Switch (train)
A Soft outdated, and mining also change or - as opposed to the air switch - sometimes track crossover called one is track design of a train , the rail cars makes the transition from one track to another without stopping. In contrast to transfer platforms or turntables , no interruption in travel is necessary.
history

The development of the turnouts began in coal mining. With the first cast-iron angle rail turnouts by John Curr from 1776, humans or animals had to pull the hunt in the desired direction. In 1797 John Curr first describes a construction with an adjustable tongue. A patent for a railway switch by Charles Fox (1810–1874 in England ) is mentioned for the first time in 1832 . The type by Richard Trevithick shown in the picture on the right is still intended for rimless wheels, but anticipates all the later elements of a switch.
Before it was used in the railway sector, the German term “ switch” was used to describe a passing point in shipping.
Different designs have emerged for different situations and purposes. The design most frequently used today, the tongue switch , is said to have replaced the tow switch in Germany for the first time on the Hanover State Railway in 1852 .
Each railway administration initially used its own switch designs. Even after the formation of the regional railway administrations in Germany, it stayed that way. After the establishment of the Deutsche Reichsbahn in 1920, there was an urgent need for action to reduce the number of different and non-interchangeable parts. In addition, the geometric properties of the turnouts should be standardized in order to avoid costly adjustment work. After the S 49 rail profile, which was new at the time, was introduced in 1922, it was also to be used for turnouts of the standard design. In 1931 the Reichsbahn turnouts were introduced as standard designs with largely the same features. The connection dimensions for switch locks, adjusting devices and additional devices have also been standardized. In the following years these types were improved; hook point locks and hinged tongues were no longer required in new buildings.
Until the 1980s, points in Germany were typically passable at 40 to 100 km / h in the branching line. With the increase in line speed on the new German railway lines (built from 1973 and commissioned from 1987) , the speed reductions in the branching line of turnouts became increasingly important. As early as the 1960s, a type of switch ( EW 60-2500-1: 26.5-fb ) that was passable at 130 km / h in the junction was developed for the new construction of the Ludwigshafen railway station , which was then also installed in the branch points and transfer points of the new lines . In addition, from 1984 in Germany, high-speed turnouts were developed for junction points , which could be passed at 160 or 200 km / h in the junction. Today they are used at a number of junction points on high-speed routes. When they were introduced at the end of the 1980s, the 200 km / h turnouts were considered to be the longest units that could still be produced using manufacturing technology.
At the end of 2019, 65,639 points were in operation in the Deutsche Bahn network , with a downward trend. In 2015, 71,441 switches were in operation on the Deutsche Bahn network, 720 of them high-speed switches. 48,000 points had point heating and 8,500 points had a locking cover. At the end of 2015, the company planned to equip a further 26,000 turnouts with systems for forecasting the availability of turnouts by 2018, and by 2020 all “essential” turnouts (30,000) should be equipped with them. This is intended to reduce the number of faults by up to 50 percent. The first 5,000 points should be equipped by the end of 2016. Deutsche Bahn spends 30 million euros annually on switch components.
The required availability of points in terms of control and safety technology at Deutsche Bahn today corresponds to an average operating time between two failures of 143,000 hours, with an average failure time of two hours.
Control of points

A distinction is first made between locally set and remote turnouts.
Placed on site
Locally set points are often mechanically locally set points, also known as "manual points" and abbreviated to MOW in Germany, in which the changeover is carried out by the operator's muscular strength on the switching lever and is transmitted via the trestle to the tongue connecting rod, the tongue device and, if applicable, the point lock . The weight or a lock of the switching lever holds the switch in the respective end position.
In Switzerland there is a different design for manual switches that are used in intensive shunting operations: Instead of the usual hand weight, there is a bracket on which a linkage switch lever used in mechanical interlockings stands. It is connected to the slide rod via an angle lever. It is advantageous that an operator does not have to bend down low and lift a heavy hand weight. In Great Britain and countries with comparable railway safety technology, it is the rule that points not set by signal boxes are operated via switch levers set up nearby on so-called "ground frames".
Meanwhile, there are also more and more electrically localized points (EOW).
Remote control
Remote turnouts are usually operated by an interlocking and secured by means of railway signals . They are passive guideway elements that are adjusted by external forces and whose correct position is monitored by the interlocking. Track vacancy detection systems are used in modern interlockings to monitor track occupancy by vehicles ; where these are not available, the freedom must be determined by looking, since occupied points must not be changed.
Control of trams

In classic tram networks, there is usually a point control operated by the railcar driver or the vehicle's on-board computer or the operations control system. Normally, the turnout is switched automatically based on the line or course number set on the on-board computer. As a rule, the driver also has the option of manually specifying a different direction of travel, for example in order to be able to drive an alternative route in the event of operational disruptions. In the event of a malfunction or when shunting, the points can also be switched manually using a point iron carried in or on the railcar . Tram switches that are only used bluntly in regular operation can usually be driven on. The switch tongues are pushed into the required position by the wheels of the vehicle when they are driven on and maintain this position after driving on.
Until the mid-1990s, it was common practice to switch points using the overhead line voltage. The point machines consisted of a pull coil ("solenoid") with a movable armature and a spring, which created a tilting behavior via levers. In addition to the contact wire, an insulated and slightly lower hanging sliding contact was installed in front of the respective switch. The pulling magnet of the point machine was between the contact wire and the sliding contact. If the sliding contact was driven with a defined current consumption, the first speed level was common, the overhead current flowed from the contact line via the pull magnet of the switch drive to the contact line contact and from there via the travel switch, resistors and traction motors to the track. The pull magnet attracted the armature, due to the inertia and supported by the retaining spring, the drive ran into the other end position. If the switch should not be changed, the contact with the travel switch was set to zero. In some cities, the turnouts also had preferred positions, for example in the right position there was always no current and in the left position with current flow. The process became problematic due to additional consumers such as lights, heating, converters, air conditioning or braking current recovery . The current flowing through it could be enough to switch a switch. Initially, the railcar drivers had to switch off the auxiliary consumers individually, later contactors were installed for this. Instead of the first driving contact of the driving switch, a defined resistance was switched on between the pantograph and the track.
If a vehicle had to start up in the area of a contact line contact, it was unavoidable that the associated switch would switch. The use of pre-sorting switches was then necessary here. Several railcars on the train with pantographs attached exacerbated the problem and ultimately led to the ban on upstream-dependent switch switching.
Since 1996, because of its susceptibility to errors, point control in Germany has no longer been allowed to depend on the power consumption of the wagon. Modern controls work with inductive message transmission , radio or infrared control. Point machines for use in road areas are usually located in the track, occasionally next to it, but always with a drivable cover at road level. The travel distances and tongue surcharges are significantly smaller compared to long-distance railway conditions, so that the road surface remains safe to drive and walk on.
The point control is sometimes carried out on independent railway bodies; in urban and underground railway networks it is generally comparable to railway networks of signal boxes with route protection. Turnout drives and locks then usually correspond to the designs customary on railways.
Components of a switch
A switch is composed of special rail parts. In the following, the switch is viewed from the top, i.e. before the rails are split. The turnout shown in the picture is described with the branch to the right.
Tongue device
Tongues and stock rails form the tongue device , a stock rail and the associated tongue is called a half tongue device . Both parts belong together and must be changed at the same time.
The rails on which the switch blades rest, called stock rails (in Switzerland Stock rail). The stock rails are machined on the inside of the rail head so that the tongues fit neatly and do not become too thin and therefore sensitive, especially at the tip. For safe guidance and the least possible jerk-free deflection of the vehicles, the tip of the tongue engages under the running edge of the stock rail.
The switch tongues are the moving parts of a switch that determine the direction of travel. In many countries, including in German-speaking countries, the switch blades are made from special asymmetrical and height-reduced switch rail profiles. In this case, the tongue is guided and supported with sliding chair plates for the correct height . In turnouts developed in France, full-height standard rails were used as the starting material for the tongues, which is why the stock rails also have to be processed in the foot area.
There are several options for designing the tongue pivot:
- Joint tongues
- (Gz) are the oldest form. These can be kept relatively short, but the tongue joint is complex and nevertheless prone to wear. Advantages of the joint tongues are that they are tension-free and their resistance to change is low. In the field of trams , this type of turnout is still often referred to today (2016) under the term "swivel chair turnout", i. that is, the joint was considered a "swivel chair". Such a designation also existed on the railway side, where it has disappeared from technical parlance.
- Spring tongues
- (Fz) avoid the hinge, the spring point lies in the tongue profile and is supported by a tongue plate over several thresholds. However, this tongue plate makes it difficult to bend the turnout into a curved turnout. The end of the tongue is forged in the die to form the standard rail, the connection to the intermediate rail is made by a standard joint, which can also be welded.
