Ceramic fiber composite

Photo: MT Aerospace , Augsburg
Ceramic fiber composite materials are a class of materials within the group of composite materials or technical ceramics . They are characterized by a matrix of normal ceramic embedded between long fibers , which is reinforced by ceramic fibers and thus becomes fiber-reinforced ceramics , composite ceramics or simply fiber ceramics . In the German specialist literature, the material class is often referred to in English as Ceramic Matrix Composites and is abbreviated as CMC . The matrix and fibers can in principle consist of all known ceramic materials, with carbon also being treated as a ceramic material in this context .
The article describes the currently industrially available composite ceramics with their most important manufacturing processes, essential properties as well as some development and successful application examples of this relatively young group of materials.
introduction
In Development and Application of composite ceramic currently come primarily carbon and so-called silicon carbide fibers for use and to a lesser extent fibers of alumina (Al 2 O 3 ) or mixed crystals of alumina and silica (SiO 2 ), so-called mullite , consist . In technical applications, the main matrix materials currently used are aluminum oxide, mullite, carbon and silicon carbide ( Lit .: W. Krenkel, 2003).
The motivation for the development of these ceramics arose from the problems that arose when using conventional technical ceramics such as aluminum oxide , silicon carbide, aluminum nitride , silicon nitride or zirconium (IV) oxide : all of these materials break easily under mechanical or thermomechanical loads because they are themselves Small manufacturing defects or scratches on the surface can become the starting point of a crack. A crack propagation is, unlike metals (keyword: ductility ) opposite but similar to glass, very little resistance. It is characterized by its brittle fracture behavior, which makes many applications difficult or impossible. Developments to improve this property by embedding foreign particles, monocrystalline short fibers (so-called whiskers ) or discs (so-called platelets ) in the ceramic have only been able to improve their crack resistance to a limited extent, but have been used in some ceramic cutting tools . Only the use of long fibers to reinforce ceramics was able to drastically increase this crack resistance and lead to improved properties such as increased ductility , fracture toughness and thermal shock resistance , with which new fields of application could and can be opened up.
The composite ceramics produced in this way are usually abbreviated in the form of “fiber type / matrix type”. For example, “C / C” stands for carbon fiber-reinforced carbon or “C / SiC” for carbon fiber-reinforced silicon carbide. If the manufacturing process is to be included in this abbreviation, it is often (and also in the following article) abbreviated to “manufacturing process-fiber type / matrix type”. For example, a carbon fiber reinforced silicon carbide produced using the liquid polymer infiltration process (see below) is simply referred to as “LPI-C / SiC”.
The most important fiber-reinforced ceramics currently available industrially are C / C, C / SiC, SiC / SiC and Al 2 O 3 / Al 2 O 3 . They differ from conventional technical ceramics mainly through the properties presented in more detail below:
- higher elongation at break of up to one percent
- significantly higher crack resistance
- extreme thermal shock resistance
- better dynamic resilience
- anisotropic properties based on the fiber orientations
history
There are several approaches available for processing CMCs using liquid, gaseous or solid starting materials. The technique of chemical gas phase infiltration (CVI) promoted the development of CMCs. The CVI technique has been studied as an extension of the Chemical Vapor Deposition (CVD) technology since the 1960s. CVD involves the deposition of a solid on a heated substrate from gaseous precursors. It has been used to make wear-resistant coatings, coatings for nuclear fuel, thin films for electronic circuits, ceramic fibers, and so on for many years. When the CVD technique is used to impregnate relatively large amounts of matrix materials in fibrous preforms, it is known as CVI. CVI was first used for the production of carbon-carbon composites by pyrolysis of methane at 1000–2000 ° C. Carbon-carbon (C / C) composites have several advantageous properties (e.g. such as low density and good mechanical properties at high temperatures). However, around 1973 it became apparent that applications of C / C composites would be limited due to their poor oxidation resistance at temperatures above 450 ° C. SiC matrix composites were seen as a solution to remedy the above mentioned deficiency of C / C composites for long life at elevated temperatures in oxidative environment. The fiber reinforced CMCs followed the development of C / C composites and CVI manufacturing technology. The development of CVI SiC / SiC composites began in the 1980s when SEP (now SNECMA ), Amercorm , Refractory Composites and others began adding equipment and processes to manufacture CMC components for aerospace, defense and other applications develop. SNECMA was at the forefront of this technology and demonstrated various CVI-SiC / SiC components with satisfactory performance on turbine engines. A number of CVI-SiC / SiC components have proven successful in turbine engines and other components. The feasibility of CVI-SiC matrix composites was investigated in 1977 and independently confirmed in 1978. CVI SiC matrix composites reinforced with SiC fibers have been manufactured since the late 1980s. The current CVI SiC / SiC composites show excellent performance under extreme conditions, such as elevated temperatures. In the meantime, alternative manufacturing processes such as melt infiltration (MI), polymer infiltration and pyrolysis (PIP) and hybrid approaches that combine CVI and other methods have been developed. There have been tremendous advances in CMC developments over the past 30 years.
Manufacturing in general
The production of components from fiber-reinforced ceramics usually takes place in three steps:
- Depositing and fixing the fibers in the desired component shape
- Introducing the ceramic matrix material between the fibers
- Finishing and, if necessary, further post-treatment steps such as the application of coatings
The first and last step is almost the same for all types of fiber-reinforced ceramics:
In the first step, the fibers (technically also referred to as rovings ) are laid down and fixed using various techniques, similar to the production of fiber-reinforced plastic : laying down fiber fabric , winding, braiding or knitting fibers are examples of this. In the third and last step, conventional grinding , drilling , lapping or milling processing techniques are common, as is the case with all ceramics with diamond tools. Due to the special properties of the fiber-reinforced ceramics, processing techniques with the water jet and the laser are also possible without any problems.
