Biogas plant
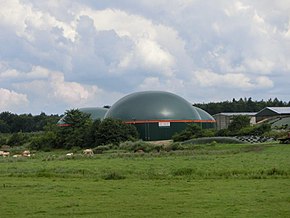

A biogas plant of production is of biogas by fermentation of biomass . In agricultural biogas plants, mostly animal excrement ( liquid manure , solid manure ) and energy crops are used as a substrate . In non-agricultural facilities, material from the organic waste bin or waste products from food production are used. A fertilizer known as digestate is produced as a by-product . In most biogas plants, the gas produced is used on site in a block-type thermal power station (CHP) to generate electricity and heat . Other biogas plants process the gas obtained into biomethane and feed it into the natural gas network.
Principle of a biogas plant
material | Biogas yield in m 3 per ton of fresh mass |
Methane content |
---|---|---|
Corn silage | 202 | 52% |
Grass silage | 172 | 54% |
Rye GPS | 163 | 52% |
Pressed sugar beet pulp ensiled |
125 | 52% |
Fodder beet | 111 | 51% |
Biowaste | 100 | 61% |
Chicken litter | 80 | 60% |
Pig manure | 60 | 60% |
Cattle manure | 45 | 60% |
Grain Meat | 40 | 61% |
Pig manure | 28 | 65% |
Cattle manure | 25th | 60% |
The anaerobic (without oxygen) microbial degradation ( fermentation ) of the substrate used takes place in a biogas plant . This usually consists of easily degradable biomass such as liquid manure, energy crops (especially maize , grain and grass silage ), agricultural by-products or biowaste . Straw and wood, which mainly contain cellulose and lignocellulose , are difficult or impossible to degrade under anaerobic conditions and are therefore not used.
Different types of microorganisms use the complex biomass (mainly carbohydrates , fats and proteins ) as nutrients and energy suppliers. In contrast to aerobic digestion (with oxygen , such as in composting ), the organisms can only use a small part of the energy contained in anaerobic fermentation. The anaerobically unusable energy is in the "waste product" methane .
The main products of anaerobic degradation are high-energy methane (CH 4 ) and carbon dioxide (CO 2 ). Since both are gaseous, they separate from the fermentation substrate and form the main components of the biogas. CO 2 cannot be further oxidized; H. it doesn't burn. However, it does not have to be separated from the high-energy CH 4 and can be burned together with this in the combined heat and power plant.
Substrates for biogas production
→ Main article: substrate (biogas plant)
The raw material used to generate biogas is called a substrate or input material. Any type of biomass that is degraded under anaerobic conditions ( fermentation ) is suitable . The respective chemical composition, in particular the carbohydrates , fats and proteins contained , is decisive for the amount of biogas that can be generated and its methane content.
In practice, the purchase and cultivation costs, the remuneration and bonuses set by the Renewable Energy Sources Act (EEG) and the suitability of the biogas plant determine the substrate used.
Whereabouts of the substrate
Part of the substrate serves the microorganisms as a nutrient to build up their cell mass ( anabolism ). The energy required for this is obtained from the fermentation of the substrate. Since the energy gain is low compared to aerobic respiration , comparatively large amounts of substrate have to be converted per cell mass produced.
In the case of easily degradable substrates, a large part of the dry matter is converted into the biogas. What remains is the so-called fermentation residue , an aqueous mixture of poorly degradable organic material such as lignin and cellulose , as well as inorganic , i.e. organic material . H. predominantly mineral substances . The digestate is mostly used as agricultural fertilizer . It still contains all of the trace elements of the substrate, almost all of the nitrogen , phosphorus and - depending on the type of process used in the biogas plant - almost all of the sulfur.
Microbial processes
The anaerobic degradation of biomass is the basis for the formation of digester gases such as landfill , sewage , swamp and biogas. Many different types of microorganisms are involved. Occurrence and proportions of the species depend on the type of substrate, the pH value , the temperature and the fermentation process . Due to the diverse metabolism of the community of microorganisms, most organic substances can be broken down. Only cellulose fibers and lignified parts of lignocellulose are enzymatically difficult to break down. A sufficient proportion of water in the fermentation substrate is a prerequisite for methane formation .
