Blast furnace
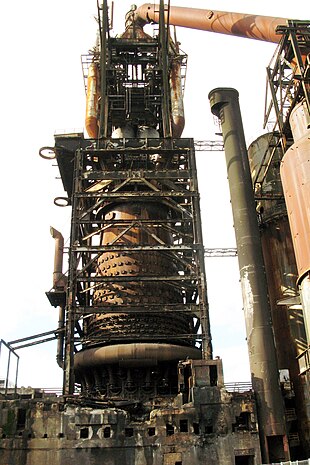

A blast furnace (also obsolete Hohofen ) is a large-scale plant with which liquid pig iron is produced from processed iron ores (mostly oxides ) in a continuous reduction and smelting process .
The entire plant is also known as an ironworks or smelting works and, in addition to the blast furnace as the central component, has other facilities that ensure continuous operation. These include the bunker for storing the input materials ( Möller : iron ore and aggregates ) and the heating materials ( coke ) with connected transport and piping systems to bring them into the furnace head in the blast furnace. Other devices serve to discharge the furnace gas at the furnace head, to feed the blower wind preheated by the blast furnace in the middle part of the blast furnace and to discharge pig iron and slag at the furnace base.
The additives contained in the Möller , such as silicon dioxide (quartz sand) , calcium oxide (lime) and others, are used during the blast furnace process to bind the undesired constituents of the ore in the slag and also lower the melting temperature of the iron . The coke, which is added in layers, serves as an energy carrier and reducing agent, and the hot blast blown in through several nozzles supplies the oxygen necessary for the combustion of the coke .
Part of the carbon and most of the phosphorus and sulfur that has been absorbed are then removed from the pig iron produced by refining before it can be processed into various types of cast iron or steel . Slag and furnace gas are also valuable blast furnace products which, after processing, are used to manufacture various building materials or as heating gas.
Modern blast furnace technology developed over the course of around 5000 years from the beginnings of the use of simple, charcoal- fueled and cold air (“fanned”) racing or lounger fires around 3000 BC. Chr. To racing furnace , piece furnace and raft furnace up to the blast furnace, which is heated with coke from the beginning of the 18th century and operated with hot blast from 1828.
history
For the earliest use and archaeological finds of iron see
The beginnings of iron smelting in Europe

One of the first simple and long-used forms of iron smelting was the so-called racing or Luppenfeuer . A funnel-shaped pit about 30 centimeters in diameter was filled with charcoal and easily reducible turf iron ore , ignited and supplied with atmospheric oxygen from a hemispherical, fur-covered bowl (an early form of the bellows ) that functions as a fan . After about ten hours, there was a fist big, black, with iron ore grains and unchanged or on the ground slag prevailed Luppe ( sponge iron accumulated). During the furnace journey, the iron does not liquefy in a racing furnace. The temperatures required for this can be reached without any problems, but the product obtained in this way would be severely carburized and no longer malleable. During operation, the temperature therefore had to be kept permanently in a range that did not allow the metal to liquefy. The racing oven , mostly made of clay or stones, was a further development of the racing fire with a side opening for the air supply and a short shaft for filling and refilling with charcoal before and during the oven. The shaft also supported the natural chimney effect , so that temperatures between 1000 and 1200 ° C could be reached. The air supply was initially realized with a natural draft, for example by building on an embankment , and the ovens were accordingly referred to as wind ovens or draft ovens . In the so-called fan ovens , on the other hand, bellows provided a more effective and controlled air supply. Depending on the size of the furnace and the duration of the furnace cycle, which could be between 4 and 20 hours, the early ironworkers received a rag with a weight of a few kilograms to several hundredweight . This was then freed of coal and slag by repeated heating (preheating) and forging , compacted and - mostly using semi-finished products - processed into the desired workpieces.
See also: Iron production in the Lahn-Dill area and iron smelting among the Teutons .
Up to the 18th century, racing furnaces with attached forges, so-called racing works, were still widespread and employed around five to ten men. The performance of the racing kilns at that time was around 60 to 120 tons of lump annually, with a charcoal consumption of 270 kilograms per 100 kilograms of iron.
Development of the blast furnace
Even though the racing furnace was used for a long time due to its simple construction, more powerful furnaces began to be developed as early as the beginning of the 13th century. The piece furnace (also known as the "wolf furnace"), which was named after the piece of iron that was taken out of the furnace, can be seen as a link to the development of today's blast furnaces . The furnace was a square brick, open-top shaft furnace , the size of which grew from about four meters in height in the late Middle Ages to ten meters in height in the 17th century, such as the piece furnaces in Vordernberg in Styria , a center of pig iron production in Central Europe at that time . The bellows of the ovens were driven by water wheels and the systems were therefore also referred to as wheelwork . They reached temperatures of up to 1600 ° C, with the mixture of iron ore and charcoal being partially melted. A further development was the blue oven, the name of which was derived from a corruption of the English word blow (= to blow). In principle it corresponds to the piece furnace, but has a closed furnace front.
In the forge , however, only the sponge iron (lobes) that had accumulated over the iron bath was initially processed ; in the piece furnaces it was so large that it was no longer processed by hand, but with forging hammers , also driven by water power . The molten pig iron produced by the smelting process, on the other hand, was initially viewed by the smelters as “spoiled iron”, which could no longer be used because it had absorbed such a high proportion of carbon that it was too brittle for forging. Of the hut people it was therefore also with various epithets as evidenced, among other Graglach or mud flow in the Steiermark and Saueisen in Germany. The latter has been preserved in English-speaking countries as a pig-iron for pig iron.
The problem was only solved with the invention of various processes for refining the iron, around the 14th century. With this possibility the way was open to further increase the efficiency of the ovens. Raft furnaces with meter-thick masonry were built, the frame of which was narrowed and in which the pig iron ( mild iron and mild steel ) and the slag produced after the smelting process was completed were drained together. Raft furnaces can be seen as the immediate "ancestors" of the blast furnace, since in principle nothing changed in the iron extraction process after their development. Amazingly, the oldest known raft oven discovered in the Kerspetal (Bergisches Land) was dated to 1275. In Siegerland there were in 1450 some 30 blast furnaces. With the increasing efficiency of the ovens and the increasing demand for iron goods, however, a new problem arose: The charcoal requirement for energy production could no longer be met. Hard coal was also used on a trial basis, but could almost only be extracted in open-cast mining . In 1755 there were almost 200 mines in the Ruhr area .
The Englishman Abraham Darby I (1676–1717) finally succeeded in 1709 in Coalbrookdale in the production of pig iron with the help of coke , after there had previously been a few less successful attempts with hard coal. Together with the steam engine developed by James Watt to drive the blowers, the performance of the blast furnaces could be increased considerably. In Germany, on the other hand, similar attempts were initially unsuccessful. It was not until the Royal Ironworks in Gliwice that a functional, coke-powered blast furnace was built in November 1796. With the help of coke, the amount of hot metal produced could be increased to two tons a day, with a consumption of three and a half tons of coke per ton of hot metal. The still small fresh furnaces could only partially process this amount of pig iron , the rest was used as cast iron .
With the development of cupolas towards the end of the 18th century, the cast iron industry experienced a veritable heyday. Cannons , church bells , cookware and, finally, art objects such as stove and fireplace plates decorated with reliefs and even jewelry were made from cast iron. Among the largest cast iron products are the Iron Bridge in England , built in 1777/79, and the 12-meter bridge built in 1794 over the Striegauer Wasser near Laasan (now Łażany ) in what is now Poland.
A final significant improvement in the performance of blast furnaces questioned the use is hot air, which later became the still used initially by tube blast stoves (Neilson, 1828) and Cowper - blast stove was delivered (1857).
The earliest known blast furnaces in Europe were in Sweden in the 13th century, for example in Lapphyttan . Individual blast furnaces in France, Belgium and above all England have been identified for the following centuries. The oldest, largely completely preserved blast furnace plant in Germany is the Luisenhütte in Wocklum near Balve in the Sauerland . In Saxony, three charcoal blast furnaces from the 17th and 19th centuries have been preserved in Brausenstein (1693), Schmalzgrube (1819) and Morgenröthe (1822). A blast furnace from 1783 can be seen at the Wilhelmshütte in Bornum am Harz and in the Sauerland the Wendener Hütte , which was also built in the 18th century, was declared a technical cultural monument. In Thuringia , in Schmalkalden - Weidebrunn, there is the New Hut Museum (Schmalkalden) . The late classicistic blast furnace from 1835 shows how pig iron was produced from local iron ores on a charcoal basis. The ironworks existed until 1924.