The second step currently knows in principle five different methods of bringing the ceramic matrix between the fibers:
- Deposition of ceramics from a hot gas mixture
- Generation by pyrolysis containing a Si and C atoms polymer
- Generation through chemical reaction
- Generation by sintering at low temperatures (1000 to 1200 ° C)
- Generation by electrophoresis with ceramic powder
The fifth method is not yet in industrial use. For all of the processes mentioned, there are also sub-variants that differ in process-related details, as well as combinations. They can be found in books, specialist journals and congress literature. They are only described in simplified form below.
The first three processes are used almost exclusively for the production of the non-oxidic, the fourth for the production of the oxide composite ceramics.
What all the methods have in common is that the manufacturing process, as explained below, leads to a porous material.
Notes on ceramic fibers
Among the ceramic fibers , not only fibers are associated with fiber-reinforced ceramic understood that, like real Technical Ceramics , a polycrystalline comprise material structure, but also those having an amorphous arrangement of atoms. Because of the high temperature in the manufacture of composite ceramics, the use of not only organic, but also inorganic metal and glass fibers is excluded. Only high-temperature stable ceramic fibers made of crystalline aluminum oxide , mullite (mixed crystals of aluminum oxide and silicon oxide), largely crystalline silicon carbide and zirconium oxide, carbon fibers with the graphitic lamellar planes in the direction of the fibers and amorphous fibers made of silicon carbide are used in applications. All of these “ceramic” fibers are characterized by an extensibility which, at over 2%, is in some cases significantly higher than the extensibility of normal ceramics (approx. 0.05 to 0.10%). The reason for this is that, depending on the manufacturer, the fibers contain various additives (e.g. oxygen, titanium, aluminum, see ceramic fibers), without which, for example, the amorphous SiC fibers never have an extensibility of 2% and a tensile strength of over 3000 MPa could achieve. With these properties, the fibers can also be two and three dimensional fiber structures woven (see figure). When processing, such as weaving, the fibers have to withstand high tensile loads and small bending radii.
Production in detail
Deposition of the matrix from a gas mixture
This process is derived from coating processes in which a certain gas or gas mixture deposits material on heated surfaces. It is called the CVD process ; CVD is the abbreviation for Chemical Vapor Deposition .
When this method is used on a fiber structure fixed in the form of a component, the coating material is also deposited on the fiber surfaces inside the component. Therefore, this method is also known as chemical vapor infiltration (engl. Chemical vapor infiltration or CVI method ), respectively.
An example of this is a process for the production of C / C: a C-fiber structure is under certain pressure (usually below 100 hPa) and temperature conditions (usually above 1000 ° C) with a mixture of argon and methane (CH 4 ) or propane (C 3 H 8 ). From the gas mixture, carbon is deposited on and between the fibers.
Another example is the deposition of silicon carbide. A gas mixture of hydrogen as a catalyst and methyl trichlorosilane (MTS, chemical formula CH 3 SiCl 3 ), which also plays a role in the production of silicones , is usually used for this purpose . The carbon and silicon atoms of the MTS molecule form silicon carbide on every surface that is over 800 ° C, the other H and Cl atoms leave the process as HCl gas with the hydrogen.
During the deposition, closed pores are inevitably created when the gas inlet openings have overgrown.
Matrix generation by pyrolysis of C- and Si-containing polymers
Suitable polymers made from hydrocarbons form carbon during pyrolysis with volume shrinkage and outgassing. Polymers in which some of the carbon atoms have been replaced by silicon atoms, for example so-called carbosilanes , similarly form an amorphous and mostly carbon-enriched silicon carbide during pyrolysis, likewise with volume shrinkage and outgassing .
Fibers, fiber fabrics or stacks of fiber fabrics and also three-dimensional fiber structures can be soaked or infiltrated with these polymers. The structure is fixed in a first stage through subsequent hardening and pyrolysis. Due to the shrinkage in volume, the matrix still has a high porosity at this stage, which is not acceptable for most applications. In order to reduce the porosity, five to eight subsequent cycles of impregnation , hardening and pyrolysis are therefore usually required to complete the structural component.
The process is mostly referred to as Liquid Polymer Infiltration, abbreviated to LPI process , and sometimes also as Polymer Infiltration and Pyrolysis, abbreviated to PIP process .
Here, too, there is residual porosity, as each polymer shrinks in volume during pyrolysis. The porosity is reduced with each infiltration and pyrolysis cycle.
Matrix generation through chemical reaction
In this process, a material is already present between the fibers that is converted into the actually desired ceramic matrix by chemical reaction with another substance. The manufacture of conventional ceramics also uses such reactions: Reaction- bound silicon nitride (RBSN) is produced by the reaction of silicon powder with nitrogen, and porous carbon is converted with silicon to form silicon-containing silicon carbide , so-called SiSiC .
An example of the production of fiber-reinforced ceramics using this process is the so-called directed melt infiltration: molten aluminum between the fibers is oxidized by the admission of oxygen to the aluminum oxide matrix. Alloy constituents in the melt prevent the continuous oxidation from being interrupted by the formation of aluminum oxide barriers. The finished material still contains residual components of unreacted aluminum.
Another example that has been introduced industrially in the manufacture of ceramic brake discs is the conversion of the matrix carbon of a porous C / C material with liquid silicon. With controlled process management under vacuum and above the melting temperature of the silicon (1410 ° C), the matrix carbon essentially reacts to form silicon carbide and the fibers remain almost untouched and can thus fulfill their reinforcement function. This process is mostly referred to as Liquid Silicon Infiltration, or LSI process for short .
In these processes, the residual porosity is as low as 3%.
