Tanning
The processing of raw animal hides into leather is called tanning . In a tannery or leather factory, the skin structure is stabilized through the use of tanning agents and leather is thus produced. Tanning is one of the oldest cultural achievements of mankind. Most of the chemicals used represent a hazard to the environment if they are improperly disposed of. The former job title of tanner is used in Germany in training to become a specialist in leather production and tanning technology .
For tanning and finishing of skins see of fur and fur processing .
Prehistory and History
Origins
Leatherworking was necessary and natural for both Neanderthals and modern humans in central and northern Eurasia as early as the Paleolithic Age . Scrapers and smoothers for removing subcutaneous fatty tissue and other tools made of bone and stone ( flint ) with typical signs of use were identified. It cannot be clearly established whether the animal hides have actually already been tanned or have only been made more or less durable using appropriate methods. Because of the rapid rotting of organic materials in the soil, the amount of leather objects found is extremely low.
With the mastery of fire, the tanning effect of smoke became known. Smoke tanning, along with tanning with animal fats, is one of the oldest tanning methods. The effect of different substances such as smoke, fat, parts of plants or mineral salts was discovered empirically and probably often by chance. The development of tannery depended heavily on the general level of development of the population group and on the materials immediately available.
Antiquity
The Egyptians knew the processing of hides and skins as early as 5000 BC. Images in graves from around 1600 BC. Chr. Represent the processing, but also the production of leather. The effects of plants containing tanning agents and of alum were known.
The oldest written records about leather production go back to the Greeks (1200 BC) and the Assyrians (700 BC). Preservation methods were vegetable tanning and fat tanning.
Even in the time of the Greeks , but of course also with the Romans , the economic importance of leather production was considerable. Presumably because of the unsanitary working conditions, the environmental pollution and not least because of the strong carrion odor that also attached to the tanners, they were not very respected; the work was mainly done by slaves . The Romans used pine , alder and pomegranate bark , gall apples , sumac and oak as tanning materials . During excavations in Pompeii , which was buried in 79 AD, parts of a tannery were uncovered.
Middle Ages and Early Modern Times


In the Middle Ages , leather was a preferred material. In Europe leather workshops arose near monasteries and in cities. The tanneries often reached impressive sizes. However, their operators had to retreat to their own neighborhoods in the cities: The production of leather was a dirty and literally disreputable business, so tannery was a socially not very recognized and dangerous job. Dealing with the rotting skin and the (poisonous) chemicals released extreme stench, and it was easy to get infected with anthrax and other diseases. A worker who survived anthrax was very valuable and enjoyed better treatment from his employer. The tanners (also tanners, Löher, Loher) belonged to the unclean crafts. In some cities, a Löhergasse or a Lohgerberstraße is a reminder of their craft.
The guild system regulated the market and also the craft. As a result, technical progress was difficult and was made, if at all, through the influence of foreign cultures. From the 14th century onwards, the areas of leather production (tannery) and leather processing separated. Subsequently, the tannery was subdivided into red tanner , Corduan (vegetable tanning ), white tanning (tanning with aluminum salts), chamois tanning (tanning with fat) and fur dresser.
From around 1700 one dealt scientifically with the tannery. If the main problem was the production of usable leather up to now, more research has been carried out into processes to accelerate and rationalize tanning. New tanning methods were developed and also published, such as those of the French chemist Armand Seguin . In 1803 the first magazine on tanning appeared.
The Berlin tannery gained significant expansion and improvement since 1734 through French immigrants. The patent leather production, which was first successfully operated in France, was soon also operated in Germany, as was the white tanning of goat, lamb and sheepskin , which was initially a special branch of industry in Annonay and its surroundings. Later the English and Americans competed in the training of fast tanning.
19th century
The first steam engines were used at the beginning of the 19th century . In addition to driving the machines, the steam was also used to produce concentrated tannin extracts. This made it possible to shorten the tanning times from several months to a few weeks. This created an efficient, rapidly growing tanning industry. In the middle of the 19th century the leather trade was the third largest branch of industry in the area, which was to be constituted as the German Empire in 1871 .
