Meissen porcelain
State Porcelain Manufactory Meissen GmbH
|
|
---|---|
legal form | GmbH |
founding | 1710 |
Seat |
Meissen , Germany![]() |
management | Tillmann Blaschke, Georg Nussdorfer |
Number of employees | 662 (December 31, 2014) |
sales | 37.9 million euros (2014) 39.2 million euros (2015) |
Website | www.meissen.com |
Meißner Porzellan (trade mark: Meissener Porzellan) is porcelain from the first European and leading manufacturer for a long time in the 18th century , which from its foundation until 1863 at the Albrechtsburg in Meißen , then produced it in its own factory.
On January 23, 1710, by decree of August the Strong, the public announcement of the establishment of the “Royal Polish and Electoral Saxon Porcelain Manufactory” in Dresden and on June 6, 1710 the establishment of their production facility in the Albrechtsburg in Meißen . In 1806 the manufactory passed from the ownership of the Crown to the ownership of the Saxon tax authorities as the “Royal Saxon Porcelain Manufactory Meissen” . In the course of the constitutional renewal of state property, the company called itself from 1918 "State Porcelain Manufactory Meissen". In the GDR the manufacture was a state-owned company . Since June 26, 1991 it has been operating as the “Staatliche Porzellan-Manufaktur Meissen GmbH”, of which the Free State of Saxony is a partner . The world's leading porcelain manufacturer is one of the best-known and oldest German luxury brands internationally.
The crossed course swords have become a symbol for the manufactory . The sword mark had prevailed against the AR mark ("Augustus Rex") and the Mercury rod from 1731, when all porcelain from Meissen had to be marked with a mark . To identify goods that are of limited use in terms of quality, but also to identify white goods, grinding lines are applied to the sword marks after the glaze. The first markings of this kind can be found on parts from around 1764.
history
Invention of European porcelain
The alchemist Johann Friedrich Böttger claimed at the beginning of the 18th century that he could make gold from worthless materials . When this was brought to the attention of the Saxon Elector August the Strong in Dresden , he had Böttger locked up in the maiden bastion to have him produce gold. After a few years Johann Friedrich Böttger was convinced by Ehrenfried Walther von Tschirnhaus to take part in his attempts to manufacture porcelain and began to work in porcelain research at the end of September 1707.
The experiments led to the invention of European porcelain in 1708. This was preceded in 1707 by the invention of marbled tiles and red Böttger stoneware ( jasper porcelain ), which was produced alongside porcelain for a few decades. In 1710, the Elector of Saxony , August the Strong, patented the production as a client and tried to keep the process a secret.
During this time, Tschirnhaus was responsible for the scientific and organizational supervision of the project together with the Freiberg hut specialist Gottfried Pabst von Ohain , the doctor Jacob Bartolomäi and the Chamber Councilor Michael Nehmitz. In addition to Böttger, the Freiberg smelters and miners David Köhler, Samuel Stöltzel , Johann Georg Schubert and Paul Wildenstein were also involved. The Freiberg stove builders Balthasar Görbig and Andreas Hoppe contributed further knowledge . Gottfried Pabst von Ohain deserves the credit for having contributed kaolin as the component required for the production of white (instead of gray) porcelain.
From January 1708, almost ten months before Tschirnhaus's death on October 11, 1708, August the Strong handed over the management of research work on the porcelain project to Böttger. The technical management continued to be the responsibility of Ehrenfried Walther von Tschirnhaus. The invention is documented as of January 15, 1708. Three months later Tschirnhaus was appointed Privy Councilor and Director of the manufactory to be founded by the King, furthermore August the Strong ordered "[...] that we have paid out 2561 thalers to Herr von Tschirnhausen [...]" Tschirnhaus asked for the title first to be allowed to lead after the start of production. After inventing the necessary hard porcelain glaze and the first decorative colors (1709), Böttger began working on factory production.
Foundation and heyday of the manufactory
By decree of January 23, 1710, the "Royal Polish and Electoral Saxon Porcelain Manufactory" was founded. Their first production facility was the Albrechtsburg from June 1710. Above all, it offered protection for the manufacturing secret of the world's first hard porcelain . In order to protect this, only a small group of employees was given a fraction of the secret. Nevertheless, the escaped arcanist Samuel Stöltzel managed to bring the recipes to Vienna , where the first competition for Meissen porcelain arose in 1718 with the Viennese porcelain factory.
The “white porcelain” for which Böttger registered a patent in 1709 together with the glaze and grinder was still missing the feldspar ; it therefore had a short sintering interval with a consequently high error rate. After the first goldsmith-style shapes, smooth vessels were produced and decorated with the onglaze colors developed by Johann Gregorius Höroldt . Preferred motifs were landscapes, chinoiseries, and framed foliage and ribbon work . Around 1740, the traditional Chinese and Japanese decors were replaced by "German flowers". In addition, the so-called onion pattern in underglaze blue came onto the market.
The figurative sculpture played a large part in the manufactory's production program. As early as the time of August the Strong, in addition to the extensive production of sumptuous and decorative tableware for the needs of the Dresden court, miniatures and sumptuous figures were made for representative and decorative purposes. Johann Gottlieb Kirchner , known for his large white animal figures, was the modeller until 1731 . After that, his colleague and successor Johann Joachim KÄNDER not only determined the development of figurative sculpture in Meissen for a generation, but also that of other German manufacturers.
