Water column machine
A water column machine is a machine that uses water power . It was first used to transport water from a mine. Water column machines were also used to drive the art of driving . In addition to its use as a prime mover in mining, the water column was also used in other areas. In the 19th century a water column machine was used to operate the bellows of an organ.
The English technical term for water column machine is "water column engine" or "water column machine".
history
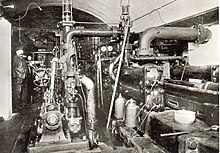

In 1731 the first water column machine was designed by the two clergymen de la Deuille and Denisart. On November 21, 1741, the engineer-ensign Georg Winterschmidt from the Principality of Wolfenbüttel submitted a promemoria about a water column machine he had invented to the mining authority in Clausthal . Subsequently, a contract was signed between the mining authority and the midshipman Winterschmidt for the delivery of a water column machine. After completion, the machine worked in a mine to the satisfaction of the mining authorities . In 1749 the head art master Josef Karl Höll used the principle of the Heronsball to convey mine water . This so-called air machine was put into operation in March 1753 on the Amali shaft in Schemnitz . However, the machine caused tremendous shocks and vibrations, so that even the shaft was affected. For this reason, the control of the machine was converted in 1808. In 1912 the original machine came to the Deutsches Museum in Munich, but was destroyed by bombing during World War II. A model of the "air machine" is at the Bergakademie Freiberg .
Development and use of the water column machines
Johann Friedrich Mende (1743–1798), art master and from 1778 the highest machine director of all Saxon mining offices, got to know the water column machine invented by Lieutenant Colonel G. Winterschmidt on a study trip to the Harz mining districts in 1767. Mende then had the first Saxon water column machine installed in the Siegfried mine in Riechberg near Freiberg from 1767–1769 . Between 1771 and 1777 Mende built three more water column machines in the Marienberg mining area. Mendes water column machines, however, still had considerable technical problems, especially leakage problems, so that they were initially not of great importance.
Christian Friedrich Brendel (1776–1861) was an art master and later the highest Saxon machine officer of the mining authorities and developer / designer of new / modified steam engines, water column machines and hut blowers. Brendel constructed four water column machines for Freiberg Gruben between 1816 and 1847. In contrast to those from Mende, the new "Brendel water column machines" proved their worth in the Saxon mining industry. Therefore, more water column machines according to Brendel have now been installed in other pits. The "Brendel piston control", invented 1820–1824 when a new water column machine was built in the Freiberg "Mordgrube" (murder pit), attracted international attention.
Brendel water column machines had a double-acting piston (impact water is applied alternately on both sides). The piston rod therefore had to be made of round steel (instead of square wood, as was previously the case), as it was fed through a stuffing box . With this, Brendel solved the problem of leaky piston seals. Any remaining leaks on the piston no longer played a major role. The tightness of the stuffing box, which was technically easy to implement, was important.
The climax and decline of the water column machines
The heyday of water column machines was in the second half of the 19th century. With the development of Brendel's piston control and the implementation of double-acting driving pistons by Christian Friedrich Brendel after 1820, water column machines became widespread in Saxon mining districts, among others. The introduction of the flywheel and air chamber further increased the smoothness and reliability of the operation. The great advantage of the water column machines in manholes was their small footprint. No large wheel chamber had to be chiseled out or blown out (which would have taken another 30 years by hand in the 18th century). But the most important advantage was the high efficiency of 70 to 90%. From 1880 the technology of water turbines was further developed ( Pelton turbine approx. 1880). Small, powerful and low-maintenance drives in the form of water turbines were now available, which could also drive centrifugal pumps and centrifugal pump cascades without any problems . When, with the introduction of alternating current in Germany from around 1890/1905, AC motors without grinder were finally available, the maintenance-intensive water column machines began to decline. Around 1900 ten water column machines were still working in the Upper Harz mining industry, the last of which ceased operations in 1924.
