Polyethylene
Structural formula | |||||||
---|---|---|---|---|---|---|---|
![]() |
|||||||
General | |||||||
Surname | Polyethylene | ||||||
other names |
|
||||||
CAS number | 9002-88-4 | ||||||
Monomer | Ethene | ||||||
Molecular formula of the repeating unit | C 2 H 4 | ||||||
Molar mass of the repeating unit | 28.05 g mol −1 | ||||||
Type of polymer | |||||||
Brief description |
light gray |
||||||
properties | |||||||
Physical state |
solid (partially crystalline) |
||||||
safety instructions | |||||||
|
|||||||
As far as possible and customary, SI units are used. Unless otherwise noted, the data given apply to standard conditions . |

Polyethylene ( abbreviation PE ) is a thermoplastic material with the simplified structural formula produced by chain polymerisation of ethene produced by petrochemicals (CH 2 = CH 2 )
- .
Polyethylene belongs to the group of polyolefins and is semi-crystalline and non-polar . It is by far the most frequently used ( standard ) plastic worldwide and is primarily used for packaging . There are several types of polyethylene, such as high-density polyethylene (PE-HD), linear low-density polyethylene (PE-LLD) and low-density polyethylene (PE-LD). All polyethylene types are characterized by high chemical resistance , good electrical insulation properties and good sliding behavior; however, the mechanical properties are only moderate compared to other plastics.
history
Polyethylene was first made by chance in 1898 by the German chemist Hans von Pechmann while he was studying diazomethane . When his colleagues Eugen Bamberger and Friedrich Tschirner characterized the white, waxy substance, they recognized that it was made up of long CH 2 chains and called it polymethylene. However, this type of production has not gained any practical importance since diazomethane is notoriously unstable and toxic.
The first industrial synthesis of polyethylene was discovered (again by accident) in 1933 by Eric Fawcett and Reginald Gibson at Imperial Chemical Industries (ICI) in Northwich , England . At extremely high pressures (approx. 1400 bar ) they produced a white, waxy material from a mixture of ethylene and benzaldehyde . Since the reaction was initiated by traces of oxygen , the first attempt was initially difficult to reproduce. It was therefore not until 1935 that another chemist at ICI, Michael Willcox Perrin , developed a reproducible high-pressure synthesis for polyethylene from the accidental discovery. This formed the basis for the first industrial LDPE production in 1939.
Since polyethylene proved to be very low-loss dielectric for high-frequency applications (wires, cables), the commercial distribution was with the beginning of World War II interrupted, provided the procedure under secrecy and polyethylene for the production of insulation for UHF - and SHF - coaxial cable in radars used. The process was further explored during World War II; 1944 began Bakelite Corporation in Sabine , Texas, and DuPont in Charleston , West Virginia, on a large scale with the commercial production, both licensed by the ICI.
A milestone in the commercial production of polyethylene was the development of catalysts that enable polymerization at mild temperatures and pressures. Robert Banks and J. Paul Hogan first discovered a chromium trioxide- based catalyst at Phillips Petroleum in 1951 . In 1953 Karl Ziegler and Giulio Natta discovered the Ziegler-Natta catalyst based on titanium halides and organoaluminum compounds . The Phillips catalyst was cheaper and easier to handle, the Ziegler-Natta catalyst, on the other hand, allowed polymerization under even milder conditions. From the 1950s onwards, the large-scale production of PE-HD was made possible; Both processes are still used intensively in industry today.
Metallocene catalysts are a modern alternative to Ziegler-Natta catalysts . These were already known in 1950, but the breakthrough came in 1973, when Reichert and Meyer added small amounts of water to a system of titanocene and alkyl aluminum chloride. The metallocene catalysts produce polyethylene with narrower molar mass distributions and more uniform co-monomer incorporation than the Ziegler-Natta catalysts. In the 1980s, Kaminsky and Sinn carried out further investigations into the metallocene / methylaluminoxane system .
The term polyethene is occasionally used to avoid the historical name for ethene . The structure-based name (after the repeating unit in the polymer chain) according to IUPAC would be polymethylene , but it is not common.
PE types
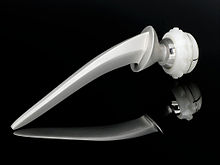

A distinction is made between the following types:
- PE-HD (HDPE)
- Weakly branched polymer chains, therefore high density between 0.94 g / cm 3 and 0.97 g / cm 3 , (“HD” stands for “high density”).
- PE-LD (LDPE)
- Strongly branched polymer chains, therefore low density between 0.915 g / cm 3 and 0.935 g / cm 3 , (“LD” stands for “low density”).
- PE-LLD (LLDPE)
- Linear low-density polyethylene, the polymer molecules of which have only short branches. These branches are produced by the copolymerization of ethene and higher α-olefins (typically butene , hexene or octene ) (“LLD” stands for “linear low density”).
- PE-HMW
- High molecular weight polyethylene. The polymer chains are longer than with PE-HD, PE-LD or PE-LLD, the average molar mass is 500–1000 kg / mol (“HMW” stands for “high molecular weight”).
