Polystyrene
Structural formula | |||||||
---|---|---|---|---|---|---|---|
![]() |
|||||||
General | |||||||
Surname | Polystyrene | ||||||
other names |
|
||||||
CAS number | 9003-53-6 | ||||||
Monomer | Styrene | ||||||
Molecular formula of the repeating unit | C 8 H 8 | ||||||
Molar mass of the repeating unit | 104.15 g mol −1 | ||||||
Type of polymer | |||||||
Brief description | |||||||
properties | |||||||
Physical state |
firmly |
||||||
density |
1050 kg / m³ (solid) |
||||||
Glass temperature |
100 ° C |
||||||
Thermal conductivity |
0.17 W m −1 K −1 |
||||||
safety instructions | |||||||
|
|||||||
As far as possible and customary, SI units are used. Unless otherwise noted, the data given apply to standard conditions . |
Polystyrene ( abbreviation PS ) is a transparent, foamed white, amorphous or semi-crystalline thermoplastic . Amorphous polystyrene is a widely used, inexpensive ( standard ) plastic that is used in many areas of daily life.
Expanded polystyrene ( EPS , mainly known under the trade name Styrofoam ) and extruded polystyrene ( XPS ) are used as foams .
history
As early as 1839, the pharmacist Eduard Simon observed in Berlin that styrene thickened over several months into a gelatinous, viscous mass, which he called styrene oxide assuming oxidation . Six years later, John Buddle Blyth and August Wilhelm von Hofmann reported that the conversion takes place without adding or releasing any element and only takes place through the molecular change of the styrene, and renamed the styrene oxide to metastyrene . The term polystyrene was first used by Abraham Kronstein , who, however, understood it to be a gel-like intermediate product that was then to form the glass-like metastyrene with styrene .
In 1931, the industrial production of polystyrene began at the IG-Farben plant in Ludwigshafen am Rhein . The use as foam plastic ( Styrofoam ) was developed by Fritz Stastny and his boss Rudolf Gäth at BASF in 1949 , patented in 1950 and presented at the plastics fair in Düsseldorf in 1952. In the USA it was developed as Styrofoam by Ray McIntire at Dow Chemical Company (patent 1944).
PS types
The following table gives an overview of polystyrene homopolymers .
Abbreviations | Other abbreviations | |
---|---|---|
Standard polystyrene, normal polystyrene | Standard PS, Normal PS, GPPS | |
Polystyrene syndiotactic | PS-S, PS- (M) | sPS |
Polystyrene foam and foamable polystyrene | PS-E | EPS |
GPPS is derived from the English name General Purpose Polystyrene , EPS from Expanded Polystyrene .
This table gives an overview of the most important polystyrene copolymers :
Styrene-butadiene graft copolymers | SB |
---|---|
Styrene-butadiene block copolymers | SBS |
Styrene-acrylonitrile copolymers | SAN |
Acrylonitrile-butadiene-styrene copolymers | SECTION |
cross-linked polystyrene | PS-X |
Tacticity
In the case of polystyrene, tacticity describes the extent to which the phenyl group is aligned (arranged) uniformly in the polymer chain. The tacticity has a strong impact on the properties of the plastic. Standard polystyrene is atactic.
Manufacturing
Polystyrene is obtained by polymerizing styrene . A large number of polymers are made by chain polymerization , u. a. four of the five most important plastics in terms of quantity, namely polyethylene (PE), polypropylene (PP), polyvinyl chloride (PVC) and also polystyrene (PS). Styrene has exceptional polymerisation properties; it can be polymerised by free radicals , cationic , anionic or using Ziegler-Natta catalysts .
There are currently two processes of industrial importance for the production of styrene, the dehydrogenation of ethylbenzene and the SM / PO process. In 2012 the annual world production of styrene was about 20 million tons.
The finished plastic is sold as granulate in order to be processed as extrudable polystyrene (XPS) into plastic parts or containers (e.g. food packaging with aluminum heat-sealed lids). Expandable polystyrene (EPS) acquires gas inclusions during the polymerization to form solid spheres. The beads are transported to the processor. If the spheres are heated there under steam a little over 100 ° C, the gas expands and the thermoplastic material puffs up. The edges of the bubbles merge. The result is a shaped solid, depending on the shape, everything from simple plates to geometrically complex molded parts is possible.
properties
Physical Properties
Unmodified polystyrene has a low melting point, is hard and brittle and relatively permeable to oxygen and water vapor.
The density of compact polystyrene is between 1040 and 1090 kg / m³. Foamed polystyrene ( EPS or PS-E) has a density between 15 (insulation in construction) and 90 kg / m³ (ski helmet).
When expanded, polystyrene has a very low thermal conductivity. For gray insulation boards to which graphite is added (e.g. Neopor ), it is slightly lower at ≈0.032 W / ( mK ) than for white insulation boards (e.g. Styrofoam ) with 0.035 ... 0.040 W / ( m · K).
