Paraffin oxidation

The paraffin oxidation is a historic chemical-industrial process for the production of synthetic fatty acids comprising the chemical industry both to consumer goods such as soap and edible fats and to greases processed for technical applications. A wide range of carboxylic acids and oxidation products such as alcohols , aldehydes , esters and ketones were also produced . The raw material was based on coal-derived paraffin slack , a saturated, high-molecular hydrocarbon mixture and a by-product of the Fischer-Tropsch synthesis . The paraffins were oxidized in the liquid state by molecular atmospheric oxygen with cleavage of the carbon chain in the presence of permanganates , at temperatures in the range from about 100 to 120 ° C. and under normal pressure .
The products of paraffin oxidation competed with naturally occurring fatty acids. Shortages due to conflicts or bottlenecks in the food supply increased the interest in synthetic fatty acid products. In Germany, the process gained commercial importance from the mid-1930s as part of the self-sufficiency efforts of the German Reich and was carried out on an industrial scale until the first years after the Second World War . This process was used to produce the raw material for the technical fat and detergent sector; the native fats previously required for this were now available to the food sector. Furthermore, the large-scale production of artificial fats suitable for human consumption (“butter”) from coal , which was made possible for the first time by the oxidation of paraffin, was considered a sensation at the time.
Due to the high availability of inexpensive native fats and the competition from petroleum-based fatty alcohols , the process lost its importance in the western world at the beginning of the 1950s. Process variants such as the Bashkirov oxidation, in which alkanes are oxidized to secondary alcohols in the presence of boric acid, without chain cleavage , are still used by the chemical industry for special syntheses, for example for the production of cyclododecanol .
history
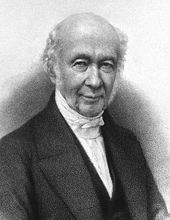
Early work
Paraffins are a mixture of alkanes , saturated hydrocarbons with the general empirical formula C n H 2n + 2 . Its name is derived from the Latin parum affinis , little involved . Paraffins were regarded as not very reactive; with reducing agents such as metallic sodium, for example, paraffins do not react at ambient temperature.
In 1854, only 19 years after the discovery of paraffins by Karl von Reichenbach , Gotthard Hofstädter pointed out that paraffins are not as inert as their name suggests. He reported for the first time on attempts to oxidize paraffins by boiling them with nitric acid . The main product he received was succinic acid , a dicarboxylic acid , and low molecular weight, water-soluble monocarboxylic acids . Other strong oxidizing agents, such as the chromic acid used by Eduard Meusel , also led to the formation of carboxylic acids. In 1874, AG Pouchet described paraffin oxidation using a mixture of fuming nitric and sulfuric acid at temperatures below 110 ° C. A number of low molecular weight, water-soluble carboxylic acids were again obtained as products. In addition, Pouchet identified a new, higher molecular weight carboxylic acid for the first time, a fatty acid that he called "paraffinic acid ".
Oxidation with air
Pompejus Bolley recognized in 1868 that paraffins absorbed the oxygen in the air at a temperature of 150 ° C, Carl Engler discovered the formation of water-soluble fatty acids in similar studies in 1879. However, the researchers did not recognize the practical significance of their observations. It was not until a few years later that Eugen Schaal identified the commercial potential of this reaction. In 1884 he filed the first patent for the conversion of petroleum and similar hydrocarbons into carboxylic acids by oxidation with air. Among other things, Schaal used chlorates , permanganates and nitrates adsorbed on kieselguhr as a catalyst . The use of inexpensive atmospheric oxygen represented a significant advance on the way to the technical implementation of the process. Since fatty acids from natural sources were sufficiently available until the outbreak of World War I , commercialization of these processes was initially not worthwhile.
It was only when fats and thus fatty acids became scarce during the World War that the chemical industry stepped up research efforts in order to obtain at least the raw material for soap production on the basis of petroleum or the tar from the smoldering of lignite . Attempts to transfer the processes already known at the time into industrial practice were only partially successful. The first technical process during the war was carried out by the Fanto company in Pardubice and used a mercury salt as a catalyst. However, the fatty acids produced were of poor quality and the paraffins took days to convert. An improvement in yield and quality was achieved through the systematic study of the influence of temperature and the amount of air on the quality of the oxidation product by Adolf Grün at Shift AG . The fatty acids technically produced by the Layer AG could be saponified well, the soaps provided a satisfactory washing effect.
