Machine tool
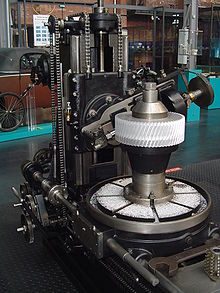

Machine tools are machines for the production of workpieces with tools , the movement of which in relation to one another is specified by the machine. The most important representatives include lathes and milling machines , eroding machines as well as mechanical presses and machine hammers for forging .
The standards DIN 8580 ff (process) and DIN 69 651 part 1 (metalworking), which refer to one another in terms of content, are used to classify them. Machine tools are part of the working machines and together with the tools , devices , measuring equipment and test equipment they are part of the operating equipment . Because of their diversity, they are classified according to various criteria: According to the underlying manufacturing process , they are divided into forming and separating (essentially: dividing , cutting and removing ) as well asjoining machines; according to the increasing degree of automation in conventional machines, automatic machines, CNC machines , machining centers , flexible manufacturing cells , flexible manufacturing systems , flexible transfer lines and conventional transfer lines .
Modern machine tools usually have a modular structure. The most important assemblies include the frame, the drive, the guides and the control. Other assemblies include foundations, tool storage and changers, tool holders, workpiece changers, measuring systems as well as supply and disposal facilities.
The forerunners of machine tools may have existed as early as the Stone Age , but the first machine tools in the modern sense did not emerge until the beginning of the industrial revolution in England and spread very quickly in all industrialized countries. Initially, several machines were driven by a single steam engine, from around 1900 each machine got its own electric drive. Since the middle of the 20th century, their further development has mainly been characterized by automation and flexibility.
Definitions
There are several definitions for machine tools. However, they only offer a more or less rough indication of which machines belong to the machine tools. In particular, primary forming or joining machines are only partially included.
Definition according to Otto Kienzle
A frequently used definition for machine tools comes from the engineer and university professor Otto Kienzle , from whom the classification of the production processes according to DIN 8580 comes. After his death in 1969, it was expanded to better reflect the state of the art.
- A machine tool is a working machine that brings a tool to work on the workpiece under mutually specific guidance . (Kienzle) She takes on the tool and workpiece handling and the recording, processing and feedback of information about the manufacturing process. (Extension)
This brief definition distinguishes machine tools from a large number of similar machines:
- The term “ work machine” excludes all power machines that are used to “generate” or convert energy, such as generators , motors or gears .
- Machine tools are used to manufacture and process workpieces . This part of the definition serves to distinguish it from process engineering machines that produce flow materials and from many other types of machines such as bookbinding or bread slicing machines.
- Machine tools use tools . These can be drills , milling tools and chisels , water , laser and electron beams or the flame of a burner. They use all possible manufacturing processes.
- Workpiece and tool must be guided in a mutually determined manner by the machine tool . The position of the tool and workpiece in relation to one another and their movements are therefore determined by the machine and not by humans. This serves to distinguish it from motor-driven but hand-operated tools such as screwdrivers , jigsaws or angle grinders ("Flex").
Definition according to DIN 69 651
In DIN 69 651, machine tools are defined as mechanized and more or less automated manufacturing equipment that generates a predetermined shape on the workpiece or a change in a predetermined shape on a workpiece through relative movement between the workpiece and the tool.
history
Early forerunners
Due to the clean drilled holes in the Stone Age stone axes has been since the early days speculated that it 6,000 years ago called Fidel drills may have been where the string of a bow is wrapped around the drill that is mounted in a rack. By moving the bow back and forth, the drill can be set in alternating rotations. Such a device would already meet all the characteristics of a machine tool. Archaeological evidence is missing, however, so that it is possible that these replica drilling machines are based on the machine tools common in the 19th century.
In ancient times , the first lathes as well as grinding and drilling machines appeared, which were powered by water power or by animals in the Göpel . However, the tool was still used here by hand. In the Renaissance , Leonardo da Vinci developed machines for the production of various workpieces. These included drilling machines, file cutting machines , machines for thread cutting or cylindrical grinding. In 1771 the first copy lathe was developed, the tool of which was already guided along a defined path by the machine itself.
During the industrial revolution

Machine tools were a prerequisite for the production of powerful steam engines . As a result, the steam engine served as a drive for numerous machine tools in the new factories . The atmospheric piston steam engine was invented by Thomas Newcomen as early as 1712 . When building the required cylinders with a diameter of around one meter and a length of two meters, however, the machines of the time reached their limits: a dimensional deviation of two centimeters was considered a good result. In 1775, John Wilkinson succeeded in building a horizontal drilling machine that could reliably maintain a deviation of a few millimeters. By drilling cylinders in iron, it made it possible to build steam engines according to the design devised by James Watt , which was much more efficient.