- PE-UHMW
- Ultra high molecular weight HDPE with an average molar mass of up to 6000 kg / mol and a density of 0.93-0.94 g / cm 3 (“UHMW” stands for “ultra high molecular weight”).
property | PE-LD | PE-HD | PE-LLD |
---|---|---|---|
Stress at the yield point in N / mm 2 | 8.0-10.0 | 20.0-30.0 | 10.0-30.0 |
Elongation at the yield point in% | 20th | 12 | 16 |
Dielectric constant | 2.4 | - | - |
Density in g / cm 3 | 0.915-0.935 | 0.94-0.97 | 0.87-0.94 |
Melting point in ° C | 130-145 | 130-145 | 45-125 |
Glass temperature in ° C | −100 | −70 | |
Crystallinity in% | 40-50 | 60-80 | 10-50 |
Modulus of elasticity at 23 ° C in N / mm 2 | ~ 200 | ~ 1000 | 60-600 |
Heat resistance up to ° C | 80 | 100 | 30-90 |
Thermal expansion coefficient | 1.7 · 10 −4 K −1 | 2 · 10 −4 K −1 | 2 · 10 −4 K −1 |
Molecular structure of the PE types
The different material behavior of the different types of polyethylene can be explained by their molecular structure. Molar mass and crystallinity play the greatest role , with the crystallinity in turn depending on the molar mass and the degree of branching . The less the polymer chains are branched and the lower the molar mass, the higher the crystalline content in the polyethylene. The crystalline proportion is between 35% (PE-LD / PE-LLD) and 80% (PE-HD). Within crystallites , polyethylene has a density of 1.0 g · cm −3 , in amorphous areas 0.86 g · cm −3 . There is an almost linear relationship between density and crystalline content.
The degree of branching of the individual polyethylene types can be shown schematically as follows:
PE-HD |
![]() |
PE-LLD |
![]() |
PE-LD |
![]() |
Polyethylene main chains and short chain branches as well as side chain branches are shown in the figure . The polymer chains are shown linearly.
The figure shows the number and length of the branch points. The branches are divided into short chain branches and long chain branches .
Chain branches
The properties of polyethylene are heavily dependent on the type and number of chain branches, depending on whether it was produced using the high pressure process (see below, exclusively PE-LD) or the low pressure process (produced using the low pressure process, see below, all other types of PE) . In the high pressure process, PE-LD is produced by radical polymerisation, resulting in numerous short chain branches as well as long chain branches. Short branches are formed by intramolecular chain transfer reactions . They are always butyl or ethyl side groups, as the reaction proceeds according to the following mechanism:
The reactive chain end ( CH 2 group with radical ) attacks the polymer chain via a six-membered transition state (backbiting). An ethene monomer is then deposited there (top line). If the reaction continues "normally" at this point, the previous chain end remains as a butyl side group (A), see bottom left. If, on the other hand, there is another intramolecular attack, two neighboring ethyl side groups (B) are formed, see below right.
In the low-pressure process , there are hardly any chain transfer reactions, so that long chain branches and thus only weakly branched PE chains are generated only rarely. However, completely linear (unbranched) PE cannot be produced even in the low-pressure process (but only through the decomposition of diazomethane , which is of no commercial importance, however). Instead, short-chain branches are intentionally introduced in the low-pressure process through the use of comonomers such as 1-butene or 1-octene. These statistical short chain branches reduce crystallinity, thereby improving machinability and flexibility. In this way, both PE-HD and PE-LLD are produced, PE-LLD, however, with a higher comonomer content and therefore lower crystallinity. In general, the low-pressure process produces polymers with higher molecular weights. In order to limit the mean molar mass in a targeted manner (and thus facilitate workability), hydrogen can be added in the low-pressure process; in the high-pressure process this is achieved by adding ethanal .
The exact properties of the polyethylene are determined by the selected process, they can be determined using the density and the melt flow index (MFR):
- The Ziegler suspension polymerization process can produce products with densities greater than 0.940 g · cm −3 and all MFR values (190/5) less than 100 g / 10 min, including ultra-high molecular weight polyethylenes.
- With the Phillips suspension polymerization process , polyethylenes with densities above 0.920 g · cm −3 can be produced, with the products having a narrow molar mass distribution . In the case of products with MFR values (190 / 2.16) greater than 0.5 g / 10 min, however, it is limited to products with a higher density and a broad molar mass distribution.
- With the gas phase polymerization process , polyethylenes of almost all densities can be produced, with the exception of very low densities (in fact elastomers ) and with the exception of very high and very low MFR values (PE-UHMW and PE waxes).
- The solution polymerization process can produce polyethylenes of any density, but it is limited to products with MFR values greater than 0.5 g / 10 min.
- With the high-pressure polymerization process , polyethylenes with densities between 0.915 and a maximum of 0.935 g · cm −3 and an MFR of 0.25 g / 10 min can be produced.
Numerous other properties are also closely related to density and MFR and can therefore also be set via the choice of the production process.
Property spectrum
With the correct choice of production process, production conditions, proportion and type of comonomers, catalysts, etc., polymers with the desired properties can be produced in a targeted manner; In addition to hard or soft plastics, waxes , fats and even oils made from polyethylene are also possible.