After the First World War in the 1920s, larger chemical companies such as IG Farben and Henkel and Hubbe & Fahrenholz, at that time one of the largest and most important oil mills in Germany, continued research in the field of paraffin oxidation. A production facility of IG Farben in Ludwigshafen produced synthetic fatty acids on a smaller scale from 1928, a joint venture between IG Farben and Standard Oil of New Jersey in Baton Rouge produced around 3 tons of fatty acids per day based on paraffins derived from petroleum in 1931. However, the fatty acids obtained in the process led to soaps of inferior quality with odor problems in further processing. Since the raw material base paraffins was scarce and therefore expensive, the process did not offer any economic advantage in comparison with the costs for the procurement of native fatty acids at this point in time.
German fatty acid works
The colloid chemist Arthur Imhausen , co-owner of the Märkische soap industry , resumed Eugen Schaal's research in the 1930s. With his colleague Werner Prosch he developed the Imhausen-Prosch process for paraffin oxidation. The process used air as the oxidizing agent and potassium permanganate as the initiator. Initially, Imhausen used paraffins from the hydrogenation of brown coal carbonized products. The commissioner for economic issues Wilhelm Keppler , who was responsible for the implementation of the four-year plan with the focus on “industrial fats and oils” as well as for the promotion of gasoline production, offered Imhausen the use of the wax slack from the Fischer-Tropsch synthesis as a raw material . Slack wax was a mixture of alkanes without significant impurities, which until then was considered a disruptive by-product of the Fischer-Tropsch synthesis. It turned out to be an ideal raw material for paraffin oxidation. Because all types of coal can be used in the Fischer-Tropsch synthesis, there was a broad raw material base for mash production. Furthermore, the empire assumed price guarantees for the raw material supplied as well as for the fatty acids produced.
In relation to the slack wax, Imhausen achieved a yield of about 50% for the target products, the main run fatty acids with a chain length of 11 to 20 carbon atoms. Imhausen did not have the necessary capital for a large-scale implementation, and there were technical problems with the processing of the crude fatty acid mixture. Since Henkel was also interested in fatty acids and had sufficient financial resources, Imhausen and Henkel founded Deutsche Fettäur-Werke GmbH in Witten on February 21, 1936 as a joint venture for the production and marketing of fatty acids using the Imhausen-Prosch process. The shareholders appointed Arthur Imhausen and Erich Grünthal as managing directors, and the chairman of the supervisory board was the Persil inventor Hugo Henkel .
Since IG Farben had also developed a process for paraffin oxidation, Keppler initiated a cooperation between the German fatty acid works and IG Farben for the purpose of optimizing production processes. The IG Farben process offered advantages in the further processing of the raw fatty acids. From around May 1938, Imhausen overcame the technical difficulties of processing crude fatty acids with the help of the IG Farben process and received a high-quality product. Since the Fischer-Tropsch fuels had a low octane number , the National Socialist economic leaders instead built more hydrogenation plants based on the Bergius-Pier process , which supplied a higher-quality motor gasoline ; Slack wax became difficult to obtain. It was not until 1940 that the Fischer-Tropsch plants increased their output considerably, which led to a good supply of mud. At Imhausen's instigation, Keppler had the Fischer-Tropsch systems converted to the medium pressure process, which delivered a higher yield of slack wax. The IG Farben plants in Ludwigshafen-Oppau and Heydebreck each produced 20,000 tons, and the Witten plant 40,000 tons of fatty acids per year. While the Witten plant processed almost only Fischer-Tropsch-Gatsch, the Oppau plant used around 80% lignite-derived TTH paraffins, 10% Fischer-Tropsch-Gatsch and 10% Nerag-Gatsch, which came from the lowering of the pour point of spindle oil .
Coal butter

Before the start of the Second World War , domestic production in Germany covered less than half of the dietary fat requirement of around 1.6 million tonnes, in the technical sector with a requirement of around 400,000 tonnes only around 13%. Germany covered the remaining demand by importing oils and fats from oil plants from East Asia and South America as well as arctic whale oils . The political intention to end the dependence of the German Reich on the import of technical fats and dietary fats soon led to the so-called fat gap . From August 1939, four days before the start of the war, the National Socialists rationed the purchase of fats and controlled their issue via a Reich fat card .