The first tannery machines were developed around 1840. Until then, processing was still done manually, little changed since the Stone Age. Only simple pumps or transport devices were used. The development of tanning vessels that allowed the hide material to move, especially the rotating tanning barrel, was of particular importance. This enabled the chemical processes to be accelerated considerably. Many modern tannery machines still work on the same principle.
New vegetable tanning agents rich in tannin were introduced from the colonies (1822 Mimosa, 1867 Quebracho). The first chrome tanning process was patented in 1861. However, chrome tanning only gained greater practical importance in the 20th century.
Some chemicals added to tanning agents from the middle of the 19th century to accelerate tanning had a negative effect on the aging resistance of the leather. The resulting accelerated decay of leather results in a reddish dust called red decay .
Environmental protection, for example in connection with wastewater treatment, was already an important issue back then.
The first relevant research and educational institutions were founded at the end of the 19th century, for example in Vienna in 1874 , in Freiberg (Saxony) in 1889 , in Yorkshire in 1891 , and later in Leeds . The development of the tannery was thereby considerably accelerated, it took place mainly in Europe and the United States .
20th century
The further development is closely related to the development of the chemical industry. The first synthetic dyes were developed in 1850. In 1907 Otto Röhm began producing enzymatic pickling; the unsanitary use of dog droppings or bird droppings could be avoided.
The first synthetic tanning agents were developed in 1911. Originally, they were intended to be a substitute for the vegetable tanning agents that were sometimes difficult to find. In fact, they have established themselves as valuable tools for accelerating vegetable tanning and as retanning agents for chrome-tanned leather. With the help of fat chemistry , such important auxiliaries as surfactants and water-thinnable fatliquors (liquors) were developed. The development of the first artificially produced paints and binders for finishing also fell during this period.
The faster and more economical chrome tanning was further developed, in particular through the efforts of Heinzerling, who was the first to produce chrome-tanned leather. New types of leather with new properties were created. Chrome tanning was the most important tanning process from the middle of the 20th century at the latest, and it has remained so to this day.
In 1921 the Kaiser Wilhelm Institute for Leather Research was founded in Dresden under the direction of Max Bergmann . It was rededicated for political reasons in 1933 and has been meaningless since then. (Continuation after the war at the Max Planck Institute for Protein and Leather Research and re-establishment in 2002 as the “Max Bergmann Center for Biomaterials”, jointly operated by the TU Dresden and the “Institute for Polymer Research” in the Leibniz Association .)
The advances in chemistry not only brought advantages for leather production. New materials were discovered that developed into competing products. The general technical development, for example the automobile, caused the demand for certain leather articles to decrease considerably. Quite a few tanneries in Europe, mainly those that were set up to produce vegetable leather, failed to make the switch and had to close.
The technical development was carried out more and more in the chemical groups of the supplier industry. The finishing department in particular benefited from the development of new binders (acrylates, butadienes, polyurethanes) and processes. Over the course of time, these internationally active corporations developed essential application knowledge, which they also marketed internationally. That means that modern technology was and is available internationally.
In the second half of the 20th century, the European and North American leather industries came under pressure. A strong, competitive leather industry established itself in Asia and South America . In addition to the difficult economic situation, environmental regulations in Europe were tightened in the 1970s. The necessary investments and, in some cases, high production costs caused the leather industry in Europe to shrink further.
Since 1937 there has been a professional training as a tanner. In 1981 the regulations were updated and a state-recognized training occupation was created in accordance with the Vocational Training Act .
The technical developments of the last few years are mainly geared towards ecological processes and products. In addition, rationalization and automation of the manufacturing processes as far as possible also play an important role.
While leather can now more and more often be replaced by modern materials, until the 20th century it was a material for whose properties there were no substitute materials.
Properties of tanned hides
The main effects of tanning are:
- Irreversible binding of the tannins to the skin - that is, the leather cannot be completely converted back into raw hide without being destroyed. This is an essential difference to preservation, which is reversible.