Basics
During the transition to civil engineering , the mine operators were faced with the problem of discharging the mine water. Especially in mines with a high proportion of mine water, the water wheels used to drive the water arts were often no longer sufficient to ensure effective dewatering . These machines had very poor efficiency . In the 18th century, the first steam engines were used to lift water in mines. These could not be used in the fuel-poor mining regions. Here the water column machines were an alternative to the pumping arts driven by water power . Particularly in the mining regions, where only small amounts of impact water , but a sufficiently large drop height was available, water column machines could be used to good effect. A water column machine takes up considerably less space than the water wheel cascades used and at the same time is more efficient. Water column machines had an efficiency of 83 percent, the overall efficiency with the connected pump was 66 percent. Towards the end of the 19th century, the power of the water column machines was between 75 and around 100 kilowatts.
construction
Every water column machine consists of a downpipe through which the impact water is introduced. The impact water is fed to the driving cylinder. There is a well-sealing piston in the drive cylinder . The piston is connected to several suction and pressure units or several art sets. There are single-acting and double-acting water column machines. In the single-acting machines, the return of the piston is achieved by its own weight or by a weight connected to the piston. In the double-acting machines, the return of the piston is brought about by the pressure of the impact water. The distribution of impact water is regulated by a controller. This control consists of two control devices. A device controls the alternating inlet and shut-off of the impact water. The other device connects the first control unit to the drive piston so that it moves without an additional drive. Initially a cock control was used, but this was soon replaced by a piston control. The control cylinders in the piston control each have two channels that allow the inflow and outflow of water to the drive cylinder. A rod with two control pistons is located in the control cylinder.
function
The principle of the perpendicular tubes is used as a drive in the water column machine . The hydrostatic pressure of the water column is used here. The height of the water column is the difference in height between the water level of the impact water and the runoff. The piston is moved back and forth in the drive cylinder through the alternating filling with impact water . The piston control opens the valves after the piston has been reset. The water is pushed out of the drive cylinder through an opening by the pushed back piston. In return, water flows in on the other side of the piston. Water column machines are so-called slow runners, they only have a cycle rate of four to eight cycles per minute. The pressure of the impact water could be 40 bar at a height of 400 meters . The impact water had to have a water level of 400 meters above the water level of the drain. A piston pump connected to the piston is moved by the movement of the piston . The pit water is then pumped out with this piston pump. The used impact water is discharged through the water dissolution tunnel .
Problems in use
The operational use of the water column machine often turned out to be problematic in the first few years. The main cause of malfunctions on the machines were leakage problems. The machine's piston seals were made from leather until the 19th century. This material was exposed to high operating pressures of up to 60 bar. The leather seals could not withstand these high operating pressures and continuous loads for long. Even with a modified version from 1755 with improved valve control, there were often control problems. In addition, the machines were often damaged due to the inelastic running. The further development failed because of the financial problems and the political dispute over competence. Only the more recent water column machines developed by Johann Karl Jordan in 1820 worked for several years without any complaints. With these double-acting two-cylinder machines of the type after Christian Friedrich Brendel , the smoothness of the machines was considerably improved. This improved running smoothness was achieved by generating a corresponding counter pressure when returning the impact water. The back pressure of the machine was generated by a machine chamber located lower down.
Increased running smoothness and avoidance of pressure surges
To reduce the pressure surges when the water flow is interrupted (impact water) when the taps / valves are reversed, slots were originally made in the taps or valves used in order to prevent the water flow from being completely interrupted from the outset. Later pistons were used as valves, which also contained slits / bevels or were conical as a whole. With the invention of Brendel's piston control for water column machines, there were practically no more pressure surges. Nevertheless, towards the end of the 19th century, air tanks were installed on the impact water pipes just before the shut-off valve of the water column machine in order to reliably avoid pressure surges. They were containers that contained compressed air above the water level. Further measures to increase the smoothness of the machines were the use of a flywheel and the installation of the water column machine below the level of the water solution tunnel in order to generate a counter pressure through the water column of the outflowing impact water, the so-called "back water column".
Brendel piston control
A typical problem with early water column machines was controlling the valves / taps . Since water, in contrast to gases / vapors, cannot be compressed, there is a risk of a strong pressure surge (water surge ) if the water flow in a long pipe is stopped abruptly (inertia of the water, the kinetic energy is converted into potential pressure energy). The short and very high pressure peaks can destroy lines, valves, cylinders and especially the piston seals. Until after 1820, the valves were usually controlled directly by the piston rods of the drive piston (working piston). The "Brendel piston control" invented by Christian Friedrich Brendel during the erection of a new water column machine in the Freiberg "Mordgrube" in 1820–1824 attracted international attention because it reliably prevents the occurrence of pressure surges, as the water flow is interrupted slowly by moving a large auxiliary piston to which a small valve piston is directly coupled with a short rod. The auxiliary piston and valve piston are in a separate housing.
