Blueprint
Blueprint is a dyeing method for fabrics of linen - or cotton , in which a white pattern is formed on a blue background. This is a reserve print with so-called models , in which the fabric is printed with a protective compound and dyed with indigo . The blue print was also called porcelain print in the 18th century because of the blue and white decoration . The blueprint in Austria , Germany , the Czech Republic ( Modrotisk ), Slovakia ( Modrotlač ) and Hungary ( Kékfestés ) has been included in the Representative List of the Intangible Cultural Heritage of Humanity .
history
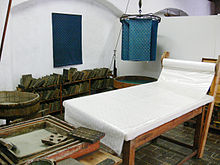
Textile fabrics were initially only colored with pigments . These adhere to the fibers without penetrating. With the Egyptian Copts as well as in India and Java processes for textile dyeing by means of reserve technique were already known at the time of Pliny the Elder . Since its description left questions unanswered, the procedure was not used in Europe. It was not until 1894, when material was found in the tomb of Bishop Caesarius of Arles , that the text written by Pliny was understood. In the meantime the procedure had come to Europe through travelers in connection with the Dutch East India Company . It spread rapidly from there at the end of the 17th century after a calico printing company was founded in Amsterdam in 1678 . The first blueprint in Germany in reserve printing was produced by Jeremias Neuhofer in Augsburg in 1689 or 1690 , but the technique spread quickly.
Reserve pressure was not in the Middle Ages in Europe familiar, because the warm vat with woad broke the reserve wax and glue easily. Pure indigo vats, on the other hand, could be used for cold dyeing, and after 1700 better protective reserves were developed; the oldest recipe for this so-called cardboard is recorded in a Dutch diary from 1727. In 1734 a guild for the blue and fairing trade was founded in Minden-Ravensberg . Further guilds were established by the beginning of the 19th century. In the beginning only linen fabrics were printed, since the 18th century also half linen and cotton fabrics, especially for bed linen , curtains and women's clothing. The craft of blueprint took off in the 18th century.
Since before industrialization wealth was mainly expressed through expensive fabrics and elaborate embroidery and processing methods such as picture knitting, blue printing, in which mainly hand-woven linen fabrics of the rural population were printed, was considered an art of the poor people. It was also possible to dye in other colors than the preferred and eponymous blue by using madder instead of indigo for a red color or yellow woof for a yellow color.
Today's distribution
Industrialization and the ensuing mechanical roller printing meant the end of most blueprint workshops. The blueprint is not produced industrially. Today there are only a few handicraft businesses in Europe that have mastered the production of models and the old printing techniques.
Most blueprinters are in Germany with 12 workshops. The oldest still active blueprint workshop in Europe is located in Einbeck in Lower Saxony. There are other blue printer workshops in Lower Saxony in Scheeßel and Jever . In Bavaria there is only one master craft business with the Fromholzer hand printing and dyeing works in Ruhmannsfelden , which has existed since 1640.
In the Czech Republic and Slovakia, three blueprinting plants are active as a family business and in Hungary six.
In Austria there are two traditional companies - Blaudruck Wagner in Bad Leonfelden in the Mühlviertel of Upper Austria and Blaudruckerei Koó in Steinberg-Dörfl in Burgenland. The Gutau Dyer's Museum (also in the Mühlviertel) has been dedicated to the art of blue printing since 1982, which was practiced here by a master craftsman until 1968.
Printing techniques
The fabric is first buckled , dried and smoothed by mangling .
Reserve pressure
The reserve print creates a white pattern on a blue background. The Chassi, a box filled with cardboard, and the model are placed on the prepared fabric. Then an ink-repellent substance called cardboard, blueprint or reserve is applied to the model.
The cardboard must have dried before the fabrics can be dyed. To do this, the fabric is stretched on a drying stretch. Cardboard is made from gum arabic , white tobacco pipe earth , copper sulfate , copper acetate and other chemical substances , among other things ; the exact recipes are well guarded and some have been handed down for centuries. After dyeing, the cardboard is removed with dilute sulfuric acid.
So it is a dyeing process, not a printing process . The term “print” refers to the alternative designation “negative pressure”, since in printing techniques that imitate the reserve pressure, ink is applied by rollers, whereas the areas are left out in blue printing. The term “reserve” refers to the fact that the chosen pattern reserves itself in the coloring, i. H. is left out.
Replacement techniques
Direct printing
With direct printing, the color is printed on the previously washed white fabric with the printing block, the pattern of which is provided by the respective model. The color is transferred directly to the fabric surface and appears as brown. After drying, the fabric is placed in a developing bath, in which the brown printing ink is transformed into a brilliant blue through a chemical reaction. The fabric is then boiled, ironed and then ready for use. Printing must be carried out very carefully, as any errors cannot be corrected. This manual process is a further development of the original reserve printing and is used when a blue pattern is to be created on a white background.
Discharge pressure
As an imitating process, a blue-colored material can also be printed with an acidic substance (etching stain), which also leads to a white pattern on a blue background.
Model
The patterns on the fabric are created using stencils called models. Even today, printing is still done by hand using models made by a specialized craftsman, the mold engraver or wood cutter . Originally they were made of boxwood , from which the pattern was cut with chisels and chisels. Since the 19th century, models have also been used in which the pattern consists of fine brass pins and plates that are hammered into pear wood. The wires can be worked with a drawing iron so that they have a square or star-shaped cross-section, for example, which then appears as a pattern on the printed material. A combination of both techniques is also possible. Finally, the surface of the model is smoothly sanded to enable a perfect print result.
