Flue gas condensation
Systems for flue gas condensation are used to separate water vapor and other condensable substances from the flue gas in combustion systems .
Depending on the composition of fuel and supply air whose both moisture and the content of chemically bound hydrogen atoms in the fuel, are formed at a combustion varying amounts of water vapor and other condensables in the flue gas. If this is cooled below the dew point in an exhaust gas heat exchanger , water vapor and accompanying substances can condense and the condensation heat released can be transferred to the heat transfer medium . Characterized because the latent heat content of the flue gas is used can consequently the fuel consumption and CO 2 - emissions are reduced.
When the fuels natural gas and heating oil are used, the flue gas condensation is usually set up as a joint component with the boiler or in the form of an air / exhaust system (for preheating the supply air). Such boilers are then referred to as condensing boilers or full condensing boilers .
In the most incomplete running combustion of biogenic materials (for example, pieces of wood -Heizungen, pellet heating , u. A. M.) As well as of coal and combustible waste of the flue gas are deposited on cooling shining soot , fly ash , flue dust , tar or tar and optionally unburned hydrocarbons from. These heavily contaminate the surfaces of the heat exchanger and usually lead to caking , which hinders or clogs the chimney draft (see also slag (combustion residue ) # caking ). That is why, for example, chimney stoves and tiled stoves without a flue gas condensation system are operated with exhaust gas temperatures above 120 ° C. The pollutants and water vapor (whose heat of condensation and residual energy content make up around 70% of the calorific value) are emitted into the environment.
Cooling down below the dew point
The dew point temperature of condensable constituents in flue gases is as Rauchgastaupunkt referred. Flue gas without carbon black and liquid water ( fog droplets) is (according to DIN EN 1443) as " exhaust gas " refers (in common usage originating from all the combustion processes gas and unknown composition is general and non-specific as "exhaust gas" hereinafter). The associated dew point is called the exhaust gas dew point .
If mixtures (for example of hydrocarbons) in multicomponent systems have a boiling point range (boiling points close to one another, no “classic boiling range” of zeotropic mixtures ) or condensation point range, only one dew point range can be measured for these.

If the Rauchgastaupunkt in furnaces and fireplaces ( chimneys ) below, so must the components, which are wetted with the condensate liquid-tight and accordingly corrosion be sfest, wherein condensation of water vapor without mineral acids , at least with respect to carbon dioxide .
If flue gas in a chimney made of non-liquid-tight masonry cools below the dew point, the moisture leads to sooting of the chimney and thus to the destruction of the masonry. A flue pipe made of aluminum , stainless steel or plastics ( polypropylene , PTFE , PVDF ) or, for new buildings, chimney flues made of sintered or glazed ceramic protects against this .
The dew point of acids in flue gas is called the acid dew point . The acid dew point of fuels containing sulfur is in the range of 120 to 150 ° C, the water vapor dew point of 45 to 75 ° C is far below. Especially for sulfuric acid, it is called sulfuric acid dew point . To distinguish it from these, the dew point of water vapor is referred to as the water vapor dew point .
Energy efficiency
When burning heating oil , the water vapor dew point in the flue gas is approx. 48 ° C, when burning natural gas (because of its higher hydrogen content) it is approx. 59 ° C. As a result, condensing boilers can be operated with higher return temperatures when burning natural gas than with heating oil and still fall below the dew point. Likewise, when the flue gas cools to approx. 48 ° C, water vapor from natural gas flue gases condenses out, which requires further cooling in the case of heating oil flue gas. Information that 6 percent (for heating oil) to 11 percent (for natural gas) of heating costs (compared to an existing low-temperature boiler with an exhaust gas temperature of approx. 140 ° C) could be saved through the use of the calorific value are rather maximum values of a theoretical nature, which in practice can hardly be achieved.
