Digital printing
Digital printing (or "digiDruck" in international parlance as Direct Digital Printing (DDP) or computer-to-print ) is a group of printing process in which the printed image directly from a file or a data stream from a computer to a printing press is transmitted without using a static printing form . The most widely used methods are electrophotography , e.g. B. laser printing , and inkjet printing . Digital printing supplements the classic printing processes such as offset printing , gravure printing , flexographic printing or screen printing in all their areas of application where the desired low run size down to the unique item (edition 1) could no longer be printed economically, and with its dynamic print image generation it opens up the possibility of different Types of customizing , e.g. B. Personalization and individualization at a favorable price-performance ratio . Since the early 2000s, the electrophotography and inkjet printing processes have achieved printing speeds that can be used for illustrated non-stop production printing with offset-like print quality.
Similarities of the digital printing process
Cross-process technical features
In contrast to traditional printing processes, digital printing processes do not require a static, ie unchangeable, printing form. Instead, pixel addressing within the print format is generated dynamically for each individual printing process , so that each print copy can have a different print image if required. In this way, for example, the pages of books and brochures can be printed already in numerical order, collect, without for a folded sheet for typical multi-page scheme impose the need. Since there is no printing form in the true sense of the word and therefore the print image - at least in the case of processes that print directly onto the substrate - is transferred with little mechanical pressure or even without contact (inkjet printing), digital printing processes are also referred to as NIP ( Non Impact Printing ). summarized. In indirect printing processes, which, like offset printing, use an intermediate carrier ( rubber blanket cylinder or rubber treadmill ) that transfers the color to the printing material, a more or less high compressive tension is necessary depending on the color consistency . The dot matrix printers, which are still indispensable for certain applications, also exert a mechanical pressure on an ink ribbon from behind, based on the typewriter principle.
Cross-procedural areas of application
In general, the various digital printing processes can be assigned to three major areas of application in which they complement or replace conventional printing processes:
Graphic digital printing
This area includes all applications in which page documents and other typographically designed files with bitmap images , vector graphics and text are printed:
- Office and corporate desktop and network printing
- Transaction printing and transpromo in in-house printers of government agencies, financial institutions and companies
- Newspaper, specialist and consumer magazine printing in commercial printing service companies and publishing houses
- Outdoor and indoor advertising printing (posters, signs, panels, exhibition stands) - as a supplement to the conventional offset and screen printing processes in commercial printing service companies
- Photo-realistic image reproductions (photo books and calendars, posters and art reproductions) - as a supplement to conventional offset printing in commercial printing service companies
- “Digital packaging printing ”, especially folding boxes and foil bags as well as labels - as a supplement to the conventional mass printing processes of offset, flexographic and gravure printing in specialized packaging printing houses
Functional digital printing
In this area, the digital print image does not serve the visual communication of the content, but it fulfills purely technical tasks.
- printed organic electronics, e.g. B. OLED , conductive antennas for transponders and MICR imprints - as an alternative to screen printing
- Functional coatings - as an alternative to various finishing technologies - with varnish-like colorless toners or inks that e.g. B. protect the print image or increase or decrease the lubricity of the printed product or allow the undamaged wettability of the printed image with water or sweat.
Industrial digital printing
Like some conventional printing processes, digital printing can also be integrated into the industrial production of goods and components of all kinds.
- Printing of shaped objects and hollow bodies using inkjet printing - as an alternative to screen and pad printing
- Decorative printing (wallpaper, veneer) in inkjet printing - as a supplement to gravure and flexographic printing
- Textile printing (printing on both lengths of fabric and individual items of clothing) using inkjet and thermal sublimation printing - as an alternative to screen and flexographic printing
- Printing form production for other printing processes: Inkjet printing with the ink-bearing copy layer sections on offset printing plates (computer-to-plate positive imaging) and with the covering stencil sections on screen mesh (computer-to-screen)
For more manual tasks, e.g. B. in the areas of vehicle decoration and interior design, object surfaces are printed directly, including using the digital airbrush and frescography processes .
Differentiating features of digital printing processes and the resulting areas of application
The specification of the various digital printing processes is based on technical criteria that result in typical areas of application. For a meaningful systematic differentiation, the categorization according to the process components is useful, because in practice the customer selects the printing process and the service provider invests in certain process groups.
Process component medium: substrates and object surfaces
Preparation of the media
- Delivery as roll goods for digital roll printing:
- for reel-to-reel printing, ie the printed web is rewound , with the rewinding (winder) acting as a buffer in terms of work organization
- For reel-to-sheet printing, ie the printed web is cut into individual copies in order to store them on a stack of sheets
- for printing web roll to copy roll (wound copies in large format large format printing)
- for printing and inline processing roll-to-end product (reel-to-product)
- Delivery as sheet goods for digital sheet printing:
- for printing pile-to-pile (pile-to-pile)
- for printing and inline further processing sheet-to-product
- Delivery as a zigzag-folded material web with separable tractor edge perforation for digital printing. Endless pile-to-endless pile (continuous stationary) ; mainly for sets of forms with self-copying function and adhesive labels
Flexibility and surface shape

- digital printing of flexible materials:
- Paper, foils and textile webs
- Envelopes and packaging materials (including corrugated cardboard )
- digital direct printing of rigid objects:
- flat surfaces (with print textures , material appearances such as stone, leather, wood and textiles can be simulated)
- Plastic cards and data carriers (CDs, DVDs)
- Window and showcase glass, signs and panels made of plastic, metal and wood
- Ceramics (tiles, tiles)
- Goods displays, transport and shipping packaging (mostly made of corrugated cardboard)
- tightly stretched textiles (T-shirts, dresses)
- curved surfaces
- Body pressure
- Containers, closures, glasses, cups and other hollow bodies
- All kinds of consumer and promotional items
- Sporting articles (balls, rackets, helmets) and toys
- rotatably fixed items of clothing (peaked caps, shoes)
- Component printing
- Dashboards , clock faces
- Control elements labeled with pictograms and text, e.g. B. Computer keyboards
- Body pressure
- flat surfaces (with print textures , material appearances such as stone, leather, wood and textiles can be simulated)
- digital direct printing of walls using portable printing frames in which a print head moves back and forth with line-by-line feed
Sheet format, roll or machine width
- digital sheet-fed printing in A4, A3, A3 + and B3 formats:
- in desktop, office and network printing
- in brochure printing (often with inline processing using a sorter, stapling or binding device)
- digital sheet-fed printing in formats B2 and B1 (corresponds approximately to printing machine format 3b):
- for high quality products
- Photo books and photo calendars, illustrated books and magazines
- color proof proofs
- Advance copies, samples and unique models ( mock-ups )
- Hybrid and complementary prints in poster, publication and packaging printing
- for layout-binding proofs
- for high quality products
- digital narrow web printing:
- for transaction and form printing
- for flexible packaging and labels ( pressure sensitive , wet adhesive and in-mold labels)
- digital normal web printing:
- for magazine and newspaper printing
- for book printing with slotted strands (envelopes are often printed separately)
- Large format printing ( Large / Wide-format printing , large format, WFP) up to 5 m Roll width:
- for posters, art prints and placards, also on linen (canvas)
- for flags, textile and PVC banners, net-like fabrics (mesh) , scaffolding covers and balloon covers
- for large and endless pattern repeats (veneers, wallpapers)
- for Translights - backgrounds used in film and TV studios, which mostly represent city and street scenes viewed through windows and simulate the time of day or season with lighting and lighting effects
- Digital direct printing on objects depending on their size (see digital direct printing on rigid objects), usually using the inkjet printing process
Printability
Not all substrates can be easily printed in all digital printing processes. The printability of the medium depends on the one hand on its surface properties and on the other hand on the printing process and the printing ink that can be used. Basically, it is important that the printing ink adheres well to the surface, i.e. is neither repelled nor completely absorbed, and the paper hardly releases any dust particles that contaminate the photoconductor drums and inkjet nozzles.