Matrix generation by sintering
In oxide composite ceramics, the matrix material is currently produced from primary materials by high-temperature treatment ("sintering"). These raw materials make it possible to keep the temperatures lower than the usual sintering temperatures of conventional ceramics, which are around 1600 ° C. The available oxidic fibers would be damaged too much by such high temperatures. The primary materials are liquids that are mixed with more or less high proportions of oxide ceramic powders to form a so-called slip and then introduced into the fibers. At temperatures between 1000 and 1200 ° C, the oxide-ceramic, porous matrix is created (associated with strong volume shrinkage). An example of the materials are mixtures of Al 2 O 3 powder with tetra-ethyl-ortho- silicate , which (as a silicon and oxygen-donor) and aluminum butylate (as aluminum donors) in the correct mixture of mullite produce as a matrix. Sol-gel approaches should also be mentioned as further possibilities for the liquids . State-of-the-art, however, are purely aqueous suspensions of powder with nanometer grain sizes, in which a proportion of coarser oxide-ceramic powders of different quality (aluminum oxide, zirconium oxide) is added.
Here, the porosity of commercially used material is around 20%.
Matrix generation by electrophoresis
In electrophoresis , dispersed , electrically charged particles in a liquid are transported to the oppositely charged surface and deposited there in the electric direct voltage field of two electrodes . If a fiber structure is used as the surface, the powder particles are deposited there and also fill the spaces between the fibers. Fiber-reinforced ceramics produced in this way are currently not in industrial use. Problems include the relatively complex preparation and dispersion of the powder, the setting of the charge and the limitation to very thin component wall thicknesses.
Permanent porosity is also created here by the overgrowth of access channels.
properties
Mechanical properties
Basic mechanism of mechanical properties
The increase in crack resistance mentioned in the introduction by embedding ceramic fibers in the ceramic matrix is based on the following basic mechanism:
When loaded, the matrix material forms cracks just like in the unreinforced form when stretched over (depending on the matrix type) 0.05% and the embedded fibers form a bridge over the crack. This bridging mechanism requires that the matrix can slide along the fibers, i.e. that it is only weakly mechanically connected to the fibers. With a firm connection between the matrix and the fibers, the fibers in the bridge would have to have extremely high extensibility or correspondingly low rigidity, which is not the case. This means that with a firm connection, the matrix crack would also go through the fibers at the same point and the fiber-reinforced ceramic showed the brittle fracture behavior of the non-reinforced ceramic.
The secret of fiber-reinforced ceramics with high crack resistance is therefore to ensure during manufacture that the connection between the fibers and the matrix allows sliding. Only in this way can the fibers form a significant bridge over cracks and bring out their extensibility (more than 2% for C and SiC fibers, almost 1% for Al 2 O 3 fibers). In the production of fiber-reinforced ceramics, this sliding mechanism is usually ensured by a thin coating of the fibers with carbon or boron nitride . These coatings have atomically arranged, lamellar sliding planes and form the lubricant between the fibers and the matrix.
Oxide composite ceramics have a special feature: the weak connection is created by the high porosity of the matrix or by artificially created gaps between the fiber and the matrix. The latter can be obtained, for example, by any coating on the fibers, for example with carbon, which burns out during the subsequent sintering process and leaves a corresponding gap. However, too high a matrix porosity leads to low compressive and flexural strengths, so that in practice a compromise has to be found between good strength values and good breaking behavior.
Properties for tensile and bending loads, crack resistance
The influence of the fiber coating on the properties of such composite ceramics becomes visible in the determination of flexural strength , tensile strength and crack resistance on material samples.

Caption: SiSiC: conventional SiSiC , SiCSiC (CVI) and CSiC (CVI): SiC / SiC or C / SiC, CSiC (95) and CSiC (93): in the LPI- Process produced C / SiC, Ox (PP): oxide composite ceramics, CSiC (Si): C / SiC produced in the LSI process.
The curves of crack resistance measurements on notched specimens are shown as an example in the picture on the right. In these tests, with increasing force, a notched specimen (see picture) is loaded until it breaks. The force and the path of the force-introducing punch are measured. In fracture mechanics , the force is normalized to the stress intensity factor (SIF, known in the art as the K 1c factor), taking into account the size of the fracture surface. Since it has been found that the size of the fracture surface in composite ceramics cannot be determined, the curves shown are normalized only to the size of the initial notch and are therefore also referred to as the formal SIF "K" in the figure . Since this value corresponds to a force, the area (the integral ) under the curves in a relative comparison of the curves with one another can be regarded as the energy that has to be expended to destroy the sample. The results are only directly comparable if the sample geometry is identical for all samples.
The crack resistance curves of the various composite ceramics shown in the picture show that the specific energy expenditure with which a crack can be driven through composite ceramic samples is many times that of conventional SiSiC ceramics. The maximum of the various crack resistance curves indicates the level of force that is required to drive the crack through the specimen. Different types and manufacturing processes lead to recognizable and clear differences in the qualities of this material class, especially with regard to crack resistance.
Material type | Al 2 O 3 / Al 2 O 3 | Al 2 O 3 | CVI-C / SiC | LPI-C / SiC | LSI-C / SiC | SSiC |
---|---|---|---|---|---|---|
Porosity (%) | 25th | <1 | 12 | 12 | 3 | <1 |
Density (g / cm³) | 2.8 | 3.9 | 2.1 | 1.9 | 1.9 | 3.1 |
Tensile strength (MPa) | 170 | 250 | 310 | 250 | 190 | 200 |
Elongation at break (%) | 0.3 | 0.1 | 0.75 | 0.5 | 0.35 | 0.05 |
Modulus of elasticity (GPa) | 100 | 400 | 95 | 65 | 60 | 395 |
Flexural strength (MPa) | 350 | 450 | 475 | 500 | 300 | 400 |
Explanations of the table: The prefix CVI-, LPI- and LSI- refers to the manufacturing process of the respective C / SiC composite ceramic. The data for the composite ceramics come from ( Lit .: W. Krenkel, p. 143), those for the oxidic composite ceramics Al 2 O 3 from the Pritzkow Spezialkeramik company and the data for SSiC from a data sheet from HCStarck Ceramics. The tensile strength for SSiC and Al 2 O 3 was calculated from elongation at break and modulus of elasticity , since tensile strengths are not specified for conventional ceramics , but usually only flexural strength values . It should be noted that these are average values. Within the individual manufacturing processes, including conventional ceramics, there are sometimes considerable deviations from the specified values.