Mechanical properties
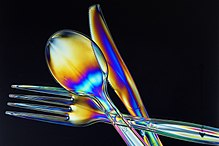
Solid amorphous polystyrene is crystal clear, hard and sensitive to impact. It creates a brittle, clattering, almost glass-like sound when knocked (butter dishes). When bent or broken, it smells clearly of styrene. Polystyrene can be colored in all colors. Solid polystyrene tends to form stress cracks . It is not very heat-resistant, aging accelerates from 55 ° C, which is why it can only be used up to 70 ° C. The glass transition temperature is, depending on the processing conditions, around 100 ° C, the melting temperature is 240 ° C for isotactic polystyrene and 270 ° C for syndiotactic polystyrene . Atactic polystyrene is an amorphous solid and has no melting temperature. Atactic polystyrene is an inexpensive plastic with a large market share, syndiotactic PS has so far only been used for special applications, isotactic PS is of no industrial interest due to its low crystallization rate.
Foamed polystyrene is white and opaque. Compared to solid polystyrene, it has lower mechanical strength, but higher elasticity.
Chemical properties
Polystyrene has good resistance to aqueous alkalis and mineral acids , but not to non-polar solvents such as gasoline and longer-chain ketones and aldehydes . It is UV sensitive.
Polystyrene can e.g. B. be dissolved with dichloromethane and welded almost seamlessly.
Even small amounts of solvents such as acetone , ethyl acetate or toluene are sufficient to "eat away" a relatively large volume of polystyrene foam by attacking the relatively low-mass foam structure and at the same time releasing the high-volume propellant gas enclosed in the foam.
Syndiotactic polystyrene crystallizes sufficiently quickly; it is used as a construction material in typical injection molding processes , especially because of its extreme resistance to chemicals, hot water and coolants. This makes it an alternative to established engineering plastics. It is made using metallocene catalysts.
Fire behavior
Polystyrene burns with a bright yellow, heavily sooting flame. The styrene released has a flowery-sweet odor; in practice, however, the vapors often have a pungent odor due to additives.
The fire behavior of expanded polystyrene is dominated by the fact that it softens at temperatures a little over 100 ° C and then drips off, whereby the drops (also due to their low mass and the associated poor heat dissipation) can catch fire and then drip off burning. Above about 300 ° C the material decomposes to styrene (flash point of about 31 ° C). If necessary, residues of the propellant pentane (flash point approx. −50 ° C) are released. This can lead to the polystyrene burning and dripping off by itself. Burning dripping polystyrene can cause fire to spread by igniting materials underneath.
The flammability of (expanded or extruded) polystyrene can be reduced by using suitable flame retardants . In the past, polybrominated diphenyl ethers or hexabromocyclododecane were often used as additives , the use of which is no longer permitted in the raw material, but can still be introduced into the end products through recyclate. Today a brominated styrene-butadiene copolymer is mostly used. These flame retardants split during combustion bromo -containing gases from, breaking thereby the entering in the combustion free radical chain reactions by scavenging oxygen , and thus inhibit the combustion; this can result in polybrominated dibenzodioxins and dibenzofurans .
The fire behavior of flame-retardant polystyrene rigid foam for construction applications is classified according to EN 13501-1 and classified in the European class for fire behavior E. When installed, the fire behavior depends on the specific structure of the insulation system. For information on the fire behavior of thermal insulation composite systems and controversies following media reports on facade fires, see thermal insulation composite system # Fire behavior .
Weather resistance
Polystyrene is resistant to the effects of water, but rots when exposed to UV radiation. Polystyrene embrittles relatively quickly when exposed to light and then tends to form stress cracks. The photo-oxidation of polystyrene occurs at wavelengths of = 253.7 nm, whereby the chromophoric groups absorb and numerous decomposition products ( hydroperoxides , hydroxyl and carbonyl compounds, aliphatic and aromatic ketones , peroxyesters , volatile compounds such as benzaldehyde and acetophenone ) are formed, radiation greater than 300 nm is not absorbed.
Effect on organisms and the environment
Polystyrene is physiologically harmless and unrestrictedly approved for food packaging.
However, as shown below, brominated flame retardant additives in packaging and their migration into food cannot be ruled out. There is also evidence that cell cultures can be negatively influenced by softening the material under culture conditions.
In countries with insufficient waste disposal, polystyrene can end up in the sea. There it accumulates in the debris of floating garbage in the oceans, through photolysis and the impact of the waves it breaks down into small crumbs that are ingested by animals (for more on this see garbage vortex ).
The flame retardant hexabromocyclododecane (HBCD), which was previously added to polystyrene for insulation boards and rigid foam boards , is classified as "very toxic to aquatic organisms with long-term effects" according to the CLP regulation . It is relatively difficult to degrade (persistent) and toxic to aquatic organisms with a very high bioaccumulation - and biomagnification spot potential. The migration in the environment of an undamaged foamed polystyrene is quantitatively low emissions can occur in case of fire, photolysis and recycling.