The Royal Porcelain Manufactory experienced a second bloom from 1774 to 1814 under Count Camillo Marcolini . The colorfully decorated small sculptures that the French sculptor and master model of the manufactory Michel Victor Acier (1736–1799) and his colleague Johann Carl Schönheit (1730–1805) created are well known. In addition, biscuit figures were made, some based on classic models. In this epoch, which was characterized by classicism , the decline began before the end of the 18th century, which culminated in the copying of forms from earlier epochs and imitations of porcelain from Sèvres and Wedgwood stoneware .
Coffee, tea and mocha pots with chinoiserie , around 1735
JJ Kellers : "Bust of Gottfried Schmiedel", 1739
JJ KÄNDER : "Cavalier at the desk", around 1740
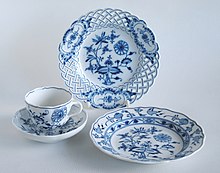

"The gardener girl with dog", "The goose girl", "The lady with cat", 1902

From the Wars of Liberation to the end of the Second World War
In the first quarter of the 19th century, the manufacture had to struggle with major sales difficulties. Significant orders from the royal houses, which were ravaged by war and debt, were rare. The out-of-date production program also contributed to the poor economic situation, which was associated with a significant decline in the number of employees. After visiting the factory in April 1813, Johann Wolfgang von Goethe wrote: “It is unique and almost unbelievable that you can find little in what you want to own in your household.” He judged the exhibition as “one of everything that is no longer like and can no longer please, and not just one, but in whole masses by hundreds, even thousands. ”Many German porcelain manufacturers had to give up during this time. In 1810, consideration was given to shutting down the Meißner factory. However, it survived the crisis and in 1831 was subordinated to the Saxon Ministry of Finance as a state institute.
As successor to Camillo Marcolini , Bergrat Carl Wilhelm von Oppel was entrusted, who headed the factory from 1814 to 1833. He implemented necessary changes in the artistic, technical and commercial areas. The main credit for these fundamental technical and technological improvements goes to Heinrich Gottlieb Kühn, who was appointed factory inspector in 1814 . He introduced the round furnace and in 1827 invented " bright gold ". In 1848 Kühn became director of the manufacture. In the middle of the 19th century, numerous shapes and decorations were developed under the influence of famous members of the Dresden Art Academy , such as Gottfried Semper , Ernst Rietschel , Julius Schnorr von Carolsfeld . The "academy porcelain" emerged as the epitome of the highest level of artistry at the time.
In order to enable more efficient work processes, the production facility was relocated from the Albrechtsburg to the newly constructed building in the Meißner Triebisch Valley , the current location, from 1863 .
The return of German and foreign royal houses to their heyday was reflected in the second half of the 19th century in increasing orders for traditional Meissen ornamental and crockery porcelain in the form language of the Baroque and Rococo. A clear recovery of the company began, in which the upper middle class of that time played an increasing part. However, this development was not conducive to the artistic concerns of the manufactory. Embellishment of traditional porcelain was often in the foreground; only sometimes are new creations within the framework of so-called historicism . The remarkable achievements of the 19th century, on the other hand, included a few unique pieces that were specially made for trade fairs and exhibitions. These included, for example, the Goethe and Dürer statuettes by Christian Daniel Rauch , the Impressionist flower still lifes by Julius Eduard Braunsdorf and the Pâte sur Pâte paintings based on the French model. The proportion of simple utensils in the production volume increased steadily during this time. In addition to popular decors such as “ Full of green wreaths ”, “Scattered flowers” and “Meissen rose”, the onion pattern decor became an absolute bestseller.
The low successes at the Paris World Exhibition in 1900, together with the increasing enthusiasm for porcelain from the Royal Porcelain Manufactory in Copenhagen, led to a change in tableware design and decoration. With discreet, high-quality onglaze colors on artistically higher-quality utility porcelain, the company consciously oriented itself towards the growing demands of medium-sized businesses. The first ideas from Art Nouveau came from Konrad Hentschel , and the large, non-relief “T-smooth” service that was created later impressed with its aesthetic “wing and maple patterns”.
In addition to their own efforts, attempts were made to include freelance artists in the porcelain design, but this did not produce any resounding success. The outsiders included the architect Richard Riemerschmid and the versatile Belgian painter, graphic artist and architect Henry van de Velde . However, both were disappointed in the expectation of being able to influence the tableware designs for mass consumption. The other Art Nouveau services and decorations by Rudolf Hentschel , Otto Voigt , Theodor Grust , Joseph Olbrich , Arthur Julius Barth and Friedrich Offermann could not dethrone the onion pattern. Art Nouveau was more successful in figurative sculpture. The model of the ball player bought by the Berlin sculptor Walter Schott in 1897 was one of the most popular small sculptures in the following years. Paul Walther gave decisive impulses to animal sculpture ; Philipp Lange and Theodor Eichler modeled folk groups and stylish small sculptures of sophisticated women. The Munich sculptor Jacob Ungerer created figures from the Rococo theme catalog for the manufactory during this period .
After the First World War and the November Revolution, Max Adolf Pfeiffer took over the overall management of the company in 1919. The artistic development of the model range was his particular concern. Shortly after joining the factory management in 1913, he engaged the painter, illustrator and sculptor Paul Scheurich , who led Meissen figurative porcelain sculpture to a new high point and found worldwide recognition. Other freelance artists working for Meissen were Max Esser , Ernst Barlach and Gerhard Marcks . Pfeiffer had already worked with these artists in the Schwarzburg workshops for porcelain art he founded. In the 1920s and 1930s, Emil Paul Börner developed simple and shapely tableware and decors that were a model for many porcelain factories. The first porcelain carillon at the Frauenkirche (Meißen) , which was also created by Börner, is famous .
