porcelain
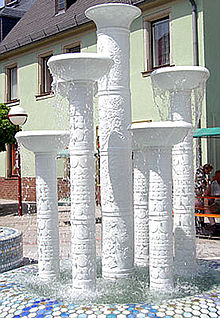
Porcelain ( Italian porcellana , English porcelain or china ), also called white gold , is a fine ceramic product made by firing with white, dense, pore-free, transparent shards in thin layers. It is made from a mixture of kaolin (china clay, porcelain clay), feldspar and quartz , which are converted into glass phase and mullite during the ceramic fire . Glazed or unglazed, it is used in the manufacture of everyday objects, technical products and for artistic purposes.
Ceramics | Class: sintered products | Subclass: porcelain |
Group 1: Hard-paste porcelain. |
composition
There are several ways to describe the composition of porcelain in general. There are currently a large number of porcelain variants, so that a general overview of their precise composition is difficult.
- General porcelain components
- Kaolin (高岭土), a special, low-iron clay consisting primarily of kaolinite , named after the Chinese mountain Gaoling (高岭),
- Petuntse ( 白 墩子 , bái dūnzi ), a feldspar or mica rock , as well
- quartz
Clay components | Glass-forming ingredients | ||
Porcelain art | Kaolin % | Quartz % | Feldspar % |
Bavarian china china | 55 | 22.5 | 22.5 |
Meissen hard-paste porcelain | 66-67 | 8-9 | 25-26 |
East Asian porcelain | 23-35 | 41-45 | 20-35 |
Porcelain types
Depending on the level of the firing temperature and the admixture of volume proportions kaolin, feldspar, quartz and other admixtures such as bone meal, a distinction is made between the following types of porcelain.
Hard and soft porcelain
Hard-paste porcelain is created by higher firing temperatures and is largely insensitive to temperature fluctuations. It consists of 50% kaolin, 25% quartz and 25% feldspar. Soft-paste porcelain, on the other hand, consists of 25% kaolin, 45% quartz and 30% feldspar and requires lower firing temperatures.
These values correspond to the average mixing ratios. The properties of the porcelain can be varied within wide limits by changing the individual components and adding more. The quartz components influence the strength. At 25% the strength decreases, higher contents cause an increase in strength, but require higher firing temperatures.
The different types of porcelain also have their own special composition, depending on the region of origin. The exact mixing ratios are confidential, and for special purposes (utility porcelain, decorative porcelain), in some cases significantly different mixing ratios apply. In addition, the raw materials are natural mineral deposits, the composition of which can vary greatly from region to region.
Special porcelains and variations
Bone china or fine bone china (Engl. Bone China and Fine Bone China) are special types of porcelain developed in England, in which particularly high translucency , brilliant shine and high strength are achieved by adding bone ash .
Dental porcelain is one of the special types of porcelain . It usually consists of 80% kaolin, 5% feldspar and other additives.
In addition to numerous variations, specifications and nuances in the production of white gold, there are examples of lithophane , biscuit porcelain and pâte sur pâte , to name just a few.
particularities
So-called fake porcelain or semi-porcelain are frit porcelain and faience .
Differences to other ceramics
The outstanding feature of porcelain compared to other ceramic products is not the high firing temperature, as is often assumed. The main difference lies in the sintering behavior : the feldspar content in the porcelain melts during the firing process, but it does not crystallize again when it cools down due to its toughness. Like glass , porcelain contains a supercooled melt ; on the other hand, other ceramics such as stoneware or earthenware form purely crystalline sintered structures. This peculiarity leads to a certain amount of light permeability ( translucency ) with some porcelains, especially with thin walls .
Porcelain has a dense body , shell-like fracture and great hardness. It is acid and alkali resistant, only hydrofluoric acid can attack it. It has a bright sound, insulates well against electricity, and is a poor conductor of heat. In addition, it does not have any particularly abrasive properties, which is why this material is preferred, among other things, in the manufacture of mortars .
etymology

The term "porcelain" goes back to the Italian name for the cowrie snails (Cypraeidae), also called porcelain snails . The Europeans heard about Chinese porcelain for the first time through the travel report Il Milione by Marco Polo , because it describes objects made of a noble white material that the Chinese used as tableware. In addition, he gives some information about its production and is said to have brought the first Chinese porcelain to Europe. In 15th century Italy it was believed that it was made from the crushed yellowish-white shells of cowrie shells, which in Italian were called porcellana . This goes back to porcellino , actually "piggy" (porcellus) , diminutive of porco "pig", for the external sexual organ of the woman, as the shape of the snail shell reminds of it, just like in comparison with clams (concha veneris) .
production
The production process for items made of porcelain can be divided into several steps, each of which is interrupted by a fire. Depending on the desired result, not every step is always necessary, but the rule is at least two fires. Various manufacturers also use the single-firing process (monobrand) in industrial series production, where the blank is provided with glaze and, after drying, is fired in a rapid- firing tunnel kiln for 5 to 8 hours at 1100 ° C to 1200 ° C. This process reduces energy consumption, but is extremely prone to problems with regard to the quality of the glaze.
