Two-stroke engine

A two-stroke engine is a reciprocating piston engine that generates mechanical power from the combustion of fuel . Two cycles result in one cycle cycle (360 ° crankshaft rotation). Like a four-stroke engine , it can work according to the gasoline or diesel cycle .
The colloquial term “two-stroke” describes a valveless gasoline engine with mixed lubrication and spark plug that works according to the two-stroke principle; since this variant is simple, inexpensive and light, it is the most common. Large two-stroke diesel engines are among the heat engines with the highest degree of efficiency .
The two-stroke engine is still widely used today in outboard motors and portable devices such as chain saws , brushcutters , lawn trimmers , leaf vacuums and leaf blowers , which are supposed to be light, powerful and require engine lubrication regardless of the position . Two-stroke large diesel engines are used as ship engines (" ship diesel ", for example Wärtsilä RT-flex96C ) or in power plants as a drive for electric generators .
Previously, two-stroke engines were used in motorcycles , mopeds , scooters and the majority of karts . In passenger cars there were two-stroke engines from DKW , Aero , Saab , IFA ( Trabant , Wartburg , Barkas ), Lloyd , Subaru , Suzuki , Mitsubishi and scooter mobiles . There were also large two-stroke diesel engines for diesel locomotives , trucks (e.g. Krupp Titan ), airplanes ( e.g. Junkers Jumo 223 ), ships and boats.
History of the two-stroke engine
prehistory
The first two-stroke engines, now called compressionless, worked according to a different principle and are only called that because they ignited with every revolution of the crankshaft - just like the modern compression two-stroke. In the first cycle, it was sucked in and ignited without compression; in the second cycle, the burned gas mixture was expelled. The gas exchange was controlled by slide valves. Attempts by Jean Joseph Étienne Lenoir , Siegfried Marcus and others to use them for mobile purposes (between 1860 and 1870) failed, among other things, because of the poor power-to-weight ratio of the engines. Carl Benz's “New Year's Eve Engine” from 1879 also worked according to this principle. The "stationary" two-stroke engine System Benz was built by the Mannheim gas engine factory from 1881 and thousands of copies were produced.
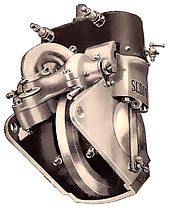
Beginnings and technical development
Dugald Clerk is considered to be the inventor of the two-stroke engine. In order to circumvent Nicolaus Otto's patent , in 1878 he developed a motor with a separate flushing pump that only required one crankshaft rotation per work cycle. This engine principle was first used in 1887 in the Petrol Cycle by Edward Butler (1862–1940) to drive a motor vehicle. In 1891, Julius Söhnlein received a patent on crankcase flushing, in which the underside of the working piston acted as a flushing pump piston. Like modern two-stroke engines, it had inlet and outlet slots and an overflow duct. At the same time, Joseph Day developed a similar principle with a baffle on the piston, for which he applied for a patent. In 1904 Alfred Angas Scott successfully designed a two-cylinder two-stroke engine, and in 1908 he built a further developed version into a motorcycle. In 1909 he founded the Scott Motor Cycle Company , which manufactured two-stroke motorcycles until 1966. Before the First World War, Hugo Ruppe further developed the two-stroke engine; his patents went to DKW , which manufactured the two-stroke engine in large numbers. In 1928 the Austrian manufacturer Titan developed the membrane control. The patented reverse flush by Adolf Schnürle , which replaced the cross-flow flush and the two-stroke piston piston from 1932, is considered a major development step. Daniel Zimmermann developed the rotary knife gate valve in 1952 and Yamaha developed the exhaust control in 1978 .
Advantages and disadvantages of the procedure
Up until the 1950s, the two-stroke engine had great development potential for cars and trucks. The two-stroke engine had particular advantages in many areas:
- Higher maximum torque , therefore potentially greater acceleration capacity in vehicles than four-stroke engines with the same displacement
- More even torque output , since twice the number of ignitions takes place per revolution compared to the four-stroke engine ( "3 = 6" advertising by DKW )
- In the simplest case, only three moving parts : piston , connecting rod and crankshaft , thereby
- low-maintenance and reliable operation. The valve control of historic four-stroke engines was extremely maintenance-intensive and therefore an argument for the two-stroke engine. However, due to constant improvements in valve control, this aspect became less important over time.
- light weight
- no engine oil change required
- Very short warm-up phase , better cold start behavior
- Low nitrogen oxide emissions
- Position-independent use with mixed lubrication , which is particularly advantageous for mobile work equipment
However, it turned out that many of the principle-related disadvantages of this type of engine could not be eliminated. The essential points include:
- Gas change : There is only a short time available around bottom dead center for exhausting the exhaust gas and filling the cylinder with fresh gas . Four-stroke engines, on the other hand, work two working strokes as a piston pump, expel exhaust gas in one stroke and suck in fresh gas in the next stroke. Two-stroke engines need their own flushing fan for this, usually a piston fan. (Blower stands for a device for transporting gases with a negligible pressure gradient.) In small Otto engines, a crankcase flushing is common, in which the piston acts with its underside as a flushing pump. In multi-cylinder engines, it may require gas-tight separation of the individual crank mechanisms. An alternative is flushing with external blowers, which mostly work with rotary lobes (typically as Roots blowers or rotary vane pumps ). The task has to be fulfilled at the start, so that turbochargers , which need hot exhaust gases to drive them, have to be supported by an electrically driven start-up fan.
- Flushing losses occur because exhaust and fresh gas can mix during the gas exchange and so fresh gas could remain in the exhaust or exhaust gas in the cylinder. However, these can be reduced considerably by direct fuel injection. Without direct injection there is a conflict of objectives between residual gas and flushed fresh gas, see also degree of capture . As a result, the fuel consumption of two-stroke gasoline engines is comparatively high, so that only two-stroke engines with a maximum of three cylinders and a displacement of 1.2 liters were used in passenger cars. An exception is the Aero 50 with a four-cylinder two-stroke engine and 2 liter displacement; its fuel consumption is given as 12–16 l / 100 km. The DKW 4 = 8 also had four cylinders, but the largest version had a displacement of 1054 cm³. The V6 two-stroke engine designed by Hans Müller-Andernach did not go into series production and was only retrofitted in some Auto Union F 102s. This engine had a displacement of 1288 cc.