The valve piston is no longer controlled by the piston rod of the drive piston (working piston), but directly by the pressure of the impact water, which, depending on the work cycle, is either on both sides of the auxiliary piston or only on the working side of the auxiliary piston. In the case of impact water on one side, the “working side” of the auxiliary piston is switched to a pressure-free state (opened to allow the trapped water to drain out of the auxiliary piston cylinder). An external three-way valve, which is controlled suddenly and directly by the piston rod of the drive piston, determines where the impact water was and whether the working side of the auxiliary piston is depressurized. The pressure difference of the impact water on the large-area auxiliary piston moves it together with the coupled small-area valve piston. The small-area valve piston allows the impact water to flow in and out of the drive piston (working piston). The valve piston is therefore a two-way valve.
Pressure surges in the water column cannot occur with the "Brendel piston control" for water column machines because briefly increased pressure in the water column (e.g. due to water surge) would move the auxiliary piston more quickly, which would counteract the pressure increase due to the increase in volume in the cylinder of the auxiliary piston (increasing Buffer volume). When the impact water flows in and out of the drive piston (working piston), the auxiliary piston stands still because the pressure of the impact water is applied simultaneously to its bottom and top. The valve piston, which is directly coupled to the auxiliary piston, is therefore now also at a standstill. So there are two temporarily "stable" states:
- Valve for filling the drive cylinder open (upward gear of the drive piston)
- Valve for emptying the drive cylinder open (downward gear of the drive piston)
and the two transition states that occur shortly before the end or start of a piston stroke (drive piston / working piston):
- Impact water valve closes slowly & drain valve opens slowly with a time delay
- Impact water valve opens slowly & drain valve closes slowly with a time delay
The pressure of the impact water is permanently present at the inlet of the three-way valve and also between the facing piston sides of the valve piston and auxiliary piston, which are coupled to one another by means of a short rod. During an entire work cycle (lifting / filling the drive piston / cylinder and lowering / emptying the drive piston / cylinder) the three-way valve is switched over abruptly twice before the piston rod of the drive piston has reached its full stroke and before it returns to the zero position (full emptying of the drive piston / cylinder). In the short periods of time before the drive piston / piston rod reaches the start and end positions, the control piston moves the valve piston and the latter gradually opens and closes the outflow and inflow of the impact water to and from the drive piston.
Before the end of the downward movement of the drive piston (emptying), the three-way valve is also reversed abruptly, so that the impact water is now on both sides of the auxiliary cylinder. Since the impact water is also on the small "inner surface" of the valve piston, the piston combination of auxiliary piston / valve piston now slowly moves in the direction of the valve piston, i.e. to "close the drain opening" and delay "release the filling opening" for the upward movement of the drive piston. If the impact water is on both sides of the auxiliary piston, there is only one stable position of the control piston / valve piston (drain opening closed / filling opening open for the upward gear: the upward gear of the drive piston begins).
Balancer
Water column machines that were located in deep shafts of mines often had a balancer . Were driving piston (piston) and pump piston for a very long wooden art linkage interconnected so this art boom had a considerable mass of several tons . Since lifting energy has to be used every time the rod is lifted, the water column machine would have had to “uselessly” this energy with every lifting process. The energetic efficiency of the water column machine would have dropped significantly. Braking might have been necessary during the downward movement (possibly also due to increased back pressure when draining the driving water from the driving cylinder, i.e. by throttling the flowing water or a counter water column). To prevent this, a balancer (counterweight) was coupled to each long piston rod or the counterweight was coupled to the upper end of the piston rod via a pulley on a rope. In the case of water column machines, balancers or counterweights were usually located in vertical shafts above the shaft in / near the hat house / winding tower . However, they can also have been arranged in underground chambers near the production shaft.
