Electric locomotive



Electric locomotives (short electric locomotives or electric locomotives , abbreviation: Electric Locomotive ) are locomotives of the railway , transport the payload itself does not (passengers, baggage or cargo). Their drive is purely electric , in contrast to diesel-electric , diesel-hydraulic or steam-electric locomotives, for example . Electric locomotives benefit from the high efficiency of the electric motors, which is often over 90%, without taking into account the inefficiency of power generation. Additional efficiency can be achieved through regenerative braking, which enables kinetic energy to be recovered during braking to bring electricity back onto the track. The main disadvantage of electrification is the high cost of the infrastructure: overhead lines or third rail, substations and control systems.
General overview

Electric locomotives are supplied with energy from overhead lines arranged above the track or, more rarely, from power rails , which is transmitted to the vehicle from pantographs arranged on the roof or on the side of the running gear in the case of power rails . This means that the energy required does not have to be carried in the vehicle, as is the case with steam and diesel locomotives.
The external electrical energy supply has the advantage that electric locomotives themselves do not emit any exhaust gases, but the disadvantage that they can only be used where there is a power supply. It is also an advantage that electric motors develop full torque when they start, in contrast to diesel locomotives, in which the torque builds up slowly when starting. This enables electric locomotives to accelerate faster or pull a somewhat heavier train than diesel and steam locomotives. Because of course the way the electricity is generated does not affect the electric locomotives, electric locomotives first spread to countries and regions where the use of electricity by e.g. B. Hydroelectric power plants is far cheaper than using coal or diesel. Switzerland, Austria and Sweden are countries where this requirement applies. The better acceleration, as well as the better ratio of power to mass as well as problems with exhaust gases in tunnels also contributed to an earlier spread of the electric drive method in these mountainous countries.
Some types of electric trains are electric power cars driven to be or run at the front and / at the end of the train and never disconnected during normal operation of the car. Technically, these are largely electric locomotives. The only difference is the equipment with only one driver's cab and the coupling and transition devices to the multiple unit intermediate cars. Examples of modern electric multiple units with multiple units are the first two generations of the ICE (ICE 1 and ICE 2), the Spanish multiple units of the 102 and 130 series , the first series of the Zurich S-Bahn and the French TGV trains. With the latter, however, in some series (TGV Sud-Est, Eurostar ) the first bogie of the intermediate car running directly behind the powered end car is also driven.
Examples of modern electric locomotive construction are Bombardier TRAXX , Siemens Vectron and Alstom Prima .
history
- An early experimental electric railroad track is attributed to Thomas Davenport , a blacksmith from Vermont, USA . In 1835 he demonstrated a small model of a railroad operated by an electric motor.
- Robert Davidson, a Scotsman in Aberdeen , is reported to have built an electric locomotive in 1838 that reached a speed of four miles per hour.
- The US patent clerk Charles Grafton Page (1812–1868) began building an electric locomotive in 1850. Its 15 kilowatt “piston” motor consisted of two coils with embedded rod anchors. These were moved back and forth by switching on the coils alternately like in a piston steam engine . This piston movement was transmitted to the drive wheels of a three-axle car with a connecting rod.
- In 1840, Johann Philipp Wagner, who was born in Fischbach near Bad Schwalbach, had a small car driven by an electric motor with a trailer on a track circle of 20 meters in circumference. He was then commissioned to build a functioning large "electromagnetically driven" locomotive and an amount of 100,000 guilders was made available to him. However, it failed to implement, allegedly due to a lack of knowledge about the relationship between battery capacity and drive power.
- The company of Werner Siemens built in 1879 for the Berlin Trade Fair biaxial electric locomotive that could pull three cars, each with six people on a 300-meter circuit. It is considered to be the first practical electric locomotive.
