Akaflieg Berlin B13
Akaflieg Berlin B13 | |
---|---|
![]() |
|
Type: | Glider |
Design country: | |
Manufacturer: | |
First flight: |
March 2, 1991 |
Number of pieces: |
1 |
The B13 is a two-seater glider with auxiliary engine, designed and built by the Academic Aviation Group of the Technical University of Berlin . The first flight took place on March 2, 1991 at Strausberg airfield . The glider index is 109, the code D-KILU and the competition code CD .
history
At the beginning of the 1980s, the idea arose to integrate the extendable auxiliary drive with a foldable propeller into a two-seater glider, developed by Aka pilot Claus Oehler at the Institute for Aerospace (ILR) at the TU Berlin . This should avoid landings and thus the risk of damage to an aircraft with a wide wing. The crew members sitting next to each other should have a very good view in the direction of flight and be able to communicate directly with one another. The fuselage was designed as a minimal fuselage in order to compensate for the disadvantages of the larger fuselage cross-section compared to a tandem arrangement of the cockpits. A fuselage model on a scale of 1: 5 was measured in the wind tunnel , a mock-up was built for seat tests and the installation of functional models of the double control . To prove the strength of the new hybrid construction, a load test was carried out on a trunk tube at the ILR in Berlin-Charlottenburg. The fuselage and tail unit construction were completed in 1986, while the originally planned wings did not withstand several load tests, so alternatives were sought. Finally, the four-part wings developed by Aka pilots Peter Jaquemotte and Alfred Schmiderer for the Stemme S10 motor glider were also used for the B13.
The aircraft first flew in early 1991, but as a pure glider. Space problems with the integration of the combustion engine - a modified Rotax 377 with 24.5 kW output - especially the fire bulkhead , prevented its use.
For practical testing, more than 100 take-offs with 100 hours of flight time including flight performance determinations in 1991 and 1992 and spin tests at the Idaflieg summer meeting in Aalen-Elchingen took place by the end of 1992 . The insufficient brake flap effect led to testing of eight configurations of the two-tier Schempp-Hirth flaps (variation of the sheet metal spacing, holes of different geometry and position).
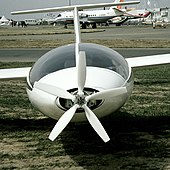
The opening / closing of the nose / supply air and exhaust flaps and the extension and retraction of the propeller slide were carried out by a rod which was guided through the instrument panel. In this rod there was another pipe for the remote control of the decompression to start the engine. The rod for extending the sled with the five-blade folding propeller was replaced by a crank drive after flight tests due to the excessive force required by the counteracting air force. The original Rotax exhaust was cut open, provided with an internal baffle plate and welded in a spiral shape in order to be able to find space in the front part of the fuselage. Unsuccessful attempts to fit the usual 0.4 mm thick sheet steel into the angled engine compartment led at the beginning of 2001 to tests of a laminate made of 0.07 mm stainless steel foil, 2 mm intumescent cardboard and 10 mm ceramic insulating material. Until the beginning of 2005, tests were carried out using metal gauze , which was supposed to distribute the thermal radiation over a larger area in the event of a fire.
In 2005 the aircraft began to be modified into a research aircraft and technology carrier for electric drives. A brushless electric motor in the nose of the fuselage, fed by fuel cells and solar modules , was supposed to drive the five-blade folding propeller with a diameter of 85 cm, which was already intended for the combustion engine variant. The patented mechanism developed by Claus Oehler for a folding propeller that can be folded against the direction of flow enabled the propeller to be stowed in the nose of the fuselage to save space. With the electrical concept, the Academic Fliegergruppe achieved second place in the Berblinger Prize of the City of Ulm in 2006 . When defining the project, it was found that due to the high structural mass of the B13, only a very low rate of climb would be achieved. As an interim solution, the aircraft was operated exclusively in glider flight with 33 kg ballast in the nose of the fuselage without a motor, propeller sledge and fuel tank .