Arthur Imhausen, who was of Jewish descent, succeeded in producing the first synthetic edible fat in the world from the pure fatty acids from paraffin oxidation through esterification with glycerine, thus supporting the efforts of the Third Reich to become self-sufficient. At the suggestion of Hermann Göring , Adolf Hitler then recognized Imhausen's family as Aryans . From 1941, the Deutsche Fettwerke Witten produced 250 tons of artificial edible fat per month in a large plant. On Wilhelm Keppler's advice, the National Socialists distributed the synthetic grease on a trial basis for about three years to prisoners in the Sachsenhausen concentration camp and in the camps of the Reich Labor Service in Trebbin and Ruhlsdorf. Doctors from the Physiological Department of the Reich Health Office also carried out feeding experiments on animals. The occurrence of odd-numbered fatty acids, which are seldom found in native fats, was considered a cause for concern. However, negative physiological effects could not be demonstrated. On the other hand, proportions of ethyl-branched carboxylic acids in fat, so-called isofatty acids, lead to the formation of dicarboxylic acids, which is harmful to health and which could be detected in the urine even after a small dose. After three years of testing, the Reich Health Office in 1939 was, a few days after the attack of the German Wehrmacht in Poland , under political pressure, the art of butter for consumption free. The fat served as an additive to heavy labor rations, to canteen meals in hospitals and supplemented the rations of inmates of labor and concentration camps and of Soviet prisoners of war . During the African campaign and on the German submarines , the military supplied the soldiers with edible fat from the Witten production. The fat hardly went rancid due to the high content of saturated fatty acids and was therefore long-lasting. In terms of taste, it came close to butter and it had the same calorific value . Imhausen's hopes for a production volume of more than 100,000 tons per year were not fulfilled, however, during the war the German fatty acid plants only produced around 3,000 tons per year.
post war period

Towards the end of the Second World War and in the first years after the war, the supply of fat deteriorated rapidly. In 1947, the annual per capita consumption in Germany, which had been 25.6 kilograms in 1938, fell to 5.7 kilograms. Politicians and industrialists tried to stimulate the import of fat and to obtain clearance for the resumption of the Fischer-Tropsch synthesis and the Imhausen-Prosch process. The production facilities of the German Fatty Acid Works had an operational capacity of around 600 tons of synthetic butter per month. In addition, the use of synthetic fatty acids for technical purposes released the same amount of native fatty acids for nutritional purposes. The Imhausen-Prosch process required seven tons of coal per ton of butter; In order to be able to import the same amount of butter, the sales proceeds of ten times the amount of coal on the world market were necessary in the post-war period .
Arthur Imhausen's son, Karl-Heinz Imhausen, succeeded in briefly resuming the production of carbon-based soaps and fats in the post-war period, with the Witten plant producing around 350 tons of synthetic fat per month in 1946. But interest in paraffin oxidation and carbonaceous fatty acids ended in the 1950s with the onset of the economic miracle . The sudden oversupply of natural fats on the world market led to a sharp drop in the price of fats and fatty acids. In the surfactant market, the carbon-derived fatty acids competed with both oleochemical and petrochemical products such as Ziegler alcohols . While the process was no longer competitive in the western world and fatty acids were hardly produced artificially, they continued to be produced in the Soviet Union and China . In 1978, for example, in the Soviet Union and China, over 500,000 tons of fatty acids were obtained from wax and kerosene by oxidation on manganese catalysts.
raw materials
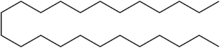
The paraffins used in the oxidation have a carbon chain length of about 18 to 30 carbon atoms, corresponding to a melting range of 28 to 66 ° C and a boiling range of 320 to 460 ° C. The target products, the fatty acids with a chain length of 10 to 18 carbon atoms, can be obtained in maximum yield from paraffins of this chain length range. The paraffins should be as straight-chain as possible in order to achieve a high product quality. The branched fatty acid soap was poor in detergency and had a characteristic odor. In the case of branched paraffins, oxygen also preferably attacks the tertiary hydrogen atom. Although straight-chain fatty acids are formed, they have a disproportionately large proportion of low-molecular fatty acids.
The paraffins came mainly from two processes, the high-pressure hydrogenation of lignite and its charring tars and from the Fischer-Tropsch synthesis. The low-temperature, high-pressure hydrogenation process produced straight-chain, so-called TTH paraffins with a degree of branching of around 10 to 15%. Although lignite was available in large quantities, the sales problems for the by-products of carbonization only led to a relatively low availability of suitable paraffins from this source. In addition, the n-alkanes resulting from the urea extractive crystallization of lubricating oils are also suitable as raw materials.
In the low-pressure process of the Fischer-Tropsch synthesis, slack wax with the correct carbon chain length distribution was obtained. The slack from the medium pressure process was more suitable because it was particularly straight-chain, but still had 15 to 20% short-chain branched paraffins. Due to their tertiary hydrogen atoms, which are more easily accessible to oxidative attack, these are particularly suitable as starting material for paraffin oxidation. In addition, the yield of target paraffins in the medium pressure process was about four to five times higher than in the low pressure process. Instead, the chain length range was shifted to higher chain lengths, which required the sludge to be prepared by distillation.