When testing the tensile strength of composite ceramics, in contrast to conventional ceramics, quasi-plastic curves and possible elongations of up to one percent, more than ten times the extensibility of all technical ceramics , are caused by the crack-bridging mechanism ; quasi-plastic because the curve turning after the linear-elastic range is not based on plastic deformation of the material, but is due to the formation of a crack system that is held together by the fibers. Since the load-bearing fibers have a smaller modulus of elasticity, the slope of the curve decreases and thus simulates plastic behavior. Here, too, the values in the table show that the different types of composite ceramics use the fiber extensibility to different degrees.
The measurement curves for determining the flexural strength look practically the same as the curves shown above for determining the crack resistance. When evaluating tensile and flexural strengths, a distinction must be made between two things:
- Material with little or, in the extreme case, no matrix has high tensile strength (namely fiber tensile strength) but almost no flexural strength.
- Conversely, material with a high matrix content and low porosity shows high flexural strengths (like conventional ceramics), which in turn say nothing about whether the elasticity of the fibers is used.
Both values must be viewed independently of one another.
Other mechanical properties
In many components made of composite ceramics, the fibers are in two-dimensional form either as stacked layers of fabric or as crossed layers of one-dimensionally aligned fibers. The materials are therefore anisotropic . The propagation of cracks between these layers is not hindered by any fiber bridge. The values for the interlaminar shear strength are correspondingly low for this material, as is the tensile strength perpendicular to the fabric. As in the fiber-reinforced plastic are possible delaminations a weak point of the material. It can be significantly improved by introducing three-dimensional fiber structures.
material | CVI-C / SiC | LPI-C / SiC | LSI-C / SiC | CVI-SiC / SiC |
---|---|---|---|---|
Interlaminar Shear Strength (MPa) | 45 | 30th | 33 | 50 |
Tensile strength perpendicular to the fiber plane (MPa) | 6th | 4th | - | 7th |
Compressive strength perpendicular to the fiber plane (MPa) | 500 | 450 | - | 500 |
Comments on the table: Due to the porosity, the compressive strength values are lower than with conventional ceramics, where more than 2000 MPa is specified for silicon carbide. Porosity and a lack of fiber bridges lead to the very low tensile strengths perpendicular to the fiber plane.
The crack-bridging effect of the fibers also allows this ceramic to be subjected to high dynamic loads. Samples are subjected to cyclic pressure and tensile loads until they break in alternating load tests, so-called “low” or “high cycle fatigue” tests. The higher the starting load, the fewer cycles the sample survives. Different starting loads plotted against the logarithm of the respective number of cycles achieved result in the so-called Wöhler line. It shows how many thousands or millions of load cycles the tested material can survive under a certain dynamic load. Fiber-reinforced ceramics can come up with excellent results here: at 80% of the ductility, when subjected to cyclical loads, SiC / SiC survives around 8 million tension-compression cycles (see picture).
The Poisson's ratio shows an anomaly perpendicular to the two-dimensional fiber plane during the measurement: it assumes negative values in the direction perpendicular to the fibers if, due to the formation of interlaminar cracks, the sample thickness increases briefly in the early phase of the measurement instead of decreasing.
Thermal and electrical properties
The thermal and electrical properties of fiber-reinforced ceramics result from the components of fibers, matrix and pores and their composition. The fiber orientation also generates direction-dependent ( anisotropic ) parameters.
The most common composite ceramics currently available can be summarized as follows:
Fiber-reinforced ceramics that use oxides are still very good electrical insulators and, because of the pores, the thermal insulation effect is significantly higher than that of conventional oxide ceramics .
The use of carbon fibers increases the electrical and thermal conductivity in the direction of the fibers as soon as there is direct electrical contact with them.
Silicon carbide as a matrix is a very good conductor of heat . As an electrical semiconductor , its electrical resistance decreases with increasing temperature. Because of their amorphous microstructure, silicon carbide fibers conduct heat and electrical current much worse. In composite ceramics with silicon carbide as a matrix, both the thermal and electrical conductivity drop to lower values because of the porosity. Some of the information is listed in the following table.
material | CVI-C / SiC | LPI-C / SiC | LSI-C / SiC | CVI-SiC / SiC | SSiC |
---|---|---|---|---|---|
Heat conduction (p) [W / (m · K)] | 15th | 11 | 21st | 18th | > 100 |
Heat conduction (s) [W / (m · K)] | 7th | 5 | 15th | 10 | > 100 |
Thermal expansion (p) [10 −6 · 1 / K] | 1.3 | 1.2 | 0 | 2.3 | 4th |
Thermal expansion (s) [10 −6 · 1 / K] | 3 | 4th | 3 | 3 | 4th |
specific electr. Resistance (p) [Ω · cm] | - | - | - | - | 50 |
specific electr. Resistance (s) [Ω · cm] | 0.4 | - | - | 5 | 50 |
Notes on the table: With (p) and (s) the properties are p arallel and s meant to enkrecht fiber orientation of the anisotropic material. There is no literature or manufacturer information on values not entered. Because of its low porosity, the LSI material has the highest thermal conductivity of all composite ceramics - an advantage for using this material as a highly stressed brake disc material. Here, too, the values can vary considerably even within the individual ceramic types, depending on the details of the manufacturing process.
