Valve control

A valve control system or a valve gear is a mechanism ( cam gear ), which in a reciprocating engine , the valves and thus the charge cycle controlled by opening and closing the air intake and exhaust gas discharge ducts.
It is used in almost all four-stroke engines - exceptions such as the slide engine are rare. In two-stroke engines , however, no valves are predominantly used, except for large two-stroke - marine diesel engines that have exhaust valves.
Typically, a valve is by a camshaft (engl. Camshaft ) via a tappet , rocker arms , or rocker arms open. The few exceptions are pneumatic , hydraulic or solenoid valves . Valves are closed by helical springs , rarely by torsion bar springs , gas springs or force-controlled ( desmodromic ) via a closing cam . In early high-revving four-stroke engines, hairpin springs were preferred, as the spring steels available at the time did not allow the manufacture of reliable coil springs. Hairpin springs could be used in pairs for safety, housed outside the cylinder head in the cooling air flow (Norton International and Manx) and, in the event of a break, could be easily exchanged without further assembly work. With the establishment of newer steel alloys, however, coil springs became widely accepted. Pneumatic closing mechanisms, which have a higher natural frequency and thus allow faster valve movements, have been used in high-revving Formula 1 racing engines since the 1990s. These springs require an air pump or - common in racing - a compressed air supply dimensioned for the duration of a race.
The camshaft is driven by the crankshaft , in four-stroke engines with a ratio of 2: 1, i.e. H. the camshaft has half the speed of the crankshaft.
During operation, valves are opened and closed several times every second - about once for marine diesel engines, but up to fifty times for racing engines - that is, they are accelerated and brought to a standstill again. The movements of the valves and the piston in the cylinder must be precisely coordinated.
Types
While the valves are predominantly constructed in a uniform manner, there are significant structural differences in the valve arrangement, valve actuation, camshaft arrangement and camshaft drive in common designs.
Basic types
A basic distinction is made according to the arrangement of the valves and camshafts in relation to the cylinder.



Sniffer valve, alternately controlled
In the first engines, only the exhaust valve was controlled, the intake valve was opened "automatically" by the negative pressure of the aspirating piston. The sniffer valve closes at the end of the intake stroke by a spring, the outlet valve was actuated by a cam via a tappet. Motors with sniffer valves can only achieve very low speeds due to their design. The Daimler riding car engine reached 700 rpm and the De Dion Bouton engine at the end of its development 1,500–1,800 rpm.
Inlet via outlet, counter-controlled (IOE)
When " Inlet over Exhaust " ( English Inlet over Exhaust ) "hang" the intake valve in the cylinder head and is plunger driven bumper and rocker arm from a bottom camshaft, the underlying standing arranged outlet valve via a tappet. IOE is also referred to as "against" or "alternately controlled". Early changeover engines had exposed rocker arms, so lubrication could be a problem. In the English-speaking world, IOE is also used to describe the sniffer valve that is above the outlet valve.
Vertical valves (SV)
Vertical valves are a simple design that is now almost only used in small engines in power generators and lawnmowers. The camshaft pushes the valves “standing” next to the cylinder into the cylinder head via tappets . The shape of the cylinder head is called "Flathead" in the Anglo-Saxon area and has been known since 1904. With the side valve, the cylinder head is just a simple cover. The cylinder block, on the other hand, is complex because, in addition to the cylinder bore, it also contains the gas channels and the valve guides. In early versions, the combustion chamber has an unfavorably large surface. The height of the combustion chamber is determined by the valve lift, the base area by the valve diameter, plus part of the piston area. Accordingly, this type of valve control is only suitable for low compression ratios . The advantages are the flat design of the engine and the simple casting of the cylinder head. Many engines get by without an oil pump because all moving parts can be lubricated by the oil mist in the crankcase. A special form of the side-controlled engine is the T-head engine , in which the inlet and outlet valves are mounted on the opposite side. This type of design with two camshafts below was widespread at the beginning of the 20th century for powerful engines (e.g. Mercedes , Laurin & Klement , Stutz , American LaFrance ), but is no longer relevant today.