Properties that require only a slight movement of the parts of a sample relative to one another are more dependent on the crystallinity and less on the molar mass of the sample; this includes melting point, softening point, elasticity and flexural modulus, yield point and surface hardness. Properties that include a more extensive movement of the parts of a sample, however, are more dependent on the molar mass; this includes the tensile strength, the embrittlement point at low temperatures and the tear strength.
The general mechanical properties depending on crystallinity and chain length can be seen in the figure. It can be seen that substances with high crystallinity are hard and brittle, while those with low crystallinity are soft and tough. More precisely, it can be said that high crystallinity leads to high density, rigidity, hardness, abrasion resistance, service temperature and chemical resistance. On the other hand, if the crystallinity is low (high amorphous content), strength, toughness, notch insensitivity and stress cracking resistance are more pronounced. At the same time, it can be seen that with decreasing molar mass, polyethylene at some point loses its plastic character and first becomes wax-like, then grease-like and finally oil-like. This is also used, for example, to produce polyethylene wax from polyethylene by means of thermal cracking .
properties
The property profile of polyethylene can be divided into mechanical, chemical, electrical, optical and thermal properties.
Mechanical properties
Polyethylene is of low strength, hardness and stiffness, but has a high ductility and impact strength and low sliding friction . If the force is continuously applied, strong creep deformation occurs , which can be reduced by adding short fibers . When touched, polyethylene feels waxy, and when it is warm it expands considerably.
Thermal properties
The usability is limited by the fact that PE softens at temperatures above 80 ° C (PE-HD, low-crystalline types soften earlier).
value | unit | Test method | |
---|---|---|---|
Upper usage temperature in air (max. Short-term) | 120 | ° C | |
Upper usage temperature in air (max. Continuously) | 80 | ° C | |
Lower usage temperature | −75 | ° C | |
Heat resistance (HDT A method) | 45 | ° C | ISO 75-2 |
Therm. Coefficient of linear expansion (along 23 - 60 ° C) | 2 | 10-4 / K | ISO 11359 |
Thermal conductivity (+23 ° C) | 0.37 | W / (K * m) | DIN 52612 |
Flammability according to UL standard (thickness 3 and 6 mm) | HB | class | UL 94 |
Vicat softening temperature (VST / B / 50) | 80 | ° C | ISO 306 |
Melting temperature | 130 | ° C | ISO 3146 |
value | unit | Test method | |
---|---|---|---|
Upper usage temperature in air (max. Short-term) | 120 | ° C | |
Upper usage temperature in air (max. Continuously) | 80 | ° C | |
Lower usage temperature | −200 | ° C | |
Heat resistance (HDT A method) | 42 | ° C | ISO 75-2 |
Therm. Coefficient of linear expansion (along 23 - 60 ° C) | 2 | 10-4 / K | ISO 11359 |
Thermal conductivity (+23 ° C) | 0.41 | W / (K * m) | DIN 52612 |
Flammability according to UL standard (thickness 3 and 6 mm) | HB | class | UL 94 |
Vicat softening temperature (VST / B / 50) | 80 | ° C | ISO 306 |
Melting temperature | 135 | ° C | ISO 3146 |
Chemical properties
Polyethylene consists of non-polar, saturated, high-molecular hydrocarbons . It therefore resembles paraffin in its chemical behavior . The individual macromolecules are not chemically linked. They tend to crystallize because of their symmetrical molecular structure ; overall it is partially crystalline . The higher crystallinity increases the density as well as the mechanical and chemical stability.
Polyethylene has a high resistance to acids , bases and other chemicals .
Polyethylene hardly absorbs water . The gas and water vapor permeability (only polar gases) is lower than that of most plastics; On the other hand, it lets oxygen , carbon dioxide and aromatic substances through.
Sun exposure can make PE brittle; mostly soot is used as a UV stabilizer .
It burns residue-free with a dripping, bright flame, even after removing the fire-causing flame. The smoke from the fire smells like that of a wax candle flame.
Polyethylene without suitable pretreatment is difficult or impossible to print or glue on.
The following table gives a rough overview of the resistance of PE-LD and PE-HD to some chemical groups (at room temperature ):
Substance class | Resistance PE-LD | Resistance PE-HD |
---|---|---|
Aldehydes | k. A. |
![]() |
Alcohols |
![]() |
![]() |
Ester |
![]() |
![]() |
Ether |
![]() |
![]() |
Ketones |
![]() |
![]() |
Hydrocarbons , aliphatic |
![]() |
![]() |
Hydrocarbons , aromatic |
![]() |
![]() |
Hydrocarbons , chlorinated |
![]() |
![]() |
Fuels |
![]() |
![]() |
Fats , oils |
![]() |
![]() |
Alkalis |
![]() |
![]() |
weak acids |
![]() |
![]() |
strong acids |
![]() |
![]() |
oxidizing acids |
![]() |
![]() |
hot water | k. A. |
![]() |
= poor to no resistance to the substance class (even a single, short-term exposure can damage the material)
= good or limited resistance to the material class (material is resistant for a limited time and may only be damaged reversibly)
= good resistance to the substance class (even long exposure does not damage the material)
- k. A. = no information
Electrical Properties
Polyethylene is a good electrical insulator . It has good tracking resistance , but is easily charged electrostatically (which can be reduced by adding graphite, carbon black or antistatic agents ).
