Landing gear (aircraft)

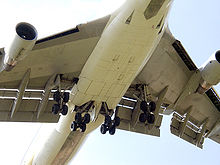
The landing gear ( English landing gear or "Undercarriage") of an aircraft represents the entirety of the wheels with aircraft tires, rims and mostly built-in brakes . In addition, they are suspended on dampened struts, spring struts or rigid structures. The landing gear supports the aircraft on the ground and enables it to move on the ground ( taxiing ). It also enables the take-off speed to be achieved (the take-off run ). During landing , the relatively high impact loads are absorbed by the landing gear ( shock absorbers ) and thus kept away from the airframe . Even jumping back up (bouncing off the runway ) after a harder touchdown is mitigated by the damping of the shock absorbers. Wheel brakes can be used to shorten the coasting distance when landing and when aborting take-off , for steering on the ground (differential braking) as well as for speed control and as a parking brake on the ground. The chassis may be fixed (rigid) or retractable (retractable landing gear, English retractable gear )
The chassis is usually a three-point support.
The landing gear is a relatively heavy part of the aircraft, it can make up to 7% of the maximum take-off weight, but usually only 4–5%.
In the case of aircraft landing gears, a distinction is made according to the arrangement of the wheels, their installation location and their design. A basic distinction is made between two types of chassis:
- Main landing gear (in front of or behind the aircraft's center of gravity)
- Support landing gear (nose or tail landing gear as well as support landing gear on the wings)
this is followed by the arrangement of the chassis
- Three-point landing gear in nose or tail wheel design
- Tandem chassis
- Special trolleys (e.g. chain trolleys or skid frames)
Tasks of the chassis
The main tasks of the chassis are:
- Enable mobility of the aircraft on the ground
- Ensuring that no other part of the aircraft touches the ground during taxiing, take-off, and touchdown
- Absorbs and dampens the vertical kinetic energy when landing
- Absorption and transmission of the horizontal kinetic energy during landing and in the event of an aborted take-off
- Suspension of uneven floors
- Resistance to the side load when taking off and landing in a crosswind .
Landing gear configuration
When it comes to the arrangement of the wheels (usually a three-point arrangement), a distinction is made between the historically older spur landing gear (until the 1930s also with a grinding spur) and the newer nose wheel landing gear. Tandem arrangement of the wheels under the fuselage is less common, which means that side supports are required (examples: motor glider Falke , Baade 152 airliner , B-52 bomber or Harrier fighter aircraft ).
In heavy transport aircraft, the main landing gear often consists of two to four groups of wheels that are arranged in two rows on the fuselage.
The number of wheels required for a particular aircraft depends on its weight, intended use and the load-bearing capacity of the airport operating surfaces. This value is indicated with the " Pavement Classification Number ".
Tail wheel landing gear (tail wheel or tail wheel landing gear)


In the first decades of aviation up to the end of the Second World War, almost all aircraft were tailwheel aircraft ( Taildragger or tailwheel ). Almost all of them had a landing gear with a spur. This is where the term conventional gear , which is still used today in English , comes from .
With a tail landing gear, the two main landing gear legs are located in front of the aircraft's center of gravity and a grinding spur or a tail wheel in the tail area provides the third support point. This star wheel could be made steerable by coupling it with the rudder control. Compared to a nose wheel landing gear, the construction is a bit simpler. A disadvantage of this type of landing gear is that the stern is lower than the bow when standing. For the pilot this means that the view to the front can be severely restricted while taxiing, forcing him to taxi in serpentine lines. To take off, he must first lift the tail of the aircraft during take-off (by lightly pressing the control stick) until the aircraft fuselage is parallel to the runway. In this neutral longitudinal incline, further acceleration takes place until lift-off. Because of the corkscrew-like air flow behind the propeller (English: slip stream) that hits the vertical tail, a more or less strong tendency to break out can arise, especially after lifting the tail, to the left in aircraft with a right or clockwise rotating propeller . The second disadvantage of the tail landing gear becomes apparent when a breakout actually begins, especially when rolling out after landing. The center of gravity behind the support line of the main landing gear, which tends to move further in the original direction, creates a moment that even supports the breakaway movement.
Landings with a tail-wheel aircraft require special practice for today's pilots, who mostly did their original training on more modern aircraft with nose-wheel landing gear. If the brakes are too strong, there is also a risk of tail-wheel planes standing on their head ( aviator memorial ) or even rolling over forwards.
A three-point landing in which all three wheels touch down at the same time is the aim of tail-wheel aircraft. The necessary large angle of attack of the wing and thus the greater resistance reduce the touchdown speed and greatly shorten the coasting distance.
