relay
A relay [ ʁəlɛː ] ( Pl. : Relay [ ʁəlɛːs ]) is a by electrical current driven, electromagnetically acting, remote controlled switch with normally two switch positions. The relay is activated via a control circuit and can switch other circuits.

Working method
A mechanical relay mostly works on the principle of the electromagnet . A current in the excitation coil generates a magnetic flux through the ferromagnetic core and a movably mounted, likewise ferromagnetic armature located on it . A force is exerted on the armature at an air gap, causing it to switch one or more contacts . The armature is returned to its original position by spring force as soon as the coil is no longer excited.
Schematic structure
As an example, a hinged armature relay with a normally open contact (also called a normally open contact) is shown here. The left picture shows the relay in the rest position; the coil is dead, the normally open contact is open. In the picture on the right, a voltage is applied to the coil, which attracts the armature to the iron core of the coil and closes the normally open contact.
![]() |
![]() |
Terms
A contact is referred to as a normally open contact or normally open contact if it is open when the armature has dropped or the excitation coil is de-energized and closed when the armature or the coil is energized. A contact is referred to as a normally closed contact or normally closed contact if it interrupts the circuit when the relay is energized. A combination of NC and NO contacts is called a changeover contact or a changeover contact. A relay can have one or more such contacts.
A relay is "closed-circuit relay" when it is in idle state current flows through it and is attracted, for example, to monitor power failure or wire breakage. In the other and predominant case, in which it is de-energized in the idle state, it is referred to as an "operating current relay".
In the circuit diagram , relays are always drawn in the dropped-out state, even if they work as closed- circuit relays. Only in rare exceptional cases is the active state shown, which is then specially marked.
use
Relays are electromechanical components. They are mainly used for the following use cases:
- Simultaneous and isolated switching of several load circuits with only one control circuit
- Switching high electrical power with low power (switching amplifier)
- For galvanic separation between the circuit to be controlled and the circuit to be switched
- To achieve low switching resistance in the closed state of the contact with at the same time very high contact resistance in the open state.
Advantages and disadvantages of electromechanical relays
Electromechanical relays have been replaced in many applications by electronic switches that operate with transistors because of their disadvantages . Relays also have advantages over semiconductor switches, which is why they cannot be replaced everywhere
- Disadvantages of electromechanical relays
- Dependency of the insulation capacity on the air pressure or on the height above sea level (except for the hermetically sealed relay housing)
- Vibration and shock sensitivity
- Noise development when switching
- High response and fall time (milliseconds compared to microseconds and nanoseconds for semiconductors, i.e. three to six powers of ten )
- Depending on the contact material, the contact resistance can change with the service life depending on the switched load
- Basic wear (electrical and mechanical), i.e. the maximum achievable number of operations must always be compared with the service life of the module
- Arcing of switching arcs when switching on and off
- Creation of self-induction voltages when switching off the coil - is usually intercepted by a protective circuit
- Advantages of electromechanical relays
- Low contact resistance in the milliohm range with simultaneously low capacitance of the switching path
- High switch-on power or high overload capacity
- Switching path does not have to be protected from induction currents of the switched load by a protective circuit.
- High insulation resistance and high reverse voltage of the switching path (safe galvanic separation )
- Relays do not require cooling like solid-state relays do with high loads
- Relays can switch the smallest signals up to high high- frequency powers and show little tendency towards crosstalk
- Depending on the contact material and the short-circuit current, relays can also switch short-circuits without losing their function
- Switching status can often be seen with the naked eye
- Immunity by pronounced hysteresis behavior and robustness of the coil, it will surge several times without prejudice towards ( EMC and ESD )
Relay types
There is a very large number of different types and designs of relays. In addition, relays can be typed according to various aspects, for example according to the number of switching states possible in the de-energized state, according to design, size, area of application, type or material of the contacts, switching capacity or functional principle. A relay can therefore often be classified as belonging to different types.