The dismissal of director Max Adolf Pfeiffer by the National Socialists could not be prevented, nevertheless Pfeiffer was head of the Königliche Porzellan-Manufaktur Berlin from 1938 to 1946 . Production was continued with the active participation of Paul Börner , Paul Scheurich was awarded several gold medals at the Paris World Exhibition in the mid-1930s. During the Second World War , production could be maintained until April 1945, despite armaments restrictions.
1945-1990
After the end of the war , some production facilities were dismantled by the Soviet military administration from June to September 1945 . Under the director Herbert Neuhaus , work was resumed with initially around 200 people, including 50 painters and 30 designers. Meißner porcelain could already be seen again at the first Leipzig post-war fair in spring 1946. On August 1, 1946, the porcelain factory was taken over as a branch of the Soviet joint-stock company "Zement" due to the German reparation obligations. In 1950 it was still operating as the State Stock Corporation for Building Materials "Cement" Porcelain Manufactory Meißen. The factory was returned from Soviet ownership on July 1, 1950. It became a state- owned company with the name "VEB Staatliche Porzellan-Manufaktur Meißen". In 1950 Waldemar Wüstenmann became director of the manufactory. From 1953 a separate department "Artistic wall design" was set up in the manufactory. So far, many murals made of Meissen porcelain for the interior design of buildings with different motifs and manufacturing techniques have been produced here. In December 1958, the works of art in the porcelain exhibition hall were returned by the Soviet Union. In the years that followed, the manufacture grew rapidly and developed into the eighth strongest foreign exchange broker in the GDR. In 1969 Karl Petermann was appointed director. He introduced an almost fully automatic production method, which made the former luxury goods mass-produced for everyone. Petermann continued to place the coexistence of traditional and free artistic forms of expression in the foreground of his efforts.
Initially, the manufactory pursued the traditional production program, but from the 1960s tried again to find contemporary forms of expression. The “Artistic Development” department was founded. Ludwig Zepner succeeded in creating the most important new creation with the service ensemble “Large Cutout”. The subtle underglaze decoration “Orchid with branch in blue” by Heinz Werner as well as the overglaze decors “Almond trees”, “1001 Nights” and “Blossoms” by Heinz Werner and Rudi Stolle stood out among the painterly decorations . Peter Strang contributed new creations for table essays and representations from the stage arts . Since the late 1970s, a one-off production has also developed in which the manufactory's artists can realize their individual ideas.
- Block of four Meissen porcelain post of the GDR 1982
Figure of Oberon (1969)
Post-turnaround time
Since June 26, 1991, the manufactory has been operating as "Staatliche Porzellan-Manufaktur Meissen GmbH", whose sole shareholder is the Free State of Saxony and whose nominal capital is eight million euros. Even after reunification, the production program included contemporary figures, vessels and dishes, but mainly still forms of classic models from the 18th century, as well as dishes with overglaze decorations and classic and redesigned onion pattern decorations. After three years of development, the modern wave game service form, designed by Sabine Wachs , was presented in 1996 , which is characterized by a sweeping shape, supplemented by a wave-like surface structure created by Jörg Danielczyk .
In the course of the restructuring caused by the turnaround , the number of employees fell from around 1800 to 784 between 1990 and 2009. For several years the company was in economic difficulties. Sales in the core porcelain business decreased between 2001 and 2009 from € 41.7 million to € 31.5 million. The operating loss in 2008 was six million euros.
In August 2010, the number of employees was further reduced from 784 to 604 on the basis of internal profitability calculations. The "Artistic Development" department was dissolved. As part of the strict renovation measures, around 20 cubic meters of Meissner porcelain inventory worth 2.6 million euros was destroyed in October 2010 in order to “help optimize costs and secure the value of the brand”. In the same year, the manufactory began to operate under the umbrella term Meissen Couture in the fields of architecture, interior design, watches, jewelry and fashion. If no porcelain was required, these products were largely made outside of the production facilities in Meißen and were made to order abroad. The subsidiary "Meissen Italia srl." Established a worldwide sales center in Milan, Italy. Other subsidiaries of the manufactory are "Meissen Asia Pacific Ltd." based in Hong Kong and "Meissen UK Ltd." based in London.
In February 2011, the Federal Cartel Office began investigating the State Porcelain Manufactory Meissen on suspicion of illegal price fixing and market sharing, and the business premises in Meissen were also searched. This suspicion was not confirmed in the course of the investigation and was dropped. After the provision for possible anti-trust fines was released, the Group was able to report a profit of 1.5 million euros in 2011. In 2012, the state-owned company posted a loss of 1.1 million euros. The reason for this was that so-called hidden taxes were dissolved. The operating result, however, grew.
present
In order to secure the cultural and historical values of the manufactory, the Free State of Saxony founded the Meissen Porcelain Foundation GmbH in 2014 , which bought all model shapes, recipes and museum objects from the State Porcelain Manufactory Meissen GmbH for six million euros. In accordance with the corporate purpose of the Porzellan-Stiftung GmbH, the molds are only made available to Meissner Porcelain Manufactory for a fee.
In March 2015, Managing Director Christian Kurtzke left the company, in the middle of the restructuring he initiated in 2008 from a porcelain manufacturer to a luxury company. There had been early resistance to Kurtzke's corporate strategy; The spokesman for a local citizens' initiative was Reinhard Fichte, former General Director of the VEB Staatliche Porzellan-Manufaktur Meißen . There was also a radical change in the supervisory board : In addition to the replacement of former Prime Minister Kurt Biedenkopf as chairman, the two deputies were also dismissed. One reason for this is the granting of loans from state funds of around EUR 10 million for 2014 alone - without the approval of the state parliament, as the Saxon State Audit Office criticized in October 2015.
