vinyl record

A record is usually a circular and mostly black disc with a center hole, the two-sided grooves of which today serve as analog sound carriers for sound signals .
Colloquially, the record is also referred to as a record or, using the terms disc or vinyl , which comes from the youth language . The word record was coined as early as the gramophone era. The term shellac record, which has become much more popular since the end of production of gramophone records, clearly distinguishes this older sound carrier from the later record made of polyvinyl chloride , which is still used today .
The signals are stored in a groove, which usually runs in a spiral inward from the edge of the plate , the flanks of which map the sound oscillation of the stored signal. During playback, the pickup tip is deflected accordingly. The reconversion into audible sound signals can be done purely mechanically via a membrane and a horn or - with today's turntables - electromechanically with subsequent electronic amplification by an audio amplifier .
story
prehistory
In March 1857, the French Édouard-Léon Scott de Martinville registered the phonograph as a patent (number 17,897 / 31,470). In 1860 he succeeded in capturing the French nursery rhyme Au clair de la lune with the help of a large funnel and scratching it on a soot-blackened roller with a membrane that transmitted the vibrations to a pig's bristle. This made the oscillation visible, but it was not yet possible to reproduce the recorded sound. This was not made until 1877 by John Kruesi's invention by the American Thomas Alva Edison , who became world famous with the phonautograph, which was also patented . Its first recording was also a nursery rhyme (Mary had a little lamb ...) . The tones were first scratched into a tin foil , later stored on a phonograph cylinder with a helical sound track in vertical writing, whereby the principle of amplitude deflection was also used here directly acoustically (membrane / funnel). The French Charles Cros , who also submitted his work to the Natural Science Academy in Paris in 1877 , also developed important theoretical foundations .
From the wax cylinder to the record
As early as 1880, the American physicist Charles Sumner Tainter ( Columbia Graphophone Company ) made the discovery that many of the technical disadvantages of the Edisonian rollers (cumbersome handling and complex duplication) could be eliminated if the sound track was spiraled into the surface of a flat, engraved round disc. Tainter developed the prototype of a suitable recording device and produced some pre-recorded wax plates, but gave up the experiments again after a short time due to technical problems. Tainters wax plates are now in the Smithsonian Institute in Washington . They are considered to be the first records in the world.
Independent of Tainter, who had not published his ideas, in 1887 the German-American inventor and industrialist Emil Berliner came up with a similar improvement concept in his experiments with the Edison phonograph. He had studied the Edison phonograph for several years and, earlier than Edison, realized that the future of sound recording lay primarily in entertainment. As a businessman, he too saw the cumbersome and expensive duplication of the rollers as the decisive weak point of the phonograph and devoted his time and effort primarily to solving this problem.
Berliner achieved the decisive breakthrough in 1887. He constructed a device that did not store the sound waves as in Edison's height writing phonograph in vertical modulation created by the up and down movement of the cutting stylus, but instead deflected the groove horizontally; He let a steel needle scratch the mechanical vibrations in the shape of a helix in a glass plate thickly coated with soot. After chemically hardening the carbon black, he was able to produce a zinc positive by electroplating and from this a negative of the plate, which could be used as a stamp for pressing any number of positives, thus inventing the record. On May 4, 1887, Berliner submitted the patent application . U.S. Patent No. 372,786 was then issued on November 8, 1887.
The oldest surviving record from Berliners is a zinc positive that he made on October 25, 1887. The new recording method was first presented to the public in a report in Electrical World magazine on November 12 of the same year; the earliest zinc plates made for demonstration purposes had a diameter of 28 cm and a playing time of four minutes at around 30 min −1 .
In the months that followed, Berliner developed his process further in collaboration with the technician Werner Suess by replacing the soot-coated glass with a zinc or copper plate coated with wax . After the sound groove had been engraved in the wax layer, the plate was exposed to an acid bath that did not attack the parts of the plate that were still covered with wax, but etched the exposed grooves into the metal, so that after the wax was removed, a durable metal master plate was created that was used for production the press dies could be used. On May 16, 1888, Berliner presented the first functional device to the scientists at the Franklin Institute in Philadelphia. Following the preference for Graecisms typical of the time, he called it the gramophone (meaning: "written sound").
In August 1888 he began for the first time to try out the reproduction of his zinc plates, which was actually intended from the beginning, by pressing the negatives into soft material. Initially, he used celluloid as the molding compound , which he obtained directly from the inventor of this material, John W. Hyatt, and which soon proved to be technically unsuitable. Very few examples of these first experimental celluloid plates, known as Hyatt Disks, have survived.
In July 1889, based on material science experiments , Berliner came to the conclusion that vulcanized hard rubber had the most favorable properties as a pressed material , and he considered his invention to be mature enough to initiate series production .
First series production
Emil Berliner went looking for investors, but met with little response from US industry. He therefore traveled to Germany in August 1889 to demonstrate the gramophone to potential customers. On November 26, 1889, he demonstrated the device to the amazed experts of the Berlin Electrotechnical Society , which immediately accepted him as a member.
Encouraged by this success, he decided at the end of 1889 to initiate series production of the panels, initially on his own account. The renowned toy factory Kämmer & Reinhardt (other sources: "Kämmerer & Reinhardt") in Waltershausen ( Thuringia ) manufactured very simple gramophones with a hand crank drive for him - probably from July 1890 - and also developed a talking doll with a miniature gramophone in the body. The matching plates were commissioned from two German companies. One of the two manufacturers was the Rheinische Gummi- und Celluloidfabrik (later Schildkröt ) in Mannheim . Another manufacturer was the gramophone factory Kämmer & Co, company abbreviation "GFKC". Plates were made with a diameter of 8 cm for the speaking doll and 12.5 cm for the gramophone; At least some of the matrices that were made in the USA were used. The pressings were available in rubber, celluloid and zinc versions, although it is not known to what extent celluloid and rubber were related to one another in chronological order; the zinc plates were apparently sold at an additional cost.
These first series records were of such inferior sound quality that notes with the full text of the respective recording were stuck on the back of the record so that the buyer could understand the contents of the record. A total of around 25,000 plates were pressed in Germany in 1889/1890, of which only very few are known worldwide today. The only surviving Berlin speaking doll is in the Heimatmuseum Schloss Tenneberg in Waltershausen . For a short time, the German Berliner products were also exported to England ; the business with the immature system turned out to be less lucrative, which is why Berliner discontinued production in 1891 and returned to the USA .
On April 23, 1889 he founded the American Gramophone Co. , which should take over the exploitation of his invention, but collapsed after a short time. Berliner spent the following two years technically improving the gramophone. He had a New York watchmaker develop a spring drive, which, however, turned out to be impractical, and hired a technician by the name of Edward L. Wilson to design a gramophone with a coin mechanism for him.
It was not until April 1893 that Berliner dared to found a new company together with the brothers Fred and Will Gaisberg, who had previously worked for Columbia Records . The United States Gramophone Company was created , based in Washington (1205 G Street NW), which was supposed to exploit the invention commercially and to which he had to cede his patents. The company produced a few gramophones and records made of Vulcanite or hard rubber, but soon ran into financial difficulties.
In 1895, Berliner succeeded in getting a group of Philadelphia investors enthusiastic about his invention. The Berlin Gramophone Company was founded , but only a small part of the shares belonged to Berliners themselves. The United States Gramophone Co. , however, continued to exist as the owner of the patents. The new company opened a factory and showroom in Baltimore (109 North Charles Street) and began manufacturing equipment and sound carriers.
The diameter of the plates was fixed at ten inches (25.4 cm) in 1894 . By the autumn of 1894, around 1,000 gramophones and 25,000 records had left the factory. Berliner published the first printed order list of the available recordings. In addition to the hand-operated gramophones, the company also offered two luxury models with electric motors. In 1895 the plate diameter was changed to 17.5 cm (6.9 "); In the same year, after long legal battles, Berliner received the US patent for his horizontal writing recording process, the existence of which was later to establish the decade-long monopoly position of the Victor Talking Machine Company (later part of RCA ) on the North American record market.
Commercial breakthrough with spring operation and shellac records
The company's sales were initially modest, as potential customers still saw Berliner's primitive, hand-crank-operated gramophone as a children's toy rather than a serious entertainment device. Encouraged by the corresponding developments in the phonograph sector, Berliner was again concerned with the idea of equipping his devices with spring motors. He commissioned the mechanic Eldridge R. Johnson from Camden City with the development and series production of a suitable spring mechanism motor , which was launched in 1896 and actually helped the product to increase sales enormously.
