Drainage (mining)

In underground mining , all mine workings , rooms and technical facilities that serve to keep the mine building free of mine water are called water retention or mining water management . In addition, the miner describes the operating process of removing the pit water from the underground area as dewatering. In open-cast mining , the drainage of open-cast mines is called swamp. Efficient dewatering is of central importance in both opencast and underground mining .
history

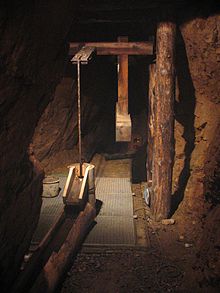
In early mining, water drainage was operated manually until the 13th century, and in some mountain areas even until the 16th century. For this purpose, miners were used as so-called water servants and they had to transport the water out of the mine using leather buckets, jugs, wooden buckets or pots . With this type of dewatering, mine structures with depths of 20 to 30 meters under the respective tunnel could be drained. However, this type of dewatering required a great deal of water servants. In some mines, there were often more servants involved in dewatering than there were diggers on site. In the Freiberg area, up to 2000 water servants were used to drain the pits. This was associated with high costs, which in turn reduced the proceeds.
The deeper the shafts became, the more difficult manual dewatering became. From the 14th century, special dewatering machines were used in mining. Initially, these machines were powered by human muscle power, and later by horses using horse pegs. The first water lifting machines used in mining were the Bulgenkunst and later the Heinzenkunst . From the middle of the 16th century, the pumping skills were used to keep water. The miners called these water-powered machines water arts . The water arts were practiced by means of a sophisticated system of ponds , artificial ditches and drainage tunnels.
For dewatering in Freiberg there as the Revierwasserlaufanstalt Freiberg , a system of reservoirs that from 1558 to 1882 for the mining industry in the Ore Mountains were built. From 1844 to 1884 the approximately 50 km long Rothschönberger Stolln was built, which was also used for drainage.
While ore mining used this system of dewatering for a long time, dewatering was very soon carried out in hard coal mining using steam engines . In the Ruhr mining industry, it was only possible to sink deeper shafts with efficient dewatering in order to mine seams at greater depths. The first steam engines were not used for pumping, but for drainage. The steam engine was arranged next to the shaft and the pump, which was arranged underground, was driven by means of a linkage that reached down to the shaft sump . This pump drive was very prone to failure, but for a long time it was the only technical possibility to discharge larger quantities of mine water. In modern mining, dewatering is carried out with powerful pumps. The entire dewatering is monitored at a central point .
Basics
The pit water, which is present in different quantities in the mine workings, creates a difficulty in mine operation that the miner has to overcome in order to be able to exploit a deposit . This requires dewatering, which is used to either raise or otherwise divert or shut off the pit water in order to ward off water ingress and seepage. Specifically, all measures are technical and organizational precautions to keep sunk shafts and mines usable both under the impact and groundwater influence. The miner uses various methods for this.
The dewatering of a mine plays a special role both for the operational phase and for the decommissioning phase as well as for the post-mining phase. Particularly in the case of a mine in the operating phase, dewatering is an existential task for the mine operation in addition to ventilation . Without a continuously functioning dewatering system, shafts and mining systems will quickly drown and become unusable and have to be swamped to make them usable again.
Salt mining , which excludes the use of hydropower in the mine , places special demands on dewatering . Because of the dangers of leaching out of the salt deposits, the ingress of water must be prevented here, and the raising of the groundwater makes special demands. If these requirements are neglected, the break of the day with catastrophic consequences can occur, as in August 1977 in Wapno, Poland .
Methods of drainage
The miner uses various procedures and methods for dewatering, whereby the miner differentiates between water solution and water uplift . For this he uses various techniques. On the one hand, the dewatering of a mine is done by damming or holding back the water so that it cannot penetrate the mine workings. Another measure is to use the natural runoff of the water via water florets or water solution tunnels . Ultimately, there is still the removal of the water from the mine building using vessels or pumps
Water solution
A water solution is all the precautions taken to keep the water away from the mine workings. The use of the natural water runoff also serves the water solution. This method is mainly used to ensure that the rainwater does not get into the underground area via the mine’s daily openings . For this purpose, the water is largely prevented from entering the pit by drainage or ditches. In order to prevent the groundwater from entering the shaft, a waterproof shaft lining is used in very water-rich mountains . Underground mines with a strong water inflow are separated from the rest of the mine by means of special water retention dams .
