Cooling tower


A cooling tower (also known as a recooling plant ) is a system that uses a heat exchanger to remove excess or technically no longer usable heat from power plant or industrial processes.
Designs
Natural draft cooling tower
Modern natural draft cooling towers are mostly built as shell structures made of concrete and are basically in the form of rotational hyperboloids , first executed in the Netherlands by Frederik van Iterson (1915). In this case, however, this geometric shape is only implemented up to about a quarter of the upper half of the hyperboloid, the upper edge therefore has a significantly smaller diameter than the lower edge. This shape is a ruled surface that can be easily built with crossed straight steel beams , which reduces construction costs compared to other shapes. The shell is stiffened by the upper and lower ring.
Such cooling towers are now being erected at heights of up to 200 m from the top of the site ( Niederaußem power plant ) and have a minimum wall thickness of 16 cm in accordance with the old regulations. Due to the amendment of the standard generation DIN 1045 (structures made of concrete , reinforced concrete , etc.) and DIN 1055 (load assumptions) in 2005, minimum wall thicknesses of 18 cm are now required.
Despite the sometimes enormous dimensions, cooling towers made of reinforced concrete are comparatively filigree concrete structures. With a construction height of 200 m, the cooling tower in Niederaussem has a wall thickness of less than 30 cm. If you compare the proportions, the wall thickness is only about a fifth as thick as that of a hen's egg. For this reason, a cooling tower is usually given a sophisticated surface protection. This is particularly necessary when the concrete is exposed to chemical loads through the introduction of smoke gas. Alternatively, special concrete formulations are used during construction, which should give the cooling tower the necessary resistance to chemical loads over the long term, so that no special surface protection has to be applied.
But even with conventional cooling towers, there are considerable loads, for example from algae growth . The biogenic by-products of algae attack the concrete. When the algae die, they shrink and tear open the concrete surface due to their intensive adhesion.
Natural draft cooling tower with combined use as a chimney (clean gas discharge)

The task of a classic cooling tower is solely to give off thermal energy. It's a purely physical process. The cooling tower does not take on the function of a chimney , which is necessary in technical combustion processes.
In some coal-fired power plants built in recent years that have to be equipped with flue gas cleaning systems, the cooling tower also takes on the function of the chimney. With this method, the flue gas is led into the center of the cooling tower at about a third of the cooling tower height (above the irrigation level) and released into the steam plumes there.
The advantage of this technology, which was first used in Germany in 1982 in the Völklingen model power plant (clean gas discharge), is that the heated and humid exhaust air from the cooling tower offers significantly more buoyancy than the flue gas. This means that the exhaust plume can be distributed with a lower overall height than with a “conventional” chimney. This is particularly advantageous in coal-fired power plants, because the exhaust gases after being washed wet in the flue gas desulphurisation system (FGD) are greatly cooled and only have a low level of buoyancy.
The disadvantages of this technology are, among other things, the disproportionately large dimensions of the combined cooling tower; the minimum height achieved is 100 m ( Völklingen model power plant, built in 1982 ), but in recent years only towers between 155 m and 200 m high have been built in order to achieve a higher cooling capacity. Especially in the case of adjacent residential developments, such as in the cities of Datteln and Duisburg-Walsum , the new blocks with the combined cooling towers for smoke evacuation were built as a new block on existing systems. In some of these old locations there was no cooling tower before, as the heat was dissipated differently (for example via water); the flue gas was discharged through conventional chimneys. Now, at these locations, the tower and the steam plumes generated during operation have undesirable effects on the microclimate , for example locally increased amounts of precipitation and extensive shading.
In order to avoid these disadvantages, planning changes were made after public protests. At the coal-fired power station Moorburg in Hamburg , for example, the original planning of a natural draft cooling tower with combined use as a chimney was changed. The implemented planning includes a low hybrid cooling tower (height 65 m). Due to the complex flue gas cleaning, a very high chimney can be dispensed with. The new conventional chimney has a height of 130 m.