At that time, long artificial rods were usually made of square timber, which in the 18th and 19th centuries was much cheaper than long forged or rolled metal rods. The artificial linkage was only allowed to be subjected to tensile loads . Pressure load could have caused the wooden bars to sag and break. For this reason, too, the use of a balancer or counterweight was essential. The effective mass of the counterweight or balancer was always slightly below that of the boom to be lifted, because when the boom and the (single-acting) drive piston went down, potential energy had to be available to empty the drive piston .
The machines operated in Saxony under Mende and Brendel had a balance. From 1822 the balancer (the counterweight is meant here) in the "Reichenbach-Jordan water column machines" now used in mining was replaced by a so-called "rear water column" ("hydraulic balancer"). For this purpose, the driving pistons (working pistons) were arranged several meters below the level of the water-dissolving tunnel / hereditary tunnel . When emptying the driving piston (downward gear), the counter pressure of this water column (from the level of the driving piston up to the water solution tunnel) had to be overcome. The machines set up in this way also worked more evenly. This principle was later applied to all modern water column machines. As a result, the balancer was omitted from many machines after 1822.
Types of water column machines
piston-free | with driving piston (working piston) | |||||
---|---|---|---|---|---|---|
|
with flywheel (and braking device for it) | without flywheel | ||||
single acting piston | double-acting piston | single acting piston | double-acting piston | |||
|
|
|
|
|
|
Flywheels were used when the pendulum movement of the piston rod had to be converted into a rotating movement, for example for the operation of lifting skills and driving skills . Flywheels also stabilized the running of the machines.
Water column machines still preserved today
Brine lifting machines and Lambach drinking water pumps
- Bad Reichenhall : Brine lifting machine to Reichenbach : in the underground spring construction of the old salt works , to be visited during guided tours.
- Grassau : Brine hoist to Reichenbach: can be viewed in the Klaushäusl Museum .
- Munich : Brine hoisting machine to Reichenbach: in 1904 the brine hoisting machine was uninstalled by Pfisterleite (Berchtesgaden) and taken to the German Museum in Munich, to be viewed in the "Kraftmaschinen" exhibition on the ground floor. In the "Academy Collection" on the 1st floor there is a working prototype by Georg von Reichenbach.
- Traunstein : Brine lifting machine to Reichenbach: to be visited in the Salinenpark Traunstein .
- different locations: several Lambach pumps for pumping drinking water have been preserved and some of them have been restored to working order.
In Saxon mines
- Brand-Erbisdorf : originally preserved, approx. 17 m high water column machine (approx. 1800–1830) in the Mendenschacht of the Alte Mordgrube mine . Not open to the public.
- Brand-Erbisdorf : machine in the Hörnig shaft of the unity pit. Not open to the public.
- Gersdorf / Saxony : Show mine "Segen-Gottes-Erbstolln" with two still existing " Brendel water column machines " in the Joseph shaft , which are part of the tour.
- Großolbersdorf : Machine in the Heidelbach lime works in Großolbersdorf near Wolkenstein . Not open to the public.
- Zschorlau : machine in the door shaft . Not open to the public.
Models in museums
- In the Czech district museum Sokolov in Castle Sokolov is a model of a water column machine in the second half of the 19th century. In the pits of Jachymov was (Ore Mountains) in use. The model was built before 1918 by the mechanic and model maker Johann Tober at the Deutsches Landes-Polytechnikum (Royal German State Polytechnic in Prague?). This model shows the drive of a large two-course cable drum through this machine, for the conveyance of rock in buckets from a depth of several hundred meters. On this model, the cable drum and connecting rod with crankshaft are located directly below the "upside-down" working cylinder (driving cylinder). A second model in this museum, the shaft of the Kübeck coal mine in Kladno , at the beginning of the 20th century, also seems to contain a water column machine, but this is only called a "pump system".
- A model of the air machine by Karl Josef Höll is at the Bergakademie Freiberg .
- Model of the water column machine (with flywheel) of the Königin-Marien-Schacht in the Upper Harz Mining Museum in Clausthal-Zellerfeld .