Water lifting
The water uplift serves to remove the accumulated water , especially in civil engineering . The water has to be lifted out of the mine so that it can either flow off via a water solution tunnel or is transported directly to the surface. Different methods are used for this. While methods such as drawing or scooping water were primarily used in mining until the 19th century , pumps are almost exclusively used in today's mining for dewatering. To remove heavily silted mine water, a method is still used in today's mining that is very similar to pulling water.
Pulling water
Water pulling was used to raise water with little work in manholes and blind manholes. In blind shafts, tall buckets or elliptical barrels are used as vessels, which are pulled up and down in the blind shaft with a reel . In the blind shaft sump, these vessels tip over automatically as soon as they have reached the water level and fill with water. Then they are pulled back up to the sole with the reel and emptied by tipping over. In day shafts, water barrels or water dogs were used as vessels . These vessels are equipped with automatic valves on the bottom, which open when immersed in water due to the water pressure. This allows the water to flow into the vessel. When the vessel is picked up, the valve closes automatically. For days, the vessel is emptied by opening the valve or by overturning the vessel.
Get water
When scooping up water, the water is scooped up manually with cans or buckets or with a throwing shovel. Since a man can only draw up to 150 liters of water per minute, this procedure was only used for small amounts of water. As a rule, the water was shut off by a dam about one meter high so that it could not run into the miners' work area. The water was manually scooped out of the place and poured behind the dam. In modern mining, this method is only used with very small amounts of water, when the use of a pump cannot be carried out so quickly. For this purpose, the water is scooped up in trolleys and transported away.
Drainage according to location
Drainage in underground mining
The dewatering in underground mining is designed differently, depending on whether the mineral resources are mined in tunnels or underground . The effort that has to be made to remove the mine water from the mine workings depends on the amount, the depth and the hydrogeology and the size of the respective mine field . It is also decisive for the effort whether the pit water can flow naturally from the mine or whether it has to be raised to a higher level.
Drainage in tunnel construction
In the tunnel construction, dewatering takes place through natural water solution. So that the water can flow out of the tunnels, the tunnels are usually driven with a slight incline. In the bottom of the tunnel, a water slope is created on one side of the tunnel, through which the pit water can run off through the natural gradient. In addition, additional auxiliary tunnels , so-called water solution tunnels , are being created, which only have the task of dewatering the tunnel system. The pit water is channeled from the upper tunnels via internal connections to the lower-lying water solution tunnels, from where it is diverted through the tunnel mouth hole into the nearest river.
Drainage in civil engineering
In civil engineering, dewatering is much more complex than in tunnel construction. In the mining operations and equipment operations , the resulting water runs into special wells, so-called pump holes, from where it is pumped through a pipeline to the next pump station. Any pit water that arises from the main lines is also collected in a pump hole and pumped out, in some cases via water bodies. The same happens with the water from the shafts and blind shafts. The pit water is pumped to the main water holding system via a complex system of pumping stations (so-called intermediate water holdings), which are connected via a pipeline network. In the swamp areas , the water is first collected and then, if necessary, pumped out for days.