- In most early commercially operated electric railways first tram-like railcars were used, such as in 1881 when by Siemens & Halske first built electric tram to the main military academy in Gross-Lichterfelde near Berlin, in 1895, put into operation the first German electric standard-gauge railway Meckenbeuren-Tettnang in the former Kingdom of Württemberg and other railways.
- The first electric locomotive to be used in continuous operation was the “Dorothea” mine locomotive manufactured by Siemens & Halske in 1882 for the Zauckerode Royal Coal Works . It went into service on August 25, 1882, on a track length of 620 meters, and was in operation there until 1927. Here one gained experience u. a. with different pantographs and starting resistors.
- From 1890 onwards, electric locomotives were used on a remarkable scale on the London Underground. Above all, the limited space of the tunnel profile forced the abandonment of the railcar and the pre-tensioning of the drive in a separate vehicle at the head of the train. The City and South London Railway used the first electrically powered trains with locomotives. Until 1935, the London Underground ran on locomotives.
- In 1895 the first electric locomotive in regular gauge went into operation. The locomotive, built by General Electric , was used by the Baltimore and Ohio Railroad to haul passenger trains through the Baltimore city tunnel . No steam locomotives could be used on this route because of the smoke nuisance.
- 1901–1903 the study society for electric express trains carried out high speed tests on the military railway Marienfelde – Zossen – Jüterbog . The required three-phase current was fed to the vehicles via a three-pole overhead line . The power regulation did not take place in the locomotives, but in the power station. An AEG railcar reached a speed of 210.2 km / h.
- 1902 Opening of three-phase current operation by Rete Adriatica on the Valtellina Railway in Northern Italy. This is the world's first electrically operated main line. The locomotives came from Ganz in Budapest .
- In 1903 the ore railway Chemin de fer de La Mure starts electrical operation. The DC power is the locomotive with the modern Achsfolge supplied wheel arrangement via a double-pole contact line with +1200 volts and -1200 volts. The railway was not switched to normal single contact line with 2400 volts until 1950.
- In 1904 the narrow-gauge Stubaitalbahn from Innsbruck to Fulpmes went into full operation as the world's first single-phase AC train (3000 volts 50 Hertz).
- In 1905 the Ammergaubahn put the first single-phase alternating current multiple units ( LAG 674-677 ) and a few weeks later the first locomotive ( LAG 1 , later the E 69 series of the Deutsche Reichsbahn ) into operation. The voltage was 5.5 kilovolts 16⅔ Hertz. The changeover to the usual voltage of 15 kilovolts did not take place until 1950.
- From 1905 to 1909, the voltage of 15 kilovolts was used for the first time at the single-phase alternating current test facility in Seebach-Wettingen in Switzerland. At the beginning of these tests, 15 kilovolts were used at 50 Hertz. A rotating converter was used in the locomotive to convert the alternating current from the contact line into direct current. The traction motors were operated with this. In the further course of the trial operation, the frequency was reduced to 15 Hertz. This made it possible to dispense with the converter and the rail motors were operated with alternating current. In addition, the faults in the telephone network were rectified.
- In 1906 three-phase operation was started on the route through the Simplon Tunnel .
- In 1907 the Maggia Valley Railway started operating in southern Switzerland with 5 kilovolts and 20 Hertz. The engines of the railcars BCFe 4/4 were operated directly with alternating current, following the example of the Seebach – Wettingen test route.
- In 1910 the Berner Alpenbahn-Gesellschaft Bern – Lötschberg – Simplon (BLS) opened its test route Spiez - Frutigen with 15 kilovolts 15 Hertz, see BLS F 2x3 / 3 .
- 1911 the Austrian Mariazellerbahn starts electrical operation with 6.5 kilovolt 25 Hertz.
- 1911 Opening of operations on the Dessau – Bitterfeld line. First electric full-line railway in Germany, initially with 10 kilovolt 15 Hertz.