In October 1896, Berliner gave up the use of hard rubber as sheet material and replaced the substance with a molding compound produced by Duranoid Co. Newark, New Jersey, which essentially consisted of slate powder, cotton flock and shellac , which briefly liquefied during the hot pressing process. also pressed against the surface of the disc and thus formed a hard-wearing material for the grooves. This improved the sound quality and durability of the records tremendously. The shellac record was born.
In the same year Berliner hired the advertising specialist Frank Seaman , whose job it should be to take over the distribution of Berliner products. Seaman founded his own company under the name National Gramophone Company and signed a 15-year contract with the Berlin Gramophone Company , which secured him exclusive rights to the distribution of all Berlin products. Seaman's brilliant advertising campaigns made the gramophone known around the world within a very short time and literally caused the sales figures for records and devices to explode - in the 1898 financial year, Berliner sold 713,753 shellac records. Berliner's invention was now in the hands of three independent companies. The United States Gramophone Company still held the patents, the Berlin Gramophone Company produced records and players, the National Gramophone Company dominated the marketing.

Berliner expanded through the establishment of foreign subsidiaries , the most important of which was the British Gramophone Company . This in turn founded the Deutsche Grammophon company as a subsidiary, headquartered in Hanover , headed by Berliner's brother Joseph.
The initially very successful entrepreneurial concept soon turned out to be fatal for Berliner, because Seaman, who was regarded as an untrustworthy character, was dissatisfied with his long-term contract in view of the enormous profits flowing into Berlin's coffers. In 1898 he began secretly with the production of his zonophones , which were technically only plagiarisms of the Berlin devices. Seaman offered Berliner to buy the Zonophone in the future and sell it under his name. Berliner rejected this indignantly, especially since he did not want to jeopardize the contract with Johnson and generally distrusted Seaman; moreover, the zonophones were of poorer quality than Berliner's products.
Seaman interpreted Berliner's rejection as a termination of his contract, renamed his company the United Talking Machine Company (UTMC) and began to make records and zonophones for his own account . Berliner sued Seaman for breach of contract. Thereupon this began confidential negotiations with the roller manufacturer Columbia, who held the patents on the inventions of Chichester Bell and Charles Sumner Tainter . In 1899, at Seaman's instigation, Columbia brought a lawsuit against Berliner on the grounds that the Berlin patents of 1887 had been granted in violation of earlier Bell and Tainter patents and were therefore null and void.
The complicated legal battles, in which Eldridge R. Johnson was also involved and in which the Columbia hired star lawyer Philipp Mauro played a decisive role, ended successfully for Seaman.
As a result, Berliner was banned from using the name Gramophone in the USA from June 25, 1900 , and he saw no future for his American company either. He dissolved his companies, sold all of his US patents to Eldridge Johnson, with whom he was reconciled, and moved to Montreal. In the following decades he led the Canadian branch of his empire very successfully and also had a decisive influence on the development of the Gramophone Company, which emerged from his British branch . In addition, he dealt with aeronautical problems and was involved in the development of one of the first usable helicopters .
The record industry emerged from 1900
Advertisement for an electrically powered Columbia Records branded gramophone , 1916
Polydor shellac record of the German number one hit Heimweh by Freddy Quinn , 1956
The great commercial success of the Berlin record and the relatively poor patent protection of the invention encouraged numerous entrepreneurs, especially in Europe, to start producing their own records and playback devices from around 1900. Within a few years, an extremely innovative, fast-moving branch of industry developed, with London , Paris , Hanover , Berlin and Vienna being its centers .
At that time, there were still a number of systems that were often not compatible with one another. Before the First World War , for example, the French company Pathé Records was very dominant in the world market. Their records could only be played with a rounded sapphire needle at 90–100 min −1 , always ran from the inside out and were recorded with what is known as deep writing . Since Pathé already had a large pool of older cylinder recordings at the time of the appearance of shellac records, the basis of which was also subscript, the company was able to enter the business with an unexpectedly large assortment of music titles at the time. The records recorded with subscript were never allowed to be played with a gramophone needle, as this immediately destroyed the record. The Pathéphone was available for these records or, as an adapter for gramophones, a Pathé sound box , which, however, could only be installed with specialist knowledge.
The first double-sided records came onto the market between 1904 and 1908.
Another early variant was the North American Edison Diamond Disc , which was presented to the public in 1911. These records were also recorded with subscript and could only be played with special turntables. The approximately five millimeter thick sound carrier did not consist of shellac, but a mixture of phenol , formaldehyde , wood flour and solvent , which was coated with a layer of varnish made of synthetic resin containing phenol . These plates are extremely rare in Europe.
In the end, the shellac record prevailed at a speed of 78 revolutions per minute, for which special needles could be bought, which, according to various recommendations at the time, should be replaced after each record. Inexpensive gramophones of simple design came on the market in a variety of forms and made the record an affordable entertainment medium for the lower social classes . By 1914, around 500 competing record brands had been created in Germany alone. Thanks to technical improvements, the sound quality has steadily increased. Gradually, great musicians such as Enrico Caruso , Nellie Melba and Hermann Jadlowker also began to be interested in the medium of record and helped the record companies to make considerable profits with their recordings .
The label Odeon , which was initially independent and later taken over by the Swedish record producer Carl Lindström , made a name for itself with technical innovations and brought the first large-format records (25, 27 and 30 cm in diameter) and the first double-sided pressings onto the market.
The First World War caused a sharp drop in record production worldwide, which was primarily due to the temporary collapse of the international trade network for raw shellac. After the end of the war, the record industry initially recovered only slowly. The global economic crises of the 1920s and the emergence of the first radio stations had a significant impact on record sales worldwide. On the contrary, this development was reversed when, from 1925 onwards, several American, Dutch and German companies presented electrical recording methods almost simultaneously, which completely replaced the old acoustical-mechanical recording devices within a short time, dramatically reduced the costs of recording recordings and enormously improved the sound quality . The introduction of electrical recording once again gave rise to a large number of short-lived, small record companies in Germany, which were often very experimental in terms of technology and music. The optical sound process developed by the inventors' collective Tri Ergon in 1928 made it possible to cut and post-process recordings for the first time. The first electric turntables came on the market. The enthusiasm for music of the late 1920s guaranteed the record companies excellent sales.
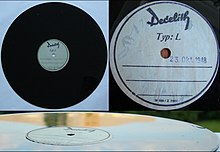
A technical advance in the early 1930s was the introduction of self-tapping gramophone records. Initially, it was cut into soft foils without any aftertreatment, later into Decelith® blanks at the usual 78 revolutions per minute. The durability of the cut decelith disc was improved by a hardening treatment of the surface layer, which, however, required the finished panel to be sent to the manufacturer of the blanks. This recording method was still in use in professional radio studios until the magnetophone was ready for series production in the early 1950s.
The year 1933 brought dramatic changes for the German record industry: In the first years of the Nazi dictatorship, numerous companies that had previously been owned by Jews were forcibly expropriated against the will of the owners and in some cases dissolved. These state criminals and activities that were largely reversed or compensated for after the war - as far as possible - were carried out under the euphemistic or propagandistic term “ Aryanization ”. Many prominent record artists, such as the Comedian Harmonists , were banned from their profession for racial and political reasons by the Nuremberg race laws . It was hardly possible to import foreign records to Germany. By 1939, the number of record brands present on the German market had therefore been reduced considerably. However, since German record companies made recordings with well-known artists abroad, these were well known on the domestic market. Swing music in particular, which became popular in Germany in the late 1930s, benefited from this practice. Regardless of the measures taken by the Reich Chamber of Music against foreign music currents, Telefunken , for example, managed a swing band with American characteristics with Heinz Wehner's “Telefunken Swing Orchestra”. In the 12/1937 issue, the American jazz magazine Down Beat called the Telefunken Swing Orchestra “the best band in the Nazi empire”. International swing bands such as Teddy Stauffer and Fud Candrix first became known through their records before they got engagements in the then most famous German jazz club, the Berlin Delphi Filmpalast , for example .
During the Second World War , a large-scale old record recycling system was to be ensured, in fact, from around 1943 onwards, German record production largely collapsed. Production continued until the end of the war only for the needs of radio and movie theaters .