Mine structures for drainage
Which and how many mine workings are required for dewatering depends primarily on the type of underground construction and the amount of incoming mine water. The simplest form of dewatering can be found in tunnel construction. The tunnels used for tunnel construction can still be used when the mine goes over to civil engineering. By using the water solution tunnel, the lifting height of the dewatering machine is reduced. In civil engineering, several pits are required for drainage. There is a swamp section and a shaft sump for collecting mine water . The pump chamber is used for the underground installation of the drainage machines . In the case of deeper mines, it may also be necessary to create certain pit structures for drainage on several levels. For lignite Tiefbauen drainage routes are in the beginning from degradation deposit ascended , so that the coals may be drained planned in advance. So that every mine in a mining area does not have to build its own water retention system, there is the option of directing all water inflows from the mines concerned underground to a large central water supply and lifting the pit water there. This also enables the number of discharge points into open waters to be significantly reduced. This measure is carried out in particular in the case of disused mines in a mountain area, by combining the discarded mine workings into so-called water provinces, in which the water is collected and fed to a central dewatering location, where all the water is pumped over the surface. This is particularly possible because the mines are hydrologically connected to one another due to the scratched mountains and old pits.
Drainage in the open pit
In open-cast mining , the type and scope depend on the amount of water that arises and the natural resources to be extracted. In lignite mining, depending on the region, between 0.5 and 1.4 billion cubic meters of swamp water is pumped out and channeled into the waters. In the 19th century, a tunnel was excavated from the side into the deepest point of the opencast mine, through which the dewatering of the opencast mine took place. Smaller opencast mines were drained with simple water siphons if water only temporarily accumulated. In the case of larger opencast mines, drainage shafts were created, which were then connected to the opencast mine by means of swamp stretches. Today, various forms of well systems are built in open-cast lignite mining, through which the groundwater is pumped out. These wells are usually created at the deepest points of the deposit. Filter wells, suction wells and seepage wells are built as wells. In many cases, special sealing walls are used to hold back the water. Vacuum drainage is used for fine sandy, silty loose rock. Here, special filter lances are driven into the loose soil to a depth of 6 meters at regular intervals, through which the water is then sucked off with a vacuum pump . In the stone and earth industry, dewatering is less expensive than in open-cast lignite mining. In particular, the removal of gravel and sand that occurs extraction of raw materials common in the wet process, so that no drainage is required. The minerals obtained are then dewatered in a processing sieve in the subsequent processing. The treatment water is then returned to a nearby body of water. When quarrying rocks, only a small amount of dewatering is usually required in the deepest part of the quarry in order to pump out any surface water and, if necessary, groundwater that penetrates the pit from crevices.
Drainage after mining has ended
After the underground construction is finished, the drainage cannot be shut down easily. This is due to the fact that water flows through gaps and through the loosened old man into the neighboring and still operating mines. Tunnels used as water-dissolving tunnels in tunnel construction will always remain water-dissolving tunnels. In civil engineering, for example in the Ruhr area, drainage must also be maintained at disused mines. For this purpose, underground areas in the individual districts are divided into water provinces. The pit water can either be pumped out conventionally using pumps installed underground or by means of well water holdings in which the pumps are lowered from above ground through a pipeline to the water level and with which the water is then pumped out. The German hard coal AG operates at several disused mines pit dewatering: Carolinenglück colliery , coal mine Peaceful neighbor , mine Robert Müser (all Bochum) Lohberg (Dinslaken), Mine Prince Leopold (Dorsten), coal mine Hansa (Dortmund), coal mine Walsum (Duisburg) , Zeche Amalie , Zeche Heinrich , Zeche Zollverein (all Essen), Zeche Haus Aden (Hamm), Zeche Concordia (Oberhausen). At certain locations, a shaft with a service facility is kept open in order to have access to the underground pumps. Thus, after the entire Ruhr mining industry has ceased, the drainage system can and will continue to be operated as part of the perpetual burdens . However, the number of locations is to be reduced to six in the long term. In the case of opencast mining, the dewatering is stopped after the mining has ended and the area overflows with groundwater or it is partially flooded with river water, so that a residual opencast lake is formed.