Iron smelting outside of Europe
The Tatara oven , a special kind of racing oven that is used in Japan to make iron, has been known since the 7th century at the latest . In contrast to the ovens used in other regions of the world, a Tatara oven is box-like in shape with a height of about 1.2 to 2 meters with an upper width of 0.8 to 1.2 meters, which extends down to only tapers about 0.5 meters. The length of the furnace, however, is about 4.5 meters. On both long sides, 18 to 20 ceramic nozzles ensure a sufficient supply of air, which in "modern" businesses is brought in via a fan blower driven by several men. The Tatara furnace is alternately charged with charcoal and iron ore sand and reaches temperatures of 1200 to 1500 ° C. After about three days, the furnace walls are smashed and a block of malleable iron and steel weighing about two tons is removed. The resulting slag was previously drained during operation. Even today, Japanese steel ( tamahagane ), traditionally made in Tatara ovens and known for its quality, is used for high-quality kitchen knives ( Hōchō ) or for the Japanese long sword katana , for example .
Chinese furnaces for iron smelting of the 19th century resembled an upside-down truncated cone about 2.5 meters high with an upper diameter of 1.2 meters, a lower diameter of almost 60 centimeters and a wall thickness of 30 centimeters and were made of clay . As a safeguard, the furnace was surrounded by a basket made of iron mesh and could be tilted by about 30 ° for easier removal of the pig iron. Brown iron stone , coal iron stone (“Blackband”) and, depending on the type of construction, charcoal or coke were charged. The air required to reduce the ore was brought in with a hand-operated cylinder blower. In this way, between 450 and 650 kilograms of pig iron could be produced per day with a coke consumption of 100 kilograms per 100 kilograms of iron. A similar blast furnace facility was also found in the Bulacan Province in the Philippines , which was operated until around 1900. The blast furnace had the shape of an upside-down truncated cone with an external height of 2.1 meters, an external diameter at the top of 1.5 meters and a wall thickness between 30 and 80 centimeters.
At the beginning of the 20th century, peoples were discovered in Africa who reduced iron ore with the help of one to three meter high shaft or draft furnaces. For the construction either termite mounds were used, which were suitably hollowed out, or the furnace was made of clay. Several ceramic nozzles installed at the lower end of the furnace ensured a sufficient supply of air, which was sucked up through the ore and coal filling due to the chimney effect of the high shaft. Ore and coal were refilled several times through the upper chimney opening, until after about 20 hours a football-sized rag was created, which was removed from below through the broken furnace breast. The very pure iron ore required for these furnaces came from Banjéli in Bassariland , among others .
construction

Components from left to right: Bunker, winch house, furnace gas lines with dust bag behind the inclined elevator for charging, blast furnace, tapping hall, wind heater
In order to ensure smooth continuous operation during the so-called " furnace journey " of 10 to 20 years until the next due maintenance date, a blast furnace system requires other essential facilities in addition to the blast furnace itself. This includes the bunker for the input materials with a connected transport system for continuous loading of the blast furnace, with which the input materials are filled into the furnace via the top hatch . A hot blast ring main which is in the hot blast stove preheated air through nozzles in the furnace is blown, the refractory lining on the inside and outside of a complex cooling system is surrounded. Connected to the blast furnace is a specially developed tapping or casting hall , in which the removed pig iron can be fed into corresponding ladle or torpedo wagons during the regular tapping and transported away for further processing.
The construction of a modern blast furnace plant is an extensive, large-scale metallurgical plant project and takes between 1.5 and 2.5 years from planning to commissioning, of which the planning work takes up about half the time. The investment costs for the construction of the new "Blast Furnace 8" in Duisburg-Hamborn, for example, amounted to around 250 million euros.
bunker
The input materials such as iron ores, coke and aggregates (e.g. lime , sand and dolomite ), which are usually delivered by rail or ship, are first brought to a bunker. This consists of several bunkers , which are either bricked or cast from reinforced concrete and in which the incoming raw materials are stored. In order to compensate for the differences in quality in the composition of Möller (iron ore, aggregates) and coke, the materials are often mixed beforehand on so-called mixed beds.
Some raw materials are already being prepared by the suppliers (including mines ). In some cases, upstream preparation, for example in an ore crushing, sintering and pelletizing plant, must ensure processing, since the particle or grain size of the raw materials must neither be too small (risk of clogging, poor gas flow) nor too large (not optimal raw material utilization).
feed
From the bunker system, Möller and coke are transported to the upper end of the shaft, the so-called gout . The supply of the material is also referred to as loading or charging and, depending on the space available, takes place either via conveyor belts , dump buckets or small bulk wagons , so-called lorries or hunte (also dogs ).
In the case of wagon loading or “skip loading”, loading takes place via an inclined elevator up to the filling opening called the “Gichtschleuse”, which forms the upper end of the blast furnace. Two elevator systems are in use for each blast furnace, which alternately transport coke and Möller. In addition to the greater supply capacity, the use of two elevators also serves to protect against failures in order to ensure the uninterrupted supply of the blast furnace. In modern blast furnaces, conveyor belts are now preferred for charging. Although these can only overcome slight gradients and require more space, they are more efficient, easier to automate and handle the bulk material more gently.
Gout obstruction
The furnace gas exiting at the furnace head consists largely of hot nitrogen (N 2 ), carbon monoxide (CO) and carbon dioxide (CO 2 ) as well as small proportions of other gases and entrained dust (see also under blast furnace products ) . Despite the dangerousness of this toxic and flammable gas mixture, the gout opening remained unlocked for a long time. It was only since the development of the blast furnace gas-heated blast furnace in the 19th century that it was provided with a lock system, which made it possible to charge the blast furnace without losing the fuel and heating gas that has now become valuable. The furnace gas is intercepted via large pipes, freed from the dust and then fed to the burners of the boiler, among other things .
The first gout seal with a simple funnel lock was invented by George Parry in Ebbw Vale in 1850 , which later became known as the "Parry funnel". The most widespread form of the top hatch sluice until the 1970s, however, was the "double bell lock" with a rotating funnel developed by McKee and interposed to distribute the bulk material. However, systems with three or four bells were also used to reduce the dump height, which can endanger the defined diameter of the ore pellets , and, in the case of blast furnaces with higher back pressure, the furnace. The great weight of this construction and the increasing problems in maintaining the tightness of the bell system ultimately put a limit on efforts to increase the performance of blast furnaces with bell locks.
The invention of the Luxembourg company Paul Wurth SA, namely Édouard Legille , who in 1970/1971 developed the so-called "bell-less gout seal" (later also "Paul Wurth gout seal") brought about a significant improvement in gout closure . Instead of a complex and heavy bell system, depending on the size and requirements of the blast furnace, there are now two or more storage tanks for coke and Möller on the furnace head, which are filled with bulk cars via belt distributors or elevator systems. Coke and Möller pass through downpipes in the middle of the furnace closure to a rotatable and swiveling chute , which can distribute the incoming material precisely and evenly on the pouring surface. The system is sealed by sealing flaps that are located above and below the storage containers. An additional material flap under the containers ensures a constant discharge speed of the bulk material. The construction height of the new “bell-less gout seal” was reduced by around 1/3, which also reduced the weight of the construction accordingly, and the tightness of the system was easier to ensure.
On January 9, 1972, the world's first bellless top hatch was put into operation on blast furnace 4 of the August Thyssen ironworks in Hamborn . Due to the many advantages compared to the old system, the bellless Paul Wurth gout stopper has successfully established itself and is preferred for use in modern blast furnace systems.
Blast furnace
design
The furnace itself resembles a shaft furnace principle, a fireplace or chimney , as these form the basis of the resulting chimney effect facilitates optimal gassing of the feed. The height of the blast furnace core determines its performance and can be between 30 and 75 m. The upper 3/5 form the actual shaft, which corresponds to an elongated truncated cone. This is followed by a short cylindrical intermediate ring with the largest inside diameter on the blast furnace, which is known as the "coal sack". Another upside-down truncated cone, the so-called "Rast", finally ends in the lower, cylindrically designed "frame". Coal sack and Rast as well as frame each make up 1/5 of the total height. With a total height of 30 m, the shaft is about 18 m, the coal sack and Rast about 6 m and the frame also 6 m.
