fiber
A fiber is a linear, elementary structure that consists of a fiber material and has an outer fiber shape (longitudinal shape: plain, curled; cross-sectional shape: round, angular, etc.). The fiber can be endless or of limited length and is a thin, flexible structure in relation to its length. To speak of a fiber in the technical field, the ratio of length to diameter should be at least between 3: 1 and 10: 1; for many textile applications it is over 1000: 1. , Fibers longitudinally no pressure , but only tensile forces take as they reach pressure load bend . In nature and in technology, fibers usually occur in a larger composite.
Classification
Fibers are divided into natural fibers and man-made fibers.
Natural fibers
All textile fibers and fiber materials that are obtained from plant and animal material without chemical modification are called natural fibers. The natural fibers are divided into organic fibers with the subgroups vegetable and animal fibers as well as inorganic fibers, such as. B. asbestos or natural basalt fibers, which are also often referred to as mineral fibers.
Vegetable fibers (plant fibers)
Plant fibers are used in plants as vascular bundles in the stems or stem , the bark (about as Bast ) and as seed before -Fortsätze.
With the property fibrous - and also woody and herbaceous - unspecifically the heavily fiber-interspersed as well as the woody parts of an herbaceous plant are designated, in distinction to the young shoot and the leaf mass , especially in the case of food these are the portions not suitable for consumption . The article Fiber Plants gives an overview of the agriculturally grown suppliers of plant fibers .
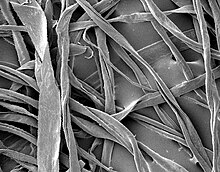
Vegetable fiber is a collective term for fibers of vegetable origin that are used as material in textile and other manufacturing processes. A subdivision is made according to the still valid DIN 60001-1 into seed fibers, bast fibers and hard fibers or according to the more recent DIN EN ISO 6938 based on international standards into seed fibers, bast fibers, leaf fibers and fruit fibers, which thus divide the hard fibers. The following list, which, if available, also contains the valid abbreviations for the fiber generic names, is mainly based on these two standards:
- Seed fibers have a unicellular structure formed by the epidermal cells of the seed. They are composed almost entirely of cellulose.
- Cotton fiber (CO) from the seed hairs of the fruit of the cotton plant
- Kapok (KP) from the inside of the capsule fruit of the real kapok tree
- Akon from silk plants
- Poplar fluff
-
Bast fibers are composite fibers obtained from the bast of certain plants, mostly from cellulose, but also accompanied by pectin bodies , hemicellulose and lignin .
- Bamboo fiber made from ( Bambusa textilis )
- Fiber nettle from the great nettle
- Hemp fiber (HA)
- Siberian hemp nettle
- Jute (JU)
- Urena (JR) from mallow family
- Flax fiber , also called linen (LI)
- Ramie fiber (RA) from the tropical nettle ramie
- Kenaf fiber (KE) from kenaf (Hibiscus Ostinischer hemp)
- Roselle (JS) fibers (Sudan Marshmallow)
- Fibers of the sun (SN) ( Crotalaria juncea )
- Abutilon from the beautiful mallow
- Punga from ( Clappertonia ficifolia )
- Castor oil from the wonder tree ( Ricinus communis )
- Bluish Dogbane from the hemp-like dog strangler ( Apocynum cannabinum )
- Leaf fibers are composite fibers obtained from leaves and are composed primarily of cellulose, as well as encrusting and intercellular materials composed of lignin and hemicelluloses.
- Sisal (SI) made from agave leaves
- Abacá (Manila hemp) (AB), leaf fiber from the leaves of the banana species [Musa textilis]
- Curauá made from bromeliads
- Fiber from agaves
- Ixtle fiber , also tampico fiber from agave lechuguilla
- Arenga fibers from the leaf sheaths of the sugar palm
- Afrik or palm fiber from a dwarf palm
- Henequen fibers (HE) from the Agave fourcroydes
- Fique (FI) leaf fibers from Furcraea macrophylla
- Phormium, also New Zealand flax (NF) from Phormium tenax
- Alfa (AL) from the leaves of the alfa grass
- Maguey from the leaves of the agave cantala
- Yucca made from the leaves of the palm lily family Yucca carnerosana
- Pita from the leaves of Aechmea magdalenae
- Fruit fibers are composite fibers obtained from fruits and are composed primarily of cellulose, as well as encrusting and intercellular materials composed of lignin and hemicelluloses.
- Coconut fiber (CC) from the shell of the coconut palm fruits
As replacement fibers z. B. used:
- Broom : the fibers from the stems of plant broom with a fiber yield of 6% to 7%
- Hops : fibers from the stems of hop plants with a fiber yield of 9% to 10%
- Cattail reed : fibers from the leaves and from the fruit heads with a fiber yield of 25 to 30%
- Willow bast : bark fibers of the willow with a fiber yield of 15% to 20%.
Bast remnants from linden and oak represent the most common finds of Neolithic fiber remains. The long fibers of these tree species were used as a material for making baskets , mats and cords . The best-known examples at the moment are probably the cloak and shoes of the man from Tisenjoch .
Animal fibers
A subdivision is made according to the still valid DIN 60001-1 into wool and hair (fine animal hair and coarse animal hair) and silks or according to the more recent DIN EN ISO 6938 based on international standards into fibers from spinneret glands, fibers separated from some types of molluscs and from Fibers derived from hair follicles. The following list, which, if available, also contains the valid abbreviations for the fiber generic names, is mainly based on these two standards:
- Fibers from spinneret glands that are secreted as secretions by some insects, especially larvae of the order Lepidoptera, in the form of two fibrion filaments that are glued together
by sericin
- Silk (SE) ( cultured silk ) - fibers from the cocoons of the mulberry silk moth ( Bombyx mori )
- Tussah silk (ST) - fibers made from cocoons of wild tussah moths (e.g. Chinese oak silk moth ) collected from trees and shrubs . Since the butterfly has mostly hatched here, the fibers are shorter and cannot be unwound.
- Mugaseide - fibers from the cocoons of the silk moth Atheraea assamensis
- Eri silk - fibers from the cocoons of the eri silk moth
- Anapheseide - fibers from the concons of Anaphe silk spinners
- Spider silk - fibers made by the spinning glands of spiders
- Fibers that are secreted by some species of mollusks
- Byssus silk - Byssus threads from mollusks, e.g. B. Pinna nobilis
The fiber from the spinning glands of silk spinners, which contains embryonic silk (Silkwormgut) (SGS), is special . This was used as medical suture material and is used in fly fishing .