Because of their inhibiting effect, the limit for the proportion of sulfur-containing compounds and phenols was 0.05%. Hydrogenation of the raw material removed disruptive olefins and oxygen-containing compounds. Petroleum was hardly suitable as a raw material for paraffin oxidation because of its naphthene content, which led to viscous fatty acids of poor washing quality. Long-chain branched paraffins, olefins and naphthenes also led to higher proportions of undesired hydroxycarboxylic acids in the oxidation . The wax suitability was checked by means of a test oxidation.
Procedure
The process consisted of the three main steps of oxidation, processing of the oxidation mixture into crude fatty acids and finally their separation by distillation into fatty acid fractions. The chemical industry further processed the fatty acid fractions into end products such as soaps, detergents , plasticizers and synthetic fat. The operators carried out the paraffin oxidation almost exclusively in a batch mode , i.e. discontinuously.
oxidation
Oxidation was an important process step. The paraffin reacted in the liquid state at the lowest possible temperatures and in the presence of a catalyst with atmospheric oxygen for about 15 to 30 hours until about 30 to a maximum of 50% of the paraffin had been converted into fatty acid. This minimized the formation of undesirable by-products, such as the proportions of dicarboxylic acids, hydroxycarboxylic acids and low molecular weight fatty acids that are insoluble in petroleum ether.
After a short latency phase, which is typical for autocatalytic reactions, the oxidation started, which was evident from the formation of water and the increase in the acid number of the product. If the raw material contained inhibitors , they first had to be oxidized before the reaction could start. The presence of cyclic and unsaturated hydrocarbons, on the other hand, led to the formation of inhibitors which suppressed a reaction that had already started or brought it to a standstill. The reaction proceeded schematically according to the general equation:
The fatty acids formed were still subject to post-oxidation, so that an excessive amount of low molecular weight fatty acids was formed compared to the statistically expected distribution. Fatty acids, alcohols, aldehydes, ketones, esters and lactones were formed as non-volatile products, while carbon dioxide , water, low molecular weight carboxylic acids and their esters, as well as peroxides, aldehydes and alcohols were formed as volatile products .
Pressure and temperature
A high reaction pressure increased the proportion of oxygen dissolved in paraffin and thus the rate of the reaction. Doubling the pressure roughly halved the reaction time. During the Second World War, Hubbe & Fahrenholz built a plant in Magdeburg that was supposed to work at a pressure of 25 bar and without a catalyst. However, the company no longer put the system into operation. All other systems worked under normal pressure. The dissolved oxygen content increased through finely dispersed bubbling of the air, for example through filter candles or fillers .
At temperatures above 170 to 180 ° C, the oxidation proceeded quite quickly, but overoxidized products were formed which were unsuitable for further processing into surfactants. A relatively low oxidation temperature was an advantage for obtaining pure fatty acids. With a turnover limitation of about 30% and at temperatures of 105 to 120 ° C, the chemical industry obtained fatty acids with high selectivity and good quality. The reaction time, which was too long for industrial purposes, made the use of a catalyst necessary.
Catalyst / initiator

The catalysts used for paraffin oxidation were varied. Often these were oxides of sub-group metals, such as cobalt salts . Potassium permanganate proved to be a good initiator for the paraffin oxidation . Alkali metal salts acted as cocatalysts, which were added to the process via the soap components of the processed and recycled paraffins.
A suspension of the potassium permanganate in the paraffins was created by adding and rapidly stirring a concentrated aqueous permanganate solution. At temperatures above 100 ° C., the water evaporated and a finely divided suspension of the initiator remained. The amount used was approximately 0.1 to 0.3% of the amount of paraffin used and varied with the quality of the raw material. By adding the catalyst, the operators achieved a target conversion of around 30% after a reaction time of 10 to 15 hours at relatively low temperatures of 110 to 120 ° C. A low reaction temperature suppressed the formation of undesired by-products such as hydroxy or dicarboxylic acids, and the product color improved.
Conduct of proceedings
The paraffin oxidation was carried out in acid-resistant steel or aluminum reactors. These had a diameter of 1–3 meters and a height of 8–12 meters. The air bubbled in through filter plates or candles, the air was distributed in the reactor through packing. The volatile acids and by-products dissolved in the washer filled with water. The oxidation of a ton of paraffin required about 50 cubic meters of air per hour. The start of the reaction initially required a temperature of about 150 ° C. After the reaction had started, after about 20 to 60 minutes, the reaction temperature was lowered to below 120.degree. The excess air transported away the low molecular weight components. The start of the reaction was shown by the accumulation of water in a condenser , which also collected the volatile oxidation products.
Since the oxidation was exothermic , the reactor had to be cooled. The amount of heat released corresponded to about 4.5% of the heat of combustion of the paraffin, per ton of oxidation product about 2100 megajoules . If the acid number of 70 was reached, this meant that the target conversion had been reached and the oxidation could be terminated. The conversion was then about 30%. The sales limit reduced the formation of fatty acid by-products such as hydroxycarboxylic acids and dicarboxylic acids.