The entire blast furnace construction is typically surrounded by a steel frame with work and assembly platforms, which on the one hand serves to accommodate the auxiliary equipment such as the material elevator and, if necessary, the top hatch, but can also be used to support and stabilize the blast furnace. A distinction can be made between two types of support structure:
Older and predominantly American blast furnaces are fitted with a support ring with support columns at about the level of the rest, via which the load lying on the blast furnace is guided from the furnace head and top hatch into the foundation. Due to the support columns, however, there is a constriction and thus an obstruction of the access to the tapping area as well as problems in the connection area between the latch and the support ring. Because of these disadvantages, the second variant is now preferred for newer blast furnaces.
This design, developed in Germany, is a so-called "free-standing blast furnace". The steel armouring of the blast furnace creates a self-supporting furnace structure, which is surrounded by complete scaffolding for work platforms and to accommodate the auxiliary equipment. This means that there are no annoying pillars in the tapping area and the blast furnace can freely follow all thermal expansions that a compensator attached to the furnace head absorbs.
The total height of such a system is about 90 m. Blast furnace 2 in Duisburg-Schwelgern, for example, has a furnace height of almost 75 m, a frame diameter of 14.9 m and a usable volume of around 4800 m³, melts around 12,000 t of pig iron per day and is currently (as of 2014) the largest blast furnace in Europe. Twelve blast furnaces in the world exceed 5,500 m³ usable volume (as of 2013). The largest known blast furnace in the world to date with a usable volume of 6,000 m³ is located in the " Gwangyang Steel Works" of POSCO in the South Korean province of Jeollanam-do.
At the lower end of the detent there is the tapping opening for the pig iron, closed with a ceramic plug, through which the resulting metallurgical products pig iron and slag can be drained. For complete emptying ("Sauabstich") when relining the blast furnace is imminent, a "Sauloch" (also oven sow ) is attached at the lowest point of the frame and in its bottom .
The nozzles of the hot wind ring line start at the boundary between the rest and the frame and are supplied by hot air heaters.
![]() |
||||
Region and period | Frame Ø d in m |
Height H in m |
Usable volume in m³ |
Output in tons per day |
---|---|---|---|---|
1) Blast furnace 1861 | 0.9 | 15.3 | 64 | 25th |
2) West German special pig iron blast furnaces from the 1930s | 4.5 | 20.0 | 425 | 450 |
3) West German steel and Thomas pig iron blast furnaces 1961 | 6.5 | 24.0 | 900 | 1,200 |
4) West German blast furnaces 1959 | 9.0 | 26.1 | 1,424 | > 2,000 |
5) Soviet blast furnaces 1960 | 9.8 | 29.4 | 1,763 | 4,000 |
6) Japanese blast furnaces 1968 | 11.2 | 31.5 | 2,255 | 6,000 |
7) West German large blast furnaces 1971/72 | 14.0 | 36.7 | 4,100 | ≈ 10,000 |
Brick lining
Originally, blast furnaces consisted of a meter thick, load-bearing and heat-insulating masonry made of bricks or rubble stones (smoke walls) and had a refractory lining on the inside (core walls ) . In modern blast furnaces, centimeter-thick steel armor and supporting structure take on the load, while the core masonry alone provides the necessary fire resistance and thermal insulation.
In order to achieve the desired service life (furnace travel) until the complete renewal of the furnace lining is due, the entire furnace core from the shaft to the frame is refractory . The furnace lining also defines the final internal profile of the furnace. With a total area of around 2000 m² and a thickness of a few decimetres to over a meter, oversized brickwork can cause enormous costs, which is why, even during the planning phase, efforts are made to only use stones that are specially tailored to the requirements of the respective furnace section.
In the upper shaft area the temperatures are relatively low, the mechanical stresses are high due to the impacting load. Accordingly, chamottes with a corundum content between 30 and 40% are used here. In addition, "impact armor" made of steel plates are attached in the entry area of the loading area, which are intended to prevent damage to the brickwork from the impact of the mortar materials.
In the lower shaft area up to the coal sack, the temperatures increase rapidly. The wear and tear caused by abrasion only sinks slowly, however, as the charge should remain firm for as long as possible and withstand the pressure of the Möll column in order to enable good gas flow. In addition, the stones in this area must be chemically stable, as the reactivity of the surrounding substances increases. Accordingly, highly refractory chamottes with a corundum content between 60 and 86% or semi-graphite bricks are used here.
At the level of the tuyeres and the catch area lining the highest temperatures and pressures is exposed, which only carbon bricks , Schmelzspinellsteine with chromium or Chromkorundsteine withstand.
cooling
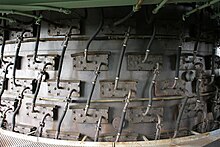
To protect against overheating, the blast furnace contains a system of cooling water lines and elements (staves) that are connected to the armor from about the upper third of the shaft to the base of the frame . Since a blast furnace with a frame diameter of 8 m has a water turnover of more than 30,000 m³ per day, which corresponds to the consumption of a medium-sized town with around 200,000 inhabitants, the cooling system must be designed accordingly and secured several times to protect against failures.
In modern blast furnaces of the 20th century, the previously widespread, open cooling circuits are mostly only used for the furnace head and rack irrigation and in emergencies (e.g. if a closed circuit fails). In open circuits, the required water is taken from the nearby bodies of water (rivers, lakes) and cleaned of solids before being used in the cooling system. After use, cooling towers take over the re-cooling of the water before it is returned to the environment. Closed cycles, on the other hand, use treated, desalinated and degassed water, which is cooled again after use via a heat exchanger and then fed back into the cooling system. In addition to protecting the cooling elements and lines from deposits, treated water has the advantage that the cooling system can absorb larger amounts of heat.
The design of the cooling elements is designed in such a way that on the one hand they can support the brickwork, but on the other hand they can also be quickly replaced if damaged. They consist either of sheet steel, cast iron or copper and are either screwed, wedged or welded to the armor. When it comes to the design of the cooling elements, a distinction can be made between two basic types:
- Cooling boxes are flat, rectangular elements with guide plates drawn in like a labyrinth to direct the water flow and a profile that tapers towards the middle of the furnace, which enables quick removal and installation. The cooling boxes are pushed between the armor plates of the shaft, so that a checkerboard-like pattern of armor plates and cooling boxes is created.
- Plate coolers or staves are made of special cast with cast-in, vertical cooling tubes. They are screwed to the side of the armor facing away from the furnace center. The support surface of the staves is criss-crossed with grooves that are filled with insulating compound.
Different types of cooling are used on the blast furnace, depending on the cooling capacity requirements. The furnace head is cooled in the area of the impact armor with an external sprinkler system. Mostly cooling boxes are installed in the area of the shaft and cooling boxes and plate coolers are used in the area of Kohlsack and Rast. Due to the particularly high heat load in this area, the cooling elements are placed at close intervals so that as much heat as possible can be dissipated. The blow molds have their own double cooling circuit. The frame and base are either cooled with trickle water or by introducing water into a double frame casing.
Hot blast stove
James Beaumont Neilson was one of the first to blast stoves in recuperative design - the air required by the heat exchanger heated - developed and patented left. Previously, blast furnaces were always operated with cold air, as the metallurgy industry had long since experienced that a blast furnace ran better in winter than in summer. Therefore, Neilsen initially encountered great resistance when attempting to use the new principle. The workers were also not yet convinced by an attempt by the Clyde Iron Works permitted in 1828 with a blower wind, which was only heated to 27 ° C and still ensured that the slag produced was less iron and significantly more fluid. Neilson's quite simply constructed boiler consisted of a piece of vault-shaped bent supply line, which was heated over a grate fire. A sheet metal box mounted over the pipe vault held the heat in for a while to improve heat transfer. Further structural improvements through the use of more heat-resistant cast iron pipes and boxes as well as elongated and curved heating coils to absorb the thermal expansion enabled these "tube wind heaters" to heat the fan up to 315 ° C.
year | Wind system | Fuel consumption in kg per t of pig iron |
Amount of pig iron in 24 hours in kg |
1829 | Cold wind | Coke 8060 | 1607 |
1830 | Hot wind | Coke 5160 | 2353 |
1833 | Hot wind | Raw coal 2280 | 3556 |
The resistance to the use of hot blast subsided completely as the pig iron profits achieved increased more and more and at the same time the required amount of fuel could be reduced considerably. Even raw coal could now be used, which was previously impossible.
Since the middle of the 18th century, blast furnace gas has also been used in metallurgy, but initially only for roasting ore, drying casting molds and burning lime and bricks. It was only Wilhelm von Faber du Faur who succeeded in developing an effective and stable tubular wind heater in early 1832, the "Wasseralfinger Winderhitzer", which was heated with furnace gas and raised the wind temperature to 540 ° C. However, this also reached the performance limit of this design.