Due to the continuing demand for machines, initially in the textile industry and later also in many other areas, the steam engine spread quickly. The associated technical and social upheavals are known as the first industrial revolution . The requirement for high accuracy was decisive for the use of machine tools instead of the traditional manual work . Transmission waves ran through the machine halls from a central steam engine. From there, the energy was passed on to the individual machines via leather straps. In the course of the industrial revolution there were further developments in many areas of production technology, which mutually stimulated and promoted each other. The use of coal instead of charcoal made it possible to produce cast steel , which was soon used for tools and frames of machine tools, which became more precise as a result. The increased use of iron as a material, in turn, increased the demand for machine tools.
Development of important machine types

The lathe proved to be particularly important for industrial production . It was decisively improved by the British Henry Maudslay . He built the first lathe with a tool holder that could be moved using cranks (support with feed). Before that, the tools were still operated by hand, so that the work result strongly depended on the skill and experience of the worker. With the development of Maudslay, the machines became more precise, more efficient, less strenuous to operate, and required less training to operate. The latter in particular was decisive for the rapid spread of the new technology, as experienced lathe operators were so rare that they were banned from emigration in England. Maudslay also invented a lathe for making screws and threads . Previously, they were made by hand, which meant that each thread was individual. The increased accuracy of the machines made it possible for the first time to manufacture screws so precisely that they could be interchanged with one another.
Further improvements come from the two students of Maudslay Richard Roberts and James Fox and Joseph Whitworth . For faster processing, machines were developed with several tools that were in use at the same time. In 1845, the American John Fitch from Connecticut built the first turret lathe in which several tools are in one turret and can therefore be changed quickly. Towards the end of the 18th century, the first mechanically controlled automatic lathes were built in America.
Between 1800 and 1840, the pillar and column drills were developed by Whitworth and William Fairbairn . The twist drill was shown for the first time at the Paris World Exhibition in 1867 . However, because of the high price, despite the great advantages, it took until 1890 for it to prevail against the pointed drill.
The first designs for planing machines come from Maudslay, his student Roberts built the first variant with mechanical feed. The first American planing machine was offered by Gay Silver & Co in 1833. Johann von Zimmermann , one of the founders of the German machine tool industry, received an award at the London World Exhibition in 1862 for his planing machine.
The first milling tool is said to be Jacques Vancanson , the oldest surviving milling machine comes from the American Eli Whitney from Connecticut, who used it in weapons production. The first automatic universal milling machine was designed by the American Joseph Brown in 1860. By around 1900, machines for milling gears were also technically mature.
As a result of the increased demands on accuracy, especially in model and weapon construction, grinding gained in importance. The first grinding machine for metalworking from 1833 is attributed to Alfred Krupp . In 1853, Hiram Barker and Francis Holt received a patent for a machine for grinding brass balls, which were needed for valves in steam locomotives. In 1855 W. Muir & Co. built a tool grinding machine for knives and blades in Manchester.
In 1842, the Englishman James Nasmyth constructed a steam-powered blacksmith's hammer . The hammer bear (tool) was lifted by the piston of the steam engine and dropped onto the workpiece. This made forgings of previously unimaginable sizes possible. Alfred Krupp built a giant steam hammer with a drop weight of 30 tons, with which one could process cast steel blocks of up to 2.5 tons. The first hydraulic forging hammers appeared in 1860. The first drop forging machines were developed towards the end of the 19th century .
By around 1900, the development of classic machine tools and the corresponding manufacturing processes had essentially ended. Almost all types known today were present.
Influences
The development of machine tools was influenced by social, organizational and technical requirements; on the other hand, it was often only a certain level of development of the machines that made these influences possible.
With his famous example of pin production, Adam Smith showed that production processes based on the division of labor could significantly increase productivity : A single unskilled worker can only produce a few pins in a day. If the work is divided into several steps (wire drawing, pinching, sharpening, etc.), five workers, for example, can produce thousands of pins in one day. For individual workpieces such as needles, a series or mass production could be realized. For the production of multi-part goods such as machines or weapons, however, one had to ensure that the individual parts were interchangeable with one another. This production method is known as replacement construction and was implemented by Eli Whitney, among others, who completed an order for 10,000 muskets in just two years. Increasingly higher accuracy requirements were placed on machine tools; on the other hand, this accuracy made the mass production of machines and weapons possible.
