Forge
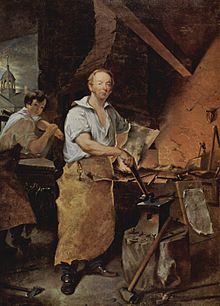
Forging is the pressure forming of metals or alloys between two tools while locally changing the cross-sectional shape. In artisanal forging, the blacksmith mainly uses hammer and anvil as tools . Dies are also used in industry. There are numerous definitions of forging. Sometimes the increased temperature of the workpieces is mentioned, sometimes not. Cold forged workpieces have higher strengths. In industrial production technology , forging is usually understood to mean free-forming (open- die forging with tools that do not contain the shape of the workpieces) and drop forging (with tools that contain the shape of the workpieces), and extrusion is sometimes also included. Forging is sometimes used synonymously for forming . In the craft sector, forging is also understood to mean heat treatment , splitting , punching and fire welding , i.e. everything that a blacksmith does to produce finished workpieces.
Advantages are lower material loss in contrast to machining and the targeted change in the structure and thus higher strength . The disadvantage is the lower accuracy compared to machining processes .
Manual forging ( open die forging ) is one of the oldest crafts . Here the blacksmith has to freely work out the shape of his workpiece on the anvil or, today, on the air hammer , which requires empathy and above all experience. The blacksmith (also metalsmith ) works with forging hammer , anvil and coal - or gas Esse .
The industrial forging provides components ago for the mechanical engineering and the automotive, aerospace and shipbuilding. Industrial forging is an important branch of the economy in Germany . In 2006 the industrial production volume in Germany was 2.75 million tons, which corresponds to at least 1.8 billion formed parts. In 2008 the industrial production volume in Germany amounted to 3 million tons, which corresponds to 2 billion formed parts.
history

The metals gold , silver and copper were probably first worked by humans . These three are in the nature solid (metallic) before - Copper however rare - and can in the cold state to plates or tools cold formed and are thus processed. So far, the oldest finds of copper plates for jewelry date from the 8th millennium BC. From Anatolia . The inhabitants of today's Afghanistan are said to have existed as early as 6000 BC. Have worked and processed metals. From about the same time the first evidence derived by smelting produced copper hatchets and chisels in today's Serbia ( Pločnik ) whose blades cold forged and thus superficially solidified were.
Finds in Mesopotamia , Egypt and India ( Indus culture ) have also shown that forging was probably carried out there in a warm state over 5000 years ago. In Central Europe, the famous Nebra Sky Disc around 4000 years ago is an important testimony to the art of blacksmithing , the manufacture of which the blacksmiths of the time had to have had extensive material experience .
According to historical research, the invention of hardenable iron (steel) was first made around 1400 BC. The Hittites . Already in the pre-Roman Iron Age found anvils of bronze or iron use. Due to their rare occurrence in solid form and the complex extraction from alternative ores as well as their good properties compared to conventional materials, these and other metals had a high material and cultural value. They were coveted commodities, cult objects and status symbols .
Forging has found its way into art and culture for all historical peoples :
- in mythology : (e.g. in the Greek saga the god “ Hephaistos ” and his helpers the “ Cyclops ” or “ Pythagoras in the forge ”, in Roman mythology “ Vulcanus ”, in Germanic “ Wieland der Blacksmith ", from the Hebrew Bible the blacksmith" Tubal-Cain "or the miracle smith " Ilmarinen "in Kalevala )
- in proverbs and idioms : ( "you have to forge the iron as long as it is" warm " ... " make plans " ... " drive someone to white heat " ... " have two irons in the fire " ... " everyone is a smith of his luck " )
- in literature: (in detail in Karl Simrock's Amelungenlied )
- in painting: ( Adolph Menzel Die Gesenkschmiede , Hans Leu the Elder Miracle of St. Eligius )
- in music: (in Richard Wagner's Der Ring des Nibelungen )
In his work Blacksmiths and Alchemists, Mircea Eliade examines the ideas and customs that were associated with mining, the work of metallurgists and blacksmiths in primeval times.
As global technology leaders, the German forges and forging companies supply the key automotive industry with around two thirds of production and mechanical engineering with a further 20 percent. In addition, there are aerospace technology , the energy sector, medical technology and shipbuilding . In the field of industrial forging, around 250 mostly medium-sized companies with over 31,000 employees are active in Germany. The industry's turnover in 2006 was around 7.8 billion euros.
- see also → blacksmith
- see also → blacksmith in culture
Forgeable materials
With a few exceptions, all metals and metal alloys are suitable for forging . The type for the most economical use can be selected from over 2500 types of steel . One speaks of forging only when the deformation takes place above room temperature, i.e. the workpiece is heated or the workpiece is heated considerably by the deformation.