Normal ceramics and technical ceramics are sensitive to thermal voltages, which are particularly high when subjected to thermal shock loads . The reason for this lies in the low elasticity and high rigidity (high modulus of elasticity ) of these materials. Temperature differences in the material produce different expansion, which, due to the high modulus of elasticity, leads to correspondingly high stresses. This causes the material to overstretch and break. In fiber-reinforced ceramics, such cracks are bridged by the fibers. A component does not suffer any macroscopic damage, even if cracks have formed in the ceramic matrix. The use of this material class in disc brakes proves the performance of composite ceramics under extreme thermal shock conditions.
Corrosion properties
Broader studies on the corrosion behavior of fiber-reinforced ceramics are not yet available. Here, too, the properties are determined by the properties of the components used, namely fibers and matrix.
In general, ceramic materials are very resistant to corrosion compared to most other materials. The large number of manufacturing variants with different additives, for example sintering aids , mixed forms, especially with the oxides, impurities, glass phases at the grain boundaries and differences in porosity have a decisive influence on the corrosion behavior ( Lit .: J. Kriegesmann).
The following can be found in key words from the literature about the matrix and fiber materials currently important in applications:
- Aluminum oxide: In its very pure state,
aluminum oxide is resistant to almost everything; amorphous glass phases at the grain boundaries and silicon oxide content determine the rate of corrosion in concentrated acids and alkalis . At high temperatures, they lead to creep behavior under load . For molten metals, aluminum oxide is only used for precious metals such as gold or platinum. - Alumina fibers:
behave similarly to alumina. The fibers available commercially are not of extreme purity and are therefore more fragile. The creep behavior at temperatures above about 1000 ° C currently allows only a few applications of oxide composite ceramics.
- Carbon:
Carbon corrodes, burns better, with oxygen at temperatures from around 500 ° C. It also oxidizes in strongly oxidizing media (e.g. concentrated nitric acid ). In most molten metals it dissolves or forms carbides .
- Carbon fibers:
Carbon fibers behave practically like carbon.
- Silicon carbide:
Very pure variants of silicon carbide are among the most corrosion-resistant materials. Only strong alkalis, oxygen from approx. 800 ° C and most metal melts react with this material. In molten metals , both carbides and silicides (compounds of silicon with metal) are formed.
When SiC reacts with oxygen to form SiO 2 and CO 2 , the silicon dioxide forms a protective layer that has a passivating effect (“passive oxidation”). At even higher temperatures (from approx. 1600 ° C) and simultaneous lack of oxygen ( partial pressure below 50 mbar), however, in addition to CO 2 and CO, gaseous silicon monoxide (SiO) is formed, which prevents any protective effect. This so-called "active oxidation" leads to very rapid degradation of the silicon carbide under the conditions mentioned.
In connection with composite ceramics, this characterization only applies to SiC matrix material that has been produced using the CVI process. There the matrix consists of very pure, finely crystalline SiC. Matrix produced with the LPI process is significantly more sensitive to all types of corrosion due to its amorphous structure and porosity. The silicon residues that are always present in the matrix of the LSI material result in a deteriorated corrosion resistance. - Silicon carbide fibers:
Since silicon carbide fibers are produced by pyrolysis of cross-linked, organosilicon synthetic resins (analogous to the production of carbon fibers), the same applies to them as to the matrix produced in the LPI process: significantly greater sensitivity to corrosion by alkalis and oxidizing media.
Applications
With fiber-reinforced ceramic, a material is available that no longer has the serious disadvantages of conventional technical ceramics, namely their low fracture toughness and high thermal shock sensitivity. Application developments have therefore concentrated on areas in which reliability is required at high temperatures, which are no longer accessible to metals, and with abrasive (= wear-causing) loads. The following priorities have arisen in developments and applications so far:
- Heat protection systems for spacecraft that are exposed to high thermal voltages and vibrations when they re-enter the earth's atmosphere.
- Components for gas turbines in the area of hot gases, i.e. in the turbine combustion chamber , the static guide blades that guide the gas flow and the actual turbine blades that drive the compressor of the gas turbine.
- Components for burner technology and hot gas ducts made from oxide composite ceramics.
- Brake discs for heavily loaded disc brakes that are exposed to extreme thermal shock conditions on the friction surface (unlike when a glowing part is immersed in water, there is no heat-insulating water vapor layer here).
- Components for plain bearings with high corrosion and wear loads.
In addition, all areas are of interest in which conventional technical ceramics are used or in which metallic components do not achieve a satisfactory service life due to corrosion or high temperatures. The following presentation of some development and application examples is far from complete and is only intended to indicate the breadth of the technical possibilities.
Developments for applications in space travel
In the aerospace sector , fiber-reinforced ceramics are of interest for components of heat protection systems and for movable control flaps of space gliders . When re-entering the earth's atmosphere, surface temperatures of over 1500 ° C arise on these elements for a few minutes, which can only be endured by ceramic materials without any major impairment. The use of fiber-reinforced ceramics for hot structures in space travel promises, in contrast to the previously used material systems, among other things:
- Weight savings
- A contribution of the heat protection system to the load-bearing structure
- Reusability for multiple re-entries
Since the available oxide fibers creep under load at these high temperatures and the amorphous SiC fibers lose their strength due to recrystallization, the material and component developments have concentrated on the composite ceramic C / SiC. The part of the HERMES -Programmes the ESA in the 1980s carried out and 1992 broken developments after several follow-up programs culminating with the development and qualification of nose cone, wing leading edges and tail control flaps of the space plane X-38 of NASA found.
