European Vital Computer
The European Vital Computer (abbreviation EVC ) is a safe vehicle computer in the European train control system ETCS and the core of the vehicle equipment.
While only a description of the infrastructure is transmitted to the vehicle from the track side, the EVC is responsible for carrying out the resulting actions, for example maintaining braking curves or controlling the main switch on protective lines of the overhead line . Other secure tasks include route and speed monitoring , the processing of ETCS driving permits and level and mode changes . The information that is provided on the track side includes, for example, permissible speeds, gradient profiles and slip paths .
Around 4,000 ETCS on-board devices are in use in Europe, and around 14,000 more have been ordered (as of October 2019).
In German-speaking countries there is no common translation for the EVC. Among the translations include on-board computer , ETCS on-board computer ETCS onboard unit , ETCS on-board computer , ETCS host , ETCS computer , ETCS central unit , vehicle computer , fail-safe computer for ETCS , vehicle system , the core of the ETCS , secure computer central unit , computer and central computer .
Integration into the vehicle
On locomotives , a common EVC is usually installed for both cabs ; on multiple units , depending on the EVC supplier and train length, two EVCs can also be used. The decisive factors are u. a. maximum cable lengths.
The installation location of the EVC receiving housing is u. a. selected taking into account aspects of suitable environmental conditions (including air conditioning / ventilation), fire protection, electromagnetic compatibility and protection against unauthorized access.
The required installation space depends on the respective supplier.
Interfaces
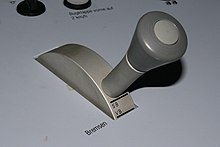
The EVC must have an interface to the train, e.g. a. to control the brake and switch off traction . In addition, information is tapped from switches, for example about the direction of travel and activation of a driver's cab. Optionally, the MMI / DMI control of the pantograph , the braking unit or the main switch can also be connected to the EVC. In some applications, a button for confirming ETCS functions is built in.

The EVC train interface can either be done with discrete inputs and outputs or by means of a bus (e.g. Profibus , MVB , CAN ). Safety- relevant signals must be transmitted via redundant and independent signal paths. Mixed forms are possible, such as braking requirements on train bus and additional access to emergency braking loops via relay ( contactor relay ). A gateway is sometimes also arranged between the EVC and the vehicle bus .
Due to the large number of different vehicles, no uniform EVC train interface has yet been defined.
Some operators consider it necessary to encrypt EVC interfaces, for example to the balise reader (BTM) or the display ( DMI ).
The transfer of train data via the vehicle bus is also possible.
construction
The EVC is not explicitly mentioned in the ETCS reference architecture. The structure and design of the EVC as well as many interfaces and peripheral systems are manufacturer-specific. EVCs are designed as 2-out-of-2 or 2-out-of-3 computer systems , depending on the supplier .
The EVC can contain modules for input and output, configuration parameters, power supply, odometry, balise antenna and GSM-R . In the case of DMIs according to ETCS Baseline 3 , which have to guarantee a reliable display of certain information, the necessary comparison of the data transmitted to the DMI and the data actually displayed sometimes falls to the EVC. The EVC can be connected to an on-board information system via an interface. With the suspension railway Wuppertal , for example, operational registration data of the train to the EVC and odometry data of the train to the on-board information system are transmitted.
For example, when equipping the 403 series , Alstom used a two-out-of-three computer system in which two computers contain all interfaces and a third only contains assemblies for configuration parameters, odometry and power supply. The third computer runs in hot standby and becomes active if one of the other two EVCs fails. If two computers fail, an irreversible emergency brake is initiated. The DMI image is calculated in the EVC.
Siemens, on the other hand, uses a high-availability 2-of-2 computer system with three height units (status: 2010). A Non Vital Computer (NVC) contains the diagnostic system, the project planning and the data transmission functionalities that are not secure in terms of signaling. The DMI image is calculated in the DMI.
Interaction with national systems
If a vehicle is equipped with other train control systems (e.g. class B systems ) in addition to ETCS , there are four options for connecting the EVC - depending on the operational, technical and economic framework conditions:
- If a national train control system is connected to the EVC as a Specific Transmission Module (STM), the necessary interfaces of the STM are routed via the EVC. The STM uses the EVC for this purpose. a. to receive odometry data, to display information on the DMI or to trigger brakes. Profibus is used to connect the EVC to STMs. This solution is associated with considerable development effort and therefore only makes sense for functionally comprehensive naitonal systems. For example, the line train control in Spain is operated as an STM. The connection as STM is generally considered to be the preferred variant.