Biodegradation
In 2015, researchers at Stanford University discovered that mealworms are able to consume polystyrene and break it down into CO 2 and rotting feces . One hundred larvae consumed 34–39 mg daily. After the month-long experiment, no difference could be found between the health status of mealworms that ate polystyrene and those that ate conventional food . The digestive process has not yet been researched in detail.
Material pests
Woodpeckers and brown garden ants usually nest in rotten trees. However, polystyrene insulation panels are used by both as alternative living spaces. Woodpeckers destroy z. B. the plaster layer of a thermal insulation system ( woodpecker damage ) to create a breeding cave in it. Another material pest is the brown garden ant . The workers create paths and nests in polystyrene insulation panels in which to raise their brood. With their pincers, they break up the individual polystyrene balls into tiny, transportable parts and transport them to other cavities or outside, which also makes the pest infestation visible.
Copolymers
As a material, polystyrene homopolymer has an excellent profile of properties when transparency, surface quality and rigidity are required. Its range of uses is further expanded by copolymers and other modifications (blends e.g. with PC and syndiotactic polystyrene). The brittleness of common polystyrene is overcome by elastomer-modified styrene-butadiene copolymers. The copolymer made from styrene and acrylonitrile ( SAN ) is more resistant to thermal stress, heat and chemicals than the homopolymer and is also transparent. ABS has similar properties, can be used at low temperatures, but is opaque.
Styrene-butadiene copolymers
Styrene-butadiene copolymers can be made with a low proportion of butene . Either PS-I or SBC (see below) can be produced, both copolymers are impact-resistant . PS-I is made by graft copolymerization , SBC by anionic block copolymerization, which means it can be transparent .
If styrene-butadiene copolymer has a high proportion of butene, styrene-butadiene rubber (SBR) is formed.
The impact strength of the styrene-butadiene copolymers results from phase separation; polystyrene and polybutadiene are not soluble in one another (see Flory-Huggins theory ). A boundary layer is created by copolymerization without complete mixing. The butadiene components (the "rubber phase") combine to form particles that are embedded in a matrix made of polystyrene. The decisive factor for the improved impact strength of the styrene-butadiene copolymers is their higher capacity for deformation work. Without applied force, the rubber phase initially behaves like a filler . When subjected to tensile stress, crazes (micro-cracks) form, which spread to the rubber particles. The energy of the spreading crack is then transferred to the rubber particles lying on its way. Due to a large number of cracks, the originally rigid material contains a lamellar structure. The formation of each individual lamella contributes to the consumption of energy and thus to an increase in the elongation at break . PS homopolymers deform until they break when a force is applied. At this point, the styrene-butadiene copolymer does not break, but begins to flow, solidifies until it is tear-resistant and only breaks when it is much more elongated.
With a high proportion of polybutadiene, the effect of the two phases is reversed. Styrene-butadiene rubber behaves like an elastomer, but can be processed like a thermoplastic.
PS-I
PS-I (from english i mpact resistant p oly s tyrene ) consists of a continuous polystyrene matrix and a rubber phase dispersed therein. It is made by polymerizing styrene in the presence of polybutadiene dissolved (in styrene). The polymerization takes place simultaneously in two ways:
- Graft copolymerization : The growing polystyrene chain reacts with a double bond of the polybutadiene. As a result, several polystyrene chains are attached to a polybutadiene molecule.
- Homopolymerization: styrene polymerizes to polystyrene and does not react with the polybutadiene present.
The polybutadiene particles (rubber particles) in PS-I usually have a diameter of 0.5 - 9 μm. They scatter visible light , which makes PS-I opaque . The material is stable (no further segregation takes place) because polybutadiene and polystyrene are chemically linked . Historically, PS-I was initially created by simply mixing polybutadiene and polystyrene (the result is a polyblend , not a copolymer ). However, this material has significantly poorer properties.
Styrene-butadiene block copolymers
SBS ( S tyrol- B utadien- S Tyrol block copolymer) is prepared by anionic block copolymerization and consists of three blocks:
Ssßßßßßßßßß bbbbbbbbbbbbbbbbbbbb ßßßßßßßßßß
S stands for the styrene repeat unit , B for the butadiene repeat unit. Often, however, the middle block does not consist of such a butadiene homopolymer, but of a styrene-butadiene copolymer:
SSSSSSSSSSSSSSSSSSS BB S BB S B S BBBB S B SS BBB S B SSSSSSSSSSSSSSSSSSS S
By using a random copolymer at this point, the plastic becomes less susceptible to crosslinking and flows better in the melt.
In anionic copolymerization, styrene is first homopolymerized; an organometallic compound such as butyllithium serves as the catalyst . Only then is butadiene added, after which styrene is added again. The catalyst remains active all the time (for which the chemicals used must be of high purity). The molecular weight distribution of the polymers is very low (polydispersity in the range of 1.05, so the individual chains have very similar lengths). The length of the individual blocks can be specifically adjusted through the ratio of catalyst to monomer. The size of the rubber particles depends on the block length. Very small particles (smaller than the wavelength of light) ensure transparency. In contrast to PS-I, however, the block copolymer does not form particles, but has a lamellar structure.