- Fibers from hair follicles with a multicellular structure made up of keratin that make up the fur, fur, mane or tail of certain animals
- Wool from sheep (WO) ( new wool (WV)) is mostly obtained by annual shearing and is also known as new wool.
- Alpaca (WP), llama (WL), vicuna (WG), guanaco (GU) are the hairs of the lama species of the same name or sheep camels. The hair is fine, soft, shiny and not very frizzy.
- Camel hair (WK) is the soft, curled down hair of camels; they drop it annually. It is very fine, soft, slightly curled and beige-brown.
- Angora (WA) (hair from angora rabbits), rabbit (WN) (ordinary rabbit hair) are very fine, smooth and very light. Since they absorb water vapor well, rabbit fabrics are very warm-keeping.
- Cashmere (WS) is obtained by combing out and sorting the downy or guard hair of the cashmere goat . This hair is as fine as the finest merino wool , and cashmere clothing is therefore fine, soft, light and shiny.
- Mohair (WM) refers to the hair of the angora or mohair goat. They are long, slightly curly, and shiny. Their color is white. You hardly felt.
- Yak (HY) - hair of the goat ox
- Goat hair (HZ)
- Bovine hair (HR)
- Horsehair (HS) is very coarse and is used as padding and filling in mattresses.
Mineral fibers
Mineral fibers are obtained from rock types with a fiber structure, which are mainly composed of silicates
- Asbestos (AS) - fibrous natural silicate
- Erionite is not used because of its asbestos-like health hazard.
- Fiber plaster
- In addition to glass fibers, wollastonite is now used as a substitute for asbestos.
Man-made fibers
All fibers are referred to as man-made fibers that are manufactured artificially, using chemical-technical processes from natural or synthetic polymers as well as from inorganic substances, predominantly in the form of filaments ( monofilaments , multifilaments) and processed into filament yarns or processed into staple fibers (staple fibers) by cutting or tearing and then spun into yarns by secondary spinning processes or z. B. can be processed directly into textile fabrics by nonwoven manufacturing processes. Due to their artificial origin, they are still referred to as synthetic fibers .
The following list of generic names to designate the generic types of man-made fibers and the abbreviations in brackets is mainly based on the DIN EN ISO 2076 standard for the designation of man-made fibers from 2014. The generic names are usually used together with the word "fiber", see above z. B. the generic names viscose as viscose fiber and glass as glass fiber.
Natural polymer fibers
- Regenerated cellulose fibers
- Viscose (CV) is produced using the viscose process from pure cellulose, mainly from beech and pine wood or eucalyptus , and increasingly also from bamboo.
- Modal (CMD) is manufactured using the modified viscose process and therefore has a higher strength than viscose when dry and wet.
- Lyocell (CLY) is produced using a wet spinning process. N- methylmorpholine- N -oxide monohydrate is used as the solvent . The fiber is characterized by its very high dry and wet strength. Due to the almost closed production cycle and the possibility to use recycled cotton in addition to fast-growing types of wood, the production is particularly sustainable.
- Cupro (CUP) is produced using the copper oxide-ammonia process.
- Cellulose ester fibers
- Acetate (CA, formerly AC) is spun from cellulose acetate dissolved in acetone in a dry spinning process (see acetate fibers )
- Triacetate (CTA) is also made from cellulose acetate, but it is dissolved in dichloromethane .
- Protein fibers (USA: Azlon)
- Regenerated protein fibers (PR) made from regenerated natural protein of vegetable or animal origin, partly also stabilized by chemical agents.
- Modified soybean protein fibers (MSP) are spun using a wet spinning process from a spinning solution consisting of a mixture of short-chain soybean proteins that have been copolymerized with polyvinyl alcohol, which serves as a fiber structure, and long-chain soybean protein molecules.
- Zein one under the trade name Vicara produced in the 1950s, fiber from corn protein.
- Casein fibers (also known as casein fibers) are regenerated protein fibers made from milk protein that are of little economic importance today; Developed as a wool substitute (hence the earlier name casein wool) during the Second World War and until the 1950s , fiber was produced under trade names such as Lanital , Aralac , Merinowa . However, this type of fiber was rediscovered and produced in a new form.
- Artificial spider fibers (Biosteel®) here, synthetic proteins produced by bacteria, are formed into a spider-like fiber.
- Polylactide (PLA) fibers consist of linear macromolecules with at least 85% by mass of lactic acid ester units. Obtained from renewable raw materials either through polycondensation of lactic acid , which is obtained from starch , dextrose or simple plant sugars through fermentation , or indirectly from the cyclic dimers of lactic acid through ring opening and polymerization. The PLA pellets obtained are, like most synthetic fibers, spun by the melt spinning process.
- Alginate (ALG) - fibers made from metal salts of alginic acid ; Obtained by extracting seaweed with soda solution, which creates a viscous, aqueous solution of sodium alginate .
- Elastodiene (ED) - fiber made from natural polyisoprene (formerly called rubber fibers ); the name is also used for fibers made of synthetic polyisoprene.
- Bio-based polyamides (PA 4.10 / PA 6.10 / PA 10.10 / PA 10.12 / PA 11) - Are polyamide fibers made from castor oil or the monomers obtained from it from 11-aminoundecanoic acid and sebacic acid . The properties, very good chemical and thermal resistance, good dimensional stability and low density enable use in a variety of applications.
Synthetic polymer fibers
- Polyester (PES), mostly polyethylene terephthalate (PET): The PES fiber shows versatile properties and therefore occupies a leading position among synthetic fibers. It is very tear and abrasion resistant and hardly absorbs any moisture. Filaments / fibers made of polytrimethylene terephthalate (PTT) and filaments made of polybutylene terephthalate (PBT) are also manufactured.
- Polyamide (PA) (USA nylon): The PA fiber is very elastic as well as tear and abrasion resistant. Textiles made from it hardly crease. Polyamide can be permanently deformed by heat, which is used during heat setting .
- Polyimide (PI): The PI fiber is infusible, extremely thermally stable and flame-retardant, which is why it is mainly used in technical textiles, e.g. B. filter media is used.