Reshaping
In forging, deformation usually takes place at higher temperatures than at the service temperature with a change in the metal structure or with high pressure even at normal temperature. The processing temperature is either above the recrystallization temperature (hot forming) or below the recrystallization temperature (cold forming).
The process of forging also includes the casting or rolling of the blank , hardening and tempering, and grinding . Compared to casting , the material remains in a solid aggregate state and is processed with a hammer and anvil or with machines such as air hammers and presses.
Hot, warm, cold forming and thixo forging
Depending on the forming temperature, one differentiates:
-
Hot forming when forging steel:
- The working temperature is above the recrystallization temperature, between 950 and 1250 ° C
- Great formability of the materials
- Low forming forces
- No change in strength on the formed workpiece
-
Warm forging when forging steel:
- Working temperature for steel is 750–950 ° C
- No or little scaling on the surface
- Lower forming forces than with cold forming
- Tighter dimensional tolerances than with hot forming
- Restricted formability or higher forces required
-
Cold forming (in a narrower sense, cold forming is not forging) of steel:
- Working temperature is room temperature, own heating up to 150 ° C by the forming energy
- Close dimensional tolerances can be achieved
- No scaling of the surface
- Increase in strength and decrease in elongation through work hardening
-
Thixo forging :
- The working temperature lies between the solidus and liquidus temperature of the respective steel alloy and thus well above the hot forging temperature
- Formability similar to casting
- Low forming forces
In hot forging , the semi-finished product to be forged is heated in a furnace to temperatures between 950 ° C and 1250 ° C and then forged (also: formed) by the pressure of a hammer blow or the pressure between two die halves. In contrast to embossing , the entire material cross-section is plasticized. At the high forging temperatures, steel changes into a different crystal structure and becomes softer. The deformation changes the structure and the mechanical properties of the material significantly.
For industrial processes, the metals steel , iron and their alloys are generally hot forged, with each metal requiring a different forming temperature. Brass , bronze , copper , precious metals and their alloys , on the other hand, are usually cold formed.
The method of forming by rolling emerged from forging. Seamlessly rolled rings are typical products of massive forging . Ring rolling enables seamless rings with square and rectangular cross-sections as well as rings profiled on the inside and / or outside. The largest available diameter in 2010 was 8.0 meters.
Hot forming when forging aluminum
- Hot forming when forging aluminum:
- Forming temperatures of wrought aluminum alloys are between 350 and 550 ° C
- Forming temperatures above 550 ° C are too close to the solidus temperature of the alloys and, in conjunction with locally different degrees of deformation, lead to an unfavorable workpiece surface topography and possibly to local melting and wrinkling
- Forming temperatures below 350 ° C reduce the formability of the material by increasing the flow stress and can lead to incompletely formed tool engravings, possible crack formation on the workpiece surface and an increase in the forming force and thus the die load
Due to the low temperature range during forming and the high thermal conductivity of aluminum, aluminum forging can only be carried out in a very limited process window. The tool temperature control is therefore of great importance in aluminum forging. In order to ensure good forming conditions, it is necessary to ensure that the temperature distribution in the entire component is as homogeneous as possible. For example, by optimizing the preform geometries, the local degrees of deformation can be specifically influenced, thus reducing local heating and finally making the temperature distribution more homogeneous.
Use of aluminum forgings
High-strength aluminum alloys achieve the strengths of medium-sized steels with significant weight advantages. For this reason, aluminum forgings are used in aviation, vehicle construction and in many other areas of mechanical engineering, especially in those applications where a high level of security against failure due to misuse, shock loads and vibrating loads must be guaranteed. In the automotive sector, these include chassis, steering and braking parts. Frequently used alloys are AlSi1MgMn ( EN AW-6082 ) and AlZnMgCu1,5 ( EN AW-7075 ). About 80% of all aluminum forged parts are made from the AlSi1MgMn alloy. The high-strength alloy AlZnMgCu1.5 (EN AW-7075) is mainly used in aviation.
Shaping
Tools for open die forging
Coal-fired forge:
The forge with coal fire has been fired for centuries with a mixture of hard coal and coke or with charcoal . The hard coal contains a lot of sulfur which penetrates the steel during the heating process and reduces the quality of the steel. That is why coke is added, it contains almost no sulfur. Charcoal is sulfur-free but lighter and burns much faster.
Gas stove:
A gas chimney produces hardly any exhaust gases, apart from carbon dioxide and water, so there is no contamination (e.g. from sulfur).