The main types are:
Small relay
The term small relay, which is somewhat unclearly defined, includes a large number of relays, mostly used in the low-voltage area, which are often intended for installation on printed circuit boards (“printed relay”). Further examples are DIL relays, comb-guided relays or SMD miniature relays.
Contactor
A relay for considerably higher outputs in heavy current engineering is called a contactor . The current strength and electrical voltage in the load circuit can be many times greater than in the coil. Contactors have a tie rod, the control of which requires a somewhat higher power, and they usually have several switching contacts of the same type, as are required for switching three-phase consumers. There are also so-called auxiliary contactors, which in turn serve to control the aforementioned main contactors.
Solid state relay
Solid-state relays (Engl. Solid state relay , SSR, therefore Germanized and solid-state relays called) are no relays, but electronic devices that switch without moving contacts.
Semiconductor relays are implemented with transistors or thyristors or triacs . They are very durable, suitable for high switching frequencies and unfavorable environmental conditions (moisture, aggressive or explosive gases).
With solid-state relays it is possible to switch alternating voltage during the zero crossing ( zero crossing switch ), with which disruptive impulses can be avoided. There are also semiconductor relays that switch at the peak of the mains voltage or immediately when activated, i.e. momentarily. Peak switches are used to switch inductivities that have little or no residual magnetization and therefore no hysteresis .
A galvanic separation between control circuit and load circuit is achieved with semiconductor relays by means of optocouplers integrated in the component . Compared to mechanical relays, semiconductor relays have higher losses in the load current path and therefore often have to be mounted on a heat sink .
So-called OptoMOS or PhotoMOS relays are similar in structure to optocouplers . On the control side, they work like an optocoupler with an infrared LED and, unlike the semiconductor relays described above, on the load side do not have triacs or thyristors, but MOSFETs with which they can switch direct and alternating voltages. They can only switch small currents, do not have to be cooled and have a lower voltage drop than semiconductor relays, but typically show a higher “ contact resistance ” than mechanical signal relays. They work bounce - free and wear - free and with switching speeds of a few microseconds.
- advantages
- noiseless, insensitive to vibrations
- Low coupling capacities between input and output
- Low switching delay
- No contact bounce
- No mechanical wear, therefore a large number of switching cycles possible
- No interference from magnetic fields, no emission of magnetic fields
- disadvantage
- With power application, higher voltage drops in the output circuit than with relays or contactors
- In comparison to relays, input and output circuits are more sensitive to overload and interference pulses
Bistable relays
Bistable relays are characterized by their property that they can adopt two different stable switching states when de-energized. The bistable relays include:
- Impulse relay (impulse switch)
- Impulse relays (also known as impulse switches in electrical installation technology) switch to the other switching state when a current pulse is received and maintain this status until the next pulse. Maintaining the state is guaranteed by a mechanical lock.
- Latching relay
- Latch relays, also known as remanence relays, use the remanence to remain in the energized state after the excitation current has been switched off. To switch to the other switching state, either a voltage of the same polarity must be applied to a second winding with the opposite direction of winding (double coil relay), or in the case of latching relays with only one winding, a voltage of opposite polarity must be applied to it.
- Backup relay
- Backup relays are mechanically locked in the controlled position. To switch to the other switching state, either a voltage of the same polarity must be applied to a second winding with the opposite direction of winding (double coil relay), or in the case of relays with only one winding, a voltage of opposite polarity must be applied to it. Back-up relays are often used to store states even in the event of power failures and to save power when switching processes have not changed for a long time.
- Double coil relay on the model railway
- In the model railroad also Doppelspulrelais be used. These usually do not use remanence and they are also not mechanically locked. These double coil relays often have a limit switch. The limit switch prevents overheating of undersized coils, which would otherwise burn out under constant load. Such double coil relays are used, among other things, to control signals .
Polarized relay
There are two types of relays that require polarity:
- with polarized relays the polarity of the excitation voltage to be applied is fixed. Polarized relays have an integrated permanent magnet, the field of which is additively superimposed on that of the excitation coil. This reduces the tightening voltage or increases the tightening sensitivity.