- National train control systems can also be connected as semi-STM (also specific bus coupling ). The system is controlled in normal operation via the existing vehicle bus; in the event of malfunctions, they can also be operated without EVC. ETCS (EVC) and the national system communicate with the surrounding systems via a common bus, the coupling of the two train control systems serves exclusively to control the transitions. While the interventions in ETCS and the national system can be reduced, additional work arises in the peripheral systems such as the DMI and the data recorder (JRU). For example, the LZB in Germany (coupled via MVB) was specified in this way by Deutsche Bahn.
- An EVC can also be designed as a bi-standard EVC (sometimes also dual-standard EVC ). The ETCS EVC takes over the function of the national train control system. The function of the national system can be linked within the EVC or by means of proprietary interfaces. This solution is ideal for simple national systems or when there is an acute lack of space. In addition, national expansions that offer operational advantages can be implemented. For example, EVM in Hungary (with implementation in EVC) or EBICAB and Bulgaria (with EVC-internal translation in ETCS telegrams) was implemented in this way. This solution is often developed by manufacturers of national train control systems for their home markets.
- In principle, parallel operation of the EVC for ETCS and a national system is also possible. Both systems largely use their own peripheral systems (e.g. data recording, odometry), the coupling of the EVC and the national system takes place via a bus connection or relay contacts and is only used to control and monitor the transitions. Such a solution comes into consideration if other solutions are not economically viable or if the systems involved are operationally independent. For example, ATS in Turkey or MIREL in Slovakia (via an RS-485 interface ) was connected.
conditions
An on-board unit must be ready to enter the driver's number within three seconds of activating the driver's cab and, in the simplest case, be ready for shunting (ETCS Mode Shunting, SH) within 15 seconds .
The power supply of the EVC is considered to be a major weak point of the ETCS vehicle architecture. The reference architecture therefore provides for two redundant power supplies. The connection to peripheral systems is also redundant.
ETCS on-board units must be used on DB Netz u. a. meet an MTBF of at least 23,000 hours and a technical availability of 99.9913%.
Testing
The conformity of EVCs to the ETCS specification is described in Subset-094 of the ETCS specification. The EVC is integrated in a test adapter, the behavior described in around 800 specified test sequences is converted into logical and physical signals and checked for functional correctness and completeness. Such a universal interface , also known as an I / OSI adapter (In / Out System Interface ), enables the functions of necessary peripheral devices such as balises and modems to be used in interoperability tests and assumed to be error-free.
The interoperability to ensure are also special interoperability tests in which, for example, a RBC with integrated, is offered. The cases described in subsets 110, 111 and 112 focus on scenarios that require the components involved to interact.
Suppliers
ETCS vehicle equipment is offered by various suppliers:
- Alstom ( Atlas )
- Bombardier ( EBI Cab 2000 )
- CRCC ( SigThemis )
- Siemens Mobility ( Trainguard 100 for Level 1, Trainguard 200 for Level 2)
- Thales ( AlTrac )
Stadler announced in 2017 that it would manufacture its own ETCS on-board devices. To this end, Stadler and Mermec founded the Angelstar joint venture . The as Guardia designated system is scheduled to start on Flirt trains of BLS are used. At the beginning of 2019, field and approval tests were carried out in Switzerland and other European countries.
The Company The Company Signaling to announced in 2019, the future manufacture ETCS on-board equipment.
Alcatel offered ETCS on- board devices under the name ALTRACS BDZ .
history
In the mid-1990s, the ETCS vehicle architecture provided for a non-secure management computer (MC) in addition to the EVC (for safety-relevant systems) . He was responsible for functions such as diagnostics or the control of the operating devices (MMI), which were therefore not included in the EVC's safety verification. By 2000, however, control was the responsibility of the EVC.
In the mid-1990s, various degrees of modularity were considered for the on-board device, ranging from full hardware and software modularity (with defined, manufacturer-independent interfaces) to black box solutions.
An Operating System Switch (OSS) was considered as an alternative to the STM around 1996 . Switching between different train control systems should have taken place. This would have required a standardized EVC - u. a. in terms of interfaces, basic functions, operating system and programming language - so that one supplier could have integrated the software of another supplier.
In the “Class 1” specification passed by UNISIG to the European Commission in April 2000 , the standardization of the vehicle architecture was largely abandoned compared to the previous version A200. I.a. standardized interfaces were not used. Such a standardized vehicle equipment was called EURO-Cab . Their elements should be connected to the EVC via an ETCS bus. The underlying project Eurocab was one of several cooperation projects of the European signaling industry ( EUROSIG ).