- Spring rail tongues
- (Fsch) manage without a tongue plate. The tongue rail is also forged at its end to form the standard rail and butt welded together with another standard rail profile. This welding point is reinforced with safety straps to protect against breaks. The spring point is in the standard rail profile; for turnouts with a curve radius of 190 meters and below (in the past also with radii of 300 and 500 meters), the rail foot is milled off on both sides to about the width of the head in order to reduce the preload. The common advantage of spring and spring rail tongues is the running edge without interruption by the joint. Their disadvantages are the pretensioning, the significantly greater length required as a result, and the greater effort required when moving. Spring rail tongues are the standard design for the Reichsbahn turnouts introduced in 1931 and standardized from the start and their successors.
- Spring tongues without tongue plate
- (also Fz) are the latest development. The spring point is again in the tongue profile, there is no tongue plate or a welding point in moving parts, there are no hindrances when bending and tamping work. Spring tongues without tongue plates are used for turnouts made of the rail profiles S54 and UIC60, and since 2008 also S49.
When driving straight ahead, the right tongue rests on the right stock rail that branches off to the right. The tongue is straight. The left tongue has a distance (called the tongue impact ) to the left stock rail, which leads straight ahead. In this position, the right tongue, together with the left stock rail, guides a vehicle straight ahead.
If the direction of travel is to the right, the left tongue rests against the left stock rail. The left tongue curves to the right. The right tongue is removed from the right stock rail. A vehicle is guided to the right by the left tongue and right stock rail.
The switch can be adjusted by moving the switch blades. The moving part of the switch tongues rests on sliding chair plates. Because of the high maintenance costs and because the introduction of lubricant into the bedding causes environmental problems and impairs the positional security of the switch, low-maintenance tongue rolling devices of various types or plastic plates made of highly sliding material are increasingly being installed today .
The term FAKOP refers to a running edge optimization on the switch device.
WITEC referred wi rtschaftlich- tec hnisch optimized switching devices. In the case of a WITEC switch device, the contact surface of the stock rail on the running edge is planed deeper in order to increase the cross-section of the switch and thus the wear reserve. This extends the length of stay.
Centerpiece
The frog is an element in turnout construction and is a summary term for the frog tip and the two wing rails. Two tracks are combined or separated at a switch . The inner strands of the tracks intersect and have to be interrupted so that the flange of a wheel that is traveling on the other rail can pass through unimpaired. This point is called the heart. The wing rails are bent at the ends, the so-called knees. The tip of the frog wedge is rounded. Therefore this does not coincide with the intersection of the driving edges. In the case of straight frogs, the running edges of the frog usually run in a straight line. The angle they form to one another is called the inclination. If a track curve joins the branch track in the same direction, then the interruption of this curve in the focal area is disadvantageous for smoothness and wear. In this case, the arch is therefore also carried out in the frog area using an arch frog . The end slope is greater in this case than with a switch with the same radius and straight frog.
Since there is a gap in the driving surface and a guideless point when driving on the frog, the wheel set is guided by a wheel guide on the opposite rail. The interruption in the driving surface always leads to bumps. To counteract these impacts, slim turnouts on high-speed routes are equipped with movable frog tips or wing rails. At an intersection there are accordingly four frogs (those at the crossing points of the outer rails have two opposite points and are therefore called double frogs).
The most severe signs of wear and tear occur at the core. In the future, highly stressed points will therefore be equipped with frogs made of bainite , a special structure of steel. These are characterized by a service life that is twice as long and therefore reduce maintenance costs.
Handlebars
Since the wheel rolls over a gap in the rail in the area of the frog (except for movable frogs) and therefore no longer has any lateral guidance, the wheelset must be specially guided. This is done by means of the wheel guides attached to the opposite rail . The running surface of the wheel usually rests continuously on the frog tip and / or wing rail while driving over this gap. Sometimes, however, this cannot be (sufficiently) ensured due to the switch or crossing geometry, which means that special constructions are necessary.
Control arms exist in different designs. The older design are compound wheel control arms. They are connected by screws to the rail and the control arm, the width of the groove is ensured by means of lining pieces. With newer types of turnouts, wheel guides are used that are separately attached to special ribbed plates or trestles. They offer the advantage of being adjustable and individually replaceable by means of inserts to compensate for wear.
Turnout sleepers
Turnouts lie on special turnout sleepers . These differ in length, type and arrangement of the rail fastening means and in cross-section. They can be made of wood, synthetic wood , steel or steel (prestressed) concrete. With the exception of the sleepers at the start and end of the turnout, each sleeper for simple turnouts is different and therefore unmistakably marked.
In today's new buildings in the area of Deutsche Bahn , concrete sleepers are primarily installed. These are characterized by a significantly higher dead weight with greater positional stability. However, concrete sleepers are usually considerably damaged in the event of derailments and must then be replaced. In the case of steel sleepers, deformations caused by derailments lead to track narrowing. This is why wooden sleepers, which are more robust in this respect, are often preferred in the station area and especially on tracks with lively shunting operations. With their smaller overall height, steel sleepers enable the installation of tracks and points even in areas with limited bedding thickness, for example on bridges. In the past, the choice of concrete or steel sleepers also depended on raw material availability and prices.
The German Federal Railroad embedded points on concrete sleepers for the first time in the summer of 1981. After good experience, all points on the new lines built in the 1980s have already been laid on concrete sleepers.
Point machine
At the tip of the switch is the adjusting device with which the switch blades or the frog are moved. The adjusting device has to overcome the switching resistances of the switch blades or the frog in order to be able to move them. The changeover resistors in modern turnouts consist of:
- Bending forces of the tongues or the frog
- Frictional forces of the tongues or the frog on the sliding surfaces
- Forces for lifting the tongues on the tongue roller
Mechanical local control
At the top of the switch there is a manual adjusting device , the so-called jack stand , on which the switch can be adjusted with muscle power. These switches are therefore colloquially called manual switches . The jack consists of the switch lever and the weight that holds the switch in the respective end position. Usually the jack is connected to a turnout signal . In the early days of the railroad, there were only locally set points, which were soon set by locomotive and train staff, shunters and, to speed up operations, by manual turnout keepers.
If mechanically locally operated turnouts have to be secured against unintentional switching or if they are located in routes and are therefore included in the signal dependency , they are equipped with a hand lock or turnout bolt .
Electrical local control
Electrical local control, also known as electrically localized points (EOW), is increasingly replacing mechanical local control in the shunting areas. As with the electric remote control, it is driven by an electric point machine. Electrically set points are equipped with a point signal designed as a light signal.
Mechanical remote control
Mechanical remote control is used for mechanical interlockings . Here, both the changeover forces and, conversely, the position information are transmitted using a rod or wire pull line. The switching forces are generated by the interlocking operator.
For rod lines , which are still common today in Great Britain, France and former colonies of these two countries, it is sufficient to connect this line to the tongue connection or slide rod. In many other countries, including in German-speaking countries, wire pull cables are becoming more popular. The point machine is connected to the control lever in the signal box via a double-wire cable and consists in the standard form of an unequal angle lever, which translates the 500 millimeter cable travel into (usually) 220 millimeter travel of the slide rod. The mechanical turnout drive includes a wire break lock that holds the turnout in the end position in the event of a wire break. The distance between the switch and the signal box is limited to around 450 meters of line length due to the friction, so that a large number of mechanical signal boxes were required to handle operations in larger stations.
Electric remote control
With the advent of electromechanical interlockings , electric remote control spread for the first time. The changeover forces are generated using an electric drive. The position of the switch blades is also monitored electrically.
At the beginning, point machines were equipped with direct current motors with separate windings for clockwise and anticlockwise rotation. Since the 1950s, in connection with the construction of track diagram signal boxes , three-phase asynchronous motors have been used. In addition to the low-maintenance structure, because it has no commutator , the use of different types of current for changeover and monitoring increases safety. The monitoring DC voltage cannot move the motor, the control AC voltage cannot trigger an incorrect order message.
Electric point machines are equipped with a slip clutch . It prevents damage from occurring if the changeover resistance becomes too great or if the movement is hindered by foreign objects between the tongue and stock rail. In the case of track diagram and electronic interlockings, the drive is switched off by a delay device in this case, which triggers a fault message. In the case of electromechanical interlockings, the operator must watch the current meter and manually reset the switch if the end position is not reached. That is why an alarm clock rings at these interlockings during the changeover. If the operator fails to reset, the control current fuse melts. The effectiveness of the slip clutch is checked regularly by holding a hammer between the tongue and stock rail during the changeover process.
Other adjusting devices
The pneumatic point drive with compressed air, which was tried and tested in the 1920s, did not prevail over the electrical or electrohydraulic drives commonly used today with an electric motor at the tip of the point and switchover using electrical signals. This type of drive was first used in electromechanical interlockings. Pneumatic point machines have been used until recently, for example in the USA.