Processing of the crude fatty acids
The crude fatty acids contained a mixture of carboxylic acids of all the chain lengths contained in the paraffin used, unconverted paraffin and a broad spectrum of oxidation products. In the work-up, the fatty acids contained in the oxidation product were first washed with water in order to separate off the low molecular weight acidic components and the catalyst.
To separate the fatty acids from the unsaponifiable fractions, the crude oxidate was first neutralized with sodium hydroxide to form soap. The esters formed also saponify at higher temperatures. The unsaponifiable fractions were then mixed with 45 percent ethanol or 20 percent 2-propanol in a stirred kettle . The soap dissolved in the alcohol, while the unsaponifiable fractions were deposited as an oily layer on the alcohol-soap mixture. The oily layer, which mostly contained paraffins and was referred to as unsaponifiable I (UV I) , was returned to the oxidation process. The proportion of UV I in the total proportion of unsaponifiable components was about 85%.
The remaining unsaponifiable parts, referred to as unsaponifiable II (UV II) , contained, in addition to residues of paraffins, above all oxidation products such as alcohols, esters and lactones. The plant operators removed these components by extraction with gasoline in countercurrent. UV II and gasoline were separated by distillation . After the alcohol and soap phases had been separated by distillation, the last step was to recover the fatty acids by acidifying them with mineral acids such as sulfuric or hydrochloric acid . Residues of short-chain carboxylic acids were removed by washing with water. Then a steam vacuum distillation separated the fatty acids into individual fractions.
Products
The main run fatty acids with a carbon chain length of about 10 to 20 carbon atoms were neutralized with caustic soda to make soaps. In contrast to native fatty acids, the synthetic fatty acids contained shares of odd carbon chains. The detergency of the soaps thus obtained did not differ from the soaps from native sources. The presence of unsaponifiable fractions, the presence of lactones and the presence of branched-chain fatty acids partly led to odor problems. A hydrogenation reduced the fatty acids to fatty alcohols. By sulfation with sulfur trioxide emerged from the fatty alcohols, fatty alcohol sulfates.
Imhausen was the first to produce fats on an industrial scale through esterification with glycerine and later to manufacture butter from synthetic fatty acids through emulsification . For this, the fatty acid works only used natural glycerine from inedible fats. A synthetic glycerine produced by IG Farben in Heydebreck turned out to be not pure enough for this purpose. The fatty acids are esterified with the stoichiometric amount of glycerin using zinc dust . After the reaction had ended, treatment with 20 percent sulfuric acid dissolved the zinc. After neutralization with sodium hydroxide solution, traces of soap were removed with a mixture of activated charcoal and fuller's earth. Imhausen obtained a pure fat by vacuum distillation, which was suitable for consumption.
The first run fatty acids were mainly reduced to alcohol and processed into plasticizers after esterification with phthalic anhydride or other anhydrides. The operators returned the trailing fatty acids with a higher molar mass to the oxidation process. The air cooler condensate contained about 80% formic acid and 9% acetic acid and was used to preserve cattle feed. The paint industry used the residue from the fatty acid distillation as a binder for pigments.
mechanism
The first approach to explaining the oxidation of paraffinic hydrocarbons was provided by the peroxide theory developed by Alexei Nikolajewitsch Bach and Carl Engler, which is known as the Engler-Bach theory. Accordingly, a secondary hydroperoxide is formed during the oxidation in the first step . This theory, according to which this hydroperoxide then decomposes radically , was confirmed later by Eric Rideal .
The function of the metal catalyst is to increase the rate of both the formation and the decomposition of this hydroperoxide. Among other things, this creates an alkyl radical that reacts with oxygen to form a peroxo radical . This forms a new alkyl radical and a hydroperoxide by abstracting a hydrogen atom from another paraffin molecule .
Alkali salts also decompose the peroxides and react as a co-catalyst. The relative speed of oxygen attack on primary, secondary and tertiary hydrogen atoms is about 1: 3: 33. The attack on the mainly occurring secondary hydrogen atoms is purely statistical and leads to the formation of an almost equimolar mixture of all theoretically possible carboxylic acids. Due to the large number of products formed, the exact elucidation of the reaction mechanism turned out to be difficult. The reaction sequence of the oxidation and the formation of the main and by-products is best explained according to the scheme designed by Wolfgang Langenbeck and Wilhelm Pritzkow :
The first stage is a hydroperoxide that breaks down as the main reaction into water and a ketone . Secondary alcohols are formed as a side reaction according to the following reaction scheme:
The ketone is subject to further oxidation. The methylene group is preferably oxidized in the α-position to the keto group. The resulting α-ketohydroperoxide breaks down into an aldehyde and a carboxylic acid with rearrangement .