Manufacture of the blank
Depending on whether in automatic lathes plate or casting green bodies for example, cans , boxes , figures are to be prepared, the prepared after a certain mixing ratio porcelain paste is compact and flexible or liquid or slurry processes. For modern dry presses, granules with a defined grain size and moisture content are produced from the liquid porcelain mass.
When processing the liquid mass, it is poured into molds that determine the external shape of the workpiece , but have no core - they are hollow. This process is called slip casting . The molds can consist of many individual parts and accordingly have many planes of division in order to create complex pieces. However, two-part shapes with a dividing plane are common, for example, for cups, vases and other axially symmetrical hollow parts. The forms are made of plaster of paris , which has the property of being able to draw in water. This removes the water from the porcelain mass in the edge area and the solid components of the mass are deposited on the mold walls. The longer the mass remains in the mold, the thicker the remaining surface layer becomes. Once the intended thickness has been reached, the remaining liquid mass is poured out of the mold. After a certain rest period, the mold can then be opened and the parts removed for final drying. Then they are deburred before the first firing and, if necessary, otherwise repaired, handles can be glued on with slip .
Since the second half of the 1990s, flatware made of porcelain granulate has been pressed dry using isostatic dry presses. For hollow tableware, the so-called injection molding process - similar to plastic molding - injects liquid porcelain mass into plastic molds under very high pressure. These shapes are porous and drain the water from the slip. As a result, after a few minutes, a soft blank, which is sufficiently firm for further processing, "grows" on the mold wall and has to be carefully dried.
Biscuit firing
After the production of the blank, an 18 to 20-hour biscuit firing takes place at 900 ° C to 1000 ° C, during which a porous, relatively sensitive body is created. This process is also known as incandescent or biscuit firing.
Typical for this fire is a "shrinkage" of the work pieces, which explains a peculiarity and difficulty of porcelain production. Different temperatures during the fire can lead to different or even uneven shrinkage and thus endanger the dimensional accuracy of the pieces. While this used to be an enormous problem depending on the size and shape of the objects and required a great deal of knowledge and experience in production, today electronically controlled ovens and new casting processes for the blanks provide a certain, but by no means complete, defusing of the problem. Overall, a porcelain portion shrinks by 12 to 15 percent compared to the raw dimensions.
glaze
The porosity after the first firing ensures that the following glaze can bond well with the piece. After glazing, the final firing takes place, during which the glaze melts and covers the body with a decorative and protective outer skin.
The glaze liquid is a very complex mixture of substances that has to be carefully matched to the respective porcelain, the intended firing temperature and furnace atmosphere as well as the properties desired later. A glaze can easily contain ten or fifteen different ingredients.
Depending on the desired decor, color bodies, engobes or coloring metal salts can be applied under, in or on the glaze in various intermediate steps . One speaks of overglaze decor , inglaze decor or underglaze decor .
Burnout
The burnout , also high fire , takes place, depending on the type of porcelain, at temperatures between 1100 ° C and 1480 ° C for about 8 to 16 hours in chamber furnaces. Today, industrially manufactured porcelain is driven through a tunnel kiln or kiln that is 40 to 80 meters long, depending on its capacity, in 80 to 120 minutes . Smooth and decor firing are usually combined with one another. This does not apply to "difficult" decors, where color mixes must not influence each other, as well as to metallic high-gloss decors such as a gold rim. Sintering is an essential feature of the smooth firing of the porcelain . This softens (melts) the fired porcelain shards.
decor
Depending on the requirements, the pieces can be used directly after the burnout as pure white porcelain or porcelain with an underglaze decoration.
The so-called inglaze became widespread , with the decoration being applied in further processing steps. This can be done either by applying prefabricated, printed decorative foils or by hand painting ( porcelain painting ). It is also common to decorate with decorations made of precious metals such as gold or platinum.
The highest quality form of decor application is usually carried out by porcelain painters , manufactory porcelain painters or, for particularly valuable individual pieces, by porcelain plate painters .