This is why the printing system providers often certify or recommend specific paper products. This is especially the case with inkjet printing media when the paper manufacturer carries out the necessary conditioning of the paper surface by applying a so-called primer , i.e. an adhesive primer . In order to be independent of the correspondingly more expensive media and also to significantly expand the range of substrates, some printing systems have integrated the primer application into the printing process. The Fujifilm Jet Press applies the primer over the entire surface in front of the first printing unit, and the HP Web Press has an additional printing unit that pre-prints a bonding agent on the paper with raster dot accuracy; Meanwhile, however, HP also offers full-surface application with a priming agent .
The printability is possible
- for low-dust uncoated papers ("natural papers")
- no problem with toner
- with inks often only after surface conditioning
- for matt and glossy coated papers and cardboard with low absorbency
- limited with toner, mostly there are specially made papers
- with inks often only after surface conditioning
- no problem with UV-curing inks
- for plastic, metal, glass, stone and wood surfaces: no problem with UV-curing inks
- for textiles, canvas and synthetic fiber fabrics: no problem with UV-curing inks and thermal sublimation inks
There is only one process that can print on all surfaces equally well: nanography. This is due to the small size of the pigments, which are transferred indirectly to the printing substrate as an already dried ink film and adhere to any micro-rough surface topography.
Process component printing ink
toner
Toners are electrostatically chargeable or magnetizable colorants and usually require a thermal fixation of the printed image. The special use of the toner allows the differentiation between the “toner printing processes”.
- digital printing processes with powdered toner:
- Electrophotography with two-component toner ( laser printing , LED printing , monochrome MICR -prints of magnetizable alphanumeric characters in check forms)
- Magnetography with one-component toner (only suitable for monochrome printing)
- Ionography with two-component toner
- Electrophotography with liquid three-component toner (pasty two-component toner plus transfer liquid), e.g. B. so-called electro-ink for hp indigo printing machines
- Elcography with liquid electrolytic printing ink (based on the principle of toner coagulation )
Milestones: Electrophotography was developed by Chester F. Carlson in 1938 and a patent pending in 1942. It was launched in 1950 by Haloid Corp. (Xerox from 1961) initially introduced as a copying process, from 1973 Canon also sold color copiers. In 1976 one can speak of the first digital printer, the IBM 3800 laser printer. In 1993, the versatile Israeli inventor Benny Landa implemented four-color digital printing for the first time with offset-like indirect print image transfer (Indigo e-Print); By investing in this machine, numerous printing companies had to accept high debts and losses, as the business models and advantages of digital printing known today were not yet popular.
ink
Inks for digital printing are low-viscosity or gel (Canon patent) printing inks based on wax, water or solvents that may contain oils, prepolymers and latex dispersions . The “ink printing processes” are differentiated depending on the preparation of the ink jets, drops or films.
- Continuous ink-jet (CIJ) : deflection of a continuously emitted, electrostatically charged ink jet in a point-addressable electrical field
- Discontinuous inkjet printing (drop-on-demand ink-jet, DOD) : Shooting of individual drops of ink, even of different volumes, through point-addressable nozzle print heads
- with thermal drop formation
- by liquefying a solid wax stick ( solid ink printer , implemented exclusively as Tektronix / Xerox - Phaser technology)
- (first implemented as a vapor lock Canon - Bubble Jet technology)
- with electromechanical droplet formation (pulsating chambers)
- by piezoelectric actuators (realized for the first time as a market-ready Epson - Micro Piezo technology)
- through so-called ink ejectors ( piezo inkjet print heads modified by Landa for nanography )
- with thermal drop formation
- Spray valve printing: digital airbrush
- Pen pressure: description of the travel path of the medium ( plotter )
- Electrography (here the ink is also called "liquid toner" because its electrostatic affinity is used):
- Coloring the charged dielectric paper coating (direct printing)
- Inking the charged dielectric transfer drum layer (indirect printing)
- electrostatic ink drop deposition (electrostatic drop-on-demand deposition) : dissolving out electrostatically chargeable pigment particles together with a non-rechargeable liquid film from the exposed surface of an ink liquid that is held in a nozzleless print head, and addition of these drops on oppositely charged metal surfaces; For this process, which was patented back in 1993, market-ready solutions for industrial and packaging printing, in particular the printing of metallic beverage cans, have only been offered since 2017; the sole patent holder is Tonejet Ltd in Melbourn , Hertfordshire, UK
Milestones: In 1948 Siemens Elema used an ink jet to record the curve of a galvanic measuring device, which William Thomson Lord Kelvin had already attempted with individual drops in 1858 . In 1976, IBM introduced the first inkjet printer that used the principle of the deflectable jet (continuous inkjet). In 1977, Siemens began the history of drop-on-demand printing (DoD) using piezo-electronic drop formation, which was later perfected by Seiko Epson. In 1979, HP and Canon launched their thermal droplet formation at the same time, which led to major patent litigation. In 2012, Landa attracted a great deal of attention for its nanographic printing , which is still in the pioneering user phase, because, apart from development partner Komori, the licensees did not perfect the machine technology, as they had hoped for at drupa 2012, so that Landa, as a technology developer, is now forced to do so also to develop and build the printing machines.