- Polyamidimide (PAI): The PAI fiber has an extraordinarily high heat and flame resistance (up to 240 ° C), is infusible and resistant to common solvents.
- Aramid (AR): AR fibers are produced as m-aramid fibers (high temperature resistance and good chemical resistance) or p-aramid fibers (high strength and high modulus of elasticity ) and are mainly used for technical textiles, e.g. B. used in bulletproof vests .
- Polyacrylic (PAN); Acrylic fibers (also known as acrylic fibers for short) contain at least 85% polyacrylonitrile by mass . Homopolyacrylonitrile fibers (pure PAN) consist of almost 100% acrylonitrile and were originally developed as an asbestos substitute for the fiber cement and friction linings industry. The PAN fibers used as textile fibers are copolymer fibers, e.g. B. with a proportion of 7% polymethyl methacrylate . They have a wool-like feel and good light and chemical resistance. Along with pitch, PAN fibers are an important starting material for the production of carbon fibers . Polyacrylonitrile is also used to manufacture hollow fibers for membrane technology.
- Modacrylic (MAC): MAC fibers are mainly produced by the wet spinning process from a copolymer in which the PAN chain molecules containing at least 50% and at most 85% acrylonitrile components contain 15% to 50% comonomers, e.g. B. vinyl chloride or vinylidene chloride , have been introduced by copolymerization. MAC fibers are self-extinguishing. They are pure or in mixtures u. a. used for protective clothing or curtains and carpeting.
- Polytetrafluoroethylene (PTFE), according to DIN EN ISO 2076 fluorine fiber: The PTFE fiber is temperature-resistant, chemically largely inert, water-repellent and can hardly be dyed. The fiber is mainly used in technical textiles.
- Polyethylene (PE): PE fibers consist of more than 85% high or low density polyethylene and are produced using the melt spinning process. They do not absorb moisture, are resistant to a large number of chemicals, have high abrasion resistance, low tear resistance, a low softening range (85 ° C to 132 ° C depending on the type) and low UV stability, if not an additional one UV stabilizing modification takes place. Use of staple fibers primarily for nonwovens. A gel spinning process produces polyethylene filament yarns with a very high molecular weight, degree of crystallization , modulus of elasticity and strength level (280-330 cN / tex ). They are primarily used for ropes, ropes and nets → Dyneema this belongs to the subgroup (UHMW-PE; Ultra-High-Molecular-Weight Polyethylene), (HM-PE; High-Modulus Polyethylene), (HP-PE; High-Performance Polyethylene).
- Polypropylene (PP): The PP fiber is the textile fiber with the lowest density. Because of their absolutely hydrophobic constitution, their dry and wet tensile strength values are the same. It is resistant to aggressive chemicals and has good rub resistance. PP fibers are used in functional sports and underwear, for geotextiles, carpets and automotive textiles. PP fibers have numerous modifications such as B. microfibers, profile and hollow fibers, elastic and flame-retardant fibers.
- Polychloride (CLF), also chlorofibers : CLF fibers consist of linear macromolecules with at least 50% by weight vinyl chloride or vinylidene chloride in the chain. The polyvinyl chloride fiber made from the base polymer polyvinyl chloride (PVC) as the most important CLF fiber was the first synthetic fiber, but it is of little importance today. CLF fibers are non-flammable, have good thermal insulation properties, are absolutely hydrophobic, and are chemical-resistant to acids and alkalis. They show no signs of rotting and are weather and lightfast. The areas of application are in the field of technical textiles, but also in very warm underwear (rheumatic underwear) as well as decorative and upholstery fabrics mostly in mixtures.
- Elastane (EL); (EA / ELAS); (PUE), (USA: Spandex, Japan: Polyurethane): The EL fiber consists of at least 85% by weight segmented polyurethane and has a very high elastic elongation. Since it can be dyed easily compared to rubber, it is mostly used in conjunction with other fibers for stretch fabrics, swimwear and stockings.
- Polybenzoxazole (PBO): The PBO fibers were developed on the basis of poly (p-phenylene-2,6-benzobisoxazole) . They achieve maximum strength values and very high module values: The cause is the perfect structure of the crystalline structure. In addition, the PBO fibers are incombustible and thermally stable. The tensile strength values are twice as high as those of p-aramid fibers. It is used in heat and cut protection clothing and as a composite material , but also in high-temperature filter materials.
- Polybenzimidazole (PBI): The PBI fiber produced by the dry spinning process is made up of a long-chain aromatic polymer with recurring imidazole groups as an integral part of the polymer chain. The mechanical-technical properties are similar to those of viscose fibers, but the PBI fiber does not burn in the air, does not melt, is resistant to acids, alkalis and organic chemicals. It is particularly suitable for heat protection clothing.
- Polyurea (no current abbreviation, former abbreviation PUA or PB): The polyurea fiber consists of linear macromolecules, the chain of which shows a return of the functional urea group (NH-CO-NH). It forms a main group of the fiber-forming polyamides, of which the urylon fiber developed and produced in Japan gained particular importance. The advantage over other polyamide fibers is their acid resistance.
- Melamine (MEL, formerly also MF): The MEL fiber consists of at least 85% by mass of cross-linked macromolecules made from melamine derivatives. It can be dyed without any problems, is resistant to aromatics, is hydrolysis-stable and has good resistance to alkalis, less to long-term exposure to acids. The MEL fiber has a high flame resistance, high permanent temperature resistance and low thermal conductivity , which is why it is very suitable for work and fire protection textiles.
- Polyphenylene sulfide (PPS): The PPS fiber consists of linear macromolecules with a p -phenylthio group in the main chain. It is manufactured using the melt spinning process. The PPS fiber has excellent chemical resistance (so far only surpassed by PTFE fibers) and excellent thermal stability, which allows long-term use up to 190 ° C (short-term up to 230 ° C) without significant damage. The main applications are therefore in the area of hot gas filter media and paper machine felts in critical areas of the drying zone.
- Trivynil (according to DIN EN ISO 2076: 2014-03 without abbreviation, formerly: TV): The trivinyl fibers are produced by the joint polymerization of acrylonitrile, vinyl chloride (or vinylidene chloride) and a third vinyl monomer, whereby none of the vinyl monomers has 50% of the mass fractions . Today these fibers are hardly of any practical importance.