- In the case of relays with an integrated freewheeling diode , the voltage can only be applied in the reverse direction of the diode. This variant is mainly found with relays in the DIL housing.
Relays in motor vehicles
Automotive relays are robustly built relays that can withstand the increased requirements in motor vehicles with regard to shock resistance and temperature range. They work with the on-board voltage of 12 V or 24 V and can switch higher currents. As a rule, they have connections with 6.3 mm flat plugs . Often they already contain components (resistor, diode) in the housing to limit the mutual induction voltage of the coil.
Special functions
The "relays", which are designed as plug-in assemblies and a. are installed in the fuse box of motor vehicles, are often relays with additional functions or electronic assemblies or small control units .
- Examples
- Fuel pump relay (time and speed-dependent control of the fuel pump)
- Flasher relay (clock generator for the flasher )
- EGR relay (control of the air pressure and speed dependent exhaust gas recirculation )
- Glow time relay for the glow plug of diesel engines (time control and current path control)
- Interval relay for the windshield wiper (electrical clock generator, some with adjustable or rain-controlled interval time)
- Control for folding exterior mirrors and curb function
Many of these small control units actually still contain a mechanical relay, but the term relay for the entire unit is more historical. In modern cars, most of the functions are integrated in larger central control units - the typical sound of the flasher relay is often generated either by loudspeaker or with a relay that does not switch any load.
Communication relay
Relays have been used extensively in the electromechanical exchanges and telephone systems . They were used for the logical flow control when setting up and clearing the dial-up connections. Relays were permanently assigned to the subscribers in the subscriber circuit as well as the switching network , which mostly consisted of voters . The most important representatives of this type of relay, which can only be found very rarely today, include the flat relay , the round relay, the ESK relay and, as relays with special tasks, e.g. B. the test relay 55 .
AC relay

Electromagnetic relays cannot easily be operated with alternating voltage, since the magnetic field that is supposed to hold the armature constantly reverses its polarity and is therefore too weak or zero in the meantime. As a rule, the armature picks up at voltages with line frequency, but rattles and precise switching of the contacts is not guaranteed. The following relays can be operated with alternating current:
- DC relay with an upstream rectifier (which is occasionally built into the relay housing).
- Phase relay is a relay with two windings on separate iron legs, whereby the current flow in one of the windings is phase-shifted by about 90 degrees by means of a capacitor connected in series. This means that one coil is always fully excited when the excitation current in the other passes through zero.
- Shaded pole relays with a shaded pole have a short-circuit winding. The current induced in the short-circuit loop, which is out of phase with the control current, maintains the holding force while the control current has its zero crossing.
Moving coil relay
The moving coil relay is a special relay polarized with a permanent magnet for low power. The structure corresponds to a moving coil measuring mechanism with a rotatably mounted coil, external permanent magnets and a return spring. Instead of a pointer in front of a display dial, the moving coil relay triggers contacts at certain angles of rotation of the moving coil. Due to the principle of the permanent magnet, moving coil relays can only detect direct quantities such as direct voltage, which is why they are combined with bridge rectifiers in AC voltage applications .
The moving coil relay was used in various forms of electrical network protection in electrical energy networks such as the distance protection relay . If certain limit values previously set on the moving coil relay were exceeded, corresponding warning and shutdown contacts were automatically triggered, which trigger the assigned circuit breakers in substations .
Other relay types
- Bimetal relays do not work electromagnetically, but use the thermal effect of the current flow. They are used for time-delayed switching. A bimetallic strip wrapped with a heating conductor is slowly heated, moves through it and then switches a contact.
- Differential relays have two windings with the same electromagnetic properties and respond to small current differences between the windings . Residual current circuit breakers , for example, work according to the principle of current difference evaluation .
- Coax relays are used to switch high-frequency signals and have a defined line impedance (e.g. 50 Ohm) between the contact path and the shield.