Decor firing
Depending on the type of decoration, one or more decoration firings can follow at comparatively low temperatures of approx. 850 ° C., each of which is preceded by a corresponding decoration step. In the case of high-quality hand-painted reproductions of paintings on porcelain plates, more than five intermediate firings can be carried out, which firmly bond the individual layers of paint to the glaze. At higher decor firing temperatures, so-called hot fire colors are used.
This is another typical feature of porcelain production. It consists in the fact that the real colors of the decor only appear after the firing and often show no resemblance to the color before the decor firing. It requires from the painter experience and anticipation skills in addition to talent and manual skills to foresee the final colors of the future picture already while painting.
Health risks in porcelain production
The efforts of occupational health and safety in the field of porcelain production primarily concern the prevention of dust exposure through breathing apparatus to prevent the development of mesothelioma , measures against the development of dermatoses and protection against cobalt-induced diseases.
history
The invention of porcelain in China
Although early forms of ceramics have existed since the Shang period (1600 BC ff), the production of so-called proto-porcelain, the mass of which already contained kaolin, can only be dated to the time of the Han dynasty around the turn of the times. From this time bulbous vessels without necks and vases are known. Another significant development took place in the Tang period , when experiments were carried out with the composition of the mass, the construction of kilns and the fuel material improved - at the end of the 8th and beginning of the 9th century. This enabled the fire to take place at high temperatures (1350 ° C), which made the clay mass very hard, dense and translucent. The pieces (small bowls, jugs and kummies) had feldspar- based glaze . Dingyao goods from the Song era with a cream-colored glaze, which were decorated with a carved or later pressed relief decoration, are famous . Hard porcelain with cobalt blue underglaze painting has been made in China since the beginning of the 14th century and exported to Europe since the 16th century, where it enjoyed a very high reputation and became very popular. The most important center for the production of porcelain in China has been Jingdezhen since the Ming period , where imperial (but also private) kilns were located, all porcelain objects were produced for the imperial court, which since the Xuande period with the six-digit imperial stamp in standard script (since Qianlong partly also in seal script ) were provided.
The individual raw materials and processes were kept secret for a long time. Chinese porcelain can contain the basic components known today kaolin, feldspar or petuntse and quartz. The manufacturing process and, in the 18th century, the decors served as models for European porcelain. However, the term porcelain in China is very broad and reflects more the German terms ceramic and stoneware . According to our own representations, a distinction is only made between hard and soft fired body. In addition, the bright, clear, bell-like sound that is typical for porcelain, which is produced when you strike it lightly, is used as a criterion. The color, thickness and density of the body are rather insignificant. So it is quite possible that semi-porcelain, such as majolica and faience , or white-burning porcelain stoneware can count as porcelain.
The invention of the European hard porcelain

On January 15, 1708, Johann Friedrich Böttger and Ehrenfried Walther von Tschirnhaus succeeded in producing the first European hard-paste porcelain in the maiden bastion of the Dresden Fortress. After Tschirnhaus' death, Böttger further developed the process in Meißen and Dresden. On March 28, 1709 he announced the invention of European porcelain in Dresden. From June 6, 1710, the first European porcelain production facility was set up in Meissen on the Albrechtsburg . The Meissen porcelain from the Meissen Porcelain Manufactory is still famous today. All porcelains from this production have had the trademark for Meissen porcelain, the "crossed swords", since 1722 . Due to the continuous production to this day, the “crossed swords” are often referred to as the oldest manufacturer's mark in use .
The second oldest porcelain factory in Europe was founded almost a decade after Meißen in Vienna. On May 27, 1718, Emperor Karl VI. the civil servant Claudius Innocentius du Paquier a "special privilege" for the production of porcelain within the Habsburg lands. The Viennese porcelain manufactory , which supplied the court and aristocracy with extremely high-quality services and ornaments, existed until 1864.
From 1718, porcelain factories were founded all over Europe. Very often this was done with the help of Meissen arcanists , but there were also re-inventions. In 1744 Dimitri Iwanowitsch Winogradow invented Russian porcelain, which from then on was produced in the Imperial Porcelain Manufactory in St. Petersburg . In Thuringia, in 1755 Georg Heinrich Macheleid achieved his goal through his own experiments.
Many of these factories had to stop their production at the turn of the 18th and 19th centuries. It was not until the middle of the 19th century that numerous new foundations took place due to kaolin deposits in Northern Bavaria, Upper Franconia, Upper Palatinate and Thuringia. At times up to 90 percent of German porcelain was produced there.
20th century
The 20th century in porcelain production is mainly characterized by increasing industrialization. The introduction of tunnel kilns and machines to manufacture simple parts streamline the production process and finally make porcelain a mass product. Due to the difficult production of complex shapes (jugs, handle cups) and the sometimes complex decoration, production cannot be fully automated to this day.