- In 1912, the Mittenwaldbahn, consisting of the Karwendel and Ausserfernbahn, was put into operation from Innsbruck to Reutte in Tyrol as the first Austrian full-line railway with 15 kilovolts and 15 Hertz. With the electrification of the Arlbergbahn , the network frequency was increased to 16⅔ Hertz.
- In the agreement on a common traction current system of 1912 , Germany, Austria, Switzerland, Sweden and Norway agreed on a common traction current system with a voltage of 15 kilovolts and a frequency of 16⅔ Hertz.
- 1913 Start of continuous electrical operation on the Bern-Lötschberg-Simplon Railway (BLS) with 15 kilovolt 16⅔ Hertz.
- In the same year, the Rhaetian Railway opened its Engadine line with 16⅔ Hertz, but with a voltage of 11 kilovolts.
- 1914 Opening of the Pressburger Bahn with 15 kilovolt 16⅔ Hertz on the overland route.
- The First World War brought progress to a standstill. 1920 Start of electrical operation on the Gotthard Railway . The electrification of this route was necessary so that Switzerland would become less dependent on coal imports from neighboring countries during times of crisis.
Electrical part
Main circuit
All cables and devices that transmit and influence the electrical drive energy of an electric locomotive are part of the main circuit. The main circuit can be subdivided into the high voltage circuit (also called high current or main voltage circuit) and the motor circuit, depending on the locomotive. The separation between the two circuits is generally the main transformer in AC locomotives. Since pure DC locomotives do not have a transformer, an exact separation between the high-voltage and motor circuits is often not possible with these locomotives.
High voltage circuit
High-voltage current from the contact line flows through the high-voltage circuit. As a rule, the following devices and cables are part of the high-voltage circuit of AC locomotives:
- Pantograph
- High voltage converter
- System selector switch
- Surge arresters
- Roof dividers
- Roof pipes
- Main switch
- Roof penetrations
- Upper current transformer
- Primary winding of the main transformer
- Grounding devices
DC locomotives have a similar structure in the high-voltage circuit, but without the main transformer. In addition, the main switches of DC locomotives are sometimes called high-speed switches. The devices used in AC locomotives differ in detail from those in DC locomotives. This is due, among other things, to the fact that the nominal voltage in direct current networks is usually significantly lower than in alternating current networks and therefore the currents are significantly higher for the same power. The current-carrying cross-sections must be dimensioned correspondingly larger. In the case of AC locomotives, however, larger distances must be maintained due to the higher voltage in order to prevent flashovers .
Motor circuit
The current that is fed to the traction motors flows through the motor circuit. For AC locomotives, this includes u. a. the following cables and devices:
- Secondary winding of the main transformer
- Power control
- Travel motor separator
- Direction reverser
- Traction motor
In DC locomotives, the high-voltage circuit is usually connected directly to the power control.
Driving and power control
In the case of electric locomotives, power control means influencing or controlling tractive effort, braking force, speed and direction of travel.
Direction control
In the case of electric locomotives with commutator motors, the polarity of the traction motor stand field is reversed using a reverser to change the direction of travel . When using three-phase motors, the direction of rotation of the rotating field must be changed to change the direction of travel.
Drive control in DC vehicles
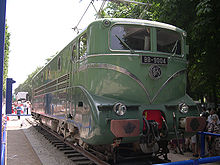
Driven by DC motors
In locomotives operated with direct current, resistors are connected upstream of the series traction motors when starting, which are short-circuited in stages with a switching mechanism. As long as the series resistors are switched on, part of the energy in the locomotive is converted into heat, so that economical operation is only achieved when the starting resistor is completely short-circuited . Further speed steps result from the use of the field weakening . The field winding is partially short-circuited so that the traction motor can reach higher speeds as the torque decreases. In the case of vehicles with several motors, there is the possibility of lossless, coarse control of the traction motors through grouping circuits. For this purpose, these are connected in series or series at low speeds, and connected in parallel at higher speeds . The various switching options with four or six drive motors result in a significantly larger number of loss-free speed levels.