Tower height | Power plants with cooling towers as chimneys | fuel |
---|---|---|
100 m | Völklingen / Fenne power plant (HKV & MKV blocks) | Hard coal |
110 m | Frimmersdorf power plant (Block Q) | Brown coal |
120 m | Jänschwalde power plant (Blocks A – F) | Brown coal |
128 m | Niederaussem power plant (units G & H) | Brown coal |
135 m | Quiersche / Weiher power plant (Weiher III block) | Hard coal |
141 m | Black Pump Power Plant (Units A & B) | Brown coal |
141 m | Staudinger power plant (block 5) | Hard coal |
141.5 m | Rostock power plant (monoblock power plant) | Hard coal |
155 m | Boxberg power plant (Block R) | Brown coal |
160 m | Lünen power plant (Lünen-Stummhafen block) | Hard coal |
165 m | Westphalia power plant (blocks D & E) | Hard coal |
172 m | Neurath power plant (Blocks F & G) | Brown coal |
174.5 m | Lippendorf power plant (R & S blocks) | Brown coal |
180 m | Datteln power plant (block 4) | Hard coal |
181 m | Duisburg-Walsum power plant (Block 10) | Hard coal |
200 m | Niederaussem power plant (Block K) | Brown coal |
Fan cooling tower
Fan cooling tower at the Peine steelworks
Fan cooling tower Dresden power plant
Hamm-Uentrop combined cycle power plant : fan cooling towers combined as blocks
Fan cooling towers (height 34-100 meters) are not as high as natural draft cooling towers (height up to 200 m) because the air draft is generated with fans. Cell coolers are also fan cooling towers, but they are significantly lower and more compact.
The fan-assisted round cooling towers (partial natural draft) combine the advantages of natural draft cooling towers (no power consumption due to complete natural draft) with those of cell coolers (better cooling characteristics in summer and better operational flexibility) and are used when the construction height is limited by proximity to residential buildings or to protect the landscape is.
Fan-assisted cooling towers are used for both industrial and power plant applications for cooling water circuits between 25,000 and 200,000 m³ / h.
This cooling tower variant can also be built in built-up areas because, in contrast to the much higher natural draft cooling towers, there is no oppressive appearance and no massive shading.
Advantages over natural draft cooling towers | Advantages over cell cooling towers | Disadvantages compared to natural draft cooling towers |
---|---|---|
compact design with low height without any visually obtrusive effect | Electricity savings through partial use of the natural chimney effect | Electricity demand |
less space required | in the event of a power failure, partial cooling by natural draft | |
better cooling characteristics in summer | no hot air recirculation | |
greater operational flexibility | higher vapor discharge |
Hybrid cooling tower

Hybrid cooling tower in the landscape: Neckarwestheim nuclear power plant
Hybrid cooling towers (height 42–65 meters) are not as high as natural draft cooling towers (height up to 200 m) because the air draft is generated by fans, as in fan cooling towers. In addition, a heat exchanger package (dry section) is installed in hybrid cooling towers that fan cooling towers do not have.
During normal operation, the warm cooling water trickles into the wet section (lower level) of the hybrid cooling tower. The upper level of the hybrid cooling tower, the dry section, is used exclusively for steam drying and only contributes a small part to the total cooling capacity of the cooling tower. Cold air is sucked in from outside via the fans in the dry area and heated by passing it past the heat exchanger packages (which are fed with warm cooling water). The introduction of this heated air into the saturated cooling tower swath causes a shift in the saturation point , which leads to a complete dissolution of the visible cooling tower swath. Hybrid cooling towers are mainly used where low construction heights and little shading are required, mostly in the vicinity of residential buildings. The introduction of flue gas into hybrid cooling towers is unusual.
Tower height | Power plants with hybrid cooling tower | fuel |
---|---|---|
42 m | Altbach / Deizisau power plant (two towers) | Hard coal |
56 m | Neckarwestheim nuclear power plant | uranium |
65 m | Moorburg power plant | Hard coal |
80 m | Rheinhafen steam power plant in Karlsruhe | Hard coal |
Types of cooling
Wet cooling with natural draft wet cooling towers is the most common type of cooling because the degree of efficiency is highest due to the evaporation cold of the water as a cooling medium. Hybrid cooling, which, in contrast to wet cooling, is less efficient but does not produce any visible vapor plumes, is much rarer. Dry cooling uses air as a cooling medium and is only used under special ambient conditions - such as low average temperature, lack of water or a low cooling requirement in power plants that dissipate waste heat as district heating (e.g. Berlin-Mitte thermal power station ). With dry cooling, the spread of germs (e.g. Legionella ) due to the lack of vapor plumes is excluded in contrast to wet cooling, but dry cooling has the lowest efficiency of all types of cooling.
Wet cooling
Natural draft wet cooling

In natural draft cooling towers, the water to be cooled is sprayed into the air and trickled over fillers . This removes heat of evaporation and humidifies the air. If ten grams of one kilogram of water evaporate, the temperature of the water drops by six Kelvin. In addition, the water is cooled by the finely divided contact with the air by convection and the air is heated. The warming of the air leads to a decrease in density and thus an increase in the buoyancy of the air. Above the cooling tower, the mixture becomes visible as vapor clouds. Around 1.5 to 2.5% of the circulating cooling water evaporates and has to be replenished. Another replacement of the cooling water by the drainage (blowdown water) is necessary to prevent the salts dissolved in the water from concentrating (accumulating) too much. Lime deposits are the main problem here; When operating a thermal power plant with 3 GW of thermal power, about ten tons of lime can be produced per day. B. must be removed from the water cycle by dissolving with formic acid. This type of construction is primarily used in steam power plants. The deepest area of a wet cooling tower, in which the sprayed cooling water collects, is called the cooling tower cup .