From the late 1970s onwards, market distortions led to a crisis in the German porcelain industry, triggered by social changes and cheap imports from other countries: The rapidly rising wages in Germany make the product expensive and many companies have no sales arguments to counter the cheap imports. From the mid-1980s to the present day there have been numerous plant closings, including a. the plants in Tirschenreuth , Waldsassen and Mitterteich , and company mergers, e.g. B. the SKV Porzellan Union, later Arzberg Porzellan GmbH, or the Sambonet Rosenthal Group. Some manufacturers also tried to counter the pressure of competition by relocating production abroad. The remaining manufacturers were forced to consolidate and streamline or realign their range.
In the last few years, there seems to be a slight trend reversal in the market: highly rationalized work processes, new sales concepts and the consistent focus mainly on the upper to luxury price segment have brought German manufacturers back to increasing sales.
Ming vase from the Yongle era (1402–1424)
Napoleon I , bisque, Sèvres , 1811
Meissen porcelain around 1900
Typical form of the 1950s: Arzberg "Form 2000", jug
Porcelain crucible with crucible shoe
Porcelain thaler as a gift to the employees of the Olympic Games in Munich 1972
regional customs
On a bachelorette party , it is a tradition to smash the porcelain brought by the guests in order to have it swept away by the bride and groom. This is considered a sign of the ability of the bride and groom to get through difficult times and problems together. The broken pieces are also said to bring good luck.
Museums
In addition to the porcelain departments of the large arts and crafts museums, independent porcelain museums are rare. Some of them are associated with companies such as Berlin , Meißen or Selb .
Museum of Meissen ART
The Museum of Meissen ART of the Staatliche Porzellan-Manufaktur Meissen GmbH today offers one of the largest collections of Meissen porcelain worldwide. At the same time, the visitor can experience the creation of Meissen porcelain in the most important stages of production up close. The manufactory's museum is open 360 days a year.
Dresden porcelain collection in the Zwinger
The Dresden Porcelain Collection in the Zwinger of Dresden , one of the museums of the Staatliche Kunstsammlungen Dresden is one of the most important and extensive special ceramic collections in the world. It includes around 20,000 exhibits of Chinese, Japanese and Saxon porcelain art. The holdings of early Meissen porcelain and East Asian products from the 17th and early 18th centuries are of particular importance . Since 2011, around 2000 items from the porcelain collection have been presented in the expanded, renovated rooms of the Zwinger. The New York architect Peter Marino created the designs for the new interior with a mixture of classic and modern.
Porzellanikon
The largest porcelain museum in Europe is the Porzellanikon in Selb in Upper Franconia and in Hohenberg ad Eger. The Porzellanikon is independent and offers, among other things, a complete overview of all porcelains of German-speaking provenance. The Porzellanikon Hohenberg - German Porcelain Museum and the Porzellanikon Selb - European Industrial Museum for Porcelain, the European Museum of Technical Ceramics and the Rosenthal Museum can be found on a total of 11,000 m² of exhibition space. In 2010, in the anniversary year of porcelain, the Porzellanikon presented "The King's Dream and Mass Goods - 300 Years of European Porcelain", the largest porcelain exhibition that ever took place on the Old Continent and presented an overview of 300 years of European porcelain history.
Grand Ducal Hessian Porcelain Collection
The Grand Ducal Hessian Porcelain Collection in Darmstadt documents the history of courtly porcelain and faience art with over 4,000 objects - the holdings of the Kelsterbach and Frankenthal factories are published in an online catalog.
Wolfshagen Castle
In the castle museum of Wolfshagen Castle in Groß Pankow (Prignitz) is the Bernhard von Barsewisch collection, the largest porcelain collection of Central European blue painting.
Leuchtenburg
The Leuchtenburg in Thuringia houses the exhibition Porzellanwelten Leuchtenburg , which thematizes the European history of porcelain with a special focus on Thuringian porcelain and shows it in artistically staged worlds.
Transparent manufactory
On June 28, 2007 in Rudolstadt in the Volkstedt district (Thuringia) in the Aeltesten Volkstedter Porzellanmanufaktur, a "Transparent Factory" with an exhibition space of approx. 800 m² was opened. You can see historical and new things from the porcelain factories Volkstedt , Unterweissbach , Scheibe-Alsbach and Plaue .
Porcelain Triptis
The museum "1891 to today" documents the development of the Neue Porzellanfabrik Triptis since it was founded in 1891 and the changes in porcelain design from then to now.