In addition to this step-by-step control, stepless controls were later developed which, instead of the series resistors, use chopper controls that allow almost loss-free power control.
Driven by three-phase motors
With the advent of modern power electronics, it became possible to convert the direct current drawn from the network into a voltage and frequency-variable three-phase current. This made it possible to use three-phase motors, which are significantly less maintenance-friendly than direct-current motors. Depending on the power electronics used, traction converters with DC chopper, intermediate circuit and inverter are used, or the DC current taken from the network is converted directly into three-phase current by the inverter.
Drive control in AC vehicles
Drive by series motors

For electric locomotives with alternating current with very low frequencies such as 16.7 Hz, single-phase series motors can be used. The voltage of the traction motors is regulated by a switching mechanism . This consists of a step switch or drive switch , with which individual taps on the transformer coils are controlled manually or via interconnected contactors . Depending on the design, the switching mechanism is arranged either on the high-voltage side or on the low-voltage side of the transformer. When arranged on the high-voltage side, the switching mechanism is smaller because the currents are also smaller, but the demands on the insulation materials are significantly higher.
When using alternating current with frequencies of 50 Hz or 60 Hz, as they are also used in the electricity network of the national supply, the use of single-phase series motors is too complicated. After the transformer , the current is either fed to a converter that generates direct current, or the current is converted into direct current by static rectifiers . The traction motors are designed as wave current motors , also called mixed current motors , which are specially designed for processing the undulating direct current.
Instead of the switching mechanism, phase control can also be used to regulate the traction motor voltage . This technology enables infinitely variable control, but in the beginning it caused major problems due to the completely different frequency spectrum of the overhead line currents compared to tap changer locomotives , which led to interference in signaling systems.
Driven by three-phase motors
Asynchronous traction motors with slip ring rotors were generally used for locomotives that draw three-phase current from the contact line . The power control was carried out by switching on additional resistors in the rotor circuit, which were gradually short-circuited when starting up, and by switching the number of poles of the motors using the Dahlander circuit . Thus only two or four economical speed levels were possible.
Today's electric locomotives use modern, energy-saving power electronics. In AC vehicles, a transformer with a fixed transmission ratio is arranged in front of the converter, which sets the voltage to a lower value and adjusts it to the various nominal voltages of the AC systems. You only have one transformer with a few fixed taps to which the traction converters (usually one per bogie or one per traction motor) are connected. These convert the supplied single-phase alternating current into a three-phase alternating current with a variable frequency, which supplies the commutator-free and low-maintenance three- phase traction motors.
Driving control in multi-system vehicles
Multi-system locomotives can run on different traction current systems. This enables cross-border traffic without time-consuming locomotive changes. Different voltages can be handled in AC networks with multiple connections on the primary side of the main transformer. In the past, DC or mixed current motors were often used as traction motors with different network frequencies and / or when driving in AC and DC networks. The alternating current generated by the transformer was converted with the help of a rectifier .
Today's multi-system locomotives use modern power electronics. Regardless of the type of current used, the energy supplied on the vehicle is converted into three-phase alternating current and fed to asynchronous traction motors .
Electrodynamic braking
In addition to the mechanical brakes, many electric locomotives use their traction motors as a generator when braking. If the energy generated is converted into heat by so-called braking resistors, it is referred to as a resistance brake . If the electrical energy is fed back into the route network, this is known as regenerative braking . A prerequisite for this is a network that is capable of receiving information, i.e. H. the generated electrical energy must be consumed by another consumer in the same feed section . Alternatively, the energy supply of the feed section must be able to pass the electrical energy on to another feed section or to feed it into the public power grid.
Auxiliaries
The auxiliaries are devices on electric locomotives that are used to supply the on-board electrical system, to store electrical energy ( accumulator ), to supply compressed air ( air compressor ) and to cool the systems (fans, pumps).