- In addition to the switching contacts, signal relays have an inspection flap which, in the case of the drop flap relay, retains its position until it is acknowledged. The mechanical-optical reporting function also has electrical contacts. In this way, signal relays with current coils can save one-time current exceedance events and display them until they are acknowledged
- Pole reversing relays have two coils and two changeover contacts that are internally connected to an H-bridge for reversing the direction of rotation of DC motors . These relays were also used to control slave clock lines in clock systems.
- Mercury relays used the metal mercury , which is liquid at room temperature and is located in a glass tube under protective gas , to switch the contact . In some older automatic staircase lights, such a glass tube ( mercury switch ) was tilted electromagnetically. Immersion armature relays (also immersion relays) had a magnet armature floating on the mercury, which, like a pull magnet , was drawn into the mercury with a current-carrying coil , thereby increasing its level to such an extent that a contact from the mercury level above was reached. There was also a design in which a magnetically held contact pin falls into the mercury when the magnetic field drops - used in electric fencers . Another design were thermal mercury relays, in which a heating element worked on a gas volume, the thermal expansion of which resulted in a change in the position of the mercury, whereby it opens or closes contacts. Naturally, they reacted quite slowly, which, however, was not a disadvantage in the often common use in temperature controllers or was even used as a time delay. Thermal mercury relays have often been used in conjunction with contact thermometers . Mercury relays were also used as impulse relays thanks to their sophisticated mechanics .
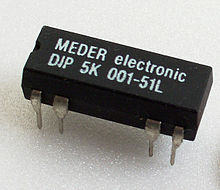
- Reed relays have a contact which is enclosed in inert gas and which is also a magnet armature.
- A signal relay in railway safety technology is a relay that has to meet special design requirements so that it can be used for safety-related circuits.
- Signal relays in electronics have gold or palladium contacts and are specially and only suitable for small currents and voltages. Power relays, however, have z. B. silver-cadmium or silver-tungsten contacts and are suitable for switching higher currents.
- Current relays have a particularly low-resistance coil so that they can be connected in series with an electrical consumer whose current flow is to be monitored .
- Telegraph relays are highly sensitive, polarized relays that played an important role in telex switching.
- Counting relays count results. To do this, they add or subtract pulses and switch as a contact when the current actual value is greater than or equal to an upper threshold value - the setpoint.
- Hybrid relay
- Load shedding relay
- Battery isolating relay
Relay in the broader sense
These relays are also provided with more or less complex mechanics or electronics.
Stepping relays were used to control historical telephone systems, traffic lights or even washing machines.
Timing relays are available in electronic or electromechanical versions; they are used for time control in machines and devices.
One form of the timing relay is the pulse relay. After receiving an activation pulse, it switches the contact for a defined period of time, so it works in the same way as a monostable multivibrator . A typical example is a stairwell switch.
A wiper relay (see also wiper contact ) is a pulse or bistable relay that responds specifically to very short ("wiped") pulses.
Monitoring relays use a sensor to report when certain preset values are exceeded or fallen below. For example, temperatures, fluid levels , voltages, asymmetries in three-phase networks can be monitored using asymmetry relays or any other physically measurable variables.
Characteristic values
The following table lists the most important characteristic values used to specify a relay. In addition, a dimensional drawing, connection assignment, etc. is of course also of interest. The examples relate to a typical 12 V vehicle relay.