When installing jet engines under the wing of low- wing aircraft, a tail wheel landing gear is useless, as the first tests with the Me 262 showed. The elevator is not effective enough to counteract the righting moment that the engine thrust creates with respect to the higher center of gravity. It was not possible to raise the stern when rolling. The trick with which this deficiency was countered was to step on the brakes briefly, which brought the torso into the desired horizontal position. Based on this knowledge, the other test aircraft of the Me 262, but also those of the competitor development, the Heinkel He 280 , received a nose wheel landing gear.
For passengers of commercial aircraft , a tail wheel landing gear means that they have to walk on an inclined plane to get on and off the aircraft, e.g. B. in the Ju 52 or DC-3 .
Nose wheel landing gear
The tricycle gear (English "tricycle gear") is compared to the tail wheel gear as the more modern form, although the Wright brothers used it in their later aircraft. The nose gear in the front area of the aircraft fuselage supplements the right and left main landing gear (main landing gear). The view for the pilot is good, especially during taxiing, but also during take-off and landing. The nose wheel can be designed to be steerable or just pivotable. In the latter case, a separate damping device must be installed to avoid the dreaded nose wheel flutter ( Shimmy ). For steering on the ground, the wheel brake of the respective main landing gear can be used in addition to the nose wheel. A rollover forwards, as with the tail wheel chassis, is hardly possible anymore. The aircraft's center of gravity is slightly in front of the main landing gear. In the event of a slight breakaway, this creates a moment that counteracts the breakaway direction and thus has a stabilizing effect.
In commercial aircraft with a nose wheel, the fuselage is always in an almost horizontal position for passengers to get on and off. The designation of the tire arrangement of commercial aircraft was standardized by the American FAA .
This configuration can be demonstrated in Germany for the first time on June 8, 1939 on a Fw 58 that the Reich Aviation Ministry had converted at Focke-Wulf. The aircraft was then made available to all German development companies for testing for some time. Walter Blume at Arado was the first to recognize the advantages and immediately applied the new chassis shape to the Ar 232 . It has prevailed since then and represents the solution commonly used today in both the military and civil sectors.
Nose wheel

The nose wheel is part of the landing gear of an aircraft. It's in the front part of the machine, the bow , hence the name.
In contrast to the main landing gear, the nose wheel only carries a relatively small part of the aircraft's weight when standing and rolling on the ground. The relatively weak design of the nose wheel can lead to breakage in the event of improper landings, so that the aircraft nose touches the runway. In the case of single-engine propeller aircraft, which usually have their propellers at the front, the propeller is then destroyed - often including the engine.
In commercial aircraft that use parking positions with passenger boarding bridges at airports , the tow bar of the aircraft tug, which pushes the aircraft back after loading, is coupled to the nose wheel, with newer tugs even the entire nose landing gear is enclosed and raised.
Fighter planes that take off and land on aircraft carriers need a very stable nose wheel: with modern designs (e.g. the F-18 Hornet and the Dassault Rafale ) it has to absorb the forces of the launch catapult and withstand heavy impact loads when landing at a very high rate of descent and cushion.
The nose wheel is only equipped with brakes on a few types of aircraft. B. with variants of the Boeing 727 and the Fokker F28 .
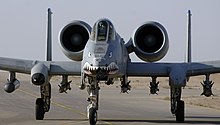
The nose wheel of the Fairchild-Republic A-10 ground attack aircraft ("Thunderbolt II" / "Warthog") is an exotic one : it is clearly offset to the right because a large on- board cannon ( GAU-8 / A Avenger ) is included on the left slightly off-center in the bow Ammunition feed is installed. The nose wheel of the Hawker Siddeley Trident airliner is also offset; it retracts from the side.
Main landing gear

The main landing gear is part of the landing gear of an aircraft. It is located in the area of the center of gravity of the machine and carries the main load of the aircraft during taxiing on the ground, hence the name.

The main landing gear can consist of just one wheel (single-track undercarriage) or a large number of wheels with complicated mechanics. Some main landing gears (or parts of them) can be steered to improve maneuverability on the ground. On the Boeing 747 as an example, the rear part of the main landing gear is controllable to allow for tighter curve radii.
Some main landing gear can already be swiveled in flight in order to be able to absorb the lateral pushing of the machine when touching down in crosswind landings (for example Boeing B-52 ).
In commercial aircraft, the main landing gear is attached to the wing with predetermined breaking points . This construction is intended to prevent the wing structures and the fuel tanks built into them from being damaged in the event of a hard landing; the "removal" of the landing gear is preferable to a far more devastating explosion of fuel for reasons of safety.