After a software upgrade to around 140 locomotives in Switzerland, there were more EVC connections at the end of 2004. If this error occurs, it should not continue to drive even after a vehicle reset. The error should be fixed with another update.
As part of the openETCS project, Deutsche Bahn pursued the idea in the 2010s of developing uniform EVC software under an open source license , which ETCS suppliers should supplement with specific APIs and hardware- specific adaptations.
For the implementation of automated driving , two conceptual approaches were discussed in the context of Shift2Rail around 2016: the implementation of the ATO functions in the EVC (with additional software) or the use of an ATO architecture with separate hardware. In any case, the safety responsibility should rest exclusively with the train control system.
From August 2017, EVCs on Cityjet multiple units of the ÖBB series 4744 and 4746 were subjected to a safety test according to Baseline 3 for the first time.
Others
In order to measure the quality of service parameters of the GSM-R data transmission, an EVC can be simulated on the vehicle side.
A train completeness check (for ETCS Level 3 ) can be implemented through position reports of two EVCs running at the beginning and end of a train .
In France, a vehicle solution called NextEVC (previously EVC Portable ) is to be put out to tender . The localization should be exclusively based on satellites and the balise information should be replaced by cellular information.
Web links
- ETCS specification on the homepage of the European Railway Agency (ERA)
- ETCS manual for train drivers in Word and HTML format on the homepage of the European Railway Agency.
Individual evidence
- ↑ a b Thorsten Büker: ETCS Level 1 LS (ESG) under the aspect of performance . In: Railway technical review . No. 11 , November 2017, ISSN 0013-2845 , p. 24-31 .
- ↑ Marcin Wójci: State of play of ERTMS deployment: recent progress track-side and on-board. (PDF) In: era.europa.eu. DG MOVE , October 16, 2019, p. 15 , accessed on October 31, 2019 .
- ↑ ETCS: Opportunities and Risks for the First Stage Rail 2000 . In: Swiss Railway Review . No. 3 , January 2003, ISSN 1022-7113 , p. 38-41 .
- ↑ Peer Jacobsen: Tradition and Future: The Wuppertal Suspension Railway with ETCS Level 3 and TETRA . In: Railway technical review . No. 6 , June 2014, ISSN 0013-2845 , p. 54-57 .
- ↑ New delay at ETCS on the NBS Mattstetten - Rothrist . In: Eisenbahn-Revue International . No. 1 , 2007, ISSN 1421-2811 , p. 13 f .
- ↑ New line VDE 8.1 opened . In: Eisenbahn-Revue International . No. 2 , February 2018, ISSN 1421-2811 , p. 70-72 .
- ↑ Stefan Seither: Online Key Management for ETCS . In: signal + wire . tape 108 , no. 9 , September 2016, ISSN 0037-4997 , p. 51-57 .
- ↑ a b c d e f g h Klaus Mindel, Oliver Scheck: Economical equipping of locomotives with ETCS . In: ZEVrail , conference proceedings SFT Graz 2011 . tape 135 , 2011, ISSN 1618-8330 , p. 32-39 .
- ↑ The future of ETCS in Germany . In: Union of German Locomotive Drivers (Ed.): Advance . 9 ff. September 2018, ISSN 1438-0099 , p. 27 / ff .
- ↑ a b Niels Neuberg: The use of ETCS Level 1 Limited Supervision at Deutsche Bahn AG . In: signal + wire . tape 106 , no. December 12 , 2014, ISSN 0037-4997 , p. 12-18 .
- ^ Klaus Hornemann, Bernd Fröhlich: Application of the Eurobalise at DB Netz AG . In: Signal + Draht Spezial . Use of the Eurobalise at DB Netz AG. No. October 11 , 2015, ISSN 0037-4997 .
- ↑ Research campus : ETCS Level 3 . In: turntable . No. 291 , ISSN 0934-2230 , p. 80 f .
- ↑ a b Markus Bolli: ERTMS / ETCS - the future has begun . In: signal + wire . tape 101 , no. 3 , 2009, ISSN 0037-4997 , p. 6-12 .
- ^ A b Christian Kindinger, Hans Kron, Dieter Wolff: ETCS in local traffic . In: Local transport . No. 4 , April 2017, p. 33-38 .
- ↑ Olaf Gröpler: Braking distances and braking distance safety at ETCS . In: ZEVrail . tape 132 , no. 1-2 , ISSN 1618-8330 , p. 31-39 .
- ^ Karl Kammel, Frank Leißner: ETCS Migration - Challenge and Possible Solution . In: Railway technical review . No. 5 , May 2007, ISSN 0013-2845 , p. 254-260 .