To supply the on-board electrical system, electric locomotives are usually equipped with a separate, smaller power converter ( auxiliary converter ) that supplies the connected auxiliary systems with three-phase alternating current. In direct current locomotives, this converter is often supplied with electrical energy directly via the contact line; AC locomotives are usually supplied with power via their own transformer tap. The output frequency of the auxiliary power converter is regulated depending on the power requirements of the loads connected to it. In older locomotives, the auxiliaries were either supplied directly by the traction current network (especially for DC vehicles), by the main transformer (for AC vehicles) or by a rotating converter .
In addition to the auxiliary electrical system, electric locomotives are equipped with accumulators that ensure an energy supply that is independent of the contact line. These supply important control circuits, the safety driving circuit, train control systems, the signal and vehicle interior lighting, the auxiliary air compressor and, in some vehicles with electrodynamic brakes that are independent of the contact wire, the brake resistor fan. The accumulators are charged by a charger , which in turn is supplied from the auxiliary electrical system, from a suitable transformer tap or from a separate converter. Typical battery nominal voltages are, for example, 24, 48 or 110 V in Europe and 72 V in the USA.
To ensure the supply of compressed air, electric locomotives are equipped with air compressors (also called air compressors). This supplies the compressed air brakes , the pneumatic devices of the vehicle and the pneumatic devices of the wagon train with compressed air. Pneumatic devices of the vehicle are for example the lifting device of the pantographs and electro-pneumatic contactors . In the wagon train, for example, the outer doors or the air suspension are compressed air consumers that have to be supplied by the electric locomotive. In addition to the main air compressor, electric locomotives are often equipped with an auxiliary air compressor, which makes it possible to lift the pantograph and switch on the main switch on a dismantled locomotive. The auxiliary air compressor is supplied with electrical energy by the accumulators. If a suction air brake is used instead of a compressed air brake , the locomotive must be equipped with a vacuum pump .
Electric locomotives are equipped with cooling devices to dissipate the waste heat from the electrical systems. The main transformer, power converters, traction motors, air compressor and the rest of the electronics must be cooled, if available. Larger waste heat generators are cooled by a separate cooling device. Today the main transformers are usually oil-cooled. To do this, an oil pump pumps the cooling oil from the transformer tank through the oil cooler (usually an oil / air heat exchanger ) and back into the transformer tank. A fan draws in machine room or outside air and pushes it through the heat exchanger to release the waste heat from the transformer to the environment. In modern electric locomotives with power electronics, the converters must also be cooled. Cooling water is often used for this, which releases the waste heat from the converter to the environment in a water / air heat exchanger. The traction motors are mostly air-cooled. In the case of self-ventilated traction motors, the cooling air required for this is sucked in by a fan wheel mounted on the drive motor shaft. With increasing performance demands on the traction motor, there was a move to externally ventilated systems, in which separate traction motor fans provide the cooling air. Depending on the vehicle type, a drive motor fan cools all drive motors or each drive motor has its own drive motor fan. As with the traction motors, the air compressors are usually air-cooled and there are both self-ventilated and externally ventilated systems. To protect the devices and fans from dirt and damage, the outside air must be cleaned. This is done, for example, by means of ventilation grids , cyclone separators and / or filter mats .
Train power supply
Electric locomotives that are to be used in passenger transport often provide the central energy supply for the attached train of cars. In Europe, a single-pole train bus has prevailed, which uses the tracks as a return conductor. In other countries, however, such as the USA, the train power supply with three-phase alternating current has prevailed. The energy for the train power supply is taken either from a transformer tap, directly from the contact line or from a converter.