Inkjet printing systems used in image printing have partially redundant nozzle arrays in order to avoid streaking in the area of adjoining print heads (weaving) and to compensate for clogged nozzles.
In the various printing processes, the inks themselves are selected according to their intended use, according to which the selection of the digital printing systems in question depends.
-
Lightfast inks, i.e. inks with pigment colorants resistant to UV rays, are used for indoor and outdoor use:
- Normal and effect pigments
- Nanopigments (nanography)
- conductive pigments for organic electronics (OLED structures), magnetic pigments (MICR)
- Soluble colorants for indoor use:
- water-soluble dyes, including food colors for printing on confectionery and chocolatier products
- Dyes dissolved in a solvent
The equipment of the digital printing system must also comply with the drying principle of the inks:
- Behavior of the carrier liquid:
- Solvent evaporates
- Water evaporates and penetrates into the medium if possible
- Water evaporates from the latex-in-water dispersion (only in large-format latex printers)
- Behavior of the binder:
- Monomers and prepolymers harden by means of UV radiation ("UV digital printing")
- Polymerization using UV lamps (cause the formation of ozone, which requires a suction device on the printing machine)
- Polymerization using LED UV arrays (ozone-free curing, lower energy consumption, less heat input)
- Phase change from molten liquid to solidly re-cooled “solid ink” wax
- Monomers and prepolymers harden by means of UV radiation ("UV digital printing")
Wax and resin paint
Colorants can also be transferred together with the wax or resin binder in which they are embedded. With the corresponding digital printing processes, a carrier material (color foil, color ribbon) is used, which is subject to a step-by-step advance with each printing process in order to always guarantee a maximum range of colors.
- Dot matrix printing: single-color mechanical printing of a coarse-resolution dot matrix matrix from behind on an ink ribbon ( typewriter principle ); As with some memory typewriters, the alphanumeric characters are not printed character by character with the forward and backward printhead, but in matrix lines, whereby 12 or 24 matrix lines can be combined into one writing line in one or two printhead runs, depending on the printhead size or print mode (resolution)
- for impressions in sets of forms with self-copying function and in simple forms (e.g. doctor's prescriptions)
- for ticket machines (at train stations and at stops)
- for printing sequential numbers on preprinted documents
- for printing accompanying notes for logistical tasks
- Thermal transfer printing: selective liquefaction of the color on the ribbon, e.g. B. for monochrome printing of self-adhesive identification labels
- Thermal sublimation printing: micropoint evaporation of the wax color on the carrier film, the temperature determining the amount of dye
- Use in high quality photo printers
- Printing of textile objects
- Printing of higher quality ID and customer cards
Color coupler reaction
In digital printing with a color coupler reaction, the coloring substances (couplers) are in a colorless state in the paper coating. When exposed to energy, these substances react with a color change.
- Thermal printing: a point heating of the heat-sensitive paper layer triggers blackening; Developed at the time for fax machines, thermal paper is now only used for sales slips and receipts
- Lume Jet: a laser print head exposes direct positive photo paper with red, green and blue laser beams and produces high-resolution prints in photo-realistic reproduction quality; Despite some advantages compared to inkjet printing and the considerable printing speed of 1.3 m / s (305 mm × 1000 mm from the roll), the application of the technology is too specifically limited to photo book and small poster printing, so that the manufacturer will go into liquidation in 2018 had to and now appears as a picture printing service provider with the existing equipment under the name L-Type
Process component printing unit (s)
Transfer of print images onto the substrate
Another distinguishing criterion of the digital printing process results from the principle of the print image transfer.
- direct transmission:
- contactless from a printhead matrix
- in contact with a load profile drum or similar transfer drum
- indirect transmission:
- all colors individually via a blanket cylinder (offset printing principle, e.g. with hp Indigo and Miyakoshi)
- all colors are collected via a register transfer belt (circumferential rubber band, e.g. in the electrophotographic systems from Konica Minolta, Ricoh / Heidelberg and Xerox iGen as well as in inkjet printing in the Landa nanography machines)
Side printing
An essential criterion is whether and according to which technical solution the back can also be printed. A distinction is made between simplex and duplex machines and simplex and duplex modes, both for roll and sheet-fed printing systems. The terms “simplex” and “duplex” were originally introduced for copiers and office printers and today in digital printing they stand for the terms “straight printing” and “perfecting” that are common in conventional printing processes.
- simplex: one-sided printing (face printing)
- for printing systems that only print on one side
- for duplex printing systems that can also print in simplex mode
- duplex: double-sided printing (front and back printing) one after the other
- in the same printing unit by means of a turning or refeeding device (sheet printing)
- in a subsequent printing unit (roll printing)
Multi-colored printing
Digital printing systems that work not only in one color (monochrome) but in multiple colors (black + spot color, four-color CMYK or CMYK + spot colors) have process-related differences in the number of media runs.
- Single pass: transmission of all colors in one pass
- the colors are transferred together with a single cylinder revolution (central cylinder construction) or a single register transfer ribbon circulation of the printing unit
- the colors are transmitted individually in several printing units connected in series
- Multi [ple] pass: the colors are transferred individually in one pass through the single printing unit (in sheet-fed printing systems, e.g. in CMYK printing, the sheet passes the printing unit four times before it is ejected)
Some digital printing systems, especially from the lower price segment of their respective technology, have the weakness that the accuracy of the individual colors in multi-color printing and the register accuracy of front and back printing in duplex printing are poor. In these cases, the design-related cause is that the conception of the sheet guiding elements originates from copier technology and does not meet the high and experienced requirements of the precision machine construction of conventional printing machines. In inkjet printing, this effect can be intensified under certain circumstances, because with contactless printing the ink is applied from a certain height, especially with traversing print heads.
The higher-priced solutions, both the toner and ink printing processes, prove that digital printing can also be done with high precision. This is particularly successful when the web or sheet guiding elements come from conventional printing press construction and are combined with low-vibration, because massive printing units.