The breakdown process is shown schematically in four successive individual biochemical processes (phases). The current system concepts usually provide for a continuous supply of substrate to the fermenter so that the four phases take place in parallel.
1st phase: hydrolysis
Microorganisms cannot process the polymeric macromolecules of carbohydrates and proteins directly. Various types of exoenzymes , such as amylases , proteases and lipases , which hydrolyze the macromolecules to soluble oligomers and monomers , therefore serve as auxiliary substances . Carbohydrates such as starch and hemicellulose are broken down into oligo- and monosaccharides (multiple and single sugars). Proteins are broken down into peptides or amino acids . Fats can into their component fatty acids and glycerin , hydrolyzed be.
2nd phase: acidogenesis or acidification phase
The products of hydrolysis are metabolized by acid-forming microorganisms in the course of acidogenesis to lower fatty and other carboxylic acids , such as valeric , butyric and propionic acids , and alcohols such as ethanol . The breakdown products of proteins are hydrogen sulfide (H 2 S) and ammonia (NH 3 ).
3rd phase: acetogenesis or vinegar-forming phase
During acetogenesis , the lower fatty and carboxylic acids and the lower alcohols are converted into acetic acid ( acetate ), hydrogen and carbon dioxide by acetogenic microorganisms .
4th phase: methanogenesis or methane-forming phase
In the past, only anaerobically running phase - the methanogenesis - the acetic acid is carried out by appropriately acetoclastic methanogens according to equation 1 in methane converted. According to Equation 2, around 30% of the methane is formed from hydrogen and CO 2 , the intermediate products from acetogenesis.
Contrary to previous textbook opinion, methane formation in agricultural biogas plants takes place predominantly via the hydrogenotropic (hydrogen utilizing) reaction path with shorter residence times and higher temperatures. Acetate is not necessarily split directly into carbon dioxide and methane (acetoclastic, acetic acid splitting path), but first converted to hydrogen and carbon dioxide (syntrophic acetate oxidation in Fig. 3, Schnürer et al. 1999), which is then converted into biogas via hydrogenotrophic methanogenesis implemented. The formation of methane via acetic acid cleavage occurs to a significant degree only with a comparatively low volume load or longer residence time and low acetic acid contents (Lebuhn et al., 2008a, 2009; Bauer et al., 2008, 2009). As an energy-supplying (exothermic) process (–ΔH ° ´: released reaction energy), methanogenesis enables the energy-consuming reactions of acetogenesis and syntrophic acetate oxidation (+ ΔH ° ´: energy-consuming reaction).
Cleaving acetic acid (acetoclastic):
(1) CH 3 COO- + H + → CH 4 + CO 2 (ΔH ° ´ = –35.9 kJ / mol)
Utilizing hydrogen (hydrogenotropic):
(2) CO 2 + 4 H 2 → CH 4 + 2 H 2 O (ΔH ° ´ = –131.0 kJ / mol)
The four phases cannot be strictly separated, as acetic acid, hydrogen and methane are already formed during acidogenesis . Methanogenesis, on the other hand, requires the special metabolic abilities of methanogenic microorganisms. These belong to the group of archaea (the class Methanobacteria, Methanococci and Methanomicrobia [10]) and are only distantly related to the bacteria that carry out the other steps of degradation.
Plant operation
Little is known about the exact interaction of the microorganisms. Therefore, the optimal setting of the various parameters (type of substrate, amount of substrate, temperature, agitator settings, etc.) can often only be found experimentally. In research projects characterizations of the microbiological populations or communities are carried out in order to better understand the relationships.
At low substrate concentrations, a not inconsiderable part of the waste heat from the biogas conversion is required to maintain the fermenter temperature of the wet fermentation in the mesophilic target range of 30 to around 35 degrees Celsius. Systems with dry fermentation require a significantly lower proportion of the heat produced. The use of waste heat for heating buildings or for drying wood and grain can be an important factor for the overall efficiency and profitability of a biogas plant.