Point machines with pressurized water drive were also more common, for example in Italy.
Positioning systems
When, at the beginning of the 20th century, the first turnouts with larger curve radii were developed, which can be used at higher speeds in the branching line. The resulting significantly longer tongues first had to be provided with two switch locks in order to guarantee correct contact with the stock rail over the entire length and to maintain the necessary distance to the stock rail in the remote position.
As the arc radius continued to increase, the number of closures rose to eight. First of all, the drive at the point of the switch was connected to several slide rods via angle levers and transmission rods. With advances in control technology, it became possible from around the mid-1970s to equip every single point lock with a drive and move it synchronously.
Because of the high circuit complexity and the necessary drives with different travel ranges, separate drives are usually only used for each lock if, as in polar and desert areas or in mountains and tunnels, increased switching resistances must be expected regularly. Under normal circumstances, only two drives, each with four locks, are installed for the switch device even with high-speed switches for 200 km / h branching speed.
Tongue monitoring
Malfunctions in the transmission parts, for example breaks in connecting rods or locking parts, can lead to changes in position and thus to derailments, especially in the case of points with high traffic. To prevent this, tongue monitoring devices have been introduced. The tongue position is transmitted to these via special connecting rods that are independent of the adjusting device. If a tongue does not reach an end position, a fault message is triggered in the interlocking.
Depending on the permissible speed and the possible traffic of passenger and freight trains, tongue checkers and bolts are used for mechanically remote switches. Tongue testers are part of the point machine and can be driven. The bolts, which are of higher quality in terms of security, require their own setting levers and wire pull cables, but cannot be opened. Manual turnouts can also be included in the signal dependency using latches .
In the early days, electrically operated bolts were used in electromechanical interlockings , both electromagnetically as part of point machines and as a special, motor-operated device, especially in manual points. It turned out, however, that tongue testers for electric drives guarantee the same level of safety with less effort and can be opened at the same time. Manual switches in electrical interlockings are more cost-effective to secure through key dependency. That is why only tongue checkers are used in electrical point machines.
Turnouts with large arc radii and multiple turnout locks are increasingly being given one or more additional tongue test contacts to monitor the end position over the entire tongue length. Mechanical center bolts or tester are possible, but very rare. Because of the large switching resistance, such switches are usually not mechanically controllable and must be equipped with electrical drives, even in mechanical interlocking areas. In the case of fallback turnouts , the monitoring signal is controlled by an electrical tongue test contact at the point of the turnout.
Non-retractable points, i.e. those with movable frog tips or wing rails as well as non-retractable drives for speeds above 160 km / h, receive a drive-up location device that already triggers a drive-up message if a vehicle approaches the wrongly located switch.
Switch lock
Most of the switches have their own components to hold the switch blades securely in place in order to avoid derailments. In many countries a so-called switch lock is used for this , in others separate locks for the tongues.
The switch lock is used to secure the positions of the switch blades produced by the adjusting device. After reaching the tongue layers, the adjusting device carries out an additional path, which actuates certain locking mechanisms. It ensures that the tongue resting on the stock rail remains connected to it even when elastic (in the bent tongue) or external restoring forces (e.g. caused by flanges blows) act. A gaping of the tongues by more than about 5 mm must be reliably prevented. On the other hand, the distance between the other tongue and the other stock rail, which is sufficient for the wheel flange passage, is ensured. In addition, the locking mechanism compensates for differences in the travel that can occur in particular with mechanical drives due to friction in the control lines.
For turnouts with large branch track radii, additional adjusting devices with locks are required for safe guidance of the long turnout tongues.
Types
A distinction is made between two basic types:
- External closures: The closure mechanisms act on the shortest path either directly between the tongues and stock rails or indirectly, but still within the track.
- Inner locks: The lock mechanism is located in the point machine.
In Germany and the successor countries of the former Austro-Hungarian monarchy, external closures have been used almost exclusively until recently.
External closures
The following types of external closures were or are in use:
- The pedal lock was no longer up to date even before 1900, the last examples disappeared from subordinate sidings around 1980.
- The hook lock was the standard lock on the Prussian, but also on Bavarian and Austrian railways. Although it has not been reinstalled there since around 1930, it was to be found in main tracks throughout the 20th century and has survived in large numbers to this day in side tracks. In other countries like the Czech Republic and Slovakia it is still widespread. Hook fasteners are sensitive to temperature-related changes in length of the tongues.
- The clip lock was the standard design in Germany and Austria for decades. It is somewhat more tolerant of temperature-related changes in length, but more prone to icing. Because the ability to compensate for temperature-related changes in position is still limited to a few millimeters, self-regulating locks such as sliding locks of the Peddinghaus design or path-controlled locking clips BKl 60 and 61 were introduced on its basis.
- The basic removal of the clip locks is done by latch locks in several designs. The principle is a clamp lock rotated by 90 °, in which the clamps (here called »locking pawls«) run on the top of the slide rod. The temperature-related changes in length are compensated for by wider locking pieces, the tongue locking can be adjusted by eccentrics without machining.
- For high-speed turnouts, more complex locks such as the HRS lock have been developed, which also reliably fix the tongue in its height position.
- Articulated locks ( locks with internal support or internal locks ) such as the locks of the Jüdel or Bruchsal types were standard designs in Switzerland until the very recent past; in southern Germany they were widespread at the time of the Länderbahn.
Interior closures
In other countries, such as Great Britain, for mechanically set points, switch locks are generally not used at all because of the low-stroke loss transfer of the actuating force through linkage lines with appropriate maintenance. In electrically operated turnouts, internal locks are used almost exclusively, in which the contact of the tongues on the stock rails is ensured within the turnout drive. The point machine must be connected to the stock rails in a very dimensionally stable manner. For a few years now, such closures have also been used in Austria and Switzerland. The use in Germany was not very successful, especially because of the complex individual securing of the tongues in the event of a fault.
location
In addition to the type of construction, a distinction is also made between locks attached to different points on the switch:
- Tip locks: They are the locks attached as standard to the switch tip or the tips of the tongues.
- Middle locks: These are one in the middle of the tongue or several additional locks distributed over the length of the tongue on points with larger radii.
Lace closures
Turnouts with small curved radii and correspondingly short tongues only have a lock at the point of the turnout.
Center locks
In switches with large branch track radii of the long elastic switch blades in a tongue are to safely guide and position assurance center or more distributed over the length of the tongue additional adjusting devices incl. Fasteners required. As a rule, all adjustments and locks are made with the help of a drive via mechanical connections; In the case of particularly long turnouts, they are operated in groups by several drives. In difficult operating conditions with expected higher changeover forces, such as in desert regions or in higher mountain locations, each point receives its own drive; however, this increases the complexity of the circuitry. Movable frog tips or wing rails always have drives that are separated from the tongues, and in difficult cases several.
The locks can be driven on
Turnout locks are usually designed so that the turnouts can be opened from the frog (the turnout is switched from the unsuitable to the appropriate position by the wheel flanges of the first of the passing vehicles). Locked points and points that are driven on at speeds of over 160 km / h (due to possible force peaks that could lead to the unintentional loosening of the retaining devices during regular driving, non-retractable drives) cannot be driven on despite the point lock that is in principle drive-open. If such a switch is opened anyway, severe damage will result. Movable frog tips and wing rails cannot be driven open, because there is no part that can be moved by a wheel set in order to loosen the clamping of the adjacent tip. Remote turnouts that cannot be driven are therefore equipped with a monitoring device that triggers a collision message when a vehicle approaches the wrongly positioned turnout. Inner locks can also be designed to be driven open, but many operators do not. Drives with only one control rod, which both move directly rigidly coupled tongues, as is common in France and often on railways that were built under British influence, cannot be driven on, comparable with movable frog tips.
Turnout signal
If required, actuating devices are equipped with a turnout signal that shows the position of the turnout from a distance. In Central Europe, turnout signals are set up with locally operated turnouts, with remote-controlled turnouts only when shunting runs without secured shunting routes. Usually this is the case with mechanical and electromechanical interlockings as well as with simplified track diagram interlockings. If the turnout signal is designed as a form signal, it is usually provided by the turnout signal connection rod, which is connected to the turnout lock. In the case of manually operated turnouts, the turnout signals (with the exception of double crossover points) are usually placed on the manual control devices. In the case of remote-controlled turnouts, the associated lever is not required, and depending on the type of drive, the weight as well. The special turnout signals for double crossing turnouts are set up next to the middle of the turnout and connected to both turnout drives via rods.
Orbital times
The changeover time of electrically set points depends on the type of drive and the changeover resistance. With German standard turnout drives of the type 1924 and the derived types WA 350 (DR) and S700 (DB), it is around two seconds. Newer types such as S700K (Siemens) or L826H (Thales) require around six seconds because of the higher actuating forces required for points with large radii and heavy rail profiles and to reduce wear.