After 1945, the record factories, as far as they had not been destroyed, resumed their work quite soon, although the shellac technique was initially retained. In the west of Germany, many new record brands emerged, which particularly tried to cover the newly emerging demand for swing and jazz influenced by the US . In the Soviet zone of occupation , on the other hand, record production was one of the first branches of industry to be completely nationalized. The only record manufacturer that remained was VEB Lied der Zeit , later VEB Deutsche Schallplatten , with the Amiga , Eterna , Litera , Nova , Aurora and Schola labels .
In the Federal Republic of Germany and most other western countries, the production of shellac records was given up in July 1958. The GDR took this step in 1961.
Development and breakthrough of the "vinyl" record
Even in the early days of record production, there had been unsuccessful attempts - for example in Great Britain by Nicole Records - to replace the expensive natural product shellac with cheaper synthetic plastics . For this purpose, among other things, sound carriers made of polyvinyl chloride (PVC) were tested. When it comes to records, one usually speaks of “vinyl” instead of PVC.
RCA Victor released the first long-playing vinyl record in 1930, marketed as "Program Transcription Discs". This revolutionary plate was intended for 33 1 ⁄ 3 revolutions per minute, had a diameter of 30 cm and was almost unbreakable. Roland Gelatt noted in his book "The Fabulous Phonograph" that RCA Victor's early introduction of a LP was a commercial mistake, mainly due to the lack of suitable playback equipment.
At the end of the 1930s, the USA began to press pre-recorded radio programs and commercials onto vinyl because they did not break when they were shipped. This advantage also led to the fact that records for children were pressed in vinyl in the USA.
With the shortage of shellac during the Second World War, the use of vinyl was forced. B. US Army V-Discs . The material enabled significantly narrower grooves (micro-writing) than shellac. Smaller styli were used and there was a significant increase in both sound quality and playing time. Usually 33 1 ⁄ 3 revolutions per minute were used, only 78 revolutions per minute for shorter recordings. Thus, the radio already had a record format similar to the vinyl LP in use long before the "micro-groove record" was presented to the general public.
Even if the vinyl record had not had any commercial success until then, people were well aware of its advantages (lower noise, better durability, longer running time).
In the late 1940s two electrical appliances manufacturers brought initially different formats out: On June 21, 1948 presented Columbia Records , the 12-inch (30 cm) -Langspielplatte with 33 1 / 3 rpm and a small center hole (7 mm) before that of Peter Carl Goldmark had been developed since 1939 (abbreviated to LP).
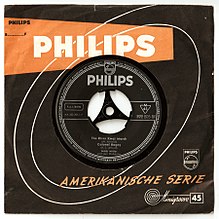
In 1949 RCA Victor followed with the 7-inch (17.5 cm) record with 45 revolutions per minute and a large center hole ( 1 1 ⁄ 2 "or 38.1 mm). The decision for this format was based on the consideration that almost all pieces of music can be sensibly divided into sentences of around 5 minutes. In order to achieve total playing times comparable to the LP, automatic record changers were offered for this format . As was already common practice with shellacs, the sale was to take place in book-like packaging with several individual records, hence the name " album " , which is still used today . Both formats have in common the use of PVC as sheet material and the micro-groove. Both formats were initially marketed in competition with one another. At that time turntables only mastered one of the two formats, so that consumers had to make a decision, which led to uncertainty among customers. It was a classic example of a so-called format war , also known as the "Battle of the Speeds".

It was not until around the mid-1950s that turntables became common that could handle the three main speeds ( 33 1 ⁄ 3 , 45 and 78 revolutions per minute) that were common up to that point and, with the help of adapters, could play records of both the above-mentioned center hole sizes. A number of turntables also had a speed of 16 2 ⁄ 3 revolutions per minute (half of 33 1 ⁄ 3 revolutions per minute), which appeared in the mid-1950s and was used for speech records. Ultimately found this format but hardly spread, compared to records with 33 1 / 3 rpm brought it hardly cost savings and the advantage of longer maturity was at the expense of sound quality. At the beginning of the 1970s it could be assumed that only a tiny minority had a need for the speeds 16 2 ⁄ 3 and 78 revolutions per minute, the turntables brought onto the market afterwards hardly offered these speeds.
The only area in which a record running at 16 2 ⁄ 3 revolutions per minute could bring significant advantages were record players built into cars , where the use of records with a diameter of 30 cm was not possible for reasons of space, whereas records with a maximum size of 17 cm were not possible run 8 minutes (with 33 1 / 3 revolutions per minute). Peter Carl Goldmark developed the Highway Hi-Fi 16 2 ⁄ 3 record for Chrysler automobiles , but that too could not help the 16 2 ⁄ 3 revolutions per minute to be successful.
Columbia's 33 1 ⁄ 3 records were used for long-playing records, while the 45 records opened their own market as singles . So the originally intentionally incompatible competition formats have become variants of one and the same format as which they are still perceived today. Mixed formats in many variations have been added since then. The equalization according to RIAA (" RIAA curve ") was also not standardized until the mid-1950s.
After these format adjustments, which mainly took place in the USA, the vinyl record was ready to conquer the world record market. At the same time, shellac records were gradually being withdrawn from the offer. In 1958, the remaining stocks of shellac records were sold at low prices in West Germany. In Western Europe and North America, they had disappeared from stores by around 1960. Until the late 1960s, however, they were still produced in some developing countries . For example, shellac pressings of Beatles records from India and the Philippines from that time are known.
Technical advancement of the vinyl record
Two-channel technology

Already on December 14, 1931, the engineer Alan Dower Blumlein invented the process, which is still used today, for recording and playing back two channels in one groove. The commercial introduction of the stereo record did not take place until 1958 by Mercury Records . Initially, two systems competed with each other for a short time. Instead of evaluating the pure sideways movement, the “+” system also converted the information from the second channel into a downward movement, which meant that the patents of Berliner and Edison were merged . The "×" system, based on the Blumlein method, on the other hand, converted the sound signals of both channels into oscillations inclined at 45 ° to the vertical. In contrast to the competing system, it was fully compatible with mono recording.
In the Blumlein process, the stereo channel separation is achieved through the 90-degree arrangement of the individual movement possibilities of the needle, each at 45 ° to the groove. This makes it possible to inductively record the projection of these movements in relation to the respective axis in separate magnet systems in the pickup. Since the needle movements of the individual channels are offset by 90 °, the channels are decoupled from one another. Mono recordings in page writing lead to in-phase signals in both pickup coils. Conversely, only the sum of both channels in a stereo groove leads to an output signal in a mono pickup. This provides both upward and downward compatibility with mono technology.
CX coding
Around 1980 CBS Laboratories introduced a compander system for long-playing records that extended the usable dynamic range to around 85 dB (practical value) or 100 dB (under laboratory conditions). In Germany, the CX system was mainly marketed by Telefunken . The name stood for "Compatible Expansion"; the adjective “compatible” indicated that playback was basically possible even without a decoder.
Needle noises, such as crackling and rumbling, were effectively suppressed by the system, while on the other hand scratches became more pronounced due to the contrast effect.
In order to be able to exploit the sonic advantages, CX-coded records required either an external CX decoder between the turntable and audio amplifier or one of the turntables offered with a built-in CX decoder. Electronics magazines also published instructions for building decoders yourself.
A major disadvantage of the CX system was that the decoder had to be precisely matched to the respective scanning system in order to be able to work optimally. The average user had to leave this work to a specialist workshop. Adjusting the tracking force of the pickup required a new adjustment of the decoder. Another disadvantage of the RN100CX CX decoder from Telefunken, which is mainly sold in Germany, was that this device already contained an equalizer preamplifier for MM systems and a connection to the phono input of the amplifier was no longer useful, which had to remain unused . However, there were also decoders that were connected to the amplifier via the tape monitor connections so that the amplifier's own phono MC or MM connections could be used, such as B. the model 220 from the American manufacturer Phase Linear. Further suppliers of CX decoders were the companies CM Labs, Kort and Phoenix Systems.
Due to the system-related inconvenience and the simultaneous appearance of digital sound carriers (especially the audio CD ), the CX system has not yet been able to establish itself with records despite its sonic advantages. The CBS label brought about 50 CX-encoded LPs onto the market from 1980 to 1982.
In 1982 the CX system, in a technically slightly modified form, became the standard method for the analog two-channel sound of the laser disc , the PAL version only with CX sound from 1982 to 1985, the NTSC version from 1982 to 2007 was produced with CX sound - a total of more than 50,000 different CX-encoded tracks. All laser disc players built since 1982 therefore contain a CX decoder as standard.