- Resistance to natural self-decomposition by microorganisms
- Leather-like drying up (raw skin dries up like a horny translucent)
- Greatly reduced swelling when soaking in water
- High resistance when heated when wet (high shrinkage temperature); The raw skin of mammals begins to glue when heated in water at around 62 ° C, which can be recognized by a significant shrinkage. Depending on the tanning, leather can reach shrinkage temperatures of over 100 ° C; one then speaks of boiling leather.
The animal skin
The animal skin consists of three layers of upper , leather and lower skin . Although the roots of the hair are often anchored deep in the dermis, they are still formed by the epidermis. The epidermis and its formation products mainly consist of the sulfur-containing protein keratin . It is made up of cells and is usually chemically dissolved; this work step is called "liming".
The subcutaneous tissue, which consists of loose, fibrous collagen loosened up by muscle tissue, blood vessels and fat cells , is removed mechanically (flesh).
The remaining middle part is composed of the thin papillary layer and the thick reticular layer . These layers consist of a third of the fibrous protein collagen and about 60% of water. The papillary layer has a denser, but less intertwined fiber structure and forms the smooth surface on the finished leather, which is known as the grain. The reticular layer is made up of coarser collagen fibers that are more intertwined. It is responsible for the mechanical strength of the skin and the leather.
Other proteins found in the dermis such as elastin , blood components ( albumins and globulins ), cellular proteins, pigments and keratin residues from the epidermis are removed as completely as possible before the actual tanning. Natural fats are extracted before or after tanning.
In fur trimming, the chemical process of epidermis and hair removal is omitted.
The dermis often has considerable structural differences over the entire surface. The area on the back and croup (core or croupon ) is denser and firmer with most types of skin, while the abdomen and armpits ( flaming ) usually have a very loose, less valuable structure. The tanning should compensate for this as much as possible and prevent the collagen fibers ( fibrils ) from sticking together and the horn-like drying out during drying . In addition to the insulation, the fibrils are crosslinked by the tannins in order to increase the dimensional stability under mechanical stress.
Work steps in the tannery
overview
A basic distinction must be made as to whether the hide is to be processed into leather without hair (leather tanning) or into leather with hair (fur tanning or fur finishing ).
The following steps are common for manual or industrial leather tanning :
- Soft
- Skin breakdown in liming (depilation and loosening of the skin fiber structure)
- Deflecting (mechanical removal of the subcutaneous connective tissue)
- Cracks (with thick skins)
- Deliming
- Enzymatic stain
- Degreasing (only for skin types with a lot of natural fat, e.g. pigs, sheep)
- Pimples (only with some tannins; preparation for tanning (e.g. chrome tanning) by acidifying the skin)
- tanning
- Drainage (wilting)
- Thickness regulation (folding)
- Wet finishing (bleaching, retanning, dyeing, greasing)
- Stretching (stretching and draining)
- Drying
- Moistening (conditioning)
- Softening through mechanical processing (studs, milling)
- dry
- Dry dressing (surface treatment)

The fur tanning is similar:
- Soft
- Deflecting (mechanical removal of the subcutaneous connective tissue)
- Laundry - degreasing
- Pimples
- tanning
- Fatliquoring, possibly retanning and coloring
- Drying
- Moistening (conditioning): treatment with moist sawdust (moist lauter)
- Softening by mechanical processing (studs)
- Sanding the leather side
- dry
- Combing the coat
- Dry lautering (treatment with dry wood flour)
- Ironing the coat
In principle, similar work steps have existed for a long time. The following has changed compared to historical tanneries:
- Until the 19th century, the wet processes were carried out in pits. The vessels were made of wood. The skins were seldom mixed because this was laborious manual work. As a result, the process times were sometimes very long.
- The work vessels used today for wet processes are the tanning barrel in leather production and the reel in fur finishing. Today, more or less intensive mixing and precise temperature control are possible in both areas. This significantly accelerated the processes. Vessels made of stainless steel or plastic are used. With modern regulation, control and dosing systems, individual processes can run automatically.
The preparation
After skinning, the raw hides are first trimmed (trimmed, cut to size). This removes parts that are not suitable for leather production. After that, the skin must be preserved as quickly as possible in order to stop organic deterioration and avoid qualitative damage. This is mostly done through salting. In regions where the distances and the supply chains allow, the hides are also preserved for a short time by cooling and thus no salt is used. In some regions where salt is scarce and the climate allows it, hides and skins are also dried.