Optical properties
Depending on the thermal history and layer thickness, PE can be almost crystal clear (transparent), milky-cloudy (translucent) or opaque (opaque). PE-LD has the largest, PE-LLD slightly less and PE-HD the least. Transparency is reduced by crystallites if they are larger than the wavelength of the light.
Manufacturing
Polyethylene is obtained by polymerization of ethylene gas produced. Petrochemical ethylene gas is almost always used as a raw material . However, biogenic ethylene gas produced by the dehydration (chemistry) of bioethanol can also be used. PE made from it is also called bio-PE. There is currently only one production plant in Brazil (made from sugar cane) and the market share of bio-PE is less than one percent. The most important technical processes for the production of polyethylene are the high pressure process for PE-LD and the low pressure process for PE-HD and PE-LLD.
Letterpress process
In the high-pressure process, high-purity ethene is radically polymerized by traces of oxygen or peroxides as free- radical initiators at pressures of 1500 to 3800 bar and at 100 to 200 ° C. The ethene is in the supercritical state under these conditions. In the process, a stirred autoclave (ICI) or tubular reactors (BASF) was used. The polymer is then transferred to an extruder at 200 ° C. and granulated .
Low pressure process
In the low-pressure process, PE is produced using Ziegler , metallocene or Phillips catalysts in solution polymerisation, suspension polymerisation or gas phase polymerisation. In the solution polymerization is above 130 ° C z. B. polymerized in n- hexane , cyclohexane or toluene at up to 70 bar. The polyethylene remains in solution and can be separated off by distillation. In suspension polymerisation, polymerisation takes place in aliphatic hydrocarbons or gasoline at 60-105 ° C between 8 and 40 bar. The polyethylene is insoluble and precipitates, which facilitates separation (e.g. by centrifugation ). The gas phase polymerization is similar to a bulk polymerization; In it, finely divided catalyst is circulated by ethene in a fluidized bed reactor at 85 to 100 ° C. and 20 bar and thus kept in suspension. The finished polyethylene is obtained as a powder.
processing
Archetypes
May be polyethylene by any known primary forming processes are processed, including injection molding , extrusion , blow molding , compression molding , thermoforming , rotational molding , transfer molding , casting , sintering , as well as a coating; the first three methods are the most common.
Injection molding is preferably carried out with PE grades with a narrow molecular weight distribution and a high melt flow rate (low viscosity ). Injection molding is carried out between 170 and 300 ° C, depending on the PE type; all PE types decompose above 310 ° C.
Polyethylene pipes are produced by extrusion at 160–240 ° C or foils, sheets and monofilament threads at up to 300 ° C. Continuous substrates such as cables can also be coated by extrusion (in the so-called extrusion covering process). Extrusion is also used to mix different polymers and to add fillers , additives etc.
PE-UHMW has an extremely high viscosity (1010 Pa-s) so that it can only be processed by compression molding, ram extrusion, gel extrusion and spinning. The processing techniques used for PE-UHMW originate in part from powder metal technology.
Post-processing and joining
The end product can be produced from polyethylene moldings by reworking and joining (if reworking is necessary). Molded parts can be glued or welded together, machined or printed.
The joining of polyethylene moldings is almost always carried out using heat. In heating element welding , a heated plate is used to melt the joint surfaces, which are then brought into contact and solidify together. During hot gas welding, a stream of hot air heats the two parts to be joined. Hot gas welding is carried out manually; the result therefore depends on the skill of the user. Vibration and ultrasonic welding are also used.
The gluing or printing of polyethylene is made difficult by the non-polar hydrophobic surface. The surface must therefore first be pretreated with lasers , plasmas ( high pressure plasma , e.g. " corona discharge " or low pressure plasma ), strong acids (e.g. chromosulfuric acid ) or polyolefin primers .
Machining polyethylene is relatively easy because it is a soft material. Carbide-tipped or high-speed steel tools can be used on metal or woodworking machines. PE-HD is outstandingly machinable, PE-LD on the other hand only moderately. Conversely, PE-LD can be shaped very well, PE-HD less so.
Chemically modified polyethylene
Polyethylene can be modified either during the polymerization by non-polar or polar copolymers or after the polymerization has been completed by polymer-analogous reactions . Common polymer-analogous reactions for polyethylene are crosslinking , chlorination and sulfochlorination .
Non-polar ethylene copolymers
α-olefins
In the low-pressure process, α-olefins (e.g. 1-butene or 1-hexene ) can be added, which are incorporated into the polymer chain during the polymerization. These copolymers produce short side chains, reducing crystallinity and density. As explained above , this changes the mechanical and thermal properties. In particular, LLDPE is produced in this way.
Metallocene polyethylene (PE-m)
Metallocene polyethylene (PE-M) with the aid of metallocene - catalysts mostly of copolymers (eg ethylene / hexene.) Was prepared. Metallocene polyethylene has a comparatively narrow molar mass distribution , extremely high toughness, excellent optical properties and a uniform proportion of comonomer. Due to the narrow molar mass distribution, it is less structurally viscous (especially at higher shear rates) . Metallocene polyethylene has a low proportion of low molecular weight (extractable) components and a low welding and sealing temperature. This makes it particularly suitable for the food sector.