- Elastolefin (EOL) (USA: Lastol): The generic name applies to fibers made up of at least 95% macromolecules by mass, partly cross-linked, composed of ethylene and at least one other olefin and which, under the action of a tensile force, stretched by one and a half times the original length after relief immediately return to almost their original position. These elastic polyolefin fibers are characterized by a high temperature resistance (up to 200 ° C) as well as a high resistance to aggressive chemicals (especially to chlorine) and UV light.
- Elastomultiester (ELE) (formerly also: EME; USA: Elasterell-p): The ELE fiber is created by the interaction of two or more chemically different linear macromolecules in two or more different phases (none of which exceeds 85% by mass). It contains ester groups as the most important functional unit (at least 85%). During heat treatment, these different polymers trigger a different shrinkage capacity at a certain temperature, which leads to a “chemical” texturing . This crimp is not reversible and leads to an elongation and rebound behavior that is superior to the usual texturing. In this way, when the ELE fiber is stretched by 50% and then relieved, it returns almost immediately to its original length.
- Polyvinyl alcohol (PVA or PVAL): Polyvinyl alcohol fibers consist of linear macromolecules with at least 85% by weight of polyvinyl alcohol, which are created through the polymerization of vinyl acetate and subsequent saponification . If the degree of saponification is low, i.e. if there are few free OH groups, the PVA fibers are water-soluble. By varying the degree of saponification, the water solubility and thermoplasticity as well as the strength and elongation values can be adjusted as required. The water-soluble fibers are used z. B. as support or auxiliary threads that lead to patterns when detached from textile surfaces. The PVA fibers made water-insoluble by additional treatments have been referred to by the generic name Vinylal since 2001.
- Vinylal (PVAL) (Japan: Vinylon, USA: Vinal, DVKR: Vinalon ): The vinylal fibers are made from highly drawn and heat-treated polyvinyl alcohol fibers by subsequent acetalization (treatment mostly with formaldehyde). The crosslinking takes place predominantly between the thread molecules of the polyvinyl alcohol which are stored in parallel as a result of the stretching. The degree of acetalization and thus the properties of the fibers can be varied through the treatment conditions. The fibers have good moisture absorption (4–5%), high abrasion resistance, but also tend to wrinkle. The melting point is 230 ° C. They have good chemical resistance. Areas of application are technical textiles, but also decorative fabrics and bed linen. Because of their high strength values and resistance to alkalis, they are used as short cuts for cement and concrete renovation. These vinylal fibers are also sometimes referred to as polyvinyl acetal fibers.
- Polycarbonate (PC): The PC fibers are spun from solutions of polycarbonate using a wet spinning process or a dry spinning process. They are used as monofilaments for technical textiles, but also as microfibres, so-called polycarbonate electret fibers with a diameter of 1 to 10 µm for fine filters in air filtration.
- Polystyrene (PST, PS): The polystyrene fiber is produced from styrene or styrene copolymers by melt spinning according to the extrusion process. The fibers have a low density (1.05 g / cm 3 ) and a low water absorption capacity, as well as excellent electrical insulation properties. Coarse monofilaments are usually produced, but staple fibers are also delivery forms of this fiber. It is used in the technical field for thermal and electrical insulation materials and in soundproofing, but also in ion exchangers . The PS fibers are also used in optical conductors .
Fibers made from inorganic materials
- Ceramic fibers are a special class of inorganic fibers. They consist of a fibrous ceramic structure. They come as oxidic (aluminum oxides, mullites , yttrium oxides ) and non-oxidic (SiC, SiCN, SiBCN → polysilazanes ) fiber types. Their main area of application is in high-temperature applications for insulation materials (for short fibers) and as reinforcement fibers in highly stressed composite materials such as fiber-reinforced ceramics . The aluminum silicate wool known as “ceramic fiber” is used as high temperature wool for thermal insulation at temperatures above 700 ° C.
- Quartz fiber , silica fibers : The silica fibers are obtained by washing out E-glass . OH groups are embedded in the SiO 2 skeleton. They are used as asbestos substitutes, insulating material, in filters and filter papers or in optical conductors and lasers . They are also used in dentistry.
- Glass fiber (GF): Glass fibers are made from glass melts by drawing. Compared to polymer fibers, they are less ductile and are more brittle. The fineness is between 3 and 13 µm. They are not flammable. The melting point is between 900 ° C and 1000 ° C and the moisture absorption is below 0.5%. The textile glass fibers are u. a. used for non-flammable curtains and decorative fabrics and for interior decoration. They are used to a large extent to reinforce plastics and in technical textiles.
- Basalt fiber (currently no abbreviation): It is produced by melting basalt igneous rock and then pulling it through platinum / rhodium nozzle holes. Basalt stones with a silicon dioxide content of over 46% are suitable for this. The resulting filament yarns can also be cut into staple fibers. They are non-flammable and temperature-resistant between −260 and +700 ° C. The tensile strength and modulus of elasticity are slightly higher than that of glass fibers. Their resistance to acids and organic solvents is good. In the alkaline range, they are less sensitive than E-glass fibers , which is why they are more suitable for reinforcing fibers in concrete and cement. They are used in fiber-plastic composites . They are processed as rovings , plied yarns and twisted threads in technical fabrics, cords, tubes and belts.
- Carbon fiber (CF) (also carbon fiber): It is produced by thermal carbonization of organic precursors and ultimately consists of at least 90% mass fraction of carbon. The carbon fiber is a heat-resistant chemical fiber (melting point 3650 ° C) with a relatively low density (1.5-2.0 g / cm 3 ), high strength and rigidity. Carbon fibers are mainly used to reinforce plastics, in composite ceramics and in technical textiles. As a fiber felt they are used for the thermal insulation of high-temperature protective gas or vacuum furnaces.
- Boron fiber : The fibers have high strength and a high modulus of elasticity. Boron fibers are used in lightweight composite materials, mostly woven into mats and embedded in resins.
- Crystal fibers : Single-crystal fibers ( whiskers ) which consist of a monocrystalline material e.g. B. made of sapphire (Al 2 O 3 ) (aluminum oxide fibers ) or YAG (Y 3 Al 5 O 12 ) and silicon carbide , silicon nitride fibers. Another type are the polycrystalline fibers, here the material is applied to a core ( tungsten , molybdenum , carbon). B. BSiC or SiCW. Photonic crystal fibers ( photonic crystal fiber PCF).