To ensure that the model does not warp and that there are no irregular patterns, the wood must be dry, evenly veined, free from knots and well deposited. Large-scale models are glued together from three layers, whereby pear wood is often combined with the lighter linden wood. The models have handles on the edges or on the back and a repeat pen on each corner , which leaves a mark on the fabric that enables seamless printing.
To dye
The fabric is hung in layers on iron frames called crown or star hoops and dipped into the dye vat, the vat , which is more than 2 meters deep . The more often it is dipped, the darker and stronger the color becomes. Indigo is yellow-green during the dyeing process and only takes on a blue hue when it is oxidized in air. After dyeing, the fabric is rinsed, boiled, dried and smoothed, earlier with a glass ball, today with a calender , i.e. with heated rollers.
The mixing process of the colors and the developing bath, like the entire blueprint, are manual work. The recipes are trade secrets that are passed on from one generation to the next.
use
Linen, Halbleinen- or Cretonne -Substances, was incorporated into the weaving no color pattern can be provided using blue print with surface-filling patterns.
Colors and patterns vary depending on the region, age, purpose and tradition. Ornamental patterns are among the oldest known patterns. Flower patterns and borders were also widely used. Motifs of Christianity and hunting are among the figurative patterns.
Blue print is not only used for tablecloths, pillow cases, curtains, wall hangings and other individual decorative purposes, but also for clothing fashion, so it is an important element in the Sorbian costume. Here it is used for jackets, skirts and aprons. Aprons , which are printed with different patterns on the front and back , are particularly artistic .
Recognition as intangible cultural heritage
In March 2010, the Austrian Commission for UNESCO included it in the national register of intangible cultural heritage in Austria as the Burgenland indigo hand-blue print . In December 2016, the German Commission for UNESCO included the blueprint in the nationwide register of intangible cultural heritage at the request of blueprinters from Lower Saxony from Einbeck, Jever and Scheeßel . On November 28, 2018, the blueprint was included on the Representative List of the Intangible Cultural Heritage of Humanity at the meeting of the intergovernmental UNESCO Committee in Mauritius as a joint cultural asset of Germany, Austria, Slovakia , the Czech Republic and Hungary .
literature
- Rose Müllers: blue with white flowers . History and technology of blueprint. Coppenrath, Münster 1977, ISBN 3-920192-27-3 .
- Friedrich Schill: The blueprint. Its historical, technical and pictorial aspects. In: Stader Jahrbuch 1980, pp. 105–127.
- Eberhard Prinz: Dye plants. Instructions for coloring. Use in culture and medicine . 2nd revised edition. Schweizerbart, Stuttgart 2014, ISBN 978-3-510-65291-4 .
- Georg Stark: Blueprint - an old craft. Self-published, Jever 2004.
- Brigitte Urbitsch, Uwe Hämsch (photos): The blueprint book . Book publishing for women, Leipzig 2006, ISBN 978-3-89798-155-3 .
- Angelika Überrück: The Christian motifs of the blueprint. Mirror of popular piety from the end of the 17th century until today . Dissertation. Theologie Interaktiv 4, LIT Verlag Dr. W. Hopf, Berlin 2008, ISBN 978-3-8258-1502-8 ( detailed description of the content of the dissertation ; Malte Plath, Julia Helmke: review ).
- Friedemann Fegert: Oh how beautiful is indigo. Dyeing and blueprinting trade through the ages . edition Lichtland, Freyung 2016, ISBN 978-3-942509-53-4 .
- Stefanie Kellner: The blue wonder of Jever , in: Monumente -Magazin October 2018, pp. 40–44
Web links
- Literature by and about blueprint in the catalog of the German National Library
- fromholzer.de Bavaria's last blueprint printer (in Ruhmannsfelden , Bavarian Forest ).
- The art of blue printing The last blue printer in Burgenland ( Steinberg-Dörfl ).
- Central Europe, Burgenland - production of blueprints. in the online archive of the Austrian Media Library (1985, ÖWF film; 34 min.)
- Blue and white fairy-tale from #brnoregion The last two blue printing workshops in the Czech Republic work in the Brno area ( South Moravian region ) (in Olešnice na Moravě and Strážnice ).
Individual evidence
- ↑ Johannes Hugo Koch: With model, Krapp and Indigo. From old hand prints on calico and canvas . Christians Verlag, Hamburg 1984, ISBN 3-7672-0840-7 , p. 81.
- ↑ Johannes Hugo Koch: With model, Krapp and Indigo. From old hand prints on calico and canvas. Christians Verlag, Hamburg 1984, ISBN 3-7672-0840-7 , pp. 65-80.
- ^ Herrmann Schrader: New Handbook of the Zeuchfärberei and Zeuchdruckerei . CF Amelang, Leipzig 1862 ( digitized in the German Digital Library ).
- ↑ Burgenland indigo hand blue print ( memento from March 23, 2014 in the Internet Archive ) at the Austrian UNESCO Commission (ÖUK) in March 2010, accessed on March 23, 2014.
- ↑ Blueprint for the Unesco World Heritage Site ennobled by ndr.de on June 4, 2019
- ↑ 34 Forms of culture newly included in the German register of intangible cultural heritage: Blueprint at the German UNESCO Commission (DUK) of December 9, 2016.
- ↑ Blueprint is intangible cultural heritage in orf.at of November 28, 2018.
- ↑ Entry on the UNESCO website , accessed on November 30, 2018. (English)