accumulator
An accumulator or short battery is a rechargeable galvanic element , consisting of two electrodes and an electrolyte , and stores electrical energy on an electrochemical basis. The Latin word accumulator means "collector" ( Latin cumulus 'pile', accumulare ' to pile up '). An earlier term for accumulators was collector .
A single rechargeable storage element is called a secondary element or secondary cell , in contrast to the non (or only to a very limited extent) rechargeable primary cell . The charging process is based on the electrolytic reversal of the chemical reactions that take place during discharge by applying an electrical voltage . Secondary cells - like primary cells and all electrical energy sources - can be interconnected to form batteries , either in series (to increase the usable electrical voltage) or in parallel (to increase the usable capacity or because they are suitable for higher currents ). Both circuit variants lead to a corresponding increase in the total energy content (product of capacity and voltage, specified in watt hours (Wh)) of the arrangement.
For every type of battery , the nominal voltage of the battery cell is determined by the materials used; Since this is too low for most applications, the series connection is often used to increase the voltage (see picture of starter battery). The capacity and the possible current intensity, however, depend on the size. Therefore it is usually not necessary to connect several cells in parallel; instead, a battery with appropriately large cells is used.
Disambiguation
accumulator
Originally a single rechargeable storage element (secondary cell) was meant by accumulator . Today the term - at least in common language - also refers to rechargeable storage devices that consist of interconnected secondary cells. When it comes to the difference, more precise terms should be used:
- single storage element: secondary cell, secondary element, accumulator cell, accumulator cell
- interconnected storage elements: z. B. Accupack , battery from secondary cells
battery
In the technical sense, a battery is a combination of several similar galvanic cells or elements that are connected in series. There are batteries made from primary cells (not rechargeable) and those made from secondary cells (rechargeable). Originally, batteries were only meant to consist of primary cells. With the proliferation of rechargeable storage devices, this limiting definition has become obsolete.
In everyday language, however , battery is used as a generic term for (real) batteries, primary cells and secondary cells. The term “batteries” is therefore often used when only single primary cells or secondary cells (accumulator cells) are actually meant.
Both cell types are available on the market in interchangeable sizes , and both are called batteries in English , which should add to the confusion. Rechargeable batteries are rechargeable batteries or accumulators .
Electrical consumers that can be operated with both primary and secondary cells are therefore often simply called battery-operated . The term battery-operated is only preferred if rechargeability plays a special role in the daily use of the device . Due to the dominance of English, the term “rechargeable batteries” or “secondary batteries” is increasingly used in the technical and scientific context.
capacitor
Capacitors are also storage devices for electrical energy, but they do not store it in chemical form, but as an electrical field between their plates. Capacitors are therefore not accumulators in the conventional sense.
history
The first preform of an accumulator, which - in contrast to the cells by Alessandro Volta - was rechargeable after discharge, was built in 1803 by Johann Wilhelm Ritter . The most famous type of battery, the lead-acid battery, was designed by the physician and physicist Wilhelm Josef Sinsteden in 1854 . In 1859, Gaston Planté developed Sinsteden's invention considerably by arranging the lead plates in a spiral. At the turn of the 20th century, lead-acid batteries powered by wood, electric drives for automobiles. Battery technology developed rapidly over the years. The following text published by the Telegraphentechnisches Reichsamt in 1924 shows this using the example of telegraphy, which was established at the time, and telephony, which was still in its infancy . Accumulators are called "collectors" here, and "batteries" were collections of galvanic elements:
“[1899] For the telegraph as well as for the telephone, wet and dry elements were the main sources of electricity. Batteries mainly made of zinc-copper elements were used for the telegraph; In addition, the telephone service mainly used wet zinc-carbon and dry elements. As more powerful power sources, collectors, which had occasionally been used since 1895 to operate microphones in the largest telephone exchanges, were introduced on a larger scale after 1900. […] To charge the 12-cell battery, dynamo machines were set up at the office, which were equipped with their own power plant (mostly light or heavy oil engines) or were driven from the local high-voltage network and supplied the required direct current in the appropriate current strength and voltage. In the beginning, work was generally carried out in alternating loading and unloading operations. H. alternately one battery fed the office while the other was charged. Later (1921) one went over to taking the current for the office directly from dynamo machines, whose electrical properties had to be specially adapted for this purpose, and to connect a 'buffer' battery in parallel. "
technology
functionality
In an accumulator during charging is electrical energy into chemical energy converted . If a consumer is connected, the chemical energy is converted back into electrical energy ( see: Galvanic cell ). The nominal electrical voltage , efficiency and energy density typical for an electrochemical cell depend on the type of materials used.