See also
- Chinese porcelain
- Porcelain electrical insulators
- Technical ceramics
- Classification of ceramic bodies
- List of porcelain manufacturers and manufacturers
- Furnace sorting
- List of German porcelain makers (list)
- China money
- Porcelain brand
- Porcelain paint
- Porcelain painting
- Fürstenberg Castle Museum
- Porcelain Biennale
literature
- Gustav Weiß: Ceramic Lexicon: Practical knowledge at hand . Haupt, Bern / Stuttgart / Vienna 1998, ISBN 3-258-05871-7 .
- Sven Frotscher: dtv-Atlas: ceramics and porcelain . Deutscher Taschenbuch-Verlag, Munich 2003, ISBN 3-423-03258-8 .
- Julius Matusz: Porcelain: Considerations from the history of the oldest manufactories in Europe . Insel, Frankfurt am Main / Leipzig 1996, ISBN 3-458-33460-2 .
- Wilhelm Mrazek, Waltraud Neuwirth: Viennese porcelain 1718-1864 . Österreichischer Bundesverlag, Vienna 1970.
- Emanuel Poche: Porcelain Brands: Porcelain brands from all over the world . 13th edition. Dausien, Hanau 2002, ISBN 3-7684-1489-2 (translated from the Czech by Helena Krausová).
- Robert E. Röntgen: German porcelain brands from 1710 until today . Battenberg, Munich 2007, ISBN 978-3-86646-013-3 .
- Li Zhiyan, Cheng Wen: Ceramics and Porcelain in China: From the Clay Pot of the Stone Age People to Porcelain Art . Foreign Language Literature Publishing House, Beijing 1996, ISBN 7-119-01314-9 .
- Georges Le Gars: IMARI, histoire d'un style, faïences et porcelaines du Japon, de Chine et d'Europe . Massin, Paris 2004, ISBN 2-7072-0482-X .
- Otto Walcha: Meissen porcelain. From the beginning to the present . Verlag der Kunst, Dresden 1973, ISBN 3-570-01638-2 .
- Wolfgang Wüst (ed.): Industrialization of a landscape - the dream of textiles and porcelain. The Hof region and the Vogtland . WiKomm Verlag, Erlangen 2018, ISBN 978-3-940804-09-9 .
Web links
- Introduction to the historical development ( Memento of September 28, 2007 in the Internet Archive )
- PorcelainService manufacturer database for determining manufacturers and manufacturing locations based on the porcelain brand
- Determine porcelain brands with pictures of the floor brand
- Collect china
- Everything about porcelain in the catalog of the German National Library
- Search for porcelain in the German Digital Library
- Search for porcelain in the SPK digital portal of the Prussian Cultural Heritage Foundation
Individual evidence
- ↑ Brockhaus - the encyclopedia. Volume 17: PERU - RAG. Leipzig / Mannheim 1998, ISBN 3-7653-3117-1 , p. 391.
- ↑ Properties of porcelain. Retrieved September 22, 2018 .
- ^ Friedrich Kluge, Elmar Seebold: Etymological dictionary of the German language . 24th edition. Verlag Walter de Gruyter , Berlin 2002, p. 713. (Google book search)
- ^ Project information sheet of the German Federal Environment Foundation (PDF; 3.24 MB).
- ↑ MT Tsou, JC Luo: Porcelain factory worker with asbestos-related mesothelioma. In: J Formos Med Assoc. 108 (10), Oct 2009, pp. 819-825. PMID 19864204
- ^ MS Gabal, GA Helmy, R. Faris: Occupational dermatoses among workers in a porcelain manufacturing factory. In: J Egypt Public Health Assoc. 69 (5-6), 1994, pp. 425-438. PMID 17212008
- ↑ F. Tüchsen, MV Jensen, E. Villadsen, E. Lynge: Incidence of lung cancer among cobalt-exposed women. In: Scand J Work Environ Health. 22 (6), Dec 1996, pp. 444-450. PMID 9000312
- ↑ E. Prescott, B. Netterstrøm, J. Faber, L. Hegedus, P. Suadicani, JM Christensen: Effect of occupational exposure to cobalt blue dyes on the thyroid volume and function of female plate painters. In: Scand J Work Environ Health. 18 (2), Apr 1992, pp. 101-104. PMID 1604269
- ↑ Today around 20,000 pieces are in the possession of the Dresden State Art Collections, of which around ten percent can be shown. Jens-Uwe Sommerschuh: The best of the most beautiful. 1st edition. 2010, ISBN 978-3-7757-2458-6 , p. 117.
- ^ Museum "1891 to today" & gallery. Retrieved April 8, 2020 .