- Slag fiber: The slag fiber is made from metallurgical slag.
- Nanotubefasern made almost entirely of carbon nanotubes ( English carbon nanotubes ). They have very high strengths and are still at an early stage of development. The NASA examines such fiber systems for the construction of space elevators .
- Metal fiber (MTF, ME / MET), very thin wire .
Absorbable fibers
Resorbable fibers are biodegradable in a relatively short time; they can consist of natural materials or man-made fibers. Various collagen fibers can be used from natural materials :
- Gut strings, catgut ( chromium , platinum, iodine catgut or cobalt catgut) are fibers which are produced from the submucosa or intestinal serosa of natural intestines .
- Animal tendons and muscles ( fascia )
The fibers used are often copolymers of lactone monomers ( lactide , glycolide , caprolactone and p -dioxanone PDO) and trimethylene carbonate (TMC) z. B. polyglycolic acid (PGA, PGS) (polyester), polylactide-co-glycolide (PLGA) (polyester) or from polydioxanone (PDS, PPDO), as well as hydroxybutyrate (PHB) (polyester), the fibers are often coated (e.g. B. with calcium stearate and others). They can be monofilament, but also multifilament , braided or twisted . These fibers are primarily used as medical sutures .
The fibers of the polyester polyhydroxyalkanoate (PHA) and polylactide (PLA) are also used, these are used as implants .
The materials are degraded by proteolytic enzymes or by hydrolysis .
properties
The properties of the fibers are made by
- the molecular structure (chemical structure)
- the supermolecular state of order (physical structure)
- the fiber geometry (fiber length, fiber crimp, fiber fineness , fiber cross-section)
- the fiber topography (surface design of the fibers)
In the case of man-made fibers, the fiber formation process (spinning, stretching , fixing, texturing) significantly influences the fiber geometry and topography, but also the supermolecular structure.
The fiber properties include the mechanical, electrical and optical properties as well as the behavior when exposed to moisture and water, when exposed to heat, when exposed to air and oxygen, when exposed to radiation and to chemicals. These fiber properties in turn determine the processing properties (technological properties such as dyeability, shrinkage behavior, etc.) and the properties of use (durability, clothing physiological behavior, etc.).
In addition to the characteristic length-diameter ratio, fibers have anisotropy (inequality in the three spatial dimensions) of the mechanical properties, i.e. H. a fiber, for example, can be stretched differently in its longitudinal direction compared to the transverse direction. In the case of several twisted fibers, a synergy of the mechanical properties is evident along the longitudinal direction , e.g. B. increases through spinning the tensile strength of the fiber bundle over the sum of the tensile strengths of the individual fibers. Most fibers are flexible due to the length-to-diameter ratio.
Fiber analysis
The different properties of fibers can be determined by various qualitative and quantitative methods. The composition can be determined by a fire test , an elemental analysis or a neutron activation analysis. During the firing test , the flame ( soot development), the smell, the pH value of the smoke and the consistency of the residue are observed, which are characteristic of the respective starting material. The fineness is determined by measuring the length and weight or with a vibroscope . Light microscopes , transmission electron microscopes and interferometers can be used to determine the fiber diameter and, in some cases, also to determine their origin. Using infrared spectroscopy , Raman spectroscopy and X-ray spectroscopy , fibers can be assigned to their origin via the respective material-dependent spectra.
Depending on the composition and structure of the fibers, they have different material properties . The characteristic mechanical properties of fibers such as elasticity , tensile , compressive , flexural , buckling and shear strength are determined with quantitative measurements in appropriate clamping devices. The anisotropy of the properties of fibers and the synergy of several twisted fibers can also be determined in this way.
International symbols for textile fibers
Extract from the list of abbreviations for the designation of natural and man-made fibers published by the international standardization office in Brussels (BISFA) based on DIN 7728:
designation | character | designation | character |
---|---|---|---|
cotton | CO | Elastane | Tbsp |
Flax, linen | LI | Glass | GF |
hemp | HF | jute | JU |
Camel hair | WK | coconut | CC |
lama | WL | Modal | CMD |
mohair | WM | Polyacrylic | PAN |
polyamide | PA | polyester | PES |
Polyethylene | PE | Polypropylene | PP |
ramie | RA | Sheep wool | WV |
Silk (mulberry silk) | SE | Sisal | SI |
viscose | CV | Goat hair | HZ |
The international standard for the abbreviations of man-made fibers is DIN EN ISO 1043-1.
For natural fibers, the abbreviations for Germany are specified in DIN 60001-1.
Textile suitability
According to the Textile Labeling Act , textile fiber is a "product that is characterized by its flexibility, its fineness and its great length in relation to its diameter".
The conditions for each type of production and application are specified in more detail by minimum requirements for individual properties (length, fineness, elasticity, moisture transport, insulating effect, etc.).
For example: Cotton for a certain yarn must be at least 12 mm long and 10 cN / tex strength, 4 mm is sufficient for wet nonwovens and 2 mm for flocking.
Man-made fibers made from polymers are very suitable for textiles, clothing and technical applications. Since the fibers are specially manufactured, their shape, thickness and length can be chosen almost freely. This explains u. a. the success of synthetic fibers compared to the traditionally used natural fibers since the early 1960s. Natural fibers can hold their own where they can have advantages over man-made fibers. In addition to the textile sector, they are also increasingly being used in technical textiles.
Natural fibers, glass fibers and carbon fibers are processed into fabrics or nonwovens. This is usually done in order to later process them into non-textile fiber composite materials , and rarely to use them directly in this form. For example, fiberglass fabrics are used as temperature-resistant insulation for cables.
Thin metal wires play a significant role in the manufacture of cables , where they are mostly braided .
If fibers are to be used in textiles, they have to be spun . Exception: nonwovens, felts and filaments.
Fiber blends
It is common today to mix fibers for textile applications. The aim is always to get a product ( yarn , nonwoven, etc.) with modified properties. Here, on the one hand, an attempt is made to obtain better usage properties, better physiological clothing properties or better care properties. On the other hand, one tries to achieve a change in the appearance or an increase in profitability. In terms of processing, blends are sometimes more difficult to handle than pure fibers. In some cases, however, fiber blends can be processed better.