Natural draft wet cooling towers (NNKT) have a very high power density due to the use of evaporation . They consume water. The water consumption is reduced by a layer of droplet separators above the water distribution . NNKT can be recognized by the fact that they create "clouds of fog" that are visible from afar, especially in cooler weather. A side effect is the introduction of water vapor into the atmosphere, which can locally ( microclimate / mesoclimate ) cause the formation of fog or precipitation. Because of this, industrial snow can often be seen in the area of cooling towers in winter . Bacteria (e.g. legionella ) can multiply at certain temperatures in the water cycle . Through the evaporation, the cooling water can theoretically be cooled down to the wet-bulb temperature , which in dry weather is significantly below the air temperature.
Forced ventilation wet cooling (fan cooling towers)
With forced-ventilation wet cooling, as with natural draft wet cooling, the water to be cooled is sprayed into the air and trickled over fillers. This removes the heat of evaporation from the water and humidifies the air.
In contrast to natural draft wet cooling, the air draft required for cooling is generated by fans, which means that the cooling towers or cell coolers can be built significantly lower and more compact. A distinction is made between suction fans (installed in the upper area of the fan cooling towers) and pushing fans (installed on the lower side edges).
Dry cooling


In dry cooling towers, the water does not come into direct contact with the atmosphere. With them, the cooling water flows in pipes equipped with cooling fins . The ambient air flows past the cooling fins, is heated, rises by convection and thus transports the transferred heat away. Large fans can support convection.
Dry cooling towers are used at power plant locations where water for wet cooling is not available or where it would be too expensive to procure. Because of their relatively high cost, they were rarely used in thermal power plants until 1985.
There are two different methods of dry cooling:
Direct dry cooling
There is only one cycle: the exhaust steam from the turbine is fed directly into the dry cooling tower, where it is condensed back into water, whereby the cooling tower also serves as a condenser in this process. The term air condenser (Luko) is common for this type of cooling tower .
Example:
Two coal-fired power plants at the Wyodak site in the US state of Wyoming :
At the Wyodak site, temperatures are extremely low in winter, so there is a risk of wet cooling towers freezing. Pure dry cooling only takes place in the cold season. At higher outside temperatures, cooling is supported by cooling ponds. If the outside temperature is high in summer, water is also evaporated in cell coolers.
- Wyodak II coal-fired power plant consisting of two power plant blocks, commissioning: 1979
- Wygen II coal-fired power plant, commissioning: 2003
Wyodak II: In order to cope with the extremely cold weather conditions at the Wyodak site, a dry cooler consisting of 69 cell coolers was built for the main power plant block. The system includes two 11 × 3 arrangements in V-shape (butterfly wing design). Power station unit 2 received three prototype cells (single-row tube bundles). When it was commissioned, the system was the largest dry cooling tower in the world and the first with a single-row tube bundle. To support the cooling capacity in summer, the system has two cooling ponds.
Wygen II: 2 × (2 single-row tube bundles). To support the cooling capacity in summer, the system has a cooling pond. The power plant has a water consumption of 7% compared to conventional wet cooling per year.
Indirect dry cooling
There are two circuits: The exhaust steam from the generator turbine is recondensed in a condenser in the heating circuit. The excess heat is transferred in the condenser to a second circuit, the water circuit. The dry cooling tower is located in this second water circuit for cooling the condenser. There are two different types of capacitors:
- Type 1: Injection Capacitors
- Type 2: surface capacitors
Example for type 1: Ibbenbüren power station, Block A , which was operated from 1967 to 1987.
The design air inlet temperature is 1.5 ° C because the turbines were designed for wet cooling processes.
Example of type 2: THTR-300 nuclear power plant , which was operated from 1983 to 1989.
The design air inlet temperature is 12 ° C. The design of the tower was oversized in order to achieve the same level of condensation as with wet cooling.
The largest cooling towers for indirect dry cooling are in the Kendal power plant in South Africa. It is also the largest power plant to use this technology. The plant has an installed capacity of 4,116 MW, the cooling towers have a diameter of 165 m at the base and are also 165 m high.