Before electric heating caught on in passenger cars, electric locomotives were also equipped with steam generators for steam heating . These steam generators were operated partly electrically, partly by burning fuel.
safety devices
To protect the vehicle, electric locomotives are u. a. equipped with the following protective devices:
- Protection against undervoltage and overvoltage in the contact line
- Protection of the entire vehicle against overcurrents and short circuits
- Overcurrent and short circuit protection of the motor, auxiliary and control circuits
- Transformer protection (including Buchholz relays )
- Converter protection
- Anti-skid device
These protective devices monitor operational and function-relevant variables of the vehicle. If the monitored values fall below or exceed a specified limit value, the protective device triggers a specified reaction. This can be, for example, the output of a warning signal for the driver, the automatic shutdown of part or the entire motor vehicle or an automatic intervention in the vehicle control.
Further protective devices for monitoring the driver are:
- Safety driving circuit (Sifa)
- Train control
Mechanical part
The locomotive usually consists of a box carried by the running gear with the driver's cabs and the engine room.
Box and engine room
The box consists of a stable main frame with welded-on side walls and removable roofs. The driver's cabs are located at the ends, between which there is a large engine room, where the electrical switching, control and transmission systems are set up protected from the weather. So that the operating personnel cannot touch dangerous electrical voltage, the devices are either housed behind bars or in newer locomotives in closed cabinets. The particularly dangerous high-voltage area is also cordoned off. Access is only possible with a key which is only released when the pantograph is lowered and the electrical equipment is grounded.
Devices for transmitting the tensile and compressive forces are attached to the box. These are usually draw hooks and buffers or a central buffer coupling .
To ensure the accessibility of the devices for maintenance work, they are arranged along aisles. In vehicles with two driver's cabs, an aisle is also used to connect them for the driver. Either one corridor can be arranged in the middle of the engine room or two corridors along the walls. A mixture of the two systems is possible. In corridors along the side walls, one of the above-described additionally cordoned off high-voltage areas usually belongs to.
Moving parts are no longer visible in the engine room of modern locomotives.
Drive and drive
The main frame for its part mostly rests on the frame of movable bogies , which in turn are supported by two or three wheel sets. Modern electric locomotives are usually equipped with single-axle drives ; for cost reasons, two motors are sometimes supplied jointly by one traction converter.
The driven wheels or axles of the first locomotives were structurally coupled to the engine in the simplest possible way, which inevitably initially led to single-axle drive; in some cases only one axle of the locomotive was driven anyway. A drive for several axles with individual motors also appeared very early on, for example in the “Le Drac” locomotive of the Chemin de fer de La Mure .
With increasingly greater powers, however, the combination of the drive in as few motors as possible was preferred, because specifically lighter and cheaper equipment could be achieved thereby. The first larger electric locomotives therefore had large, slow-running motors on the main frame , and the chassis consisted of several drive axles coupled with rods, which were driven either via helical cranks or jack shafts. Similar to steam locomotives , there were also additional running axles to support overhanging frame parts. In addition, engines were mechanically coupled to one another in pairs in the locomotive body .
It soon became apparent, however, that at higher speeds and when several motors were coupled, resonance vibrations of the gearbox and the entire locomotive structure occurred, which caused considerable damage. Efforts were therefore soon made to develop a single-axle drive that would meet the requirements at higher speeds. In addition to the “Siemens Schuckert drive” with vertical motors, the Swiss Jakob Buchli developed the Buchli drive for Brown, Boveri & Cie in 1918 .
In locomotives for speeds of up to 140/160 km / h, the traction motor is partly carried by the axle and partly by the bogie frame ( tatzlager drive ). This construction enables a simple drive, since the motor cannot move relative to the axis. The disadvantage is the large mass of the motor, which lies directly on the wheels, unsuspended. This has the effect that the shocks are not attenuated by the rails when the vehicle is moving and that relatively large forces act on the rails. For higher speeds, the traction motors are completely suspended from the bogie frame or the locomotive body , so that the impact on the track can be better cushioned. The drive must be able to compensate for the relative movement between its spring-loaded suspension and the axle, so that a hollow shaft drive is usually used.
Driver's cab
In the driver's cabs there are all operating devices and display devices necessary for operating the traction vehicle.