After the transport, the skin goes through the water workshop , in the course of which the non-leathery components (hair, subcutaneous connective tissue, fat and unstructured proteins) are removed.
In the first step, the soak , the skin is soaked in water so that it is cleaned and brought to its original, natural water content.
Then it is placed in the liming for a few hours to days to break down the skin (remove the hairy epidermis and loosen up the fiber structure). In the traditional process, milk of lime was usually used for this . Today the process mostly takes place in the highly alkaline range with lime and sulphides and / or enzymes , which significantly accelerates depilation. The more intense the skin exposure, the softer the finished leather will be. The softened and depilated skin is called nakedness .
When flesh is removed, the subcutaneous tissue is removed mechanically so that ultimately only the dermis remains. In the past this was done manually on the gerber tree - see picture. Today this is done automatically.
When splitting , the dermis is cut once or several times horizontally across the entire surface. The grain gap is obtained with the papillary layer and the reticular layer and the flesh gap , which consists only of the reticular layer (see split leather ).
The waste that arises when removing the flesh and the inferior split pieces are called glue leather and are processed into skin glue , gelatine or dog chews.
The strong alkaline treatment of the liming causes the skin to swell up. When liming , the liming chemicals are removed from the skin, the pH value is largely neutralized and the skin retains its natural state of swelling. This allows the subsequent chemicals and tannins to penetrate the skin.
If you want to make a soft leather, the so-called nakedness is stained with enzymes. Raw materials with a lot of natural fat are given a special degreasing with surfactants.
The tanning
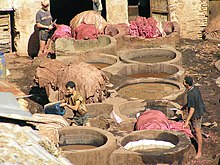
The work described so far has chemically and mechanically changed the skin, but it is still present as native protein with all its disadvantageous properties. This is why tanning now follows . The tanning process basically consists of three phases: depletion of the collagen, penetration and penetration of the tanning extract, binding and fixing to the skin fiber.
It is only through the action of the tanning agents that the proteins are fixed and crosslinked and converted into leather. This takes place via ionic bonds in the case of the sparingly soluble mineral salts ( complex bond ) or via covalent bonds in all other processes. In addition, there are also hydrogen bonds and van der Waals forces for further stabilization. In addition to binding, tanning agents are stored in excess between the collagen fibers.
The different types of tanning agents require different processes, see below: Tanning processes and tanning agents .
Different tannings are often combined to give the leather the desired properties. Exotic tanning processes such as smoke tanning are mostly based on the action of several tannins.
After tanning, mechanical dewatering (wilting) follows . The leather is then brought to a uniform thickness using folding machines. With this thickness regulation , shavings are removed from the leather , similar to an electric plane .
Wet finishing
During wet finishing, the final leather properties are determined, such as softness, color, body, structure, elasticity and water absorption.
In principle, all groups of tanning agents can be used for retanning. Synthetic tanning agents, vegetable tanning agents and resin and polymer tanning agents are of particular importance, as these have a particularly beneficial effect on the fullness and structure of the leather.
During the neutralization , the inherent charge of the leather is neutralized in order to allow a deeper diffusion of the anionic dyes and fatliquors often used in chrome tanning.
The coloring is done with dyes that form a chemical bond with the leather fiber. In addition to their good dyeing properties (e.g. absorption behavior on the leather, combinability, wide range of colors) and fastness properties, modern dyes are notable for their low environmental impact.
The natural leather color depends on the tanning agent used. Chrome tanning gives a light, gray-green inherent color, vegetable leather can be yellow-brown - red-brown. Aluminum salts and synthetic tanning agents produce white to light beige leather. Glutaraldehyde and fatty tanning agents color the leather yellowish.
Not all types of leather have to be colored over the entire cross-section. Some types of leather (for example chamois leather ) are only dyed superficially during dry finishing.
The greasing causes a better softness and suppleness. The fatliquoring agents cover the leather fibers with a thin film of fat. As a result, the fibers do not stick together as strongly during drying and can move more easily against each other. Fatliquors bind to the leather fiber to a greater or lesser extent, but do not cause crosslinking like fat tanning agents.