Whether a condensing boiler or a flue gas condensation system is working optimally can only be determined from the amount of condensate generated. A maximum of approx. 0.9 liters of condensate is calculated for the combustion of one liter of heating oil, and a maximum of approx. 1.63 liters for one cubic meter of natural gas. Since this 900 ml condensate corresponds to approx. 6% energy saving, the efficiency can be calculated from this: 900 ml: 6 = 150 ml. Approx. 150 ml condensate from an oil condensing heating system therefore corresponds to approx. 1% calorific value benefit, which also applies roughly to natural gas. The approximate actual efficiency can then be determined based on the device efficiency specified by the manufacturer.
All data marked with "approx." In the literature are approximate data that also provide approximate calculation results. The reason for this is that heating oil and natural gas have a variable composition and therefore exact values are not possible. Details are only provided by the fuel supplier's calorific value and gross calorific value information. Since this information is mostly related to 0 ° C, the heat of evaporation of water (at 0 ° C equals 2676 kJ / kg) can be used to calculate how much pure water condensate could theoretically accumulate.
When exhaust gases cool below the dew point, the exhaust gas remains 100% saturated with water vapor and other condensates (with a lower proportion of absolute humidity ) despite the separation of condensate . This makes the exhaust gas “drier”, but not necessarily completely dry. A high dew point (with natural gas combustion) allows high return temperatures for cooling, but deeper cooling would still increase the amount of condensate and thus increase the energy yield.
The flue gas can be cooled down to a maximum of the temperature of the coldest medium in the entire heat transfer process:
- when producing hot water, the temperature of the drinking water inlet (approx. 8 ° C) (provided that no return flow booster is installed in which the heat exchanger is never exposed to cold water)
- when reheating or reheating the contents of a hot water storage boiler, the temperature of the hot water (which varies between the cold water temperature and the hot water temperature, depending on the temperature zone of the storage tank that is being reheated)
- with active heating water circulation the temperature of the heating return
- when reheating a heating buffer storage tank, the respective temperature of the storage tank water (which varies between the return temperature of the heating and the maximum operating temperature of the storage tank, depending on the temperature zone of the storage tank that is currently being reheated)
- with installed air preheating, the temperature of the fresh air drawn in,
Depending on the output of the boiler, this can bring cold water to the desired final temperature in one heating process, in such a case the calorific value effect is usually used well. However, if the output of the device is too low, this “temperature spread” (difference between flow temperature and return temperature) is small and the water in a storage boiler has to be circulated twice or more until the target temperature is reached. In this case, the calorific value effect is only used at the beginning and continuously decreases as the storage water heats up. In order to still be able to use the calorific value effect, either the flow rate through the boiler must be reduced, which increases the temperature spread, or the target temperature of the storage water is reduced (lowering the flow temperature or the hot water temperature).
(see condensing boiler technology ).
The humidity of the supply air can only be condensed in a flue gas condensation system if the temperature of the heat transfer medium would undershoot the dew point of the intake air, which is rarely the case. If air preheating is installed, the exhaust gas cannot be cooled below the temperature of the fresh air in winter, so the dew point of the fresh air is never fallen below (in this case). The moisture content of the fresh air then remains uncondensed in the exhaust gas and goes through the heating system as a "pass-through item".
The air humidity represents a gain because for the residual moisture in the exhaust gas after condensation, only the difference between the supply air humidity and dew point humidity has to be fed from the fuel and the "excess" condenses out with heat gain. The heat gain is therefore higher, the more humid the supply air is (the amount of condensate “saved” by the air is the same as its water content). The moisture in the supply air also does not lead to the flame cooling (and, due to incomplete combustion, poor fuel utilization) since the moisture is already in vapor form (unless mist- containing air is sucked in). When intake of fresh air from the boiler room (in the basement) so other restricted latent heat can (from the drying out of the building moisture if the boiler room is used for drying laundry, bathroom and sauna exhaust air from the controlled ventilation ) are recovered.