Chronology of the inventors and developers
- 1731: the French clergy de la Deuille and Denisart invent a water column machine
- 1741: Ensign engineer Georg Winterschmidt , first self-developed water column machine put into operation in Clausthal / Harz, ran until 1760
- 1753: Joseph Karl Höll (1713–1789), pistonless "air machine" first tested in Schemnitz / Lower Hungary in 1753, ran there until 1808
- from 1769: Johann Friedrich Mende (1743–1798) builds the first water column machines with single-acting pistons in Saxony
- 1810: Georg Friedrich von Reichenbach , construction of a brine lifting machine / water column machine and application in the brine pipeline (Bad Reichenhall)
- from 1816: Christian Friedrich Brendel improves Mende's water column machines and later invents the double-acting piston
- 1817: Georg Friedrich von Reichenbach puts more of its own brine lifting machinery in the construction of the 25 km long brine line from Berchtesgaden to Bad Reichenhall a
- 1820: Johann Karl Jordan (senior) (1789–1861), from 1810 machine inspector in the Upper Harz mining district, further development / designs for water column machines with double-acting pistons based on the well-known brine lifting machines by Georg Friedrich von Reichenbach and Brendel's water column machines with piston control: " Reichenbach-Jordan water column machines ".
- 1820–1824: Christian Friedrich Brendel invents the "Brendel piston control"
- ? Mr. Jordan (jun.), Further development of the water column machines
- 1873: Albert Schmid presents a small "water motor" with a double-acting piston and flywheel at a world exhibition
- around 1880: Gottlieb Lambach (1838–1921) invents the Lambach pump , a water column machine for pumping drinking water. Founder of a machine factory in Marienheide-Oberwipper and construction / sale of the first "Lambach pumps" from 1898.
- 1880–1892: Karl Meinecke (1839–1920), further development of the water column machines, construction of two machines with air tanks in the Kaiser-Wilhelm-Schacht (Clausthal)
- 1932: Wilhelm Sauer, dead-point, counter-rotating water power machine with coupled air pump (aquarium aerator, laboratory air pump), Reich patent 543656. The Wuppertal company WiSa-Pumps emerged from the development, the water power pumps (former technical term "tandem pumps") were built until the 1960s and still are waited until 2004
See also
- Water motor, with animation of the drive piston of a double-acting water column machine (principle diagram without pumps)
- Brine hoist
- Brine pipeline (Bad Reichenhall) #Technology
- Lambach pump
Web links
- Animation of the functional principle of a Lambach pump (water column machine) (youtube video)
- Information page on Lambach pumps (water column machines from Lambach)
literature
- M. le Brun: MACHINE HYDRAULIQUE, INVENTEE PAR MESSIEURS DENISART ET DE LA DEUILLE, ECCLESIASTIQUES, PRESENTEE A LÀCADEMIE PAR M. LE BRUN . in: Machines et inventions approuvées par l'Académie Royale des Sciences depuis son établissement jusqu'à présent - 5.1727 / 31 (1735), Académie des Sciences Paris. Paris 1731, p. 159 ( digitized version - the water column machine by Denisart and de la Deuille (1731)).
- Nicolaus Poda von Neuhaus : Calculation of the air machine, which was invented and built in the Lower Hungarian mountain town of Schemnitz near the Amalia Schacht, by Mr. Joseph Karl Höll and started in 1753 on March 23rd. Vienna 1771 ( digital copy - description and calculations for Höll's air machine, an early water column machine).
- Friedrich Nicolai : General German library, the nineteenth volume first piece . tape 19 (first part). Berlin and Stettin 1773, p. 269–272 ( digitized version - description of the air machine by Josef Karl Höll in the Amalia shaft in Schemnitz ).
- Friedrich Gottlieb von Busse : Consideration of the Winterschmidt and Höll's water column machine along with suggestions for their improvement and occasional discussions about mechanics and hydraulics. Freyberg (Freiberg in Sachsen) 1804 ( digitized - description of the Höll air machine in the Amalia shaft in Schemnitz , an early water column machine without pistons, as well as the water column machine from engineer-ensign G. Winterschmidt in Clausthal / Harz).
- Franz Joseph von Gerstner : Manual of mechanics . Ed .: Franz Anton von Gerstner . tape 3 . JP Sollinger, Vienna 1834, Chapter XI. Water column machines, p. 355-424 ( digitized version ).