Accumulator types
The accumulator types are named according to the materials used:
- Li-Ion - lithium-ion accumulator (3.2-3.7 V nominal voltage / cell), generic term for various lithium-ion accumulator types:
- LiCoO 2 - lithium cobalt dioxide accumulator , (3.6 V / cell), first available technology
- LiPo - lithium polymer accumulator (3.7 V nominal voltage / cell), (design with polymer as electrolyte )
- Li-Mn - lithium manganese accumulator (3.6 V nominal voltage / cell)
- LiFePO 4 - lithium iron phosphate accumulator (3.3 V nominal voltage / cell)
- LiFeYPO 4 lithium iron yttrium phosphate accumulator (yttrium doping to improve the properties)
- LiTi - lithium titanate accumulator (2.4 V nominal voltage / cell)
- LMP - lithium metal polymer accumulator (accumulator technology from DBM-technology, Berlin)
- Lithium accumulators with metallic lithium do not belong to the larger and better known group of ion accumulators:
- Lithium-air battery (in development since the 1970s)
- Lithium-sulfur accumulator (in development since the 1960s)
- Na / NiCl - sodium-nickel chloride high-temperature battery (brand name: Zebra battery ) (2.58 V nominal voltage / cell)
- NaS - sodium-sulfur accumulator , high temperature accumulator with 2 V cell voltage
- Na-Ion - sodium ion accumulator , (1.6–1.7 V nominal voltage / cell)
- NiCd - nickel-cadmium accumulator (1.2 V nominal voltage / cell)
- NiFe - nickel-iron accumulator (1.2–1.9 V nominal voltage / cell)
- NiH 2 - nickel-hydrogen accumulator (1.5 V nominal voltage / cell)
- NiMH - nickel metal hydride accumulator (1.2 V nominal voltage / cell)
- NiZn - nickel-zinc accumulator (1.65 V nominal voltage / cell)
- Pb - lead accumulator (2 V nominal voltage / cell)
- PTMA - modified PTMA, more precisely: 2,2,6,6-tetramethylpiperidinoxy-4-yl methacrylate, an environmentally friendly organic polymer
- RAM - Rechargeable Alkaline Manganese (1.5 V nominal voltage / cell)
- SnC / Li 2 S - tin-sulfur-lithium accumulator
- Silver-zinc accumulator (1.5 V nominal voltage / cell)
- Vanadium redox accumulator (1.41 V nominal voltage / cell at 25 ° C)
- Zinc-bromine accumulator (1.76 V nominal voltage / cell)
- Zinc-air accumulator (in development)
- Silicon-air accumulator (in development)
Energy density and efficiency
The energy density is important for many applications, in particular for mobile devices in the field of entertainment electronics, hearing aids or vehicles . The higher this is, the more energy can be stored in a battery per unit of volume or mass. The mass-related energy density is often referred to as specific energy. In relation to the types available on the market, accumulators (secondary cells ) usually have a (often significantly) lower energy density than primary cells .
Batteries with a particularly high energy density are often disproportionately expensive or have other disadvantages, in particular a limited service life. Lead-acid batteries typically cost € 100 / kWh; Li-ion batteries, on the other hand, are currently (2012) typically 350 € / kWh (200 € / kWh 2013), and the trend is falling. The reasons are the start of mass production, which significantly reduces unit costs through better technology and economies of scale . However, the falling production costs are only passed on to customers with a delay, as there is little price pressure on this market, especially in Germany, due to the few offers .
When rechargeable batteries are charged and discharged, the internal resistance of the cells releases heat, which means that some of the energy used for charging is lost. The ratio of the energy that can be drawn to the energy that can be used for charging is referred to as the charging efficiency . In general, the charging efficiency decreases both through rapid charging with very high currents and through rapid discharge ( Peukert effect ), since the losses in the internal resistance increase. The optimal window of use is very different depending on the cell chemistry.
Accumulator type | Energy density (Wh / kg) | Charging efficiency (as of 2007) | Specialty |
---|---|---|---|
Lead accumulator | 30th | 60-70% | |
Lithium-ion battery based on LiCoO 2 | 120-210 | 90% | newer models can be charged quickly |
Lithium polymer accumulator | 140-260 | 90% | practically any design possible |
Lithium iron phosphate accumulator | 80-140 | 94% | Fast charging, high current capability, intrinsically safe |
Lithium titanate accumulator | 70-90 | 90-95% | fast charging |
Lithium-sulfur accumulator | 350 | 90% | Laboratory prototype |
Sodium nickel chloride accumulator (zebra battery) | 100-120 | 80-90% | 300 ° C operating temperature, no self-discharge, but heating losses 10–20% |
Sodium-sulfur accumulator | 120-220 | 70-85% | 300 ° C operating temperature, no self-discharge, but heating losses 15–30% |
Nickel-iron accumulator | 40 | 65-70% | very insensitive to over- and deep discharge |
Nickel-cadmium accumulator | 40-60 | 70% | Banned across the EU, with the exception of emergency systems and the medical sector |
Nickel-metal hydride accumulator | 60-110 | 70% | |
Nickel-hydrogen accumulator | 60 | 75% | |
Nickel-zinc accumulator | 50 | 65% | |
Silver-zinc accumulator | 65-210 | 83% | expensive, short-lived, sensitive, very high capacity |
Tin-sulfur-lithium accumulator | 1100 | ? | Experimental prototype |
Aluminum ion accumulator | 1000 | ? | fast charging, experimental prototypes |
A comparison with the storage of electrical energy shows the advantages and disadvantages of rechargeable batteries compared to other storage methods.
Charge amount (capacity)
The amount of charge that an accumulator can store is specified in ampere-hours (Ah) and referred to as capacity (nominal capacity). This must not be confused with the capacitance of a capacitor , which is defined as the amount of charge that depends on the voltage and is specified in Farad (F). 1 F is one ampere second per volt (As / V). The specified nominal capacity of the battery always relates to a certain discharge current and decreases - depending on the battery type - to different degrees with higher discharge currents.