Walking beam
In valve control with "walking beam", the camshaft located below actuates the valves located on the side of the cylinder head via long rocker arms. The combustion chamber is cuboid, narrow and high, with rounded corners at the top. This valve control was invented around 1900. The best known are the marine, aircraft and vehicle engines developed by Fred S. and August S. Duesenberg , which were manufactured between 1910 and 1918 by the Duesenberg Motors Corporation . Passenger car engines were manufactured by Rochester-Duesenberg until 1923 and aircraft engines by Lycoming until the late 1930s . "Walking Beam" is the English name for balancer .
Overhead Valves (OHV)
When OHV valve control ( English overhead Valves ) "hang" all valves in the cylinder head, the camshaft is located in the crankcase, in V engines on the crankshaft. One also speaks of a “camshaft below”. The valves are operated via tappets, push rods and rocker arms. The combustion chamber can be shaped favorably. This construction was common at the beginning of mass motorization and is still common, from Harley-Davidson to VW Beetle to the current Corvette . The pipe engine from 1905 is considered to be one of the first OHV engines.
Overhead camshaft (OHC)
With the OHC valve control ( English Over Head Camshaft , also SOHC - Single Over Head Camshaft ), the camshaft is located in the cylinder head and is driven either by a series of gear wheels, a vertical shaft , push rods, a chain or a toothed belt. In 1908, Clément-Bayard introduced an early OHC valve control on his racing engine. The valves are operated via bucket tappets, rocker arms or rocker arms. The rotating drive between the crankshaft and cylinder head reduces inertia and enables higher speeds. This type of construction is the most common, the variations are many. CIH ( Camshaft In Head ) is an OHC variant in which the camshaft is located on the side of the cylinder head; Rocker arms are required.
Dual overhead camshafts (DOHC)
With Double Overhead Camshaft (DOHC) there are two camshafts in the cylinder head, one of which actuates the intake valves and the other actuates the exhaust valves. The first engine with two overhead camshafts was the racing engine from Peugeot from 1912. The moving masses are even lower and thus even higher speeds are possible, but also less wear and tear with a well-designed combustion chamber, and the placement of spark plugs is unproblematic. In the DOHC engine, the valves are now operated with bucket tappets . Modern racing engines and motorcycle engines are exclusively equipped with DOHC valve trains. DOHC does not automatically mean four valves per combustion chamber; In principle, two valves per combustion chamber can also be actuated with the DOHC valve control (see Kawasaki Z1 ).
Valve arrangement
Depending on the arrangement of the valves, a distinction is made between parallel, V-shaped and radial:
Parallel valves
In an overhead camshaft, the hanging parallel (in a row) valves via tappets or cam followers actuated at CIH motors via tappet and rocker arm, with a bottom camshaft via tappet rods and rocker arms.
V-shaped arrangement
In this valve arrangement, the overhanging each other at an angle in the cylinder head valves form a V . Compared to a cylinder head with valves hanging in parallel, this results in a more favorable combustion chamber shape and larger valve diameters can be used. With this valve arrangement, the inlet and outlet are usually opposite each other in a cross-flow cylinder head or the inlet is "up" at the angle of the "V", for example in the engine of the BMW 328 , Peugeot or the twelve-cylinder engines from Lamborghini of the 1960s.
This arrangement can be used for both two-valve and multi-valve engines; Such a cylinder head is preferably built as a four- or five-valve (three inlet valves) with liquid cooling because of the two adjacent outlet channels, since a considerable amount of heat has to be dissipated locally there. Nonetheless, the engines of this type used by Honda and MV Agusta in motorcycle racing in the 1960s and 1970s were air-cooled throughout, and numerous series engines such as the Suzuki GSX series of that time were also air-cooled.
With two overhead camshafts, the valves are usually operated directly via bucket tappets, more rarely via short rocker arms. With an overhead camshaft in the middle, the easiest way is to use rocker arms. At the British manufacturers Triumph and Rover, the intake valves were operated via bucket tappets and the exhaust valves via rocker arms. In the two-valve versions of the Alfa Romeo Arese V6, the intake valves were operated via bucket tappets, the exhaust valves via horizontal bucket tappets, short horizontal bumpers and L-shaped rocker arms above the valves.