By using water repellants , leather can be made dirt-repellent and water-repellent to waterproof.
In vegetable tanning, wet finishing has less influence on the properties of the leather. The leather properties of vegetable leather are mainly dependent on the selection of the tanning agents and the way the tanning is carried out. The main tasks are fixing the tanning agent, bleaching or dyeing and fatliquoring.
Drying, mechanical processing
Prior to the actual drying, the leathers are in stretching out stretched, smoothed and partially dehydrated.
The actual drying takes place by hanging, stretching on frames or in a vacuum dryer. During vacuum drying, the leathers are placed on a heated steel plate. Then an airtight lid is placed over it and a negative pressure is created inside. Due to the negative pressure, the water evaporates at lower temperatures that are gentler on the leather. The water vapor can then be pumped out.
Some leathers are then rehydrated to a water content of about 20 percent (Stoll humidity) and by mechanical processing (herein fully dried (8 to 12 percent water content), cleats or Millen ) made soft and supple. In some modern tanning processes, the leather is only dried to the point where it is damp and then processed further.
After staking or milling, the leathers are dried to a final water content of around 12 to 15 percent.
Dry dressing
The leather surface is treated in the dry finishing. In addition to the final color design, the surface feel, the structure, the gloss and the mechanical and chemical resistance of the surface are significantly influenced. Superficial leather defects can also be compensated for by dry dressing.
In Raul springs such as suede , nubuck or Hunting , the surface is ground, dust and dirt with non-film-forming chemicals and water repellent.
For smooth leathers like Nappa, box or sleek leather special coatings can be applied. In addition to various binders, the paints contain the usual paint additives that determine the gloss and surface feel, and possibly also pigments and / or dyes. If the finishes contain pigments, they have an opaque effect and are characterized by high resistance. If it contains dyes or no coloring substances, the result is transparent finishing films that clearly reveal the natural structures of the leather. One then speaks of an aniline dressing. Most of the finishing products are water-thinnable one or two-component systems based on polyurethane , polyacrylate or polybutadiene . In addition, polyamide , casein , cellulose esters and cellulose ethers are also used as binders. After drying and hardening, water-insoluble, more or less stable coatings are created. Only a few types of leather, such as patent leather, require the use of coating agents that can only be diluted with solvents.
It is applied by pouring, high-pressure spraying, low-pressure spraying, airless, airmix or by roller coaters in several work steps. More or less thin foils can also be ironed onto the leather for surface finishing.
The individual layers are compressed by ironing, embossing or polishing. A method that is seldom used today is shining. A glass or agate cylinder is quickly pulled over the surface at high pressure. This results in very shiny surfaces, which, however, clearly reveal the natural structure of the leather. Polishing with stone or cloth rollers produces a similar, but not so strong smoothing effect. When ironing, the surface structure is leveled and when embossing the leather is given a new surface structure. Temperatures of up to 160 ° C and pressures of up to 200 bar are used.
The thicker this coating, the more uniform, hard-wearing and easy to care for the leather surface. However, as the finishing thickness increases, the leather usually loses its natural character. A high-quality finish gives the leather an even, resistant surface with the most natural look and feel possible. Leather is therefore only dressed as much as is necessary to meet the requirements. Due to the high demands in the automotive sector, car leather is usually heavily dressed, whereas expensive shoe or saddle leather is rarely dressed, and perhaps not at all.
From a dry layer thickness of 150 micrometers, the material must be designated as coated leather material and may no longer be marketed as leather.
Tanning processes and tanning agents
Vegetable tanning
Tannins: tannins in leaves, bark, woods and fruits
In the first half of the 20th century, vegetable tanning (vegetable tanning, tanning , red tanning) was the most common type of tanning, today it only plays a minor role. For example, quebracho , chestnut or oak wood , parts of the mimosa and sumac plants and other wood or bark tannins were used to extract the gerberas . From this use the Lohwälder originated. The vegetable tanning agents are ground in a tan mill and leached with water. The brew used is also called broth or extract.