Characteristic value | Explanation | example |
---|---|---|
Kitchen sink | ||
nominal voltage | Nominal operating voltage (working range), type of current of the relay coil | 12 V (10 ... 16 V) DC |
Coil current or resistance | Coil current at nominal voltage | 117 mA / 103 Ω |
Pick-up voltage | Typical voltage at which the armature picks up | 3… 7 V |
Dropout voltage | Typical voltage at which the armature drops. It is less than the starting current or the starting voltage. This allows a relay z. B. remain attracted (unintentionally) even with external power supply with lower voltage. | 1.2 ... 4.2 V |
contacts | ||
Contact execution | Number and type of switching contacts | 1 × On (SPST) |
Switching current | Current that can be switched on / off depending on the load and the type of current | 100/40 A |
Continuous current | Current that is allowed to flow continuously when switched on (thermal continuous current load capacity) is usually higher than the cutoff current | 40 A |
Switching voltage | Maximum voltage that can be switched, depending on the load behavior and the type of current | approx. 35 V DC @ 10 A |
Ambient temperature | Temperature range in which the relay may be operated | −40 ... + 85 ° C |
Test voltage | Maximum voltage that may be applied between the coil circuit (winding) and the contact circuit | 500 V AC |
Electrical life | Number of switching operations that the contacts can withstand at a specified load in compliance with the electrical parameters | 100,000 at 20 ° C / 14 V DC / 40 A |
Mechanical life | Number of switching operations that the mechanics can withstand in a specified environment | 1,000,000 at 20 ° C |
Voltage drop or contact resistance | Maximum voltage drop at a specified current or contact resistance across the switch contacts | 2 mΩ (at the beginning) |
Contact material | Material of the contacts, mostly alloys (high switching capacities) or precious metals (signaling purposes) | Silver alloy |
Overall system | ||
response time | Typical / maximum time between applying the actuating voltage and closing the contacts | 6.5 / 15 ms |
Fallback time | Typical / maximum time between falling below the holding current and opening of the contacts | 2/15 ms |
Switching frequency | Maximum operating frequency of the relay | unspecified |
Vibration and shock resistance | Acceleration in the event of shock / vibration (frequency range), in which the relay does not suffer any mechanical damage, the function is retained and the contacts reliably remain in the respective position | 20 g / 4.5 g (10 ... 100 Hz) |
Identification of a relay
Standardized identification of the connections
- A1, A2 : coil
- 11, 12 : normally closed
- 13, 14 : normally open contact (contact closes when voltage is applied to the coil)
- 11, 14, 12 : changeover contact (11 is the common connection (COM), 14 the normally open contact and 12 the normally closed contact)
- 15, 16, 18 : special changeover contact (15 is the common contact, the tongue, voltage must always be applied here)
If relays have several actuating coils, the other coils are labeled A3 / A4 etc. The first digit of the contact designation is increased numerically in a relay with several contacts, the last one indicates the type of relay contact. So called z. B. 53/54 the 5th switching contact, which is a normally open contact.
In the (German) telecommunications system, the following regulation is common (DIN 41220): One designates:
- the arrangement in the contact set with Roman numerals
- the associated contacts with the corresponding lowercase letters
- Coils with capital letters
Usual designation of the switching contacts
In data sheets and comparison tables for relays, English abbreviations are often found for the number of switching contacts and positions:
- Number of contact points:
- The simplest switch has a contact point; one of the conductors is directly connected to the movable switching element:
- SM - Single Make (working contact)
- SB - Single Break (normally closed contact)
- SM-SB - changeover contact
- There are also switches with two contact points, whereby the movable switching element either creates or disconnects the connection between the two conductors (common with contactors):
- DM - Double Make (working contact)
- DB - Double Break (normally closed contact)
- DB-DM - changeover contact
- P Pole - number of switching contacts ( S ingle, D ouble, ...)
- Order of Abbreviations:
- A contact arrangement is identified as follows:
- Number of poles
- Switch positions (throws)
- Idle state (normal position)
- Occasionally a break-make specification follows (mostly omitted)
- NC, NO and changeover contacts:
- NC - Normally Closed = normally closed contact; also: break
- NO - Normally Open = normally open contact; also: Make
- CO - Change Over = changeover contact; also: Break - Make (BM)
- T Throw - number of switching positions ( S ingle, D ouble)
Some examples:
SPST NO = S ingle P ole, S ingle T hrow, N ormally O pen - Single pole switch with normally open contact |
SPDT - single pole changeover switch (also: SP CO) |
DPST NO - two-pole on-off switch |
DPDT - two-pole changeover switch (also: DP CO) |
Switching of relays with transistors
When controlling the relay coil with a transistor , it should be noted that self-induction when switching off the current through the relay coil creates a high voltage with opposite polarity. This voltage clearly exceeds the nominal voltage of the relay and can destroy the transistor by exceeding the maximum reverse voltage of the transistor.