So-called high - speed drives are used for shunting and especially drainage points of the first series of drainage mountains . These drives, which are usually derived from the standard turnout drive, differ from the latter in that they have a lower reduction gear and a gear unit that rotates only 180 ° instead of 270 °. The travel is correspondingly smaller. In connection with a coordinated switch lock, the changeover time of a high-speed drive is only about 0.6 seconds. High-speed drives are not permitted for turnouts that are located in train routes.
Additional equipment

In many countries, a boundary sign is to be attached to each switch between the branch tracks, which marks the point at which the two branch tracks reach the minimum track spacing, i.e. the two clearance profiles meet. A branch track can be occupied up to this point, so that vehicles can still run on the other branch track.
A point heater can also be installed. The switching process of a switch can be made more difficult in cold weather: Snow can hinder the switch mechanism, the switch tongue can freeze to the stock rail, or blocks of ice from trains can fall into the locking compartment and / or the switch device. In addition, the friction of the slide chair plates can be increased. In many cases, point heating prevents these problems. It is located in the tongue area and in the area of moving frogs and is intended to prevent the moving parts (tongue and stock rail) from freezing together, but also to prevent blocking due to the accumulation of snow and ice.
Construction of points
All turnouts installed today are prefabricated in the turnout factory, dismantled again, transported to the construction site and there again preassembled in a free area. If possible, locks, drives, transmission parts and tongue test contacts are also installed. The large turnout parts created in this way (tongue area, middle area and frog area) are then installed, aligned, ballasted, stuffed and welded using a turnout crane. In some cases, the large turnout parts are completely prefabricated and preassembled in the turnout factory (with or without additional equipment such as drives, transmission parts, point heating systems, etc.) and can be installed immediately. They are brought to the construction site by truck or switch trolley and installed with the help of a crane or a special switch transport and installation device. Crossover switches and switches with large radii and complex transmission parts are preferably delivered in this way. The pre-assembly quality in the switch factory clearly exceeds that possible on the construction site. Another reason for delivery in a pre-assembled state is a lack of pre-assembly space near the construction site. In order to comply with the vehicle boundary profile, the loading areas of the switch transport wagons are tilted for the journey. Turnout transport wagons are used by many railway administrations.
If there is enough time available, it is also common practice to install turnouts at the installation location in the track gap ("in the hole"). In the case of switches in slab tracks, they must be installed on site after the slab has been concreted.
The Witten switch plant is the only Deutsche Bahn production facility for railway switches. The Deutsche Reichsbahn operated switch works in Kirchmöser and Gotha , which today also belong to Voestalpine BWG GmbH , as does the Butzbach switch factory , which was founded in 1920 . Voestalpine BWG employs 750 people. Voestalpine took over the Butzbacher Weichenbau Gesellschaft (BWG) in 2003.
The former superstructure workshop in Hägendorf, today SBB Railway Technology Center in Hägendorf, is the only plant in Switzerland that produces switches in series. Although it is owned by the SBB, it also produces switches for other railway administrations (including narrow-gauge and cogwheel switches). As a rule, the control switches leave the factory, if possible, assembled on the switch transport wagons.
In 2012, around 1,750 points were replaced in the Deutsche Bahn network.
Special designs
Simple switches
In a simple turnout, a branch track branches off from a main track . If the main track is straight, one speaks of a straight turnout. Although the main track is curved, they are called soft curved point . If the main track is bent in the same direction as the branch track, it is an inner curved turnout . If the main track is curved in the opposite direction to the branch track, the turnout is called an outer curved turnout .
Standardization in Germany
At Deutsche Bahn AG , the turnouts are standardized and their designation can contain the following information ( using the example of EW 60-500-1: 12 L Fz H ):
Abbreviation | Explanation | Remarks |
---|---|---|
EW | Switch shape | Single turnout (EW), outer curved turnout (ABW), inner curved turnout (IBW), double turnout (DW), one-sided double turnout (EinsDW) |
60 | Rail profile | UIC60, u. a. 49 (S49: DRG, DB, DR), 54 (S54: DB) and 65 (R65: DR) |
500 | radius | of the branching track (in m) |
1:12 | Turnout inclination | at the end of the turnout ( tangent of the turnout angle) |
L. | Branch direction | left (L) or right (R) |
Vehicle | Tongue design | Spring tongue (Fz, without tongue plate, with older S49 turnouts also with tongue plate), spring rail tongue (Fsch, standard design for S49 turnouts), hinged tongue (Gz) |
H | Sleeper design | Wooden sleepers (H), hardwood (Hh), steel sleepers (St), concrete (B) |
The following designs for simple switches (control switches) are available in the Deutsche Bahn AG network:
Type of turnout (short) | Centerpiece | permissible branching speed |
---|---|---|
EW xx-190-1: 7.5 / 6.6 | bent | 40 km / h |
EW xx-190-1: 7.5 | bent | 40 km / h |
EW xx-190-1: 9 | straight | 40 km / h |
EW xx-300-1: 9 | bent | 50 km / h |
EW xx-500-1: 12 | bent | 60 km / h |
EW xx-500-1: 14 | straight | 60 km / h |
EW xx-760-1: 14 | bent | 80 km / h |
EW xx-1200-1: 18.5 | bent | 100 km / h |
EW xx-2500-1: 26.5 | bent | 130 km / h |
Special feature: symmetrical outer curved turnout | ||
sym. ABW xx-215-1: 4.8 | straight | 40 km / h |
(EW xx: rail profile, e.g. EW 60 )
Turnouts with end inclinations less than 1: 9 (so-called steep turnouts ) should be avoided for reasons of wear; their installation is subject to approval in individual cases.
Curved turnouts (with the exception of the special symmetrical outer curved turnout sym. ABW 215 ) are not manufactured as regular turnouts, but are made from straight turnouts by bending. Turnouts should not be bent further than symmetry. The changes in length resulting from the bending are compensated for in the intermediate rails so that the machined large parts (tongues, frogs) can be replaced. Depending on the radius of the two strands, the permissible speed changes when bending.
"Y-switch"
The term Y-turnout is often found in connection with model railway tracks, but has no conceptual equivalent in the technical terminology of the railway. In fact, the symmetrical outer curved turnout sym. ABW 215 corresponds roughly to what the model railroader understands by it. In reality, however, the sym. ABW 215 is subject to the restriction that it does not usually appear in main tracks, but only in sidings and shunting systems. It can be found or was in older drainage systems, especially in France, where many tracks have to be reached by the shortest possible route and where it is important for the process operation that as many drainage routes as possible run through the same number of points and bends. This goal is achieved today by several bundles of tracks after the runoff mountain with around eight tracks each. Then the switches are arranged in such a way that after the first switch two, then four and finally eight tracks are arranged next to each other approximately symmetrically.
Double turnouts
If there are two branch tracks that branch off from a straight main track either directly next to one another or close behind one another, one speaks of a double turnout, sometimes also called a three-way turnout. In the first case one speaks of a symmetrical double turnout, in the second case of an asymmetrical or crossed double turnout.
Since the tongues are right next to each other in symmetrical double turnouts, the so-called central tongues must be made particularly thin. This makes them very sensitive and requires a lot of maintenance. Furthermore, a special adjusting device is necessary. They are therefore probably no longer installed in the railway sector today.
With asymmetrical double turnouts, a distinction is made between two-sided and one-sided variants. In the first case the branch tracks go in both directions from the main track, in the second case they go to the same side.
Although space-saving, double turnouts are rarely used. With trams , they are still common, however, is then preferred usually a tongue device locally to avoid expensive special components.
Symmetrical double turnout in Châtillon-sur-Seine
Crossing switches
A simple junction switch (EKW) is an intersection that has been supplemented by switches in such a way that the transition from one track to the other is possible in at least one direction of travel (also called half-English ). A double crossing switch or double crossing switch (DKW) enables transitions in both directions. In new buildings, these switches are only installed in exceptional cases, for example in cramped conditions, due to the greater wear and tear. A third variant is the turnout loop . It arises when one of the two straight lines is omitted from a double crossing switch. This also eliminates the need for double frogs. However, this superstructure construction is very rare.
With both types, a distinction is made between the crossover points with internal tongues (mostly occurring design, also called English because of their earlier frequency in the British network ) and those with external tongues (often referred to as the "Bäseler" system). The external tongues enable larger arc radii and thus higher speeds, but are even more complex because of the multiple frogs required.
In the case of particularly narrow track conditions, double-crossing points with curved entry , known as steep DKW by the Swiss Federal Railways (SBB) , were installed. In these extremely rare switches, the stock rail is curved in the area where the switch tongue rests. This increases the turnout inclination. Because passenger trains on DKW with curved entry derailed in Lucerne and Basel in 2017 , SBB replaced the critical points and adapted the track geometry.