Styrene-butadiene rubber
Styrene-butadiene rubber (SBR from English Styrene Butadiene Rubber ) is produced, like PS-I, by graft copolymerization, but with a lower styrene content. As a result, SBR consists of a rubber matrix with a polystyrene phase dispersed in it . Unlike PS-I and SBC, it is not a thermoplastic , but an elastomer .
The polystyrene phase aggregates into domains within the rubber phase. It thus creates a physical crosslinking on a microscopic level. When the material is heated above the glass transition point, the domains disintegrate, the crosslinking is temporarily removed and the material can be processed like a thermoplastic.
Product forms and use
Polystyrene is one of the standard plastics and takes fourth place in terms of production volume after polyethylene , polypropylene and polyvinyl chloride . In Germany, around 12.06 million tons of plastics (excluding adhesives , varnishes , resins , fibers ) were processed in 2015 , of which 655,000 tons (5.4 percent) were polystyrene and expanded polystyrene PS / PS-E.
Films and sheets are manufactured by extrusion .
The low tendency of polystyrene to shrink or shrink during production enables components that are very near net shape (see lost foam process ). Furthermore, very fine contours, edges and straight surfaces can also be produced for plastics. This property enables the production of components that are relatively precisely fitting. So z. B. tape cassettes and CD cases made of transparent polystyrene.
Polystyrene is approved for use as food packaging , for example as a yoghurt cup or foam tray, if certain requirements are met.
Injection molded parts made of unfoamed polystyrene are used in plastic model making .
In Electrical Engineering polystyrene is used because of its good insulating property. It is used to manufacture switches , bobbins and housings (High Impact Polystyrene, HIPS ) for electrical appliances. Polystyrene is used for mass-produced items (e.g. classic CD packaging, video cassettes ), in precision engineering and for inspection glasses.
Polystyrene is the main component of Napalm -B, which is used in incendiary bombs .
Polystyrene film
Transparent polystyrene film is used, among other things, for packaging purposes.
Stretched polystyrene film (trade names: Styroflex for the copolymer with butadiene, Trolitul) is used together with aluminum or tin foil to produce low-loss and tightly tolerated capacitors .
In infrared spectroscopy , polystyrene film is used as the wavelength standard. A card with a film that fits into the sample holder is enclosed with the device by the device manufacturer.
Foamed polystyrene
Propellants such as cyclopentane or carbon dioxide are added to the raw material , which cause the material, which is liquid under the action of heat, to foam.
Since foam polystyrene can be cut very well with a thermal saw and is also very inexpensive, it has established itself as a building material in model and scenery construction. The foamed material is used in model aircraft construction . Model builders as well as city and landscape planners use it for landscape elements because it can be edited very well.
Loose free-flowing polystyrene foam balls with a typical diameter of around 2–6 mm are used as filling for beanbags , vacuum mattresses in rescue services, in road construction , to loosen heavy soils in gardening and landscaping and sometimes as a means of buoyancy when lifting shipwrecks .
Polystyrene foam is also used in nuclear weapons , where it is used to maintain the cavity of the subcritical masses and for compression in fusion bombs .
Expanded polystyrene (EPS)
Styrofoam is generally known as a light, white packaging and insulating material . It is a rather large pores EPS rigid foam ( E xpandierter P oly s tyrol). For production, granules are filled into a mold and foamed in hot steam. The particles of the granulate stick together, but usually do not completely fuse. The spherical, foamed granules are often recognizable in the end product and can sometimes be separated individually. Depending on the manufacturing process, expanded polystyrene rigid foam is more or less permeable to air and water vapor.
EPS rigid foam boards can be cut from a block in almost any thickness.
Foamed polystyrene is widely used as packaging material and for protective helmets , solid life jackets and surfboards .
Styrofoam is originally a brand name of BASF . The IVH (Industrieverband Hartschaum e.V.) has been exercising the rights to the name Styropor since the 1990s . Only those manufacturers of EPS who submit to the special quality requirements of the IVH are allowed to name their material Styrofoam .
Other well-known trade names for EPS are Austrotherm , Steinopor , Sagex , Swisspor , Hungarocell (Hungary), Telgopor (Spanish-speaking countries) and Frigolit (Sweden).
In 2014, under the direction of the European Manufacturers of Expanded Polystyrene (EUMEPS), the common brand name airpop was introduced with the aim of minimizing the wide variety of names for EPS in Europe. In Germany, the IK Industrievereinigung Kunststoffverpackungen eV is responsible for implementing the European strategy in the field of EPS packaging.
Extruded Polystyrene (XPS)
Another method of making polystyrene foam is extrusion . The starting material made of polystyrene granulate and blowing agent is foamed by heat and at the same time continuously pushed out through a defined opening and cooled. In this case a homogeneous, feinporigerer arises XPS foam (E x trudierter P oly s Tyrol), which generally has a closed surface and a closed cell structure. It is classified as impervious to air, water and water vapor and only absorbs a small amount of water.