Transport aircraft
Transport aircraft have special requirements for the landing gear:
- very high load (therefore a lot of wheels, no long or graceful landing gear legs)
- Military transporters must be able to take off and land on unpaved runways (depending on requirements and intended use)
- Lowest possible loading edge (possibly also hydraulically lowerable)
- Very large shift in the center of gravity during the loading process (aircraft must be supported at the tail when moving heavy loads inside the aircraft so that they do not tip over backwards)
Nose wheel landing gear designed for this is usually used.
Tandem chassis
The tandem configuration (English "tandem gear") is also common for special applications - for example for gliders, vertical take-offs, high-altitude reconnaissance vehicles or some bombers. The first version of the airliner 152 developed in the GDR also had such a landing gear, which mostly required lateral supports.
The Boeing B-52 has four main pairs of wheels under the fuselage, two next to each other
Main landing gear and support wheels under the wings of the Soviet bomber and reconnaissance aircraft Jakowlew Jak-28
Gliders
Old gliders were often not equipped with a wheel, but only with a skid.
With a few exceptions such as the Stemme S10 , gliders do not have adjacent wheels. When it is not moving, a wing always rests on the floor, with rubbing strips or small wheels attached to the wing tip to protect the surface.
In modern gliders, the main load is carried by a - often retractable - main wheel in the area of the center of gravity. With the first school gliders , this function was performed by a skid. Even with many older models such as the Schleicher ASK 13 , the main wheel is supported towards the front by a runner. With more modern types, a smaller nose wheel is used in front of the main wheel instead. In the meantime, the use of a small wheel instead of the previously common abrasive spur has also established itself at the rear. Since this wheel can only be steered to a very limited extent (if at all), a spur roll is mounted on the ground for easier maneuvering .
Other solutions
Depending on the application, other chassis solutions can also be used. Special heavy-duty landing gear designs have a very large number of main landing gear wheels in order to keep the ground pressure low, and some are designed to be adjustable in height on the ground in order to simplify loading and unloading. In rare cases, the landing gear was designed to be ejectable in order to improve the aircraft's performance data, for example with the Messerschmitt Me 163 .
Other types of landing devices or landing gear are:
swimmer
Runners
Skids are occasionally used, for example on the North American X-15 , or on the Lockheed C-130 for polar use.
Crawler tracks
Occasionally, a crawler track was also used for use on low load-bearing ground . However, this could not prevail due to the high weight and unsolvable technical difficulties.
Air cushions
In the 1970s, an air cushion system called the Air Cushion Landing System (ACLS) was also tried. The first aircraft was a Lake LA4 , which Bell had equipped with an air cushion. In 1972 the conversion of a DHC-5 Buffalo started. The Buffalo landed on the air cushion for the first time on April 11, 1975.
Fixed (stationary) or retractable landing gear
The fixed chassis is historically older. In the early days of aircraft construction, the percentage share of the landing gear in the air resistance of the aircraft with its angular shapes, the many struts and braces was insignificant. Only with the general improvement of the aerodynamic shape did it become more and more important. Since the landing gear was not used during the flight, the idea was to make it disappear completely during this phase. Therefore one spoke of the disappearing landing gear. The landing gear is retracted into the engine nacelle, into the wings or into the aircraft fuselage .
Retractable landing gear is the norm today to reduce drag by up to 25%. The simpler fixed landing gear is only used for smaller aircraft with less high speeds. There are also forms in which the landing gear is only partially retracted.
Fixed chassis
If the landing gear is attached to the aircraft in such a way that, apart from the changes in its shape caused by the compression, it maintains its shape throughout the flight, it is referred to as a fixed landing gear. The wheels of each of the two main landing gear halves sit on a spring strut, which contains both the various types of components required to cushion the rolling and landing bumps, as well as a device for effective damping of this spring movement. These struts can now be cantilevered in their rigid mount without any lateral support. One then speaks of a monopod undercarriage (examples: Bücker Bü 181 , Klemm Kl 35 A and B ). These struts are subject to great bending stresses due to the forces acting laterally on the wheel. The other type is the three-legged landing gear, in which the now articulated suspension strut is guided by two support struts, usually arranged in a V-shape and also articulated. All three parts move during compression. Chassis of this type change their track width (examples: Junkers Ju 52 , Fieseler Fi 156 ). In order to reduce air resistance, the main landing gear legs and the wheels are usually aerodynamically clad ( HB 23 ). In the case of particularly slow aircraft and many helicopters, however, this is also omitted.