Anvil:
Anvils are either cast or forged and most of the time the anvil track (the middle part) is hardened. There are many different types of anvils, each tailored to the work (e.g. horseshoes, tools, or blacksmithing, etc.) performed on the anvil. The size of the anvil is also matched to the type of use. If the anvil weight is misinterpreted, the anvil can begin to bounce or vibrate, which has an adverse effect on the forging process.
Vice:
Most of the vices in blacksmiths' shops are bottle vices. The guide of the movable jaws is connected by a fixed pivot point. This means that the jaws are not parallel to one another when they are open. This has a negative effect because the workpiece cannot be clamped over the entire jaw surface. However, the jaws are forged or made of cast steel, which makes them many times more robust and thus less sensitive to impacts. They are also provided with curves and edges to make bending work easier.
Hammers:
Different hammers are used for forging depending on the situation .
Auxiliary hammers are split hammers, hole hammers or blow hammers. They are used to forge holes in the workpiece or to split it. A splitting hammer has a rounded cutting edge, which ensures better straight guidance than a straight cutting edge. Blowing hammers are used to punch a hole in an elliptical, rectangular, flat, or circular shape.
The hammers are operated by a second blacksmith and weigh between 5 and 15 kilograms. They are divided into two main types of cross hammer and sledgehammer. Cross hammer hammers have their fins in the direction of the hammer handle. Sledge hammers have the fin across the hammer handle.
Pliers:
The pliers are mostly self-forged; There is a suitable or specially made pliers for every job. The area of the pliers that holds the workpiece is called the mouth, the pivot point is called the eye and the handles are called the legs. The ratio of mouth to leg is made about 1: 6, so that the clamping force is guaranteed.
Manual open die forging
Art blacksmiths use open-die forging primarily in restoration, in the preservation of monuments and in the design of individual items such as canopies, grilles , gates , railings , fountains , etc. or lights, cloakrooms , candlesticks.
The following forging processes are used in open die forging on the anvil:
- Separate:
-
Forming :
- Points (Describes the forging of round or square rods into an equally fine point. Examples of the history are forged arrowheads , chain armor or even hand-forged foliage in ornamental grids and much more.)
- Widths
- Drop
- Upsetting
- stretch
- anticlastic forging (especially for jewelry)
- Finishing
- To bend
- Twisting
Both the blacksmith and the farrier heat their forgings in the forge fire. The workpiece absorbs heat , they say it has heat . If “ one heat ” is not enough, it gets a “second heat” .
While the UK coke-fueled fire is common to almost exclusively used in continental Europe, with a special fat coal (called "fat nut") charged charcoal fire and, more recently, gas-fired, sometimes filled with ceramic chips or volcanic rock fire. However, the reserves for good forged coal worldwide are exhausted or unprofitable for the usual large-scale industrial mining; The coal that is mostly available today has a far too high proportion of volatile components (up to over 30%).
Industrial open die forging
In open die forging, the forging is formed between non-shape-related tools, the saddles , by a press or a hammer (air hammer). The material can move into the areas not enclosed by the tools.
Particularly very large individual pieces are processed using industrial open die forging; for example crankshafts for marine diesel engines or generator rotors for turbo drives. Piece weights of up to 250 t are possible. Large forging manufacturers in Germany include Buderus-Edelstahl , Schmiedewerke Gröditz and Saarschmiede . The latter is Europe's largest forge.
The heating of the large forgings takes place in the same way as the temperature-controlled cooling in fuel- heated chamber or shuttle kilns .
Correspondingly large grippers, so-called forge manipulators, are used to move the workpiece .
Drop forging
Drop forging differs from open die forging in that the forging is almost completely enclosed by the closed tool, the die . In the die from the mold maker introduced negative mold determines the shape of the finished forging. Drop forging is mainly used to manufacture safety-relevant parts such as smaller crankshafts, connecting rods , gears or tie rod ends, steering parts , gear parts and wear parts for construction machinery. The forging gives the material a favorable fiber flow. This reduces the crack sensitivity and increases component safety. The disadvantage of closed-die forging is that a minimum number of similar forgings has to be produced, since the costs for a die are high. The dies are manufactured by means of engraving or milling and / or die sinking according to original shapes in an oil bath.
Precision forging
If workpieces that are almost ready for installation are produced by forging , it is called precision forging . It is irrelevant which forging process is used, only the accuracy achieved defines a forging process as precision forging. A tolerance of IT8 to IT6 (better than ± 0.1 mm) is usually assumed here . Precision forging is widely used in industry. Mainly parts in internal combustion engines (e.g. cams for "built" camshafts for valve control) as well as on the drive train of motor vehicles - e.g. B. Transmission gears - are made this way.