- Loss of stroke : Compression only begins when the piston has closed the inlet and outlet slots. The four-stroke engine can start compression from bottom dead center, if you disregard gas dynamics or special cycles such as Miller or Atkinson .
- Thermal load : Due to the higher number of work cycles and the energy conversion, higher heat flows occur for the cylinder, piston and piston pin , which can be reduced, for example, by cooling or lower power. Piston cooling with spray oil , however, is particularly opposed to crankcase flushing (also: crankcase flushing). If the exhaust gas is blown out through slits, the temperature on the sliding surface of the piston rings and on the lubricating film is higher than with a four-stroke engine. The problem is compounded because significantly more heat has to be dissipated through the piston in a two-stroke engine than in a four-stroke engine.
- Mechanical load : The piston rings in particular are at risk in the area of the inlet slots. Because the piston and bearing are constantly under pressure, maintaining the separating lubricating film is more difficult. In the four-stroke cycle, the direction of pressure on these components changes when they are pushed out and sucked in, so that oil can flow into the gap by itself.
- Oil supply : In the case of crankcase flushing with minimized lubrication, the crankshaft must be stored in deep groove ball bearings instead of plain bearings in order to ensure lubrication reliability. This means that the advantages of plain bearings, which cause less mechanical noise and fail less than ball bearings, are foregone.
- Control times : The control times cannot be changed for control slots.
- Overall height : If the control slots are closed by the piston, a longer piston skirt and a correspondingly long cylinder must be provided. In order to be able to continue using a plunger , the connecting rod must also be made longer. In practice, a four-stroke engine can be made more compact than a two-stroke engine despite the valve control.
- Exhaust gases : Due to the requirement for safe flammability, the mixture quality is worse to control at λ = 1 than with a four-stroke engine. Therefore, the catalytic reduction of pollutants ( CAT ) in the exhaust gas is more difficult. Since the control slots are located in the lubricated cylinder running surface and the oil supply can be less precisely adjusted to the actual requirement with mixed lubrication , two-stroke engines carry more oil with them than four-stroke engines. The result is a high amount of HC in the exhaust gas ( 30 times greater in the Trabant than in a comparable four-stroke engine).
- Smooth running : Even engine running only when under load. In idle the engine is running due to a high proportion of residual gas in the combustion chamber restless. In overrun mode (if no overrun cut-off is installed), irregular ignitions (the so-called slide jerk) often occur. Some two-stroke vehicles are equipped with a freewheel that prevents overrun.
- Braking force : The two-stroke engine develops less engine braking force in overrun mode. In the case of a non-lockable freewheel, the engine braking force cannot be used at all.
Since low consumption and good exhaust gas values are required in many areas of application, the area of application of two-stroke engines has been reduced to a few areas.
The two-stroke process was not able to establish itself successfully in the automotive industry; In the course of the 1950s / 60s, automobile manufacturers such as Saab, Suzuki, Mitsubishi and DKW abandoned the two-stroke process. The two-stroke engine was retained for a particularly long time in the GDR automobile industry ; In 1962 the company still saw itself as a domain of two-stroke engine construction and was full of expectations that the inherent disadvantages of this engine would still be overcome. This did not succeed, and yet the two-stroke engine was retained, so that the Trabant 601 and Barkas B 1000 vehicles built until 1990 were the world's last series-produced passenger cars and trucks with two-stroke engines.
The two-stroke engine had a longer existence in motorcycle construction . Many motorcyclists were not bothered by the noise and exhaust emissions or the uncultivated idling behavior. In motorcycle racing, the two-stroke engine played out its inherent advantages over four-stroke machines. From 1994 legal bans for reasons of air pollution superseded the two-stroke engines.
The two-stroke engine has held up in areas of application in which position independence, simplicity and low weight are important. These include small mobile work equipment, boat engines, jet skis , ultra- light flight engines and small engines (model making). Furthermore, large two-stroke diesel engines are the most efficient prime movers and are used in ships. The only thing that counts there is cost-effectiveness, as exhaust emissions in shipping are hardly regulated by law to this day.
Current developments
Efforts are still being made to cope with the scavenging loss and exhaust gas problem of the two-stroke process in order to make the advantages over four-stroke engines more widely usable again.
Motorcycle manufacturers such as Betamotor , KTM , GasGas or Husqvarna offer two-stroke petrol engines for their modern off-road sports vehicles . At KTM these are now without exception direct injection (reverse flush design). The flushing losses are kept within limits so that the engines become more efficient and cleaner. In addition, the Envirofit International project has existed since 2007 , in which conventional two-stroke engines are converted to orbital direct injection in order to achieve more environmentally friendly emissions. This is achieved by replacing the cylinder head and retrofitting an injection (kit). The aim of this project is to convert the millions of light motorcycles with conventional two-stroke engines that can be found in Asia and the associated environmental problems into more environmentally friendly vehicles. Other examples include BRP Rotax engines, which have become more environmentally friendly thanks to a direct injection system (Ficht FFI), such as the Rotax series, which are also used in snowmobiles of the Ski-Doo series. Tohatsu builds two-stroke engines with the TLDI ( Two Stroke Low Pressure Direct Injection ) system for boats, Yamaha has the so-called HPDI ( High Pressure Direct Injection ) system.
A number of small firms have developed or are in the process of developing functional opposed piston engines to take advantage of their potentially lower fuel consumption. The design of the pivot motor is unusual . With its water-cooled pivot piston and direct injection, it enables flushing losses to be reduced to a minimum and with mixtures of up to 1: 300 compared to conventional piston arrangements (usually 1: 50–1: 100) work.
Working method
Two-stroke engines implement the sequence described below , regardless of type and cycle process; the description begins with the bottom dead center . The processes under the piston in two-stroke engines with crankcase scavenging are shown in italics. Larger two-stroke diesel engines have purge fans for changing gas.
First cycle : compression / suction
- Due to the upward movement of the piston, the gas contained in the cylinder (air or fuel-air mixture) is compressed . The compression increases the temperature and pressure of the gas. If the heat exchange with the environment is left aside, this is isentropic .
- The upward running piston increases the volume in the crankcase, which creates a vacuum in the crankcase. As soon as the intake duct is released from the carburetor into the crankcase, fresh gas flows in.