Trade names are e.g. B. Austrotherm XPS (color pink), Floormate , Jackodur (JACKON Insulation, color purple), Roofmate , Styrodur ( BASF , color green), Styrofoam (Dow Chemical, color blue) and URSA XPS (URSA Deutschland GmbH, color yellow).
In the construction sector
Foamed polystyrene is used as an insulating material for the thermal insulation of buildings. The construction industry is the largest consumer of EPS: In 2012, it accounted for more than 60% of global EPS sales, which are expected to increase to US $ 15 billion by 2020.
Due to its high compressive strength and low water absorption (closed porosity), XPS is used, for example, to insulate buildings from the ground ( perimeter insulation ). This material is used for shower elements at ground level and floor level because of its high compressive strength.
As of the end of 2014, buildings in Switzerland contained almost 500,000 tons of EPS and 200,000 tons of XPS as insulation. Rigid foam panels for the construction sector are specially equipped to meet the various requirements:
- Panels for footfall sound insulation should absorb and damp vibrations elastically.
- Panels that are used for thermal insulation must generally be flame-retardant . The lighter and finer-pored the panels, the higher their insulation value . Sheets with graphite offset ( gray EPS ) are offered under the trade name Neopor .
- Panels for perimeter insulation and for inverted roofs may only absorb small amounts of water so that the intended insulation value is maintained even in a damp environment.
For EPS insulation materials, the requirements of EN 13163 apply, for XPS insulation materials those of EN 13164. In Germany, facade insulation panels made of EPS rigid foam must also comply with the general building authority approval Z-33.4-… or Z-33.40-… of the manufacturer ; Quality guidelines and test provisions of the Federal Department of Quality Assurance EPS rigid foam (BFA QS EPS) must be met.
Recycling and disposal
In Germany, around 5 million tons of plastic waste were generated in 2016, of which 110,200 tons or 2.2% EPS and XPS waste. 33% of this was recycled, 65% used for energy recovery and 2% disposed of.
recycling
The following material recycling processes are currently available:
- Extrusion: After shredding and extrusion, the polystyrene waste is used for the recovery of polystyrene regranulate .
- Mechanical recycling: The EPS waste is ground in a mill and the resulting grist is dedusted. The EPS granulate is z. B. used for bound EPS fillings, EPS recycling panels, as a lightweight aggregate for concrete or for porosity of masonry bricks.
The biggest problems of EPS recycling are:
- EPS waste causes extremely high specific transport costs due to its very low bulk density of approx. 6.5 kg / m³.
- EPS is hardly recycled because of soiling and mixing. EPS recyclate can therefore only be processed in small quantities into polystyrene granulate and subsequently for high-quality injection molding applications. Part of the EPS waste is thermally recycled.
- Recycled foam containing flame retardants is currently being processed into other products. As a result, significant residual levels of brominated flame retardant additives cannot be ruled out even in sensitive applications (packaging, flower trays, etc.).
One solution is a collection and recycling process which comprises Freising he Fraunhofer Institute IVV helped develop. Polystyrene waste is already selectively dissolved in a solvent during collection (and its volume reduced to 1/50). Highly pure polystyrene can be recovered from the solution. The world's first solvent-based EPS recycling plant with an annual output of 600 tons went into operation in Montreal (Canada) in 2018. In Terneuzen (Netherlands), the PolyStyreneLoop cooperative is to build an EPS and XPS recycling plant based on the CreaSolv® process with an annual output of 3,000 tons.
Energy recovery
If not recycled, polystyrene waste is used to generate energy by incineration.
The city of Würzburg has investigated the co-incineration of HBCD-containing polystyrene foam waste together with municipal and commercial residual waste. It has been shown that the safe destruction of the flame retardant HBCD is guaranteed.
In Germany, HBCD-containing polystyrene insulation materials had to be disposed of as hazardous waste from October 1, 2016 following a change in the Waste Catalog Ordinance . This classification led to disposal bottlenecks as many waste incineration plants did not have the appropriate permit. In order to continue to enable disposal in these waste incineration plants, some federal states have issued decrees that polystyrene insulation materials containing HBCD are permitted up to a certain percentage in mixed construction waste. Following a further amendment to the Waste Catalog Ordinance, HBCD-containing polystyrene insulation materials are considered non-hazardous waste from December 28, 2016 and can be disposed of in waste incineration plants. On July 17, 2017, the POP Waste Monitoring Ordinance and an amendment to the Waste Catalog Ordinance were issued ( BGBl. I p. 2644 ). HBCD-containing polystyrene insulation materials can therefore continue to be disposed of in waste incineration plants, but they are subject to a separate collection requirement, a ban on mixing, and obligations to provide evidence and register. In Austria, EPS insulation materials containing HBCD are classified as non-hazardous waste (waste code number 57108 “Polystyrene, Polystyrene foam”). They may be incinerated in incineration plants for non-hazardous waste (waste incineration plants).