Crossing points have three disadvantages: On the one hand, they are more expensive and complex than two simple points, and with internal tongues there is usually no space to equip each tongue with its own lock and tongue tester. Adjacent tongues are connected with coupling rods, the tongue checking or locking rods are connected to the tongue that is not equipped with a lock. In particular, double crossing points with locks on the inner tongues are sensitive to the longitudinal migration of these inner tongues. In addition, a complete under- or Nachstopfen a EKW / DKW is very difficult because in some places the tamping picks can not be submerged due to space constraints. Nowadays, crossing points are only left in the track plan or newly installed if there is very little space available. Because existing crossing points are replaced by simple points wherever possible, their number is steadily decreasing.
Switch with a movable centerpiece
With conventional turnouts, the wheel is temporarily not guided in the frog gap ( guideless point ). The track guidance is ensured by the control arms acting on the rear surfaces of the wheels on the opposite rail. This solution cannot be used if vehicles with wheel flanges of different widths and thus different rear surface spacing are used on a route (e.g. tram vehicles on railway lines). Course for the high-speed ( high-speed switches ) due to the shallow crossing angle have very long crossings and heart gaps. If conventionally constructed frogs were used, then the load would have to be borne by the then very long and thin frog point and by the wing rail leading away to the outside with only very small contact surfaces, which would lead to severe signs of wear and impair running safety.
In both cases, points with movable frogs are used, for which there are two different types:
- Movable frog point : The frog point can be moved laterally (springy or rotatable) and is pressed against the wing rail like a switch tongue (see picture)
- Movable wing rails : With this design, the wing rails are shifted against the fixed tip.
In both cases, the gap in the core is closed. The tip of the frog no longer has to bear any load and is slightly lowered. It is only used for lateral guidance. This is now uninterrupted, so that control arms are not required. This also eliminates the unpleasant "bump" at higher speeds when the wheel set hits the wheel guide, which is unavoidable due to the sinusoidal run of railway wheel sets .
Movable frogs are sometimes installed even in busy switches and crossings, even if this is not absolutely necessary for geometric reasons. The main reason for this is the significantly lower wear and tear on the gapless rail, which outweighs the additional costs for the additional drive.
Another reason is the movement of vehicles with different wheel tire and wheel flange shapes. Typical for this is mixed operation of trams and railroad vehicles on the same track. Because of the greater distance to the rear surface of a tram wheel set and the generally narrower treads, safe guidance by the long-distance wheel guide and the crossing of the frog gap are not guaranteed. Clearly visible examples are the Vienna Philadelphiabrücke – Baden route of the Vienna – Baden local railway , the mixed-use routes of the Cologne / Bonn city railway on lines 7, 16 and 18 and the Zwickau – Zwickau-Zentrum line .
Such points also existed outside of Germany, e.g. B. in 1927 on line 11 of the HTM ( The Hague , Netherlands), which was converted from a local train to a tram . In order to be able to serve the industrial companies connected to the route as far as Scheveningen with railroad cars, the whole line was equipped with points with movable frogs. The last freight train ran on this route in 1974. Some switches still exist today, but when switches are changed they are replaced by regular switches with tram dimensions.
Movable frogs can never be driven open. If they are driven on in the wrong position, damage will always occur.
Spring-loaded centerpiece, presented in 1979 at the IVA Hamburg
High-speed switches
Turnouts with a high branch track speed are referred to as high-speed turnouts. Movable frogs create a continuous running surface, very slim, long tongues are intended to reduce the forces resulting from a discontinuity. Due to the long tongues, several force application points are necessary.
The planned since the early 1970s, new lines in Germany called for new designs of switches that could meet the increased physical stress. Initially, the operational requirements focused on the permitted speed. Since only the straight main track is driven at high speed on rarely used track changes , it was initially assumed that simple EW 60-1200-1: 18.5 turnouts with fixed frogs would be sufficient, so that this design in the transfer points of the first German high-speed line Hanover – Würzburg was mainly used.
For a long time EW xx-1200-1: 18.5 were the switches with the highest branch track speed on German railways. By the mid-1970s, DB had developed two types of frogs with a movable tip: articulated and spring-movable. Both were tested in a total of 32 switches. For high speeds, the EW 60-1200-1: 18.5 turnouts (for 100 km / h on a branch track, in one version each for both frog constructions) and the EW 60-2500-1: 26.5 with spring-loaded movable tip (branch track speed 130 km / h).
As a high-speed turnout, which is also suitable for higher speeds in the junction, there was only the EW 60-2500-1: 26.5 (permissible speed in the junction 130 km / h) in the beginning, which was due to the large gap between the frogs due to the geometry an had a movable frog point. It was therefore suitable for B. on the high-speed line Hanover – Würzburg for the Sorsum junction (to and from Hildesheim), the further arc of which only allows a speed of 130 km / h anyway.
Other junctions, which were to be used at even greater speeds, required even longer switches. Thus, in the Mannheim-Stuttgart high-speed railway , the (two different radii having) first basket arch soft EW 60-7000 / 6000-1: 42 and EW 60-6000 / 3700-1: 32.5 installed. They not only require movable frogs, but also considerably longer switch blades and thus several drives.
In principle, turnout lanterns are only necessary where maneuvering is carried out without technically secured shunting routes and the staff must be able to recognize the set route. In contrast to this, the high-speed turnouts with a movable frog point still have (several) conventional point lanterns to provide the maintenance staff with feedback on the synchronous position of the blades and frog point.
The following types of high-speed switches (control switches) are available from Deutsche Bahn AG, designed for the first German high - speed routes Mannheim – Stuttgart and Hanover – Würzburg :
Type of turnout (short) | Drives / locks switch device / frog point |
permissible speed of main track / branch |
||
---|---|---|---|---|
EW 60-1200-1: 18.5-col | 1/3 + 1/2 | 280 km / h / 100 km / h | ||
EW 60-2500-1: 26.5-col | 1/4 + 1/3 | 280 km / h / 130 km / h | ||
Basket bow turnouts | ||||
EW 60-6000 / 3700-1: 32.5-col | 2/7 + 1/3 | 280 km / h / 160 km / h | ||
EW 60-7000 / 6000-1: 42-col | 2/8 + 1/3 | 280 km / h / 200 km / h |
(Note: -fb = spring-loaded frog )
With basket arch turnouts , the curve begins at the switch blades with a larger radius (with the EW 60-7000 / 6000 with 7000 meters) and then changes to a smaller radius (here: 6000 meters) around the middle of the turnout . After the center piece, there is a transition curve in the branch , which leads the track back into the straight line. For this reason, arched turnouts cannot be used in crossovers with the usual track center distance .
EW 60-7000 / 6000-1: 42 , high-speed route Mannheim – Stuttgart: An Intercity branches off at the Saalbach junction from Mannheim in the direction of Karlsruhe. (In operation since 1988)
EW 60-6000 / 3700-1: 32.5 in the Rheintalbahn, connecting curve Ubstadt, junction from Heidelberg to the high-speed line towards Stuttgart. (In operation since 1988)
EW 60-7000 / 6000-1: 42 at junction Rohrbach in the high-speed line Hannover-Würzburg with three drives. (In operation since 1994)
EW 60-6000 / 3700-1: 32.5 fb on the Saale-Elster valley bridge (branch-off at 160 km / h, commissioning 2015)
Clothoid turnouts
Clothoid turnouts are a new type of high-speed turnouts. Their curvature increases linearly and is used for jerk-free driving dynamics. The radius of the branching line decreases continuously, according to the geometric shape of the clothoid . The jolt when changing tracks, which is uncomfortable for passengers, is therefore much gentler than with the arched turnouts that have been used up to now, and there is less wear and tear. In the case of clothoid switches for branch points, the branching line ends as a circular arc. In the case of clothoid turnouts for track connections, it ends as a straight line in order to obtain an intermediate straight line of sufficient length together with the neighboring turnout.
In the Deutsche Bahn network, the new design was first used in large numbers on the high-speed line from Hanover to Berlin, which opened in September 1998 . Since the introduction of the LuFV, however , the additional costs of clothoid turnouts compared to circular arc turnouts or basket arch turnouts are no longer eligible for funding. After 2008, therefore, no more clothoid turnouts were installed in Germany, and existing clothoid turnouts will be replaced with conventional turnouts when renewals are due. In 2018, for example, this affected an EW 60-16000 / 6100 in the Bitterfeld train station, which was replaced by an EW 60-7000 / 6000 arched turnout that could be used at 200 km / h.