The nature of vegetable tanning agents requires careful pre-tanning for the first stabilization of the skin's fiber structure. In the past, and to a very small extent still today, this stabilization was carried out by tanning with less concentrated, already emaciated tanning solutions (broths) in several steps in a “color cycle”. Only then was it tanned with ground tan and concentrated broths in tanning pits. This tanning process can take up to twelve months and is known as "old pit tanning".
In modern vegetable tanning, the pelts are pre-tanned with synthetic tanning agents or aldehydes and tanned in rotating tanning barrels with concentrated tanning liquors. The tanning process can be shortened to a few days.
Lately may from extracts of olive leaves (olive leather) and rhubarb roots (rhubarb leather) natural tannin are produced.
Tanning with mineral salts
Tanning agents: chromium, aluminum, zirconium or iron salts
Today tanning with mineral salts, especially tanning with chromium III salts , is the most important tanning method. Aluminum salts - mainly alums - and zirconium salts are mainly used in the "white tanning" of fur skins. All mineral tanning agents require a “pimple” as pre-treatment. The pimple consists of acids (usually sulfuric acid or formic acid ) and neutral salt ( sodium chloride or sodium sulfate ). By acidifying the skin, the mineral tanning agents can completely penetrate the skin. The tanning agents are then fixed in the leather by gradually adding lye (basifying). It is carried out in rotating tanning barrels. The tanning is done in 10 to 15 hours. To complete the leather properties, however, neutralization, retanning, dyeing and fatliquoring are necessary.
Fat tanning
Tannins: fish and sea animal oils (trane) or fats of the brain
In fat tanning (chamois tanning), special oils with a tanning effect ( Trane ) are drummed into the hides. If the skins are permeated with tanning agent, the oils oxidize and develop their tanning effect. After drying, the excess tannins are washed out and the leather is dried again. A special retanning is not necessary.
Tanning with aldehyde tanning agents
Tannins: formerly formaldehyde , today mainly glutaraldehyde
Aldehyde tanning agents are mostly used in combination with synthetic tanning agents or as pre-tanning agents for vegetable tanning or fat tanning. The workflow is similar to that of mineral tanning agents with pimples - penetration - basification for fixation. Today most chrome-free car seat leathers are made with aldehyde tanning agents. The so-called "medical tanning", which is often used for lambskins, is also an aldehyde tanning. The tanning agent gives the “medicinal lambskins” their typical yellowish color.
Tanning with synthetic tanning agents
Tanning agents: resin tanning agents , polymer tanning agents , polyphosphates , paraffin sulfochloride
Synthetic tanning agents (syntans) are also rarely used as sole tanning agents. Their tanning behavior is similar to that of vegetable tanning agents. They are mainly used for retanning chrome leather and as pre-tanning agents in vegetable tanning.
Special tanning process
- Glacé tanning: combination of aluminum salts with salt, egg and flour.
- Shrink tanning: Tanning with special tanning agents that cause the hides to contract (shrink). The name gives the result, not the method.
- Hungarian white tanning: tanning with aluminum salts and special fatliquoring.
- Two bath chrome tanning: Was used in the early days of chrome tanning. Chromium VI salts were worked into the skin and then converted into tannable chromium III salts by reduction.
environment
Due to the use of toxic substances, the tannery has always been associated with risks to the environment and health, the environmentally harmful tannins were drained into rivers without further treatment, and some of them seeped into the ground. Today, problems arise primarily with the chromium processes in third world and emerging countries, as there are often inadequate environmental protection measures. Such cases occur time and again, especially in densely populated India. The two places Ranippettai (India) and Hazaribagh (district of Dhaka, Bangladesh) were therefore on the list of the ten most polluted places in the world, which has been published by the American Blacksmith Institute since 2006 .
Apprenticeships
- The profession of tanner is now called, in accordance with the German vocational training law, specialist in leather production and tanning technology .