Various z. Sometimes quite different system concepts are used in practice, which are primarily based on the composition of the substrate. But the framework conditions of the Renewable Energy Sources Act for the remuneration of the electricity fed into the grid also play a role. Hygiene regulations and the avoidance of emissions must also be taken into account when planning the biogas plant.
Wet and dry fermentation
The fermentation substrate of the wet fermentation has a high water content. It is stirrable and flowable and is continuously mixed during the fermentation. The dry fermentation or solid fermentation takes place with stackable organic biomass that neither liquefied nor constantly mixed during the fermentation. The choice of process depends essentially on the substrates.
Only wet fermentation can be used for the use of liquid manure , while structurally rich biomass can block the agitators required for wet fermentation. For wet fermentation, the solid biomass is crushed well and made pumpable by adding water. In Germany, wet fermentation is predominant because most of the plants were built by cattle-raising farmers who often use both energy crops and liquid manure.
The domain of dry fermentation is the fermentation of stackable biomass, such as occurs in horticulture and landscaping , as well as meadow or field grass. Dry fermentation is also used to supplement or replace composting . Even with "dry fermentation", the microorganisms necessary for fermentation require sufficient moisture.
As of 2004, within the framework of the Renewable Energy Sources Act (EEG), a technology bonus of 2 cents / kWh was paid for the electricity generated by dry fermentation. In the following years, the importance of dry fermentation also increased significantly in agriculture. The technology bonus does not apply to newly built systems from 2009, as the process is now considered an established technology.
Batch and continuous fermentation
Most plants are operated with continuous fermentation, in which the process is usually fed several times a day substrate and biogas and digestate are removed. The ability to automate and the relatively uniform gas production are advantageous , so that subsequent components such as gas cleaning, gas processing and combustion in the block-type thermal power station (BHKW) also take place continuously. In addition to wet fermentation, dry fermentation can also allow continuous plant operation.
When the dry matter content is high or the substrate is very fibrous or compact, e.g. organic waste , household waste and green waste , batch fermentation is often used. The biogas production is completed for each substrate batch and the fermenter is emptied before the next batch is introduced. The staggering of several fermenters also enables quasi-continuous gas production here.
Single and multi-stage systems
The individual steps of microbial degradation have certain optima. The hydrolysis runs optimally at a low, slightly acidic pH value , which is why many systems have a hydrolysis stage with a downstream methane stage. The methanogenesis contrast preferably runs off in a slightly alkaline medium. Often, however, there is only one or more fermenters connected in parallel without separating the degradation stages. As a rule, a storage container is connected downstream, which is hermetically sealed and functions as a secondary fermenter.
Use of the products
Biogas
→ Main article: biogas
In Germany, biogas is currently mainly used directly at the biogas plant for decentralized, coupled electricity and heat generation ( combined heat and power ) in combined heat and power plants (CHPs); The biogas is less frequently processed into biomethane . With direct use, the gas mixture is dried, desulphurized and then fed to a biogas engine that drives a generator . The current produced is in the power fed. The heat contained in the exhaust gas and engine cooling water is recovered in a heat exchanger . Some of the heat is required to heat the fermenters, as the microorganisms that break down the biomass grow best at temperatures of 30–37 ° C (mesophilic) or 50–60 ° C (thermophilic). Excess heat from the engine can be used, for example, to heat buildings, dry the grain harvest, dry wood chips or operate aquaculture systems. Systems whose excess heat can be used all year round are particularly economical and energy-efficient.
Biomethane
→ Main article: Biomethane
In several more recent projects, the biogas is purified to natural gas quality in processing plants and fed into the natural gas network as biomethane (bio natural gas) . This increases the profitability of biogas plants at locations without heat consumers. The bio natural gas can, for example, be forwarded to CHP units that are in the immediate vicinity of continuous heat consumers, such as B. swimming pools are built. This means that almost all of the waste heat can be used. Processed biogas can also be used as fuel for vehicles that run on natural gas. The system technology for processing biogas into biomethane and feeding it into the natural gas network is currently still quite cost-intensive and only economically viable for "large systems" (from 1.5 MWel).