Landfill
In 2006, 870,000 tons of polystyrene plates and cups and 590,000 tons of other products were landfilled in the USA . Since polystyrene does not biodegrade in the absence of light, it remains in landfills.
Norms
- DIN 4102-1 Fire behavior of building materials and building components - Part 1: Building materials; Terms, requirements and tests .
- DIN 4102-20 Fire behavior of building materials and components - Part 20: Special evidence for the fire behavior of external wall cladding .
- DIN EN ISO 1622-1 Plastics - Polystyrene (PS) molding compounds - Part 1: Designation system and basis for specifications (ISO 1622-1: 2012); German version EN ISO 1622-1: 2012.
- DIN EN ISO 1622-2 Plastics - Polystyrene (PS) molding compounds - Part 2: Production of test specimens and determination of properties (ISO 1622-2: 1995); German version EN ISO 1622-2: 1999.
- DIN EN ISO 19063-1 Plastics - Impact -resistant polystyrene (PS-I) molding compounds - Part 1: Designation system and basis for specifications (ISO 19063-1: 2015); German version EN ISO 19063-1: 2015.
- DIN EN ISO 2897-2 Plastics - Impact -resistant polystyrene (PS-I) molding compounds - Part 2: Production of test specimens and determination of properties (ISO 2897-2: 2003); German version EN ISO 2897-2: 2003.
- EN 13163 Thermal insulation products for buildings - Factory made expanded polystyrene (EPS) products - Specification .
- EN 13164 Thermal insulation products for buildings - Factory made extruded polystyrene foam (XPS) products - Specification .
- EN 13501-1 Classification of building products and types of fire behavior - Part 1: Classification with the results from the tests on fire behavior of building products .
Other regulations
- BfR recommendations on materials for food contact - Polystyrene, which is obtained exclusively through the polymerization of styrene; As of September 1, 2017.
- BfR recommendations on materials for food contact - styrene mixed and graft polymers and mixtures of polystyrene with polymers; As of September 1, 2017.
literature
- Handbook of elastics and plastics. VEB Chemical Works Buna, 1967.
- Gerhard W. Becker, Dietrich Braun, Hermann Gausepohl, Roland Gellert: Polystyrene. Becker / Braun Kunststoffhandbuch 4, Hanser Verlag, 1995, ISBN 3-446-18004-4 .
Web links
- Industrieverband Hartschaum e. V.
- Infrared and Raman spectrum of polystyrene
- www.waermedaemmstoffe.com technical information on the insulation materials polystyrene (EPS and XPS)
- Material archive: Expanded polystyrene - Extensive material information and images
- Videos on material properties of polystyrene published by the Institute for Scientific Film . Provided in the AV portal of the technical information library .
- Stress corrosion cracking of PMMA and PS Youtube Video: Crazes at PS
- Polystyvert - EPS recycling plant in Montreal (Canada)
- PolyStyreneLoop - planned EPS and XPS recycling plant in Terneuzen (Netherlands)
Footnotes
- ↑ J. Kahovec, RB Fox, K. Hatada: Nomenclature of regular single-strand organic polymers (IUPAC Recommendations 2002) . In: Pure and Applied Chemistry . 74, No. 10, January 1, 2002. doi : 10.1351 / pac200274101921 .
- ↑ Entry on polystyrene. In: Römpp Online . Georg Thieme Verlag, accessed on August 4, 2019.
- ↑ a b c data sheet polystyrene (PS) from material database RIWETA 4.1, accessed on October 31, 2015.
- ↑ This substance has either not yet been classified with regard to its hazardousness or a reliable and citable source has not yet been found.
- ↑ Plastics the Facts 2014/2015 on plasticseurope.org. (PDF) Retrieved May 18, 2019 .
- ↑ a b About plastics - Polystyrene; In: Plasticseurope.org. Retrieved April 4, 2020 .
- ↑ E. Simon: About the liquid Storax (Styryx liquidus). In Liebigs Annalen der Chemie , Volume 31 (1839), p. 265, doi: 10.1002 / jlac.18390310306 ; cited in Kunststoff-Handbuch Volume V Polystyrol, p. 87 (1969).
- ^ J. Blyth, A. W. Hofmann: About styrene and some of its decomposition products. In Liebigs Annalen der Chemie, Volume 53 (1845), p. 289, doi: 10.1002 / jlac.18450530302 , cited in Kunststoff-Handbuch Volume V Polystyrol, p. 87 (1969).
- ↑ A. Kronstein: On the knowledge of the polymerization . In: Reports of the German Chemical Society . tape 35 , no. 4 , October 1, 1902, ISSN 1099-0682 , p. 4150-4153 , doi : 10.1002 / cber.19020350454 .
- ↑ A. Kronstein: On the knowledge of the polymerization . In: Reports of the German Chemical Society . tape 35 , no. 4 , October 1, 1902, ISSN 1099-0682 , p. 4153-4157 , doi : 10.1002 / cber.19020350455 .