Edward Alfred Cowper (1819–1893) was able to record a decisive improvement in the supply of blast furnaces with hot blast by no longer constructing the blast heater from a system of tubes, but with refractory, air-permeable multi-perforated bricks . Even in the first stage of development, the "Cowper wind heaters" brought 29 m³ of air to a temperature of 650 to 700 ° C within one minute. At that time, the wind temperature could only be measured with melt samples of different metals. The previously used samples made of lead ( SP = 327.4 ° C) and zinc (SP = 419.5 ° C) could no longer be used with Cowper's wind heaters and even antimony (SP = 630.6 ° C) melted within seconds . Another innovation, also developed by Cowper, was the regenerative alternating operation of two heaters, in which one was heated by furnace gas firing, while the other gave off the stored heat to the cold air that was blown in.
More modern "Cowper wind heaters" consist of a vertical steel pipe 20 to 35 m high and 6 to 9 m in diameter. Inside, there is a layer of heat-insulating bricks and then a layer of fireproof chamotte bricks. The core consists entirely of stacked multi-hole silica bricks . On one side of the shaft, a fireproof lined burning shaft is divided up to the level of the dome, which takes up about a third of the cross-section of the heater. The burner nozzles and the connections for cold air and hot air are located on the lower combustion shaft. Another possibility is the construction of a combustion shaft that is located on the outside independent of the heater shaft. This design has the advantage that, on the one hand, cracks that occur in the dividing wall between the combustion and heating shafts due to the strong temperature fluctuations are avoided and, on the other hand, the heater itself has more space for multi-perforated bricks and thus the heating output can be increased again.
Usually three, and in the case of larger blast furnaces, four “cowpers” ensure a smooth and trouble-free supply of hot air to the blast furnace. While two are heated at different times, an axial or radial fan pushes cold air (around 1.4 t per ton of pig iron) through the third heater at a pressure of 2 to 4.5 bar. The previously used steam or gas piston blowers proved to be uneconomical and difficult to control. In a continuous cycle, there is then a change to the previously heated cowper, while the cooled cowper is heated up again. The heating phase takes about 50 minutes, the wind phase, however, only about 30 minutes, as the wind heater must not fall below a temperature of 721 ° C, which is critical for silica stones. Below this temperature, silica bricks undergo several changes of modification , which leads to a “jump in volume” that destroys the solid structure of the multi-perforated brick trim and can cause it to collapse. The third or fourth “cowper” also serves as a reserve against failures and during maintenance work.
Hot wind ring line and nozzles


With a maximum achievable temperature of 1270 ° C (1980) to 1350 ° C (1985), the hot blast arrives via the "hot blast ring line" to the between 10 and 40 nozzles, depending on the size of the blast furnace, and via the so-called blow molds into the furnace. To reduce the consumption of coke, substitute reducing agents such as animal fat or heavy fuel oil are blown into the molds in many plants. However, since the price of oil continued to rise over time, there were various attempts with other substitutes.
At Armco in the USA , coal dust was successfully used as a fuel substitute for long periods and in Chinese companies from 1963 onwards. Since 2006, finely pelletized old plastics (6 mm × 9 mm) have also been added, which in addition to the environmentally friendly recycling of plastic waste , in contrast to landfill, also reduce the emission of CO 2 and SO 2 .
To protect against damage caused by the heat load, the ring main and the supply connection are given a fireproof lining, which also has a heat-insulating effect in order to avoid heat loss. The blow molds themselves are intensively cooled with water, as they can protrude up to half a meter into the furnace, depending on the degree of wear and tear of the furnace lining, and are then exposed to the highest stresses due to the temperature and pressure of the Möll column. In modern blast furnaces, therefore, only hollow forms made of electrolytic copper with a double-chamber cooling water circuit are used. If the front chamber burns down during the furnace cycle, the corresponding cooling circuit can be switched off and the main chamber can be continued until the next standstill.
Pig iron and slag tapping

The pig iron - racking at regular intervals of about two to three hours. Here, the ceramic plug at the tap hole is with a compressed air - drill drilled. In rare cases, for example if the drill fails, the opening is also pierced with an oxygen lance.
The pig iron then flows for around 15 to 20 minutes in a specially developed tapping or casting hall with a working platform and a fireproof brick channel system that is additionally stamped or poured with refractory compounds. In older blast furnaces with higher slag production, part of the slag was first tapped off as so-called "pre- slag " at the level of the mold platform. Then the pig iron and slag were tapped together using a kind of siphon, the so-called " fox ", which separated the slag from the pig iron (like decanting ) and diverted it in different directions via a correspondingly designed channel system. Modern blast furnaces with lower slag production, but a daily pig iron output of 3000 tons and more, do not need any preliminary tapping of the slag, but between two and four tap holes. The system of gutters and foxes is correspondingly complex and requires careful monitoring.
In the main channel between the taphole and the fox, which is around 8 to 14 meters long and holds around 20 to 60 tons of pig iron including slag, the slag has time to separate from the pig iron and collect on the surface. In front of the fox, whose “nose” dips into the melt, the slag builds up and is drained off via channels branching off to the side. The pig iron, on the other hand, flows under the fox through to a hole under which a ladle or torpedo wagon is ready to transport the captured iron to the steel or casting works for further processing . The slag is also collected in special wagons and transported away for further processing.
After completion of the tapping phase, the tap hole is closed again with the help of a "tap hole tamping machine" until the next tap.
Modern casting halls have to be "dusted off" to protect employees and the environment, which means that suction systems are installed in the area of the tap holes and at the transfer point to the collecting containers and the channel system is covered with steel plates. The captured exhaust gases are cleaned in appropriate filter systems.
function
Blow on
Before a new blast furnace can go into production, it must first be slowly dried with the help of gas burners or by blowing in hot air. Only then does the actual “blowing” into the furnace take place. The choice of the blowing method has a major impact on its subsequent mode of operation and its service life, can vary from plant to plant and takes about one to two weeks (with older blast furnaces sometimes even several months).
After drying, the frame is filled with wood and coke for the first time. In the shaft above, layers of coke and the moler consisting of iron ore and slag-binding aggregates are poured in, ignited and fanned by blowing in hot air. The composition of the blown stratification differs greatly from the later operational stratification. It contains considerably more coke, as warming up the furnace lining and the cold coke-Möller column consumes a lot of energy. The use of a correspondingly high amount of slag ensures that the frame is warmed up and protected.
Structure and behavior of the loading during the furnace passage
The shape, composition and mechanical properties of the charge, especially of the ores, as well as a grain size that is as uniform as possible are of decisive importance for the efficiency of a blast furnace . The reduction behavior at elevated temperature also plays a role, with the aim being as low a low temperature breakdown as possible and a high softening temperature with a simultaneously low temperature range of the softening phase. Only if sinter and pellets remain in pieces and in a solid state for as long as possible can they withstand the pressure load of the layers above and ensure good gas penetration.
The reducibility of the sinter depends on its composition and is determined by the empirical size of the basicity
which shows the mass ratio of calcium oxide and magnesium oxide to silicon dioxide . The reducibility is better when the basicity of the composition is in the basic range (B> 1.0), and reaches a maximum reducibility in the range from 2.0 to 2.5. The mechanical strength is also greatest in this area. From a basicity of 2.6 and higher, the proportion of the melt phase in the sintered portion increases, which closes the pores and reduces the ability to reduce, since the reducing gases no longer reach the ore portion directly. In the case of acidic sintering (B <1.0), the softening phase begins in some cases when only about 15% of the ore has been reduced.
In contrast to sinter, pellets tend to have an acidic composition, because their stable spherical shape means that there is less tendency towards fine grain formation and deterioration in mechanical properties. Pellets therefore mainly consist of hematite , various silicates to bind slag and pores. The proportion of hematite must, however, remain limited, since otherwise the structure of the pellets would loosen up too much in the course of the reduction and the pellets would eventually disintegrate into concentrated dust, which would result in a considerable loss of compressive strength. The simultaneous excessive increase in the pellet volume (thresholds) also harbors the risk of blast furnace clogging .