- a fiber mixture ( melange ) as a multi-colored color effect in a yarn
- Vigogne (VG) is a mixture of cotton and viscose
- Vigoureux is a partially strip-shaped roller-printed fiber mixture to achieve high-quality, calm melange color effects
Generation and Consumption
The largest man-made fiber producers
The most important producer of man-made fibers is by far China, followed by Taiwan and the USA. In Europe, Germany and Italy are the most important producers.
rank | country | Production (in thousand tons ) |
rank | country | Production (in thousand tons) |
---|---|---|---|---|---|
1 |
![]() |
7905 | 8th |
![]() |
838 |
2 |
![]() |
3105 | 9 |
![]() |
800 |
3 |
![]() |
2744 | 10 |
![]() |
672 |
4th |
![]() |
2381 | 11 |
![]() |
555 |
5 |
![]() |
1681 | 12 |
![]() |
550 |
6th |
![]() |
1347 | 13 |
![]() |
423 |
7th |
![]() |
1289 | 14th |
![]() |
318 |
With the above figures it should be noted that production in China in particular has increased significantly since 2001. In 2006 the production there was just over 19 million tons.
PET fibers in particular are obtained on a large scale from recycled plastic. Around 40% of all PET bottles collected in Europe in 2009 were processed into textile fibers.
The largest natural fiber producers
Natural fibers are grown and processed in almost every country in the world - a total of almost 30 million tons annually. Cotton is by far the dominant natural fiber with 20 million t, followed by wool and jute with around 2–3 million t. Despite its widespread use, the main areas of natural fiber production can be identified in South Asia, East Asia and China, Central and Eastern Europe, East Africa and Brazil.
Textile fiber consumption
In 2009 approx. 76 million tons of textile fibers were produced (11 kg / world inhabitant). From that:
rank | group | Highest proportions | % |
---|---|---|---|
1 | cotton | China, USA, India | 33 |
2 | Filaments | PES, PA, PP | 33 |
3 | Chemical staple fibers | PES, PAN, CV | 24 |
4th | Otherwise. vegetable Fibers | JU, LI, CC, SI | 7th |
5 | Animal fibers | WHERE, WL, WK, WM | 2 |
The statistics do not include glass fibers, 1.7 million tons of which were used for composites alone.
literature
- Fabia Denninger, Elke Giese, Herbert Ostertag, Alfons Hofer (up to 7th edition): Textile and Fashion Lexicon. 2 volumes: Volume 1: A – K and Volume 2: L – Z , 8th edition, Deutscher Fachverlag , Frankfurt am Main 2006, ISBN 3-87150-848-9 .
- Jürgen Dispan: Chemical fiber industry in Germany. Industry report 2015. (= IMU Information Service. 2/2015). Stuttgart 2015, ISBN 978-3-934859-49-4 .
- Alfons Hofer: Fabrics 1. Textile raw materials, yarns, effects. 7th edition, Deutscher Fachverlag, Frankfurt am Main 1992, ISBN 3-87150-366-5 , pp. 228-251.
- AR Bunsell, P. Schwartz: Handbook of Tensile Properties of Textile and Technical Fibers. Woodhead, 2008, ISBN 978-1-4398-0145-1 .
- AR Horrocks, SC Annand (Ed.): Handbook of Technical Textiles. Woodhead Publishing, Cambridge 2000, ISBN 1-85573-385-4 .
- Walter Loy: Chemical fibers for technical textile products. 2nd edition, Deutscher Fachverlag, Frankfurt am Main 2008, ISBN 978-3-86641-197-5 .
- Peter Eyerer, Thomas Hirth, Peter Elsner (Eds.): Polymer Engineering. Springer, 2008, ISBN 978-3-540-72402-5 .
- Gajanan Bhat: Structure and Properties of High-Performance Fibers. Woodhead, 2017, ISBN 978-0-08-100551-4 .
- PR Lewis: High Performance Polymer Fibers. Rapra Technology Limited, 1997, ISBN 978-1-85957-159-0 .
- Wolfgang Bobeth (ed.) U. a .: Textile fibers. Springer, 1993, ISBN 978-3-642-77656-4 .
Web links
- Fiber table , from ginetex.ch, accessed on July 19, 2018.
- Industrievereinigung Chemiefaser e. V. (IVC)
- International year of natural fibers
- News portal renewable raw materials
- Substance lexicon
- Lexicon of textile furnishing - rubric chemical fibers
Individual evidence
- ↑ Günter Schnegelsberg: Manual of the fiber - theory and systematics of the fiber. Deutscher Fachverlag, Frankfurt am Main 1999, ISBN 3-87150-624-9 , p. 504.
- ↑ Anton Schenek: Encyclopedia yarns and threads: properties and production of textile yarns. Deutscher Fachverlag, Frankfurt am Main 2006, ISBN 3-87150-810-1 , p. 149.
- ↑ Chokri Cherif (ed.): Textile materials for lightweight construction. Techniques - Processes - Materials - Properties. Springer-Verlag, Berlin / Heidelberg 2011, ISBN 978-3-642-17991-4 , p. 14.
- ↑ Wolfgang Bobeth (Ed.): Textile fibers. Texture and properties. Springer-Verlag, Berlin / Heidelberg / New York 1993, ISBN 3-540-55697-4 . (Overview, rear attachment)
- ↑ a b DIN 60001-1: 2001-05 Textile fiber materials - Part 1: Natural fibers and abbreviations. Beuth Verlag, Berlin 2001, p. 2.
- ↑ a b c d e f g h i j k DIN EN ISO 6938: 2015-01 Textiles - natural fibers - generic names and definitions. Beuth Verlag, Berlin 2015, p. 4.
- ↑ Anton Schenek: natural fiber lexicon . Deutscher Fachverlag, Frankfurt am Main 2001, ISBN 3-87150-638-9 , p. 105.
- ^ Jose Luis Cenis, Salvador D. Aznar-Cervantes, Antonio Abel Lozano-Pérez and others. a .: Silkworm Gut Fiber of Bombyx mori as an Implantable and Biocompatible Light-Diffusing Fiber. In: Int. J. Mol. Sci. 17 (7), 2016, 1142; doi : 10.3390 / ijms17071142 , online (PDF; 10.25 MB), at mdpi.com, accessed on March 24, 2017.