Hybrid cooling (combined wet and dry cooling)
Hybrid cooling combines the technical and physical advantages of dry cooling and wet cooling (high cooling capacity, better efficiency) with significantly reduced water consumption. Since water also evaporates with hybrid cooling, it should be assigned to wet cooling rather than dry cooling. It is sometimes mistakenly assigned to dry cooling. Because of their special nature as a mix of dry and wet cooling, they should be listed as a separate class. Compared to wet cooling, however, it is less efficient because of the power required for the fans required. In addition, the investments for hybrid cooling with the same performance as wet cooling are much higher.
Hybrid cooling is therefore often built in systems or power plants , where there may be complaints from residents, lack of acceptance or planning, traffic and approval problems due to swaths and industrial snow.
Hybrid cooling tower
Hybrid cooling systems can be built in a tower design. Either such a hybrid cooling tower has fans in the lower area and presses the ambient air into the cooling water curtain inside, or the cooling tower has the fan in the upper area and sucks in the air through the so-called air inlet in the lower area of the cooling tower.
In the case of the hybrid cooling tower, a warm air flow generated in heat exchangers and fans is added to the steam before it leaves the cooling tower . As a result, the air remains undersaturated and is not visible when leaving the cooling tower, so there are hardly any visible vapor plumes. Hybrid cooling towers are built from concrete, wood , GRP or steel.
Cell cooler (hybrid version with wet and dry level)
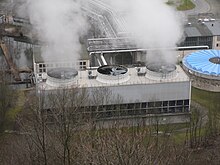
A cell cooler is a very compact fan cooling tower made of wood, GRP, steel or concrete, in which the cooling water heated by processes is re-cooled. A cell cooler is thus a forced-ventilated cooling tower (either sucking in air by fans or pushing air from the underside) in which the water to be cooled is distributed over trickle bodies by spray heads connected to the water distribution pipes.
With a suction design, there is a diffuser with a fan on the top of the cell cooler, which is driven by an electric motor and a gearbox. With a pushing construction, the fans are arranged in the lower third on the sides of the structure.
These fans generate an air flow in the cell cooler. Cool air enters through the air inlet in the lower area of the cell cooler and is sucked or pushed upwards through the trickle bodies, where the heated, saturated air is then pushed out or sucked out again through the diffuser on the top. A layer of droplet separators ( demisters ) directly above the water distribution system reduces water losses. This means that large drops of water are not carried outside.
Cell coolers can be built as wet coolers or as hybrid coolers. In the case of the hybrid cooler version, a second level with fans must be available, which mixes the steam with a warm air flow generated in heat exchangers before it leaves the system. As a result, the air remains undersaturated and there are no or barely visible vapor clouds.
A cell cooler can be equipped with soundproofing elements in the air inlet and outlet to reduce noise emissions. Several cell coolers are usually connected in parallel to increase the cooling capacity, resulting in a rectangular overall structure.
Example : The currently largest solar thermal power plant in the world, Andasol 1–3. Each power plant block has a nominal output of 50 MW and a water consumption of 870,000 m³ per year.
Dry cooling tower in combination with a cooling pond
Dry cooling towers can also be used in combination with cooling ponds in particularly hot places . This method offers the advantage that the water in the cooling circuit can be conducted in a closed circuit. The heat from the cooling circuit is transferred to a cooling pond, the evaporative cooling of which cools the cooling circuit back. Since the cooling effect occurs through the evaporation of water from the cooling pond, this process is also part of hybrid cooling and not dry cooling.
Example : El dorado energy gas power plant 27 km southwest of Boulder City, Nevada, 40 km southwest of Lake Mead (Hoover Dam), 40 miles southeast of Las Vegas. This gas power plant is used as a medium and peak load power plant. One of the main tasks is to offset the peaks in electricity demand in Las Vegas that the Hoover Dam power plant cannot meet.
Geographical data | |
---|---|
Location | Boulder City, Nevada |
Coordinates | 35 ° 47 '18.1 " N , 114 ° 59' 37.9" W. |
Height above sea level | 765 m |
power plant | |
Power plant name | El Dorado Energy |
Installation | 2000 |
Electrical power | 480 MW |
Cooling tower | |
design type | Cell cooler dry cooling tower in combination with cooling ponds |
Cooling tower manufacturer | GEA Power Cooling, Inc. |
Cooling ponds | 3 |
Cooling pond area | 3 × (200 m × 150 m) = 90,000 m² |
Water consumption per year | ? |
Application in industrial processes
Application in the thermal power plant process to generate electricity
Thermal power plants generate heat using various processes:
- Combustion of fossil fuels such as coal, gas, oil, peat
- Thermal energy from nuclear fission processes in nuclear power plants
- Heat from solar or geothermal energy
According to the laws of thermodynamics , thermal energy can only be converted into another form of energy if there is a temperature difference . In addition to a heat source, a heat sink is also required. This heat sink can be provided by a cooling tower.