Optical scanning
In addition to mechanical scanning with needles, a record can be read optically without contact using a laser record player or software-supported “scanning” of a high-resolution optical digitized item in a computer.
Playback quality
The playback of records is characterized, among other things, by the following possible errors and interfering noises:
- linear distortions , d. H. Deviations from the ideally straight frequency response :
- due to inadequate scanning systems (e.g. due to mechanical and electrical natural resonance)
- due to unsuitable equalization amplifier: it must match the cutting characteristic and the scanning system
- on the inner tracks, the wavelength at 20 kHz and 33 1 ⁄ 3 min −1 is already in the range of the needle radius. Large amplitudes can no longer be reproduced there, even below the audible limit
- nonlinear distortion leads to additional harmonics and intermodulation :
- principal distortions, also called geometric distortions:
- the needle cannot follow the track faithfully because of its finite tip radius
- avoidable nonlinear distortions:
- the needle lifts off due to insufficient contact pressure, too hard needle suspension or insufficiently compensated skating force .
- non-linear characteristic of the scanning system, typically with large amplitudes of electromagnetic scanning systems
- principal distortions, also called geometric distortions:
- too low crosstalk attenuation :
- due to non-right-angled cut or warped panel
- due to a scanning system that is not manufactured at right angles
- due to a non-vertical (twisted) scanning system
- Crackling, crackling, hissing
- from dirt and scratches on the panel or from contaminated panel raw material
- by electrostatic discharge of the plate charged by static electricity
- Rumble (rumble-to- noise ratio : aurally accurate evaluation in the frequency range 15 to 315 Hz), caused by vibrations (impact sound), imbalances or inaccuracies in the drive system or (with magnetic and electrodynamic scanning systems) also by magnetic contamination in the turntable
- Wow and flutter caused by non-concentric center hole in the disk or insufficient synchronization of the turntable; A distinction is made between short-term fluctuations and long-term drift
Best reproduction quality values that can be determined with special measuring equipment (measuring records, evaluation filters):
- Synchronism
- the manufacturing errors of the disk are often no better than ± 0.06% and <0.075% can be expected from the playback device. Laypeople can hear 0.25% wow and flutter in the rhythm of the record speed. Hifi standard DIN 45500: <0.2%
- Crosstalk attenuation
- 25 to 30 dB in the medium frequency range can be achieved
- rumble
- HiFi standard DIN 45500 requires> 35 dB rumble-to-noise ratio and> 55 dB rumble-to-noise ratio
- Frequency response
- ± 2 dB level deviations at frequencies between 40 Hz and 12.5 kHz can be achieved; the highest playback frequency should be well above 20 kHz
- Nonlinear Distortions
- Intermodulation <0.5% can be achieved.
Record versus audio CD
The audio CD uses 16-bit sampling depth and theoretically achieves a dynamic range of 96 dB, which is better than the practically achievable signal-to-noise ratio for a record playback (typically 50 dB) and can map the entire audibility range. However, since the sampling rate of the audio CD (44.1 kHz) only allows accurate reproduction of just over 20 kHz ( Nyquist frequency approx. 22 kHz), the frequency range of the audio material must be strictly limited before it is digitized in order to avoid artifacts avoid.
With the introduction of the audio CD in the mid-1980s, sales and production numbers of records fell ever faster. In 1990, twice as many CDs were sold as long-playing records. At the beginning of the 1990s, the most important groups in the phono industry jointly proclaimed the "death of the record". From then on, the focus was only on the audio CD, or later on further developments such as SACD and DVD-Audio , which, however, could not prevail.
Source: Federal Association of the Phonographic Industry / Federal Association of the Music Industry . Data for 1990 from July with the new federal states
Compared to audio CDs, records require a great deal of effort in terms of the playback chain in order to be able to keep the physical inadequacies of the analog LP as small as possible: the drive, combination of cartridge and tonearm, stylus and phono pre-stage are the most distinctive components that improve the sound quality influence.
In the case of an audio CD, the scanning is not subject to any limitations with regard to geometric inadequacies and synchronization. Among other things, the grooving background noise (rumbling, background noise) that is unavoidable on records and causes losses in dynamics , especially in classical music , is eliminated .
There are also differences between records and CDs in terms of their long-term durability and the effects of faults on the sound carrier: while a scratched record can suffer from the well-known loss of sound and the possibility of getting stuck or jumping over the sound groove, errors on the CD only become noticeable when the sound drops out if the missing information cannot be reconstructed by the internal error correction of the CD player .
Compared to the smaller CD booklet , the record sleeve expresses the design of the sleeve more clearly. In addition, complete recordings of operas etc. are often included as “booklets”.
The record is still popular with DJs , especially in the fields of house , techno , hip-hop , drum and bass, and the like, because its technology makes it well suited for merging individual tracks (pieces of music). The record is mixed (mix) into the other tracks by means of two special turntables with continuously adjustable playback speed or moved by hand alternately in and against the playback direction ( scratching ) to create special sound effects .
This preference of DJs for the records, also known as “vinyl” for short, has led to the development of new systems (“ Final Scratch ”, “ Rane Serato Scratch Live ”) with which digital recordings can be controlled with conventional turntables. Special records are used for this, on which a time code was recorded instead of the audio signal . An external sound card (which often doubles as a dongle ) digitizes this timecode, which software then uses to control the playback speed and direction of a digital piece of music.
At the beginning of the 2010s, around 15,000,000 records were produced annually in Europe. After the introduction of the new phonograms, sales of vinyl records recovered somewhat. Worldwide sales of newly produced vinyl records increased by 89 percent in 2008 compared to the previous year. In 2006, 600,000 long-playing records were sold in Germany, 700,000 in 2007 and 900,000 in 2008. The record business still accounts for just under one percent of sales in the German music market.
The first record CD, which consisted of a side CD and a side vinyl, came on the market in 2007 with the single Deathcar by the band Fightstar .
Technical specifications
The sound storage takes place mechanically by recording the sound in a spiral groove and belongs to the needle tone method . Different mechanical or electrical pickup systems can be used for playback . The technical properties of the record in the form used today are specified in the DIN standard DIN IEC 98 (earlier standards: DIN 45536, DIN 45537, DIN 45546 and DIN 45547).
Formats
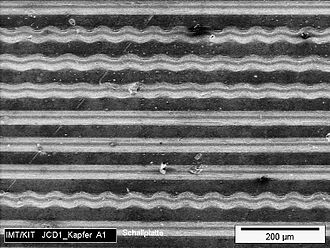
The technical design of the record was constantly changed during its development in order to improve playing time, frequency response and durability. The formats were specified in centimeters from the start, the English inch designations are only rough approximations; note:
- Actual diameter 17.5 cm: English designation: "7 inch" (2.8 mm deviation)
- Actual diameter 25.0 cm: English designation: "10 inch" (4 mm deviation)
- Actual diameter 30.0 cm: English designation: "12 inch" (4.8 mm deviation)
In addition to various special formats, some formats have established themselves as standards. The following are found in current publications:
- Single : diameter: 17.5 cm; Center hole1 1 ⁄ 2 ″ or 38.1 mm, also 7 mm; Playback speed: mostly 45 revolutions per minute, rarely33 1 ⁄ 3 revolutions per minute; Playing time (at 45 revolutions per minute) about 4–5 minutes per side.
- 10 ″ single : diameter: 25.0 cm; Center hole: 7 mm; Playback speed: mostly 45 revolutions per minute, in the 1950s to 1970s often33 1 ⁄ 3 or 78 revolutions per minute (shellac record, about 3 minutes per side). The 10 ″ single format is rarely chosen for new releases.
- Maxi-Single (Twelve-Inch): Diameter: 30.0 cm; Center hole: 7 mm; Playback speed: usually 45 revolutions per minute, less with33 1 / 3 revolutions per minute, very rare combinations of the two speeds on a record (. A- and B-side, for exampleYellowish); Playing time up to 16 minutes per side. Shellac records with 78 revolutions per minute of this diameter had about 5 minutes playing time per side.
- Extended Play (EP): Diameter: 17.5 cm or 30.0 cm; Center holes like single or maxi-single; Playback speed: 45 or33 1 ⁄ 3 revolutions per minute; Playing time 5–8 (30 cm: up to 15) minutes per side. The EP represents an intermediate format between a single and a long-playing record.