Polyethylene with multimodal molecular weight distribution
Polyethylene with a multimodal molar mass distribution consists of several polymer fractions that are homogeneously mixed. Such polyethylenes offer particularly high stiffness, toughness, strength, stress cracking resistance and increased crack propagation resistance. They consist of equal proportions of higher and lower molecular weight polymer fractions. The lower molecular weight components crystallize more easily and relax more quickly. The higher molecular weight fractions form connecting molecules between the crystallites and thus increase toughness and resistance to stress cracking. Polyethylene with a multimodal molar mass distribution is produced either in a two-stage reactor, with "bi-catalysts" (two different active centers on a carrier) or by blending in extruders.
Cycloolefin Copolymers (COC)
Cyclo-olefin copolymers are produced by copolymerization from ethene and cycloolefins (mostly norbornene) with the help of metallocene catalysts. The resulting polymers are amorphous and particularly transparent, as well as being heat resistant.
Polar ethylene copolymers
As structural motifs for polar comonomers, vinyl alcohol ( ethenol , an unsaturated alcohol), acrylic acid ( propenoic acid , an unsaturated acid) and esters from one of the two compounds are used.
Ethylene copolymers with unsaturated alcohols
Ethylene-vinyl alcohol copolymer (EVOH) is formally a copolymer of ethylene and vinyl alcohol . Since vinyl alcohol is not stable, the preparation takes place by hydrolysis of ethylene-vinyl acetate copolymer (EVAC).
The acetyl groups are split off from ethylene-vinyl acetate copolymer by hydrolysis . In this case, acetic acid free, and there is formed the ethylene-vinyl alcohol copolymer. However, the hydrolysis is incomplete; yz acetyl groups remain unchanged.
EVOH usually has a higher proportion of comonomer than the EVAC that is usually used. EVOH is used in multilayer films as a barrier layer (barrier plastic) in packaging. Since EVOH is hygroscopic (water-attracting), it absorbs water from the environment, whereby it loses its barrier effect. It must therefore be surrounded by other plastics as the core layer (such as PE-LD , PP , PA or PET ). EVOH is also used against corrosion as a coating on street lamps, traffic light masts and noise barriers.
Ethylene acrylic acid copolymer (EAA)

Copolymers of ethylene and unsaturated carboxylic acids such as acrylic acid are characterized by good adhesion to various materials, resistance to stress cracks and high flexibility. However, they are more sensitive to heat and oxidation than ethylene homopolymers. Ethylene-acrylic acid copolymers are used as adhesion promoters .
If the salts of an unsaturated carboxylic acid are present in the polymer, thermo-reversible ion networks are formed; they are then ionomers . Ionomers are crystal clear, transparent thermoplastics that are characterized by high adhesion to metals, high abrasion resistance and high water absorption.
Ethylene copolymers with unsaturated esters
When ethylene is copolymerized with an unsaturated ester, either the alcohol residue can be in the main polymer chain (as is the case with ethylene-vinyl acetate copolymer) or the acid residue (as with ethylene-ethyl acrylate copolymer).
Ethene-vinyl acetate copolymers are produced by high pressure polymerisation, similar to LD-PE. The proportion of comonomer has a decisive influence on the behavior of the polymer.
The density decreases up to a comonomer content of 10% because of the disturbed crystal formation. With a higher proportion, the density approaches that of the polyvinyl acetate (1.17 g / cm 3 ). As a result of the falling crystallinity, ethylene-vinyl acetate copolymers become softer with increasing comonomer content. The chemical properties (compared to polyethylene) are significantly changed by the polar side groups: weathering stability, tackiness and weldability increase with an increasing proportion of comonomer, while chemical resistance decreases. The mechanical properties also change: stress cracking resistance and toughness in the cold increase, while yield stress and heat distortion resistance decrease. With a very high proportion of comonomers (around 50%), rubber-elastic thermoplastics ( thermoplastic elastomers ) are formed.
Ethylene-ethyl acrylate copolymers behave similarly to ethylene-vinyl acetate copolymers.
Networking
Various processes can be used to manufacture cross-linked polyethylene (PE-X also XLPE (cross linked) or in German VPE) from thermoplastic polyethylene (PE-LD, PE-LLD or PE-HD). The crosslinking allows the low-temperature impact strength , abrasion resistance and stress cracking resistance to be increased significantly, while hardness and rigidity are somewhat reduced. PE-X no longer melts (similar to elastomers ) and can withstand higher thermal loads (over longer periods of time up to 120 ° C, briefly without mechanical stress up to 250 ° C). With increasing crosslinking density, the maximum shear modulus also increases (even at higher temperatures). PE-X thus has significantly expanded application possibilities compared to normal PE. Since PE-X cannot be melted, the finished semi-finished product or molded part is always cross-linked.
Types of networking
A basic distinction is made between peroxide crosslinking (PE-Xa), silane crosslinking (PE-Xb), electron beam crosslinking (PE-Xc) and azo crosslinking (PE-Xd).