In order to prevent the destruction of the switching transistor (T1 in the figure), this counter voltage is short- circuited by a freewheeling diode (D1 in the figure) or limited to the forward voltage of the diode. However, this means that the magnetic field in the coil collapses more slowly and the switching time of the relay is significantly longer.
The disadvantages with regard to the switching time of variant A are solved by adding a zener diode (ZD 1 in the figure, variant B), the zener voltage of which should roughly correspond to the nominal voltage of the relay - the magnetic field in the coil can collapse much more quickly. It should be noted, however, that the reverse voltage of the switching transistor must still be greater than the operating voltage plus Zener voltage in order to prevent its destruction.
There are other protective circuits, for example with a parallel protective resistor or with an RC element ( snubber ) matched to the inductance of the coil . These measures work independently of polarity and are also suitable for relays with AC actuation.
Some relay types already have a built-in free-wheeling diode or a protective resistor.
There are also special switching transistors suitable for switching inductive loads, which in turn have a built-in limiter diode (e.g. the Darlington transistor 2SD1843).
History of the relay
telegraphy
Around 1820, research into electronic data transmission focused on electromagnetism. Early models were designed by André-Marie Ampère, Pierre-Simon Laplace and many others. Became known z. B. Joseph Henry in 1835, who developed communications from his laboratory to his house himself, or Charles Wheatstone , who introduced rail telegraphy in England in 1837 with William Fothergill Cooke. After correspondence with J. Henry, Samuel Morse improved the relay so that it responded to weaker impulses and used it as a signal amplifier . The idea of a telegraph had been around since the mid-18th century, but the relay was ultimately the key to success. It had to be inserted into the signal path of the telegraph lines every 30 km in order to regenerate the incoming weak signals. This created the basis for transmitting impulses over long distances. The first demonstration of the telegraph took place between Washington, DC and Baltimore in 1844 . Based on the post office relay stations, where the mail riders could exchange their horses for fresh ones, the new device was named relay .
Telephone exchange
A major impetus for the further spread of the relay was the introduction of subscriber self-selection in telephone switching technology at the end of the 19th century. The first self-dialing device in Germany was put into operation on July 10, 1908 in Hildesheim for local traffic with 900 participants. National telephone traffic was gradually automated from 1923 and would have been inconceivable without the massive use of relay technology.
Relay at the beginning of computer development
The relay also enabled the development of the computer , which was first built in 1941 by Konrad Zuse under the name " Z3 " with 2,000 relays for the arithmetic unit and the memory.
In computer technology, however, relays were largely replaced by electron tubes as early as the mid-1940s . Later the function of transistors and integrated circuits (IC) was taken over.
See also
literature
- Werner M. Köhler: Relay basics, designs and circuit technology . 2nd Edition. Franzis-Verlag, Munich 1978, ISBN 3-7723-1602-6 .
- Harry Dittrich, Günther Krumm: Elektro-Werkkunde . Volume 5: Professional experience for telecommunications installers, telecommunications electronics technicians, telecommunications mechanics and telecommunications craftsmen with technical calculations and technical drawings. 5th edition. Winklers Verlag, Darmstadt 1973.
- Günter Springer: Expertise in electrical engineering . 18th edition. Verlag Europa-Lehrmittel, Wuppertal 1989, ISBN 3-8085-3018-9 .
Web links
- Relay glossary
- Terms and general information about the structure of industrial relays
- Representation in the virtual physics museum of the Laurentianum grammar school
- State education server Baden-Württemberg
- Relays as one of the main components in electromechanical switching technology
- eltako.com (PDF)
Individual evidence
- ↑ relko.cz
- ↑ Type CB1a-12V. Panasonic, accessed October 19, 2019 .
- ↑ panasonic-electric-works.de Inrush current, not specified, but tested, see page 6