Digestate
→ Main article: Digestate
The fermentation residues from biogas plants are used as agricultural fertilizers. They are more tolerable for the plants than raw liquid manure, the nitrogen availability is higher and the smell less intense. The digestate from wet fermentation ("biogas slurry") is a substance similar to slurry. With dry fermentation, stackable digestate is created, which can also be used as fertilizer and makes up about half of the initial amount. The amount of digestate can be further reduced by aerobic aftertreatment, which also reduces the burden of germs (disinfection) and hydrogen sulfide compounds. In addition, incineration is possible to further reduce quantities and generate energy.
Development of biogas plants
General technical and market-related development
As early as 1789, the Italian physicist Alessandro Volta investigated a flammable gas that was formed in the sediment of Lake Como. Scientists such as Faraday (who identified the gas as a hydrocarbon ), Davy, and Dalton have replicated Volta's experiments. Avogadro discovered the chemical formula for methane (CH 4 ). This easily generated gas was very popular in physical and chemical experimental lectures in the 19th century.
At the end of the 19th century it was discovered that wastewater can be treated by anaerobic digestion. From 1906 wastewater treatment plants with heated fermenters were built in the Ruhr area. The primary goal at that time was not biogas production, but waste reduction. It was not until around 1922 that biogas was collected and fed into the urban gas network. Some sewage treatment plants were able to cover their operating costs with it. By 1937, some German cities had converted their vehicle fleets to biogas. The garbage collection of the city of Zurich ran on biogas until 1973.
Attempts to obtain biogas not only from wastewater were made in the late 30s and then again in the 50s, first with solid manure and later with liquid manure. About 50 plants were built. These attempts were discontinued because of the cheap availability of oil.
The energy crisis of 1973 made biogas technology topical again. However, falling oil prices again slowed further development.
Due to the larger amount of agricultural waste or liquid manure relative to the area that can be used as arable land, the Netherlands, Switzerland (see Kompogas ) and Sweden gained experience with biogas at an early stage. In these countries it is used less often to generate electricity locally, but is more often processed into biomethane. In the Netherlands and Switzerland it is fed into the natural gas network. In Sweden it is used for motor vehicles.
The oil glut from 1955 to 1972 and the subsequent oil crisis from 1972 to 1973 as well as the national legal framework such as the Renewable Energy Sources Act in Germany had a decisive influence on the spread of biogas use .
In India, biogas was already being used for energy supply at the end of the 19th century. Many small biogas plants exist in countries like India, South Korea, Taiwan, Malaysia and also in Botswana for private energy supply. There are over 40 million home appliances in China . The biogas is mainly obtained from manure and excrement and is mainly used for cooking and heating purposes, which reduces local deforestation and improves people's quality of life.
Development in Germany
The cultivation of renewable raw materials for biogas use in Germany increased from 400,000 hectares in 2007 to 530,000 hectares in 2009.
The number of systems and the installed electrical power has also risen sharply in recent years. A comparatively high increase can be seen in the first amendment to the Renewable Energy Sources Act (EEG), which came into force in 2004 . While the number of systems in 2004 before the amendment was still 2010, in 2005 there were already 2,690 systems in Germany. In 2007 this number increased further to 3711. This development can be explained by the increase in the remuneration for the kWh generated by biogas plants . The electrical output rose from 247 MW in 2004 to 665 MW in 2005 to 1270 MW in 2007. As the output of newly installed systems increases, the total output increases faster than the number of systems. Because many biogas plants release a large proportion of the waste heat into the environment without being used, there is still further potential here, for example through the development of local heating networks or processing into biomethane.
In 2009, 4671 biogas plants were in operation in Germany, producing a total of around 11% of electricity from renewable energies. At the end of 2011, 7,100 biogas plants with an installed capacity of around 2,800 MW were in operation, corresponding to the nominal output of two large nuclear power plants . With the EEG 2012 and the new remuneration structure, the addition of biogas plants in 2012 was significantly lower than in the previous year. The German Biogas Association states the number of plants as of December 31, 2012 at 7,515 with an installed capacity of 3,352 MW.
With the 2nd amendment of the EEG, valid from 2009 to 2011, a slurry bonus was introduced, which is intended to promote smaller plants with a high proportion of slurry. In Germany, it is estimated that only 15% of the manure available from animal husbandry is used for energy. With the use of this potential, biogas technology could further expand its contribution to climate protection.