Process component software for work preparation and data preparation
Usage regime: functionality vs. workload
Digital printing systems differ greatly in terms of their workload and the corresponding functionality. Wherever there is permanent printing, the printing speed is an essential selection criterion.
- sporadic use, but rich in functions - typical for “office printing”: standby times between print jobs; As a result, when purchasing the machine, you will place more value on multifunctionality (network capability, copying and faxing, scanning and saving in PDF files and sending as e-mails) rather than printing speed
- permanent utilization - typical for “production printing”: processing of print job queues as seamlessly as possible; The decisive factor is therefore the printing speed, which for sheet-fed printing systems is usually given in A4 pages per minute and for web printing systems in running meters per minute and then according to the color assignment (single, multi-colored), selectable print resolution (dots per inch, dpi - dots per inch) simplex / duplex and maximum sheet format or maximum web width is specified; In terms of performance, the digital sheet-fed production printing systems generally begin with four colors (CMYK), A3 + format and 60 A4 color pages / min
Workflow concept
Three business models typical for digital printing are based on the following organizational and economic concepts of print data organization:
- Demand- dependent printing, Print (ing) -on-Demand (PoD): printing of small numbers of copies (typically: 1 to 500 copies) with exact order quantities instead of printing on stock (avoidance of “dead capital” and storage costs); In addition to specialized service providers who acquire PoD orders via an Internet interface, PoD is often also offered in copy shops, where the customer brings his files on data carriers and waits for his small print runs to be "taken away"
- Location-dependent printing, distribute-and-print , first distribute, then print : Distribution of the print files to any output location worldwide, where a demand-oriented number of copies is printed, thereby avoiding the costly dispatch of a centrally printed edition; Daily newspapers offer z. B. would like to offer the business section as a digitally printed excerpt for flight passengers, but this concept has now been replaced by the download of e-papers, which can be read on the digital device even after leaving the internet connection
- Printing of variable data, variable data printing : this concept exploits the unique selling point of digital printing to be able to output each print copy with different content (see customizing )
Print resolution vs. productivity
When preparing the data stream on the control computer, the digital front end (DFE) , the relationship between print resolution and productivity is set. Due to the dependency on the processor speed for the recalculation of the print image, it must be accepted that the print speed can only be increased at the expense of the print resolution (lower quality level), or conversely, a high resolution is at the expense of productivity. It may be necessary to adjust the screening method.
The print resolution is usually specified in the longitudinal and transverse directions, e.g. B. 600 dpi × 600 dpi, especially since the numbers do not have to be identical due to the process. Although the print resolution is physically specified by the number of addressable pixels or ink jet nozzles, there is a technical possibility of apparently increasing the native resolution:
- through grayscale interpolation (apparent doubling of the resolution, e.g. from "600 dpi × 600 dpi native" to "1200 dpi × 1200 dpi interpolated")
- in inkjet printing also by varying the predefined drop volumes (given in picoliters) (up to 7 distributed over the tonal value range) or the dot size with a constant drop volume (variable dot) ; There is, within certain limits, the possibility of increasing the speed by increasing the firing frequency (up to 50 kHz) without any loss of quality
Customizing
The possibilities of partial editions or copies at low printing costs represent the outstanding unique selling point of all digital printing processes. The largest share in such applications is made up of customer or target group-related content adjustments. Even long print runs can be individually varied in terms of content at low cost - the prime example of highly valued mass customization . Product examples are effective advertising packaging with the individual first name, the book with a personal dedication page or the photo books , photo calendars and greeting cards that can be created in the Internet dialogue , which generate millions in business thanks to widespread digital photography and the ever-available smartphones.
- Transactional printing in this combination than - permanent printing of invoices, reminders, credit card statements, account and account statements, policies, invoices, receipts, etc. (letter-like) in a standardized layout, depending on the amount of information with different pagination, often supplemented with advertising printing: Transpromotional designated
- Versioned printing : printing with target group-specific content, e.g. B. in different languages or with different price labels
- Personalized print: Print product with a standard layout used over the entire run and inserted personalized text (address, salutation, code, lot number, etc.), e.g. B.
- in serial letter-like advertising mail (direct mailings) , i.e. advertising tailored to the recipient ( direct marketing ).
- on packaging (personalized advertising on the surface of shipping boxes) and labels (as part of promotions, especially first names)
- individualized printing: completely individually compiled image, graphic and text content, e.g. B. Individual guides
Automatic imposition
PDF print documents consisting of continuous pages must be delivered in numerical page order for digital print output. The solution implemented in the workflow or DFE software for document and data stream preparation usually adjusts the arrangement and order of the pages fully automatically according to the print format and the further processing task ( imposition ).
- Collated print: Printing of the final format pages of a document in numerical order, also in duplex mode, usually in combination with inline processing (stapling, binding)
- Printing in strands: Special form of collated printing on digital web printing machines, where the printed web is slit lengthways into strands, the strands are cut crosswise to form sheets and the sheets are gathered into book blocks and fixed with auxiliary glue on the front
- Imposition printing: printing of larger-format copies, ie with 4, 8 or 16 duplex pages in print format, taking into account subsequent processing in a folding and / or gathering machine
Combination with other printing methods or processes
Digital and conventional printing processes separated in time and space
The organizational and technical unique selling points of digital printing enable economically interesting and useful application scenarios, e.g. B. as a test method and as a supplement to high-quality mass printing methods.
- Sample and model production, mock-ups : One-off prints, especially of folding boxes and goods displays , the appearance of which is demonstrated in a printed and fully assembled state, whereby the (usually non-digital) target printing process is simulated
- Proof print: one-off prints that simulate the (usually not digital) target printing process
- in its expected color rendering (color-binding proof, digital proof), if necessary in combination with the raster model of the target printing process
- in the form of the imposed printed sheet with front and / or back printing
- Hybrid production: digital realization of print jobs in the lower run range (typically: 1 to 500 copies), if the usual economic run size of the original mass printing process is not required; The decisive factor is the maximum achievable reproduction quality of the mass printing process to be simulated (e.g. offset printing)
- Complementary production: digitally printed addition and improvement, e.g. B.