The company is currently run by Tillmann Blaschke and Georg Nussdorfer. In the future, the manufactory should concentrate on its core business, porcelain, instead of on interchangeable luxury products. Here, the production of cheaper series is intended, but also the revitalization of historical models with new decorations and for new purposes.
In November 2019, at a works meeting called at short notice, the management announced that it would cut a third of the positions by the end of March 2020 and reduce the number of employees from 619 to 418. The unprofitable brand stores in Germany that were set up only a few years ago are also to be closed. The Meißner state parliament member Daniela Kuge blamed the changing strategy of the management for this development: “Unfortunately, the unfortunate situation as we find it today does not come as a surprise to me. It is the result of the work of a manager who has neither developed a feel for the manufacture nor for the people who work there. It is precisely these people who now have to pay a high price ”. There are “contacts to the employment agency to find solutions for affected employees”.
Museums and collections
In January 1916, the show hall opened its doors on a property next to the factory on Talstrasse. The company museum was run under its own management until 2014, and over the years it was expanded to include a demonstration workshop and a visitor center built in 2006. Since 2015, the Meissen porcelain Foundation GmbH serves as the owner of the museum by the Porcelain Museum . Here Meissen porcelains from 1710 to the present are shown in chronological order to illustrate the design development of the various epochs.
The most important collection of historical Meissen porcelain is housed in the southern arched galleries of the Dresden Zwinger . Its core holdings go back to the collection of East Asian and Saxon porcelain begun by August the Strong around 1715, which grew to become the largest in Europe in just two decades. It was originally presented in the chinoisen interiors of the Dutch Palace on the northern bank of the Elbe, which was expanded into the Japanese Palace between 1727 and 1733 . The porcelain collection, comprising around 20,000 objects, is part of the Dresden State Art Collections.
The largest and most important special collection after Dresden is exhibited in Lustheim Palace near Munich. After extensive renovation in 1971, the world-famous Meissen porcelain collection of the industrialist Ernst Schneider was established as the first branch museum of the Bavarian National Museum . The presentation of over 2000 exquisite porcelains offers an insight into the impressive diversity of the products made by the Meissen manufactory and their almost inexhaustible inventiveness in the first decades from its foundation in 1710 to the time of the Seven Years' War .
With over 1400 objects, the Rijksmuseum Amsterdam houses the most important collection of Meissen porcelain outside of Germany that goes back to the banker Fritz Mannheimer .
The Hetjens Museum in Dusseldorf showed from October 2018 to March 2019 arguably the world's largest private collection of Meissen Blue Onion, which together contributed the Munich porcelain lovers Hartmut Lubcke in over 25 years.
Brands and marks of the Meissen porcelain
History of the trademark
Due to the competition arising in Vienna, the necessity of being able to identify the porcelain without any doubt was recognized. Inspired by the imperial brands ( nien-hao ) on Chinese porcelain, which, however, do not primarily mark the place of manufacture, but rather the period of manufacture, a manufacture brand was developed that was applied to the porcelain. With the Saxon course swords as a model, this brand developed into the world-famous "crossed blue swords". In the first few years there were attempts to develop such a trademark, but it was not until the introduction of the blue underglaze color in 1720 that a high level of protection was offered, which largely ruled out forgeries and imitations.
Since then, this marking has been applied by hand painting, but initially there was no uniform orientation. The signs were only applied irregularly and according to the wishes of the client and buyer. The most frequently used brand was the monogram "AR" for "Augustus Rex" (ie "King August"), which refers to the Saxon Elector Friedrich August I (called "August the Strong", as August II. King of Poland) relates.
The breakthrough came later with the marking of porcelain with swords. In addition to the pair of crossed swords, hand-painted sequences of letters were common up to around 1730, such as KPM for “Royal Porcelain Manufactory”, MPM for “Meissen Porcelain Factory” or KPF for “Royal Porcelain Factory”. There were also various other letter combinations. From 1731, the sword figurative mark prevailed on the basis of a written order from the electoral court in Dresden.
The swords initially turned out very different. Their characteristics varied and repeated over the years, sometimes making timing difficult. A six-pointed star under the swords or between the crossguards is characteristic of the Marcolini period (1774–1814) . The typical "Knauf sword mark" with its button-shaped knobs appeared in the middle of the 19th century and was retained in variations until 1924. From 1924 there were correctly drawn swords bent towards each other without knobs, which until 1934 had an additional point between the blades. The individuality of earlier periods was finally ended.
The registration of the brands of the porcelain manufactory took place after the introduction of the Reich Law on trademark protection in Germany on May 20, 1875. The trademarks "Böttgersteinzeug" and "Meissener Porzellan" were registered in 1919 and 1985.