Types of clothoid turnouts in the inventory of Deutsche Bahn AG:
Type of turnout (short) | Drives / locks switch device / frog point |
permissible speed of main track / branch |
Remarks |
---|---|---|---|
EW 60-3000 / 1500 1: 18,132 col | 4/4 + 3/3 | 330 km / h / 100 km / h | For branch points |
EW 60-3000 / 1500 / ∞ 1: 23.735 col | 4/4 + 3/3 | 330 km / h / 100 km / h | For rail connections |
EW 60-4800 / 2450 1: 24.257 col | 5/5 + 3/3 | 330 km / h / 130 km / h | For branch points |
EW 60-4800 / 2450 / ∞ 1: 30.686 col | 5/5 + 3/3 | 330 km / h / 130 km / h | For rail connections |
EW 60-10000 / 4000 1: 32.05 col | 6/6 + 3/3 | 330 km / h / 160 km / h | For branch points |
EW 60-10000 / 4000 / ∞ 1: 39.173 fb | 6/6 + 3/3 | 330 km / h / 160 km / h | For rail connections |
EW 60-16000 / 6100 1: 40,154 col | 8/8 + 3/3 | 330 km / h / 220 km / h | For branch points |
EW 60-16000 / 6100 / ∞ 1: 47.6539 col | 8/8 + 3/3 | 330 km / h / 220 km / h | For rail connections. This crossover was specified, but was never installed. |
Heart pieces with flat groove
Even if the frog angle is too steep, the wheelset falls into the gap between the tip and the wing rail. Since such steep crossing angles usually only occur on tracks that are driven on at low speeds (industrial connections, trams, etc.), a frog with a flat groove is usually installed in this case . The wheel runs briefly on the flange and is lifted over the gap in this way. Such frogs are subject to greater wear, since the contact surface of the wheel flange is much smaller than that of the running surface.
Fallback switch

A fallback switch automatically returns to its original position after opening. Fallback switches are often used on single-track routes, e.g. B. in train control . In stations with at least two fallback switches, train crossings are possible without switch operation. A fallback switch is held in one position with the help of a manual device. This manual control device is locked by a switch lock and secured against unauthorized operation. It is connected to the slide rod by a spring member instead of the trestle rod. When approaching from the frog , the flange of the first axle pushes the tongue that was previously remote into the other position. The return spring is tensioned in the spring member. After the switch device has been released, it "falls" back into its basic position after a delay of a few seconds, driven by the spring force of the oil-damped return spring, hence the designation fallback switch . A fallback switch can be switched over for maneuvering or, in the event of a fault, like a normal local switch using the manual control device. To monitor the correct end position of the fallback switch and, if necessary, the lock of the key in the key dependency, a monitoring signal Ne 13 is set up in front of the switch tip, which is controlled by a tongue test contact. If the fallback switch is in the end position of its basic position, the monitoring signal shows a white light over an orange horizontal stripe and a white-orange diagonally striped mast sign; if the fallback switch has not reached its end position, the light is dark. Other signaling may occur in old systems.
In tram networks, it is common to install fallback switches (often referred to as spring switches ) when turning . When traveling from the frog, they are driven up as planned by each axle (or bogie) and immediately fall back into their basic position after being passed through. This briefly creates a "wrong" point under a car.
Sand switch
A sand switch has switch tongues similar to a simple switch, but the branching line ends in a sand case before the frog. This is a special design of the protective switch . Runaway wagons in downhill railway stations were directed through the sand switch into a section of track that was filled with sand. Often, however, this process resulted in derailments, so is also in Switzerland the term Entgleis - in other countries derailment switch used. Sand turnouts thus act in a similar way to track barriers and, like these, serve as flank protection devices , but could also be installed in tracks used by trains. Sand switches or sand tracks are rarely used today, e.g. B. in the train station Dresden-Friedrichstadt .
Tow switch

With the drag switch, the entire track is swiveled, there are no continuous outer rails with conventional double-rail tracks. The switch tongues are straight and movably mounted at the point of the switch, the adjusting device is at the inner end of the switch tongue and moves the rails on the straight or branching line. Instead of a core, drag switches, which are driven on by vehicles with double-flanged wheels, have a rotatable piece of rail that is rotated into the rail track to be driven on.
The first railway switches were drag switches. Since they were not operationally safe, especially at higher speeds, they were soon replaced by other designs on the railways. One area of application today is still mountain railways, which for safety reasons have double flanges or are equipped with caliper brakes. A well-known example of this was the Pöstlingbergbahn in Linz , which was equipped with drag switches until it was renovated in 2008/2009. A few examples can also be found on field railways .
Since 1999, Rigi-Bahnen have been using newly developed rack and pinion turnouts , known as spring turnouts , in which the track is bent from one end position to the other along a defined curve. The construction has fewer moving parts than a conventional rack and pinion switch and does not require switch heating .
Rail-bound traffic systems that are equipped with a track system that differs from the conventional two-rail track and whose vehicles encompass the route or protrude into it, in particular all types of monorail tracks (e.g. Alwegbahnen and symmetrical or asymmetrical suspension railways such as the Wuppertal suspension railway or magnetic suspension trains ) are on instructed to use long towing switches. Towing switches on monorails are both more complex in terms of construction and much more time-consuming and cumbersome in operation than tongue switches. They need about eight to ten times the time of a tongue switch to switch. As a result, the route formation time is much longer and thus the line capacity is lower than with double-rail systems. This is a major reason why such systems remain isolated island operations and do not develop into a network.
Contact wire switches for trolleybus operation as well as in tram networks with pantographs work according to the principle of the drag switch.
Tongue-less switch
General
Tongue-less turnouts are used at the beginning and end of a three- or four-rail track. Whether the switch is used in a straight line or in the branching line depends on the gauge. Tongue-less turnouts have a centerpiece, wing rails and several wheel guides. In order to guarantee the passage of the wheel flanges through the smallest possible gap in the jointly used strand, they are also required on the outside of the runways. If the narrow-gauge track branches off against the side of the common line, and if a four-rail track is split up, a double frog is also required. In early horse trams , switches without a tongue were also used, whereby the direction of travel was determined by the direction of the horse 's pull.
Connection without tongue and frog (ZHA)
A special form of the tongue-free turnout is the tongue and frogless connection (ZHA), which is not called a turnout and is used in turnout-less track connections . The two rails of the main track are continuous, but those of the branching track are interrupted. If the branch is to be operated, the rails of the main track must be cut, bent in the direction of the branching track and lashed to it. After operation, the rails are bent back and welded to the main track . This type of branching is used for connections that are rarely used, e.g. B. at substations for transformer transport . Separating and re-welding is cheaper than maintaining a normal switch. Examples in Germany can be found near Langenfeld (Rhineland) , on the new Erfurt – Leipzig / Halle line at the junction to the Erfurt -Vieselbach substation , at the Saalbach junction of the Mannheim – Stuttgart high-speed line in the connecting curve to Karlsruhe and at the Heidelberg-Kirchheim / Rohrbach station .
Climbing switch
A climbing Soft , even Auflegeweiche or Aufliegeweiche called, is usually used only for trams and light railways. As a makeshift, it is usually placed on the existing track due to construction work in order to transfer trains to another track. The climbing switch consists of firmly connected rail profiles. The trains can run onto the temporary switch via flattened ends and be diverted.
Switch in the multi-rail track
Turnouts located in the course of three or four-rail tracks are special constructions with mostly several frogs. The number of frogs required depends on the type of multi-rail track. The position (side) of the narrower track within a three-rail track also has an effect in this regard. There are also differences in the type of branching track. This can either be one of the two gauges or a multi-rail track.
Rack railway switch

In the case of rack and pinion railways, two fundamentally different systems must be considered, also and especially with regard to the type of switch. On the one hand there are rack and pinion railways whose racks are above the running rails, on the other hand there are those in which the top edges of the rack and running rails are at the same height. In the case of the former, it is possible that the vehicles equipped with gear wheels also drive on conventional points, since the gear wheels lie above the upper edge of the rail even in the most unfavorable permissible wear condition. Examples of this are the routes with adhesion and rack-and-pinion mixed operations such as the Swiss Matterhorn-Gotthard Railway (MGB, formerly FO and BVZ). Toothed rack points can be solved in such railways by quite simple folding constructions, especially when it comes to the two-lamellar Abt system. Individual slats are then pushed over the running rail without moving the latter. Such simple constructions are only possible if the full force does not have to be transmitted via the rack, for example on low inclines or in the plane. Such switches are preferably used when z. B. in a crossing station would like to save the extension and retraction from or into the rack, because it leads to decelerations. However, the advantage of being able to install conventional switches is accompanied by a disadvantage: at level crossings in the rack section, complex technical solutions for lowering the rack are required, or a transverse shaft is created for road traffic. Such transverse waves are generally no longer approved today. An example of a lowerable rack is the intersection of the road and steam train Furka mountain route in Oberwald.