Peroxide, silane and radiation crosslinking are shown. In every process, a radical is first generated in the polyethylene chain (top center), either by radiation (h · ν) or by peroxides (ROOR). Two radical chains can then either crosslink directly (bottom left) or indirectly through silane compounds (bottom right).
- Peroxide crosslinking (PE-Xa): The crosslinking of polyethylene with the help of peroxides (e.g. dicumyl peroxide or di-tert-butyl peroxide ) is still of great importance today. In the so-called Engel process , a mixture of PE-HD and 2% peroxide is first mixed in an extruder at low temperatures and then crosslinked at high temperatures (between 200 and 250 ° C). The peroxide breaks down into peroxide radicals (RO •), which abstract (remove) hydrogen atoms from the polymer chain, which leads to radicals in the polymer chain. When these combine, this leads to networking. The resulting polymer network is uniform, of low tension and high flexibility, which makes PE-Xa softer and tougher than (radiation-crosslinked) PE-Xc.
- Silane crosslinking (PE-Xb): In the presence of silanes (e.g. trimethoxyvinylsilane ), polyethylene can first be Si- functionalized by irradiation or a small amount of peroxide . In a water bath, hydrolysis leads to the formation of Si-OH groups, which then condense and cross-link the PE by forming Si-O-Si bridges. Catalysts such as dibutyltin dilaurate can accelerate the reaction.
- Beam crosslinking (PE-Xc): Polyethylene can also be crosslinked by means of a downstream radiation source (usually electron accelerators , occasionally isotope emitters ). For example, PE products are cross-linked below the crystallite melting point by splitting off hydrogen . In this case, possess β-radiation , a penetration depth to 10 mm , ɣ radiation mm to 100th In this way, the interior or certain areas of the shape can be excluded from the network. However, due to the high installation and operating costs, radiation crosslinking plays a subordinate role compared to peroxide crosslinking. In contrast to peroxide crosslinking, crosslinking takes place in the solid state. As a result, the crosslinking takes place primarily in amorphous regions , the crystallinity is largely retained.
- Azo crosslinking (PE-Xd): In the so-called Lubonyl process , a polyethylene is crosslinked after extrusion in a hot salt bath with the aid of previously mixed azo compounds.
Degree of networking
A low degree of crosslinking initially only leads to a multiplication of the molecular weight of the macromolecules . The individual macromolecules are still unconnected and not present as a covalent network. The polyethylene, which consists of huge molecules, behaves similarly to polyethylene with an ultra-high molar mass (PE-UHMW), i.e. like a thermoplastic elastomer .
In the event of further crosslinking (e.g. from a degree of crosslinking of 80%), the individual macromolecules are ultimately also connected to form a network. From a chemical point of view, this cross-linked polyethylene (PE-X) is a thermoset ; above the melting point it shows rubber-elastic behavior (and can no longer be processed in the melt ).
The degree of networking (and thus also the extent of the change) varies depending on the process. According to DIN 16892 (quality standard for pipes made of PE-X ), at least the following degree of crosslinking must be achieved:
- with peroxide crosslinking (PE-Xa): 75%
- with silane crosslinking (PE-Xb): 65%
- with electron beam crosslinking (PE-Xc): 60%
- with azo crosslinking (PE-Xd): 60%
Chlorination and sulfochlorination
Chlorinated polyethylene (PE-C) is an inexpensive material with a chlorine content between 34 and 44%. It is used in blends with PVC because the soft, rubber-like chloropolyethylene is embedded in the PVC matrix and thereby increases the impact strength. It also increases the weather resistance. It is also used to soften PVC films without the plasticizers being able to escape. In addition, chlorinated polyethylene can be crosslinked peroxidically to form an elastomer which is used in the cable and rubber industry. When chlorinated polyethylene is added to other polyolefins, it reduces flammability.
Chlorosulfonated PE (CSM) is used as a raw material for ozone-resistant synthetic rubber .
application areas
With a share of around 38 percent, polyethylene is the most widely used plastic worldwide. In 2011, 190 million tons of plastics ( polypropylene , polystyrene , ABS, PVC, PET, polycarbonate , polyethylene) were used. PE-LD had a share of 10 percent, PE-LLD of 11 percent and PE-HD of 17 percent.
PE-LD and PE-LLD
- This material is mainly used in film production. Typical products for PE-LD are cling film, carrier bags, agricultural films, milk carton coatings, garbage bags and shrink films . An important area of application is the use as a sealing medium in composite films. To a lesser extent, PE-LD and PE-LLD are also used to manufacture cable sheathing, as a dielectric in coaxial cables and for pipes and hollow bodies. PE-LLD is mainly used for stretch films, films for industrial packaging, thin-walled containers and for high-performance bag films. In 2009, PE-LD was sold for around 15.9 billion euros (22.2 billion US dollars) worldwide. The world market for PE-LLD reached just under 17 billion euros (24 billion US dollars).