Additional character
In addition to the obligatory trademark and the characters assigned to the sword mark, the following additional characters can appear on Meissen porcelain:
- Chandelier sign
- Inventory mark of the type "KHCW" in underglaze blue for "Royal Court Confectionery Warsaw"
- technical embossing marks on dishes, such as those used to indicate the size of bowls
- Form numbers on ornamental china
- Embossing and scratch marks from lathe operators, formers and embossers
- Painter's mark on the glaze and in underglaze blue
- Sanding lines used to mark white goods or defective goods
- special brands and symbols are anniversary and dedication brands
- Year mark, struck in the bottom of each piece since 1948; this makes it possible to determine the year of manufacture of the white porcelain without any doubt
Extraction of raw materials - the Aue and Seilitz kaolin pits
The kaolin required for the experiments to manufacture Meissen porcelain was initially mainly obtained from a deposit near the Aue . As early as 1698, extensive kaolin deposits were discovered here, which were mined from 1700 by the “ White St. Andreas Fundgrube ” owned by Veit Hans Schnorr von Carolsfeld . The kaolin, the so-called "Schnorrsche Earth", was needed, especially for the production of paint in the surrounding blue paint factories . In the course of the attempts to manufacture porcelain in 1708, all Saxon mining authorities had to send samples of white clay to Dresden. Their investigations showed the particular suitability of the kaolin from the “White St. Andreas Treasure Trove” for porcelain production, which, after replacing the Colditzer clay first used by Böttger, advanced to become the sole raw material supplier for the royal porcelain manufactory Meißen, founded in 1710. Strict safety regulations applied to the mine: miners and carters were obliged to maintain secrecy, non-employees were not allowed to enter or drive the mine (this requirement was only relaxed in 1838). In addition, the Auer kaolin was no longer allowed to be used to produce blue paint, and it was also not allowed to be exported. The sentence even stipulated death by hanging for violators . At times 30–40 miners were employed in mining and processing. At the beginning of the 19th century, the deposits were exhausted after the mine had delivered around 6,500 tons of kaolinite to Meissen between 1713 and 1815. After further exploration, another 1500 tons could be extracted by 1851 (last delivery). After that, the deposit was considered to have been completely dismantled, so that the state porcelain manufactory ceased operations in 1855.
More than 100 years earlier, from 1750, the porcelain manufacturer had other kaolin stores in Saxony explored. In 1764 a farmer, who was employed as a blue painter at the factory, discovered a kaolin deposit while plowing in Seilitz , only a few kilometers from Meißen. Parts of the occurrence of the up to 13 m thick "Seilitzer Earth" proved to be particularly suitable for porcelain production. They exceed all other known occurrences in terms of whiteness , because on the one hand it is a primary occurrence (no relocation of the kaolin after its formation) and the kaolin is protected by a layer of rock surrounded by water and metal oxide. In the year of the discovery, mining in opencast mining began in Seilitz , and in 1825 underground mining began . The Meißner manufactory had been in sole possession of the Seilitzer mining rights since 1814. The Seilitz kaolin mine is a supplier of raw materials for the production of Meissen porcelain. The extraction amounts to around 150 to 300 tons of raw kaolin per year, whereby the extraction is done manually with a pick, shovel and hammer drill due to the softness of the material. Two miners are employed in the quarrying itself, making the mine the smallest active and oldest kaolin mine in Europe still in operation.
Money made from bisque and Böttger stoneware
From 1920 to 1921, the state-owned porcelain factory in Meißen produced porcelain money from Böttger stoneware and bisque porcelain. The reason was the lack of change. After the Meissen manufactory also submitted the first test pieces of a so-called Saxony money in 1920, the State of Saxony decided at the beginning of 1921 as the first state to put emergency money into circulation. The designing artist Emil Paul Börner always succeeded in adding symbols to the coins, in addition to the obligatory indication of value, year and origin, with typical motifs of branches of production and their products, historical buildings and regional things. The sword mark on each coin indicated its origin from the Meissen porcelain factory. The Meissen Manufactory was directly commissioned by the Saxon State, represented by the Minister of Finance, to start producing money for Saxony. With the award of the state contract, the Saxon Ministry of Finance demanded special security precautions for the newly established coin department from the manufactory. Coins made from Meissen porcelain were also in demand abroad. As early as 1920, coins worth 2 pesos were made from Böttger stoneware on behalf of Guatemala . When in 1921 there were further orders from cities, municipalities and companies in Germany, the necessity arose to work in multiple shifts.
The porcelain money should not be confused with medals or tokens made of porcelain that had no official currency function. Additional money, emergency money or tokens in the form of city coins, company coins and donation coins were made in the Meissen manufactory. In 1924, tokens were made for the casino in Sopot .
Medals made of bisque and Böttger stoneware
Porcelain medals, plaques and memorial plaques made of brown Böttger stoneware or white bisque porcelain were designed, modeled, designed and produced in the most varied of sizes and shapes in the Meissen porcelain factory as early as the 18th century. They can often also be decorated in color. All pieces are considered examples of medal art in professional circles and have at the same time become coveted collectibles in numismatics. In the Meissen manufactory, they are mainly created for souvenir purposes, for anniversaries of cities, communities and organizations. In addition, these pieces serve as gifts of honor or awards, as well as commemoration. These products can be ordered by private customers. The crossed course swords can be found on all delivered products of this type as a sign of origin and trademark. Over the centuries, from a design point of view, concessions had to be made in order to do justice to the respective concerns of the client. Paul Scheurich, Emil Paul Börner, Max Esser, Manfred Wünsche and Silvia Klöde are among the best-known medalists at the Meissen Manufactory.
Personalities around the Meissen porcelain of the 18th century
- Johann Friedrich Böttger , one of the inventors, introduced factory-made porcelain
- Johann Gregorius Höroldt , porcelain painter, designer and color developer
- Carl Friedrich Wenzel , Improvements to the Underglaze Cobalt Blue
- Johann Joachim Kellers , porcelain designer
- Friedrich August Köttig , inventor of the Meissen translucent stone blue
- Heinrich Gottlieb Kühn , inventor of bright gold and shimmering colors
- Camillo Marcolini , electoral politician and head of the manufactory
- Ehrenfried Walther von Tschirnhaus , thought leader and inventor of European porcelain
Well-known artists of the manufactory
- Georg Jahn became a porcelain painter at the age of 14. In the following five years (1883–1888) his artistic talent was recognized and he was sent to the Dresden Art Academy (1888–1890) on a scholarship.