In the case of a low-installed rack according to the original Riggenbach type, as it is, for. B. is the case in Stuttgart with the cog railway of the Stuttgarter Straßenbahnen AG, street crossings at the same level are not a problem, since the resulting gaps with the usual tooth pitches are not wider than with rail grooves and there are no height differences in the road surface. In return, however, you are now forced to equip both the rack and the rails with movable pieces, which are moved together with the switch blades, since the gearwheels protruding below the upper edge of the rails would otherwise collide with the intersecting intermediate rails.
In the case of pure rack-and-pinion railways, the locomotives of which do not have adhesion engines, you have to rely on points with a rack.
Track turner

On the only rack railway with rack and pinion system Locher, crossings between the rail and rack are not possible due to the horizontally positioned gears, so that the use of conventional switches is not possible. Instead, so-called track turners are used. These consist of a frame to which a track for the left strand is attached on the top and a track for the right strand on the bottom. The frame can be rotated 180 ° in the direction of the track axis, so that rails and rack are continuous in both positions. Originally, instead of switches, the Pilatusbahn had wide transfer platforms with one track each for the straight and branching line next to each other, which could also be used continuously, as is still the case today at the Aemsigen crossing station. At the moment there are only two track turners at the Pilatus Kulm station. In the planned renovation of the Alpnachstad valley station, three more are to replace the current transfer table.
Arc turntable

A curved turntable is a turntable with a curved track on it. Depending on which of the two arch ends is turned in the direction of the entry line, the opposite arch end points either to the left or right exit line. On railways, curved turntables are more of a theoretical nature and are rarely or not at all used, but this design is the standard switch for the Lartigue monorail .
A curved turntable with two intersecting tracks, one of which is straight and the other built in a curve, is located in the Vitznau station of the Vitznau-Rigi-Bahn to connect the vehicle halls to both platform tracks.
Abt switch on funiculars
The Abt switch is a special construction for funicular railways , which is used at the passing point in the middle of the route. The turnout has no moving parts because the cable car cars are guided by wheels with double flanges on the outer rail and have no flanges on the wheels of the inner rail.
Tram switches


Two different switch constructions are used in tram networks. For those sections of the road that lie in the road surface, points made of grooved rails are used. In the wheel guide area, the grooves of the grooved rails narrow; in older designs, wheel guide rails with flat grooves were also installed in the area of flat groove frogs. Typical turnout drives for grooved rail turnouts are usually located between the stock rails. Because the tongues form the inner edge of the groove in the remote position, the tongue impact is only about as large as the groove width and therefore significantly smaller than with railway switches.
Tram turnouts, which are uncovered on a section of the route with their own track, usually correspond to the designs customary for railways. There are visible differences, depending on the wheel tire profile used, in the guide and groove widths of the wheel guides and frogs. These are significantly narrower in classic tram companies, and the control arms do not protrude above the upper edge of the rails. Tram switches can have much smaller arc radii. Crossing switches are rare on trams. If turnout drives typical for trams are used, then the tongue impact is also in the case of Vignole-rail turnouts in the amount customary for grooved rail turnouts.
In the past, many companies, e.g. B. in Leipzig , grooved rail switches are also used on their own track structure. If a switch is only partially located in the street area, it is possible to change from grooved to Vignole rails within the switch, but not in the tongue or frog area.
Regular railway switches are generally used on tracks with mixed operation of road and rail vehicles. If tram vehicles are to run without modifications on the vehicle side, frogs without interrupting the running edge are required. This is made possible by moving frog tips or wing rails. The latter use, for example, the Rheinuferbahn and the local railway Vienna – Baden .
Simple switch
Grooved rails have a continuous track channel. For this reason, no special wheel guides and wing rails are required for switches in the subgrade. However, the groove width narrows in the wheel control area. Since the running surface of the wheels of trams is usually narrower than that of main railways, this leads to stronger impacts, especially in the area of the frogs, since the contact surface of the wheel is smaller. In the frog and in the wheel guide area, the grooved rail is therefore often designed as a flat groove in which the flange rolls on the bottom of the groove. For a number of years, slightly wider wheel tires have been used, making deep-groove frogs possible in many cases. The smoothness of the vehicles is much better on these.
Tongue-less switches were common in the early horse trams. When driving at a sharp point, the direction of pull of the horse and carriage determined the direction of travel on the switch. Deeper grooves were used for the preferred direction of travel, especially at intersections. With the use of tram cars, tongues were necessary to control the direction of travel, and switches were often equipped with only one tongue.
Single soft
Single tongue switches are switches that only have one tongue. In the past, they were used all over the world due to their lower production costs, but now they can still be found in the cities of the former Soviet Union and, for example, in Toronto (Canada) and San Francisco (United States). The tongue works next to the stock rail like a normal turnout, whereas it acts as a wheel guide. This single-turn switch construction is only possible as a hinged switch switch with a small curve radius and grooved rails. The tongue-less side of the point of the turnout is usually a flat groove with a flange.
Separations of three-rail tracks with large curved radii are also designed as single turnouts to ensure a continuous running edge.
Extended tongue device
Especially in the case of trams, points can also be located in the area of busy streets or tight curves. In order to minimize the susceptibility to failure, these are often placed a few meters further away from such an inconvenient location using short four-rail tracks with rails lying directly next to each other.
This type of construction is also known as an extended tongue device.
Pre-sorting gate
With a pre-sorting switch only used on trams , the multi-rail track is extended so that it extends, for example, over the entire length of a stop and several trains can enter it. This enables the railcar drivers to drive slowly when entering the stop in order to control the switch position. As long as the switch was switched depending on the upstream current, it was also possible to use the contact line contact in the outlet and thus in some cases without power consumption.
The exit from the stop can now be done more quickly, because even when several trains are in close succession, no switches need to be set and they cannot be switched over by mistake. Even after the introduction of point setting devices that are independent of traction current and points locked under the train, such pre-sorting points relieve the drivers, who can focus their attention more on the traffic situation. The disadvantage is that in the event of sudden disturbances (e.g. accidents), the direction of travel can no longer be changed at short notice in such a case.
Points with special tasks
Protective switch

Protection or derailment points are points whose only task is to prevent a train journey from being endangered by other train or shunting movements ( flanking ) by means of their distracting position . The deflecting line of the turnout usually leads to a short stump track, which is often closed by a buffer stop . In train stations you can find protective switches z. B. as the end of crossing or passing tracks as well as siding, if these have a slope to the main track.
A special form is the anti-stretching switch. If a long train enters a passing track and releases the brakes a little after stopping, the springs in the wagons' buffers relax, which causes the train to stretch backwards. In order to prevent a stretching train from getting into the clearance profile of the neighboring track, there are then special switches that have to be switched after the train has entered so that the train is stretched to another track.
In the border stations of the GDR , safety points were used to prevent escapes from the GDR . If this was not possible due to lack of space, track closures were also used as a special solution .
Collecting switch
The task of a catch point is to prevent vehicles from escaping down a slope. In its basic position, the switch lies on the distracting line, which, similar to the protection switch, usually leads to a short stump track with a buffer stop, but in contrast to this it lies in the route of the train and is only changed shortly before it is driven on. Fall arrest points can be found both in the exit path of the uphill station and behind the entrance signal for the valley station.
Approaches
A switch will either
- pointed (approach to the point of the turnout with the option of choosing left or right) or
- Drive bluntly (opposite direction, without such a choice).
In the case of double-track lines with a preferential direction of travel (right-hand traffic in Germany), the track changing areas at transfer points also have a corresponding nomenclature. The confusing term for changing tracks only includes the possibility, not the necessity of the same.
In tram networks, track changes with butted traffic were often installed because there is less risk of derailment and, above all, so that there is no risk of unintentional flanking. Such a flank drive or derailment can occur when z. B. the switch tongue is not correctly positioned due to foreign bodies and at least one axis takes the wrong route. In turnouts with railroad-type turnout drives, when a vehicle runs into the switching process from the top, because of the larger tongue impacts in comparison to tram drives. This process is known as two-lane driving or fork driving .
In order to avoid switchbacks at a construction site during the repair or renewal of a tram route, the intact track is used in both directions. For this purpose, a track connection with a climbing switch is laid in front of the construction site , via which the tram can switch from the construction site track to the track in the opposite direction. Behind the construction site, the permanently installed, now acutely used track change is used to get back to the originally used track.