One of the methods of precision forging is flashless forging. In contrast to forging with burrs, this process requires no or only very little excess material (in the form of burr) to fill the mold. By means of burr-free forging or precision forging, components can therefore be produced with a very high level of accuracy and a high surface quality.
Thixo forging
Here the material is in a special "semi-liquid" state that is known as thixotropic . This results in a very high formability, low machining forces and high accuracy.
Long forging
Through long forging long workpieces with simple geometries (eg. As gun barrels) made with non-dimensionally bonded tools. This process is an automated open-die forging with particular accuracy of the workpieces. Forging takes place in longitudinal forging machines, in which hammers attached perpendicular to the workpiece work against each other in pairs. The feed and the adjustment of the hammers are program-controlled.
Multi-directional forging
Multidirectional forging is the forming of a workpiece in different directions in one forming step. The multi-directional forming is achieved through design measures on the tool: The vertical movement of the press ram and thus the forming force is deflected in horizontal directions via wedges.
Forging machines

A distinction is made between open- die , drop forging hammers and forging presses.
Hammers are suitable for large workpiece masses. Depending on the type, hammers are suitable for small to large forgings. The unit weights can range from around 100 grams to 1,000 kilograms. High forming speeds occur in forging hammers. The penetration depth of the deformation is limited because of the friction losses in the workpiece. With forging presses, the force is applied more slowly, which means that the flow process can penetrate deeper into the material. This is particularly important for very large workpieces. The working capacity of closed-die forging hammers is given in kJ and the working force of presses in kN.
A distinction is made between the following types of forging machines:
- work-related
- Machine hammer for open die forging, e.g. B. air hammer, spring hammer, drop hammer
- Drop forging hammer
- Screw presses
- bound away
- force-bound
- Hydraulic presses (slow force build-up)
literature
- Johannes Grossewinkelmann: Forging - Development of a trade from handicraft to factory. (= Museum educational work materials. Booklet 2). Rheinland-Verlag, Cologne 1989, ISBN 3-7927-1065-X .
- Stahl-Informations-Zentrum (Ed.): Forged steel - always in shape . Steel Information Center, Düsseldorf 2008. (PDF; 951 kB)
- Werner W. Adlof: Forged parts - design, application, examples. Hagen 1994/1995, ISBN 3-928726-12-9 .
- Axel Specker: Investigations into burr-free drop forging of crankshafts . PZH-Verlag, reports from the IPH 04/2009, ISBN 978-3-941416-25-3 .
- Industry association for massive forming : Lightweight construction through massive forming. Massive Forming Information Series, March 2007, ISBN 978-3-928726-20-7 .
Web links
- Process chain for the manufacture of precision forged high-performance components. Institute for Materials Science at Leibniz University Hannover
Individual evidence
- ↑ Industry information 2008 , Industrieverband Massivumformung , accessed on June 3, 2013.
- ↑ Angelika Franz: Archaeologists are puzzling over 7000 year old copper finds . In: Spiegel Online . December 27, 2010, accessed October 3, 2013.
- ↑ Manufacturing technique of the sky disc and enclosed finds (swords) . State Office for Monument Preservation and Archeology Saxony-Anhalt / State Museum for Prehistory. Retrieved October 3, 2013.
- ↑ Friedrich Cornelius : Geistesgeschichte der Frühzeit , Volume 1, Verlag Brill-Archive, 1960, p. 132.
- ↑ E. Doege, B.-A. Behrens: Handbook of Forming Technology: Basics, Technologies, Machines. Springer Verlag, 2010, p. 671f.
- ↑ M. Stonis: Multi-directional forging of flat long aluminum parts. In: B.-A. Behrens, P. Nyhuis, L. Overmeyer (Eds.): Reports from the IPH. Volume 01/2011, PZH Produktionstechnisches Zentrum GmbH, Garbsen 2011.
- ↑ J. Richter, M. Stonis: Quality improvement in aluminum forging . In: Aluminum Practice. Giesel Verlag, 20th year, No. 6/15, 2015, p. 20.
- ^ Karl Gissing: Forging All Techniques . Graz 2016.
- ↑ Burr-free forging: potentials, development trends, implementation. Retrieved November 25, 2019 .
- ^ Günter Spur , Dieter Schmoeckel , Theodor Stöferle: Handbook of Manufacturing Technology. Volume 2: Forming and cutting. Hanser-Verlag, Munich 1984, ISBN 3-446-13805-6 , p. 620 f.
- ↑ Behrens, Stonis, Rüther, Blohm: Flash reduced forging of complicated high duty parts using preforming operations. IPH - Institute for Integrated Production Hannover gGmbH, Hannover 2014.