To find out how the structure and condition of the loading change on the way from the furnace to the tap opening and what reactions take place in the respective furnace section, several tests were carried out in the 1970s, especially in Japan, in which blast furnaces were stopped in the middle of production and cooled it down intensely with water. All ongoing reactions within the Möllersäule were thus “frozen”. The subsequent analyzes of the layering composition on various levels showed that the softening and melting zone bulges upwards in the shape of a bell on the central axis. The center of the bell consists of coke, which is still gas-permeable in the 1000 to 1600 ° C hot zone. The melting ores and slag reach the inside via this active coke bell and sink into the rest and the frame, while the hot blast that is blown in is distributed evenly outwards and upwards. The so-called “dead man” assumed so far - a resting and unresponsive, conical body made of coke and solidified iron - does not exist.
Only the foot of this "cohesive zone" is impermeable to gas and is ideally at the level of the rest. It should also not be affected by the gassing, so that, on the one hand, the delivery (refractory lining) of the coal sack and rest are less affected and, on the other hand, the resulting turbulence of the hot wind would make a uniform reduction of the loading difficult or even prevent it. In order to optimize the gas flow in the form described and thus reduce energy consumption while simultaneously increasing the quality of the pig iron, careful calculation of the zone cross-sections as well as the amount and composition of the hot blast introduced is of great importance.
The following additional findings were obtained from the investigation on "frozen" blast furnaces:
- The alternating charging of Möller and Coke is maintained throughout the furnace run down to the deeper layers. Only the layer thicknesses decrease in the course of the reduction.
- At the level of the blowing plane, instead of the solid ores, there are only drops of metallic iron and coke mixed with slag.
- The reduction begins 3 to 4 meters below the loading level, with the result that the grain size of sinter, pellets and lump ore decreases evenly. The sinter decomposes at a temperature of 200 to 500 ° C, whereas that of lump ore only occurs at around 800 to 900 ° C.
- 7 meters below the surface, the reduction has progressed so far that the sinter portion does not break down any further. However, this does not apply to the other Möllerstoff, since up to a depth of 18 meters an ever increasing proportion of fine grain below 5 millimeters was found. Whether and where fine grain is formed in the blast furnace depends, however, on the temperature and gas flow distribution, on the heating rate and on the type of charge. In the case of sintering, the proportion of fine grain is generally higher.
- The reduction is much faster in the middle of the furnace cross-section than in the edge area.
- At the height of the gout, the firmness of all substances in the oil initially decreases sharply and increases again as the depth increases, which is related to the progress of the reduction and the associated increase in the iron content.
Reduction pest sulfur
The alkalis and sulfur compounds always present in the feed have a major influence on the reduction processes . The sulfur compounds, in particular, have a particularly detrimental effect on the reduction processes taking place, since they can never be completely driven out despite the complex pretreatment of ore and coke. Even small amounts of sulfur dioxide (SO 2 ) of around 5 to 50 ppm in the reducing gas initially accelerate the breakdown of oxygen considerably; However, as soon as the first metallic iron appears, the process is reversed and the decomposition of oxygen is greatly slowed down. The cause of this reaction is the property of sulfur to combine with the metallic iron on the surface and thereby prevent the absorption of carbon.
The reaction of the wustite (iron (II) oxide, FeO) with carbon monoxide (CO) usually takes place not only over the surface of the FeO, but also over the surface of the iron that has already precipitated out. Due to the better absorption behavior of iron, a large part of the gas transport to and from the iron-iron oxide phase boundary takes place via the same . However, this only happens when the iron has been able to absorb (carburize) sufficient carbon. If the absorption of the carbon is blocked by the sulfur, the reduction can only take place on the surface of the iron oxide.
Sulfur as a reduction pest is also the cause of the excessive swelling of the pellets as described above. Since the iron can only crystallize out in the direction of the degrading iron oxide, the iron crystals develop in an elongated, fibrous manner. The pellet structure, which has already been loosened due to the first reduction stage, strengthens again and the pellet volume can grow to two to three times its original volume.
In order to keep the proportion of sulfur compounds as low as possible, sulphidic ores are converted into oxides by careful roasting and sulfur-binding additives are introduced.
Chemical reactions during the reduction
In the blast furnace, various metallurgical processes sometimes take place at the same time, in which, on the one hand, the iron ore is reduced to pig iron over several stages and the non-reducible components are transferred to the slag.
In order to initiate a reduction in iron ores in the first place, however, the necessary reducing gases must first be generated. This takes place in the lower area of the blast furnace when the carbon contained in the coke is burned with oxygen .
The reaction is strongly exothermic , which means that heat is released, which is 394.4 kJ / mol in this reaction and the blast furnace in the area of the hot blast ring nozzles to a temperature of 1800 to 2000 ° C, even if additional oxygen is used heated to 2200 ° C. However, two immediately following endothermic , i.e. heat-consuming reactions lower the temperature again to around 1600 to 1800 ° C.
The so-called " Boudouard reaction " , which however requires a minimum temperature of 1000 ° C, requires 172.45 kJ / mol.
A simultaneous splitting of the steam in the hot gas requires another 131.4 kJ / mol.
The two reducible gases carbon monoxide and hydrogen rise against the flow of material in the blast furnace. Due to this property - sinking Möller coke column on the one hand and rising reaction gases flowing counter to the moving bulk material on the other - the blast furnace is also referred to as a “countercurrent reactor” and a “moving bed reactor”.
The so-called "indirect reduction" takes place in the temperature zone between 400 and 900 ° C. The various iron oxides react with carbon monoxide or hydrogen in three stages, until finally metallic iron is present:
Reaction with carbon monoxide (CO) | Reaction with hydrogen (H 2 ) |
---|---|
The more ferrous magnetite is formed from hematite . | |
Of magnetite produced wustite . | |
Metallic iron is made from wüstite and accumulates in the blast furnace below. |
As long as the resulting carbon dioxide (CO 2 ) remains in the temperature range of over 1000 ° C, it is repeatedly regenerated to carbon monoxide (CO) by the Boudouard reaction and is available again for the reduction process. The reduction by hydrogen is particularly effective at around 800 ° C. A content of only 10% hydrogen in the reaction gas triples the reduction rate, but this decreases again with a further increase in temperature. The grain size of the ore must not exceed a certain level, so that the diffusion paths of the hydrogen do not become too large.
In the temperature range from 900 to 1600 ° C, there is also a "direct reduction" with carbon:
The iron companions manganese , silicon and phosphorus are also included in the process and reduced, whereby heat is consumed:
At the same time, the already reduced iron in the carbonization zone at around 1100 to 1200 ° C takes up carbon either directly from the glowing coke or from the carbon monoxide gas.
The uptake of carbon lowers the melting point from 1538 ° C (pure iron ) to around 1300 to 1400 ° C (melting point of the eutectic mixture , the ledeburite , with 4.3% by weight C: 1147 ° C).
Monitoring and regulation of the blast furnace process
In the course of automation and quality assurance to maintain competitiveness on the one hand, and the increased safety requirements for the protection of people and machines on the other, various measuring and control devices are inevitable. The smelting process is naturally subject to greater or lesser fluctuations, as the composition of the burner, coke and hot air, including the additives blown in, also vary within the tolerance limits. The course and speed of the reaction also fluctuate accordingly, which without monitoring and suitable counter-regulation measures would lead to severe disruptions.
Important measured variables are above all:
in the amount of gout |
|
from the shaft to the coal sack |
|
at the level of the hot air supply |
|
on the frame bottom |
|
In addition, horizontal probes are also used to measure the thickness of the Möll layers as well as the pressure and speed of the gas passing through the Möll column. To protect against failures, some measuring devices, such as those for measuring the depth of the loading surface, are redundant.
Disturbances in the blast furnace process
Hanging loading
Due to the disintegration of the Möller and coke during the reduction, the Möller column in the shaft can become compacted and eventually back up. A Möller column "hanging" in this way is initially noticeable in that the depth measurement no longer registers any sinking movement on the loading surface, but the pressure and temperature of the top gas also decrease because it is difficult to get through the increasingly narrow gaps in the compacted Möllers column. The wind pressure, on the other hand, increases as it encounters greater resistance.
Below the hanging zone, however, the reduction and melting process continues unabated until a cavity is formed between the hanging and sinking Möller. Since on the one hand there is the risk that a Möller column suddenly collapsing into the cavity leads to serious process disruptions and damage to the blast furnace and on the other hand pig iron and slag threaten to rise to the blow molds, a reaction to the aforementioned characteristic changes in the measurement results must take place as early as possible . This includes, for example, the so-called "upsetting", a one-time or, if necessary, repeated strong throttling of the amount of wind and thus the counter pressure on the Möll column, which forces it to slide due to its own weight.