Drainage costs
The costs for dewatering are different in the respective mountain areas . They are made up of various factors. Most of the cost is spent on energy. Added to this are the costs for the maintenance and repair of the systems as well as the costs for the interest and the repayment of the investment capital. The costs increase with the supply of mine water. In addition, they rise with increasing depth. The composition of the mine water has a further influence on the costs, as this, depending on the chemical composition, can severely impair the service life of the water lifting machines and pipelines. In addition to the direct costs for dewatering, there are also indirect costs, which can be seen as additional costs, e.g. B. by maintaining the affected pit areas. In addition, there are costs for waterproof clothing for the miners working in the respective areas and payment of water money . High dewatering costs combined with poor production inevitably lead to poor operating results for the mine concerned. In the German hard coal mining regions, the costs of dewatering the closed mines are perpetual costs.
literature
- FP Springer: From Agricola's pomps in the mining industry, which pulls the water through the wind, to the rod pumps in oil production. Erdoel-Erdgas-Kohl, Issue 10, 2007, pp. 380–386.
Web links
- Principle of drainage
- The water problem of the old mines
- Manuscript of a radio report about the central drainage of the RAG
- Spektrum .de: After hard coal comes water on December 19, 2018
Individual evidence
- ^ Heinrich Otto Buja: Engineering handbook mining technology, deposits and extraction technology. 1st edition, Beuth Verlag GmbH Berlin-Vienna-Zurich, Berlin 2013, ISBN 978-3-410-22618-5 , p. 389.
- ^ A b c Heinrich Veith: German mountain dictionary with evidence. Published by Wilhelm Gottlieb Korn, Breslau 1871.
- ^ Joachim Huske: The coal mining in the Ruhr area from its beginnings to the year 2000. 2nd edition, Regio-Verlag Peter Voß, Werne, 2001, ISBN 3-929158-12-4 .
- ^ A b Rolf Dieter Stoll, Christian Niemann-Delius, Carsten Debenstedt, Klaus Müllensiefen: The open- cast lignite mine. 1st edition, Springer Verlag, Berlin Heidelberg 2009, ISBN 978-3-540-78400-5 , pp. 93-107.
- ↑ a b Peter Goerke-Mallet, Frank Mersmann, Thorsten Beermann, Max Thomas Stöttner: Optimizing the long-term dewatering of mining operations with the help of long, directed boreholes and pipe liner technology. In: Mining Report Glückauf: Gesamtverband Steinkohle eV (Ed.), Bergbau-Verwaltungsgesellschaft mbH Verlag, 152, No. 2, Essen 2016, pp. 171–177.
- ^ A b J. B. Maner: Attempt at an encyclopedia of mining art. Printing and publishing by Rud. Friedr. Hergst, Coblenz 1840, pp. 163-174.
- ^ A b Marcus Dehler: Water management in historical mining. Online (last accessed on October 8, 2012; PDF; 1.3 MB).
- ↑ a b c d e f g Albert Serlo: Guide to mining science. Second volume, fourth revised and up to the most recent edition supplemented, published by Julius Springer, Berlin 1884, pp. 504-516.
- ^ Freiberg Revierwasserlaufanstalt. Online (accessed on January 21, 2016; PDF; 290 kB).
- ↑ The book of inventions trade and industry. Fifth volume mining and metallurgy, publishing and printing by Otto Spamer, Leipzig 1899.
- ↑ a b c d e f g h Association for mining interests in the Oberbergamtsiertel Dortmund (ed.): The development of the Lower Rhine-Westphalian hard coal mining in the second half of the 19th century. Volume IV, extraction work - water management, Springer Verlag Berlin, Berlin 1902, pp. 8, 113–121, 127–132.
- ^ Conrad Matschoss: The development of the steam engine. A history of the stationary steam engine and the locomobile, the ship engine and the locomotive; First volume, published by Julius Springer, Berlin 1908, pp. 29–33.
- ↑ A. Hörmann: The new dewatering machines on the Dechenschächten near Saarbrücken, the civil engineering plant in Rüdersdorf and the Ferdinand mine near Katowice. Verlag von Ernst & Korn, Berlin 1874, pp. 2–11.
- ↑ a b RAG Aktiengesellschaft (ed.): Tasks for eternity. Mine water management, polder measures and groundwater management in the Ruhr area. Herne 2016, pp. 9–11, 13.