-
Long Play / Langspielplatte (LP): diameter: 30.0 cm, previously also 25.0 cm (Medium Play, MP); Center hole: 7 mm; Playback speed: 33 1 ⁄ 3 revolutions per minute, rarely 45 revolutions per minute; Playing time approx. 20-25 minutes per side (MP approx. 15 minutes per side). For a short time, long-playing records were also produced with 16 2 ⁄ 3 revolutions per minute, which reached up to 60 minutes of playing time per side. Due to their limited sound quality, these records were only intended for voice recordings, such as radio plays, but could not establish themselves because only a few record players had the corresponding setting. Their production ended quickly, so they are very rare. Long-playing records for special purposes (playback of pre-produced radio programs, etc.) were also produced, especially in the USA, with a diameter of 16 ″ (40.64 cm) and a speed of 33 1 ⁄ 3 revolutions per minute, their playing time was around 30 Minutes per side.
The groove speed of a 30 cm long-playing record is 50 cm / s on the outside at the beginning of the modulated groove at 29.2 cm diameter and only 20 cm / s on the inside at the end of the modulated groove at 11.5 cm diameter. This also explains the audibly decreasing sound quality of a record towards the inside. - Intermediate formats: Diameters: 2 ″, 4 ″, 5 ″, 6 ″, 8 ″, 9 ″, 11 ″ are known, but very rare.
The playing times given are only rough guidelines, as the actual playing time depends, among other things, on the modulation of the cutting stylus and the low-frequency components, especially in the S-signal ( subscript ) during record production, which influence the packing density of the playback groove.
Plate fonts
There are three main engraving methods, two of which are still in use today. The size of the groove has continued to decrease over the years. While shellac records had a groove width of 120 µm (normal groove) , the microgroove commonly used today is 40 µm wide without modulation; the bottom of the groove has a radius of 8 μm. The distance between the grooves is about 70 µm with a linear feed without the use of filler letters.
Subsection (vertical section)
In the case of the indentation used by Edison and Pathé , the information is imprinted on the record by the depth of the cutting stylus. The depth is directly proportional to the amplitude of the recorded signal. The maximum amplitude to be recorded is small, as the immersion depth cannot be arbitrarily large. In order to be able to reproduce high frequencies, the needle must also follow the indentations of the groove very quickly. In order to achieve this, the contact force of the cartridge has to be increased, which, however, leads to increased record wear.
Page writing (horizontal section)
In the side font introduced by Emil Berliner in 1888 , the information is embossed in the horizontal deflection of the groove. The advantage over the subscript is a larger dynamic range and the easier production of copies. In contrast to lettering, the crackling is significantly reduced. The side script was used on gramophones and early record players. It is only suitable for one channel and, in the case of gramophones, uses a steel needle to deflect a membrane that opens into a funnel. When playing a mono record in side-by-side writing with a stereo pickup, the mono signal is played on both playback channels.
Flank font (V-cut)
The flank font, developed by Alan Blumlein around 1930 but not marketed by EMI until 1957, made monocompatible stereo recordings possible for the first time. The sound information for the left and right channels is imprinted on the 45 ° flanks of the groove. The left channel is saved in the inner flank and the right channel is saved in the outer groove flank. The direction in which the cutting stylus is deflected is out of phase with the left and right channels, so that a mono signal recorded with a stereo cutting head generates page writing. This ensures downward compatibility with mono systems: If a stereo record is played on a mono player, only the horizontal deflection of the groove is played. This corresponds to the sum (L + R) of both channels.
Rheinsches Füllschriftverfahren
The fill lettering process was invented by Eduard Rhein in 1949 and does not designate a new disc font of its own, but rather the level-dependent control of the groove spacing on the sound carrier. It was developed to further increase the playing time. Since the lateral deflection of the recorded groove depends on the volume of the sound material, the groove spacing can be reduced for quiet passages. In practice, the material to be recorded is monitored before the cutting head. The groove feed is then influenced by the volume of the following rotation. The additional cycle time gained by using the filler font instead of the constant groove spacing depends on the program. It is greatest for speech; for music, the playing time can be up to 1.7 times longer. The word “filler font” was very effective in advertising because it suggested a “fuller” sound.
Scanning
Depending on the size of the groove, styli with different rounding radii must be used; the sizes of spherical styluses are given:
- Normal groove: 65 µm
- Microgroove: 25 µm
- Stereo groove: 15 µm
The normal groove corresponds to a shellac record (78 revolutions per minute), the micro groove to a mono record from the 1950s and 1960s, and the stereo groove to a stereo record that is still used today. For the latter, however, more modern needle cuts with smaller and different rounding radii are mostly used today.
Playing time
The playing time of an LP side with 33 1 ⁄ 3 revolutions per minute is limited by the technical specifications and the desired sound quality. Playing times of up to 25 minutes are possible without loss of sound. Playing times of up to around 28 minutes per side can be found in pop and rock, and in individual cases even over 30 minutes ( UFO 2 - Flying - One Hour Space Rock ). The "louder" you engrave the content, the less playing time is available. A high bass component also has a disadvantageous effect here, since it requires greater deflections. In order to achieve the highest possible sound quality, avoid cutting too far inwards. This is particularly noticeable with classic records. Ultimately, this makes it possible to set very different priorities for optimization or to represent corresponding technical "philosophies". The difference in volume is particularly noticeable between hit samplers and albums. If the volume setting of the amplifier is unchanged, a music track on an album is considerably louder than the same track on a hit compilation, on which ten tracks are pressed per side. The dynamic difference is even greater with contemporary techno, bigbeat, trance and Goa records, which are basically pressed in LP size, but only contain one title per side. These club titles, which are only produced for DJs, are recorded particularly loudly because there is a correspondingly large amount of space available for the groove on the record.
The French manufacturer MDR (Magnetic Disc Recording) pushed the technically possible playing time to extremes in the early 1970s and released LPs under the label name Trimicron , which had a running time of up to 58 minutes per side. Their sound quality was correspondingly inferior, because this length could only be achieved through an extremely narrow groove spacing and an unusually low level. These sound carriers could only be used with particularly carefully adjusted playback devices and with the use of brand-new scanning needles.
lifespan
With appropriate care and storage, a vinyl record has an almost unlimited shelf life; When playing with a needle, however, mechanical wear occurs, which shortens the service life of a record and impairs the sound quality - this can only be avoided by optical scanning, for example with a laser record player (see above).
Manufacturing
Industrial pressing

For the production of a record in large numbers, the mastered program material is first cut into the lacquer of a coated film with a heated cutting stylus. According to a standardized characteristic curve, the higher-frequency sound components are raised ( pre-emphasis ) and the lower ones are weakened; During playback, the frequency response is reversed equalized. This lacquer plate is first coated with silver so that it is electrically conductive, and then galvanically copper-plated or nickel-plated. This metal layer forms a negative about 0.5 mm thick, the "father". Several positives, "mothers", are deducted from this in a further galvanic process . These are played back by the master engraver to check the recording and, if necessary, reworked. The actual press dies ("sons") are in turn manufactured from the mother plates using a galvanic process. In order to increase the durability of the press dies for larger quantities, they are chrome-plated . This process must be repeated for both sides of the record.

In order to avoid the detour via “fathers” and “mothers”, Teldec developed the so-called DMM process (“Direct Metal Mastering”) at the beginning of the 1980s . Here the cut is made directly into a copper layer applied to a stainless steel plate, from which the "sons" are then created immediately. The advantage of lower distortion is offset by the disadvantages of lower groove depth (durability) and deflection (playback level).
Polyvinyl chloride (PVC) is used as the raw material for the pressed records , to which around 20% polyvinyl acetate (PVAc) and other additives are added. The actual raw material is milky-transparent and can be colored by adding dyes. The previously necessary admixture of soot is no longer necessary today. There are no significant qualitative differences between black and colored pressings, and the exact composition of the material varies between different press shops.
When producing a record (so-called audiophile pressing), recycled vinyl cannot be used, only pure, fresh PVC raw material ("virgin vinyl"), since the label paper cannot be completely removed during recycling and this paper residue leads to pressing defects or increased crackling being able to lead.
The pressing process of a record takes about 30 seconds. A metered amount of raw material (150-180 g) is placed between the two press dies together with the labels and pressed at a pressure of about 8 · 10 6 Pa (about 80 kg / cm²) and a temperature of about 150 ° C. After a short cooling phase, in which the matrices are cooled with water, the press is opened and the record is removed. Production can also be partially automated: after opening the press, the record is placed on the cutting plate using a retaining ring and a punching plate. This creates a vacuum for fixation and is then set in rotation. A knife attached to the outer edge of the cutting plate cuts off the pinch burrs created during the pressing process. The record is then removed from the plate by means of a transport arm and temporarily stored on a spindle until it is packaged, while the record is cooled by the ambient air for about 10 seconds. In the meantime, the extruder produces another press cake and the process starts all over again.