- Konrad Hentschel , first as a drawing student in Meißen in 1889, from 1897 modeler at the manufactory. He is particularly famous for his Hentschel children, a series of twelve children playing.
- Henry van de Velde , worked as a porcelain designer from 1903 to 1904
- Richard Riemerschmid , worked as a porcelain designer from 1904 to 1905
- Oskar Erich Hösel , from 1904 to 1929 Hösel was the design director of the Meissen manufactory.
- Paul Scheurich , worked as a porcelain artist from 1918 to 1936
- Max Esser , from 1920 to 1931 worked as a porcelain artist, from 1924 as head of a master's atelier
- Emil Paul Börner , from 1930 to 1937 Börner was director of the artistic departments of the Meissen manufactory. He created the first working porcelain carillon (1929).
- Heinz Werner , from 1943 apprenticeship as a painter, 1959 to 1962 visiting student at the Dresden University of Fine Arts, then artist in artistic development
- Ludwig Zepner (1931–2010), long-time artistic director of the manufactory (1960–1990), inventor of tunable organ pipes made of porcelain (for the Meißner Frauenkirche ).
- Peter Strang , active as a sculptor from 1968, from 1993 to 2001 artistic director of the manufactory
- Rudi Stolle , since 1970 porcelain artist in artistic development, since 1976 production of unique pieces (profile-defining)
- Volkmar Bretschneider , from 1976 porcelain artist in artistic development; Production of unique items (determining the profile)
- Andreas Ehret, from 1987 master student of Peter Strang, from 1991 to 1994 and 1999 from 2007 production of unique pieces (profile determining)
- Olaf Fieber, from 1987 master class student of Peter Strang, from 1991 to 2005 production of unique pieces (profile determining)
- Jörg Danielczyk , student of Peter Strang, was appointed artistic director of the design / white production department in 1994 . From 2011 to 2018 he held the position of chief sculptor
Decor types
- Reliefzierate and cut ornaments: Staff Relief , Alto ornamental , Sulkowski-Ozier , Brandenstein-relief , Marseille-relief , swan design , Doulong , Gotzkowsky , B-shape , X shape , Brühl MOORISH Allerlei , Wellenspiel -relief, Great Neck -relief
- Indian decors in colorful on-glaze painting: old rich yellow lion , Kakiemon porcelain , dragon pattern ( Ming dragon , court dragon ), table pattern , rock and bird painting, Indian purple and Indian green
- Indian decors in underglaze blue: everlasting flower pattern , onion pattern , rock and bird painting,
- Flower decors: woodcut flowers , German flowers , Indian flowers , Marcolini flowers, mannerist flowers ( Meißner rose , scattered flowers ), naturalistic flowers, meadow flowers, orchid with branch in blue
- Wreath, garland and thread decors: full green vine wreath (colloquially vine leaves), floral wreath, festoon pattern, leaf edge pattern
- Art Nouveau decors: crocus decor, wing decor, maple decor, clover leaf decor, primrose decor, arnica decor, snowdrop decor, umbel decor, line decor, sweet peas decor, Van de Velde decor, Riemerschmid decor
- Striped decors
- Aquatint
In addition, there are hundreds of other tableware decors, which, however, are carried out much less frequently and rarely appear on tableware. These include, for example, fruit, bird and butterfly decors, special flower decors, hunting scenes, landscape and fairytale decors as well as Indian decors.
- Overview of the different decors of Meissen porcelain
Ming dragon , red
Scattered bouquet with insects
- Full of green wreath
(here with gold edge) Blue panicle decor
Roses in Marcolini style ( house painting ?)
Wave game , wild poppy seeds
particularities

- Moldings of Meissner medals of honor from the GDR were made as prototypes using the bronze casting process .
- Entire picture walls were made in the Meissen porcelain factory . This special type of artistic wall design was created as small-format wall pictures, often as large-format picture walls, by the corresponding artist or several artists, often as commissioned works.
- The first exhibition of contemporary porcelain art took place in the Albrechtsburg in 2016 . After the second edition in 2018, this show will continue to take place every two years.
See also
- Sample Bourgeois Meißen from the Teichert-Werke
- List of porcelain manufacturers and manufacturers
literature
- Karl Berling : Meissen porcelain and its history. Brockhaus, Leipzig 1900 ( digitized version )
- Reimo Gareis: Meissen porcelain. An encounter . 1st edition. Krone, Leichlingen (Rhineland) 2004, ISBN 3-933241-98-7 .
- Jürgen Helfricht : Little ABC of Meissen porcelain . 4th edition. Husum, Husum 2017, ISBN 978-3-89876-552-7
- Johannes Just: Meissen Art Nouveau porcelain. Edition Leipzig, Leipzig 1983, ISBN 3-570-09020-5 .
- Jürgen Karpinski: Beautiful decors on Meissen porcelain. Edition Leipzig, Leipzig 2001, ISBN 3-361-00529-9 .