In the case of primary cells and accumulators, the nominal capacity is stated in ampere-hours (Ah), and in the case of smaller units also milli- ampere hours . The prefix for units of measurement Milli stands for one thousandth. The statement that an accumulator delivers 1000 mAh, i.e. one ampere-hour, does not say much about the performance of the battery if the voltage is not known. The voltage is strongly dependent on the load on the cell, as it has an internal resistance. Theoretically, it delivers its maximum power at half the nominal voltage. Then internal and load resistance are equal and the discharge efficiency reaches 50 percent. Since the cell becomes very hot in the process, such high loads are only possible for a short time. An example of this are starter batteries in cars, which give off a few hundred amps for a few seconds when they are started. Some cell types cannot withstand such high loads and have protective circuits to prevent this.
Figures in Wh or kWh (often found in traction batteries) always relate to a specific load profile. In order to compare the performance of batteries, you have to know which load profile was used when measuring the capacity.
State of charge
An important characteristic of devices operated with secondary batteries is the state of charge of accumulators ( English State of Charge , SoC or SOC). It is usually given in percentages, with 100% representing a fully charged accumulator. 100% minus the value of the state of charge gives the degree of discharge (DoD or DOD).
Various methods are used for determination: chemical, voltage-dependent, current-integrative (charge balancing), pressure-dependent and measurement of the accumulator impedance .
Self-discharge - recommended storage
If a battery is not used, it will lose part of its stored energy over time. This process is called self-discharge . The degree of self-discharge depends on the type and age of the battery and on the storage temperature.
The following is usually recommended for the storage of batteries: ( Note: The state of charge is seen relative to the final discharge voltage . This means that if a battery has a state of charge of 0%, then it means that it has reached its final discharge voltage, with NiCd and NiMH batteries, this is e.g. 0.9 V or 1.0 V.)
- Li-Ion : state of charge 60%, 20 ° C; Self-discharge monthly <2%
- Lead accumulator : state of charge 100%, store as cool as possible; Self-discharge monthly 5–10% (lead-acid) or 2–5% (lead-gel), a battery that has been discharged for a long time is destroyed
- NiMH : state of charge 40%; Self-discharge monthly by 15-25%, newer types than NiMH with low self-discharge with only about 15% per year
- NiCd : state of charge 40%; Monthly self-discharge by 10%
- Alkaline manganese RAM cells : state of charge 100%; Cell voltage should not drop below 1.2 V.
Sanyo launched a modified NiMH battery called Eneloop in 2005 (market launch in Europe in August 2006) , which is subject to self-discharge of only 15% per year. These are so-called LSD batteries (Low Self Discharge), which are sold as pre-charged batteries due to their low self-discharge and therefore, unlike conventional batteries, do not have to be charged by the buyer before the first use.
All information on self-discharge relates to a room temperature of approx. 20 ° C.
Service life and cycle stability
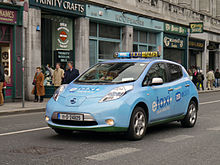
According to the manufacturer, lithium iron phosphate batteries achieve more than 5000 cycles at a respective depth of discharge of 80%, and after 7000 cycles still 70%. BYD is the world's largest manufacturer of lithium iron phosphate batteries and has developed a wide range of cells for cycle-resistant applications, such as those used in stationary storage systems, through precise manufacturing. After 6000 cycles with 100% loading and unloading at a rate of 1 C, they still have a remaining capacity of at least 80%. With a full cycle per day, this corresponds to a service life of at least 20 years.
The Sony Fortelion lithium iron phosphate battery has a remaining capacity of 71% after 10,000 cycles with 100% discharge . This accumulator has been on the market since 2009.
Lithium-ion accumulators used in solar batteries sometimes have a very high cycle stability of more than 10,000 charge and discharge cycles and a long service life of up to 20 years.
Varta Storage gives a guarantee of 14,000 full cycles and a service life of 10 years on its Engion Family and engion home product families.
The service life of stationary batteries at a constant room temperature of 10–25 ° C can only be achieved with drive batteries through thermal management. Unequal temperature fluctuations of the cells within the drive battery lead to differences in capacity and different aging of the cells. The available capacity of a lithium battery decreases as the operating temperature falls, especially below the 25 ° C operating temperature at which the nominal capacity is determined, and should not fall below the freezing point of the electrolyte due to ice formation. On the other hand, the higher the operating temperature, the faster a cell ages, with a strongly increasing tendency above approx. 40 ° C. The aim of thermal management is that all cells in the volume have the same temperature at the same time, which provides the highest possible performance with little aging.
Furthermore, the BMS has a significant influence on the capacity of the cells connected in series, which is determined by the weakest cell during passive balancing . As a result, the overall capacity is reduced and the weakest cell is used the most and ages the fastest. In contrast, the complex active balancing can carry out a charge equalization from the cells of high capacity to those of low capacity and keep the service life and the capacity of all cells available even in an older battery that is no longer homogeneous. Depending on their technology, the manufacturers grant widely differing guarantees on the service life of drive batteries.