Retractable landing gear
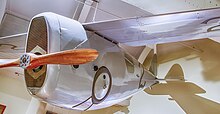
If, on the other hand, the aircraft landing gear is designed and installed in such a way that it can be retracted, it is referred to as a retractable landing gear or retractable gear. The retraction and extension can be done manually or automatically (mostly hydraulic , occasionally electric). In the latter case, there must be an emergency extension system, which in the past often had to be operated by hand (hand pump or hand crank). The landing gear is fully or partially retracted into the fuselage, the wing, the motor gondolas or its own gondolas.
Retractable landing gears found their way into aircraft construction in the mid- 1930s . The Dornier Do 11 is considered to be the first European military aircraft with retractable landing gear to meet the need for increased flight speeds. Other early examples are the Heinkel He 70 "Blitz" and the Airspeed AS 5 "Courier". Probably the first aircraft with retractable landing gear was the American Dayton-Wright RB-1 racing aircraft ; it took part in the "Gordon Bennett Trophy" for the USA in 1920.
Since the position of all the wheels cannot be seen by the pilot from his seat, the position of each undercarriage section, whether retracted or extended, must be displayed via devices. There are electrical and mechanical displays that show the position of the chassis. The landing gear lever as such (usually with a wheel at the end) and, above all, its position can be recognized immediately in modern cockpits without confusion. There is a separate display for each landing gear leg; In the case of an aircraft with five landing gear legs, there are therefore five displays, which can light up in red or green depending on the position of the landing gear. The semantics are simple:
- no light: landing gear retracted and locked
- green light: landing gear extended and locked
- Red light: The position of the landing gear does not match the position of the selector lever (e.g. while driving).
The gear retraction is almost instantaneous for multi-engine aircraft after takeoff when a positive rate of climb on the riser diameter ( vertical speed , English "Vertical Speed Indicator." - VSI) appears, usually on the latest by the end of the runway. In the case of some aircraft, the air resistance increases as soon as they are retracted when the landing gear compartment flaps have to be opened first. This can become critical at low speeds (for example when going around with a failed engine). In this case, the landing gear should only be retracted after the required speed has been reached. Before the retraction process, the wheels are brought to a standstill by actuating the brakes or automatically in order to avoid undesirable effects of the still rotating wheels in the landing gear shafts.
Landing gear extension is done while descending on the glide path and is typically started about 600 meters (2000 feet) above the runway on commercial aircraft.
Modern aircraft have a Ground Proximity Warning System (GPWS). There are warning signals if the machine with the running gear retracted falls below a height of approx. 150 m above ground.
Others; Records
Some of the heaviest aircraft in the world (see also aircraft weight ) were developed for military use:

- the Antonow An-225 Mrija (first flight in 1988) has seven twin wheel sets on both sides (see photo), the four rear wheels of which are controllable. The nose landing gear has two landing gear legs with two wheels each.
- Antonov An-124 Ruslan
- Lockheed C-5 Galaxy
- Lockheed Tristar MRTT (the L-1011-250 has a take-off mass increased to 224,982 or 231,332 kg)
- Airbus A310 MRTT
- Xian Y-20 (first flight January 2013; allegedly the maximum take-off weight is 200 or 220 tons)
The construction of ground landing gear on which landing gear without landing gear can take off and land is also tested .
If there are problems with retractable undercarriages, a manual gravity drop is sometimes carried out, i. H. the undercarriage that is still retracted is unlocked so that it falls / extends into the "extended" position due to gravity and then mechanically engages there.
See also
Web links
- Dimensions and power requirements of trolleys (PDF file; 384 kB)
Individual evidence
- ^ Ajoy Kumar Kundu: Aircraft Design . Cambridge University Press, New York 2010, ISBN 978-0-511-67785-4 , pp. 194 (English, limited preview in Google Book search).
- ↑ Designation of the tire arrangement by the FAA (PDF; 555 kB)
- ↑ The Plane Crash - Full documentary , explanation of the correct procedure by an air accident investigator from minute 60
- ^ Norman S. Currey: Aircraft Landing Gear Design: Principles and Practices , p. 307
- ↑ August A. Cenkner Jr .: Aerospace Technologies of Bell Aircraft Company: A Pictorial History (1935–1985) , p. 88
- ^ Herbert Ringlstetter: Night fighters and bombers: German Air Force 1933–1945 . GeraMond 2012, p. 7 (with photo).
- ↑ cf. HF King: The First Fifty Years ... , in: Flight and Aircraft Engineer , Vol. 64, No. 2324, 1953, p. 762 ( available online (PDF, English))
- ↑ cf. Gordon Bennett Trophy, 1920 , English Wikipedia
- ↑ Hamburg Aviation: "Future by Airbus" uses ground landing gear concept from Hamburg , October 1, 2012. ( Memento from October 20, 2014 in the Internet Archive )