- Julius Weisbach : Textbook of engineering and machine mechanics, second part: practical mechanics . Friedrich Vieweg u. Sohn, Braunschweig 1846, 6. From the water column machines, p. 334–387 ( digital version - structure, description of the mode of operation, calculation and sectional drawings of water column machines).
- Johann Georg Krünitz : Economic Encyclopedia or general system of the state, city, house and agriculture . tape 81; 1773-1858 . Berlin ?, p. 453–457 ( digitized - description, illustration and function of the "air machine" by Joseph Carl Höll from 1753 in the Amali shaft in Schemnitz ).
- Walther von Dyck : German Museum, biographies and documents: Georg von Reichenbach . Self-published by the Deutsches Museum Munich, Munich 1912, (description of the working method and sectional drawings (Fig. 39 and 40) of both single-acting water column machines by Ilsank and Pfisterleite by Georg von Reichenbach ), p. 72-74 .
- Herbert Pfisterer: The brine line from Reichenhall to Traunstein 1617-1619 . Munich 1978 (descriptions of several Reichenbachsch brine lifting machines).
- Collective of authors: ABC Fachlexikon Researchers and Inventors . Brockhaus Verlag Leipzig GDR / Verlag Harri Deutsch Frankfurt FRG 1992, ISBN 3-8171-1258-0 . Leipzig / Frankfurt-Main 1992, p. 93–94 (Christian Friedrich Brendel p. 93-94, mode of operation of the Brendel water column machine piston control: illustration p. 94).
- Mathias Döring: 400 years of Upper Bavarian brine pipelines. Water management 4/2020, 12–18.
- Mathias Döring: Energy generation underground - The Reichenbach-Jordan water column machines . in: Christoph Ohlig: "UNESCO World Heritage Upper Harz Water Management" ( volume 19 ), ISBN 978-3-8482-0803-6 . Siegburg 2012, p. 39–59 ( digitized version - on the history of the development of water column machines in general and their use in Saxony, Bavaria and the Harz Mountains, as well as on Georg von Reichenbach, with information on many literature sources on water column machines).
Individual evidence
- ^ A b Carl Friedrich Richter: Latest mountain and hut lexicon. Second volume, Kleefeldsche Buchhandlung, Leipzig 1805.
- ↑ a b c d Wilfried Ließmann: Historical mining in the Harz. 3rd edition, Springer Verlag, Berlin and Heidelberg 2010, ISBN 978-3-540-31327-4 .
- ↑ David Joy: About a new water column machine. In: Polytechnisches Journal . 148, 1858, pp. 401-402.
- ↑ FM Feldhaus: The technology of prehistoric times, historical times and primitive peoples. Published by Wilhelm Engelmann, Leipzig and Berlin 1914.
- ↑ Collective of authors: ABC specialist lexicon researchers and inventors . Brockhaus Verlag Leipzig GDR / Verlag Harri Deutsch Frankfurt FRG 1992, Johann Friedrich Mende pp. 398–399, ISBN 3-8171-1258-0 .
- ↑ Collective of authors: ABC specialist lexicon researchers and inventors . Brockhaus Verlag Leipzig GDR / Verlag Harri Deutsch Frankfurt FRG 1992, Christian Friedrich Brendel pp. 93–94, How Brendel's water column machine piston control works, Figure p. 94, ISBN 3-8171-1258-0 .
- ^ Mathias Döring: Energy production underground - The Reichenbach-Jordan water column machines. In: Christoph Ohlig: "UNESCO World Heritage Upper Harz Water Management" (Volume 19), ISBN 978-3-8482-0803-6 . Siegburg 2012, information on Georg Winterschmidt's water column machines p. 39–40.
- ^ Mathias Döring: Energy production underground - The Reichenbach-Jordan water column machines. In: Christoph Ohlig: "UNESCO World Heritage Upper Harz Water Management" (Volume 19), ISBN 978-3-8482-0803-6 . Siegburg 2012, p. 53.
- ↑ a b c Franz Anton Ritter von Gerstner (Ed.): Manual of Mechanics. Third volume, printed by JP Sollinger, Vienna 1834.