The advantages of this valve arrangement were also used in engines with camshafts installed below or centrally (V and boxer engines) with bumpers and the more complex valve train was accepted. The boxer engines from BMW and Citroën have, similar to the V-engines of the 1950s from Lancia, inclined rocker arms, i.e. rocker arms with laterally offset lever arms. The “Vs” of the valves and the crankshaft lie in parallel planes, which means that the inlets and outlets of the cylinders are not on the side, but in the front and back. In Puch boxer engines, Peugeot and Chrysler Hemi engines , the bumpers are inclined and meet rocker arms lying opposite one another as an extension of the cylinder axis. The plane of the "Vs" is perpendicular to the crankshaft. Fiat engines (in 1800 and 1500 ff.) Have a similar arrangement of the rocker arms , but the “V” is tilted towards the inlet side. Therefore, the bumpers are steep, as in engines with valves hanging in parallel, and that's how the engine block was originally designed. In the BMW 328, the inlets are operated by simple rocker arms and the outlets by two L-shaped rocker arms connected by horizontal bumpers. Here, too, the engine block with side camshaft, tappets and push rods was intended for a cylinder head with rocker arms and parallel hanging valves.
The first engine with valves in a V-arrangement in a car was in 1903 that of the “Premier Special” racing car with a king-shaft driven overhead camshaft and rocker arms.
Radial arrangement
In this valve arrangement for a four-valve engine, the valves on the inlet and outlet side are not each parallel to each other, but the valves with the same function are arranged at an angle to each other so that the valve plates do not form a roof-shaped combustion chamber (as in the case of V-shaped hanging valves ), but an almost hemispherical combustion chamber. Due to the possibility of arranging an additional coolant channel at this angle between the outlet valves, the cylinder head can withstand higher thermal loads in this design. In addition, the valve openings with this valve arrangement can be larger than with a cylinder head with valves suspended in parallel. The valves hanging at an angle to each other are either actuated by a camshaft with conically ground cams or a two-part camshaft with a bevel gear set in the middle (Grand Prix racing motorcycle BSA 250). Alternatively, rocker arms arranged at an angle are also used; direct actuation requires a camshaft each for intake and exhaust valves (DOHC). A camshaft (e.g. Honda Radial Four Valve Combustion Chamber) is sufficient for valve actuation via rocker arms. The pioneer of this design was the British motorcycle manufacturer Rudge, who was already using engines with fully radial (all valves are radial to the combustion chamber) and semi-radial (parallel hanging inlet valves, radially arranged exhaust valves) in the 1920s (which is why evil tongues claim that the abbreviation RFVC at Honda do not stand for Radial Four Valve Combustion Chamber, but for Rudge Four Valve Copy). Further examples: Rolls-Royce Condor, Honda XR 500 R, Honda XL 600, current engines from MV Agusta
A special form of this valve arrangement is the radial-diametral four-valve valve from Ludwig Apfelbeck .
Opposite valves (T-head)
The T-head engine is an early variant of the side-controlled engine, in which intake and exhaust valves are mounted on opposite sides of the cylinder. Each side usually has its own camshaft housed in the crankshaft housing. T-head engines were designed for high performance and were used in early sports and racing cars (including Mercedes , Panhard & Levassor , Hotchkiss , Delahaye , Chadwick , Packard , Mercer ) as well as in commercial vehicles. The fire engine manufacturer American LaFrance used them until 1950. The Pierce motorcycle from 1907–1913 had a four-cylinder T-head engine.
Valve actuation
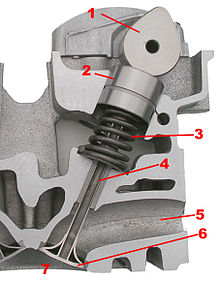
1. Camshaft cams
2. Bucket tappets
3. Valve spring
4. Valve stem
5. Gas duct to inlet (fresh gas) or outlet (exhaust gas)
6. Valve disk that seals the combustion chamber (7) against the valve seat ring
7. Combustion chamber
A distinction is made according to the type of valve control:
- Bucket tappets - here the cam actuates a cup-shaped hollow cylinder which - apart from play compensation elements - presses directly on the valve stem. The distance between the cam and valve is the smallest with this type of construction, and there is no force deflection by rocker arms or rocker arms, making this type of construction light, very stiff and therefore suitable for the highest speeds. This type of actuation also offers the lowest overall height of the valve control. For the possibilities of valve clearance adjustment and automatic clearance compensation see under bucket tappets.