- Shortly before top dead center, the fuel-air mixture in Otto engines is ignited by a spark plug. It burns so quickly that the piston moves little further during the combustion period, the volume remains almost constant ( isochoric heat supply). In the diesel two-stroke engine, the combustion of the diesel oil that is only then injected takes a little longer; the pressure remains almost the same ( isobaric heat supply). In both cases there is high pressure.
Second cycle : work / precompaction
- The hot gas expands and presses the piston, which runs back. The gas cools down; Heat is converted into mechanical energy.
- The piston moving downwards compresses the fresh gas that is sucked in as soon as the intake duct is closed.
- In the vicinity of the bottom dead center, the outlet opening opens first and then the overflow or inlet channels. The exhaust gas escapes, initially until the pressure has dropped below that in the overflow channels, the rest is flushed out by the incoming fresh gas. Large diesel engines commonly have controlled exhaust valves and intake ports. Small engines are slot-controlled, which means that the piston releases exhaust and intake openings in the cylinder. The fresh gas can be a fuel-air mixture or just air in engines with direct injection .
- When the transfer channels open, the pre-compressed fresh gas can flow from the crankcase into the cylinder.
On the way of the piston to top dead center, the inlet and outlet openings are closed again and the process begins again with the compression. The fresh gas (either mixture or air) must be under pressure for purging. To generate this, either the crankcase and piston underside are used as a pump or an external charging fan is used. Exhaust gas turbochargers (in large diesel engines) are combined with auxiliary fans, as the exhaust gas is insufficient to operate them with sufficient efficiency when starting up or at low loads.
The ideal gasoline or diesel cycle only approximates the process in the engine, because the gas exchanges heat with the environment and combustion and gas exchange take a certain amount of time. The deviations are described by the quality grade .
Technical principles
Flushing

The goal of the rinse, are free in the short time in the inlet and outlet openings to replace the burned mixture, by air (with direct injection , for example, diesel engine ) or the fuel-air mixture (in the gasoline engine with manifold injection or Carburetor ). On the one hand, as little residual gas as possible should remain in the cylinder, but on the other hand as little fresh gas as possible should also be lost through the outlet. There are three types of flushing:
Cross-flow flushing
The outlet and inlet ducts face each other and are both released and closed by the piston. The outlet opens first and closes last. In order to flush the cylinder as well as possible, either the piston is shaped in such a way that it deflects the inlet flow in the direction of the cylinder head ( nose piston ), or the opening of the overflow channel is directed obliquely upwards. This design is only rarely used today because other types of flushing are more effective and less lossy; For example, the last multi-cylinder motorcycle engine with cross-flow flushing was installed in the Silk 700 .
As recently as 2018, there were low-power engines such as lawnmowers and mopeds with this type of flush; however, the 4-stroke engine has largely prevailed there too.
DC purging
In DC-scavenged engines, the outlet and inlet ducts are at opposite ends of the cylinder chamber. The fresh gas pushes the exhaust gas in the same direction from the inlet to the outlet. In opposed piston and double piston engines , only slots a little above the bottom dead center of the individual pistons are used for gas exchange. In cylinders with one piston, slots at bottom dead center are usually used for the inlet and a controlled valve in the cylinder head for the outlet. The outlet can be closed before the inlet, which reduces the scavenging losses and is necessary with supercharged engines.
Reverse flush
In this variant developed by Adolf Schnürle in 1925, two opposite overflow channels open tangentially to the cylinder wall. The exhaust port lies between them, so all three next to each other on one side of the cylinder. The two gas flows from the overflow ducts meet and are deflected on the cylinder wall in the direction of the combustion chamber and there towards the exhaust duct. By the time the gas flow reaches the outlet, the piston has almost closed it. The loss of fresh gas is lower than with cross-flow purging and the piston crown can be made flat. With the first reverse flush there were only two overflow channels, later systems with main and secondary channels were developed, which in the 1980s led to up to eight overflow channels. Reverse scavenging is still used in two-stroke gasoline engines today.
- Examples of steering angles
The overflow and outlet control angles can vary considerably depending on the application. With slot-controlled two-stroke engines, transfer angles are found in the range between 115 ° and 140 ° of crankshaft rotation, and exhaust control angles between 135 ° and 200 °, with the outlet always opening in front of the transfer channels.
Gas dynamics
- Use of the crankcase as a pump ("crankcase flushing")
The crankcase, together with the piston, is used as a pump chamber to generate the overpressure required for flushing. The upward movement of the piston compresses the gas in the combustion chamber and at the same time creates a vacuum in the crankcase, which draws in fresh gas. In the downward movement this is then compressed (pre-compressed). The cylinder inlet is connected to the crankcase via an overflow duct. In the vicinity of the bottom dead center, the piston opens the inlet opening and the fresh gas, which is now under pressure, flows through the overflow channel into the cylinder.
- Response in the inlet and outlet tract
The two-stroke engine is - like, to a lesser extent, the four-stroke engine and, in general and to varying degrees, other heat engines - a resonance system whose power development, however, unlike the 4-stroke engine, is very much dependent on the vibration properties of the gases used ( inertia ). During the exhaust process, the flow of the exhaust gases can be used particularly efficiently through a suitable design of the exhaust system (see the animation above).
As soon as the piston clears the outlet slot, the exhaust gases flow into the exhaust. The flow velocity only decreases in the diffuser . As long as the gas continues to flow unchanged, its inertia creates a pressure gradient in the direction of the exhaust (figuratively: the gas column sucks at the outlet). Contrary to a widespread misconception, the only task of the diffuser is to bring the exhaust gas to a lower speed without the flow being interrupted. A little later, the pressure wave is reflected on the second truncated cone. Here the gas accumulates due to inertia and the resulting wave runs back towards the cylinder outlet. This pushes fresh gas that has been pushed / drawn into the exhaust back into the cylinder. However, this only happens completely at the optimum operating point for which the exhaust system has been calculated. If the engine speed is different, some of the exhaust gases will return to the cylinder, or not all of the fresh gas will be pushed back. However, within a certain speed range these losses are acceptable, since they do not affect consumption, exhaust quality or performance too much. In the case of motor-assisted bicycles and mopeds, however, this is often used to throttle the power by limiting the speed by optimizing the exhaust system for a low speed.