The organization Plug in America conducted a survey among drivers of the Tesla Roadster regarding the service life of the installed batteries. It was found that after 100,000 miles = 160,000 km the batteries still had a remaining capacity of 80 to 85 percent (no information about the measurement in the source). This was independent of the climatic zone in which the vehicle was driven. The Tesla Roadster was built and sold between 2008 and 2012. Tesla gives an 8-year guarantee with unlimited mileage for its 85 kWh batteries in the Tesla Model S.
The best-selling electric car is the Nissan Leaf , which has been in production since 2010. In 2015, Nissan stated that until then only 0.01 percent of the batteries had to be replaced due to defects or problems, and that only due to externally inflicted damage. There are a few vehicles that have already driven more than 200,000 km. These would also have no problems with the battery.
loading time
The charging time of a rechargeable battery or a battery made of rechargeable battery cells depends on various factors. These include parameters such as the internal resistance, which has a direct influence on the charging current and is in turn influenced by the temperature. Shorter charging times mean higher current load and higher wear and tear, so they conflict with the lifespan of the battery. Depending on the application, cell chemistry and technical implementation (air conditioning, monitoring), the practically achievable charging times are very different.
The charging current recommended / permitted by the manufacturer is described using the C-factor and may be. a. also depending on the state of charge. The charging voltage is determined by the cell chemistry and the structure of the battery. These two parameters result in an upper limit for the maximum charging power, which is often reduced in favor of a longer service life. The practically achievable loading times are therefore usually higher than the technically possible loading times. In addition to the temperature, the available voltage and current sources and the charging method used should be mentioned as external factors . The battery cell manufacturers specify the parameters and usage windows to be observed in their data sheets, which must be observed by the manufacturers of the end products.

For classic batteries such as lead, NiCd and NiMH, normal charging rates of 0.1 C to 0.2 C are common. This corresponds to charging times of 5–10 hours. With modern lithium batteries, the manufacturer's data sheets usually specify normal charge as 0.5 C, which corresponds to a charging time of 2 hours. In addition, a maximum permitted, higher charging current is specified, for example 3 C, which would enable charging in 20 minutes. In practice, charging times of 1.5 to 4 hours are common in the mobile device sector. Electric cars such as Tesla Model S , Renault ZOE , BMW i3 , Nissan Leaf etc. can charge their batteries to 80 percent at current (2017) fast charging stations within about 30 minutes. However, today's lithium batteries can often be charged much faster. In the model building sector, charging times of 10 to 15 minutes are usual for fast charging. In practice, the upper limit of the charging capacity is no longer determined by the accumulator cells, especially for larger batteries in electric vehicles, but by the structure of the traction battery (air conditioning) and the available charging technology. New fast charging systems can charge electric cars with appropriately designed traction batteries to 80 percent in around 15 minutes.
Battery research
Researchers at Justus Liebig University in Giessen , together with scientists from BASF SE, have developed a new reversible cell based on sodium and oxygen. Sodium superoxide occurs as the reaction product .
Scientists from the University of Oslo in Norway have developed an accumulator that can be recharged in less than a second. In the opinion of the scientists, this accumulator would be interesting u. a. for city buses , which could be charged at any stop and would therefore only need a relatively small battery. According to the researchers, one disadvantage is that the larger the battery, the greater the charging current. Thus, the battery cannot be very large. According to the researchers, the new battery could also be used as a buffer in sports cars to provide short-term power. For now, however, the researchers are thinking of areas of application in small and micro devices.
In laboratories of the company StoreDot from Israel, according to reports, the first laboratory samples of unspecified batteries in cell phones (battery capacity in the range of 1 Ah) can be charged in 30 seconds as of April 2014.
In 2014, researchers from Singapore developed a battery that can be charged to 70 percent after 2 minutes. The batteries use lithium-ion technology. However, the anode, the negative pole in the battery, is no longer made of graphite, but a titanium dioxide gel. The gel significantly accelerates the chemical reaction and thus ensures faster charging. In particular, these batteries are intended to be used in electric cars. Researchers at the Ludwig Maximilian University in Munich discovered the basic principle back in 2012.
Solid-state accumulators are a special design in which both electrodes and the electrolyte are made of different solid materials. Since there are no liquids present, there is no problem with leaks should the accumulator be damaged.
Work is also being carried out on accumulators made of organic material.
Scientists at Stanford University in California have developed a new type of battery with very favorable properties. In the aluminum-ion secondary battery , the anode is made of aluminum and the cathode consists of graphite. The battery manages more than 7500 charging cycles without any loss of quality. The materials required to manufacture the battery are very inexpensive and also very light. The battery cannot catch fire even if the battery is pierced. The charging process takes one minute. In addition, the battery is flexible and can therefore be bent and folded into a desired shape. The battery is not yet ready for the market because the voltage and energy density are still too low.
According to estimates, lithium-sulfur and lithium-air battery technology will be usable in the automotive sector by 2025 or at the latest by 2030. Both have a higher energy density than the lithium-ion technology used in 2015 and promise greater ranges in electric mobility.
In Germany, the BMBF has been supporting research on a magnesium-air accumulator that works without lithium since 2013 . Such accumulators have a high capacity and the raw material is available in sufficient quantities, but the service life has so far been short.