- Rocker arm / rocker arm - between the cam and valve there is a lever that is mounted on its own axis or a ball pin. Advantage: The valve clearance can be easily adjusted.
- Rocker arm The rocker arm has two arms. The tilt axis is located between the camshaft on one side and the valve on the other. The valve clearance can be adjusted using a screw with a lock nut on the valve side of the rocker arm or can be adjusted using the rocker arm mounting by shifting the pivot point, i.e. the tilt axis, or rotating it with an eccentric . In addition to the valve clearance, the length of the lever arm also changes, which changes the valve stroke somewhat ( lever law ).
Opel CIH engines and CVH engines from Ford are equipped with a hydraulic tappet between the cam and the rocker arm for valve clearance compensation. Normally the camshaft actuates a rigid tappet and the valve clearance is adjusted using a screw on the rocker arm. V-shaped hanging valves can also be controlled with just one camshaft; the rocker arms are then usually arranged opposite one another and not mounted on a common axis (exception: PRV and Douvrin motors).
- Desmodromic, which is used, for example, on Ducati motorcycles, is a forced control without valve springs. Instead, the valves, which are opened via rocker arms, are closed via an additional closing cam on the camshaft and a closing lever. This type of construction runs particularly smoothly, as no additional spring force has to be overcome by the camshaft. The system is thus suitable for high speeds. However, the valve clearance must be set separately for opening and closing. Newer designs have a double hydraulic valve clearance compensation. A weak additional valve spring for closing allows the engine to be started; without it, compression would not be possible when the engine is cold. With positive desmodromic valve actuation, the same cam (double contour cam) is used for opening and closing.
- Variable valve control. In the meantime, there are designs with which the valve lift and opening duration can be changed during operation. Motors with variable valve control do not need a throttle valve in normal operation and are more efficient. In the Valvetronic made by BMW, the cam acts on the rocker arm of the valve via an intermediate lever with variable lever arms. In the Multiair system from Fiat and Schaeffler, there is a hydraulic system between the cam and valve that can be used to reduce valve lift and opening times.
Selection criteria
The selection of the valve train by the designer depends on various criteria:
- Number of valves to be operated: If you want to equip a four-valve engine with only one camshaft, not all valves can be operated directly via bucket tappets, which is why two camshafts are often used. This also applies accordingly to five-valve engines with two camshafts.
- Position of the spark plugs and injectors in the cylinder head
- Maximum engine speed: approx. 65–150 / min for marine diesel engines (low-speed engines), approx. 3500 / min for truck diesels, approx. 6000–8000 / min for car gasoline engines, up to 17,000 / min for motorcycle engines , up to 20,000 / min for Formula -1- and four-stroke motorcycle racing engines.
Camshaft drive
There are various options for transmitting the rotational movement from the crankshaft to the (overhead) camshaft. Widespread are:
Other options are
- Spur gears or
- (especially on older motorcycles) the bevel shaft
- and very rarely the drive with a pair of push rods . This type of drive assumes that the camshaft is arranged parallel to the crankshaft, which is the prevailing design.
As a matter of principle, the camshaft of a four-stroke engine always rotates at half the crankshaft speed - apart from four-stroke radial engines , see there for details.
In order to reduce fuel consumption, automobile manufacturers are increasingly using camshaft adjustment . Here, the timing of the intake valves is changed as a function of the engine speed by adjusting the camshaft, and in some cases also of the exhaust valves. In this way, the filling of the cylinder and thus the efficiency of the engine can be improved over a broader speed range. If the valve lift can also be adapted to the engine load, the throttle valve becomes superfluous, as in the Valvetronic from BMW or MultiAir from FIAT.
In radial engines, the control shafts are called "cam drum", "cam ring" or "cam disk" due to their different shape. They usually run coaxially with the crankshaft, so that only gears can be used as drives.