- ^ André Daubitz, Frank de Gavarelli, Marcus Schenkel: A major project on the home straight - the new line between Erfurt and Leipzig / Halle . In: Railway technical review . No. December 12 , 2015, ISSN 0013-2845 , p. 33-42 .
- ↑ a b Joachim Nordmann: LZB80 based on an ETCS core with PZB90 function . In: signal + wire . tape 96 , no. 9 , 2004, ISSN 0037-4997 , p. 41-46 .
- ↑ Jesús Telo Rodríguez: Dammam - Riad, first ETCS L1 line in the MENA region in Saudi Arabia successfully in operation . In: signal + wire . tape 110 , no. 10 , 2018, ISSN 0037-4997 , p. 6-11 .
- ↑ a b Hartmut Thies, Andreas Wik: The SBB's FSS pilot project - the world's first application of ETCS Level 2 . In: signal + wire . tape 92 , no. September 9 , 2000, ISSN 0037-4997 , pp. 16-24 .
- ↑ a b Marc Joseph, Michael Trobler: Free travel in Switzerland for ETCS Level 2 with Siemens Trainguard 200 and "Switzerland Package" . In: Eisenbahn-Revue International . No. 10 , 2008, ISSN 1421-2811 , p. 492-494 .
- ↑ Suspension railway with ETCS . In: Eisenbahn-Revue International . No. 7 , July 2012, ISSN 1421-2811 , p. 360 .
- ^ Johannes Braun, Jean-Yves Koulischer, Christian Schunke-Mau: With ETCS "active" through Germany . In: signal + wire . tape 102 , no. 5 , May 2010, ISSN 0037-4997 , p. 34-38 .
- ^ A b c Bernhard Ptok: ETCS - core of the "European Railway Traffic Management System" . In: The Railway Engineer . No. 3 , March 1996, ISSN 0013-2810 , pp. 56 ff .
- ↑ a b Installation of ETCS on- board units . In: Swiss Railway Review . No. 4 , November 2004, ISSN 1022-7113 , p. 484 .
- ↑ a b ÖBB Cityjet in the ETCS safety trial . In: Eisenbahn-Revue International . No. October 10 , 2017, ISSN 1421-2811 , p. 518 .
- ↑ National ETCS solutions or standardization of the ETCS? In: Eisenbahn-Revue International . No. 2 , February 2009, ISSN 1421-2811 , p. 66-69 .
- ↑ a b c d e f Carsten Haselkuss: Engineering for on board units . In: Peter Stanley (Ed.): ETCS for engineers . 1st edition. Eurailpress, Hamburg 2011, ISBN 978-3-7771-0416-4 , pp. 288-296 .
- ↑ a b Roland Stadlbauer: Efficient equipping of rail vehicles with ETCS using the example of Slovakia . In: signal + wire . tape 108 , no. November 11 , 2016, ISSN 0037-4997 , p. 29-37 .
- ↑ a b c d e ETCS installation in class 403 multiple units . In: Union of German Locomotive Drivers (Ed.): Advance . No. October 10 , 2017, ISSN 1438-0099 , p. 24-26 .
- ↑ ETCS specification , subset 026, version 3.6.0, section 2.5.3, p. 11.
- ↑ Dana Schiffer: Redundant and secure - requirements for a modern DMI in ETCS . In: Railway technical review . No. 9 , September 2019, ISSN 0013-2845 , p. 70-72 .
- ^ A b Ines Hamberger: ETCS operation of the Westbahn between Vienna and Salzburg . In: ZEVrail . tape 140 , no. 8 , August 2016, ISSN 1618-8330 , p. 292-297 .
- ↑ a b c d e f g h i Josef Löwe, Ulrich Lehmann: ETCS migration of traction vehicles with Trainguard . In: signal + wire . tape 102 , no. 4 , April 2010, ISSN 0037-4997 , p. 18-23 .
- ↑ François Lacôte, Jacques Pore: ERTMS / ETCS is reality . In: signal + wire . tape 96 , no. 10 , 2004, ISSN 0037-4997 , p. 6-12 .
- ↑ ETCS specification , subset 041, version 3.2.0, p. 14.
- ↑ a b Francesco Flammini, Stefano Marrone, Mauro Iacono, Nicola Mazzocca, Valeria Vittorini: A multiformalism modular approach to ERTMS / ETCS failure modeling . In: International Journal of Reliability, Quality and Safety Engineering . tape 21 , no. 1 , 2014, ISSN 0218-5393 , p. - , doi : 10.1142 / S0218539314500016 .