A team led by Yan Yu at the Chinese University of Science and Technology in Hefei developed a battery that has a high capacity and voltage even after being charged and discharged 2,000 times (96% capacity retained). It is based on tri-sodium-di-vanadium-triphosphate (Na 3 V 2 (PO 4 ) 3 ) inside a graphene mixed material. Scientists at the Japanese Nagoya Institute of Technology also examined sodium as a battery material and identified the sodium-vanadium compound Na 2 V 3 O 7 as a suitable cathode material. Because of the low energy density, stationary use is initially considered.
Price development
Lead-acid batteries typically cost € 355 / kWh. The prices for Li-ion batteries have fallen significantly in recent years: in 2007 the costs were more than 1000 US dollars / kWh, in 2014 they were still 300 dollars / kWh, and the trend is still falling. So gave z. For example, the head of General Motors, Mary Barra, announced that the battery costs of the Chevrolet Bolt , whose series production will start at the end of 2016, should be around 145 dollars / kWh. For 2022, she expects battery costs of 100 dollars / kWh. Eric Feunteun, head of the electric vehicle division at Renault, announced in July 2017 that one kWh battery costs $ 80 for Renault. The market prices for Li-ion batteries, including the profit margin, are also expected to fall below $ 100 / kWh by 2030.
For 2015, the US Department of Energy put the cost of lithium-ion batteries for electric cars at around $ 250 / kWh; The target is a value of 125 $ / kWh in 2022. The reasons for the price decline are increasing mass production, which has reduced unit costs through better technologies and economies of scale .
According to a study by McKinsey, battery prices fell by 80 percent between 2010 and 2016.
use
Areas of application

Accumulators are often used when an electrical or electronic device is to be operated without a permanent connection to the fixed power grid or to a generator . Since they are more expensive than non-rechargeable primary batteries, they are mainly used in devices that are used regularly and have a non-negligible power requirement, such as cell phones , laptops or cordless tools .
In motor vehicles, too, a rechargeable battery in the form of a starter battery is used to supply power for lights, on-board electronics and, above all, the starter for starting the internal combustion engine. If the motor, the accumulator is on the operating as a generator alternator recharged. The same applies to ships and aircraft.
In the electric drive of electric vehicles , their batteries are then referred to as traction batteries to distinguish them from mere starter batteries and are interconnected to form traction batteries (often referred to as drive batteries). Drive and traction batteries are used in electric cars , electric motorcycles , electric scooters , battery buses and electric trucks . Pedelecs , a special electric bike, are becoming increasingly popular . Electric aircraft for short-haul flights are also under development .
Accumulators are also used in the form of battery storage power plants or solar batteries to compensate for fluctuations in the regenerative generation of electricity with wind and / or sun. Battery storage power plants are u. a. used to cover peak loads in the power grid and also to stabilize the grid in power grids. It is also possible to operate as a stand-alone system in an isolated network when a remote point of use or only at disproportionate cost can be connected to the mains. Often such consumption points are also equipped with an emergency power generator that kicks in before the batteries are charged, e.g. B. is no longer sufficient after several days of calm. Examples of such installations are not only remote huts, cell phone base stations in less developed regions or space satellites , but also many parking ticket machines , where connecting to the power grid would be more expensive than installing a solar cell and a battery.
Conventional submarine drives consist of diesel engines with generators (driving and charging the batteries when the trip is not submerged / snorkeling) and electric motors powered by batteries (diving trips).
In systems for uninterruptible power supply (UPS), batteries are also used for short to medium-term bridging of failures in the stationary energy supply. Important areas that need to be secured with an emergency power supply include: B. data centers, alarm systems and life support systems in hospitals. If high outputs are required or longer periods of time have to be bridged, a diesel generator is also installed; the batteries then only take over the supply as long as the diesel generator needs to start up and reach the rated speed. If the time to be bridged in this way is only short, systems other than accumulators can also be used, in particular on the basis of centrifugal masses or even capacitors.
Selection criteria
Criteria for choosing a battery type for a particular application include:
- The gravimetric energy density, also known as specific energy. It states how much electrical energy an accumulator can deliver per unit of mass (e.g. kilograms). This value is particularly interesting for electrically powered vehicles. Conventional lead-acid batteries achieve around 30 Wh / kg, lithium-ion batteries (Li-ion batteries) up to 140 Wh / kg.
- The volumetric energy density. It states how much Wh of electrical energy an accumulator can deliver per volume (for example per liter of volume). Here the value for conventional lead-acid batteries is approx. 50 Wh / l, for Li-Ion batteries approx. 500 Wh / l.
- The maximum possible discharge current. It is important for all applications where there is a short-term very high power requirement. This is the case, for example, when starting vehicle engines, but also with power tools and autofocus cameras, especially those with integrated flash units .
- The possible dimensions (dimensions and weight) and designs of the battery cell. They are crucial if the accumulator is to be integrated into electronic devices in the smallest possible space. A gas-tight construction, for example of a gel lead-acid battery, enables it to be used in any position without the risk of leaking electrolyte or corrosive gases
- The memory effect with NiCd or the battery inertia effect with NiMH occurs depending on the charging and discharging process and can lead to considerable reductions in capacity (NiCd) or voltage (NiMH). In applications in which the accumulator is not regularly fully discharged and then fully charged again, types of battery should therefore be used that are not susceptible to these effects, for example lead batteries or Li-ion batteries.