The EEG 2012 no longer provides for bonuses.
With the introduction of the EEG 2014 on August 1, 2014, the focus will be on the use of agricultural residues, the use of renewable raw materials in new plants to be built de facto no longer plays a role. The new construction of agricultural biogas plants is mainly limited to plants in the power range up to 75kWel, the so-called farm biogas plants. The main input materials of this plant class are liquid manure and manure from the respective local animal production on the “farm”.
Remuneration in Germany
In Germany, the feeding of renewable electricity into the power grid is regulated by the Renewable Energy Sources Act (EEG). The operators of the transmission grids have to purchase the generated electricity at defined prices, but can pass these costs on to the end customer. The additional costs for the mandatory purchase of electricity are compensated between the transmission system operators so that the additional burden on the end customer is the same nationwide. The level of remuneration in accordance with the 2009 EEG amendment is shown in simplified form in the table below. If the biogas is only used thermally, the biogas plant operator does not receive any EEG remuneration. For landfill and sewage gas, the EEG defines its own minimum remuneration rates and bonuses.
Plant size | Base salary (2009) |
NaWaRo bonus |
CHP bonus |
Technology bonus |
Liquid manure bonus |
Formaldehyde bonus |
---|---|---|---|---|---|---|
up to 150 kW el | 11.67 | 7th | 3 | up to 2 | 4th | 1 |
up to 500 kW el | 9.18 | 7th | 3 | up to 2 | 1 | 1 |
up to 5 MW el | 8.25 | 4th | 3 | up to 2 | 0 | 0 |
up to 20 MW el | 7.79 | 0 | 3 | 0 | 0 | 0 |
The remuneration is guaranteed for 20 years from the year of commissioning. There is no adjustment for inflation . A degression of the remuneration of 1% per year applies to new systems. For a system that was commissioned in 2009, the tariff rates according to EEG 2009 apply for 20 years. A system that is commissioned in 2010 receives 99% of these rates for 20 years and so on.
The NaWaRo bonus is granted if only plants or plant components are used in the biogas plant that arise in agriculture , forestry , horticulture or landscaping and have no other purpose than utilization in the biogas plant. In addition, liquid manure may also be used in a NaWaRo plant. If there is at least 30% manure content in the substrate (at any time), a manure bonus is also granted, which is 4 cents for systems up to 150 kW el and 1 cents / kWh el for systems up to 500 kW el .
The amount of the CHP bonus is variable, depending on the system concept. It depends partly on the power to heat ratio from (SKZ) that by dividing the electric through the thermal efficiency of the cogeneration plant is calculated. Multiplying the SKZ and the amount (kWh th ) of the actually and sensibly used CHP waste heat results in the amount of electricity (kWh el ) for which the bonus is actually granted. A high degree of electrical efficiency and a large amount of heat actually used provide a high bonus. Eligible heat utilization concepts are defined by the EEG 2009.
The technology bonus is granted when new technologies are used in the biogas plant, provided that heat is used or certain electrical efficiencies are achieved. These can e.g. B. the use of a Stirling engine , an ORC turbine , a Kalina process , a fuel cell or a gas turbine . In addition, the bonus applies when processing the biogas to natural gas quality for feeding into the gas network and for certain processes for the fermentation of biowaste.
For systems up to 500 kWel, an emission reduction bonus (increase of the basic remuneration by 1.0 c / kWh for systems according to BImSchG when complying with the corresponding formaldehyde limit values according to the emission minimization requirement of TA Luft) of 1 cent / kWh is granted if certain limit values are observed.
Significant innovations compared to the EEG 2004 are the abolition of the technology bonus for dry fermentation, the increase in the basic remuneration for small systems and the renewable energy bonus, the introduction of a liquid manure , landscape maintenance material and emission reduction bonus and the structured promotion of gas feed-in for different capacities as well as numerous detailed regulations.
Since the introduction of the EEG 2012, the remuneration structure has been redefined. There are no more bonuses, only basic remuneration and remuneration for assignment classes. There is also a market premium and a flex premium as part of direct marketing.