A steam generator is required to generate electricity from heat . The steam drives a turbine , which in turn drives a generator that generates the electricity. The exhaust steam from the generator turbine must be recondensed with the aid of a condenser . This creates a pressure difference between the hot and cold side, which sets the steam in motion and enables a turbine to be driven in the first place. Considerable amounts of cooling water are required to condense the steam . In a large thermal power plant, up to 100,000 m³ of water per hour can pass through the system components and the cooling tower.
In a power plant there are usually two separate water circuits.
- Steam process: The water is heated and evaporated in a steam boiler. The turbine extracts the flow energy from the steam and makes it available as mechanical energy, which then drives the generator. During the expansion in the steam turbine, the steam is already condensed up to 15% (temperatures around 36 ° C). The remaining steam is then deposited in the condenser. The liquid water is brought to the pressure level in an energetically favorable manner by the feed pumps.
- Cooling circuit: In the second water circuit, the so-called cooling circuit, the thermal energy is removed from the condenser and, if necessary, the water is cooled in a cooling tower.
The reasons for operating a cooling tower are, on the one hand, the requirement to provide the coldest possible end (heat sink) of the steam cycle in the thermal power plant and, on the other hand, to be independent of a nearby running water or other heat consumer. A cooling tower is also necessary if, for environmental reasons, the cooling water may only be released into the flowing water at a limited temperature.
In the case of thermal power plants, the focus is usually on generating electrical power. For physical reasons, the heat generated can only be partially converted into electricity. There is always a remainder of heat that is usually not directly usable. One then speaks of waste heat , which is primarily converted in the cooling tower. In the case of heat-controlled power plants with a focus on heating energy production, the term combined heat and power plant or district heating plant is used.
Cooling water consumption in various power generation processes
power plant | Type | Water volume m³ / year |
Amount of electricity MWh / year |
Water consumption m³ / MWh |
Literature value gallons / MWh |
---|---|---|---|---|---|
Nuclear power plants | Nuclear power | 1.893-4.164 | 500-1100 | ||
Parabolic trough solar thermal power plants | Solar thermal | 2.877-3.483 | 760-920 | ||
Andasol | Solar thermal | 870,000 | 180,000 | 4.833 | 1277 |
Nevada Solar One | Solar thermal | 493.393 | 135.050 | 3.653 | 965 |
Coal power plants | coal | 0.416-1.136 | 110-300 | ||
Gas power plants (combined cycle) | gas | 0.757 | 200 |
Use outside a power plant
Cooling towers are not only found in power plants, but are also used in other systems, for example water cooling in the chemical industry, general cooling in industry and cooling of shopping centers, sports halls, etc.
The cooling towers or recooling plants of these systems are considerably smaller because of the mostly lower amounts of heat ( waste heat ).
Necessary data for planning cooling towers
Cooling towers are designed according to various DIN and ISO standards, depending on the cooling method . Some basic data on the power plant and cooling tower must be taken into account. In addition, various EC directives must be observed. The Machinery Directive has been binding since the end of December 2009 . The following is a non-exhaustive list of the most important parameters:
Power plant :
- Power plant location
- Air pressure (ISO standard: altitude)
- Ambient temperature (ISO standard: 15 ° C)
- relative humidity (ISO standard: 60% relative humidity)
- Power plant output
- Water temperature in the heating circuit
- Water pressure in the heating circuit
- Steam pressure in the heating circuit behind the condenser
Cooling tower:
- Inlet water temperature in the cooling circuit
- Water outlet temperature in the cooling circuit
- Type of cooling tower
- Air inlet temperature into the cooling tower
- Air outlet temperature from the cooling tower
- Water circulation
- Water consumption
Possible uses of waste heat from industrial processes as an alternative to cooling towers

In power plants for generating electricity, the condenser transfers a relatively low temperature to the cooling circuit of the cooling tower due to the process. This low temperature waste heat can no longer be used technically, but should be reduced even further to increase the efficiency of the thermal cycle. A cooling tower can take on this task if it dissipates the existing process heat that can no longer be used to generate electricity to the environment. If required, this condensation heat (e.g. in a district heating network or heat storage system) could also be dissipated at a higher temperature.
This heat extraction reduces the electrical efficiency and thus the electrically usable output of the power plant, since a smaller part of the thermal energy can now be used directly to generate electricity. However, more energy from the fuel used is used for two processes (electricity production and district heating production). Thus, the fuel efficiency is improved. The combined electricity and heat utilization process in power plants is known as combined heat and power .