- completely personalized printed envelopes for conventionally printed magazine content, e.g. B. “This copy belongs to our loyal reader [first name name]” for anniversary editions
- digital printing of page elements in free areas in conventionally preprinted copies, e.g. B. personalized information under the letterhead or in printed advertising material
- Offline further processing: temporally buffered and spatially separate further processing of the digital print copies
- on the existing systems for conventional print production (intermediate storage and transport on pallets to the first postpress)
- on special finishing equipment
- for typical digital print products, e.g. B. for lamination with cling film or for lamination on frameless picture material
- for digital signage printing , e.g. B. the anodized sealing of the printed inks under a transparent, protective anodized layer , which is firmly embedded in the aluminum shield , making the prints more resistant to mechanical, thermal and chemical influences
- Nearline postpress: modularly organized offline postpress in the immediate vicinity of the digital printing machines
Process-integrated digital printing
Process-integrated digital printing ranges from marking and imprinting to fully automated inline production of complete printed products. Simple marking and coding tasks are carried out with low-resolution matrix print heads using the dot matrix or inkjet printing process or, alternatively, laser ablation . Demanding impressions with image and text content must be made using high-resolution processes such as inkjet printing or electrophotography.
- digital printing of page elements in areas kept free during printing in the conventional printing machine, e.g. B. Articles or advertisements with regional or target group-related content in newspapers
- digital identification:
- Batch number and best-before date on packaging, closures and labels
- Consecutive numbers on tickets, lot numbers (often digitally overprinted with scratch-off varnish) on winning tickets and in printed advertising
- Codes on printed sheets for the purpose of traceability or organization of the final production
- Inline post-processing: seamless post-processing of the digital print copies, e.g. B. to brochures or to folded and enveloped mailings on systems specially designed for digital print production
Differentiation of digital printing from other processes or scenarios
"Computer-to- ..."
According to the definition given above, all technologies in which printing forms are imaged in the printing machine are not counted as digital printing. Instead of “computer-to-print”, one speaks in these cases of “computer-to-press” or “integrated computer-to-plate”. As a result, the risography cannot be classified, at least technically, in digital printing, because a screen-like paper or foil template, i.e. a static print-through form, is generated digitally controlled. However, due to its low material value, the stencil can justify the typical digital print run of 10 copies or more.
Copiers and multifunctional systems
The transition between a high-performance photocopier and a digital printing system is fluid. Copiers often still have options for saving and sending (fax, e-mail) the print template and are therefore also referred to as multifunction devices. Mainly the higher printing speed and the limitation to the scan and print function distinguish digital printing systems from copiers. Depending on the application, digital printing systems also have a higher resolution. In the case of color printing systems, there is also the stabilization of the desired color reproduction quality, which is why digital printing systems have a color management system. Regardless of this, many copy shops operate digital printing on one and the same multifunctional device, which usually works in four-color laser printing, as a supplement to their offer.
3D printing
The term 3D printing itself is misleading, as it is not about coating surfaces with color, which is what printing is all about, but - to put it more precisely - about additive manufacturing , i.e. the layered construction of three-dimensional objects. This changes the fact that some additive manufacturing processes use the digital printing technology of inkjet printing, e.g. B. Binder Jetting (3DP) and Multi Jet Modeling (MJM), nothing.
Growth forecast for digital printing
Overestimated in the initial visionary euphoria, comprehensible growth forecasts are now emerging for the market shares of digital printing. The “Global Trends Report” published by the printing trade fair drupa 2016 found in a company survey that “digital technologies are growing the fastest (an average of 28% annually)”. (...) "Functional printing is a growth sector for screen printing (+ 11%), whereby digital technologies are also very important here." (...) "Although the majority of sales are still generated by conventional printing processes, digital printing is and steadily increasing in value. An exception is packaging printing , where only 13% of respondents reported that it accounted for over 2% of sales (compared to 35% for commercial printing , 24% for publishing and 59% for functional printing ). Digital printing can particularly show its advantages when it comes to printing variable content: 59% of functional printing companies and 35% of commercial printers report that over 25% of their digital sales are attributable to variable content. "
Publishing alternatives
Digital printing enables the inexpensive production of small and very small editions of all kinds. This also opens up alternatives to the classic publishing business, which, taken literally, means spending a sum of money on behalf of an author for the production of books. Since a book is not produced in its circulation size on suspicion, but is ordered from the book trade or via internet platforms and can therefore be reordered and reproduced at any time as required, the slightly higher copy costs are offset by the minimization of the publishing risk of capital commitment , sitting on a larger printed edition to stay and to have to pay fees for storage and delivery . Last but not least, there is also the opportunity for repeat orders to printing errors adjusted or print versions or otherwise revised as necessary a corrigendum to incorporate.
Under these conditions, it has become common for books by (as yet) unknown authors to be produced in initially small numbers. This sometimes happens at your own risk by self-publishing or through small specialized publishers - at marketable prices and in commercial quality. So z. B. a 200-page paperback (with a 4-color soft cover) can be produced as a single copy for around 20 euros; With a print run of 20 copies, the unit price can drop below 2.50 euros, but on the other hand, even with a print run of over a hundred, it can hardly fall below the 2 euros limit (as of April 2017).
Market studies by Interquest that analyze the book and magazine market in the specialist press can be viewed in an extensive collection of articles.
Guidelines, standards and quality certificates
Guidelines
System test digital printing
In December 2018, the Federal Association of Printing and Media and the Fogra Research Institute for Media Technologies published the jointly developed guideline "Technical testing of sheet-fed printing systems with electrophotographic print image transfer". This set of rules enables an objective evaluation of the performance of toner printing systems based on standardized quality criteria and test procedures. Both providers and users can use it to determine, agree and check important quality properties of the printing systems, which is particularly important when making investment decisions and concluding contracts.
The focus of the 15 test criteria is on image and color reproduction as well as register and register tests and apply to electrophotographic sheet-fed printing systems up to SRA3 format (320 mm × 450 mm). Since the offered digital printing systems differ greatly in terms of price and performance, the guideline contains a value scale for each test criterion instead of specific limit values that shows the quality spectrum of commercially available printing systems. For better orientation, the typical quality values for offset printing are also marked there. In this way, the contractual partners can compare the system properties with the respective requirements.
The guideline is supplemented by the required test print files in sheet format SRA3. Since the prints generated in this way can sometimes only be reliably evaluated with special measuring systems or software solutions, external support may be required for the system check.