- Christian Beatus Kenzelmann: Historical news about the Royal Porcelain Manufactory in Meissen and its founder Johann Friedrich Freiherrn von Böttger . Gödsche, Meissen 1810 ( digitized version )
- Royal Saxon Porcelain Manufacture Meissen in the Kingdom of Saxony, oldest porcelain factory in Europe, founded in 1710 . Klinkicht & Sohn, Meissen 1896 ( digitized version )
- Caren Marusch-Krohn: Meissen porcelain 1918–1933 - The Pfeiffer period. Edition Leipzig, Leipzig 1993, ISBN 3-361-00402-0 .
- Ingelore Menzhausen : Old Meissen porcelain in Dresden. Henschelverlag Art and Society, Berlin 1988, ISBN 3-362-00142-4 .
- Rainer Rückert : Meissen porcelain 1710–1810. Exhibition in the Bavarian National Museum in Munich . Hirmer, Munich 1966.
- Rainer Rückert: Biographical data of the Meissen manufacturers of the 18th century (catalog of the Meissen porcelain collection, Ernst Schneider Foundation, Lustheim Palace, Oberschleißheim in front of Munich, branch museum of the Bavarian National Museum in Munich, supplement). Bavarian National Museum, Munich 1990, ISBN 3-925058-13-3 .
- Alessandro Monti: The price of the “white gold” - pricing policy and strategy in the mercantile system using the example of the Meissen porcelain manufacture 1710–1830. Oldenbourg, Munich 2011, ISBN 978-3-486-70435-8 .
- Adriano Sack: Meissen is renewing itself. In: Welt am Sonntag compact , December 9, 2018, pp. 40–41
- Bettina Schuster: Meissen. Stories about the past and present of Europe's oldest porcelain factory. Orbis, Munich 1996, ISBN 3-572-00811-5 .
- Pauline Gräfin von Spee, The classicistic porcelain sculpture of the Meißen Porcelain Manufactory from 1764–1814 , Diss. Bonn 2004.
- Günther Sterba : Utility porcelain from Meissen. Edition Leipzig, Leipzig 1988, ISBN 3-361-00193-5 .
- Otto Walcha : Meissen porcelain. From the beginning to the present. 8th edition. Verlag der Kunst, Dresden 1986, ISBN 3-364-00012-3 .
- Julia Weber : Meissen porcelain with decors based on East Asian models. Ernst Schneider Foundation in Lustheim Palace. Hirmer, Munich 2013, ISBN 978-3-7774-9091-5 .
- Peter-Christian Wegner: Remarkable motifs on Meissen porcelain from the Marcolini period . Ludwig, Kiel 2016.
- Ernst Zimmermann : The invention and early days of Meissen porcelain. A contribution to the history of German ceramics . Reimer, Berlin 1908 ( Textarchiv - Internet Archive ).
- The Royal Porcelain Manufactory in Meissen . In: Louis Oeser (Ed.): Album of the Saxon Industry . Volume 1. Louis Oeser, Neusalza 1856, pp. 84–85 ( Wikisource )
- Germany's great workshops. No. 7 . In: The Gazebo . Issue 7, 1869, pp. 107–110 ( full text [ Wikisource ]).
Movies
- Blue swords on white gold - Real Meissen. Documentary, Germany, 2016, 28:22 min., Script and director: Anne Mehler, production: MDR , series: Der Osten - Discover where you live , first broadcast: January 24, 2017 on MDR, synopsis by MDR, online video available until January 24, 2018.
- White gold in the red - where is the Meissen porcelain factory going? Documentary, Germany, 2015, 30:00 min., Script and director: Birgit Menzel, production: MDR , series: Exakt - Die Story , first broadcast: April 15, 2015 on MDR, synopsis by MDR.
- 300 years of porcelain from Meissen. Documentary, Germany, 2010, 4:45 min., Book: Christina Küfer, camera: Rick Rennington, production: Deutsche Welle (DW), series: euromaxx , first broadcast: January 23, 2010 on DW, online video from DW.
- The secret of the white gold. Documentary film, Germany, 2000, 42:30 min., Script and direction: Christian Twente and Nina Koshofer, production: ZDF , series: Sphinx , first broadcast: January 1, 2001 on ZDF, summary by 3sat , online video .
Web links
- State Porcelain Manufactory Meissen
- Dresden porcelain collection. In: Staatliche Kunstsammlungen Dresden
- Meissen porcelain collection Ernst Schneider Foundation in Lustheim Palace
Individual evidence
- ↑ a b ts / dpa : Meissen boss Kurtzke goes to Porsche Design . In: Manager Magazin , March 9, 2015.
- ↑ a b c Finances - Production Company - State Porcelain Manufactory Meissen GmbH. (No longer available online.) Saxon State Ministry of Finance, archived from the original on November 4, 2016 ; accessed on December 30, 2016 . Info: The archive link was inserted automatically and has not yet been checked. Please check the original and archive link according to the instructions and then remove this notice.
- ↑ a b Staatliche Porzellan-Manufaktur Meissen GmbH - 2014 annual financial statements (PDF; 144 kB; 14 pages) November 17, 2015, accessed on February 12, 2017 .
- ↑ dpa : Meissen in the red. Porcelain manufactory makes another loss . In: Handelsblatt , July 5, 2016.
- ↑ The State Porcelain Manufactory Meissen . Section: onion misunderstanding. In: starcookers.de , accessed on February 12, 2017.
- ↑ Klara van Eyll , Renate Schwärzel: German Economic Archives. Evidence of historical sources in companies, chambers and associations of the Federal Republic of Germany. Volume 1. 3., completely revised edition, Steiner, Stuttgart 1994, ISBN 978-3-515-06211-4 , p. 250, excerpt in: Google books .