A distinction is made between electricity-based and heat-based design of CHP systems, depending on the priority assigned to one of the two forms of energy. Current-controlled systems optimize the electricity yield, heat-controlled systems optimize the heat yield. The highest degree of utilization is achieved with a heat-controlled design, because this results in the lowest energy losses. The heat storage can be accomplished by using a district heating storage. The heat generated is used as warm water, so-called district heating, or water vapor via insulated pipes for heating buildings, for industrial purposes (process heat) or in food production (e.g. aquaculture). By using large heat accumulators, the (always simultaneous) production of heat and electricity in the CHP process can be temporally decoupled again, since the heat can be temporarily stored. In this way, a CHP plant can be operated with electricity and still ensure the heat supply of a heat-controlled operation. In times of high electricity and low heat demand, the system can be operated at full load and the excess heat can be loaded into the storage tank. In times of low demand for electricity but high heat demand, the CHP system can be operated at partial load, the remaining heat can then be temporarily provided by the heat storage system.
Since the combination of CHP systems and large heat storage systems leads to a high degree of flexibility with efficient fuel use, the Federal Government has included the promotion of heat storage systems in the last amendment to the Combined Heat and Power Act.
District heating
In the multi-stage turbines of the power plants, the water vapor is usually expanded right up to the beginning of condensation ; if district heating is decoupled, this process must be interrupted beforehand, which means a loss of up to 25% of the electrical output. A primary circuit temperature of 130–150 ° C is necessary to operate a district heating network due to the large number of heat exchangers and the temperature gradients required there. In summer, the cooling capacity (for cooling water in power plant operation) of a district heating network drops sharply due to the lower heating requirements of external district heating users, so that investments must still be made in (sometimes smaller) cooling towers or heat storage systems. That is why we are looking for ways to use the remaining energy in summer. District cooling is a sensible area of application.
District cooling
When using or producing district cooling , hot water is supplied to the external customer, as is the case with district heating, in winter, which generates cold on site with the help of absorption chillers . This method is currently used for facilities with high cooling requirements, for example hospitals or shopping centers. In Chemnitz there is a central cold storage facility that supplies the city's facilities.
Chemnitz (then Karl-Marx-Stadt) has been the second German city to have a district cooling network since 1973 . The approximately four-kilometer-long network operated by Stadtwerke Chemnitz supplies the technical university , opera house , town hall , district court and several large shopping centers. By using absorption chillers, it is possible to largely do without chillers driven by electrical energy (compression chillers).
In Vienna, the first cooling center for district cooling in Spittelau went online in 2009, which supplies the General Hospital of the City of Vienna and various office buildings with district cooling. In the meantime, there are also other cooling centers from Wien Energie throughout the city, and in 2014 the central station district cooling system went into operation. With an output of 20 megawatts in the final stage, this cooling center is one of the largest district cooling projects in Europe. 65 megawatts (as of 2014) of district cooling capacity are in operation throughout the city. Without the use of district cooling, a large part of the energy would be released unused to the environment via cooling towers in summer.
The combination of joint electricity and heat generation (as well as district cooling by converting the heating energy) is known as combined heat and power . This system can only be operated in a decentralized manner with maximum efficiency in order to minimize line losses. Short distances for heat transport are therefore a prerequisite. With the increasing price of fuels and increased environmental protection requirements, combined heat and power will continue to gain in importance.
Absorption chiller with 1.4 MW cooling capacity on a transporter
hazards
Fire hazards
As soon as a natural draft cooling tower is out of operation, it can pose a considerable fire hazard due to the very light trickle installations (polypropylene, polyvinyl chloride, asbestos cement, wood) and the chimney effect . On May 12, 2003, a natural draft cooling tower burned down in the decommissioned Schwandorf power plant while preparations were being made to demolish it , after no fire protection measures had been taken inside . 108 tons of built-in parts made of polypropylene burned down within 45 minutes ; after a further 50 minutes, 60 tons of wooden built-in parts were also burned. The fire brigade called early could not extinguish the fire in time due to the risk of collapse. Tests by the VGB have shown that a fire in a natural draft cooling tower cannot be extinguished and always results in total loss.
Health risks from contamination of the environment

In the case of cooling towers and recooling plants that work with open water circuits (wet cooling), there is a risk of germs and germs spreading as bioaerosol . Contaminated cooling towers can cause infections with Legionella pneumophila within a radius of more than 10 km .