The application of the above criteria results in a number of typical areas of application for each battery type, with the transitions flowing particularly smoothly with NiCd, NiMH and Li-Ion batteries:
- Lead accumulator : starter batteries for vehicles with internal combustion engines, stationary operation in emergency lighting systems and island photovoltaic systems
- NiCd battery : power tools, drives in model making, portable electronic devices with short-term high power consumption (photo flash units), drive batteries for electric cars , e.g. Citroën AX electrique
- NiMH battery : portable electronic devices with constant power consumption, model making, electric cars , e.g. General Motors EV1 , Toyota Prius
- Li-ion battery : portable electronic devices with small dimensions and long operating times (cell phones, notebooks , cameras)
- Li-Po battery (also lipo, lithium polymer): drives in model making, mobile phones, drive batteries for extreme ranges, e.g. Kruspan- Hotzenblitz
- Li-Mn battery : drives in model making, new professional class of power tools, pedelecs , vehicle batteries for long ranges
- Li-Fe battery : drives in model making, new professional class of power tools, vehicle batteries for long ranges
- Lithium (nano) titanate battery : drive electric vehicles with long ranges
- not a battery, but alkaline-manganese cells : for applications with such low energy consumption that they run for more than a year, such as clocks, remote controls, thermometers, fire alarms, scales that are rarely used.
Further development
As a further development of conventional accumulators, fuel cell systems are used that generate electrical energy with the help of hydrogen or methanol from chemical energy and can also reverse this process ( reversible fuel cell ). Fuel cells generate electrical energy without exothermic combustion and additional conversions. Since the fireplace insert itself cannot store any energy, it is therefore always necessary to use a storage system whose space requirements and weight must be taken into account. The storage media hydrogen, methanol and similar gases or volatile liquids have different technical requirements than conventional accumulators. The terms electrochemical cell and redox flow cell were created in parallel.
Competing energy storage systems are hydraulic storage systems in which the energy is usually stored mechanically.
literature
- Edmund Hoppe: The accumulators for electricity . Julius Springer, Berlin 1892.
- Thomas B. Reddy (Ed.): Linden's Handbook of Batteries. 4th edition. McGraw-Hill, New York 2011, ISBN 978-0-07-162421-3 .
- Lucien F. Trueb, Paul Rüetschi: Batteries and accumulators. Mobile energy sources for today and tomorrow . Springer, Berlin 1998, ISBN 3-540-62997-1 .
- Martin Winter, Jürgen O. Besenhard : Rechargeable batteries. Part 1: Batteries with aqueous electrolyte solution. In: Chemistry in Our Time . 33, No. 5, 1999, pp. 252-266. ( doi: 10.1002 / ciuz.19990330503 or PDF )
- Martin Winter, Jürgen O. Besenhard: Rechargeable batteries. Part 2: Batteries with non-aqueous electrolyte solution. In: Chemistry in Our Time. 33, No. 6, 1999, pp. 320-332. ( doi: 10.1002 / ciuz.19990330603 or PDF )
- DIN 40 729 accumulators - Galvanic secondary elements - Basic terms .
Web links
- Advice on batteries and rechargeable batteries (PDF 3.7 MB) from the Federal Environment Agency
Individual evidence
- ↑ Ernst Grimsehl among other things: Textbook of Physics. Volume II, Teubner, Leipzig 1954, p. 38.
- ↑ Telegraph Technical Reichsamt: The German telegraph, telephone and radio system 1899-1924. P. 29.
- ↑ Options for storing electrical energy in energy supply systems with regenerative power generation (PDF, 1.06 MB), (Jun .-) Prof. Dr. Dirk Uwe Sauer, ISEA ( RWTH Aachen University )
- ^ Winston Battery Company Overview , added February 12, 2012.
- ↑ Zinc-air batteries for the network. Accessed June 12, 2019 (German).
- ↑ Peter Glösekötter: Project zinc-air battery . Ed .: FH-Münster.
- ↑ tng, Smartmedia PresSservice GmbH, October 2012: Electricity storage from sand and air , accessed October 4, 2012.
- ↑ Wolfgang Kempkens: E-Cars: New Batteries Should Bring the Breakthrough Wirtschaftswoche online, "Green" section, "Innovation" section, February 28, 2013.
- ↑ Now it runs ( memento from December 20, 2017 in the Internet Archive ), December 2, 2017.
- ↑ M. Seiwert, R. Böhmer, J. Rees, FW Rother: E-Car Batteries: Daimler and Evonik are looking for partners for Li-Tec. Online on Wiwo.de from June 15, 2013. In it Audi boss Rupert Stadler: “Three years ago the prices per kilowatt hour were 500 euros ... now it's around 200 euros. And I assume that this is not the end. "
- ↑ Batteries for electric cars are becoming cheaper and cheaper. In: electric car. February 2012, accessed May 19, 2012.
- ↑ Everything about rechargeable batteries ( information about rechargeable batteries and batteries and charging technology / storage devices ) , funkcom.ch, Matthias Frehner
- ↑ The fast charging super battery , pro-physik.de.