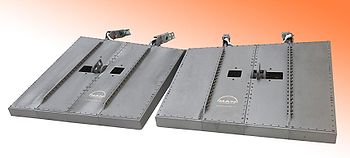
Size: 1.5 × 1.5 × 0.15 m, weight: 68 kg each, assembled from individual parts with over 400 screws / nuts made of CVI-C / SiC each.
Photo: MT Aerospace
One of these developments was used, for example, to qualify screws and nuts made from composite ceramics. Screws made of technical ceramics are available, but due to the notches in the thread root, they are fragile and by far do not have the required reliability. The use of screws made of C / C is also too risky due to its sensitivity to oxidation.
Another important component of these control flaps is the centrally located bearing through which the force for the movement is introduced. This bearing was successfully tested under realistic conditions (4 tons load, 1600 ° C on the underside, oxygen concentration at the level when re-entering the earth's atmosphere and simultaneous 8 ° bearing movements with a movement cycle in four seconds) at the DLR in Stuttgart; five re-entry phases were simulated in this way.
The use of C / SiC has forced the development and qualification of coating systems that prevent the rapid burnout of the C fibers under re-entry conditions. Experiments in the plasma stream under simulated re-entry conditions have proven the success of this development work.
A further qualification step for airworthiness took place through deformation tests at over 1000 ° C on an IABG test stand in Munich. The deformation under 4 tons of load confirmed the corresponding calculations and the design. Final ground tests after the flaps had been installed on the X-38 space glider in Houston, Texas, USA, intended for the flight test, were also successful. For financial reasons, NASA was no longer able to achieve the goal of the project, namely the transport of the X-38 with a space shuttle flight into orbit and the subsequent (unmanned) reentry into the earth's atmosphere.
It must be pointed out at this point that these qualifications served the use of C / SiC composite ceramics for this special case. The high temperature load lasts about 20 minutes when re-entering. If it is reusable, the duration adds up to a few hours of cyclical loading. The use of oxidation-protected C / SiC for industrial high-temperature applications with a service life of several hundreds or thousands of hours is not yet guaranteed.
Developments for use in gas turbines
The aim of using composite ceramics in gas turbines is to increase the gas temperature, which leads to an increase in efficiency.
The complex shape of guide vanes and turbine blades in gas turbines as well as the very high thermal and mechanical stress on these parts have led to the fact that initially only the development of combustion chambers made of composite ceramics was successfully advanced. Advances in this area have come furthest in the United States. A combustion chamber made of SiC / SiC composite ceramic based on a special high-temperature-resistant SiC fiber has been in use in a gas turbine for over 15,000 hours. Since SiC is already noticeably attacked by oxidation at temperatures of around 1100 ° C in such periods, a very effective oxidation protection had to be developed here as well. It consists of a multilayer system of oxide ceramics.
The fact that the tested temperature level does not yet offer any advantages compared to conventional metallic combustion chambers cooled with an air film, and that the components following the combustion chamber (guide vanes and turbine blades) are also developed and developed for a higher temperature level, prevents the results so far from being implemented quickly in real applications must be qualified and that the costs for the production of the composite material system from special SiC fibers, SiC matrix and special coating system are still very high.
Use of oxide composite ceramics in burners and hot gas ducts
Oxygen-containing, hot gases with a temperature of more than 1000 ° C lead sooner or later in burners with conventional flame tubes made of high temperature resistant steel to their scaling , in the case of tubes made of silicon carbide to damage by oxidation. Since these parts are not exposed to high mechanical stress, but only to strong thermal shocks, oxide composite ceramics are particularly suitable for such uses up to 1300 ° C. The series of images below shows the flame tube of a burner made of oxidic aluminum oxide composite ceramics, which has been used for 15,000 hours in a baking line for crispbread and has now reached more than 20,000 operating hours. A service life of up to 20 times that of conventional materials can be achieved in these applications.
Flaps or fans for regulating or conveying oxygen-containing hot gas flows in various systems can be made from oxide composite ceramics in the same form as metals. They have the advantage that they do not deform (“ warp ”) - like metals at temperatures above 650 ° C. The use of this material for lifting gates (see picture series), for example in sintering furnaces, which are also subjected to high thermal loads of up to 1300 ° C with frequent opening and closing processes, has proven itself in one case for more than 12 months with over 260,000 opening and closing cycles .
Use as a brake disc
According to the brake discs made of C / C material, which has long been in racing cars of the formula 1 are used and in brakes of aircraft, have now brake discs made of C / SiC material, which are prepared by the LSI process, commercially available and are installed in expensive sports cars, sometimes at an additional cost. The LSI process offers cost advantages in production. The panes made from a mixture of short fibers and resin are pressed, hardened, pyrolysed to form a C / C pane and then, as described above, converted into an LSI-C / SiC pane using molten silicon.
The advantages of these brake discs can be summarized as follows:
- The disc wear is very low. The service life compared to a conventional cast iron washer is around six times longer. Depending on the driving style, this also allows a window to be used over the entire service life of the vehicle. Up to 300,000 km are specified under normal load.
- Even under high stress there are no fluctuations in the coefficient of friction , the so-called fading effect known from metal disks .
- In contrast to brake discs made of C / C, no influence of moisture on the braking performance is observed.
- The pane material is extremely corrosion-resistant and therefore insensitive to the effects of road salt in winter.
- The mass can be reduced to approx. 40% compared to a steel disk. Because of the significantly lower unsprung masses of the wheels, this means improved driving comfort and, at the same time, better grip, as the wheel can more easily follow the contour of the ground.
Since the C fibers are largely protected from oxidation by the SiC matrix and the period in which the brake discs can significantly exceed temperatures of over 500 ° C is limited to a few hours over the entire service life of a vehicle, oxidation of the material plays a role in this Application does not matter.