The problem can be avoided by using dry cooling towers, but dry cooling is less efficient than wet cooling. Thus, for the same cooling capacity with dry cooling, either more electrical energy is required for operation (with fan dry cooling towers) or the towers require more interior space (natural draft dry cooling towers).
Another possibility to limit the contamination of cooling towers is the use of special metal-mineral catalysts. These are able to at least inhibit and slow down the growth of a biofilm and thus reduce the risks from contamination of the cooling towers.
Natural draft cooling towers (wet cooling) with a thermal output of up to 200 MW are subject to the VDI 2047 guideline series "Hygiene in recooling plants." The voluntary limit value for Legionella in Germany is 1,000 CFU / 100 mL.
Examples of Legionella - contaminated cooling systems:
- European epidemics: Murcia, Spain (2001, ventilation system with a cooling tower); Barrow-in-Furness, England (2003, cooling tower); Lens, France (2004, cooling tower) and Geneva, Switzerland (2001, likely cooling tower).
- January 2010 in Ulm, was due to a test operation of a new recooling plant for cooling systems
- In the summer of 2012, over 20 people in Rhineland-Palatinate and Saarland were infected with Legionella.
- The outbreak of legionnaires in Warstein in 2013 is attributed to a recooling plant.
- The coal-fired power station Moorburg was shut down in trial operation in 2013 because Legionella with 2,300 cfu / 100 mL were detected in the cooling circuit.
- The 2014 legionella outbreak in Jülich led to Unit F of the coal-fired power plant in Weisweiler being shut down several times because an excessive number of legionella was detected in its cooling circuit. As a result, the inspection of all cooling towers in North Rhine-Westphalia was ordered and a legislative initiative was introduced through the Federal Council to regularly examine cooling systems for Legionella. The decontamination in Weisweiler proved difficult and dragged on over three months. Despite numerous measures, the peak was reached with 275,000 CFU and resulted in a two-week operating ban.
Use and design of the facade of cooling towers
Protection of the landscape through color design
To protect the landscape, there is the option of building the necessary cooling systems for power plants and industrial plants either particularly compact and low (cell cooler, fan cooling towers and hybrid cooling towers) or to make the systems less visible with the help of color design.
In recent years, cooling towers have often been coated in a light gray (light gray), but there are also attempts to achieve even better results with the help of different colors and patterns.
Art objects
In some cases, cooling towers are also used as canvas and art objects. The largest map in the world is located on the 26,000 m² outside of the cooling tower of the Meppen-Hüntel power plant (Emsland). The concept comes from the artist Christoph Rihs . Another example of the use of a cooling tower as an art object can be found in France. At the Cruas nuclear power plant , a painting was painted on the cooling tower. After the power plant was converted into an amusement park, the fan cooling tower of the former Kalkar nuclear power plant was designed in color with a mountain landscape on the outside and equipped with a chain carousel on the inside.
Political protest messages from environmental organizations
Overpainted protest message "Nuclear power harms the country!" (2001, with skull symbol ) on the hybrid cooling tower of the Neckarwestheim nuclear power plant
In particular, the cooling towers of nuclear power plants were used by environmental protection organizations as objects for protests in the past. In the dark, for example, images were projected onto them , or permanent messages were attached with color.
Others
At the listed Dobl transmitter from around 1940, southwest of Graz, there is a wooden cooling tower with an octagonal floor plan, about 7 m wide, tapering conically towards the top and about 20 m high. Around 2000 it was heavily populated with pigeons.
Doka Group has developed self-climbing cooling tower formwork for the production of hyperparabolic natural draft coolers with a daily reinforced concrete production cycle. An inclination of 22 ° from the vertical and a minimum of 70 m radius of curvature vertically are possible.
swell
- ↑ VGB guideline for structural design, calculation, construction and execution of cooling towers, edition 2005 .
- ↑ Völklingen / Fenne power plant at power-saar.steag-saarenergie.de .
- ↑ Power plant Moorburg technical details on vattenfall.de .
- ↑ http://www.atominfo.ru/news3/c0289.htm
- ^ Moorburg - The power plant technology. Retrieved March 11, 2013 . ( Flash is required to display information about the cooling tower).
- ↑ wet cooling towers . VDI reports 298, 1977, VDI-Verlag, Düsseldorf.
- ↑ Handbook series Energy, ed. by Thomas Bohn: Conception and construction of steam power plants . Technischer Verlag Resch, TÜV Rheinland, Graefelfing 1985, ISBN 3-87806-085-8 .
- ↑ Information from GEA about the Wyodak II power plant ( memento of the original from November 1, 2009 in the Internet Archive ) Info: The archive link has been inserted automatically and has not yet been checked. Please check the original and archive link according to the instructions and then remove this notice. .