Usually, the cams are arranged on a camshaft in such a way that the tappet moves radially to the rotating shaft; the cam contours run mostly parallel to the shaft, the plunger is perpendicular to it. Of Ludwig apple Beck , however, motors have been designed with tapered cam in which the follower can assume other angles to the camshaft. In some sports motorcycle engines, conically ground cams are used.
Designs with axial valve timing movement in the direction of the camshafts are rare, for example in some of the British Chater Lea motorcycles and in designs by Richard Küchen . The cams operate rotatably mounted levers.
In principle, a rotating camshaft is not necessary for valve control - the time-controlled actuation of tappets is also possible with camshafts that only rotate back and forth by less than a full revolution, or with translatory “cam tracks”. However, such a construction has not yet been used in the series. Valves can also be operated hydraulically, pneumatically or electromagnetically. High-revving Formula 1 racing engines rely on mechanical actuation via a tappet in combination with a pneumatic locking device, which allows very high speeds due to its high natural frequency. The free-valve technology used by the Swedish car manufacturer Koenigsegg controls the valves using pneumatic-hydraulic-electric actuators. By dispensing with the camshaft and toothed belt, there is less friction, which enables higher engine performance with lower consumption.
Valve
To control the gas exchange in the internal combustion engine, poppet lift valves are used almost exclusively in four-stroke engines and partially in two-stroke engines . The valve consists of the valve disk which , when closed, seals the inlet or outlet channel against the suitably ground or turned valve seat in the cylinder head. The valve disk merges into the valve stem in a parabolic shape in order to offer the least possible resistance to the gases flowing past. The valve stem is a long, thin cylinder that is firmly attached to the poppet. Valve stem and disk are mostly separately manufactured components for cost reasons, which are then connected to one another using the friction welding process. With highly stressed engines, this creates a source of defects at the connection point, which can lead to serious engine damage if the valve disc is torn off. These are nowadays avoided in racing engines by means of one-piece manufactured valves made of high-temperature steel (e.g. Nimonic).
Tasks, stresses and construction
Valves are thermally and mechanically highly stressed components that are also exposed to corrosive influences. The mechanical stresses arise as a result of deflection of the valve disk under ignition pressure, as a result of hard contact when closing (impact) and through inertia forces as a result of high accelerations. These tensions can be influenced by the corresponding thickness and shape of the plate.
The valves with a large surface area absorb heat from the combustion chamber. The outlet valve is also heated on the top by the hot exhaust gases flowing out during opening. In the valve, the heat mainly flows to the valve seat, a smaller part via the shaft to the valve guide. Inlet valves reach temperatures of 300 ° C to 500 ° C, outlet valves 600 ° C to 800 ° C. If the seal on the valve seat is not perfect during the combustion phase, local overheating and melting occur, which lead to failure of the valve.
In order to improve the heat conduction through the shaft, it is made hollow and filled with sodium (sodium cooling) for particularly high requirements. The movements of the sodium, which is liquid at temperatures above 97.5 ° C, increase the heat transport. In this way, the valve temperatures can be reduced by up to 100 ° C. The liquid inside the valve also leads to vibration damping. The hollow valve stem of sodium-filled valves is a weak point in these designs under extreme loads. The steels available today that can withstand high thermal loads make it possible to dispense with the use of a sodium filling and to use one-piece valves without a predetermined breaking point.
To reduce wear, the seat can be armored by welding on stellite - a special hard metal alloy.
The material of the valve must have high heat resistance and scale resistance. Special RSH steels have been developed for this. A typical designation is X15NiCr25.20 (material no. 1.4841) (or material no. 1.4541 (X6CrNiTi18-10)). In addition to steel, high-speed engines sometimes use lighter titanium alloys. Mario Illien first used beryllium as an alloy additive in valve materials in the Ilmor engines that he developed for Mercedes' Formula 1 vehicles .
material | Density (g / cm³) | Melting point (° C) | Thermal conductivity (W / (m K)) | Mohs hardness |
---|---|---|---|---|
Valve steel (RSH steel) | 7.80 | 1538 | 14.5 | 4.0 |
titanium | 4.50 | 1668 | 22nd | 6.0 |
Beryllium (alloy additive) | 1.84 | 1287 | 190 | 5.5 |
Tungsten (alloy additive) | 19.30 | 3422 | 170 | 7.5 |
Valve seat inserts are often built into the cylinder heads for reasons of wear. In the course of further technical development, ever increasing demands are placed on them in terms of design, material, precision and performance stability.