- ↑ High Energy Batteries for use in mobile electronics, rc modeling or solar racing ( Memento from November 3, 2013 in the Internet Archive ), manufacturer information, requested on November 2, 2013.
- ↑ Sand improves the performance of batteries , welt.de, WeltN24
- ↑ Sion Introduces a Lithium Sulfur Rechargeable Battery ( Memento of June 18, 2009 in the Internet Archive ), accessed on February 8, 2011.
- ↑ Researchers Develop Novel High-Performance Polymer Tin Sulfur Lithium Ion Battery at greencarcongress.com, accessed on March 10, 2012.
- ^ Oak Ridge, National Laboratory: Aluminum-Ion Battery to Transform 21st Century Energy Storage. (PDF) (No longer available online.) Oak Ridge National Laboratory, archived from the original on November 19, 2015 ; accessed on October 30, 2014 .
- ↑ Konrad Reif: Batteries, vehicle electrical systems and networking . Springer, 2010, ISBN 978-3-8348-9713-8 , pp. 26 ( Google Books ).
- ↑ Dietrich Naunin: Hybrid, battery and fuel cell electric vehicles technology, structures and developments . Expert Verlag, 2007, ISBN 978-3-8169-2625-2 , pp. 57 ( Google Books ).
- ↑ Specification WB-LYP100AHA cell type , manufacturer information from Winston Battery, accessed on May 31, 2019.
- ↑ Lithium iron phosphate accumulator in Akkuzelle Blogspot from August 25 , 2014 , accessed May 31, 2019.
- ↑ BYD on fenecon.de , accessed May 31, 2019.
- ↑ Sony Fortelion p. 13 ( Memento from June 6, 2014 in the Internet Archive ), PDF, inserted on June 3, 2014.
- ↑ Photovoltaic storage system from Bosch impresses with its very high cycle stability; Lithium-ion batteries successfully complete aging test ( Memento from March 30, 2014 in the Internet Archive ) "The tests exposed the batteries to extreme loads. Over a period of 5 years, more than 10,000 equivalent full cycles were achieved at a depth of discharge of 60%. " and "Simulations based on our laboratory results and those of our colleagues at ZSW show that, taking into account both aging processes, the batteries in the BPT-S 5 Hybrid can be used for up to 20 years", accessed on March 29, 2014.
- ↑ "According to the manufacturer, the cells have an expected service life of 20 years and could be charged up to 15,000 times" ( Memento from June 9, 2014 in the Internet Archive ), solarserver.de, accessed on March 29, 2014.
- ↑ VARTA Storage guarantees 14,000 cycles for battery storage. July 13, 2015, accessed July 13, 2015.
- ↑ VARTA Storage extends warranty for battery storage to 14,000 cycles. ( Memento of July 13, 2015 in the Internet Archive ) accessed on July 13, 2015.
- ↑ Development of a modular battery management system for lithium polymer accumulators on esa.informatik.tu-darmstadt.de. Accessed June 4, 2019
- ↑ Tesla Roadster - battery lasts longer than expected. (No longer available online.) In: greenmotorsblog.de. Archived from the original on April 7, 2014 ; accessed on March 31, 2014 .
- ↑ Plug In America Research Shows That Tesla Roadster Battery Performance Bests Tesla Motors' Own Projections. ( Memento of February 3, 2016 in the Internet Archive ) pluginamerica.org, accessed on March 31, 2014.
- ↑ Battery guarantee : 8 years, unlimited km. teslamotors.com, accessed April 5, 2014.
- ↑ Battery upgrade? Unlikely! In: time online. April 1, 2015, accessed February 22, 2016.
- ↑ Winston Batery: data sheet WB-LYP100AH. accessed August 22, 2017.
- ↑ The OnePlus 3 is official. Quote: If the battery is empty, it goes from zero to 60 percent in 30 minutes, according to the manufacturer . Retrieved June 15, 2016.
- ↑ phonearena.com OnePlus 3's Dash charging solution is fast and cool: 63% of battery juice in 30 minutes, June 14, 2016.
- ↑ New charging station: charge electric cars in 20 minutes. In: golem.de , BMU, March 2011.
- ↑ Depending on the station, the charging time takes between 30 minutes (DC charging station) and around eight hours (domestic socket). In: zeit.de.
- ↑ The batteries in the Renault Zoe can be charged up to 80 percent in the fastest of four charging speeds in 30 minutes. In: bild.de.
- ↑ With a quick charger, the i3's battery can be charged to 80 percent in just 30 minutes. In: golem.de.
- ↑ byd-auto.net ( Memento from February 6, 2016 in the Internet Archive ) BYD website: 40 (min) / 15 (min 80%).
- ↑ Inside EVs, January 2017: 400 “Ultra-Fast” 350 kW Charging Station Network Planned By 4 Automakers For Europe , accessed August 22, 2017.
- ↑ all-electronics.de, August 2, 2016: Standardization of high-voltage charging systems: HPC. accessed August 22, 2017.
- ↑ heise.de, October 21, 2016: European 350 kW charging station corridor , accessed August 22, 2017.
- ↑ electrive.net, January 3, 2017: Elon Musk: Tesla Supercharger V3 with over 350 kW. accessed August 22, 2017.