Worksheets of the professional association ETEM
In digital printing, precautionary measures and action aids on occupational safety, health and environmental protection are the focus of the employers' liability insurance association for energy, textiles, electronics, media products ( BG ETEM ):
- "Risk assessment - practical help for digital printing (04/18)" with checklists
- Industry information "Toner-based digital printing systems" (release of ozone, VOCs, chemicals and dust; extraction and protective clothing)
- “Toner dusts”: practical guides and specialist publications
- "InkJet digital printing": safety technology, working materials and health protection (release of ozone and VOCs, hazard assessment of solvents; workplace design, suction and protective clothing)
- Brochure "Safe working in inkjet digital printing": The brochure provides information on hazards and protective measures when handling large-format digital printing machines (essential aspects of safety technology, e.g. with regard to moving machine parts, chemical hazards from paints, inks and solvents, as well as workplace design e.g. cutting, storing and transporting, and organizational aspects).
Standards
Because digital printing represents a heterogeneous group of processes, there are only a few cross-process standards. Mostly, criteria worthy of standardization are reflected in various standards that largely follow the systematics of the process components. The English original titles of the standards and their German translation by Beuth Verlag may have different terminology. ISO documents marked with TS only have the informative status of a technical specification.
Cross-procedural
- ISO 12647 : Graphic technology - Process control for the production of half-tone color separations, proofs and production prints - Part 7: Proofing processes working directly from digital data; Part 8: Validation print processes working directly from digital data
- ISO 15311: Graphic technology - Requirements for printed matter for commercial and industrial production - Part 1 / TS: Measurement methods and reporting schema (parameters and measurement methods); Part 2 / TS: Commercial printing (printing for commercial production); Part 3 / FograSpec: Large format digital printing
- ISO / IEC 24712, ISO / IEC 19798 and ISO / IEC 2471: Test images for color printers
- Media Standard Print 2018: System of typical applications for digital printing processes and the associated working color spaces, ISO paper categories, technical criteria and exchange data formats
Media and inks
- ISO 2836 (DIN ISO 2836): Graphic technology - Prints and printing inks - Assessment of resistance of prints to various agents (determination of the resistance to various agents): chemical resistance of prints and printing inks including toners and inks
- ISO 21139-21 / TS (draft): Permanence and durability performance in commercial applications - Part 21: Display window - Light and ozone stability: Light and ozone stability of digital prints and photo prints in shop windows and backlit billboards
- ISO 18055-1: Photography and imaging - Inkjet media: Classification, nomenclature and dimensions - Part 1: Photo-grade media (paper and film)
- DIN 53131: Testing of paper - inkjet media Part 1: Cockle test, Part 2: drying time, inkjet test form; Part 3: Print image quality - optical resolution, optical density, color values, print image disturbances
VDP, customizing
Page description languages (selection) that can be used for printing variable data (VDP) and their adaptation in ISO standards and guidelines:
- APS, IPDS: IBM Advanced Function Presentation with variable processing of the data stream Intelligent Printer Data Stream is supported by all manufacturers
- FreeForm: applicable without specific software for VDP document design is, in all EFI Fiery RIPs supported
- PCL: Hewlett-Packard Printer Command Language , is supported by all manufacturers
- PDF : Adobe PDF can beconvertedto software- specific Optimized PDF in almost all VDP workflows
-
PDF / VT: Printing of personalized transaction documents, often combined with advertising (variable transactional and transpromotional work) on the basis of PDF document pages ; is supported as one of the target formats of Optimized PDF algorithms across all manufacturers
- ISO 16612: Graphic technology - Variable printing data exchange; Part 2: Using PDF / X -4 and PDF / X-5 (PDF / VT-1 and PDF / VT-2); Part 3 (draft): Using PDF / X-6 (PDF / VT-3)
- PDF / VT Application notes (application notes)
-
PostScript : Adobe PostScript files of different levels (1, 2, 3) are converted in VDP workflows from various solution providers to a software- specific Optimized PostScript that is not compatible with other solutions and is therefore converted to PDF / VT if necessary
- VIPP: PostScript, optimized by the Xerox Variable-data Intelligent PostScript Printware, is also supported on non-Xerox systems
-
PPML : Personalized Print Markup Language; PPML and the associated template format PPMLT are supported by all manufacturers
- Printing On Demand initiative (PODi) - The Digital Printing Initiative: PPML specification and tools
- PPML / VDX: The Committee for Graphic Arts Technologies Standards (CGATS) publishes its own, extended PPML specification: Personalized Print Markup Language / Variable Data Exchange (PPML / VDX)
- ISO 16612-1: Variable printing data exchange - Part 1: Using PPML 2.1 and PDF 1.4 (PPML / VDX-2005)
- JLYT, SNAP: J-Layout and, more rarely, Swift Native Accelerated Personalization are native document formats that are generated in the HP SmartStream Designer for the HP indigo Press series and use elements of PPML
- PDF / VCR: ISO 16613-1: Graphic technology - Variable content replacement - Part 1: Using PDF / X for variable content replacement (PDF / VCR-1); is supported across all manufacturers
- XMP : the Microsoft XML Paper Specification was developed as an alternative to Adobe PDF; Documents in XMP and the incompatible Open XMP from ECMA International are supported in Windows 10, but at best play a role in corporate network printing
Furthermore, graphic file formats such as DCS, EPS, GIF, JPEG and TIFF (instead of PostScript or PDF / X) can be printed directly and combined with variable text.
Energy consumption according to the usage regime
- ISO 20690: Graphic technology - Determination of the operating power consumption of digital printing devices (determination of the energy consumption of digital printing devices in the operating state); preferably to be used for permanent digital production printing with sheet-fed and web printing systems, but not for large format printing (LFP / WFP)
- ISO 21632: Graphic technology - Guidelines to determine the energy consumption of digital printing devices including transitional and related modes. preferably to be used on sporadically used printing systems with a higher stand-by component
Quality certificates
Quality certificates for digital printing document standardized data processing and the print and color reproduction quality that can be achieved in the respective digital printing process. They are the final result of commissioned consulting services, in the course of which the current state is recorded, analyzed and optimized until the digital print shop is finally able to independently achieve the required quality. The evaluations are made across processes and for different production scenarios of digital printing, whereby the very high quality of offset printing can also be used as a benchmark, namely when hybrid and complementary production is to be implemented. The optimization takes into account several relevant ISO standards beyond the actual digital printing norms, ie standards for data preparation and measurement technology.
- Quality Seal of Digital Printing (QSD): The audited company must prove that it has a high level of consulting and media competence, can work professionally and in a standardized manner, delivers reliable print quality at the highest level (over the entire print run and homogeneously in print format), and uniform color reproduction can guarantee for different products and printing processes and act safely when handling variable data.