PE-HD
- The most important areas of application are blow molded hollow bodies, for example bottles for household cleaning agents, but also large-volume containers with a capacity of up to 1000 l (so-called IBCs ). Over 8 million tons, almost a third of the amount produced worldwide, were used for this area of application in 2007. Especially China, where HDPE beverage bottles were only introduced in 2005, is a growing market for rigid HDPE packaging due to its rising standard of living. HDPE sheets and HDPE films produced by extrusion are also deep-drawn and used in the packaging industry. In addition, PE-HD is used for injection molded parts , e.g. B. packaging and housewares, as well as processed into technical articles. Fibers, foils and pipes made of polyethylene are manufactured using extrusion and vacuum processes. PE-HD is also used to manufacture foils for hydraulic engineering and landfill construction, as well as geogrids and geo-wovens for landfill construction or road and embankment construction. Another area of application that is growing rapidly, particularly in the emerging countries, is cable lines and pipes , for example for gas and drinking water supply . Polyethylene pipes made of PE 80 or PE 100 are often used here, which can replace pipes made of concrete or PVC . PE-HD is easy to weld, but if it is laid in the ground, the line must be embedded in sand. Alternatively, PE pipes are now also available that are provided with special protective jackets and thus enable trenchless (ie without a sand bed) pipe laying (see also horizontal directional drilling process ).
PE-UHMW
- Ultra-High-Molecular-Weight PE is used due to its high wear resistance for pump parts , gears , sliding bushings , implants and surfaces of endoprostheses , where particularly smooth running with the least possible abrasion is important. In the chemical industry it is used for seals and membranes. Fibers made of PE-UHMW are among the strongest known artificial fibers (based on weight) and are processed into tape loops and cords .
PE-X
- PE-X is used as an insulation material as an electrical insulator for medium and high voltage cables , as a pipe for gas and water installations and for molded parts in electrical engineering, apparatus engineering and automotive engineering . In contrast to other PE materials, it is also suitable as a hot water pipe and, thanks to its high scratch resistance (scratch depth max. 20% of the wall thickness), it is particularly suitable for trenchless installation methods, such as the flush drilling method or installation in the ground using a laying plow . PE-X has very poor welding properties that only allow welding by means of electrofusion welding .
PE-X pipe with oxygen diffusion barrier layer
Trade names
Well-known trade names are: Alathon, Dyneema , Hostalen, Lupolen, Polythen, Spectra, Trolen and Vestolen.
Web links
- Video: Cutting polyethylene shredding - single cut . Institute for Scientific Film (IWF) 1975, made available by the Technical Information Library (TIB), doi : 10.3203 / IWF / E-2018 .
- Video: Shredding of polyethylene - granulator . Institute for Scientific Film (IWF) 1975, made available by the Technical Information Library (TIB), doi : 10.3203 / IWF / E-2083 .
Individual evidence
- ↑ Abbreviations of Polymer Names and Guidelines for Abbreviating Polymer Names
- ↑ Entry on POLYETHYLENE in the CosIng database of the EU Commission, accessed on February 25, 2020.
- ↑ a b Data sheet Polyethylene, medium density from Sigma-Aldrich , accessed on April 12, 2011 ( PDF ).
- ↑ Plastics the Facts 2014/2015 on plasticseurope.org. (No longer available online.) Archived from the original on June 10, 2015 ; accessed on June 10, 2015 . Info: The archive link was inserted automatically and has not yet been checked. Please check the original and archive link according to the instructions and then remove this notice.
- ↑ von Pechmann, H .: Ueber Diazomethan und Nitrosoacylamine . In: Reports of the German Chemical Society in Berlin . 31, 1898, pp. 2640-2646. "S. 2643: It should also be mentioned that from an ethereal diazomethane solution, when standing, sometimes minimal quantities of a white, flaky body crystallizing from chloroform are deposited; [...] "
- ↑ Eug. Bamberger & Fred. Tschirner (1900): On the action of diazomethane on β-arylhydroxylamines , In: Reports of the German Chemical Society in Berlin , 33: 955-959. P. 956: The separation of white flakes from diazomethane solutions is also mentioned by v. Pechmann (these reports 31, 2643); but he did not examine her because of lack of substance. Incidentally, I had Mr. Pechmann announced some time before the appearance of his publication that a solid, white body was created from diazomethane, which was found to be (CH 2 ) x in the analysis , whereupon Mr. v. Pechmann wrote that he had also observed the white body, but not examined it. It is first mentioned in the dissertation of my student Hindermann, Zurich (1897), p. 120.
- ↑ Eug. Bamberger & Fred. Tschirner (1900): On the action of diazomethane on β-arylhydroxylamines , In: Reports of the German Chemical Society in Berlin , 33: 955-959. P. 956: A partial - incidentally always only minimal - conversion of the diazomethane into nitrogen and polymethylene also takes place in very different reactions; [...]
- ^ Winnington history in the making . In: This is Cheshire , August 23, 2006. Archived from the original on January 21, 2010. Retrieved February 20, 2014.
- ↑ Kenneth S. Whiteley, T. Geoffrey Heggs, Hartmut Koch, Ralph L. Mawer, Wolfgang Immel: Polyolefins . In Ullmann's Encyclopedia of Industrial Chemistry , Wiley-VCH, Weinheim 2005, doi : 10.1002 / 14356007.a02_143.pub2
- ^ Poly - The All Star Plastic . In: Popular Mechanics , July 1949, pp. 125-129. Retrieved February 20, 2014.