- ↑ Pascal Hartmann, Conrad L. Bender, Milos Vračar, Anna Katharina Dürr, Arnd Garsuch, Jürgen Janek, Philipp Adelhelm: A rechargeable room-temperature sodium superoxide (NaO2) battery . In: Nature Materials . 2012, doi : 10.1038 / nmat3486 .
- ^ Ridiculously-Fast-Charging Batteries (Not Supercapacitors) Developed In Norway. In: cleantechnica.com.
- ↑ De har lagt grunnlaget for batterier som kan lades 1000 ganger raskere. In: tu.no.
- ↑ Galaxy S4 charged in 30 seconds: StoreDot demonstrates new battery technology. In: netzwelt.de , accessed April 9, 2014.
- ↑ "Inexpensive" quantum dot battery charges in 30 seconds. In: winfuture.de , accessed April 9, 2014.
- ↑ “A new type of battery reaches a 70 percent charge after just two minutes on electricity. Electric cars in particular should benefit. ” ( Memento from October 20, 2014 in the Internet Archive ), bluewin.ch, accessed December 30, 2014.
- ↑ "Ultra-fast charging batteries that can be 70% recharged in just two minutes" , sciencedaily.com, accessed December 30, 2014.
- ↑ "New battery charges in a few minutes" , golem.de, accessed December 30, 2014.
- ↑ “Lithium-Titan charges in seconds” , elektroniknet.de, accessed December 30, 2014.
- ↑ Inexpensive: Researchers develop batteries from organic material , Deutsche Mittelstands Nachrichten , accessed January 28, 2014.
- ↑ "Researcher: Aluminum storage device 'has everything you can dream of for a battery'" , ecomento.tv, accessed May 14, 2015.
- ↑ Meng-Chang Lin et al: An ultrafast rechargeable aluminum-ion battery . In: Nature . tape 520 , 2015, p. 324–328 , doi : 10.1038 / nature14340 .
- ↑ Kai Stoppel: Tough progress in research. The dream of a super battery is about to burst. Interview with Dirk Uwe Sauer, Head of the Institute for Power Electronics and Electrical Drives at RWTH Aachen University. n-tv.de, August 31, 2015, accessed on November 29, 2015 .
- ↑ StromAir (Alias): DE relies on batteries with lithium-sulfur / lithium-air. Summary of the lecture by Dr. Patrick Plötz from the Competence Center Energy Technologies and Energy Systems, Fraunhofer Institute for Systems and Innovation Research ISI on August 31, 2015 at the 2nd Swiss eSalon in Bern on the topic of battery perspective. tff-forum.de, August 31, 2015, accessed on November 29, 2015 .
- ↑ Metal-air battery . Energy Storage Funding Initiative, October 18, 2016
- ↑ Magnesium-air batteries promise four times the range for electric cars. New battery technology. In: ingenieur.de. VDI Verlag, January 4, 2019, accessed on November 27, 2019 .
- ↑ C. Zhu, P. Kopold, PA van Aken, J. Maier, Y. Yu: High Power – High Energy Sodium Battery Based on Threefold Interpenetrating Network. In: Adv. Mater. 28, 2016, pp. 2409-2416. doi: 10.1002 / adma.20150594 .
- ↑ Japanese researchers want to build sodium as an alternative to lithium. Perfect sodium compound calculated. In: ingenieur.de. VDI Verlag, February 12, 2019, accessed on November 27, 2019 .
- ↑ a b Paul Donohoo-Vallett include: Revolution Now ... The Future Arrives for Five Clean Energy Technologies - 2016 Update . United States Department of Energy . Retrieved November 6, 2016.
- ↑ Ingo Stadler: Energy Storage - Demand, Technologies, Integration . Springer Vieweg, Berlin 2014, ISBN 978-3-642-37379-4 .
- ↑ Full load . In: Technology Review . February 24, 2016. Retrieved June 26, 2016.
- ↑ Chevrolet Bolt battery cells to cost "industry-leading" $ 145 per kWh , GM: Chevrolet Bolt Arrives In 2016, $ 145 / kWh Cell Cost, Volt Margin Improves $ 3,500
- ↑ Is the combustion engine over? . Quote: "At the moment, one kilowatt hour costs us around 80 dollars," reveals Renault electrical expert Eric Feunteun ". In: blick.ch , July 2017. Retrieved on July 16, 2017.
- ↑ Electric drive before the breakthrough? This car could change everything. In: focus.de , July 6, 2017. Retrieved July 16, 2017.
- ^ Gert Berckmans et al .: Cost Projection of State of the Art Lithium-Ion Batteries for Electric Vehicles Up to 2030 . In: Energies . tape 10 , no. 9 , 2017, p. 1314 ff ., doi : 10.3390 / en10091314 .
- ↑ Chevrolet Bolt battery cells to cost "industry-leading" $ 145 per kWh , study on electric cars: 80 percent drop in prices for batteries between 2010 and 2016
- ↑ Airbus and Siemens are working on the electric aircraft . In: Manager Magazin . April 8, 2016. Retrieved June 26, 2016.
- ↑ Hotzenblitz with lithium-polymer batteries Article on the conversion project of the companies Kruspan Engineering and MDW-Temperatursensorik GmbH , Solar- und Elektromobil Nachrichten.