Injection molding
An injection molding process can also be used for the production of small formats (7 ″ singles and smaller special formats) in large quantities . To do this, hot plastic material in liquid form is placed between the matrices. The material cools down in the hollow mold and solidifies.
These plates do not have a paper label, instead the die contains the lettering in a raised form so that the lettering is slightly deepened on the plate. In a further process, the middle part of the plate is colored so that it stands out visually from the recessed black characters. At least some of these panels are more fragile than conventional pressed vinyl panels.
A further development of injection molding is compression molding , which is also used in CD production.
Single cut
For very small quantities, the clay material is cut directly into a blank ( dubplate ) with a cutting stylus . Originally there were only lacquer dubplates ; they consist of a thin aluminum plate coated with polyvinyl acetate (PVAc) into which the audio material is cut. Lacquer dubplates only have a limited lifespan.
To produce vinyl dubplates , blanks are cut from a PVC-PVAc mixture on a so-called vinyl cutter . The result is a real, long-lasting vinyl record that, when professionally manufactured, does not differ from pressed, commercially available vinyl. The production of such unique pieces is particularly interesting for producers and DJs who want to try out self-produced pieces as quickly as possible at events or who want to use titles that have not been released on vinyl for turntablism .
Special forms
Vertical writing plates
From around 1900, various manufacturers, including the French group Pathé , used the so-called vertical font format. The recording did not take place here through lateral deflections, but through an up-and-down movement. The pick-up function was not a needle that would quickly destroy the depth differences in the groove, but a tiny, movably mounted sapphire ball that rolled through the groove. Systems of this type remained particularly popular in France and the United States until the 1920s.
Unusual plate diameter
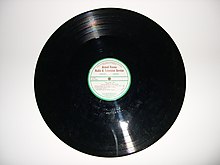
In addition to the standard record formats with a diameter of 25 and 30 cm, there were numerous other commercially used record diameters in the shellac era. Apart from advertising and toy records , the smallest series records of the shellac era were the American Durium Junior pressings from 1930 with a diameter of 10.2 cm (4 ″). The huge Pathé Concert pressings from the time before 1914, which had a diameter of 50 cm, are considered to be the largest series plates . In the United States, during and after World War II, radio broadcasts were recorded on 16 ″ (40 cm) records [less often 12 ″ (30 cm)] and sent to troops stationed around the world. Initially made of shellac , these so-called V-Discs had an astonishingly high sound quality for the time; they are sought-after collector's items today. In the 1960s and 1970s, broadcasters still used some 16 ″ (40 cm) diameter disks, which also required appropriately sized playback devices.
Very rarely there are plates with a normal large outside diameter, but more than a normal large label diameter inside . The grooved ring from the outside to the inside is effectively narrower, and an LP cut in this way becomes a de facto EP. One example is the German children's record Der Froschkönig (also pressed onto colored vinyl).
Unusual materials
In the course of the first 70 years of record production, there were repeated attempts to replace the expensive, hard-to-find raw material shellac with other, cheaper materials. Shortly after 1900, the British company Nicole Records presented records made of a celluloid- coated fiber material. A little later, the first "sounding postcards" with glued-on celluloid sound foils appeared at Zonophone in Berlin. The steel needles of the gramophones destroyed these sound carriers very quickly, however, because the celluloid used lacked the necessary abrasion resistance . Later, after the micro-groove had generally prevailed, distribution Qualiton "sounding" Postcards called Tonpostkarten for 45 revolutions per minute (or 33 1 / 3 rpm) in the envelope to avoid damage during shipment and exposure to dust in storage . Playable postcards are still produced in small editions today.
In 1905 the Berlin company Auto-Record brought a cardboard sheet with a celluloid clay backing onto the market. Around 1906, the British Neophone group also temporarily produced sheets of cardboard that were covered with a waxy carrier material and were not heat-resistant. In the 1920s, the Berlin-based company Metallophone produced records from painted sheet steel . In the 1940s, records made of coated glass were used primarily in studio technology . Around 1910, the confectionery manufacturer Stollwerck presented records pressed from chocolate, which contained well-known children's songs , could only be played a few times and could then be consumed.
During the Cold War , illegal images were partially cut onto used X-ray images in the Soviet Union and traded on the black market. The advantage of the carrier material was its general availability and flexibility. The flexible panes could be hidden better under clothing than conventional panels. The quality of the recordings was naturally very poor. Due to the origin of the foils, these sound carriers were colloquially referred to as rock on the bones ( рок на костях ), ribs ( ребра ) or simply bones ( кости ).
At the end of 2015, the German Federal Institute for Materials Research and Testing presented a record made of ultra-high-strength concrete for advertising purposes . The filigree malleability of the material was to be demonstrated.
Unusual shapes and colors
Transparent maxi-single on printed slip film
Record from an X-ray film : "Music on ribs"
Especially in the field of rock music , rap and electronic music , records are made that stand out from the standard record by their appearance. So are z. For example, the so-called picture discs , in which transparent material is pressed around a printed image, are quite common. Colored and / or transparent PVC is also common. These plates often appear in limited editions and can be of great collector value. Another variant are the so-called shape vinyls . Unlike ordinary records, they are not round, but can have the most unusual shapes (which, however, only refers to the outer contour - the sound is recorded in the usual spiral shape). This eccentricity is used as a combination of photo and shape: A photo (likeness of the star, guitar, heart, full body or band photos, etc.) is not reduced to the round record shape, but the photo is sawn out of the record, so to speak. The outlines form the playback medium, the maximum area in the inscribed circle of the disk contains the grooves.
Reverse spiral direction ("inside out cut")
While the needle moves from the outside to the inside with "normal" records, there are also formats that are played from the inside out. The best-known in record history are the deep writing records made by the French company " Pathé Frères" before the First World War. But also the records produced by the Reich broadcasters during the Nazi era for internal use and mutual exchange were partly part of it. According to the standard, turntables rotate to the right, i.e. clockwise , when viewed from above, while the stationary needle rotates to the left relative to the moving plate. The normal groove runs to the left from the outside to the inside. The groove of a plate with what is known as the “inside out cut”, however, when viewed as a spiral to the left, leads to the outside and, during operation, does the needle as well. In any case, the groove must form a closing circle near the outer edge, because turntables do not switch off here.
Reversing the spiral direction can also be advantageous for purely sound reasons: A lower running speed causes less running noise, while a higher running speed can reproduce louder and more dynamic material more reliably. For example, pieces of music that begin quietly and end loudly can be optimally accommodated, without having to accept the disadvantages of the otherwise usual direction of movement from the outside to the inside or having to compensate for them with appropriate tonal changes.
Early long-play formats
The British sound engineering pioneer Michaelis made the first attempts with micro-groove formats, which should enable a longer playing time of the record, in 1906. His company Neophone produced 25 cm records with a running time of around 12 minutes. In 1926, Thomas Alva Edison presented one of his last inventions, a long-playing record with extreme micro-grooves (see Diamond Disc ), which had a running time of more than 20 minutes per side at 80 revolutions per minute and 24 cm in diameter. The record could only be reproduced with a special diamond pickup and was half a centimeter thick in order to eliminate any flexibility. The sensitivity of the micro-grooves, the walls of which could be damaged by normal contact with the plate, prevented any commercial success of the system, which only remained on the market for a few months. The first commercially recorded LP with 33 1 / 3 rpm came on 17 September 1931 on the market.
Plates with atypical central holes
A phenomenon that was particularly widespread in the USA before 1914 were records with particularly large center holes. Record manufacturers such as Aretino and Busy Bee tried to set their own standards in this area. The background was not based on technical considerations, just marketing strategies. On the other hand, unusually small center holes, which resulted from an industrial standard deviating from the western standard , were a feature of Soviet records from the 1920s and 1930s.
At the end of the 1950s, Seeburg, an American manufacturer of jukeboxes , brought out a special record changer and a record format that has a diameter of 22 cm, center holes of 5 cm and a speed of 16 2 ⁄ 3 revolutions per minute. This was intended for background music.