- ↑ a b Introducing Wygen II , at www.blackhillscorp.com, accessed December 30, 2009.
- ↑ O. Scherf: Air-cooled condensation system for a 150 MW block of the Ibbenbüren power plant . BWK 20 (1968), No. 2, pp. 56-60.
- ↑ Cleve: Design problems and calculation bases of dry cooling towers . Seminar lecture, RWTH Aachen, Jan. 10, 1974.
- ↑ Kendal Power Station. In: www.eskom.co.za. Retrieved September 6, 2015 .
- ↑ U. Häuser: Investigations into the operating behavior of hybrid cooling towers . Dissertation at the TU Braunschweig, 1981.
- ↑ a b Information from GEA about the various power plants ( memento of the original from January 19, 2009 in the Internet Archive ) Info: The archive link was inserted automatically and has not yet been checked. Please check the original and archive link according to the instructions and then remove this notice. .
- ↑ - ( Memento of the original from March 23, 2010 in the Internet Archive ) Info: The archive link was inserted automatically and has not yet been checked. Please check the original and archive link according to the instructions and then remove this notice. .
- ↑ - ( Memento of the original from July 22nd, 2009 in the Internet Archive ) Info: The archive link was inserted automatically and has not yet been checked. Please check the original and archive link according to the instructions and then remove this notice.
- ↑ Information from GEA about the power plant in Boulder (Nevada) ( Memento of the original from January 17, 2012 in the Internet Archive ) Info: The archive link was inserted automatically and has not yet been checked. Please check the original and archive link according to the instructions and then remove this notice.
- ↑ - ( Memento of the original from February 20, 2009 in the Internet Archive ) Info: The archive link was inserted automatically and has not yet been checked. Please check the original and archive link according to the instructions and then remove this notice.
- ^ Archived copy ( Memento of December 30, 2010 in the Internet Archive ).
- ↑ [1]
- ↑ District cooling concept: cooling from the thermal power station . In: Spiegel Online. Retrieved November 3, 2008.
- ↑ Cold storage in Chemnitz .
- ↑ Wien Energie yearbook 2013 . Wien Energie GmbH, Vienna 2014.
- ↑ VGB PowerTech , trade journal: VGB Kraftwerkstechnik 06/2006.
- ↑ VDI 4250 sheet 1: 2014-08 Bioaerosols and biological agents; Environmental medical assessment of bioaerosol immissions; Effects of microbial air pollution on humans (bioaerosols and biological agents; Risk assessment of source-related ambient air measurements in the scope of environmental health; Effects of bioaerosol pollution on human health). Beuth Verlag, Berlin. P. 24.
- ↑ Federal Office of Public Health PDF ( Memento of the original dated November 7, 2017 in the Internet Archive ) Info: The archive link was inserted automatically and has not yet been checked. Please check the original and archive link according to the instructions and then remove this notice. - see module 15, p. 48
- ↑ http://www.vdi.de/index.php?id=44414 .
- ↑ a b Legionella paralyze Moorburg. klimaretter.info , September 4, 2013, accessed on October 12, 2014 .
- ↑ http://www.laborveritas.ch/php/bdata/files/filesDatei_bdataFileExtPDF/53_Legionellen_Bericht_BAG.pdf .
- ↑ - ( Memento of the original from October 6, 2014 in the Internet Archive ) Info: The archive link was inserted automatically and has not yet been checked. Please check the original and archive link according to the instructions and then remove this notice. .
- ↑ Other power plants checked. Die Welt , October 2, 2014, accessed October 5, 2014 .
- ↑ Source of outbreak still unclear. WDR , October 9, 2014, accessed October 11, 2014 .
- ↑ Weisweiler: Almost no more legionella. Aachener Zeitung , January 6, 2015, accessed on March 23, 2014 .
- ↑ Another legionella alarm at the Weisweiler power plant. WDR, December 3, 2014, accessed on March 23, 2015 .
- ↑ Trial series against Greenpeace people. Schwäbisches Tagblatt , February 22, 2012, accessed on March 23, 2015 .
- ↑ Taz: "Climate protests in Corona times". March 16, 2020, accessed on March 17, 2020 (German).
- ↑ Cooling tower formwork SK175 - the self-climbing formwork for cooling towers doka.com, accessed October 29, 2019.
Web links
- Animation of how a hybrid cooling tower works
- Hartlieb, Norbert (enpros consulting GmbH): Expertise on the comparison of different cooling options for the planned gas and steam turbine cogeneration plant in Klingenberg in the Lichtenberg district of Berlin (October 15, 2015, accessed October 2015)