With this type of gas exchange, the fresh gas losses are considerably reduced; Such an exhaust system is called a resonance exhaust . The length and shape of the exhaust in conjunction with the height of the outlet slots determine the speed range that the exhaust supports. With short exhausts and high outlet slots, the time in which the burnt exhaust gas is reflected or sucked out is shorter, and the engine is therefore designed for higher speeds. The opposite is true for long exhausts and flat exhaust slots. In this way, a two-stroke engine can be tuned relatively well to a certain speed range; On the other hand, the flow conditions can be optimally adjusted to a single load point, for example in stationary operation, with correspondingly high efficiencies and good exhaust gas behavior. The resonance frequency can also be influenced to a certain extent by means of a membrane inlet and a vibration chamber at the inlet, but not nearly as much as by the resonance method described.
Since, as a first approximation, there is always atmospheric pressure in the cylinder at the end of the intake process, one can speak of quality control in Otto two-stroke engines. Only the ratio of mixture to residual exhaust gas in the cylinder is varied via the throttle valve of the intake system. The high proportion of exhaust gases in the cylinder in the partial load range leads to poor combustion qualities with a high carbon monoxide (CO) and hydrocarbon content (C m H n ) in the exhaust gas with low nitrogen oxide emissions (NO x ).
The illustrated resonance effect is also used to a lesser extent in four-stroke engines in order to achieve better gas exchange when the valve overlaps .
lubrication
Mixture lubrication
Mixture lubrication is consumption lubrication in which oil is mixed with fuel. As a result, the oil component is also burned during the combustion process. A disadvantage is the carbon oil produced during the combustion process, which is deposited in the work area and in the exhaust system and impairs the performance of the engine. The removal of the deposits in the exhaust system can be done by "burn out" or chemical dissolution. At the beginning of the 1930s the mixing ratio was 1 (oil): 10 (petrol), later this was reduced to 1:15 and 1:18. Until the 1970s, racing motorcycles were driven with a mixing ratio of 1:20, sometimes mixed with castor oil , to prevent piston jamming during overrun. For many years, the ratio 1:25 was common for normal motorcycles or scooters; so also with the first model of the Trabant P 50 . By using high-performance oils, the oil ratio in engines with mixed lubrication has been reduced over the years from 1:33 (e.g. Trabant P 50) to 1:50 (e.g. Trabant 601 ) and 1: 100. Modern chainsaws and other portable power tools are operated with a mixing ratio of 1:50 (2% oil).
Separate lubrication
With separate lubrication, the required lubricating oil is provided separately from the fuel. Scott's first motorcycle , the basic model of the 3 3/4 built in 1908 , already had separate lubrication. In the 3S model developed in 1934 , three oil pumps delivered the fresh oil to the cylinder liners. In 1961 DKW brought a “fresh oil automatic” onto the market for the Auto Union 1000 model ; the oil was pumped from a separate container by a metering pump into the carburetor float chamber and mixed there in a ratio of 1:40. In 1964, Yamaha developed the "Autolube system" for motorcycles, in which the oil was directed into the intake port of the carburetor. At full load , the “Autolube system” achieved a mixing ratio of 1:20, at idle 1: 150.
In 1971 , Suzuki again offered the "real" separate lubrication for series motorcycles with the GT 750 , in which a metering pump delivers the oil directly to the lubrication points (bearings, cylinder walls). The pump conveys the oil depending on the load through the position of the throttle grip, a system that was later also used by Kawasaki and corresponds to the oil sump lubrication of the four-stroke engine .
Circulating oil lubrication
Larger two-stroke engines can be built with a closed lubricating oil circuit, comparable to a four-stroke engine. Typical representatives of such engines are two-stroke diesels for commercial vehicles. You then need to have a supercharger, as the crankcase cannot be used for pre-compression.
Loss lubrication
Large two-stroke engines such as marine diesel engines can be designed as cross-head engines, especially in the case of older designs with loss lubrication . For this purpose, the lubrication points such as the main and connecting rod bearings or crosshead are supplied with lubricant directly via an oil line, which then emerges into the open air next to the bearing and drips off.
Control procedure
Inlet control
Piston edge control
This is by far the most common form, inexpensive and mechanically simple, and is mainly used in small motors. The upper edge of the piston releases the overflow and outlet openings in the cylinder wall near the bottom dead center. The lower edge of the piston releases the inlet into the crankcase near top dead center. The advantage here is the opening and closing of the inlet, the overflow channels (overflows) and the outlet without additional mechanical components.
Rotary valve control
Already in 1911 Alfred Angas Scott developed a water-cooled motor in the 3 3/4 model with rotary valve control. The rotary knife gate valve as we know it today was developed by Daniel Zimmermann in the 1950s, patented in the GDR and used on the Trabant . Here, the inlet into the crankcase is opened and closed through an opening in a rotating disk attached to the crankshaft. The advantage over piston-controlled engines is the possibility of controlling the opening time independently of the closing time (asymmetrically in relation to the crankshaft angle). See also: Slide control in two-stroke engines
Membrane control
The first diaphragm-controlled two-stroke engine was the 350 cm³ engine from the Austrian motorcycle manufacturer Titan from 1928. Engineer Karl Schüber was the designer of the inlet control with a 4-leaf membrane inlet. The diaphragm valve, designed as a tongue valve, was attached to the inlet channel, which opens when there is negative pressure in the crankcase and closes when there is overpressure. The advantage was the automatic adjustment to the flow conditions at all speeds. The reliable working range of this diaphragm valve ended at a maximum speed of 5,000 min −1 .
The weakly resilient and lightweight membrane (also known as the tongue valve) opens at a low negative pressure and closes suddenly when pressure equalization is reached; it prevents blowback and adapts to a wide speed range. A fundamental difference between a control element opened by the negative pressure and a slot released by the working piston is the (relatively) gentle lifting of the membranes or valves compared to the rapid opening to the crank chamber, in which there is already a significant negative pressure. The resulting increased intake noise is not a factor in racing engines, but it does in everyday life.
In 1971, Yamaha redesigned the diaphragm valve by making the diaphragm tongues a roof shape. As a result, a relatively large flow cross-section was achieved. The piston first closes the path leading to the diaphragm, the crankcase pressure drops and suddenly tears open the diaphragm tongues, much further and more effectively, also to fan the desired vibrations. Since the intake channel also serves as a (fifth) overflow channel, the fresh gases flowing upwards create a static negative pressure behind the diaphragm tongues - the faster, the stronger - and suck in an additional quantity of fresh gas, directly from the intake path into the working cylinder.