Mechanical accessories
In addition to the devices mentioned, electric locomotives also have other components, including:
power supply
The first railways with electric traction were operated with direct current or three-phase current, which allowed the construction of vehicles with simple traction motors and simple controls. Only later was the technology available for the use of single-phase alternating current , which simplified the contact line and the energy supply.
Direct current
Electrification with direct current was the easiest to do. The drive motor had a simple structure and its output could be regulated with series resistors. It is more difficult to transfer energy over long distances, so that many feed points are necessary. On the other hand, the vehicles can be built easily because no transformer is required on the vehicle. The system is still used today. Electrification with 3000 volts DC is the most widespread system worldwide in terms of sections (as of 1980). However, it is no longer used for new large projects in long-distance transport. Problems are caused by the large currents that z. B. must be transmitted from the contact line for high-speed operation and thereby cause high losses.
Accumulator locomotives are a special form of direct- current powered locomotives. As with the accumulator railcars used in passenger transport, the advantage is that they do not depend on any other infrastructure for power supply apart from the stationary charging stations.
However, due to the limited battery capacity, the area of application is limited to short distances. Battery locomotives have been used on the London Underground since the 1930s as service vehicles for service work in tunnel sections where the conductor rail is switched off for maintenance work. Battery locomotives have been used underground in mining for much longer ; these are narrow-gauge mine locomotives. In addition, they are occasionally used in works rail transport. The test locomotive FS E.421 was built as early as 1921 and since 1916 the NSB Ea1 was in service in Norway both in shunting and mainline service.
Three-phase current
Three-phase current was used for the first time in trial operation on the Marienfelde – Zossen line . The asynchronous traction motors of the locomotive were supplied directly from a three-pole contact line , the speed control was carried out by changing the frequency of the supply voltage in the power station.
For practical operation, a two-pole contact line with the running rails as the third outer conductor prevailed. Compared to direct current operation, the energy could be transmitted better over longer distances and an operationally reliable regenerative brake could be easily implemented, which is why the system is still used today on some Swiss mountain railways . Stepless speed control was not possible with classic controls. For the most uninterrupted energy supply even in turnouts, it is necessary to drive with two widely spaced pantographs per locomotive because of the crossing point of the contact wires with different feed phases. The construction of the contact line is particularly complicated at crossings and crossings. Operated in the North of Italy Ferrovie dello Stato five individual networks with 3.6 kilovolts at 16 2 / 3 Hz. However, they were no longer connected. The decisive factor for the replacement by the technically simpler direct current system was that the fixed, two-pole contact line was not suitable for speeds over 100 km / h. The Italian "Trifase" operation ended in 1976.
Alternating current

Thanks to its high voltage, alternating current can be transmitted over long distances with low losses. On the other hand, at the beginning of electrification, the construction of traction motors for single-phase alternating current was extremely complex and only succeeded with low mains frequencies. Trial runs with single-phase alternating current were carried out as early as 1905, but the system did not establish itself as the most suitable energy supply for long-distance railways until later. The high AC voltage is stepped down to operate the motors and switchgear on the traction vehicle with transformers to lower values.
Advances in power electronics made it possible to use the widespread network frequency of 50 Hertz later. In the beginning, the 50 Hertz alternating current was rectified with diodes and then served to supply so-called mixed current motors. For new electrifications, the system with 25 kilovolts at 50 Hertz is usually used today, which is the second most common in the world today.
Application of traction current systems
This historical development shows that different traction current systems are used today, depending on when the first systems were built. In Europe, the various systems hinder cross-border traffic, which can only be managed with multi-system vehicles .