Pritzkow used cyclohexanone as a model substance and thus showed the correctness of the model concept. The aldehyde is converted into the carboxylic acid via the peroxycarboxylic acid stage and further reaction with another aldehyde. The formation of the carboxylic acid esters and other carboxylic acids takes place via the Baeyer-Villiger oxidation of the ketone with peroxycarboxylic acid according to the following equation:
Another possible reaction of the α-ketohydroperoxides is the formation of diketones .
These react with peroxycarboxylic acids to form acid anhydrides and carboxylic acids.
Bashkirov oxidation

If the paraffin oxidation is carried out in the presence of boric acid , secondary fatty alcohols are the main product . This process is called Bashkirov oxidation after its discoverer Andrei Nikolajewitsch Bashkirov, who developed the process in the 1950s. The Bashkirov oxidation does not break down the original paraffin; the chain length of the alcohols produced corresponds to that of the paraffins used as raw material. The chain lengths of the original paraffins are correspondingly shorter compared to those used in the paraffin oxidation.
The process is carried out at a temperature of 150 to 160 ° C., a proportion of 0.1% potassium permanganate as initiator and about 5% boric acid . The boric acid catches the hydroperoxides that are formed and converts them into their esters, which are insensitive to further oxidation. Subsequent hydrolysis of the ester gives secondary alcohols which are converted to secondary alkyl sulfates or with ethylene oxide to form nonionic surfactants . In order to contain side reactions, the conversion is limited to about 20%, the oxygen content of the air is reduced to 3.5% by dilution with nitrogen. In this process, the conversion can be monitored by infrared analysis through the absorption intensity of the boron-oxygen stretching vibration of borate wax. The Bashkirov oxidation is used in special processes, for example in the production of cyclododecanone . In this process, cyclododecanol is obtained through the oxidation of cyclododecane with atmospheric oxygen , which is then dehydrated to cyclododecanone.
literature
- Friedrich Asinger : Chemistry and technology of paraffin hydrocarbons . Akademie Verlag, 1956.
- Wilhelm Keim , Arno Behr , Günther Schmitt: Basics of industrial chemistry. Otto Salle Verlag, 1985, ISBN 3-7935-5490-2 .
- Klaus Weissermel , Hans-Jürgen Arpe : Industrial organic chemistry: important preliminary and intermediate products. Wiley-VCH, 2007, ISBN 978-3-527-31540-6 .
- Birgit Pelzer-Reith and Reinhold Reith : “Fat from coal”? Edible fat synthesis in Germany 1933-1945 . In: Technikgeschichte , Vol. 69 (2002), H. 3, pp. 173–205.
Web links
- Welt im Film 121/1947 - September 19, 1947 (from 2:40 to 4:20 min.) , Fat from coal, newsreel from 1947 about the production of butter and soap at the Deutsche Fettsäurewerke
Individual evidence
- ↑ Karl Freiherr von Reichenbach, Franz Wilhelm Schweigger-Seidel: Creosote in chemical, physical and medicinischer relation . 2nd, presumably edition, Leipzig, Barth 1835.
- ↑ P. Gotthard Hofstädter: About artificial and mineral paraffin. In: Annals of Chemistry and Pharmacy . 91, 1854, pp. 326-334, doi: 10.1002 / jlac.18540910307 .
- ↑ CH Gill, Ed. Meusel: XLI. On paraffin and the products of its oxidation. In: Journal of the Chemical Society . 21, 1868, p. 466, doi: 10.1039 / JS8682100466 .
- ^ AG Pouchet: Effect of nitric acid on paraffin. In: Polytechnisches Journal . 214, 1874, pp. 130-132.
- ↑ P. Bolley: About some new properties of paraffin and about the paraffin baths. In: Polytechnisches Journal . 190, 1868, pp. 121-124.
- ↑ C. Engler, J. Bock, Ber. German chem. Ges. , 1879, 12, p. 2186.
- ↑ Patent US335962 : Converting Petroleum and similar Hydrocarbons into Acids. Published on February 9, 1886 , inventor: Eugen Schaal.
- ↑ a b c d e f g Arthur Imhausen: The fatty acid synthesis and its importance for securing the German fat supply. In: Colloid Journal . 103, 1943, pp. 105-108, doi: 10.1007 / BF01502087 .
- ^ Adolf Grün: The oxidation of paraffin. In: Reports of the German Chemical Society (A and B Series). 53, 1920, pp. 987-996, doi: 10.1002 / cber.19200530618 .