The dew point is increased by excess air in the flue gas (and thus the yield of condensate is reduced), because the additional air binds more water vapor, but at the same time cools the combustion, i.e. it lowers the combustion temperature and the flue gas temperature, which must be taken into account when using the calorific value .
The deeper the flue gas is cooled, the more water vapor or condensates can condense and the more condensation heat can be used. After condensation, the flue gas remains 100% saturated (with a now lower absolute amount of water vapor or condensates) .
The formation of carbon monoxide (with a residual calorific value) in the event of incomplete combustion also leads to a significant reduction in the thermal energy yield and thus to lower energy efficiency (for energy efficiency see also Boiler # Energy Waste and Degree of Use ).
Dew point curves
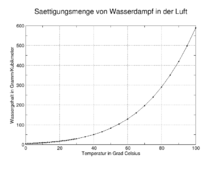
If you create a diagram in which the humidity of the air is plotted against the temperature, then all states in which the water vapor is saturated , i.e. all possible dew points, form a humidity-dependent and temperature-dependent dew point curve . This is similar to the shape of the phase boundary line in a fabric - phase diagram between the state rooms gas and liquid, but is this not the same . Starting from a known gas humidity, a horizontal line can be drawn in the diagram, the intersection of this line with the dew point curve is the "dew point" corresponding to this gas humidity , its assigned temperature (a vertical line drawn in the diagram) then the so-called dew point temperature , which is simplified and abbreviated also often referred to as "dew point" is referred to and also with the unit ° C is specified.
A "dew point (s) curve of water vapor in air" is formed from the pairs of values from humidity and the associated dew point temperature. It can be read from it below which dew point temperature water vapor condenses depending on the moisture content of the air.
This dew point curve is often used approximately for the condensation of the condensable substances in an exhaust gas, although the actual course of the curve depends on the material composition of the exhaust gas and the prevailing pressure (for example with natural drafts or an induced draft fan of a vacuum furnace).
Dew points can also be read from a carrier diagram (according to Willis Carrier ). Such a carrier diagram according to DIN 4108 shows the curves in which the relative humidity corresponds to values from 10%, 20%, ... to 100%, the 100% curve being the same as the dew point curve.
A Mollier-hx diagram shows the same thing as a carrier diagram with reversed axes (the diagram placed on edge and mirrored).
The respective dew point temperature is at the same time (also approximately approximately) a measure for the respective existing humidity of an exhaust gas. The statement “When heating oil is burned, the water vapor dew point in the flue gas is approx. 48 ° C” basically describes the amount of moisture that comes from the oxidation of the hydrogen atoms in the heating oil, which corresponds to a certain dew point temperature. The water vapor oversaturation (more precisely the condensate oversaturation), which occurs when the temperature falls below the dew point, leads to the fact that the excess water vapor condenses out and a residual moisture corresponding to the current temperature remains in the exhaust gas. A further decrease in the temperature of the exhaust gas (through heat transfer) then leads to further condensation.
The above statement, the water vapor dew point would be 45 to 75 ° C, takes into account the dependence of the dew point on different exhaust gas compositions and thus different moisture contents of various fuels.
Condensation areas in a heat exchanger
Depending on their dew points, the condensable substances condense at different temperatures, in the hottest zone of a heat exchanger (close to the combustion chamber) the substances with the highest dew point and in the coldest zone of the heat exchanger (near the chimney or in the chimney pipe) the substances with the lowest dew point . In between, all substances condense according to their content in the carrier gas at all temperatures that their pure substance dew point curve allows. This can lead to different substances being deposited or deposited on different heat exchanger pipe sections. Pyrolyzed unburned resin, tars and fatty acids with a dew point of 70 ° C stick one heat exchanger section and the water vapor condenses on another heat exchanger section. However, the watery condensate components returning from the chimney are not always able to detach the tarry deposits (to which fly dust also sticks), as a result of which this part of the heat exchanger sticks together and baked up with fly dust. -This is one of the reasons why condensing flue gas condensation in small wood heating systems is only hesitantly addressed by manufacturers.