It remains to be seen whether the manufacturing costs for such windows can be reduced to such an extent that mid-range vehicles can also be equipped with them. The current status can be found on the providers' websites.
Applications in plain bearings
Conventional SSiC or the cheaper SiSiC has been used with great success in the plain bearings of pumps for over 20 years ( Lit .: WJ Bartz, 2003). The bearing uses the liquid delivered by the pump as a lubricant . The reason for the success of this bearing concept is the corrosion resistance to almost all media and the extremely low wear caused by the great hardness due to frictional loads or abrasive loads from particles, as well as the low coefficient of friction with liquid lubrication . The SiC components of the plain bearing consist of the so-called shaft protection sleeve, which is mounted on the shaft and rotates in the bearing bush. The SiC bearing bush is usually shrunk into its metallic environment and is under compressive stress . A brittle breakage of this component is therefore very unlikely. The SiC shaft protection sleeve does not have this advantage and is therefore usually designed with a large wall thickness and / or installed with special structural precautions. In the case of large pumps with correspondingly large shaft diameters (100 to 300 mm) as well as pumps with high bearing loads, the ceramic bearing concept could only be implemented with the use of composite ceramics due to the risk of failure of the protective shaft sleeve. On the test bench it could be shown that the bearing pairing of CVI-SiC / SiC and conventional SSiC can withstand almost three times the specific bearing load under mixed friction conditions as many other tested pairings. With specific load is the product of coefficient of friction (dimensionless), running speed (m / s) and bearing load (MPa or N / mm²) is meant; it indicates the power converted in the bearing gap in W / mm² and is often also given as a “P times V value”, omitting the coefficient of friction.
Boiler feed water pumps in power plants , with which several thousand m³ / h of hot water are pumped from 160 ° C to 20 bar pressure, or tubular casing pumps, with which several ten thousand m³ / h of lock water or sea water for desalination plants are pumped, have been the preferred applications for desalination plants since 1994 water-lubricated plain bearings with shaft protection sleeves made of CVI-SiC / SiC composite ceramics (picture at the beginning of this article).
The application of this type of plain bearing in turbo pumps, with which liquid oxygen (Liquid Oxygen = LOx, boiling point: −183 ° C) is conveyed in aerospace engines , is still being developed. The tests so far have shown:
- SiC and CVI-SiC / SiC are compatible with LOx and do not react with oxygen even under severe conditions (to determine the auto-ignition temperature, powder is heated to 525 ° C under 20 bar pure oxygen gas according to the French standard NF 29-763.).
- Frictional wear tests have shown a halved coefficient of friction and wear reduced to a hundredth compared to a standard metallic pairing .
- The LOx with lubrication hydrostatic designed bearings has a test a few hours at a speed of 10,000 min -1 with different bearing loads and 50 Start / Stop areas under mixed friction conditions survived practically wear-free.
The advantage of these ceramic bearings with composite ceramics compared to bearings with conventional ceramics is the greatly increased reliability. Damage to the protective shaft sleeve does not result in splintering into several larger and hard fragments with major consequential damage to the pump housing and wheel.
Other applications and development approaches
The following application and development examples can also be mentioned:
- Thrust control flaps in jet engines of combat aircraft , with which the jet cross-section is adapted to the engine power.
- CVI-SiC / SiC plates with a three-dimensional fiber structure as a lining for hot areas of fusion reactors . The three-dimensional fiber structure increases heat conduction perpendicular to the plane of the plate. Since crystalline SiC has proven to be a comparatively stable material in the environment exposed to neutron radiation, crystalline SiC fibers are also used here, the high-temperature stability of which is greatly improved compared to the amorphous.
- Thrusters ("fins"), flame holders and hot gas guide tubes in supersonic rockets, which have to guide and deflect extremely hot exhaust gases, in the case of solid fuels, also with particles, for a short time in a controlled manner.
- Brake pads for rapid braking of sledges in simulation systems for accidents in automobile traffic with the advantage of low wear and tear and very stable braking deceleration values even after several tests.
- High-temperature heat exchangers with the problems of hot gas corrosion , similar to those of gas turbines, and the necessary gas tightness.
- Rigid structures for precision mirrors.
- Cladding elements in the area of exhaust pipes from Formula 1 racing cars and washers for the heavily loaded clutches of these vehicles.
Industrial manufacturers in Europe
- WPX fiber ceramics: Oxidic fiber ceramic parts and components for industrial heat treatment and high temperature applications
- KLETKE Advanced Composites: Components made of C / C, C / C with SiC coating using C-CVI and LSI processes
- SGL Carbon : Brake discs (LSI process)
- Schunk Group : Axial bearings, radial bearings, sliding linings, furnace linings made of C / C material
- BJS Ceramics: aerospace components, plain bearing components (CVI process)
- Snecma : components for space travel, defense technology, brake discs (CVI process)
- Brembo : brake discs (LSI process)
- Pritzkow special ceramics: high temperature resistant components for industrial needs made of oxide composite ceramics
- CERAFIB GmbH: High temperature resistant filaments and materials
Research institutions in Germany
- University of Bremen : Department of Ceramic Materials and Components and Bioceramics
- University of Stuttgart : Institute for Manufacturing Technology of Ceramic Components (IFKB)
- University of Karlsruhe : Institute for Ceramics in Mechanical Engineering (IKM)
- Dresden : Fraunhofer Institute for Ceramic Technologies and Systems ( IKTS ), as well as the Institute for Lightweight Construction and Polymer Technology (ILK) at the TU Dresden
- University of Bayreuth : Chair of Ceramic Materials at the Institute for Materials Research (IMA)
- Institute for Textile Chemistry and Chemical Fibers (ITCF Denkendorf): fiber research and development
- DLR Institute for Building Methods and Construction Research: Development of tailor-made CMC materials, e.g. B. Thermal protection systems
- Fraunhofer Center for High-Temperature Lightweight Construction (HTL): Research and development of Ceramic Matrix Composites (CMC), ceramic fibers and high-performance ceramics
literature
- W. Krenkel (ed.): Ceramic composite materials . Wiley-VCH, Weinheim 2003. ISBN 3-527-30529-7
- J. Kriegesmann (Ed.): DKG - Technical Ceramic Materials . HvB-Verlag, Ellerau 2005. ISBN 978-3-938595-00-8
- WJ Bartz (Hrsg.): Ceramic bearings, materials - plain and roller bearings - seals . Handbook of Tribology and Lubrication Technology. Vol. 12. Expert Verlag, Renningen 2003. ISBN 3-8169-2050-0
References
- ↑ Narottam P. Bansal, Jacques Lamon: Ceramic Matrix Composites Materials, Modeling and Technology . John Wiley & Sons, 2014, ISBN 978-1-118-83289-9 , pp. XV ( limited preview in Google Book Search).