This principle finally made it possible to equip all series engines with diaphragms and a better torque curve, regardless of the three-digit liter output. The reed valve works reliably up to a speed of 8,000 min −1 . The latest technology replaces the metal membrane tongues with glass or carbon fiber reinforced membrane tongues. The inertia is lower than that of metal membrane plates. Another positive side effect of the diaphragm-controlled engine are significantly better consumption values.
Fuel injection
The Gutbrod Superior and the Goliath GP 700 with two-stroke engines were the first passenger cars with gasoline direct injection in 1951. The system developed under the direction of Hans Scherenberg was supplied by Bosch . In the 1950s, NSU Motorenwerke made experiments with gasoline direct injection (mechanical pressure surge injection) on motorcycle engines. In 1973 Motobécane worked with Bosch to develop an analogue electronic intake manifold injection into the transfer ports on their three-cylinder two-stroke motorcycle, the Motobécane 350 , for series production. In 1997, Bimota presented the Bimota Vdue, a two-cylinder two-stroke engine with direct fuel injection. Two injection nozzles per cylinder injected the fuel directly into the cylinder at the level of the transfer ducts. Aprilia followed in 2001 with the 50 cc scooter SR 50 DiTech with gasoline direct injection.

Exhaust control
The first form of exhaust control comes from Yamaha, by changing the opening duration of the exhaust port. The opening cross-section of the exhaust duct was only fully opened at higher speeds with a small rotary roller valve. The first purely mechanically controlled Yamaha Power Valve System (YPVS) appeared in 1978 on the OW 35, the 500 cc racing machine from Yamaha. The electronic control followed from 1983, also in the series engine in the model RD 350 LC YPVS . In the Suzuki version ( Suzuki Intake Power Chambre ) an additional resonance chamber is opened by means of a rotary valve at low speeds; so also with the system from Kawasaki ( Kawasaki Integrated Power-Valve ). With the exhaust control from Honda ( Autocontrol Torque Amplification Chamber , ATAC for short ), the exhaust volume is increased at low speeds (example Honda NS 400 R ). The filling gain of the outlet control is between 20 and 40% compared to the uncontrolled version.
Construction as a gasoline engine
- Single cylinder: In the case of portable devices, the two-stroke engine is usually designed as a fan-cooled single cylinder.
- Two-cylinder: two-cylinder in line (crankshaft across the direction of travel) were initially air-cooled and later water-cooled ( DKW ); with rotary valve control, the primary drive is located between the cylinders. Cars with two-cylinder two-stroke engines were the DKW F1 to DKW F8 and their successors; in the FRG DKW F89 and in the GDR the IFA F8 , the P70 and the passenger cars of the Trabant brand . There were also various models from Lloyd (car brand) and the Goggomobil . Two-cylinder two-stroke engines were also installed in cars in Sweden ( Saab 92 ), Japan ( Kei cars from various manufacturers) and Italy ( Vespa 400 ).
- Three-cylinder: The Scott 3S motorcycle from 1934 had a three-cylinder two-stroke engine installed lengthways; one engine copy is said to have been sold to DKW in 1939. In 1939, DKW presented the three-cylinder DKW F9 , in 1950 the Industrieverband Fahrzeugbau launched the IFA F9 and in 1953 Auto Union launched the DKW F91, a three-cylinder in passenger cars. Their successors were built by Auto Union until 1966 ending with the DKW F102 and by IFA until 1989 ending with the Wartburg 353 . In 1969, Kawasaki introduced an air-cooled in the Kawasaki 500 H1 and in 1971 in the Suzuki GT 750 a water-cooled, three-cylinder in-line engine was standard for motorcycles; Motobécane followed in 1973 with the Motobécane 350 model . In addition, the three-cylinder with two vertical and one horizontal cylinder by DKW (1953) were developed and used from racing; two horizontal and one vertical cylinders were built in 1983 by Honda (NS400 R, water-cooled). As a radial engine , three-cylinder engines were built by the König company around 1937 with a 500 cm³ displacement as a boat engine, and in the 1990s in different displacement variants as a drive for ultralight aircraft.
- Four-cylinder: DKW built V-engines with four cylinders into the 4 = 8 model in the 1930s. The four-cylinder two-stroke engine with cylinders arranged in a square was used in the motorcycle model RG 500 Gamma from Suzuki , and in the form of a 50 ° V-engine with two crankshafts in the RD 500 LC from Yamaha .
- Six-cylinder: There were V6 engines in racing boats .
- Eight-cylinder: Developed by Galbusera . In addition, Evinrude developed and produced two-stroke V8 engines with the 250XP, 270XP, 300XP and 3.6XP series and the 4.0XP in the 1980s. The 300XP holds the record for outboard motors on water at over 175 mph (280 km / h). In the standard version, it generates 230 kW (300 hp) at 6,250 rpm from a displacement of 3.6 liters. The engine was later also available in a 4.0 liter version, but with slightly more power.
Special designs
Double piston engine
In a double piston engine, two pistons work in a common combustion chamber; Usually one piston controls the overflow and the other controls the outlet openings. Depending on the design of the crank mechanism, asymmetrical control times can be achieved. A distinction is made between the following types of crank drives:
- A connecting rod forked across the crank axis with a sliding piece (e.g. Puch 250 S4 ).
- The main and secondary connecting rods based on the Arnold Zoller patent .
- A crankshaft with two offsets offset by several degrees and separate connecting rods for each piston. ( Triumph BD 250)
- A crankshaft with an offset and a connecting rod forked along the crank axis (Triumph BDG). This version enables direct current purging, but no asymmetrical control times.
Advantages:
- DC purging, d. H. less mixing of old and fresh gas.
- Larger overflow channels and outlet openings, as a larger cylinder cross-section is available.
- Lower flushing losses, especially if no special resonance exhaust system is provided.
Disadvantage:
- Problematic cooling situation of the thin wall between the cylinder bores.
- No arbitrary design of the combustion chamber shape is possible, since a diversion of the fresh gas through the combustion chamber that is as streamlined as possible must be ensured.
Due to the systematic research and utilization of the vibration processes in the exhaust system since the end of the 1950s, the disadvantages of the double-piston engine in the small engine sector outweigh the reverse-flushed single-piston two-stroke engine.