If a return flow increase is built into the heat exchanger , a variable part of the (hot) flow medium is added to the (cold) return flow using a mixing valve, thus raising the minimum condensation temperature. This is to prevent acidic water vapor or tar from condensing on heat exchanger sections that are unsuitable for this (insufficiently corrosion-resistant or difficult to clean) or to prevent resublimation or recombination of glossy soot . When replacing an old heating system with a new condensing boiler, a return increase must be removed in order to be able to use the condensing effect.
ecology
- Increased use of heat: Since the condensation of the condensable substances in the flue gas means that all of the heat, including latent heat, is used, flue gas condensation has positive ecological effects.
- Flue gas condensation also has a cleaning effect on the flue gases; apart from the condensable components, fine dust components and ionized substances that could recombine to fine dust are washed out with the condensate. As a result, heavy metals accumulate in the condensate or, in the case of large combustion systems, in the neutralized condensate sludge, but are then no longer emitted into the air.
- Since the pH value of condensate is always acidic due to the acids it contains and domestic wastewater is mostly basic and helps to neutralize the condensate, condensates from small combustion systems can be discharged into the sewer system in accordance with the respective officially established discharge conditions.
Flue gas condensation in large combustion systems
System structure using the example of a large combustion system

The stage upstream of the flue gas condensation is usually the economizer , which uses the sensible heat of the flue gas and, in the case of dusty flue gas, also a centrifugal separator and / or electrostatic filter .
The flue gas is then fed to the condenser, which uses the latent heat that can be obtained at temperatures of approx. 55 to 70 ° C, depending on the fuel. The condenser is therefore only suitable for generating low-temperature heat, so the latent heat is extracted and used, for example, for a hot water local heating network. The lower the water temperature with which the condenser is charged, the higher the energy yield of the condenser.
The condensation does not take place at a single temperature, but takes place over an extensive temperature range. The temperature zone for condensation depends on the composition of the flue gas. Your course is z. B. described by the saturation curve in the Mollier diagram . In addition, the temperature in the cross section of an exhaust pipe has a parabolic course, the flue gas is cooler on the walls of the heat exchanger or on the exhaust pipe than in the hotter core of the exhaust gas flow. Special fixtures for swirling the flue gas provide a remedy.
The flue gas, which has now cooled down to below the original dew point , still contains a residual proportion of water vapor and usable heat, which can be extracted in an air preheater ( rotary heat exchanger or, in the case of small combustion systems, in an air-flue gas system ). Air is warmed up, which can be used either to dry the fuel, as preheated combustion air or as exhaust air.
A discharge stage can be arranged as the last stage of the system. This serves to avoid or reduce the plume of water vapor at the chimney outlet. The formation of a steam plume is primarily dependent on the dew point of the exhaust gas and the current air temperature, the resolution of the steam plume on the current air humidity, more precisely the moisture absorption capacity of the air. By adding air from the air preheater to the exhaust gas, its relative humidity is reduced and the tendency to form plumes is reduced.
Modern procedures
By using flue gas condensation, biomass heating power plants can increase the thermal efficiency by 30% to 117%.
Various methods are available for "network return heating" (heating the return of a local or district heating network), for example:
Flue gas condensation ...
- with absorption chillers
- with combustion air humidification
- with lithium bromide absorption process
- with heat pumps
- for heating the feed water in steam power plants
Ecological aspects in large systems
- Lowest dust pollution: Since in large systems the flue gas condensation generally follows the normal flue gas dedusting and dust is also extracted via the condensate , the dust contents are much lower and mostly only slightly above the detection limit.
- Neutralization and cleaning of the condensate necessary: The condensate contains fly ash and fly dust , which are separated out as sludge. This sludge has a low solids content, so it consists almost entirely of acidic water and has to be dewatered and neutralized in a complex process.