- ^ A b c Friedrich Asinger: Chemistry and technology of paraffin hydrocarbons . Akademie Verlag, 1956, pp. 491–493.
- ↑ a b c d Bernd Kaiser: The implications of economic policy framework conditions for the procurement of raw materials by international industrial companies and the resulting corporate strategies using the example of the Henkel Group . Inaugural dissertation to obtain the academic degree of Doctor of Economics and Social Sciences (Dr. rer. Pol.) From Friedrich-Alexander-Universität Erlangen-Nürnberg, 2009, pp. 142–154. ( PDF )
- ↑ a b c d Ralph Klein: Arthur Imhausen (1885–1951) . In: Wolfgang Weber (Hrsg.): Engineers in the Ruhr area (= Rheinisch-Westfälische Wirtschaftsbiografien ). tape 17 . Aschendorfer Verlagsbuchhandlung GmbH, Münster 1999, ISBN 3-402-06753-6 , p. 344-372 .
- ^ A b Karl T. Zilch: Synthetic fatty acids in Eastern Europe. In: Journal of the American Oil Chemists' Society . 45, 1968, p. 11, doi: 10.1007 / BF02679036 .
- ↑ a b c d e f Synthetic Fatty Acids and Detergents. (No longer available online.) In: BIOS Final Report No. 1722, Item No. 22. Archived from the original on April 2, 2015 ; accessed on March 14, 2015 . Info: The archive link was inserted automatically and has not yet been checked. Please check the original and archive link according to the instructions and then remove this notice.
- ↑ a b c d e Birgit Pelzer-Reith, Reinhold Reith : "Fat from coal"? Edible fat synthesis in Germany 1933–1945 . In: Technikgeschichte , 69, 2002, pp. 173–206.
- ↑ Michael Wildt: The dream of getting full. Hamburg 1986, ISBN 3-87975-379-2 , p. 17.
- ↑ Bruno Fischer: Ruhr area 1933–1945. The historical travel guide . Ch. Links Verlag, 2009, ISBN 978-3-86153-552-2 , p. 86.
- ↑ Berend Strahlmann: Imhausen, Arthur. In: New German Biography (NDB). Volume 10, Duncker & Humblot, Berlin 1974, ISBN 3-428-00191-5 , pp. 145 f. ( Digitized version ).
- ↑ Richard Breitman: The Architect of the "Final Solution". Heinrich Himmler and the extermination of the European Jews. Paderborn 1996, pp. 52-53.
- ^ H. Kraut: The Physiological Value of Synthetic Fats. In: British Journal of Nutrition . 3, 1949, p. 355, doi: 10.1079 / BJN19490049 .
- ↑ a b Hans Heinrich Meyer-Döring: Is the use of synthetic fatty acids for food safe? In: Clinical weekly . 27, 1949, p. 113, doi: 10.1007 / BF01471275 .
- ↑ a b c Twenty minutes of stealing coal, but double fat filtration . In: Der Spiegel . No. 49 , 1947, pp. 6 ( online ).
- ^ W. Heimann: Fette und Lipoide , Springer Verlag, 1969, ISBN 978-3-642-46190-3 , p. 7.
- ^ JW Vincent: Aspects of the Synthetic Fatty Acid and Synthetic Fat Industries in Germany. (No longer available online.) In: BIOS Final Rept. 805, 1946. 1946, archived from the original on April 2, 2015 ; accessed on March 18, 2015 . Info: The archive link was inserted automatically and has not yet been checked. Please check the original and archive link according to the instructions and then remove this notice.
- ↑ The triumph of the petroleum men . In: Der Spiegel . No. 31 , 1952, pp. 10-11 ( online ).
- ^ H. Fineberg: Synthetic fatty acids. In: Journal of the American Oil Chemistry Society. 56, 1979, p. 805A, doi: 10.1007 / BF02667451 .
- ↑ a b c d e f Friedrich Asinger: Chemistry and technology of paraffin hydrocarbons . Akademie Verlag, 1956, pp. 493-497.
- ^ Wilhelm Keim, Arno Behr and Günter Schmitt: Fundamentals of industrial chemistry. Technical products and processes, Otto Salle Verlag, 1985, ISBN 3-7935-5490-2 , p. 250.
- ↑ a b c d e G. Wietzel: Production of synthetic fatty acids by oxidation of paraffinic hydrocarbons with molecular oxygen. In: Chemical Engineering Science . 3, 1954, pp. 17-IN4, doi: 10.1016 / S0009-2509 (54) 80003-0 .
- ↑ a b c d Friedrich Asinger: Chemistry and technology of paraffin hydrocarbons . Akademie Verlag, 1956, pp. 498-499.