Opposed piston engine
In the opposed piston engine , two pistons work against each other in a cylinder. This solution has lower thermal losses with the same number of pistons, since the cylinder heads are missing. They are available with two crankshafts coupled by a gear transmission or with a crankshaft on the side and long twin connecting rods that act on the second piston via a yoke, or the crankshaft in the middle and rocker arms with two connecting rods each.
Valve two-stroke
Disk valves in the cylinder head for exhaust control are used in long-stroke two-stroke engines in large diesel engines. The direct current purging has thermodynamic and purging dynamic advantages and enables asymmetrical inlet and outlet control times.
Racing
formula 1
Theoretically, the two-stroke engine achieves twice the power of a four-stroke engine under the same conditions (displacement, speed). In practice, due to the high proportion of exhaust gas in the fresh gas charge, it does not achieve the mean pressure of a four-stroke engine. The Formula 1 regulations have forbidden the use of two-stroke engines since 1984; From 1934 to 1937, only the vehicle weight was limited to 750 kg in the forerunner class , so there were attempts to take part in the racing series with a supercharged twin-piston engine .
Motorcycling
In motorcycle races, the two-stroke engine only became competitive with the four-stroke engine in the racing motorcycle Scott Model 3 3/4 by Alfred Angas Scott in 1911 . In 1912 and 1913, Scott Model 3 3/4 riders won the senior class races of the Isle of Man TT on the Snaefell Mountain Course .
In 1932 the first racing motorcycles with double piston engines from DKW appeared , later with piston charging pumps. The most successful model in the class up to 250 cm³ displacement before the Second World War was the almost unbeatable DKW ULD 250 .
The motorcycle world championship introduced in 1949 dominated two-stroke engines in classes up to
- 50 cm³ from 1962 to the dissolution of the class in 1983 , interrupted only in the 1965 season by Honda with a four-stroke engine,
- 80 cm³ from 1984 to the dissolution of the class in 1989 ,
- 125 cm³ from 1967 until the class was dissolved and the two-stroke engine was banned in 2011 ,
- 250 cm³ from 1968 to the dissolution of the class and the ban on the two-stroke engine in 2009 ,
- 350 cm³ from 1974 to the dissolution of the class in 1982 ,
- 500 cm³ from 1975 until the class was dissolved and the two-stroke engine was banned in 2001 .
The last dominant 500 cc two-stroke engine was the series winner from the 1994 season , the Honda NSR 500 , which achieved a peak power of 132 kW in its last expansion stage .
Motorcycle team : From 1975 to 1996 and in the 1997 Sidecar World Cup, two-stroke engines dominated. In 2001 the 500 cc two-stroke engines were banned and replaced by 1000 cc four-stroke engines.
The era of the two-stroke engines in road racing motorcycles lasted from 1911 to 2012, when it finally ended with the introduction of the Moto3 class. In off-road sport (hard enduro), the modern two-stroke continues to dominate due to its compact and lightweight construction with a comparatively high output. The best-known manufacturers of two-stroke motorcycles here are KTM, Beta, GasGas, Yamaha and Sherco.
Racing boats
The two-stroke engine is still regularly used today as a drive for racing boats in the motor boat sport of the Union Internationale Motonautique . In the class up to 2600 cm³ z. B. a V-60 degree 6-cylinder outboard engine 200 HP (147 kW) at 6500-7000 min −1 .
Boat engines
As an outboard engine , two-stroke engines have limits with regard to the oil emissions that also end up in the water during the combustion process. The first regulations can be found in the 1993 Lake Constance Shipping Regulations . Since January 1, 2007, emission regulations for two-stroke engines have existed across Europe as a guideline. The limit values contained therein can only be achieved for two-stroke engines with direct injection, if at all. In accordance with the national shipping regulations of individual countries, however, there may be deviations from the guideline under applicable law. The LSchiffV Brandenburg only stipulates the limitation of the oil content in fuel to 2%.
Emissions from two-stroke engines
With large two-stroke engines, good emission values can in principle be achieved. Simple and small two-stroke engines usually have more emissions than much larger four-stroke engines. The reasons for this are:
- Flushing losses through which the unburned fuel-oil mixture gets into the exhaust gas.
- Inhomogeneous, d. H. Incomplete combustion of the mixture leads to the emission of intermediate combustion products such as fine dust .
- The piston rings overflow the flushing openings; this pulls oil from the cylinder wall into the gas flow, which leads to more emissions, even in engines with oil sump lubrication. The two-stroke engine has one or two piston rings, the four-stroke engine usually three (compression ring, intermediate ring and oil control ring).
Legal limit values
In the past, scooters with two-stroke engines (up to 50 cm³ displacement) played a dominant role in air pollution in large cities due to their harmful emissions. The Euro 4 emissions standard has been in force for two-wheelers since January 2016 , regardless of whether a two-stroke or four-stroke engine is used. This led to a general installation stop of two-stroke engines in the field of small motorcycles, for which the Euro 4 standard (previously Euro 2) has also applied since 2016. Even the Euro 3 standard could not be achieved for two-stroke engines. The last two-stroke motorcycle with street legal over 150 cm³ displacement was the Aprilia RS 250 with 249 cm³ displacement and 55 HP / 40 kW power, which was built until 2002 and had the revised engine of the Suzuki RGV 250 Gamma . Exception: The road version of the KTM Freeride 250 R, which has been built since 2013, has a two-stroke engine that has been throttled to 7 HP (5 kW) in order to meet the Euro 3 standard. Small motorcycles (up to 50 cm³ displacement) are still allowed to emit five times the amount of hydrocarbons and nitrogen oxide from car engines.