Tax treatment in Germany
For the tax treatment of biogas plants, see BMF letter of March 6, 2006, IV C 2 - S 2236 - 10/05 / IV B 7 - S 2734 - 4/05.
Development in Switzerland
The cost-covering feed-in tariff (KEV) has been in effect in Switzerland since January 1, 2009 ; This is associated with an increased feed-in tariff (feed-in tariff for electricity generated from biogas) for renewable energies, which also includes biogas. The remuneration consists of a fixed purchase price and an additional so-called agricultural bonus, which is granted if at least 80% of the substrates consist of farm manure. The Swiss funding model is intended to promote sustainable development in the energy sector, as it particularly supports the manure-based and therefore most sustainable biogas plants.
When it comes to biomass utilization, the Swiss funding instrument for renewable energies (KEV) takes into account the fact that there are no areas available for the cultivation of renewable raw materials. So far, the law has not resulted in any increase in agricultural biogas plants in the area of the use of liquid manure. The low attractiveness of green waste as a co-substrate for agricultural systems and the resulting untapped potential has led biogas companies to design new system models. Combined with solid manure, leftover food or organic waste from municipalities, there are new possibilities without having to transport the raw materials over long distances to central plants. The possibility of refining liquid manure at the same time represents a new type of concept for generating renewable energy. The largest biogas plant in Switzerland is operated by Recycling Energie AG in Nesselnbach .
safety
Since large quantities of flammable gases are generated and processed in biogas plants, operational safety is of great importance. If the biogas plant is operated incorrectly, if there are design errors or material damage, there is a possibility of a deflagration or explosion. In 2007 there were around three accidents in biogas plants (in Riedlingen , Walzbachtal and Deiderode ). The entry of fermentation substrates or fermentation residues into bodies of water caused fish to die in the course of an accident in Barßel . In individual cases, harmful gases can be emitted to a considerable extent, e.g. B. Hydrogen sulfide in an accident at Zeven in 2005, in which four people died.
reviews
In addition to hydropower plants , solar plants , biomass heating (power) plants and wind power plants , biogas plants are important producers of electricity and heat from renewable energies . Advantages and disadvantages also vary with substrate type and system construction:
advantages
- Renewable energy source with locally available, renewable raw materials ; thereby saving fossil fuels
- Use of plants and plant parts that cannot be used otherwise, such as biowaste, catch crops, crop residues and other by-products
- Higher energy yield per cultivated area compared to other bioenergies such as biodiesel and BtL fuel
- The decentralized power generation reduces the effort of power distribution to the end user.
- Base load capacity as well as the possibility of demand-based generation, also through the storage of biogas; thus a good addition to electricity generation from wind power and solar systems
- Processed biogas can be fed into the natural gas network as biomethane and replace natural gas in the electricity, heat and transport sectors.
- Improved fertilizer quality of the digestate compared to raw liquid manure:
- reduced odor and less caustic effect during application
- better plant availability of nutrients
- The fermentation of liquid manure reduces methane and odor emissions (minimization of GHG emissions).
- Increased added value and alternative income for the agricultural area
- Saving of artificial fertilizers by using arable digestate
disadvantage
- Negative environmental influences through intensification of agriculture (e.g. decline in species).
- Regional competition for land between areas used for food, feed and energy crops. In developing countries in particular, there is a threat of a shortage of arable land for food supply.
- The rise in lease prices for agricultural land and high investments by farmers indirectly lead to an increase in food prices.
- Gases generated in the biogas plant can lead to explosion, asphyxiation or poisoning. Protein-rich substrates increase the proportion of the highly toxic hydrogen sulfide in biogas.
- Unscheduled escaping methane has a 25 times higher greenhouse effect than carbon dioxide.
- It must be prevented that manure from animals that have been treated with antibiotics gets into the digester in too high a concentration .
See also
literature
- Biogas guide - from extraction to use. Fachagentur Nachwachsende Rohstoffe e. V. (FNR). 5th edition 2010. ISBN 3-00-014333-5
- Comprehensive, up-to-date 272-page literature on biogas and (agricultural) biogas plants. The handout can be obtained free of charge from the FNR.