- ↑ Information brochure for the Europe-wide market research process to prepare for the manufacture, delivery and maintenance of electric rail vehicles for future use in Baden-Württemberg. (PDF) In: nvbw.de. Ministry of Transport Baden-Württemberg, p. 8 , accessed on December 7, 2019 .
- ↑ a b Michael Meyer zu Hörste, Mirko Caspar, Lennart Asbach, Oliver Röwer: V&V from LST components ... from the line to the laboratory . In: Railway technical review . No. 3 , March 2019, ISSN 0013-2845 , p. 32-36 .
- ↑ Uwe Kohlsdorf, John Patrick Brady Steinebach: Test and trial for the commissioning of the ETCS line equipment in the VDE 8.2 project . In: signal + wire . tape 109 , no. 1 + 2 , January 2017, ISSN 0037-4997 , p. 6-14 .
- ^ Roger Hall: ETCS vehicle equipment in the Netherlands . In: signal + wire . tape 98 , no. 9 , September 2006, ISSN 0037-4997 , p. 6-10 .
- ↑ Keith Barrow: CRRC unveils SigThemis ETCS solution. In: railwayjournal.com. June 10, 2019, accessed October 31, 2019 .
- ↑ Ubbo Lanske: ETCS test and presentation train Trainguard® for Europe-wide use . In: Railway technical review . No. 3 , March 2006, ISSN 0013-2845 , p. 140-144 .
- ↑ European Train Control System (ETCS) compliant solutions. In: thalesgroup.com. Thales, accessed October 31, 2019 .
- ↑ SBB train accelerates and brakes automatically . In: Eisenbahn-Revue International . No. 2 , February 2018, ISSN 1421-2811 , p. 78 .
- ↑ Flirt from BLS receive Guardia train protection . In: The Railway Engineer . No. 1 , January 2019, ISSN 0013-2810 , p. 67 .
- ^ The Signaling Company. A Better ETCS Onboard. In: thesignallingcompany.com. Retrieved October 31, 2019 .
- ^ Josef Doppelbauer, Dietrich Rhein, Christo Angelov, Manfred Hartberger: Introduction of ERTMS / ETCS from a Supplier's Point of View . In: signal + wire . tape 92 , no. 9 , 2000, ISSN 0037-4997 , p. 57-60 .
- ↑ a b Bo Gedda: ETCS Eurobalise . In: signal + wire . tape 88 , no. 11 , November 5, 1996, ISSN 0037-4997 , pp. 5-7 .
- ^ Peter Winter : ETCS project history . In: UIC (Ed.): Compendium on ERTMS . DVV Media Group, Hamburg 2009, ISBN 978-3-7771-0396-9 , p. 69-81 .
- ^ Jörn Pachl : Train control systems of European railways . In: Railway technical review . No. November 11 , 2000, ISSN 0013-2845 , pp. 725-733 .
- ^ Ulrich Lehmann: Activities of Siemens for the introduction of the EURO-Balise S21 . In: signal + wire . tape 88 , no. December 12 , 1996, ISSN 0037-4997 , pp. 21-26 .
- ↑ Klaus-Rüdiger Hase: An open approach to interoperability . In: Railway Gazette International . No. 3 , March 2012, ISSN 0373-5346 , p. 51-53 .
- ↑ Klaus-Rüdiger Hase, Jean Koulischer: openETCS: Open Source Principles for the European Train Control System . In: ZEVrail conference proceedings SFT Graz 2011 . tape 135 , 2011, ISSN 1618-8330 , p. 54-63 .
- ↑ Christoph Gralla: Are we ready for driverless local and long-distance traffic? In: signal + wire . tape 108 , no. 4 , April 2016, ISSN 0037-4997 , p. 6-14 .
- ↑ Andreas Göttig, John Patrick Brady Steinebach: ETCS requirements for GSM-R at DB Netz AG using the example of VDE 8.2 . In: signal + wire . tape 109 , no. 1 + 2 , January 2017, ISSN 0037-4997 , p. 15-24 .
- ↑ Chris Jackson: ETCS Level 2 to boost network capacity . In: Railway Gazette International . tape 172 , no. 4 , April 2016, ISSN 0373-5346 , p. 41-43 .
- ↑ NEXT EVC - CONSULTATION PREALABLE. (PDF; 150 kB) In: Association of Historical Railways Switzerland . SNCF Réseau DGII TTD, February 14, 2019, accessed on May 4, 2019 (French).
- ^ Next EVC - Presentation Generale Du Projet. (PPTX; 1.6 MB) In: Association of Historical Railways Switzerland . SNCF Réseau DGII TTD, October 10, 2018, accessed on May 4, 2019 (French).