- Process standard digital printing (PSD): is essentially based on ISO 15311 and also checks the implementation of associated ISO standards
Initial and continuing education
Due to the variety of processes and applications in digital printing, there is no uniform job description of the “digital printer”. Since the professional content of the printer and other activities in the printing industry have changed in general , not least to take account of the link with digital media and digital transformation in general, digital printing has been given special consideration in the revision of the official educational offers in recent years .
In practice, however, additional in-house qualifications are not uncommon. If a digital printing machine is purchased, the relevant employees (often offset printers, but also employees from departments that have been streamlined or completely unskilled workers) are simply trained and trained, for which the machine suppliers send instructors and offer learning courses on site.
The special features of a digital printing workflow are also brought closer to users in training courses by specialized technical advisors. In Germany and Austria these are some consultants in the printing and media associations and Fogra, and in Switzerland the consultants in the PDFX-ready initiative. In addition, freelance consultants are on the go.
Germany
The official routes to digital printing are summarized in the BVDM brochure Qualification made to measure in digital printing . A digital printing specialization can take place in the case of three vocational training offers with a final examination by the Central Media Committee, namely in the training professions
- "Media Technologist Printing",
- "Media technology screen printing",
- "Media designer digital and print".
The qualification profiles "digital printing" (focus on personalization / individualization) and "large format digital printing" (focus typical for screen printing companies) are available for this purpose. The trainees compile their profiles from mandatory and optional (following the specific operational requirements) modules: database application, virtual printing form, digital image processing, data preparation, data output processes, digital printing process, mailing production, product processing, hardware and software. In the meantime there are also further training offers with exams, namely
- the three-part seminar "Certified digital printing professional according to VDM" for employees in printing and media service companies; The digital printing professional is a joint initiative of the regional printing and media associations in Baden-Württemberg, North West and Bavaria
- the digital printing expert course for “certified media producer / f: mp.” for employees in advertising and production agencies
Switzerland
The joint vocational training center (PBS) - supported by the viscom - swiss print & communication association and also supported by the Association of the Swiss Printing Industry (VSD) - looks after and reviews various media job profiles. The Federal Certificate of Proficiency (EFZ) is issued as a conclusion . The apprenticeships with digital printing specialization are structured similarly to those in Germany and are called here
- "Media Technologist Print"
- "Media Technologist Screen Printing"
- "Media technologist print media technology"
In addition to the opportunity to take the digital printing expert course "Geprüfter Medienproduktioner / f: mp", which is offered from Germany, further training courses are partly privately organized and not regularly held:
- Further education media technologist in the field of digital printing, carried out by the consulting company Digital Print Innovations AG
- "Variable Data Operator" course of the VSD specialist group Vereinigung Druck Schweiz (VDS)
Austria
In Austria there is only one apprenticeship that specializes in digital printing, namely that of printer with a final apprenticeship examination :
- "Apprenticeship printing technician - focus on digital printing".
The Berufsförderungsinstitut (BFI) and the Wirtschaftsförderungsinstitut (WIFI) offer various courses and colleges for further training, which, however, build on the training specializations already taught.
Trade fairs and events
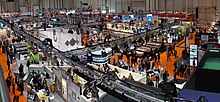
For many years, digital printing has had a growing role at trade fairs for the printing industry, where it is presented with live demonstrations. Selected examples:
- drupa : the world's leading trade fair for the printing and media industry that takes place every four years in Düsseldorf
- Print (spelling PRINT): annual in Chicago, USA, held by the Association for Print Technologies (APTech) trade fair for the printing and media industry with international exhibitors and focus on the American market
- International Graphic Arts Show (IGAS): A trade fair for the printing and media industry, usually held every four years in Tokyo , with international exhibitors and a focus on the Japanese and Southeast Asian markets
- FESPA: annual world and continental trade fairs for the screen printing industry with a high proportion of digital large format and textile printing
- Labelexpo Europe: annual trade fair for label printing and coding solutions in Brussels
- Viscom: European trade fair for visual communication, including digital sign, poster and banner printing, held annually in Düsseldorf parallel to PSI (leading trade fair for the promotional products industry)
- InPrint: organized by Mack Brooks Exhibitions Ltd, St Albans (UK), in turn in Germany, Italy and the USA, trade fair for industrial printing applications, including digital printing solutions
In the meantime, exclusive digital printing events have also established themselves:
- hunkeler innovationdays: in Lucerne every uneven year, the in- house exhibition of the Swiss machine and module manufacturer Hunkeler AG, which also sees itself as an integrator for networked digital printing solutions for numerous manufacturers of printing and finishing machines; International participation and response as well as innovative concepts mean that the event has the character of a leading trade fair for digital printing solutions
- Digital printing congress (ddk): solution and strategy-oriented event of the Federal Association of Printing and Media with best practice examples of innovative digital printing users and clients that has been taking place in Düsseldorf since 2015
- FESPA digital: Occasionally organized digital printing spin-off from FESPA
- Mailingtage: annual congress that has been resumed after a long break since 2018 with an expo on cross-media and dialogue marketing
In addition, some organizations have created international discussion platforms and information offers for digital printing:
- Digital Printing Working Group (dpwg): Digital printing working group supervised by Fogra
- Information Management Institute (IMI): developer conferences and seminars on inkjet printing held worldwide
See also
Individual evidence
- ↑ Glunz & Jensen: iCtP PlateWriter 3600 Pro. In: YouTube, January 13, 2017. Retrieved January 24, 2019 .
- ↑ Screen printing partner: Computer-To-Screen (CTS). In: Screen printing makes more of glass (event presentation). Retrieved January 24, 2019 .
- ↑ D. Hangs: Michelangelo Computer Airbrush. Retrieved January 24, 2019 .
- ↑ RM Latzke: Frescography wall pictures. Retrieved January 24, 2019 .
- ^ D. Zwang: Production Inkjet — The Next Wave: HP High Definition Nozzle Architecture. In: WhatTheyThink ?, 02/09/2015 (event presentation). Retrieved January 24, 2019 .
- ↑ Landa Corp .: Nanography White Paper (2012). Retrieved January 24, 2019 .
- ^ R. Schlözer: Digital printing - past and present. In: VDD seminar, November 27, 2008 (event presentation). Retrieved January 24, 2019 .