- ^ Francis Francis, Walter Frederick Millard and a .: XLVI - The velocity of oxidation of paraffin wax. Parts I-IV. In: Journal of the Chemical Society, Transactions . 125, 1924, p. 381, doi: 10.1039 / CT9242500381 .
- ^ Friedrich Asinger: Chemistry and technology of paraffin hydrocarbons . Akademie Verlag, 1956, pp. 478-490.
- ^ Friedrich Asinger: Chemistry and technology of paraffin hydrocarbons . Akademie Verlag, 1956, pp. 502–503.
- ↑ Patent DE739570 : Process for the production of oxidation products, such as fatty acids or alcohols, by oxidation of hydrocarbons. Published on August 12, 1943 , inventor: Karl Blass.
- ^ A b c Friedrich Asinger: Chemistry and technology of paraffin hydrocarbons . Akademie Verlag, 1956, pp. 500–502.
- ↑ Patent US2249708 : Method of oxidation of paraffin. Published July 15, 1941 , inventor: Mildred M. Hicks-Bruun.
- ^ NM Emanuel ': The Oxidation of Hydrocarbons in the Liquid Phase. Elsevier, 2013, ISBN 978-1-4831-4925-7 , p. 324 ( limited preview in Google book search).
- ↑ a b c d Friedrich Asinger: Chemistry and technology of paraffin hydrocarbons . Akademie Verlag, 1956, pp. 504–508.
- ↑ a b c d e Friedrich Asinger: Chemistry and technology of paraffin hydrocarbons . Akademie Verlag, 1956, pp. 508-513.
- ↑ Ludwig Mannes: About the by-products of paraffin oxidation. In: The chemistry . 57, 1944, p. 6, doi: 10.1002 / ange.19440570102 .
- ^ C. Engler, W. Wild: About the so-called activation of oxygen and about superoxide formation. In: Reports of the German Chemical Society . 30, 1897, p. 1669, doi: 10.1002 / cber.18970300295 .
- ↑ AN Bach: On the role of peroxides in the processes of slow oxidation. In: Zh. Soot. Phys-Chem. Soc. , 29, 1897, pp. 373-395.
- ^ P. George, EK Rideal, A. Robertson: The Oxidation of Liquid Hydrocarbons. I. The Chain Formation of Hydroperoxides and Their Decomposition. In: Proceedings of the Royal Society A: Mathematical, Physical and Engineering Sciences. 185, 1946, p. 288, doi: 10.1098 / rspa.1946.0019 .
- ↑ W. Langenbeck, W. Pritzkow: Investigations on the mechanism of paraffin oxidation, 1st part. In: fats, soaps, paints . 55, 1953, p. 435, doi: 10.1002 / lipi.19530550704 .
- ↑ W. Langenbeck, W. Pritzkow: Investigations on the mechanism of paraffin oxidation, 2nd part. In: fats, soaps, paints . 55, 1953, p. 506, doi: 10.1002 / lipi.19530550805 .
- ^ A b c Mihaly Freund, Gyula Mozes: Paraffin Products: Properties, Technologies, Applications. Elsevier Science Ltd., 1983, ISBN 978-0-444-99712-8 , p. 64.
- ↑ Wilhelm Pritzkow: About the autoxidation of ketones, I. Part .: The oxidation of cyclohexanone. In: Chemical Reports . 87, 1954, p. 1668, doi: 10.1002 / cber.19540871110 .
- ↑ TO Bashkirov, V. Kamzolkin: Synthesis of Higher Aliphatic Alcohols by Direct Oxidation of Paraffinic Hydrocarbons. In: Proc. World Pet. Cong. , 4, 1959, pp. 175-183 ( abstract ).
- ↑ F. Novak, V. Kamzolkin, Y. Talyzenkov, A. Bashkirov: Mechanism of the effect of boric acid on liquid-phase oxidation of paraffin hydrocarbons. In: Petroleum Chemistry USSR 7, 1967, pp. 59-64, doi: 10.1016 / 0031-6458 (67) 90010-X .
- ^ Wilhelm Keim, Arno Behr and Günter Schmitt: Fundamentals of industrial chemistry. Technical products and processes, Otto Salle Verlag, 1985, ISBN 3-7935-5490-2 , pp. 124-125.
- ^ W. Zenker: Infrared Method for the Direct Control of Paraffin-Wax Oxidation in the Presence of Boric Acid. In: fats, soaps, paints . 77, 1975, pp. 221-224, doi: 10.1002 / lipi.19750770605 .
- ↑ K. Weissermel, H.-J. Arpe: Industrial Organic Chemistry: Important preliminary and intermediate products. Wiley-VCH, 2007, ISBN 978-3-527-31540-6 , pp. 243-244.