- ↑ Florian Langenscheidt , Bernd Venohr (Hrsg.): Lexicon of German world market leaders. The premier class of German companies in words and pictures . German Standards Editions, Cologne 2010, ISBN 978-3-86936-221-2 .
- ↑ Main State Archives (H.St.A.) Dresden, Loc. 1341
- ↑ Main State Archives (H.St.A.) Dresden, Loc 2097, No. 49
- ↑ Johann Melchior Steinbrück: Life and death story of the world famous knight and Mr. Ehrenfried Walther von Tschirnhauß, auff Kießlings-Wald and Stoltzenberg, Königlichen and Churfürstl. Saxon Council. Jacob Rohrlach, Görlitz 1709, p. 8.
- ^ GDR - That's us . DEFA documentary series, episode 7. 1970
-
↑ Meissen manufactory cuts every fourth digit. In: Sächsische Zeitung , July 7, 2010, beginning of the article .
dpa : Meissen: Porcelain Manufactory dismisses 180 employees . In: FAZ , July 6, 2010. - ↑ Peter Anderson: smashed porcelain for 2.6 million euros. In the state parliament yesterday secret details of the hen party in the manufactory became known . In: Sächsische Zeitung , March 10, 2011.
- ↑ Peter Anderson and Nicole Preuß: Shards in the porcelain factory annoy the Meißner . In: Sächsische Zeitung , November 16, 2010.
- ↑ Biedenkopf confirms the destruction of porcelain. In: MDR Sachsenspiegel from November 15, 2010.
- ↑ Tatjana Meier: We're going to Milan . In: Focus , September 13, 2010, No. 37, interview with renovator Christian Kurtzke.
- ^ Dapd : Porcelain Manufactory Razzia at Meissener . In: Mitteldeutsche Zeitung , February 8, 2011.
- ↑ Peter Anderson: Manufactory sells more again. In: Saxon newspaper . February 21, 2014, accessed December 10, 2016 (fee required).
- ↑ A black year for the manufactory . In: Meissner Tageblatt, January 14, 2016, accessed on January 22, 2016
- ↑ Press release of the Free State of Saxony from November 16, 2014 , accessed on January 22, 2016
- ↑ Participations of the Free State. Companies with cultural objectives. ( Memento of the original from January 22nd, 2016 in the Internet Archive ) Info: The archive link was inserted automatically and has not yet been checked. Please check the original and archive link according to the instructions and then remove this notice. In: Free State of Saxony .
- ↑ Harald Schiller: The porcelain pop star portrait in the PR Report of April 26, 2012
- ↑ State Porcelain Manufactory. Biedenkopf is no longer a Meissen supervisory board . ( Memento from June 2, 2016 in the web archive archive.today ) MDR , September 2, 2015.
- ↑ Juliane Morgenroth: This is where our tax money is being sunk in Saxony ( Memento of the original from January 28, 2016 in the Internet Archive ) Info: The archive link was automatically inserted and not yet checked. Please check the original and archive link according to the instructions and then remove this notice. . In: mopo24 .com October 14, 2015.
- ↑ top-magazin-frankfurt.de
- ↑ Porzellanmanufaktur Meissen is building 200 jobs by March from the MDR of November 14, 2019 (accessed on January 27, 2020).
- ↑ German traditional company. Porzellan-Manufaktur Meissen cuts every third digit . In: Focus from November 14, 2019 (accessed January 27, 2020).
- ↑ Saxon traditional company. Porzellanmanufaktur Meissen cuts every third digit . In: Spiegel. Economy from November 14, 2019 (accessed January 27, 2020).
- ^ History of the museum. In: Meissen Porcelain Foundation GmbH .
- ^ Meißen porcelain collection, Ernst Schneider Foundation . in Lustheim Palace . In: Bavarian National Museum .
- ↑ Exhibition “To Heulen Schön”, Meissen onion pattern in all its diversity (1730 to 1888) . Rheinische Post, November 12, 2018
- ↑ For the history of Auer kaolin mining see Otfried Wagenbreth: The kaolin mining in the "Weißenerdezeche Weißer St. Andreas" near Aue / Erzgeb. In: Sächsische Heimatblätter , 2004, issue 2, pp. 138–152.
- ↑ on kaolin production in Seilitz see: Municipality of Diera-Zehren in the district of Meißen (Saxony). (No longer available online.) In: diera.de. Archived from the original on March 4, 2016 ; accessed on February 12, 2017 . Info: The archive link was inserted automatically and has not yet been checked. Please check the original and archive link according to the instructions and then remove this notice.
- ^ Sächsisches Oberbergamt / Saxon State Office for Environment and Geology : The mining in Saxony. Annual report 2007. Freiberg 2008, p. 29.
- ↑ Author collective, medals from Meissen porcelain, catalog, transpress-verlag, Berlin 1984
- ^ A b Johannes Just: The artistic renewal process of the Meissen Porcelain Manufactory around 1900. Dissertation, 1972, p. 55.
-
↑ 400 years of Arita porcelain, Japan / Ludwig Zepner's 85th birthday . (PDF; 4.2 MB; 2 pages) meiland.de, Meißen City Museum ; accessed on February 12, 2017.
Uwe Hofmann: City Museum Meißen shows porcelain from Japan and the hand of Ludwig Zepner . In: Dresdner Latest News , March 17, 2016 - ↑ a b c d Jürgen Schärer: Meissner contours . Edition Leipzig, Leipzig 1991, ISBN 3-361-00349-0 , p. 23-50 .
Coordinates: 51 ° 9 ′ 20 ″ N , 13 ° 27 ′ 58 ″ E