- ↑ Tonejet Ltd: The only nozzle-less jetting technology with less than 0.5 μm printed ink layer. Retrieved January 24, 2019 .
- ^ R. Schlözer: Digital printing - past and present. In: VDD seminar, November 27, 2008 (event presentation). Retrieved January 24, 2019 .
- ^ A. Boehringer, P. Ebeling, F. Lohmann: Landa. In: Print.de topic. Retrieved January 24, 2019 .
- ↑ KwikKopy: LumeJet Print Technologies enters liquidation. Retrieved January 24, 2019 .
- ↑ The strengths of digital web printing. In: World of Print 3/2018. Retrieved January 24, 2019 .
- ↑ KBA-Digital & Web Solutions: Lean and broadly based for more flexibility in media change. In: Print & Production October 07, 2015. Retrieved January 24, 2019 .
- ↑ Messe Düsseldorf: 3rd drupa Global Trends report, March 17, 2016. Retrieved January 24, 2019 .
- ↑ Interquest: Free Articles (press review on publishing market studies). Retrieved January 24, 2019 .
- ↑ bvdm, Fogra: Technical testing of sheet-fed printing systems with electrophotographic print image transfer. Retrieved January 24, 2019 .
- ↑ bvdm, Fogra: Test forms for system testing of digital printing. Retrieved January 24, 2019 .
- ↑ Employer's liability insurance association ETEM: Risk assessment - practical aid for digital printing. Retrieved January 24, 2019 .
- ↑ BG ETEM: toner-based digital printing systems. Retrieved January 24, 2019 .
- ↑ Employer's Liability Insurance Association ETEM: Toner dust. Retrieved January 24, 2019 .
- ↑ ETEM trade association: InkJet digital printing. Retrieved January 24, 2019 .
- ↑ Employer's Liability Insurance Association ETEM: Safe working in inkjet digital printing. Retrieved July 10, 2019 .
- ↑ MedienStandard Druck 2018. Retrieved on January 24, 2019 .
- ↑ DIN ISO 2836: 2005-10. Retrieved January 24, 2019 .
- ↑ ISO / DTS 21139-21. Retrieved January 24, 2019 .
- ↑ ISO 18055-1: 2004-06. Retrieved January 24, 2019 .
- ↑ DIN 53131-1: 2003-10. Retrieved January 24, 2019 .
- ↑ DIN 53131-2: 2010-09. Retrieved January 24, 2019 .
- ↑ Inkjet test form: drying time to DIN 53131-2. Retrieved January 24, 2019 .
- ↑ DIN 53131-3: 2010-11. Retrieved January 24, 2019 .
- ↑ APFConsortium. Retrieved January 24, 2019 .
- ↑ EFI: Fiery FreeForm - the direct route to professional VDP products. Retrieved January 24, 2019 .
- ^ PCL - HP Page Description Language. In: Undocumented Printing Wiki. Retrieved January 24, 2019 .
- ↑ ISO 16612-2: 2010. Retrieved January 24, 2019 .
- ↑ ISO / CD 16612-3. Retrieved January 24, 2019 .
- ^ The PDF Association: PDF / VT Application notes. Retrieved January 24, 2019 .
- ↑ Helge Blischke: "Optimized postscript specification". In: PostScript Programming, May 28, 2008 (Adobe Forum). Retrieved January 24, 2019 .
- ↑ Xerox: DocuPrint NPS Guide to Using Page Description Languages. Retrieved January 24, 2019 .
- ↑ PODi: PPML homepage. Retrieved January 24, 2019 .
- ↑ NPES CGATS: Application Notes for CGATS.20 (PPML / VDX). Retrieved January 24, 2019 .
- ↑ ISO 16612-1: 2005. Retrieved January 24, 2019 .
- ^ Hewlett-Packard: HP SmartStream Design. Retrieved January 24, 2019 .
- ↑ ISO 16613-1: 2017. Retrieved January 24, 2019 .
- ↑ ISO 20690: 2018-02. Retrieved January 24, 2019 .
- ↑ ISO 21632: 2018-12. Retrieved January 24, 2019 .
- ↑ Quality seal digital printing. Retrieved January 24, 2019 .
- ↑ Process standard digital printing. Retrieved January 24, 2019 .
- ↑ T. Zintel: Qualification to measure digital printing. Retrieved January 24, 2019 .
- ↑ Central Technical Committee for Vocational Training in Printing and Media (ZFA). Retrieved January 24, 2019 .
- ^ ZFA: Media Technologist Print. Retrieved January 24, 2019 .
- ↑ ZFA: Media Technologist Screen Printing. Retrieved January 24, 2019 .
- ↑ ZFA: Mediengestalter Digital und Print. Retrieved January 24, 2019 .
- ↑ VDM Initiative: Certified Digital Printing Professional. Retrieved January 24, 2019 .
- ↑ Fachverband Medienproduktion: Geprüfter Medienproduktioner / f: mp. Retrieved January 24, 2019 .
- ↑ viscom: Factsheet media technologist. Retrieved January 24, 2019 .
- ↑ VSD: Basic Education. Retrieved January 24, 2019 .
- ↑ dp-i AG: What we do. Retrieved January 24, 2019 .
- ↑ VSD: 11-day “Variable Data Operator” course. Retrieved January 24, 2019 .
- ↑ Berufslexikon.at: printing technician - focus on digital printing. Retrieved January 24, 2019 .
- ↑ Trade fair info: trade fair calendar with print trade fairs. Retrieved January 24, 2019 .
- ↑ APTech: PRINT organizer homepage. Retrieved January 24, 2019 .
- ↑ IGAS: trade fair homepage. Retrieved January 24, 2019 .
- ↑ a b FESPA: Events. Retrieved January 24, 2019 .
- ↑ Labelexpo Europe: Trade fair homepage. Retrieved January 24, 2019 .
- ↑ Viscom trade fair for visual communication. Retrieved January 24, 2019 .
- ↑ Mack Brooks: Inprint-Organizers homepage. Retrieved January 24, 2019 .
- ↑ Hunkeler: innovationdays homepage. Retrieved January 24, 2019 .
- ^ Bvdm: Digital Printing Congress: reports and dates (if forthcoming). Retrieved February 13, 2019 .
- ↑ Mailingtage (congress homepage). Retrieved January 24, 2019 .
- ↑ Fogra: dpgw. Retrieved January 24, 2019 .
- ^ IMI: Completed Programs. Retrieved January 24, 2019 .