- Increased electricity demand: The pressure loss due to the additional heat exchangers causes a higher or additional electrical drive power in the exhaust air and flue gas fans in large systems and causes a considerable energy demand.
Individual evidence
- ↑ Poisonous fire leech. In: Der Spiegel. 1/1988, Spiegel online
- ^ Lueger: Lexicon of technology. Volume 17, p. 223.
- ↑ H. Göddekke, A. Höß, A. Kalisch, E. Memmert, R. Michel, W. Münz, D. Stehmeier, I. Steiglechner, H. Vogel: exhaust systems. Comment on DIN EN 15287-1 . 2nd, expanded edition. Beuth Verlag, Berlin / Vienna / Zurich 2009, ISBN 978-3-410-16295-7 ( limited preview in Google book search).
- ↑ a b Günter Cerbe: Fundamentals of Gas Technology . 7th edition. Hanser Verlag, Munich / Vienna 2008, ISBN 978-3-446-41352-8 ( limited preview in Google book search).
- ↑ Helmut Effenberger: Steam generation . Springer, Berlin / Heidelberg / New York 2000, ISBN 3-540-64175-0 ( limited preview in the Google book search).
- ↑ a b Technical terms explained in a simple and understandable way: condensing technology
- ↑ Effectiveness of the calorific value heating. (No longer available online.) In: Brennwert.info. ConSoft GmbH, archived from the original on March 4, 2016 ; accessed on February 26, 2016 . Info: The archive link was inserted automatically and has not yet been checked. Please check the original and archive link according to the instructions and then remove this notice.
- ↑ Wolfgang Naumer: Build and modernize energy-saving . Haufe, Munich 2008, ISBN 978-3-448-08599-0 ( limited preview in the Google book search).
- ^ Klaus Jens: Lectures on building technology. (PDF file; 678 kB) ( Memento of the original from October 17, 2013 in the Internet Archive ) Info: The archive link was inserted automatically and has not yet been checked. Please check the original and archive link according to the instructions and then remove this notice. at the Vienna University of Technology
- ↑ Bernd Genath: Pellets have a hard time with calorific value. Document of the Federal Association of Chimney Sweepers PDF file ( Memento of the original from August 1, 2012 in the Internet Archive ) Info: The archive link was inserted automatically and has not yet been checked. Please check the original and archive link according to the instructions and then remove this notice.
- ↑ Heat recovery in a reference system of 4.1 MW at a biomass cogeneration plant in Grindelwald / Switzerland; Scheuch; As of March 26, 2010
- ^ Jürgen Karl: Decentralized energy systems. New technologies in the liberalized energy market . 3. Edition. Oldenbourg, Munich 2012, ISBN 978-3-486-70885-1 ( limited preview in Google book search).
- ↑ Frequently asked questions: What does the term "dew point" mean? ( Memento of the original from October 2, 2013 in the Internet Archive ) Info: The archive link was inserted automatically and has not yet been checked. Please check the original and archive link according to the instructions and then remove this notice. at procondens.de
- ↑ a b Matthias Gaderer: Newer concepts for combined heat and power with biomass. Bavarian Center for Applied Energy Research eV (ZAE-Bayern) ( PDF file ( Memento of the original from October 17, 2013 in the Internet Archive ) Info: The archive link has been inserted automatically and has not yet been checked. Please check the original and archive link according to the instructions and remove then this note. ).
- ↑ Bebette Hebenstreit, Rosemarie Schnetzinger, Ernst Höftberger: Final Report ActiveCond. Active flue gas condensation with heat pumps to increase the efficiency of near-series, automatically charged biomass firing. PDF file , Graz 2012, at bioenergiy2000.eu
- ↑ Reinhard Schu, Karl J. Thomé – Kozmiensky, Michael Beckmann: Increasing the energy efficiency of waste incineration plants through process management and system switching. (PDF file) , 2006, at ecoenergy.de