Among other things, the valve seat rings in the inlet and outlet area for large diesel engines (drive units for ships and stationary power generators) are manufactured using the centrifugal casting process. The materials used for this (nickel-based alloys, heat-resistant ferritic steels and application-specific materials) not only offer good temperature resistance up to 400 ° C, but also high wear and corrosion resistance when using different fuels such as heavy oil, diesel, sulfur-free fuels and Gas.
A seat ring must always be provided for light metal cylinder heads (alloy centrifugal casting, in special cases also cast iron with a coefficient of thermal expansion equal to that of light metal). In highly stressed engines, seat rings made of alloyed centrifugal cast are also used for gray cast iron cylinder heads, especially for the exhaust valves. The valve seat inserts are pressed in or shrunk. By combining suitable materials, contact welding between the valve head and the valve seat insert is avoided, thus preventing seizure damage. First valve seat rings were only in gas engines used and engines with aluminum cylinder head, as in gasoline engines by only used until the 1980s, leaded petrol a protective layer between the valve head and cylinder head formed and thus prevented the contact welding. In diesel engines , the soot takes on this task. The use of twisting devices also prevents valve plates from sticking in their seats.
The plate of the intake valve usually has a larger diameter than that of the exhaust valve, since in this way the power output is highest for a given combustion chamber diameter. In turn, the shaft of the exhaust valve is thicker in order to promote heat transport. The heat is passed on to the valve guide and from there to the cylinder head, which is usually cooled by cooling water and rarely by air.
Valve actuation
Direct actuation
With direct actuation, the valve is opened directly by the overhead camshaft and closed by the valve spring. Their power is transmitted via the spring plate , which is held in place by two valve wedges that engage in an annular groove on the upper valve stem. A bucket tappet, on which the cam slides during actuation, is arranged as a transmission element between the cam and the valve stem. The tappet must keep the resulting transverse forces away from the valve stem. The tappet diameter is determined by the maximum tappet speed, the cam width is determined by the surface pressure between the camshaft and the tappet. Since cams and tappets have to slide on each other under high surface pressure, the material pairing is important. Hardened steel and gray cast iron work well. To avoid uneven wear, the tappet is often allowed to rotate around its axis. To do this, it is offset laterally by 1 to 4 mm towards the center of the cam. In addition to rigid tappets, in which the valve clearance can be adjusted by inserting small plates of different thicknesses (1/10 mm increments) or changes to the valve or valve seat, there are also tappets with automatic clearance adjustment, so-called hydraulic tappets .
Actuation via lever
Rocker arms are a relic of the engines with a camshaft below, here they were driven by bumpers as a transmission link. With an overhead camshaft, they are used when the valves are arranged in a V-shape in the combustion chamber. In the course of the current measures to improve the mechanical efficiency, rocker arms are often used again in DOHC engines, in which the camshaft runs on a roller. This significantly reduces the friction compared to the use of bucket tappets. There is a high bearing force at the pivot point of the rocker arm, so that the bearing must be designed to be particularly rigid. For the rocker arm ratio i = l 2 / l 1 , values between 1 and 1.3 are generally aimed for as a compromise between low surface pressure on the tappet, low moving mass and high rigidity. The force of the rocker arm should be transmitted as axially as possible to the valve stem in order to avoid a lateral force on the valve stem. Rocker arms are mostly cast or forged. Cheap variants consist of deep-drawn sheet metal, but these are less rigid. It is advantageous to adjust the valve clearance on the stationary lever mounting, but in the case of forged levers the adjusting screw is normally located opposite one another, which increases the moving mass of the valve drive. Rocker arms (or: rocker arms) are much less stressed than rocker arms. Changes in the support point have less influence on the kinematics. In the case of rocker arms, the installation of hydraulic valve clearance compensation in the lever bearing is a very clever design solution that takes up little space, changes the overall elasticity only slightly and is therefore often preferred to other solutions.