Approach formation
The caking of Möller and coke on the inner walls of the blast furnace can have various causes. Over time, the profile of the armor changes due to physical and chemical abrasion , which can result in easier attachment conditions in places. As a result, protruding cooling elements also facilitate the formation of deposits. The composition of the Möller itself also has an influence on the caking process, since, among other things, a basic slag has a correspondingly higher proportion of different alkalis , which act as caking aid, for better sulfur binding. Smaller batches are hardly noticeable at first, but can grow very quickly and lead to disruptions in the blast furnace process; especially if these suddenly break off and then cause irregularities in the composition of the Möllersäule.
Larger approaches can be measured by narrowing the cross-section of the furnace and thus increasing the flow speed of the wind, which entrains more dust particles. In addition to the increased dust emission, the formation of deposits can also promote the aforementioned hang-ups. Furthermore, fluctuations in the furnace cycle and in the quality of the pig iron due to crumbling deposits are the result. Finally, build-up on cooling elements protruding inwards can also cause damage to them.
By means of pressure and temperature sensors in the furnace walls as well as measuring probes that can be pushed horizontally into the Möll column, changes in cross-section and thus approaches can now be localized faster and more precisely. Appropriate changes in bedding can then usually eliminate them. In the past, larger furnaces in particular had to be blown down first and then the approaches either drilled or blasted off.
Water ingress
Ingress of water through damaged cooling elements can lead to considerable disruptions in the blast furnace process, since with larger quantities the evaporating water entails a high loss of thermal energy and the various reduction processes come to a standstill. A water ingress can be measured on the one hand by an increased hydrogen content in the top gas and on the other hand by the increased consumption of feed water , which is supposed to compensate for the water loss in closed cooling circuits.
Sensible subdivision and connection of the cooling elements and lines with one another in horizontal zones or "cooling disks" allows damaged elements to be discovered and replaced more quickly and water losses to be kept low. In open cooling systems, however, a pressure test is necessary on each cooling element.
Shutdown
Different procedures are necessary depending on whether the iron and steel works want to shut down the blast furnace only for a short time (steaming) or completely shut it down and shut it down (blowing out) .
Steaming
If a blast furnace is only to be shut down temporarily, for example in the event of supply bottlenecks or minor repairs, it is dampened . In doing so, the loading is first adjusted depending on the planned duration of the break in operation. It now consists, on the one hand, of a “light” steaming oiler, which means less iron, and on the other hand of a higher number of layers of coke. During the last tap before shutdown, care is taken to ensure that pig iron and slag drain off as completely as possible. If the steaming phase is to take longer, the oven sow is also used. If the furnace is at a standstill, all supply and discharge lines are closed, the hot air nozzles are bricked up and the charging surface is covered with fine ore or slag sand so that the furnace can keep its heat for as long as possible and the natural draft does not lead to unnecessary coke burns. In order to prevent water ingress, which would lead to serious disruptions in the blast furnace process, the cooling system is only switched off after a careful leak test.
The re-inflation after longer damping phases takes place in the reverse order of the individual working steps during steaming, although initially only a few tuyeres of the hot blast system in the tap hole area, then further nozzles are gradually put into operation. If necessary, the needle hole is also set higher for some time.
Blow out
If regular operation is no longer possible, among other things because the lining is so worn that it has to be replaced, the furnace is "blown out".
The blast furnace process initially continues in the lower area, but the feed supply is switched off and the wind supply is greatly reduced in the initial phase and finally also switched off. In the deep-blowing phase (lowering of the coke-Möller column), water vapor is injected through special nozzles at all points where “dead”, i.e. empty spaces are formed. Sometimes water is also added from above. This prevents the formation of explosive gas-air mixtures. Dead spaces arise above all above the loading surface up to the top vent, but also in the spaces between the top gas lock, depending on the position of the shut-off valves on the gas vent between the furnace and dust bag or in the dust bag itself as well as in the vortices and in the furnace valve. Another method of avoiding gas explosions is to burn off the furnace gases escaping from the charging surface with the aid of a continuously burning coke gas ignition lance. The blow-out is completed by tapping the furnace sow , whereby, in addition to slag, depending on the duration of the blast furnace journey and the cooling conditions in the rack, several tons of pig iron can accumulate.
At the end of the kiln journey, the entire refractory brick lining is usually renewed and damaged steel components replaced. Often, such a downtime is also used to replace technically outdated equipment such as measuring and analysis devices with new ones. In addition to improving the quality of the blast furnace products, this also helps to reduce energy consumption and environmental pollution.
It usually takes several months for all damaged or outdated components to be replaced. However, if the remaining components are of good quality, a blast furnace can survive several furnace journeys until it is finally shut down. In March 2008, for example, the "Large Blast Furnace 1" in Duisburg-Schwelgern started its fifth furnace tour.
Blast furnace products
Pig iron
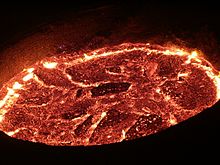

The aim of an optimally adjusted blast furnace process is the production of the highest possible quality pig iron that has as little foreign matter as possible and has not absorbed too much carbon.
According to DIN EN 10001 , pig iron is defined as an alloy made of iron with more than 2% carbon and some other elements with the following maximum proportions: manganese ≤ 30%, silicon ≤ 8%, phosphorus ≤ 3% and chromium ≤ 10%. The proportion of other admixtures should not exceed 10%. For quality assurance purposes, a sample is taken for a chemical analysis with every tap.
In 9 out of 10 blast furnace plants so-called “white pig iron” (also steel pig iron ) is produced, in which the carbon contained is bound in the form of iron carbide or manganese carbide and the fracture surface has a bright, silver-white sheen . White iron is usually directly in liquid form using a closed torpedo cars to nearby steel transported, but may also stockholding either handy ingots or iron granules (grain size ≈ 2-16 mm) are cast. White pig iron is used as a starting material for steel production and is freed from its undesirable accompanying substances and a large part of the carbon in a blow steel mill (“steel boiler”) by blowing in oxygen. These leave the glowing, finished steel either as gases (sulfur dioxide, carbon dioxide) or with the additives as slag (calcium and manganese silicates or phosphates).
The small remainder of the ironworks mostly produces "gray pig iron" (also foundry iron ), in which the carbon crystallizes unbound as graphite and the fracture surface shows a darker matt gray. Gray pig iron is used as a raw material for the production of various types of cast iron, such as gray cast iron with lamellar graphite or spheroidal graphite , malleable cast iron and cast steel . A few companies have also specialized in special types of pig iron such as ferro- manganese (fried iron) or ferrosilicon .
slag
The produced during the blast furnace process slag consisting of about 38-41% calcium oxide (CaO), 7-10% magnesium oxide (MgO), 34-36% silica (SiO 2 ), 10-12% alumina (Al 2 O 3 ), 1, 0–1.5% sulfur (S), 1.0% titanium dioxide (TiO 2 ), 0.16–0.2% iron oxide ( FeO ) and various other oxides and sulphides.
Experienced smelters often see the still liquid slag to see what approximate composition and properties it contains. A simple “hook test”, in which an iron hook is dipped into the slag, is usually sufficient to test the same. If the slag remains hanging on the hook in short, tough drops when it is lifted (short slag) , it is “ basic ” with a weight ratio of CaO: SiO 2 > 1.0. If, on the other hand, the slag runs off the hook in long threads (long slag) , it is "acidic" with a ratio of CaO: SiO 2 <1.0.
While the slag in the blast furnace still had the task of absorbing the gangue of the ores and the ashes of the coke, desulphurising the pig iron and serving as a protective wall in the frame against heat radiation, after tapping, depending on its composition and properties, it becomes a valuable raw material for used for various purposes. In addition to generating blast furnace slag , slag bricks or -bims and slag wool it is also road and railway ballast , breeze blocks , Portland cement and blast furnace cement processed.
Furnace gas

The top gas exiting at the blast furnace head at a temperature of 150 to 200 ° C consists of 22–24% carbon dioxide (CO 2 ), 18–21% carbon monoxide (CO), 52–59% nitrogen (N 2 ), 1–3% hydrogen (H 2 ) as well as from water vapor and traces of methane . In addition to its main use as a fuel supplier for firing the wind heaters, it is also used, among other things, as heating gas in rolling mills , steam boilers , coking chambers and district heating systems, as well as fuel for gas engines .