- ↑ a b Hans-Ulrich Tschätsch: Coal mining: RAG is and remains active. " In: GeoResources Portal Manfred König (Ed.): GeoResources Zeitschrift, specialist journal for mining, tunneling - geotechnics and equipment, No. 4, 3rd year, Duisburg 2017, ISSN 2364-8414, pp. 53-55.
- ↑ a b c Horst Roschlau, Wolfram Heinze, SDAG Wismut (Hrsg.): Knowledge storage mining technology. 1st edition. German publishing house for basic industry, Leipzig 1974, pp. 135-139.
- ↑ a b c d e Gustav Köhler: Textbook of mining science. Sixth improved edition, published by Wilhelm Engelmann, Leipzig 1903, pp. 341, 342, 641–643.
- ↑ Carl Hartmann: Concise dictionary of the mountain, hut and Saltwork science of mineralogy and geognosy. Third volume, 2nd edition, Bernhard Friedrich Voigt bookstore, Weimar 1860.
- ↑ Stefan Uhlig, Rolf Stoll, Perry Arnswald, Saxon State Office for the Environment - Agriculture and Geology (ed.): Improving water quality in mining areas. LfULG series of publications, Issue 15, Dresden 2014, ISSN 1867-2868, pp. 12, 13.
- ↑ a b c d e f g h i j Carl Hellmut Fritzsche: Textbook of mining science. Second volume, 10th edition, Springer Verlag, Berlin / Göttingen / Heidelberg 1962, pp. 642–677.
- ^ Carl Hellmut Fritzsche: Textbook of mining science. Second volume, eighth and ninth completely revised edition, Springer Verlag, Berlin / Göttingen / Heidelberg 1958, pp. 520–523.
- ↑ Anja Hoffmann, Maja Lange, Anna Sophia Asbeck-Wienemann, Britta Handke: About underworlds. Signs and magic of the other room. Educational project of the LWL-Industriemuseum for the exhibition. In: LWL-Industriemuseum Westphalian State Museum for Industrial Culture. (Ed.), Dortmund 2014, p. 24.
- ^ A b Albert Serlo: Guide to mining science. Second volume, 3rd edition, published by Julius Springer, Berlin 1878, pp. 394–405.
- ↑ a b c d e f Fritz Heise, Fritz Herbst: Textbook of mining studies with a special focus on hard coal mining. First volume, fifth increased and improved edition, published by Julius Springer, Berlin 1932, pp. 692–704.
- ^ Emil Stöhr, Emil Treptow : Basics of mining science including processing. Spielhagen & Schurich publishing house, Vienna 1892.
- ^ BW Boki, Gregor Panschin: Bergbaukunde. Kulturfond der DDR (Ed.), Verlag Technik Berlin, Berlin 1952, pp. 573-578.
- ^ Carl Friedrich Richter: Latest mountain and hut lexicon. Second volume, Kleefeldsche Buchhandlung, Leipzig 1805.
- ↑ a b c d e f Isabelle Balzer, Markus Roth: Mine water management in the Ruhr area - a task for eternity. In: GeoPark Ruhrgebiet News. GeoPark Ruhrgebiet eV (Ed.), No. 2, Essen 2017, pp. 4–8.
- ^ Carl Hartmann: Handbuch der Bergbaukunst. Second volume, Verlag Bernhard Friedrich Voigt, Weimar 1852.
- ^ A b c d Walter Bischoff , Heinz Bramann, Westfälische Berggewerkschaftskasse Bochum: The small mining encyclopedia. 7th edition, Verlag Glückauf GmbH, Essen 1988, ISBN 3-7739-0501-7 .
- ↑ a b c d RAG Aktiengesellschaft (ed.): Concept for the long-term optimization of pit water management by RAG Aktiengesellschaft for North Rhine-Westphalia. Herne 2014, pp. 5–11, 17, 18, 25.
- ↑ a b Federal Association of Brown Coal: Lord of the Thousand Pumps and Pipes (accessed on June 10, 2016).