Emission limit values for motorcycles in mg / km |
|||||
---|---|---|---|---|---|
standard | Euro 1 | Euro 2 | Euro 3 | Euro 4 | |
Type test | from June 17, 1999 | from April 1, 2003 | from Jan. 1, 2006 | from Jan. 1, 2016 | |
CO | 8,000 / 13,000 3 | 5,500 | 2,000 | 1,140 / 1,000 6 | |
HC | 4,000 / 3,000 3 | 1,200 / 1,000 5 | 800/300 5 | 170/380 4 /100 6 | |
NO x | 100/300 3 | 300 | 150 | 90/70 4 /300 6 | |
PM | 80 6 |
Emission limit values for small motorcycles (KKR) and passenger cars in mg / km |
||||
---|---|---|---|---|
standard | Euro 4 (KKR) | Euro 5 (car) | Euro 6b (car) | |
Type test | from Jan. 1, 2016 | from Jan. 1, 2011 | from September 1st, 2015 | |
CO | 1,000 | 1,000 | 1000 | |
HC | 630 | 100 | 100 | |
NO x | 170 | 60 | 60 | |
PM | - | 4.5 7 | 4.5 | |
Particle number | - | - | 6 · 10 11 |
(As of December 2016)
Diesel two-stroke
Historic diesel two-stroke

Well-known two-stroke diesel engines with exhaust valves in the cylinder head were the series 53, 71, 92, 149 (cubic inches) of the Detroit Diesel Corporation (DDC). These two-stroke engines used a Roots blower - some with upstream turbochargers - and water-cooled intercoolers to generate the flushing pressure . Two-stroke diesel engines for trucks with controlled exhaust valves were also produced by the Krupp factories until the 1950s. Opposite piston diesel engines are the Junkers Jumo aircraft engines with two crankshafts, the Napier Deltic with three rows of cylinders and three crankshafts and the Commer TS-3, a truck engine with one crankshaft and two connecting rods and a rocker arm per piston.
Modern, valve-controlled two-stroke engines
Many of today's two-stroke engines have controlled exhaust valves and intake ports. They are flushed with separate cargo pumps. This results in a clean gas exchange. Mixture lubrication is no longer necessary, the crankshaft runs in plain bearings lubricated with pressurized oil, as in the four-stroke engine.
This design is particularly suitable for slow-running engines with a large displacement (marine diesel, with bores of almost one meter and strokes of over three meters), since the low speed always leaves enough time for the gas change and the weight of the external loader is irrelevant. Because of the fuel used ( bunker oil ), such valve-controlled two-stroke engines are only available as diesel.
In terms of thermal efficiency , the large, turbocharged two-stroke marine diesel engine is only surpassed by stationary combined gas and steam turbines among heat engines . A marine diesel with a specific fuel consumption of less than 160 g / kWh can convert up to 55% of the chemically bound energy of the fuel into usable mechanical work. Passenger car four-stroke turbo-diesels achieve an efficiency of 40–42%, truck four-stroke turbo-diesels to 45%, four-stroke gasoline engines with turbo to 35–37%.
A special application is the Japanese Type 90 tank, which is powered by a Mitsubishi 10ZG two-stroke engine with direct diesel injection and Roots blower for charging. The American M113 armored personnel carrier is equipped with a water-cooled two-stroke V6 diesel engine from General Motors (the production division was later spun off and renamed the Detroit Diesel Corporation ). It delivers 156 kW (M113A1 and M113A2) or 202 kW (M113A3).
literature
- Christian Bartsch (ed.): A century of motorcycle technology . VDI-Verlag, Düsseldorf 1987, ISBN 3-18-400757-X .
- Wolf Albrecht Doernhoeffer: Two-stroke practice. 3. Edition. Christian-Rieck-Verlag, Eschborn 2004, ISBN 3-924043-19-1 . (This book was published under the original title Two-Stroke Internship - Operational Pocket Book for Small Two-Stroke Otto Engines in Franckh-Kosmos-Verlag as early as 1942. Except for recent developments in the areas of materials, engine management and pollutant reduction through CWI and the like, this book is still to this day current.)
- Michael Heise: two-stroke vehicle engines . Fachbuchverlag, Leipzig 1953.
- Pavel Husák: two-stroke motorcycles. 1st edition. Motorbuch Verlag, Stuttgart 1987, ISBN 3-613-01161-1 .
- Hans List: The gas exchange of the internal combustion engine. Volume 4, Part 2: The two-stroke . Springer, Vienna 1950.
- Christian Rieck: Two-stroke engine tuning . Rieck, Eschborn 2004, ISBN 3-924043-25-6 . (explains how the two-stroke engine works and ways to increase performance)
- Herbert J. Venediger: Two-stroke flush, in particular reverse flush . Franckh, Stuttgart 1947.
Web links
Individual evidence
- ↑ Photo: Two-stroke engine System Benz ( Memento from December 12, 2013 in the web archive archive.today )
- ↑ Scan: Day-Motor (accessed on May 27, 2013)
- ^ Siegfried Rauch: The two-stroke engine in motorcycle construction. In: Christian Bartsch: A century of motorcycle technology . VDI-Verlag, Düsseldorf 1987, ISBN 3-18-400757-X , p. 125.
- ↑ Christian Bartsch: Ideen und Rohrkrepierer , on: automobil-industrie.vogel.de , August 13, 2007 (accessed on May 26, 2013)
- ↑ New petroleum engines. In: Polytechnisches Journal . 303, 1897, pp. 246-251.
- ↑ In 1971 the membrane control was perfected by Yamaha
- ↑ The usable two-stroke petrol engine for passenger and delivery vehicles . In: Motortechnische Zeitschrift . 4/1949, pp. 92-94.
- ↑ a b Mainly taken from the location of the two-stroke engine as a car drive . Part I + II: two-stroke diesel engine; Part III + IV: two-stroke petrol engine. In: MTZ . Springer Vieweg / Springer Fachmedien, July 2001, ISSN 0024-8525 .
- ↑ The two-stroke engine and its special advantages . In: Automotive Technology . 10/1964, pp. 371-374.
- ↑ Bosch Kraftfahrtechnisches Handbuch, 25th edition, page 472 Disadvantages of the two-stroke engine
- ↑ The two-stroke engine - yesterday, today and tomorrow. In: Automotive Technology . 2/1962, pp. 52-56.
- ↑ Winner of the Transport and Mobility Category 2007 Envirofit International : Project Philippine Two-Stroke Engine Retrofit Project at: cleanenergyawards.com (accessed on June 14, 2013; PDF; 272 kB)
- ↑ 2-cylinder Rotax engines for use in snowmobiles at: rotax.com (accessed on 22nd Jabzar 2017)
- ↑ TLDI model overview at: tohatsu.de (accessed on January 22, 2017)
- ↑ Piston design and flash animation at pivotalengine.com (accessed on June 14, 2013)
- ^ Richard von Basshuysen: Handbook Internal Combustion Engine: Fundamentals, Components, Systems, Perspectives. Vieweg + Teubner Verlag, 2007, p. 440ff.
- ^ Pavel Husák: Two-stroke motorcycles. 1987, p. 130.