- ↑ Patent US2681321 : Production of porous materials from film-forming organic thermoplastic masses. Inventors: Stastny Fritz, Gaeth Rudolf.
- ↑ according to DIN EN ISO 1043-1
- ↑ University of Bayreuth: script for the practical course macromolecular chemistry WS 06/07 , experiment: coordinative polymerisation.
- ^ JM Davies: Lightweight Sandwich Construction , Blackwell Wissenschafts-Verlag GmbH, Berlin, 2001, ISBN 0-632-04027-0 , p. 35.
- ↑ Bénédicte Mailhot, Jean-Luc Gardette: Polystyrene Photooxidation, 1. Identification of the IR-Absorbing Photoproducts Formed at Short and Long Wavelengths , in: Macromolecules , 1992 , 25 (16), pp. 4119-4126 ( doi: 10.1021 / ma00042a012 ).
- ↑ Recycling of EPS waste to re-expandable polystyrene
- ↑ Udo Knauf, Wolfgang Albrecht, Andreas Mäurer: EPS-Loop: Recycling of EPS waste to re-expandable polystyrene : final report; Project duration: August 1, 2003 - July 31, 2005, Fraunhofer Inst. Packaging, 2005.
- ↑ Max Müller: On the mass transfer of low-volatility additives in polymer coatings. Investigations with the aid of convocal micro-Raman spectroscopy . scientific Publishing, Karlsruhe 2012, ISBN 978-3-86644-997-8 ( limited preview in the Google book search).
- ^ Andrei P. Sommer, Mike Kh. Haddad, Hans-Joerg Fecht: It is Time for a Change: Petri Dishes Weaken Cells. In: Journal of Bionic Engineering. 9, 2012, pp. 353-357, doi: 10.1016 / S1672-6529 (11) 60125-X .
- ↑ Sto-Polystyrene insulation boards ( Memento from November 26, 2014 in the Internet Archive ) (PDF; 71 kB)
- ↑ Regulation (EU) No. 618/2012 of the Commission of 10 July 2012 amending Regulation (EC) No. 1272/2008 of the European Parliament and of the Council on the classification, labeling and packaging of substances and mixtures for the purpose of adaptation to the technical and scientific progress , accessed May 18, 2019 . In: Official Journal of the European Union .
- ↑ Güven Purtul, Christian Kossin: Thermal insulation - the madness continues . ( Memento of May 12, 2012 in the Internet Archive ) NDR report, series 45 min , part II, first broadcast on November 26, 2012, 9:00 p.m.
- ↑ Hexabromocyclododecane in the Federal Environmental Specimen Bank
- ↑ Sabine Kemmlein, Oliver Hahn, Oliver Jann (BAM): Emissions of flame retardants from building products and consumer goods, Environmental Research Plan, Research Report 299 65 321, UBA-FB 000475. (PDF; 3.97 MB) Federal Ministry for the Environment, Nature Conservation and Nuclear Safety, September 2003, accessed January 21, 2013 .
- ↑ Jordan, Rob .: Plastic-eating Worms May Offer Solution to Mounting Waste, Stanford Researchers Discover. Stanford News, September 2015, accessed April 26, 2017 .
- ↑ Der Ornithologische Beobachter, volumes 95-96, Ala, Swiss Society for Ornithology and Bird Protection, 1998, p. 76
- ↑ Wolfram Scheiding, Peter Grabes, Tilo Haustein, Vera Haustein, Norbert Nieke, Harald Urban, Björn Weiß Wood protection: Wood science - fungi and insects - Constructive and chemical measures - Technical rules - practical knowledge, Carl Hanser Verlag GmbH Co KG 2016 - 296 pages, ISBN 978-3-446-44844-5 , p. 160
- ^ W. Keim : Kunststoffe: Synthesis, Manufacturing Processes, Apparatus , 379 pages, Verlag Wiley-VCH Verlag GmbH & Co. KGaA, 1st edition (2006) ISBN 3-527-31582-9
- ↑ Overview of polystyrene on chemgapedia.de. Retrieved April 24, 2016 .
- ↑ Peter Elsner, Peter Eyerer: Domininghaus - plastics: properties and applications . Ed .: Thomas Hirth. Springer, 2012, ISBN 978-3-642-16173-5 .
- ↑ Impact PS on chemgapedia.de. Retrieved April 24, 2016 .
- ↑ a b Jürgen Maul, Bruce G. Frushour, Jeffrey R. Kontoff, Herbert oak Auer, Karl-Heinz Ott, Christian Schade: Polystyrene and Styrene copolymer . In: Ullmann's Encyclopedia of Technical Chemistry . August. doi : 10.1002 / 14356007.a21_615.pub2 .
- ↑ a b PS graft copolymers on chemgapedia.de. Retrieved April 24, 2016 .
- ↑ PS block copolymers on chemgapedia.de. Retrieved April 24, 2016 .
- ↑ styrenic block copolymers - IISRP. (PDF) Retrieved September 30, 2019 .