Valve clearance
Metal that is heated during operation expands so that the valve becomes longer. As a result, it can happen that it no longer closes completely. Even if the valve seat wears faster than the cam, the valve can no longer close completely.
Then there is a risk of burning the valve seat and the valve disk, since the hot combustion gases flow past the valve that is not fully closed and it can hardly dissipate any heat to the cylinder head. Because of the gases flowing through, there is also a loss of power, since the part of the combustion gases that escapes past the valve does not transfer its energy to the piston.
To ensure that the valve closes safely under all operating conditions, a valve clearance is provided - a small gap somewhere in the valve train. This distance decreases when the operating temperature is reached, but must not be zero. Too much play in turn causes a loss of power, loud noise and increased wear on the valve train.
The manufacturers therefore specify a range for the valve clearance, on the order of a few hundredths to tenths of a millimeter, mostly based on the cold engine. The valve clearance should be checked and, if necessary, readjusted at regular maintenance intervals (based on mileage, sometimes also operating hours) if the engine does not have an automatic valve clearance compensation.
The play is usually measured with feeler gauges and then set differently depending on the design: With rocker arms that are operated by bumpers, there is often a locked screw in the levers, on which the setting can be made. In other constructions, the pivot point of the lever is adjusted. Bucket tappets, on the other hand, have hardened insert plates (“shims”), which are placed between the tappet and cams or the tappet and valve stem. These are available in fine gradations of thickness and are replaced if necessary.
Many newer engines have hydraulic valve lifters that no longer require valve clearance. Regular maintenance is then not necessary, but the hydraulic valve lifters themselves wear out and may cause rattling and loss of performance after a long period of operation. Hydraulic valve clearance adjustments can also be constructed within levers or to raise the lever pivot point ("hydrolifter").
literature
- Mahle GmbH (publisher): Ventiltrieb: Systems and Components (ATZ / MTZ book) . Springer Vieweg, 2012, ISBN 978-3-8348-2490-5 , p. 323 .
- Hans-Hermann Braess, Ulrich Seiffert: Vieweg manual automotive technology. Friedrich Vieweg & Sohn, Braunschweig / Wiesbaden 2001 (2nd edition), ISBN 3-528-13114-4 .
- Hans Jörg Leyhausen: The master craftsman's examination in the automotive trade part 1. Vogel, Würzburg 1991 (12th edition), ISBN 3-8023-0857-3 .
- Wilfried Staudt: Handbook of Vehicle Technology Volume 2. Bildungsverlag EINS, Troisdorf 2005, ISBN 3-427-04522-6 .
- Max Bohner, Richard Fischer, Rolf Gscheidle: Expertise in automotive technology. Europa-Lehrmittel, Haan-Gruiten 2001 (27th edition), ISBN 3-8085-2067-1 .
Individual evidence
- ↑ a b c Ludwig Apfelbeck: Ways to the high-performance four-stroke engine. Motorbuch Verlag, Stuttgart 1978, ISBN 3-87943-578-2 , p. 11.
- ↑ “Duesenberg walking beam engine” | Search Results | The Old Motor. Retrieved March 17, 2019 .
- ↑ Ludwig Apfelbeck: Paths to the high-performance four-stroke engine. Motorbuch Verlag, Stuttgart 1978, ISBN 3-87943-578-2 , p. 12.
- ^ Paul Niedermeyer: Museum Classic / Automotive History: 1903 Premier - The First OHC Hemi Head Automobile Engine And The Search For The Hemi's True Father. Retrieved March 17, 2019 (American English).
- ↑ Motor Talk - Koenigsegg: The future of the internal combustion engine - the end of camshafts, toothed belts and timing chains. February 26, 2013, accessed October 16, 2018 .
- ^ Franz Pischinger: Internal combustion engines. Lecture reprint Volume I; RWTH Aachen 1987.
- ↑ Elvira Moeller: Handbook of construction materials: selection, properties, application . Carl Hanser Verlag GmbH & Co. KG, 2007, ISBN 978-3-446-40170-9 , p. 337 .