Museums
Germany

- Annweiler , museum under the Trifels with tannery workshop
- Calw , tannery museum
- Dippoldiswalde , Tanner Museum
- Doberlug-Kirchhain , white tanner museum
- Enger , Enger tannery museum
- Grefrath , Bremer tannery in the Lower Rhine open-air museum
- Hirschberg , Museum of Tannery and City History
- Mülheim an der Ruhr , leather and tanner museum
- Offenbach am Main , German Leather Museum
- Ohrdruf , old tannery
- Schiltach , Schüttesägemuseum
- Weida , technical monument tannery Franke
Other countries
- Malmo , Sweden, Tannery Museum
literature
- Gerhard E. Moog: The tanner. Leather making manual. Ulmer, Stuttgart 2005, ISBN 3-8001-1228-0 .
- Helmut Ottiger, Ursula Reeb: Tanning . Leather and hides. 2nd edition, Ulmer, Stuttgart 2004, ISBN 3-8001-4651-7 .
- Anthony D. Covington: Tanning Chemistry. The Science of Leather. Royal Society of Chemistry, Cambridge 2009, ISBN 978-0-85404-170-1 .
- Morris Charles Lamb, Ludwig Jablonski: Leather dyeing and finishing. Julius Springer, Berlin 1912.
- Emanuel Stickelberger : Attempting a History of the Tannery. 1915.
- F. Stather: Tanning chemistry and technology. Akademie Verlag Berlin, 1967.
- K. Pauligk, R. Hagen: Leather production. VEB Fachbuchverlag Leipzig 1987, ISBN 3-343-00272-0 .
- Hans Herfeld (ed.): Library of leather. Volume 1–11, Umschau Verlag, Frankfurt am Main, ISBN 3-524-82000-X .
- E. Heidemann at al .: Fundamentals of Leather Manufacture. Eduard Roether KG, Darmstadt 1993 (English), ISBN 3-7929-0206-0 .
- G. Reich: From Collagen to leather - the theoretical background. BASF Service Center, Media and Communications, Ludwigshafen, Germany 2007 (English).
Movie
- Andreas Geiger: How to tan and color a hide , SWR television - craftsmanship! from January 10, 2019 (YouTube)
Web links
- Enger, Gerbermuseum ( Memento from October 8, 2007 in the Internet Archive )
- Leather media
- Dippoldiswalde, Tanner Museum
- Doberlug-Kirchhain, white tanner museum
- Frickingen-Leustetten, Gerbermuseum Zur Lohmühle
- Mülheim an der Ruhr, leather and tanner museum
- Wittislingen, Historic Lohmühle
Individual evidence
- Jump up ↑ Marie Soressi, Shannon P. McPherron, Michel Lenoir, Tamara Dogandži, Paul Goldberg, Zenobia Jacobs, Yolaine Maigrot, Naomi L. Martisius, Christopher E. Miller, William Rendu, Michael Richards, Matthew M. Skinner, Teresa E. Steele, Sahra Talamo, Jean-Pierre Texier: Neandertals made the first specialized bone tools in Europe . In: PNAS , Volume 110, No. 35, pp. 14186-14190, doi: 10.1073 / pnas.1302730110 ( PDF ).
- ↑ Bruno Bucher: The old guild and traffic regulations of the city of Krakow. Gerold, Vienna 1889, p. 17 plate 14 .
- ↑ Bernhard Trommer: The collagen matrix of archaeological finds compared to artificially aged leather samples from historical tanning processes . Freiberg (Saxony), Techn. Univ. Bergakad., Diss. 2005 ( d-nb.info ). , Pp. 68f., On the basic chemistry and the history of the discovery of the phenomenon.
- ^ Genealogy of the training to become a tanner , website of the BiBB, accessed on February 13, 2014.
- ↑ Olive leather on leder-info.de, accessed on April 13, 2017.
- ↑ Rhubarb leather on leder-info.de, accessed on April 13, 2017.
- ^ Sascha Peters: Materialrevolution II. De Gruyter, 2014, ISBN 978-3-03821-000-9 , p. 83.
- ↑ Jörg Zimpel: Industrial and commercial wastewater discharges into public wastewater systems: Requirements and problem solutions. expert-Verlag, 1997, ISBN 3-8169-1421-7 , p. 195.
- ↑ Top Ten Threats 2013 of the Blacksmith Institute (English, Pdf file). Retrieved April 7, 2015.