Due to many measures for better ore and gas utilization while at the same time reducing coke consumption, the total amount of blast furnace gas produced and its calorific value fell over time. Since the 1990s, around 1500 to 2000 m³ of furnace gas with a calorific value between 3150 and 3570 kJ / m³ have been produced per ton of pig iron . By adding coke or natural gas , this value is increased to around 4500 kJ / m³. In addition, there are around 25 kg of blast furnace dust per tonne of pig iron, which corresponds to a dust content in the blast furnace gas of around 20–30 g / m³.
In order to protect the burners, gas engines and turbines operated by the furnace gas from damage by abrasion , but also for reasons of environmental protection , the furnace gas has been dedusted and cleaned since the beginning of the 20th century . Blast furnace gas turbines since the 1970s require z. B. high-purity gas with a dust content of at most 0.5-1 mg / m³.
The cleaning takes place in several stages from dry coarse cleaning with the aid of dust bags and swirlers to wet cleaning in gas scrubbers and disintegrators to fine cleaning with the help of bag or bag filter systems and electrostatic filters . The then usable clean gas still contains a dust content of 0.006 to 0.03 g / m³.
Performance and consumption
Up until 1914, a blast furnace supplied around 300 to 400 tons of pig iron per day and between 1950 and 1960 it was already able to produce 2,500 tons per day.
In the 1970s, the best furnaces in the world produced 60 tons per square meter of rack space and more per day, with an average consumption of coke and oil of around 503 kilograms per ton of pig iron. For medium-sized blast furnaces with a frame diameter of 10 to 11 meters, this corresponds to a daily output of 5000 to 6000 tons.
In 1980 the specific coke consumption of a blast furnace in the Federal Republic of Germany was around 515 kilograms per ton of pig iron. The specific consumption of heating oil was 23 kilograms per ton of pig iron. By 1994, coke consumption fell to around 379 kilograms, while heating oil consumption rose to around 45 kilograms per ton. Since 1985, coal has been increasingly used as a reducing agent instead of processed coke.
Large blast furnaces such as "Blast Furnace 5" of the Rogesa blast furnace on the Dillinger Hütte factory premises with a frame diameter of 12 meters produce around 7,000 tons per day. Larger blast furnaces can produce up to 12,000 tons of pig iron per day.
In 1950 annual global production was around 189 million tons of pig iron, but increased to around 1808 million tons by the end of 2018. ThyssenKrupp Steel's "Blast Furnace 2" in Schwelgern , which was started up at the end of 1993 , had a frame diameter of 14.9 meters and a daily output of more than 10,000 tons of pig iron.
In 2007, large blast furnaces with a frame diameter of around 15 meters produced an average of around 12,000 tons of pig iron per day, which corresponds to an annual production of around 4 million tons. In order to achieve this, around 19,200 tons of iron ore, 4,000 tons of coke, 1,750 tons of injected coal (coal dust to be injected through the hot air nozzles) and 11 million cubic meters of air are required every day. This corresponds to a consumption of around 1,600 kilograms of ore, 330 kilograms of coke, 146 kilograms of injected coal and 917 cubic meters of air per ton of pig iron. The by-products produced 3300 tons of slag and 17 million cubic meters of furnace gas per day. About one ton of coke is used to melt the slag for every 3.2 tons of slag.
See also
Sources and References
literature
- Direct purchase of the blast furnace
- Manfred Rasch (Ed.): The coke oven from 1709 to the present. 2nd Edition. Klartext Verlag , Essen 2015.
- Hans Schoppa: What the blast furnace operator needs to know about his work . 4th edition. Verlag Stahleisen, Düsseldorf 1992, ISBN 3-514-00443-9 .
- Gerhard Winzer, Eberhard Reichenstein: Development of blast furnace technology . Reports held in the Contact Study “Metallurgy of Iron; Part I: Ironmaking ”. In: F. Oeters, R. Steffen (Ed.): Metallurgie . tape 2 . Verlag Stahleisen, Düsseldorf 1982, ISBN 3-514-00260-6 , p. 79-84 .
- H. Dickmann: Development of the blast furnace wind heating up to the invention of EA Cowpers . In: Brohltal AG for stone and clay industry (ed.): Hundred years of Cowper wind heating . Burgbrohl (District Koblenz) 1958.
- MA Pavlov (М. А. Павлов): Design and calculation of blast furnaces . In: Metallurgy of pig iron . 2nd Edition. tape 3 . VEB Verlag Technik, Berlin 1953, DNB 453723004 , license number Dg.-No. 370/39/53 (DDR) - (Russian: Металлургия Чугуна, Часть третья: Доменная печь . Translated by Erich Marquardt).
- Blast furnace process
- K. Grebe: The blast furnace behavior of Möller and coke . Reports held in the Contact Study “Metallurgy of Iron; Part I: Ironmaking ”. In: F. Oeters, R. Steffen (Ed.): Metallurgie . tape 2 . Verlag Stahleisen, Düsseldorf 1982, ISBN 3-514-00260-6 , p. 85-145 .
- MA Pavlov (М. А. Павлов): The blast furnace process . In: Metallurgy of pig iron . 2nd Edition. tape 2 . VEB Verlag Technik, Berlin 1953, DNB 367559374 , license number Dg.-No. 370/40/53 (GDR) - (Russian: Металлургия Чугуна, Часть вторая: Доменный Процесс . Translated by Rudolf Rickert, Walter Philipp, Alexander Junge, Heinz Frahn).
- Association of German Ironworkers (Ed.): The blast furnace process - The kinetic-dynamic simulation model . Report on a joint work with contributions from the lecture conference "Mathematical Models of the Blast Furnace Process" on December 2nd and 3rd, 1971 in Düsseldorf. Verlag Stahleisen, Düsseldorf 1973, ISBN 3-514-00124-3 .
- Richard Troska: The furnace dimensions based on the furnace process. Weimar 1867 ( available online in Google Book Search; last accessed on May 27, 2012)
- General
- Jürgen Ruge, Helmut Wohlfahrt: Technology of materials . 8th edition. Springer Verlag, 2007, ISBN 3-8348-0286-7 .
- Karl Taube: Steel production compact: Basics of iron and steel metallurgy . Vieweg Technik, Braunschweig / Wiesbaden 1998, ISBN 3-528-03863-2 , p. 60–159: blast furnace .
- Part I: Iron making . Reports held in the Contact Study “Metallurgy of Iron”. In: F. Oeters, R. Steffen (Ed.): Metallurgie . tape 2 . Verlag Stahleisen, Düsseldorf 1982, ISBN 3-514-00260-6 .
- Association of German ironworkers (ed.): Common representation of the ironworking industry . 17th edition. Verlag Stahleisen, Düsseldorf 1970.
- Fritz Toussaint: The way of the iron . 6th edition. Verlag Stahleisen, Düsseldorf 1969.
- Otto Johannsen (on behalf of the Association of German Ironworkers): History of the iron . 3. Edition. Verlag Stahleisen, Düsseldorf 1953.
- Robert Durrer : Basics of iron extraction . Francke Verlag, Bern 1947, p. 56-58 .
- Johann Christian zu Solms-Baruth, Johann Heinrich Gottlob von Justi: Treatise of the iron hammers and high furnaces in Germany. Rüdiger, Berlin / Stettin / Leipzig 1764. (E-Book: Becker, Potsdam 2010, ISBN 978-3-941919-73-0 )
- AF Holleman , E. Wiberg , N. Wiberg : Textbook of Inorganic Chemistry . 102nd edition. Walter de Gruyter, Berlin 2007, ISBN 978-3-11-017770-1 .
- Peter Atkins : Physical Chemistry . 2nd Edition. Wiley-VCH, Weinheim 1996, ISBN 3-527-31546-2 .
Web links
- Pictures of all processes in iron and steel production and further processing
- From iron ore to pig iron: the blast furnace structure
- Radwerk IV blast furnace museum in Vordernberg
- Jun-Ichi Kokado: The technical development of the Japanese steel industry ( Memento from January 17, 2008 in the Internet Archive )
Individual evidence
- ↑ Hohofen . In: Heinrich August Pierer , Julius Löbe (Hrsg.): Universal Lexicon of the Present and the Past . 4th edition. tape 8 . Altenburg 1859, p. 472 ( zeno.org ).
- ↑ a b Johannsen: History of Iron , pp. 9–11.
- ↑ Matthias Zwissler, Roman Landes: Investigations into racing fire products , racing fire symposium of the IGDF International Society for Damascus Steel Research eV in Polle, August 20, 2005 ( investigations into racing fire products PDF; 3.54 MB).
- ^ Johannsen: History of Iron , p. 11, 121.