- ↑ DIN EN ISO 6938: 2015-01, Beuth Verlag, Berlin 2015, p. 10.
- ↑ Hans-J. Koslowski: Chemical fiber - Lexicon. 12th edition, Deutscher Fachverlag, Frankfurt am Main 2008, ISBN 978-3-87150-876-9 , p. 50.
- ↑ Anton Schenek: Encyclopedia yarns and threads - Properties and production of textile yarns. Deutscher Fachverlag, Frankfurt am Main 2006, ISBN 3-87150-810-1 , p. 76.
- ↑ DIN EN ISO 2076: 2014-03, textiles - man-made fibers - generic names. Beuth Verlag, Berlin 2014, pp. 7-18.
- ^ Walter Loy: p. 33.
- ↑ Fabia Denninger, Elke Giese: Textile and Model Lexicon. Volume: A – K , 8th completely revised and expanded edition, Deutscher Fachverlag, Frankfurt am Main 2006, ISBN 3-87150-848-9 , p. 355.
- ↑ Dr. Hermann Rath: Textbook of textile chemistry including textile chemical technology. Springer, Berlin / Heidelberg, 1952, ISBN 978-3-642-53161-3 , p. 180. f.
- ↑ Milk makes fashion: Biofibers made from casein ( Memento from 23 August 2018 in the Internet Archive ).
- ↑ Textile fibers from milk protein on ingenieur.de, accessed on January 26, 2017.
- ↑ AMSilk and the secret of the spider. In: Groz-Beckert . Newsletter 2, 2013, accessed on June 21, 2018.
- ↑ Sneaker made of biotech spider silk on biooekonomie.de, accessed on March 17, 2017.
- ^ Walter Loy: p. 31.
- ^ Walter Loy: p. 31.
- ^ Walter Loy: p. 110.
- ^ Walter Loy: p. 83.
- ^ Walter Loy: p. 54.
- ^ Walter Loy: p. 61.
- ↑ Hans-J. Koslowski: Chemical fiber - Lexicon. 12th expanded edition, Deutscher Fachverlag, Frankfurt am Main 2009, ISBN 978-3-87150-876-9 , p. 183.
- ^ Walter Loy: p. 82.
- ↑ Günter Schnegelsberg: Manual of the fiber - theory and systematics of the fiber. Deutscher Fachverlag, Frankfurt am Main, 1999, ISBN 3-87150-624-9 , p. 151.
- ↑ DIN EN ISO 2076: 2014-03, textiles - man-made fibers - generic names. Beuth Verlag, Berlin 2014, p. 16.
- ^ Walter Loy: p. 110.
- ^ Paul Schlack : Current questions of man-made fibers in research and development. Lenzinger Reports, Volume 15, October 1963, pp. 8-13, online (PDF; 1.07 MB), at lenzing.com, accessed on February 6, 2017.
- ↑ Alois Kießling, Max Matthes: Textile specialist dictionary. Fachverlag Schiele & Schön, Berlin 1993, ISBN 978-3-7949-0546-1 , pp. 297 and 302.
- ↑ DIN EN ISO 2076: 2014-03, textiles - man-made fibers - generic names. Beuth Verlag, Berlin 2014, p. 15.
- ^ Walter Loy: p. 111.
- ↑ Hans-J. Koslowski: Chemical fiber - Lexicon. 12th edition, Deutscher Fachverlag, Frankfurt am Main 2008, ISBN 978-3-87150-876-9 , p. 132.
- ↑ DIN EN ISO 2076: 2014-03, textiles - man-made fibers - generic names. Beuth Verlag, Berlin 2014, p. 15.
- ^ Walter Loy: p. 117.
- ↑ Hans-J. Koslowski: Chemical fiber - Lexicon. 12th expanded edition, Deutscher Fachverlag, Frankfurt am Main 2009, ISBN 978-3-87150-876-9 , p. 176 f.
- ↑ DIN EN ISO 2076: 2014-03, textiles - man-made fibers - generic names. Beuth Verlag, Berlin 2014, p. 16.
- ↑ Hans-J. Koslowski: Chemical fiber - Lexicon. 12th expanded edition, Deutscher Fachverlag, Frankfurt am Main 2009, ISBN 978-3-87150-876-9 , p. 233.
- ↑ DIN EN ISO 2076: 2014-03, textiles - man-made fibers - generic names. Beuth Verlag, Berlin 2014, p. 15.
- ↑ Hans-J. Koslowski: Chemical fiber - Lexicon. 12th expanded edition, Deutscher Fachverlag, Frankfurt am Main 2009, ISBN 978-3-87150-876-9 , p. 72.
- ↑ DIN EN ISO 2076: 2014-03, textiles - man-made fibers - generic names. Beuth Verlag, Berlin 2014, p. 17.
- ↑ Hans-J. Koslowski: Chemical fiber - Lexicon. 12th expanded edition, Deutscher Fachverlag, Frankfurt am Main 2009, ISBN 978-3-87150-876-9 , p. 72.
- ^ Walter Loy: p. 69 f.
- ↑ DIN EN ISO 2076: 2014-03, textiles - man-made fibers - generic names. Beuth Verlag, Berlin 2014, p. 14.
- ↑ Hans-J. Koslowski: Chemical fiber - Lexicon. 12th expanded edition, Deutscher Fachverlag, Frankfurt am Main 2009, ISBN 978-3-87150-876-9 , p. 241.
- ^ Bernhard Schrader , Paul Rademacher: Short textbook of organic chemistry. 3rd edition, De Gruyter, Berlin 2009, ISBN 978-3-11-019447-0 , p. 194.
- ↑ Wolfgang Bobeth (Ed.): Textile fibers. Texture and properties. Springer-Verlag, Berlin / Heidelberg / New York 1993, ISBN 3-540-55697-4 , p. 364.
- ↑ Hans-J. Koslowski: Chemical fiber - Lexicon. 12th expanded edition, Deutscher Fachverlag, Frankfurt am Main 2009, ISBN 978-3-87150-876-9 , p. 166.
- ^ Walter Loy: p. 258.