- ↑ Andreas Berkner, Tobias Thieme (ed.): Brown coal planning, post-mining landscapes, water balance rehabilitation. Analyzes and case studies from the Rhenish - Central German and Lusatian regions, Academy for Spatial Research and Regional Planning, ARL working material, No. 323, Hanover 2005, pp. 1, 2.
- ↑ Volker Patzold, Günter Gruhn, Carsten Drebenstedt: The wet mining. Exploration - extraction - processing - evaluation, 1st edition, Springer Verlag, Berlin / Heidelberg 2008, ISBN 978-3-540-49692-2 , pp. 179-199.
- ^ Hessian State Office for Environment and Geology (ed.): Raw material security concept Hessen. Technical report natural stones and natural stone, volume 15, Hessen 2006, p. 59.
- ^ Günter Maier: Water-bearing tunnels - a main component of the old mine renovation. In: 12th Mining Forum . Conference proceedings, Leipzig 2013.
- ^ A b RAG Aktiengesellschaft (ed.): Pit water in the discussion. Optimizing mine water management - why are we doing this? Herne 2015.
- ↑ a b WDR.de: Coal long-term costs higher than expected (last accessed on November 8, 2012).
- ↑ Ralf E, Krupp: Effects of groundwater management in the Rheinisches Braunkohlerevier on the topography and the groundwater levels, as well as the resulting consequences for buildings, agricultural areas, infrastructure and the environment. Study on behalf of the Bündnis 90 / Die Grünen parliamentary group in North Rhine-Westphalia, Burgdorf 2015, pp. 45–66.
- ↑ a b c Ernst-Ulrich Reuther: Textbook of mining science. First volume, 12th edition, VGE Verlag GmbH, Essen 2010, ISBN 978-3-86797-076-1 , pp. 45, 54, 213.
Remarks
- ↑ The idea of channeling all mine water in the Ruhr area to the lowest point of the Ruhr coal basin (at this point in time this was the second underground floor of the Hugo I shaft, which was at a depth of 539.51 meters) to a central drainage system , in order to then divert it to this central point was planned and discussed in a commission towards the end of the 19th century, but was never implemented. (Source: Association for Mining Interests in the Upper Mining District Dortmund (Hrsg.): The Development of Lower Rhine-Westphalian Coal Mining in the Second Half of the 19th Century. Volume IV.)
- ↑ The water separated during treatment is mostly mixed with suspended particles. These suspended particles must be clarified before the water can be returned to a body of water. This can be done on specially created clarification fields or on sewage fields provided with vegetation . (Source: Volker Patzold, Günter Gruhn, Carsten Drebenstedt: The wet mining. )
- ↑ For this purpose, the respective mountain area is divided into several rooms (water provinces) that are connected to one another. The individual water provinces are modeled as boxes. In this so-called box model, all important data of the individual mines (operated or shut down) of the respective mining area, such as production rates, pumping levels, waterway connections, floodable cavity volumes and water levels are entered. The pit water quantities and currents as well as the flow paths can be simulated using the box model. This means that when the dewatering level is increased in one area, the effects on neighboring mine fields and dewatering can be analyzed. In addition, the number of discharge points can be reduced with the box model. (Source: RAG Aktiengesellschaft (Ed.): Tasks for Eternity. )
- ↑ Well water systems have the advantage that, in contrast to conventional water systems, they do not require an open pit building. (Source: RAG Aktiengesellschaft (Ed.): Concept for the long-term optimization of pit water management by RAG Aktiengesellschaft for North Rhine-Westphalia. )
- ↑ In the Ruhr and Saar districts, the RAG calculates a future annual amount of pit water to be pumped out of 110 million cubic meters. (Source: Hans-Ulrich Tschätsch: Hard coal mining: RAG is and remains active. " In: GeoResources Portal Manfred König (Ed.): GeoResources Zeitschrift.)
- ↑ The annual costs per 100 meters depth were in 1986, depending on the mountain area, per cubic meter of raised pit water between 25,000 and 50,000 German marks. (Source: Ernst-Ulrich Reuther: Textbook of Mining Studies. )