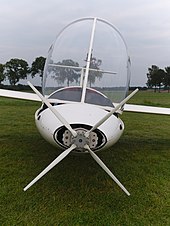
In 2014 the electric motorization was taken up again. An Enstroj Emrax 207 electric motor, which drives a four-bladed propeller with 22 kW of power, should ensure a range of more than 50 kilometers with a climb rate of 1.2 m / s.
construction
The fuselage with a large constriction was created as a shell - stringer construction in a hybrid construction made of carbon and aramid fiber reinforced plastic (CFRP / AFK). The cockpit is spanned by a one-piece acrylic glass hood with a reinforcing stringer. The manually retractable braked main wheel was taken over from the Schleicher ASH 25 .
The wing profile is a modified HQ 41. The four-part wings - triple trapezoidal in plan - measure 23.20 meters and have double-decker Schempp - Hirth brake flaps that extend upwards and flaps overlaid with the aileron control . The T-shaped tail is in CFK / GFK - clamshell running. The contour of the horizontal stabilizer corresponds to that of the glass wing 604 Kestrel . The engine compartment with a slide for extending the folding propeller is located between the legs of the crew in the tip of the fuselage.
Technical specifications
Parameter | Data |
---|---|
crew | 1 + 1 (side by side) |
Hull length | 8.55 m |
span | 23.20 m |
Vertical tail unit height | 1.70 m |
Wing area | 18.95 m² |
Wing extension | 28.4 |
Wing profile | HQ 41 / 14-35 |
Glide ratio | 49 at 105 km / h |
Slightest sinking | 0.55 m / s at 75 km / h |
Payload | 210 kg |
Empty mass | 579 kg |
Max. Takeoff mass | 820 kg |
Wing loading | 35-42 kg / m² |
Top speed | 280 km / h |
Comparable types
Related developments
See also
literature
- Dietmar Geistmann: Gliders in Germany . 2nd Edition. Motorbuch Verlag, Stuttgart 1994, ISBN 3-613-01449-1 , p. 20 .
Web links
- B13 in the J2mcL Planeurs glider database
- B13e on the Akaflieg website
Individual evidence
- ↑ a b c Akaflieg Berlin: B13 - A new two-seater concept has matured . In: aerokurier . No. 5 . Motor Presse, 1991, ISSN 0341-1281 , DNB 011086580 , p. 76 .
- ↑ Ralf Schneider: 75 years of idaflieg . Ed .: Idaflieg . 1st edition. M. Wehle, Witterschlick / Bonn 1997, ISBN 3-89573-045-9 , p. 201 .
- ↑ Frank Urzynicok: B13 - fledged past two years . In: Akaflieg Berlin (Ed.): Annual Report 1991/1992 . Berlin 1993, p. 27 f .
- ↑ Torsten Sadowski: B13 - something is moving . In: Akademische Fliegergruppe Berlin (Ed.): Annual Report 1999/2000 . Berlin 2001, p. 10-12 .
- ↑ Christina Politz: B13 - State of the art . In: Akademische Fliegergruppe Berlin (Ed.): Annual Report 2003/2004 . Berlin May 2005, p. 13-16 .
- ↑ City of Ulm awards Berblinger Prize 2006 (PDF; 110 kB) November 28, 2006, accessed on November 28, 2019 .
- ↑ B13e - engine. In: b13e.akaflieg-berlin.de. Akaflieg Berlin, accessed on November 4, 2018 (German, English).
- ↑ Akaflieg Berlin: B13 - A new two-seater concept has matured . In: aerokurier . No. 5 . Motor Presse, 1991, ISSN 0341-1281 , DNB 011086580 , p. 75 .
- ^ A b Peter Hofmann: B13 electric turbo . In: Akademische Fliegergruppe (Ed.): Annual Report 2013/2014 . Berlin 2015, DNB 013347667 , p. 9-13 .