- ↑ Alois Kießling, Max Matthes: Textile specialist dictionary. Fachverlag Schiele & Schön, Berlin 1993, ISBN 978-3-7949-0546-1 , p. 295.
- ↑ Bela von Falkai: Properties and possible uses of polycarbonate fibers. In: Lenzinger reports. 32, 1971 [1] (PDF; 1.97 MB), from lenzing.com, accessed on March 3, 2017.
- ↑ Hans-J. Koslowski: Chemical fiber - Lexicon. 12th expanded edition, Deutscher Fachverlag, Frankfurt am Main 2009, ISBN 978-3-87150-876-9 , p. 180.
- ↑ Fabia Denninger (Ed.): Lexicon of technical textiles . Deutscher Fachverlag, Frankfurt am Main 2009, ISBN 978-3-86641-093-0 , p. 323
- ↑ Th. Nemetschek and U. Hofmann: Fine fibers from silica. In: Z. for Naturf. B . 8 (8), 1953, pp. 410-412, (PDF; 4.18 MB), doi : 10.1515 / znb-1953-0804 .
- ^ Hilmar Fuchs , Wilhelm Albrecht: Nonwovens. 2nd edition, Wiley-VCH, 2012, ISBN 978-3-527-31519-2 , p. 43 f.
- ↑ DIN EN ISO 2076: 2014-03, textiles - man-made fibers - generic names. Beuth Verlag, Berlin 2014, p. 14.
- ↑ Hans-J. Koslowski: Chemical fiber - Lexicon. 12th expanded edition, Deutscher Fachverlag, Frankfurt am Main 2009, ISBN 978-3-87150-876-9 , p. 97.
- ↑ Walter Loy: p. 94 ff.
- ↑ Chokri Cherif (Ed.): Textile materials for lightweight construction - Techniques - Process - Materials - Properties. Springer-Verlag, Berlin / Heidelberg 2011, ISBN 978-3-642-17991-4 , p. 92.
- ↑ Walter Loy: p. 100 ff.
- ↑ Hans-J. Koslowski: Chemical fiber - Lexicon. 12th expanded edition, Deutscher Fachverlag, Frankfurt am Main 2009, ISBN 978-3-87150-876-9 , p. 33.
- ↑ DIN EN ISO 2076: 2014-03, textiles - man-made fibers - generic names. Beuth Verlag, Berlin 2014, p. 14.
- ↑ Hans-J. Koslowski: Chemical fiber - Lexicon. 12th expanded edition, Deutscher Fachverlag, Frankfurt am Main 2009, ISBN 978-3-87150-876-9 , p. 118.
- ↑ Martin Bertau, Armin Müller u. a .: Industrial inorganic chemistry. John Wiley & Sons, 2013, ISBN 978-3-527-64958-7 .
- ^ Wilhelm Albrecht, Hilmar Fuchs , Walter Kittelmann: Vliesstoffe. Willey-VCH, 2000, ISBN 978-3-527-62569-7 , p. 64.
- ↑ Single-crystal Fibers on rp-photonics.com, accessed March 5, 2017.
- ↑ Heinz M. Hiersig: Lexikon production technology process engineering. Volume 2, Springer, 1995, ISBN 978-3-642-63379-9 , p. 266 f.
- ↑ Philip Russell: Caged Light. Photonic crystal fibers. In: Physics in Our Time . Volume 39, Issue 4, 2008, pp. 168–174, doi : 10.1002 / piuz.200801166 , online at yumpu.com, accessed March 5, 2017.
- ↑ Hollow-core fiber on itwissen.info, accessed on March 5, 2017.
- ↑ Modern suture materials and suture techniques in surgery (PDF; 4.04 MB), on ueberweisungspraxis-bremen.de, accessed on March 24, 2017.
- ↑ Monika Franziska Maria Flury: Historical roots of the various suture material properties. Dissertation, Julius-Maximilians-Universität Würzburg, Würzburg 2002, DNB 969152930 , online (PDF; 6.51 MB), at opus.bibliothek.uni-wuerzburg.de, accessed on March 24, 2017.
- ^ J. R Siewert, M. Rothmund, V. Schumpelick (eds.): Gastroenterologische Chirurgie. 3rd edition, Springer, 2011, ISBN 978-3-642-14222-2 , pp. 164–176, limited preview in the Google book search.
- ↑ Severian Dumitriu: Polymeric Biomaterials. Second Edition, Marcel Dekker, 2002, ISBN 0-8247-0569-6 , pp. 492–506, limited preview in the Google book search.
- ↑ Wolfgang Bobeth (Ed.): Textile fibers. Texture and properties. Springer-Verlag, Berlin / Heidelberg / New York 1993, ISBN 3-540-55697-4 , p. 13.
- ^ American Association of Textile Chemists and Colorists: AATCC Technical Manual. (2005), Volume 80, Library of Congress Catalog Number 54-34349, online at academia.edu, accessed February 6, 2017.
- ↑ WE Morton, JWS Hearle: Physical Properties of textile fibers. 4th edition, Woodhead, Cambridge 2008, ISBN 978-1-84569-220-9 , pp. 33-57, pp. 134-137.
- ↑ Lisa Yount: Forensic science: from fibers to fingerprints - Milestones in discovery and invention. Chelsea House, 2007, ISBN 978-0-8160-5751-1 .
- ↑ Handelsblatt : The world in numbers. Scherz, 2005, ISBN 978-3-502-15049-7 .
- ↑ Man-Made Fiber Yearbook 2007. IBP International Business Press Publishers, ISSN 1434-3584
- ↑ H.-J. Koslowski: Chemical fiber - Lexicon. 12th edition, Deutscher Fachverlag, Frankfurt am Main 2008.
- ↑ Recycle it! Krones Magazin, 03/2012, p. 16, on docplayer.org, accessed on January 28, 2017.
- ↑ M. Carus et al. a .: Study on the market and competitive situation for natural fibers and natural fiber materials (Germany and EU). (PDF; 3.9 MB).
- ↑ a b c d The Fiber Year 2011. ( Memento from January 30, 2013 in the web archive archive.today ) on oerlikontextile.com.
- ↑ Statistics at faostat.fao.org.
- ↑ Louis Pilato: Phenolic Resins: A Century of Progress. Springer, Berlin / Heidelberg 2011, ISBN 978-3-642-04713-8 , limited preview in the Google book search.