially supported on a hollow shaft encompassing the axis , which is elastically connected to this, which leads to smaller forces compared to the pawl bearing drive.
- Frame motor - traction motor is completely housed in the spring-loaded chassis and transmits the power to the wheel set (s) using rods , hollow shafts or cardan shafts .
In the past, traction motors were also used in which two electric motors were housed in the same housing:
- Twin motor - the shafts of the two rotors are side by side
- Tandem motor - the two rotors are on a common shaft, used in Italian direct current locomotives and for 50 Hz single-phase series motors.
The drive motors can also be differentiated according to their installation position in the vehicle:
- Transverse engine - the most common arrangement in locomotives and railcars
- Longitudinal engine - on tram cars and high-speed trains
- Vertical motor - used on some locomotives
Electric brake
Most electric locomotives have an electric brake and the motors are operated as generators. Similar to a hybrid car, the driving force of the generator represents a braking force for the vehicle. The electrical power generated can either be converted into heat in braking resistors or fed back into the overhead line . Accordingly, the electric brake is also referred to as a resistance brake or, in the case of energy recovery, as a regenerative brake or regenerative brake . Modern traction vehicles usually have a regenerative brake, but can also be equipped with braking resistors that also allow electrical braking if no energy can flow back into the overhead line network. DC vehicles always have braking resistors because the rectifier stations cannot feed energy back into the AC network.
Web links
Individual evidence
- ^ Rossberg R. German railway vehicles from 1938 to today
- ↑ Jürgen Janicki, Horst Reinhard: Rail Vehicle Technology . Bahn Fachverlag, 2008, ISBN 978-3-9808002-5-9 , p. 4–.
- ↑ IEC 60050 - International Electrotechnical Vocabulary. IEC , September 1991, accessed October 11, 2014 .
- ^ Zarko Filipovic: Electric railways: Basics, traction vehicles, power supply . Springer-Verlag, February 3, 2007, ISBN 978-3-540-26438-5 , pp. 195–.
- ↑ Winfried Reinhardt: Public transport: technology - legal and business basics . Springer-Verlag, October 20, 2011, ISBN 978-3-8348-8234-9 , p. 219.