The most important traction current systems in the world (in order of voltage level):
- 50 Kilovolt, 60 Hertz ~
individual applications in Canada, USA and South Africa - 25 kilovolt, 50 Hertz ~
France (northern part and TGV routes), Spain (AVE routes), Great Britain (north of London and Channel Tunnel Rail Link ), Denmark, Germany (only Rübelandbahn ), Finland, Luxembourg (except Luxembourg- Arlon), Belgium (partially), Netherlands (partially), Switzerland ( Genève – La Plaine and Basel – Saint-Louis ), Hungary, Czech Republic (southern part), Slovakia (southern part), Croatia, Serbia, Bulgaria, Italy (new High-speed routes), Greece, Portugal, Romania, Russia (partially), Ukraine (partially), Kazakhstan, Lithuania, Belarus, India, China, South Korea - 20/25 kilovolt, 50/60 Hertz ~
various power grids of Japan Railways ( e.g. the Shinkansen high-speed lines, and the conventional lines in the north of the island of Honshu) - 15 kilovolt, 16 2 ⁄ 3 or 16.7 Hertz ~
Germany, Switzerland, Austria, Norway, Sweden - 3000 volts =
Italy, Spain, Belgium, Luxembourg ( Luxembourg – Arlon route ), Poland, Russia (partly), Ukraine (partly), Estonia, Latvia, Georgia, Armenia, Azerbaijan, Czech Republic (northern part), Slovakia (north and east) ), Slovenia, North Korea - 1500 volts =
France (southern part), the Netherlands, the Czech Republic ( Tábor – Bechyně ), large parts of the conventional routes in Japan (especially in metropolitan areas such as Tokyo, Nagoya or Osaka), common on meter -gauge routes in Spain and Switzerland - 750 volts =
England (south of London up to the canal, power supply via a side busbar coated from above)
In the case of tram, light rail, underground and S-Bahn networks, DC voltages between 500 and 1500 volts are mostly used if they are operated independently of long-distance train networks. The contact wire voltage in tram networks rarely exceeds 1000 volts.
literature
- Helmut Bendel: The electric locomotive. Structure, function, new technology. transpress, Berlin 1994. ISBN 3-344-70844-9
- Klaus-Jürgen Vetter: The big manual for electric locomotives. Bruckmann, September 2003. ISBN 3-613-71370-5
- Günther Klebes: The electric and diesel traction vehicles at the railway technology exhibition in Seddin on the occasion of the railway technology conference in Berlin from September 21 to October 5, 1924 . Monographs and Communications, Volume 20 (double issue). Published by the German Society for Railway History eV Karlsruhe 1978. ISBN 3-921700-18-3
- Günther Klebes: 100 years of electric train transport - 100 years of electric locomotives from Siemens. Eisenbahn-Kurier-Verlag, Freiburg Br 1979. ISBN 3-88255-823-7
- Klaus-Jürgen Vetter: The big manual for electric locomotives. Bruckmann, September 2003. ISBN 3-7654-4066-3
- Raimo Gareis: yesterday's electric locomotives. Vol. 1. Mainline locomotives. Krone, January 2000. ISBN 3-933241-18-9
- Andreas Steimel: Electric traction vehicles and their energy supply: Basics and practice , Oldenbourg Industrieverlag, Munich 2006, ISBN 3-486-63090-3 .
Web links
Individual evidence
- ↑ www.hochsitzszuege.com - Overview of the French high-speed trains. The axle formulas (driving axles, running axles) are specified with the trains.
- ↑ http://www.physikalischer-verein.de/index.php/verein/historisches
- ↑ a b c d e f g h i j k l Bendel, Helmut: The electric locomotive: structure, function, new technology . 2., arr. and additional edition Transpress, Berlin 1994, ISBN 3-344-70844-9 .
- ↑ a b Lecture notes "Rail Vehicles" ( Memento of the original from April 26, 2009 in the Internet Archive ) Info: The archive link was automatically inserted and not yet checked. Please check the original and archive link according to the instructions and then remove this notice. by Andreas Haigermoser, TU Graz, edition 07.2002
- ↑ 16.7 Hertz in the DA-CH network and asynchronous converter sub-networks, cf. Traction current