Turnout records
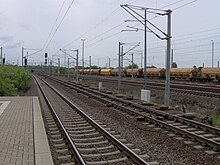
The currently largest switches in Germany are on the Leipzig – Berlin line at Bitterfeld station , they serve to separate the points towards Halle and Leipzig and were the largest switches in the world at that time. The radius of the branching line of these clothoid turnouts of the type EW 60-16000 / 6100-1: 40.15 decreases from an initial 16,000 meters towards the center of the turnout to 6100 meters and then increases again to the initial value. Eight drives are required to switch the blades and a further three drives to switch the frog point. The total length of these switches, which branched off at 200 km / h, is 169.2 meters each. To this day (as of 2011) they are the longest switches in the Deutsche Bahn network. The first of the two switches, switch 61, was installed south of the platforms in January 1998. 1999 followed with the switch 03 a second switch ( 51 ° 38 ′ 6.2 ″ N , 12 ° 19 ′ 11 ″ E ) of similar dimensions in the northern head of the station. Both are left turners.
At the junction in Saalbach of the high-speed line Mannheim – Stuttgart (commissioning: 1987) and at the junction to the Nantenbach curve of the high-speed line Hanover – Würzburg (1994), turnouts that branched off at 200 km / h were used for the first time in Germany. The basket bow turnouts EW 60-7000 / 6000-1: 42 have been newly developed and are 154 meters long and 210 tons in weight, the radius in the area of the tongues is 7000 meters and about 6000 meters from the middle of the turnout. The length of the tongues is 56 meters.
These six turnouts are the fastest used turnouts in Germany today in the branching line. Two further turnouts (EW 60-16000 / 6100) that branch off at 200 km / h were built by the end of 2010 to integrate the Weissig – Böhla connecting curve into the Berlin – Dresden railway line .
On the high-speed route Madrid – Barcelona – French border , a total of 136 even larger switches are now in use, especially at transfer points (EW 60-17000 / 7300-1: 50). The radius of the 180-meter-long structures, which branch off at 220 km / h, is between 7,300 and 17,000 meters.
In June 2001, the LGV Méditerranée went into operation at the junction of Les Angles (Paris – Montpellier route ) at 220 km / h.
The world's fastest turnout is located on the LGV Est européenne and was driven on as part of the V150 record run on April 3, 2007 at 560 km / h on the main track.
literature
- Gerhard Müller: Turnout manual . 4th, revised and supplemented edition. Transpress-Verlagsgesellschaft, Berlin 1991, ISBN 3-344-70733-7 .
- Volker Matthews: Railway construction. (With 57 tables) . 6th, revised and updated edition. Textbook, construction. Teubner, Wiesbaden 2003, ISBN 3-519-50113-9 .
- Günter Berg, Horst Henker: Switches . 2nd Edition. transpress VEB Verlag for Transport, Berlin 1986, ISBN 3-344-00041-1 .
- Joachim Fiedler: Railways. Planning, construction and operation of railways, S, U, light rail and trams . 5th, revised and expanded edition. Werner, Düsseldorf 2005, ISBN 3-8041-1612-4 .
- Max Schmid v. Schmidsfelden: Switch with uninterrupted main track for branching off industrial railways . In: Paul Kortz (Red.): Journal of the Austrian Association of Engineers and Architects . Volume 49.1897, issue 45. Österreichischer Ingenieur- und Architektenverein, Vienna 1897, ZDB -ID 2534647-7 , p. 607 ff. - full text online (PDF; 13.2 MiB) .
Web links
Switches. In: Viktor von Röll (ed.): Encyclopedia of the Railway System . 2nd Edition. Volume 10: Transitional bridges - intermediate station . Urban & Schwarzenberg, Berlin / Vienna 1923, p. 310 ff.
Individual evidence
- ^ John Curr: The Coal Viewer, and the Engine Builder's Practical Companion. John Northall, 1797.
- ^ Friedrich Kluge, Elmar Seebold: Etymological dictionary of the German language . 23rd edition, Verlag Walter de Gruyter, 1995, entry Weiche .
- ↑ a b K. G. Baur: New points for fast trains . In: Railway courier . No. 199, 4, 1989, ISSN 0170-5288 , p. 38 f.
- ↑ Peter Münchschwander (Ed.): The high-speed system of the German Federal Railroad . R. v. Decker's Verlag G. Schenk, Heidelberg 1990, ISBN 3-7685-3089-2 , p. 86.
- ↑ Infrastructure status and development report 2019. (PDF) Performance and financing agreement II. In: eba.bund.de. Deutsche Bahn, April 2020, p. 126 , accessed on May 17, 2020 .
- ↑ How points are strengthened . In: DB World . No. 7 , July 2015, p. 14 .
- ↑ The future of rail - together for more quality, more customers, more success. (PDF) Deutsche Bahn AG, Berlin, October 2015, p. 20 , archived from the original on January 1, 2016 ; accessed on December 27, 2017 .
- ↑ The switch reports sick . In: DB World . No. October 10 , 2016, p. 6 .
- ↑ The courage to change makes everyone win . In: DB World . No. 11 , November 2016, p. 7 .
- ↑ Study on the introduction of ETCS in the core network of the Stuttgart S-Bahn. (PDF) Final report. WSP Infrastructure Engineering, NEXTRAIL, quattron management consulting, VIA Consulting & Development GmbH, Railistics, January 30, 2019, p. 269 f. , accessed April 13, 2019 .
- ^ Adolf Bloss: Superstructure and track connections . Reference library for civil engineers, Part II: Railways and urban development, Volume 4. Berlin, Springer 1927, p. 131 ff. Limited preview in the Google book search, accessed on October 10, 2016.
- ↑ voestalpine BWG GmbH: FAKOP® kinematic optimization (PDF; 330 KiB) brochure (4 pages).
- ↑ marjorie-wiki: WITEC
- ↑ centerpiece. In: Viktor von Röll (ed.): Encyclopedia of the Railway System . 2nd Edition. Volume 6: Freight Transport Crises . Urban & Schwarzenberg, Berlin / Vienna 1914, pp 186 -187.
- ↑ Special turnouts made of bainite for the highest demands. Deutsche Bahn AG, October 15, 2012, archived from the original on January 21, 2013 ; Retrieved October 24, 2012 .
- ^ Theophil Rahn: Express rail traffic - a challenge and necessity for the new railway . In: Rolf Kracke (Ed.): Railway on New Paths - Research and Innovation for Rail Transport of the Future ( Scientific Work , No. 30), Institute for Transport, Railway Construction and Operation of the University of Hanover, Hanover, 1987.
- ^ Fengler, Wolfgang: Handbook Railway Infrastructure . 2., rework. Edition 2013. Springer Vieweg, Berlin, Heidelberg 2013, ISBN 978-3-642-30020-2 .
- ↑ Point heating systems at Deutsche Bahn AG . In: Deine Bahn , Issue 1/2010, pp. 51–56, ISSN 0948-7263 .
- ↑ Switch works with a very eventful history . In: DB World . No. 3 , March 2008, p. 3 .
- ↑ Manfred Köhler: With heart and tongue . In: Frankfurter Allgemeine Zeitung . No. 13 , January 16, 2016, ISSN 0174-4909 , p. 41 ( faz.net ).
- ↑ number of courses . In: mobile . January 2013, p. 37.
- ^ A b Walter von Andrian: Switches as part of the chain of causes for derailments ?. In: Swiss Railway Review. No. 3/2018. Minirex, ISSN 1022-7113 , pp. 136-137.
- ↑ a b Otto Morgenschweis: Switches for express rail traffic . In: The Railway Engineer . tape 28 , no. 3 , March 1977, ISSN 0013-2810 , pp. 101-107 .
- ↑ a b voestalpine, References high speed
- ^ Matthews, Bahnbau, 8th edition, pp. 184-186, ISBN 978-3-8348-1291-9
- ↑ Illustration of a double drag switch of the Ffestiniog Railway
- ↑ Peter Pfenniger: New special bendable rack switch RIGI-VTW 2000. (PDF) Rigi Bahnen, February 2001, accessed on July 15, 2017 .
- ^ Rudolf Breimeier, pp. 11, 22f.
- ↑ Tongue-less switch on a Japanese horse-drawn tram.
- ↑ Recovery of parked steam locomotives using a climbing switch
- ↑ Technical details of the Weißer Hirsch funicular in Dresden
- ↑ Lothar Friedrich, Albert Bindinger: The components of the route for the ICE system in the test . In: Eisenbahntechnische Rundschau , 1992, Issue 6, pp. 391-396, ISSN 0013-2845 .
- ^ Hubertus Höhne: Rail technology of the high-speed rail line Madrid - French border . In: The Railway Engineer . tape 54 , no. 12 , 2003, ISSN 0013-2810 , p. 37-42 . - online. (PDF; 445 KiB) Archived from the original on September 27, 2007 ; accessed on December 27, 2017 .
- ^ Sven Andersen: Traffic stops on the TGV route Paris - Marseille . In: Eisenbahn-Revue International , Issue 12/2001, ISSN 1421-2811 , pp. 557-561.
- ↑ Vossloh AG: Vossloh: understanding mobility . Brochure (16 pages). P. 6