Constant scanning speed disks
The path that the needle covers during the playback process on the record per revolution becomes smaller as the playback time increases due to the helical course of the sound groove. Since the speed of the turntable remains constant with conventional records, the speed of the needle decreases continuously relative to the record surface from the outer edge of the record to the inner one. This change can be perceived acoustically under certain circumstances. In order to eliminate the phenomenon, experiments have been carried out since the 1920s with plates that have a constant linear speed through permanent adjustment of the speed. However, each player had to be equipped and adjusted with a special device. One of these devices was the so-called World Disc Record Controller in the USA . Such systems have not caught on.
With digital optical media such as the laser disc encoded with pulse-pause lengths and later also the compact disc and its successors, appropriate techniques are easier to implement because dynamic intermediate storage decouples the synchronism from the disc. See also CLV .
Plates with several grooves
In the early 1930s there were records with four grooves: "The series for good house music". At the beginning of each page there was a groove with the concert pitch A, according to which you could tune your own instruments. Only after the pickup arm was put on again did the second groove begin to play along with singing.
In the early stages of self-cutting vinyl records, several sections were common, each with a groove until it was completely filled in order to save blanks. Each section had its own outlet groove at the end, and you had to put the pickup by hand at the beginning of the next section if you wanted to continue playback.
Multi-Groove Occasionally, records have been released with two or more intertwined, parallel grooves. It is a matter of chance in which groove the tonearm touches down, so that the listener does not initially know which music he will be listening to. This technique became generally known in 1979 with a special pressing of the hit single Pop-Muzik by Robin Scott , which also contained the track M-Factor on the same page and was marketed as "The First 'Double Groove' Disk" according to the advertising text on the record cover. However, the comedy troupe Monty Python had already released the "three-sided" LP Matching Tie and Handkerchief in 1973 , which also caused confusion because both sides of the record were provided with identical labels (but the front and back could be embossed on closer inspection Die number can be distinguished). In 1975 the record Wim Thoelke presented: The Grand Prize - Die Volksstümliche Schlager-Starparade came out (Sternmusik in Ariola-Vertrieb, 88909XT). The first title on the A-side is a car race with music and commentary by Wim Thoelke, in which one of three cars wins, depending on the inlet groove hit. Multi-groove records were particularly popular when the same song was released in different versions, mostly as a 12 ″ single due to the larger space requirement. In 2009 the triple A single HimmelblauPerfektBreit by the band Die Ärzte was released on a 12 ″ vinyl record with a triple helix.
Records being digital data carriers


After modulation (digital-to-analog conversion with a digital-to-analog converter ), each audio carrier can also be used for the storage of digital content. A demodulator is required to recover the data . These methods were particularly popular in the era of home computers or small computers in the 1980s, although a record was only rarely used for this. The standard medium was the magnetic tape or audio cassette , which was also designed for sound recording (in drives, usually referred to as datasette , which were technically cassette recorders ), which were, however, replaced by the much faster and more convenient floppy disk drives in the course of the 1980s .
The only data record produced in large numbers was a pressing of the GDR youth radio DT64 , the software often used for the small computers KC 85 , HC 900 , Z1013 and others. contained. It was distributed along with a book.
The German band Welle: Erdball also pressed a program for the home computer Commodore 64 on their first vinyl release "Horizonterweiterungen" in 2005 . After copying it to a magnetic tape cassette, it could be executed via a datasette on the C64.
Another example is provided by the Synthpop band Information Society with their album "Love & Peace Inc.", which saved a short text for fun in this way. Its decoding, however, was left to the user.

Digital vinyl systems use time code records that do not contain music, but a digital time signal that is evaluated by software . The technology makes it possible to determine the speed and position of the tonearm on the record at any time and evaluate it almost instantaneously. The timecode vinyl can thus be used to control digital music files (for example in MP3 format). The turntable serves as a control interface.
Vinyl video
The Viennese artist Gebhard Sengmüller introduced in the late 1990s together with physicist Martin diamond for a system with which it was possible to store videos on ordinary LPs. The video images were pressed onto the plates in analog form. Since a record, due to the maximum storable frequency of almost 20 kHz, only allowed a very small bandwidth, the video signal had to be very heavily compressed and then converted into a sound signal, which could then be pressed onto the record. For this reason, the resulting picture was only black and white, the frame rate was greatly reduced compared to a normal television picture and the resolution was far below that of VHS . In addition, due to the error-prone analog storage, there were many image disturbances, such as flickering and trembling. Because of these technical limitations, the quality of the films shown was more reminiscent of the early days of television history .
Any conventional record player could be used for playback, whereby an additional device was required that decoded the analog signals with the help of digital technology and converted them back into a standardized PAL or NTSC video signal.
The project was intended purely as an experiment and a technical gimmick to fill a gap in the history of video recording, especially since a large number of very high-quality video systems already existed on the market at that time . Accordingly, 1950s-style vinyl video was advertised.
Only a very small number of decoders were produced and only a few dozen titles were available, most of which were short films by independent artists.
Flexible Disc (Flexidisc)
The flexible disc ( Flexidisc , sound foil or Flexi ) is a record made of very flexible material. Mostly they are films made of polyethylene or similar plastics. Flexi are used, for example, as a supplement in fanzines or children's magazines. A normal record with a small center hole is required as a base for playback. For technical reasons, they are often only played on one side. The sound quality is worse than that of vinyl records.
Vinyl disc
A combination of analog record and CD or DVD has been manufactured and marketed exclusively by the German company optimal media GmbH since autumn 2007 . The protected vinyl disc is the size of a CD and contains digital information on the silver underside and a record groove on the black top for playback on analog turntables with a playing time of up to 3 minutes at 33 1 ⁄ 3 revolutions per minute. The centering on the turntable is done by means of an included adapter. The vinyl side can be printed with up to three colors using CD screen printing. The surface is additionally matted to simulate the appearance of a conventional record label . The main purpose is the promotion of new music titles (analog part), whereby information, video clips or computer games can also be accommodated on the digital part.
The actual idea comes from the small label Squoodge Records from Austria. In January 2007 it published the first small series of a vinyl disc in the so-called DigitalVinylTrash Club without having the format legally protected.
Advertising in the cinema
Up until the 1970s, it was common in the cinema to show advertising slides (a few 35mm slides , but mostly in medium format ) before the main film. Music and texts for individual slides were provided on records. The presenter had to manually play the appropriate advertising single for each slide.
Talking dolls
In speaking puppets for children, very small exchangeable records were used, which were played according to the gramophone principle, so-called miniphon records. Small records for sound reproduction were also built into other toys (“ salmon sack ”). These records found a musical use in the work "Choirs and Solos" by the German band Die Tödliche Doris .
Voyager Golden Records
The Voyager Golden Records are data disks with image and audio information that are attached to the two interstellar space probes Voyager 1 and Voyager 2, which were launched in 1977 . They are gold-plated discs made of copper with a diameter of 30 cm, which contain greetings, sounds and music, as well as pictures stored in analog form.
Press weight
The record pressing plants offer pressings of various weights. For long-playing records, for example, 120, 130, 140, 150, 180, 200 grams, etc., each weighed without inner sleeve and cover. In the 1970s and 1980s, 120–140 g was common, today 180 g is often chosen. The industry tries to give the impression that higher weight is associated with better sound. However, this naive notion is a legend. Although the needle has to plunge into the groove, this plunge depth is many times less than half the thickness of even very thin plates. The "sound" is cut in width and scanned on the groove flanks. Even the obvious idea that a particularly heavy plate is less prone to thermal deformation (vertical runout) than a light one does not correspond to the facts. On the contrary: because of their mass, 180 gram plates hold their shape more difficult than the usual 130 g. 180 g vinyl is a pure marketing gag in order to be able to sell the expensive product better and to be able to justify the currently very high record prices to the customer. Several blind tests showed that the listeners preferred the “thin” first editions from the seventies and eighties to the heavy 180 g pressings because of their better sound quality. Decisive for the sound is not the weight of the record, but factors such as the condition and treatment of the mother tapes, the care of the sound and cutting engineers, and the quality of the polyvinyl chloride.
Measures against static electricity
Newer records are made of the non-conductor polyvinyl chloride and thus attract dust and dirt due to the electrostatic charging of the material. In addition, the plate rubs against the inner casing when it is pulled out of it. In the history of vinyl records, there have been a number of methods of unloading the records and keeping the grooves clean.
- The antistatic pad is placed on the turntable and is supposed to reduce the charge due to its electrically conductive material.
- The antistatic cloth is a chemically impregnated cloth with a sometimes slightly sticky surface, which is used to remove dust from the records before playing them.