- Biogas measuring program II - 61 biogas plants in comparison. Fachagentur Nachwachsende Rohstoffe e. V. (FNR). 1st edition 2010, ISBN 978-3-9803927-8-5 , ( online ), comprehensive, up-to-date 168-page literature to compare 61 biomass biogas plants that only use energy crops and manure.
- B. Eder, H. Schulz: Biogas practice. Basics, planning, plant construction, examples and profitability of biogas plants. Ökobuch Verlag Staufen 2006, 3rd edition, ISBN 978-3-936896-13-8
- M. Madigan, J. Martinko, J. Parker: Brock - Microbiology. Spektrum Akademischer Verlag Heidelberg, German translation, Berlin 2001, ISBN 978-3-8274-0566-1
- Safety rules for biogas plants. Social insurance for agriculture, forestry and horticulture (Ed.) ( PDF )
- Brochure biogas plants in agriculture. aid information service. 5th edition 2009, ISBN 978-3-8308-0856-5
- Biogas figures of thumb. Board of Trustees for Technology and Construction in Agriculture V. (KTBL). 2nd edition 2009, ISBN 978-3-941583-28-3
Individual evidence
- ↑ Fachagentur Nachwachsende Rohstoffe e. V. (FNR): Biogas basic data Germany. (PDF; as of October 2008). Source for all information except for pressed pulp.
- ↑ Biogas yields of different substrates, division potatoes / beets lfl.bayern.de, see pressed pulp ensiled .
- ↑ Basics of biogas ( page no longer available , search in web archives ) Info: The link was automatically marked as defective. Please check the link according to the instructions and then remove this notice.
- ↑ Germany continues to rely on renewable raw materials. ( Page no longer available , search in web archives ) Info: The link was automatically marked as defective. Please check the link according to the instructions and then remove this notice. Fachagentur Nachwachsende Rohstoffe e. V.
- ↑ Monitoring of the effect of the EEG on the development of electricity generation from biomass (BMU, 2007). Biogas Association (2007)
- ↑ Inventory development of biogas plants in Germany ( Memento from September 2, 2010 in the Internet Archive )
- ↑ Biogas plants replace two nuclear power plants. ( Memento of May 27, 2012 in the Internet Archive ) In: agrarheute.com , May 25, 2012. Retrieved on May 25, 2012.
- ↑ Fachverband Biogas e. V. Industry figures ( Memento from December 20, 2013 in the Internet Archive ) (PDF)
- ↑ Renewable Energy Sources Act (EEG 2009)
- ↑ Thurgauer Zeitung - New boost for the biogas industry (PDF; 263 kB).
- ↑ Biogas Journal - Biowaste still offers potential for biogas (PDF; 1.6 MB).
- ↑ Biogas Journal - Energy resource for municipal bio-waste (PDF; 989 kB).
- ↑ Yves Demuth: Is the plastic cover really necessary for cucumbers? In: observer.ch . April 25, 2019, accessed May 11, 2019 .
- ↑ Deflagration in the biogas plant. In: ka-news.de , June 15, 2007.
- ↑ Biogas plant explodes. In: Spiegel online , December 16, 2007
- ↑ Disaster in the biogas plant: Expertise gives operators hope. ( Memento from September 17, 2008 in the Internet Archive ) In: Schwäbische Zeitung , August 26, 2008.
- ↑ Sparks of sweat kindle fire. In: NWZ online , September 24, 2008, accessed January 20, 2019.
- ↑ Biogas heats the mind. In: NWZ online , September 24, 2008. ( Page no longer available , search in web archives )
- ↑ a b c Federal states criticize expensive biogas boom. In: Spiegel online , December 11, 2010
- ↑ Nutrition worldwide: responsible - sustainable - safe! ( Memento from September 15, 2014 in the Internet Archive ), A summary by Uwe Möller, Club of Rome, PDF, 7 pages
- ↑ Johannes Bachmaier, Andreas Gronauer: Climate balance of biogas electricity: Climate balance of the energetic use of biogas from farm manure and renewable raw materials . Bavarian State Institute for Agriculture, 2007, OCLC 214385061 .