- ↑ Technical data DKW Super Sport 250 and SS 350 , at: motorradonline.de (accessed on August 2, 2013)
- ^ Pavel Husák: Two-stroke motorcycles. 1987, p. 164.
- ↑ On the move: Maico MD 250 WK , on: motorradonline.de (accessed on May 22, 2013)
- ↑ Stihl: Correct fuel mixture
- ↑ Husqvarna: Product Catalog 2013
- ↑ Dolmar: 2-stroke engine oil
- ^ A b Alan Cathcart in MOTORRAD CLASSIC 5/2013, pp. 72–79.
- ^ Pavel Husák: Two-stroke motorcycles. 1987, p. 166 ff.
- ^ LJK Setright: The Guinness Book of Motorcycling. Facts and Feats. 1982, ISBN 0-85112-255-8 , p. 28.
- ^ Gabriele Klinger, Andreas Winter: 101 years of Austrian motorcycle manufacturers. 1st edition. Weishaupt Verlag, Gnas 2001, ISBN 3-7059-0093-5 , p. 86.
- ^ Pavel Husák: Two-stroke motorcycles. 1987, p. 134.
- ↑ Photo: Reed valve Yamaha RD 80 ( Memento from June 29, 2013 in the web archive archive.today )
- ^ Pavel Husák: Two-stroke motorcycles. 1987, p. 135.
- ↑ Diaphragm control - and again Yamaha. In: H. Hütten: Fast engines - dissected and coiffed. 6th, completely revised edition. RC Schmidt, Braunschweig 1977, ISBN 3-87708-060-X , pp. 252-253.
- ↑ Scan: Bosch gasoline injection at Gutbrod ( Memento from July 2, 2013 in the web archive archive.today )
- ↑ Motobecane 350 on classicbikersclub.com ( Memento from June 28, 2013 in the web archive archive.today )
- ↑ Jürgen Stoffregen: Motorcycle technology. Basics and concepts of engine, drive and chassis. 7th edition. Vieweg Verlag, Wiesbaden 2010, ISBN 978-3-8348-0698-7 , p. 62.
- ↑ Yamaha OW45 , Yamaha Classic Racing Team ( Memento from December 3, 2013 in the web archive archive.today )
- ↑ YPVS (Yamaha Power Valve System) on: yamaha-motor.eu (accessed on May 19, 2013)
- ^ Pavel Husák: Two-stroke motorcycles. 1987, p. 151.
- ^ Pavel Husák: Two-stroke motorcycles. 1987, p. 154.
- ↑ Jürgen Stoffregen: Motorcycle technology: Basics and concepts of engine, drive and chassis. 7th edition. Vieweg Verlag, Braunschweig 2010, ISBN 978-3-8348-0698-7 , p. 59.
- ↑ Double piston engine: Two strokes in a double pack on: oldtimer-markt.de (accessed on November 14, 2013)
- ↑ Photo: DKW ULD 250 (accessed on May 11, 2013)
- ↑ Photo: Triumph BD 250
- ↑ Scan: Triumph comparison double piston two-stroke - OHV four-stroke brochure 1952 (accessed on November 14, 2013)
- ↑ Arnold Zoller developed a 6-cylinder two -stroke double-piston engine for the racing car in 1934 , which was built by the Röhr works. → The ZOLLER racing community on roehrauto.de ( Memento from April 29, 2013 in the web archive archive.today )
- ↑ Honda NSR 500 on visordown.com ( Memento from June 30, 2013 in the web archive archive.today )
- ↑ Honda Worldwide | Motor Sports | MotoGP | Honda World Grand Prix 700 Wins (History of the Honda NSR 500, on world.honda.com, English, accessed June 8, 2017)
- ↑ 2017 Offshore Rulebook. (PDF; 55.4 MB) Union Internationale Motonautique (UIM), p. 126 , accessed on January 22, 2017 (English, "The engines may be of the two-stroke or the four-stroke types.").
- ↑ OptiMax 200XS ROS ( Memento from January 22, 2017 in the Internet Archive ) on: mercuryracing.com (accessed on January 22, 2017)
- ↑ Eligibility of engines / engine changes on Lake Constance , district of Konstanz (accessed on January 22, 2017)
- ↑ Directive 2003/44 / EC of the European Parliament and of the Council of June 16, 2003 amending Directive 94/25 / EC on the approximation of the legal and administrative provisions of the member states relating to recreational craft . In: EUR-Lex .
- ↑ Outboards have to get even cleaner: Strict limit values on Lake Constance are causing problems for engine builders ( Memento from July 1, 2013 in the web archive archive.today ), in: International Commission for the Protection of Water on Lake Constance (IGKB): Seespiegel No. 13, June 2001 ( PDF; 1.2 MB ).
- ↑ 2-stroke outboard motors fall below the limit values for 4-stroke outboard motors ( memento from June 30, 2013 in the web archive archive.today ), DLRG Group Radolfzell
- ↑ List of type-tested engines of emission level II and I of Annex C of the Lake Constance Shipping Regulations (built-in and outboard engines) ( memo from July 18, 2013 in the Internet Archive ) of the Konstanz District Office (PDF; 96 kB; accessed on May 27, 2013 )
- ↑ § 25 Ordinance for shipping on the navigable waters of the State of Brandenburg (Landesschifffahrtsverordnung - LSchiffV).
- ↑ G. Merker, Chr. Schwarz, G. Stiesch, F. Otto: Internal combustion engines. 2nd Edition. Teubner, Stuttgart a. a. 2004, ISBN 3-519-16382-9 .
- ↑ Heinz K. Müller, Bernhard S. Nau: Piston rings for engines and compressors ( Memento from December 22, 2015 in the Internet Archive ), Chapter 15 from fachwissen-dichtungstechnik.de (PDF; 484 kB)
- ↑ Piston ring sets 2015. (PDF; 7.2 MB) Mahle, accessed on January 22, 2017 (product catalog with supplementary description).
- ↑ Two-stroke scooters are a dominant source of air pollution in many cities , in: Nature Communications 5, 2014, doi: 10.1038 / ncomms4749
- ↑ Motorcycle catalog 2017, pp. 91, 148.
- ↑ Regulation (EU) No. 168/2013 of the European Parliament and of the Council of January 15, 2013 on the approval and market surveillance of two-, three-wheel and four-wheel vehicles , Annex VI. In: EUR-Lex .
- ^ W-X52. Winterthur Gas & Diesel, accessed on January 22, 2017 (English).