- ↑ M. Kunz, "Ceramic Matrix Composites" , cfi / report of the DKG, Volume 49, No. 1, 1992, p. 18
- ↑ M. Kunz: Crack resistance of ceramic fiber composite materials . Dissertation at the University of Karlsruhe, Shaker Verlag , Aachen, 1996.
- ↑ A. Mühlratzer, M. Leuchs: Applications of Non-Oxide CMCs , from: High Temperature Ceramic Matrix Composites , Ed. W. Krenkel et al., Wiley-VCH, Weinheim, 2001, ISBN 3-527-30320-0 , P. 288
- ^ H. Pfeiffer: Ceramic Body Flap for X-38 and CRV . 2nd International Symposium on Atmospheric Re-entry Vehicles and Systems, Arcachon, France, March 2001
- ^ H. Pfeiffer, K. Peetz: All-Ceramic Body Flap Qualified for Space Flight on the X-38 . 53rd International Astronautical Congress, Houston, Texas, USA, October 2002, Paper IAF-02-I.6.b.01
- ↑ H. Lange, M. Dogigli, M. Bickel: Ceramic Fasteners for High Temperature Applications . 5th International Conference on Joining: Ceramics, Glas and Metal, Jena, May 1997, DVS reports Volume 184, Deutscher Verlag für Schweißtechnik, p. 55, ISBN 3-87155-489-8
- ↑ M. Dogigli, H. Weihs, K. Wild Rotter, H. Lange: New High-Temperature Ceramic Bearing for Space Vehicles . 51st International Astronautical Congress, Rio de Janeiro, Brazil, October 2000, Paper IAF-00-I.3.04
- ↑ N. Miriyala, J. Kimmel, J. Price, H. Eaton, G. Linsey, E. Sun: The evaluation of CFCC liner After field testing in a gas turbine - III . ASME Turbo Expo Land, Sea & Air, Amsterdam, June 2002, Paper GT-2002-30585
- ^ KL More, PF Tortorelli, LR Walker, JB Kimmel, N. Miriyala, JR Price, HE Eaton, EY Sun, GD Linsey: Evaluating Environmental Barrier Coatings on Ceramic Matrix Composites After Engine and Laboratory Exposures . ASME Turbo Expo Land, Sea & Air, Amsterdam, June 2002, Paper GT-2002-30630
- ↑ WEC Pritzkow: Ceramic sheet, a material for the highest demands . cfi special edition for the DKG-DGM Symposium High Performance Ceramics 2005, W. Krenkel (Ed.), ISSN 0173-9913 , p. 40
- ^ WEC Pritzkow: Oxide-Fiber-Reinforced Ceramics . cfi / Ber. DKG 85 (2008) No. 12, p.E1
- ↑ a b K. Gaffal, A.-K. Usbeck, W. Prechtl: New materials enable innovative pump concepts for pumping feed water in boiler systems . VDI reports No. 1331, VDI-Verlag, Düsseldorf, 1997, p. 275
- ↑ W. Kochanowski, P. Tillack: New pump bearing materials prevent damage to tubular casing pumps . VDI reports No. 1421, VDI-Verlag, Düsseldorf, 1998, p. 227
- ↑ JL Bozet, M. Nelis, M. Leuchs, M. Bickel: Tribology in Liquid Oxygen of SiC / SiC Ceramic Matrix Composites in Connection with the Design of Hydrostatic Bearing . Proceedings of the 9th European Space Mechanisms & Tribology Symposium (ESMAT), Liège, Belgium, September 2001, ESA Document SP-480, p. 35
- ↑ M. Bickel, M. Leuchs, H. Lange, M. Nelis, JL Bozet: Ceramic Journal Bearings in Cryogenic Turbo-Pumps . 4th International Conference on Launcher Technology - Space Launcher Liquid Propulsion, Liège, Belgium, December 2002, Paper # 129
- ↑ P. Boullon, G. Habarou, PC Spriet, JL Lecordix, GC Ojard, GD Linsey, DT Feindel: Characterization and Nozzle Test Experience of a Self Sealing Ceramic Matrix Composite for Gas Turbine Applications , ASME Turbo Expo Land, Sea & Air, Amsterdam, June 2002, paper GT-2002-30458
- ↑ B. Riccardi, L. Giancarli, A. Hasegawa, Y. Katoh, A. Kohyama, RH Jones, LL Snead: Issues and Advances in SiC f / SiC Composite development for Fusion Reactors . Journal of Nuclear Materials, Vol. 329-333, 2004, p. 56
- ↑ a b c d W. Krenkel: Application potentials of fiber-reinforced C / C-SiC ceramics , in Lit .: W. Krenkel, 2003, p. 220