- The surface of the plate is sprayed with an antistatic spray.
- For discharging with piezoelectricity , the Polydor company brought a batteryless rod on the market in the 1980s, which stimulated a piezo crystal to emit sparks on the underside by moving the upper part back and forth . The rod was moved over the surface of the plates and the generated “thunderstorm” neutralized part of the static charge.
- Disco film (brand name) was applied to the record from a spray can or with a sponge. After the chemical dried, it formed a cohesive film that also reached into the grooves. You could pull it off in one piece and thus remove dirt and solids from the grooves. In practice (mostly when the layer was too thin) the film broke again and again, which led to the time-consuming removal of individual fragments.
- If a record was very dirty from static electricity, it was washed in an aqueous surfactant solution . Afterwards it was imperative to rinse the plate with distilled water in order to remove the residues of the cleaning agent and the lime-containing water.
- In the early 1980s, record brushes with extremely thin, conductive carbon fiber bristles came onto the market. Static charges could be discharged through body contact with the brush housing.
- The Maxell company brought an apparatus onto the market in the mid-1980s. In this system, a small device rotated on the plate, on the underside of which a wide brush made of very soft conductive carbon fibers brushed the dirt out of the grooves.
- In record washing machines (which are still available), the record is wet cleaned in a closed system, sometimes also with ultrasound ; then the grooves are freed of dirt and cleaning solution by strong suction.
Care set from Teldec for cartridges and records
Wet playing of records
When playing wet, in addition to the tonearm, there is an additional cleaning arm running on the rotating record, on the underside of which there is a small brush that wets the groove flanks with a mixture of distilled water and isopropanol . This cleans the flanks and floats up remaining dust particles so that they are not noticeable when scanning. After the liquid film has evaporated, however, small residues remain in the groove flank and the remaining dust particles now adhere more firmly to the surface than before. For this reason, records that have been played wet should also only be played wet in the future.
In addition, the rotation speed of the turntable must be readjusted when playing wet, as the additional brush brakes the record slightly when it is turned.
See also
- German record award
- German Record Critics' Prize
- Recording company
- Endless groove
- Tefifon (sound tape)
- Image plate
- puck
- The talking book
literature
- Fritz Bergtold: Modern record technology . Pocket textbook of gramophone playback. Franzis, Munich 1959.
- Stefan Gauß: Needle, groove, funnel. Cultural history of the phonograph and the gramophone in Germany (1900–1940). Böhlau, Cologne / Weimar / Vienna 2009, ISBN 978-3-412-20185-2 .
- Rainer Haarmann: Longplay, the history of records and modern jazz / The History of Records and Modern Jazz. JazzPresso, Bad Oeynhausen 2008, ISBN 978-3-9810250-7-1 . (Catalog of the JazzBaltica exhibition, Landeskulturzentrum Salzau, July 4th - August 17th, 2008).
- Antonia Kosseva-Göldi: Sound packed: record sleeves and their special conservation and restoration problems - with special consideration of laminated sleeves. University of the Arts (HKB), Bern 2012. Master's thesis.
- Frank Wonneberg : Vinyl-Lexikon - Truth and Legend of the Record. Technical terms, collectors' Latin and practical tips. Schwarzkopf & Schwarzkopf, Berlin 2000, ISBN 3-89602-226-1 .
Web links
- Article from the magazine Schalltrichter about the very first record in the world
- Directory of records at discogs.com
- Map of Germany 6/2017 "Record stores" by ZEITmagazin, February 20, 2017
- Video: Record production "How Vinyl Record are made": Part 1 and Part 2 on YouTube
- Ralf Klee: Sounds from the past: memory in gelatine. in: Zeitgeschichten on Spiegel-Online, January 7, 2008 (with audio samples)
- Bodo Mrozek: History in Discs: Records as contemporary historical sources. In: Zeithistorische Forschungen / Studies in Contemporary History, online edition, 8 (2011), no. 2.
- Sound archeology software makes 120-year-old records audible again
- Electro-mechanical relationships in vinyl mastering
Individual evidence
- ↑ Publication of the US patent "GRAMOPHONE" for E. Berliner (English)
- ↑ The record cutter: cutting and playback case, type: Ela A 107/1, Telefunken Berlin 1932
- ^ Ron Penndorf: Early Development of the LP. (No longer available online.) Archived from the original on November 5, 2005 ; Retrieved October 4, 2006 .
- ↑ netzeitung.de: Congratulations, record ( memento from February 1, 2014 in the Internet Archive ) , accessed on June 22, 2008.
- ↑ a b Michael Dickreiter, Volker Dittel, Wolfgang Hoeg, Martin Wöhr: Handbuch der Tonstudiotechnik , Verlag Walter de Gruyter 2009, 1332 pages, page 588f
- ↑ a b http://www.fl-electronic.de/analog/schallplattenwiedergabe.html Record playback , message from FL-electronic GmbH, accessed on Nov. 2, 2020
- ↑ a b c d e Harry Wolff: Music market and media under the aspect of technological change. (= Osnabrück contributions to systematic musicology . Volume 3). Electronic Publishing, Osnabrück 2002, ISBN 3-923486-37-5 , p. 30.
- ↑ 2012 sales figures ( memento of August 13, 2013 in the Internet Archive ), accessed on March 11, 2014.
- ↑ 2013 sales figures ( memento of September 27, 2014 in the Internet Archive ), accessed on September 11, 2014.
- ↑ Sales figures 2014. (No longer available online.) Musikindustrie.de, formerly in the original ; accessed on August 4, 2015 . ( Page no longer available , search in web archives )
- ↑ Paragraphs 2014 ... (PDF) Musikindustrie, 2015, accessed in 2020 .
- ↑ Florian Drücke (ViSdP), Sigrid Herrenbrück, Georg Sobbe, Anna Jakisch: paragraph music industry 2015. (PDF) Prof. Dieter Gordy, Dr. Florian Drücke, accessed on May 22, 2017 .
- ↑ Florian Drücke (ViSdP), Sigrid Herrenbrück, Georg Sobbe Collaboration: Katharina Meinert, Sandra Wögerer: Sales Federal Association of the Music Industry. (PDF) Prof. Dieter Gordy, Dr. Florian Drücke, accessed on May 22, 2017 .
- ↑ BVMI | Unit volume. Retrieved January 10, 2019 .
- ↑ BVMI | Unit volume. (PDF) Retrieved August 24, 2019 .
- ↑ BVMI | Unit volume. Retrieved February 4, 2021 .
- ↑ Susanne Groth, Alexander Uhl: CD decay threatens cultural heritage. In: Heise online . German Music Archive , July 22, 2007, accessed on February 17, 2014 .
- ↑ They have a disk! In: Spiegel Online. May 22, 2009, accessed December 10, 2014 .
- ↑ (Tmn): Precious items in vinyl: records last almost forever. (No longer available online.) In: RP Online . Archived from the original on February 3, 2014 ; accessed on February 17, 2014 .
- ↑ Flexi Records
- ↑ Gunnar Leue: History of the record: The shine of shellac . In: The daily newspaper: taz . July 16, 2020, ISSN 0931-9085 ( taz.de [accessed July 17, 2020]).
- ↑ Florian Hassel: Later visit to a myth. In: Berliner Zeitung , August 13, 1998. ( berliner-zeitung.de ( Memento from January 25, 2013 in the Internet Archive ))
- ↑ Roman Tschiedl: Bootlegs on X-ray film: The illicit sound of the Cold War. Ö1 Diagonal - Radio for Contemporaries , April 2, 2016. ( oe1.orf.at ( Memento from April 17, 2016 in the Internet Archive ))
- ↑ And it sounds: The concrete record is here , accessed on June 5, 2020
- ↑ The VINYL CUT ( Memento of 8 February 2005 at the Internet Archive ) Vince LaDuca, September 1 2000th
- ↑ Rille backwards - Ravel's Bolero new on vinyl, stereoplay, issue 4/13 Website of the record company TACET Musikproduktion. Retrieved February 22, 2018.
- ↑ Andreas Kunz: The 180 gram myth . In: Stereo 10/2017, supplement Hifi analog , pp. 18–21.
- ↑ NN: Myth of 180 gram vinyl . In: Mint 02/2016, p. 17.
- ↑ Record lovers point out that distilled water , formerly known as battery water , still contains unwanted (mineral) residues, which can be avoided with double distilled water - especially when washing records . However, it is significantly more expensive.