- ↑ Study on the production, processing and recycling of plastics in Germany 2015 - short version , consultic, 23 September 2016
- ↑ D. Bender, H. Gausepohl, D. Braun, R. Gellert: Polystyrol. Hanser Verlag 1995; ISBN 3-446-18004-4 ; P. 467f: Requirements for polystyrene food packaging.
- ↑ Front-contact Styroflex capacitors for use in LF measurement and control technology , in the catalog of Oppermann-electronic.de
- ↑ Helmut Günzler, Harald Böck: IR Spectroscopy - An Introduction (VCH-Taschentext 193), p. 104.
- ^ Textbook plastics - materials of our time , p. 63, In: PlasticsEurope.org; Publisher: German Plastics Industry Working Group, 18th revised edition
- ↑ Ship World Series: Sinking of Ships - Tanker Vessel youtube.com, April 29, 2016, accessed July 11, 2017. - Video (42:37 minutes), lifting of a tank wreck broken into 3 parts, PS foam balls in the tank: here about in minutes 16 to 17.
- ↑ Information on the international Styrofoam brand in the register of the German Patent and Trademark Office (DPMA). Registered trademark of BASF, filing date July 19, 1954. With this and various later trademark registrations, various processed plastic products (not just polystyrene) are protected.
- ↑ airpop - a new name for a proven material. Press release of the IK Industrievereinigung Kunststoffverpackungen, May 9, 2014, accessed on April 4, 2016 .
- ↑ Market study expandable polystyrene . Ceresana.
- ↑ on this the floor tiles are glued. Shower elements are not to be confused with shower trays (these are made of acrylic, enamelled steel or mineral casting).
- ↑ Study “Built-in insulation EPS / XPS” , 2015
- ↑ Quality guidelines for facade insulation panels made of EPS rigid foam for thermal insulation composite systems (ETICS) (PDF; 139 kB).
- ^ Ulrich Schlotter: Generation and Management of EPS and XPS Waste in Germany. (PDF) November 7, 2017, accessed May 19, 2019 .
- ↑ a b IBP report BBHB 019/2014/281 “Dismantling, recycling and recovery of ETICS” , Fraunhofer Institute for Building Physics, November 12, 2014.
- ↑ Recycling of EPS waste to re-expandable polystyrene (EPS loop) (PDF; 91 kB)
- ↑ The CreaSolv® process
- ↑ Patent WO2006131376 : Process for recycling plastics and their use. Registered on June 8, 2006 , published on December 14, 2006 , applicant: Fraunhofer Society for the Promotion of Applied Research e. V., inventors: Andreas Mäurer, Otto Beck, Martin Schlummer.
- ↑ Polystyvert unveils the world's first polystyrene dissolution recycling plans. (PDF) August 20, 2018, accessed September 30, 2019 .
- ^ A demonstration plant next to an existing chemical recovery complex. Retrieved September 30, 2019 .
- ↑ Recycling of polystyrene foam waste with HBCD , Plastics Europe, August 2015.
- ^ Frank E Mark, Juergen Vehlow, Hans Dresch, Bogdan Dima, Werner Grüttner, Joachim Horn: Destruction of the flame retardant hexabromocyclododecane in a full-scale municipal solid waste incinerator . In: Waste Management & Research . 33, No. 2, 2015, pp. 165–174. doi : 10.1177 / 0734242X14565226 .
- ↑ Bernd Freytag: Disposal emergency for insulation boards . FAZ. October 1, 2016. Accessed February 1, 2017.
- ^ Pia Grund-Ludwig: The first federal states regulate the disposal of HBCD insulation . EnBauSa. October 20, 2016. Retrieved February 1, 2017.
- ↑ Current development on HBCD (D) -containing insulation materials, change in the Waste Catalog Ordinance . Bavarian State Office for the Environment, Information Center UmweltWirtschaft (IZU). January 11, 2017. Archived from the original on February 1, 2017. Info: The archive link was automatically inserted and has not yet been checked. Please check the original and archive link according to the instructions and then remove this notice. Retrieved February 1, 2017.
- ↑ Federal Council simplifies disposal of Styrofoam . Federal Council. July 7, 2017. Retrieved July 13, 2017.
- ↑ Information on HBCDD-containing insulation waste . Federal Ministry for Agriculture, Forestry, Environment and Water Management, January 25, 2017.
- ↑ Polystyrene Facts (PDF; 49 kB), King County Green Schools Program, May 2008.
- ^ Abhijit Bandyopadhyay, G. Chandra Basak: Studies on photocatalytic degradation of polystyrene . In: Materials Science and Technology . 23, No. 3, 2007, pp. 307-317. doi : 10.1179 / 174328407X158640 .
- ↑ BfR Recommendations - Polystyrene, which is obtained exclusively through the polymerization of styrene (PDF; 48 kB).
- ↑ BfR recommendations - mixed and grafted styrene polymers and mixtures of polystyrene with polymers (PDF; 119 kB).