- ↑ Johannsen: History of Iron , pp. 121-122.
- ↑ Albrecht Jockenhövel: The way to the blast furnace - The time of the medieval and early modern mass huts. In: Eisenland, on the roots of the Nassau iron industry. Ed. Association for Nassau Antiquity and Historical Research e. V., Taunusstein 1995, ISBN 3-922027-88-1 , pp. 83-98.
- ↑ a b c Durrer: Fundamentals of iron production , pp. 56–58.
- ↑ Johannsen: History of Iron , p. 133.
- ^ Meyers Konversationslexikon - Blauofen
- ↑ General description of the iron and steel industry , p. 7.
- ^ Ludwig Beck : Contributions to the history of the iron industry in Nassau. In: Nassau Annals. Volume 33 (1902/03), p. 212.
- ↑ Michael Gechter: Mining archeology in the Bergisches Land. In: gv-roesrath.de. History Association Rösrath eV, accessed on April 18, 2019 .
- ↑ Aufbruch ins revier , Hoesch 1871–1961, page 34
- ↑ Aufbruch ins revier , Hoesch 1871–1961, page 43
- ↑ Johannsen: History of Iron , p. 296.
- ↑ a b Common description of the iron and steel industry , pp. 8–9.
- ↑ Harald Pöcher: Wars and battles in Japan, which made history: from the beginnings to 1853. LIT Verlag, Münster 2009, p. 34 restricted preview in the Google book search
- ↑ Johannsen: History of Iron , pp. 22-23.
- ↑ Johannsen: History of Iron , p. 35.
- ↑ Peter Dahlmann , Gerhard Endemann, Hans Jürgen Kerkhoff, Hans Bodo Lüngen: Ways to increase efficiency in the steel industry , Steel Institute VDEh. Wirtschaftsvereinigung Stahl, September 2010 ( Ways to increase efficiency in the steel industry PDF 1.7 MB, p. 6 ( Memento from December 17, 2015 in the Internet Archive ))
- ^ A b Construction of blast furnace 8 in Duisburg-Hamborn of ThyssenKrupp Steel AG
- ↑ Schoppa: Was der Hochöfner… , pp. 52–53.
- ^ Taube: Steel production compact , p. 92.
- ↑ Johannsen: Geschichte des Eisens , pp. 371–372.
- ↑ a b Roger Kneip: FROM THE HISTORY OF THE STEEL INDUSTRY - Over 25 years of bell-less gout stop
- ↑ Schoppa: Was der Hochöfner… , pp. 55–56.
- ↑ General description of the iron and steel industry , p. 59.
- ↑ Schoppa: Was der Hochöfner… , pp. 38–39.
- ↑ Taube: Steel production compact , pp. 62–63.
- ↑ a b Ten years of blast furnace Schwelgern 2 and 38 million tons of pig iron ( memorial from November 29, 2011 in the Internet Archive )
- ↑ ThyssenKrupp: First furnace tour ended after 21 years: Europe's largest blast furnace is being modernized. Press release of May 16, 2014.
- ^ Vaclav Smil: Still the Iron Age. Iron and Steel in the Modern World. , Butterworth-Heinemann (Elsevier), Oxford Cambridge 2016, page 90. ISBN 978-0-12-804233-5 . Excerpt , accessed on September 29, 2016.
- ^ Three of top 10 world melting pots owned by Korea's POSCO. In: Arirang News. August 24, 2013, with video (0:37 min.)
- ↑ Flat steel - frame delivery in blast furnace B completed without accidents ( memento from September 19, 2015 in the Internet Archive )
- ↑ General description of the iron and steel industry , p. 101.
- ↑ a b stahl-online.de - Pig iron and steel production ( Memento from January 15, 2012 in the Internet Archive ) (According to pig iron and steel production ( Memento from February 10, 2011 in the Internet Archive ), values have been unchanged since October 2007 Website)
- ↑ a b Common description of the iron and steel industry , p. 61.
- ↑ HW Gudenau, H. Kainer, G. Pitzko, M. Scheiwe: Thermal-mechanical behavior of blast furnace frame linings. In: Steel and Iron. 111 (1991) 9, pp. 71-81, 188.
- ↑ Schoppa: Was der Hochöfner… , pp. 43–44.
- ↑ Taube: Steel production compact , pp. 71–73.
- ↑ Taube: Steel production compact , pp. 84–85.
- ↑ Dickmann: Development of the blast furnace wind heating ... , p. 1.
- ↑ Johannsen: History of Iron , p. 325.
- ↑ Johannsen: History of Iron , p. 327.
- ↑ Dickmann: Development of the blast furnace wind heating ... , p. 4.
- ↑ Dickmann: Development of the blast furnace wind heating ... , p. 6.
- ↑ Dickmann: Development of the blast furnace wind heating ... , p. 9.
- ↑ Schoppa: Was der Hochöfner ... , p. 58.
- ^ Taube: Compact steel production , p. 47.
- ^ Taube: Steel production compact , p. 46.
- ^ Taube: Steel production compact , p. 59.
- ↑ a b Winzer, Reichenstein: Development of blast furnace technology , pp. 80–81.
- ↑ Innovation report: Blast furnace: plastic pellets instead of coke and heavy oil
- ↑ By using old plastics, voestalpine reduces CO 2 emissions in Linz by more than 400,000 tons per year. (PDF 32 kB) In: voestalpine.com. voestalpine AG, June 16, 2007, accessed on July 17, 2019 .
- ↑ a b Ruge, Wohlfahrt: Technologie der Werkstoffe , p. 195.
- ↑ Schoppa: Was der Hochöfner ... , p. 49.
- ^ A b Taube: Compact steel production , pp. 152–154.
- ↑ Schoppa: Was der Hochöfner ... , p. 51.
- ↑ a b c d Schoppa: Was der Hochöfner… , pp. 85–88.
- ^ Toussaint: Der Weg des Eisens , p. 65.
- ^ Grebe: The blast furnace behavior of Möller and Koks , pp. 95-101.
- ^ Grebe: The blast furnace behavior of Möller and Koks , pp. 101-109.
- ↑ Winzer, Reichenstein: Development of blast furnace technology , p. 79.
- ↑ Grebe: The blast furnace behavior of Möller and Koks , pp. 91–92.
- ^ Grebe: The blast furnace behavior of Möller and Koks , pp. 104-107.
- ^ Atkins: Physical Chemistry , p. 1108.
- ^ AF Holleman , E. Wiberg , N. Wiberg : Textbook of Inorganic Chemistry . 102nd edition. Walter de Gruyter, Berlin 2007, ISBN 978-3-11-017770-1 , p. 897.
- ↑ a b c Taube: Compact steel production , p. 131.
- ↑ Schoppa: Was der Hochöfner… , pp. 64–66.
- ↑ Taube: Steel Production Compact , pp. 118–124.
- ↑ Schoppa: Was der Hochöfner ... , p. 88.
- ^ Taube: Steel production compact , p. 147.
- ↑ Schoppa: Was der Hochöfner… , pp. 89–90.
- ↑ Taube: Steel Production Compact , pp. 146–147.
- ↑ Schoppa: Was der Hochöfner ... , p. 90.
- ↑ Taube: Compact steel production , p. 148.
- ↑ ThyssenKrupp: The fifth kiln journey can begin: Large blast furnace 1 in Duisburg-Schwelgen is blown again at the beginning of April after modernization ; Press release from March 19, 2008, 11:00 a.m.
- ↑ a b Common description of the iron and steel industry , pp. 78–79.
- ↑ a b Taube: Compact steel production , pp. 158–159.
- ↑ Gemeinfassliche representation of ironmongery , pp 83-84.
- ^ A b Karl-Heinz Schmidt, Ingo Romey, Fritz Mensch: Coal, petroleum, natural gas: chemistry and technology. Vogel Verlag, Würzburg 1981, ISBN 3-8023-0684-8 .
- ^ Taube: Steel production compact , p. 159.
- ↑ Schoppa: Was der Hochöfner ... , p. 102.
- ↑ General description of the iron and steel industry , p. 96.
- ↑ Schoppa: Was der Hochöfner ... , p. 63.
- ↑ Bergbau-Lexikon der steinkohle-portal.de - blast furnace ( Memento from March 30, 2012 in the Internet Archive )
- ↑ On the subject of climate protection at stahl-online.de: Steel is indispensable for a low-emission world.
- ↑ World Steel Association: World Steel in Figures 2019 . (PDF 1.9 MB) June 6, 2019, p. 6 , accessed on July 17, 2019 .