- ^ A b Moritz Rühlmann: General machine theory . First volume, Verlag CA Schwetschke und Sohn, Braunschweig 1862.
- ^ A b Rolf Meurer: Hydraulic engineering and water management in Germany . Parey Buchverlag, Berlin 2000, ISBN 3-8263-3303-9 , p. 55.
- ↑ H. Schellen: The school of elementary mechanics and machine theory. Second part, printed and published by Friedrich Vieweg and Son, Braunschweig 1862.
- ^ Carl Stegmayer: Manual of mining art for everyone. Publishing house by JL Kober, Prague 1862.
- ^ FE Johannes Crüger: Basics of physics with regard to chemistry. Tenth edition, g. W. Körner's publishing house, Erfurt 1866.
- ^ A b Mathias Döring: Montane energy generation from hydropower in the Harz and Erzgebirge. In: Christoph Ohlig (Ed.): Water historical research with a focus on the mining sector. (Writings of the German Water History Society (DWhG) 3), Siegburg 2003, ISBN 3-8330-0729-X , pp. 41–46.
- ^ Mathias Döring: Energy production underground - The Reichenbach-Jordan water column machines. In: Christoph Ohlig: "UNESCO World Heritage Upper Harz Water Management" (Volume 19), ISBN 978-3-8482-0803-6 . Siegburg 2012, p. 46, Fig. 8: Control piston (valve piston) with slots to reduce pressure surges in the design by Georg Friedrich von Reichenbach from 1822.
- ^ Mathias Döring: Energy production underground - The Reichenbach-Jordan water column machines. In: Christoph Ohlig: "UNESCO World Heritage Upper Harz Water Management" (Volume 19), ISBN 978-3-8482-0803-6 . Siegburg 2012, p. 46, Fig. 8: Control piston (valve piston) with slots to reduce pressure surges in the design by Georg Friedrich von Reichenbach from 1822.
- ↑ Collective of authors: ABC specialist lexicon researchers and inventors . Brockhaus Verlag Leipzig GDR / Verlag Harri Deutsch Frankfurt FRG 1992, Christian Friedrich Brendel pp. 93–94, How Brendel's water column machine piston control works, Figure p. 94, ISBN 3-8171-1258-0 .
- ^ A b c d Mathias Döring: Energy generation underground - The Reichenbach-Jordan water column machines. In: Christoph Ohlig: "UNESCO World Heritage Upper Harz Water Management" (Volume 19), ISBN 978-3-8482-0803-6 , Siegburg 2012, illustration of the model of the former water column machine in the Kaiser Wilhelm II shaft in Clausthal / Harz in the Upper Harz region Mining Museum (designed in 1820), Figure 7 and others, pp. 7, 40, 45–48, 55.
- ^ Walther von Dyck: German Museum, biographies and documents: Georg von Reichenbach. Self-published by the Deutsches Museum München, Munich 1912, description of the working method and sectional drawings (Fig. 39 and 40) of both single-acting water column machines by Ilsank and Pfisterleite by Georg von Reichenbach, pp. 72-74.
- ↑ Mining monuments in the mining region Erzgebirge / Krusnohory, German / Czech, Karlovy vary district, Czech Republic 2014, p. 75.
- ^ Mathias Döring: Energy production underground - The Reichenbach-Jordan water column machines. In: Christoph Ohlig: "UNESCO World Heritage Upper Harz Water Management" (Volume 19), ISBN 978-3-8482-0803-6 . Siegburg 2012, information on Georg Winterschmidt's water column machines p. 39–40.
- ^ Mathias Döring: Energy production underground - The Reichenbach-Jordan water column machines. In: Christoph Ohlig: "UNESCO World Heritage Upper Harz Water Management" (Volume 19), ISBN 978-3-8482-0803-6 . Siegburg 2012, p. 55: The water column machines in the Kaiser Wilhelm Ii shaft (with air tanks).
- ^ Mathias Döring: Energy production underground - The Reichenbach-Jordan water column machines. In: Christoph Ohlig: "UNESCO World Heritage Upper Harz Water Management" (Volume 19), ISBN 978-3-8482-0803-6 . Siegburg 2012, p. 55: The water column machines in the Kaiser-Wilhelm-II shaft (1892–1924.)