- ^ Ray Hoff, Robert T. Mathers: Chapter 10. Review of Phillips Chromium Catalyst for Ethylene Polymerization . In: Ray Hoff, Robert T. Mathers (Eds.): Handbook of Transition Metal Polymerization Catalysts . John Wiley & Sons, 2010, ISBN 978-0-470-13798-7 , doi : 10.1002 / 9780470504437.ch10 .
- ↑ J. Kahovec, RB Fox and K. Hatada: Nomenclature of regular single-strand organic polymers (IUPAC Recommendations 2002) in Pure Appl. Chem. , 2002, vol. 74, no. 10, pp. 1921-1956, doi: 10.1351 / pac200274101921 .
- ↑ a b Datasheet Low Density Polyethylene at Acros, accessed on February 19, 2010.
- ↑ Data sheet High Density Polyethylene at Acros, accessed on February 19, 2010.
- ↑ a b Technical plastics, high-temperature-resistant polymers ( Memento from July 15, 2010 in the Internet Archive ), January 1999 (PDF, 6.5 MB) p. 9, accessed on May 12, 2010.
- ↑ a b c d e f g h i j k l m n o p q r s Wolfgang Kaiser : Kunststoffchemie für Ingenieure: From synthesis to application . 2nd Edition. Carl Hanser, 2007, ISBN 978-3-446-41325-2 , pp. 228 ( limited preview in Google Book search).
- ^ Wilhelm Keim: Kunststoffe: Synthesis, Manufacturing Processes, Apparatus . 1st edition. Wiley-VCH, Weinheim 2006, ISBN 3-527-31582-9 , pp. 60 ( limited preview in Google Book search).
- ↑ a b c R. B. Richards: Polyethylene structure, crystallinity and properties . In: Journal of Applied Chemistry . 1, No. 8, May 4, 2007, pp. 370-376. doi : 10.1002 / jctb.5010010812 .
- ↑ a b Plastics and their properties. Accessed January 30, 2020 .
- ↑ a b c d e f g h i j k l Peter Elsner, Peter Eyerer, Thomas Hirth: Domininghaus - Kunststoffe , 8th edition, Springer-Verlag, Berlin Heidelberg 2012, ISBN 978-3-642-16173-5 , P. 224.
- ↑ Chung, CI Extrusion of Polymers: Theory and Practice; 2nd ed .; Hanser: Munich [u. a.], 2010.
- ↑ Oliver Türk: Material use of renewable raw materials . 1st edition. Springer Vieweg, Wiesbaden 2014, ISBN 978-3-8348-1763-1 , p. 431-438 .
- ↑ a b c d e f g h i j Cornelia Vasile, Mihaela Pascu: Practical Guide to Polyethylene . iSmithers Rapra Publishing, 2005, ISBN 1-85957-493-9 , pp. 19–27 ( limited preview in Google Book Search).
- ^ Edited by Andreas Kalweit, Christof Paul, Sascha Peters, Reiner Wallbaum: Handbook for Technical Product Design, Material and Production, Decision - Making Bases for Designers and Engineers , 2nd edition, Springer-Verlag Berlin Heidelberg, Berlin, Heidelberg 2012, ISBN 978-3- 642-02642-3 .
- ↑ a b c d e f g Erwin Baur, Tim A. Osswald: Saechtling Kunststoff Taschenbuch 10/2013, ISBN 978-3-446-43729-6 , p. 443. Preview on kunststoffe.de
- ↑ a b Sebastian Koltzenburg, Michael Maskos, Oskar Nuyken: Polymers: Synthesis, Properties and Applications , 1st edition, Springer Spectrum, 2014, ISBN 978-3-642-34773-3 , p. 406.
- ↑ a b c Kenneth S. Whiteley: Polyethylene . In: Ullmann's Encyclopedia of Industrial Chemistry . August. doi : 10.1002 / 14356007.a21_487.pub2 .
- ^ A b Günter Neroth, Dieter Vollenschaar: Wendehorst building materials science: Basics - building materials - surface protection . 27th edition. Vieweg + Teubner Verlag / Springer Fachmedien, Wiesbaden 2011, ISBN 978-3-8348-9919-4 , pp. 931 ( limited preview in Google Book search).
- ↑ Chlorosulfonated polyethylene (CSM) at ChemgaPedia
- ↑ IHS Markit, SPI Film & Bag, May 2011 ( Memento of the original from October 10, 2015 in the Internet Archive ) Info: The archive link was inserted automatically and has not yet been checked. Please check the original and archive link according to the instructions and then remove this notice.
- ↑ Plastics Europe, Polyolefine ( Memento of the original from October 8, 2016 in the Internet Archive ) Info: The archive link was inserted automatically and has not yet been checked. Please check the original and archive link according to the instructions and then remove this notice.
- ↑ Market study polyethylene-LDPE . Ceresana Research 2010.
- ↑ Market study polyethylene-LLDPE . Ceresana Research 2010
- ↑ Market study polyethylene-HDPE . Ceresana Research 2013
- ↑ HDPE plastic sheets. Accessed December 1, 2013.
- ↑ G. Kiesselbach and W. Finzel: PE piping systems in gas and water supply , 2nd edition. Edition, Vulkan-Verl., Essen 2006, ISBN 9783802754173 . limited preview in Google Book search