America suffered a shortage of labor, especially skilled workers, in the 19th century. Efforts were therefore made to replace all human work as far as possible with machines that were as easy to use as possible and that worked as quickly as possible. The methods of the division of labor were refined around 1900 by Frederick Winslow Taylor through his scientific management . Henry Ford perfected mass production in the early 20th century through the consistent application of Taylor's principles and the introduction of assembly line manufacturing . During his lifetime, however, Taylor was known for another invention: high-speed steel . With it, the cutting speed of cutting machine tools could be increased approximately three times. However, the drives and frames of the existing machines were not designed for such high performance, so that new ones had to be constructed, which found brisk sales due to the high productivity.
The second industrial revolution
By the end of the 19th century, the machines were precise enough to produce usable steam turbines . At the turn of the century, the first power plants for generating electrical energy were put into operation. At first they were mainly used for street lighting. The development of combustion and electric motors made it possible in the course of the second industrial revolution to equip each machine with its own drive, which no longer had to rely on steam boilers in the vicinity. This change took place in several phases. The principle of transmission waves still prevailed in the factories . When large machines were switched on or off, the other machines suffered jerky jolts, which worsened the work result. For this reason, the largest machines were initially equipped with their own drive and then operated for several years via transmissions.
In the second phase, the central steam boilers were replaced by central electric motors, which now drove the transmission shafts. Only in the third phase did each machine get its own motor as a drive. The transition to the single drive was facilitated by the development of high-speed steel: new machines were needed in order to be able to exploit its potential. By eliminating the transmissions, which had a poor level of efficiency, significantly less energy was now used. Machine tools were later given a separate motor for each feed axis . At the same time, the machines were increasingly automated, initially through further development of the mechanical controls, later with simple electrical controls or punch cards . The USA and Japan led the way in this development.
Scientific research
The first technical and scientific schools and academies were founded in the course of the 18th century. Towards the end of the century, the first school of a new type opened: the Polytechnic School in Paris. Many other schools, which were upgraded to technical universities in the course of the 19th century, were built based on their model in France and in German-speaking countries. In the first half of the century, the focus was still on so-called " mechanical technology ", a forerunner of today's manufacturing technology . Karl Karmarsch , director of the polytechnic school and later university in Hanover , wrote a book on the "System of Mechanical Technology" and put on a tool collection that is important in research and teaching. His successor Hermann Fischer published a book on machine tool technology in 1900, in which he classified and described existing machines, but also went into the operation and the meaning of the main and off-peak times .
At that time, the field of production technology still formed a unit: Research was focused on manufacturing processes, but also machine tools, other machines such as mining or textile machines, accounting (for determining cost costs ) and the planning and operation of factories. At the beginning of the 20th century, the first professorships were founded that only dealt with machine tools. Around 1900 the relationship between science and practice was reversed: During the industrial revolution, it was resourceful entrepreneurs who continued to improve machine tools; science could only describe the process. Since 1900, a better theoretical understanding of production became a prerequisite for technical progress. Initially, some companies, such as Ludwig Loewe AG, which is considered exemplary in this regard, or Taylor himself, tried their hand at research, but soon reached their limits. To this day, a large part of production research is carried out jointly by universities, research institutes and industry. In America and England, technical schools and colleges were established with a delay of several decades, and they were also relatively few in number. The best known is the Massachusetts Institute of Technology . Around 1900, therefore, a widespread shortage of well-trained engineers became noticeable in the Anglo-Saxon countries.
Third industrial revolution
Around 1950, numerical control was developed at the Massachusetts Institute of Technology (MIT) , which made it possible to mill complex geometries with computers. However, the hardware required for the control alone was more expensive than a conventional machine tool. In addition, there was the high expenditure for programming, so that numerical controls could not initially establish themselves. The development of the microprocessor at the beginning of the 1970s made it possible in the third industrial revolution to equip every machine with its own computer, which made it possible to use numerical controls at low cost. The programming procedures were also simplified so that the new technology spread quickly. Its advantages are, on the one hand, the ability to create geometries of almost any shape and, on the other hand, the high degree of flexibility: For the production of another product type, you only had to load a new program into the memory. This significantly reduced the production costs for individual parts and small series . This effect was reinforced by the development of the first machining centers (BAZ) that combine several manufacturing processes. In the past, you often had to turn workpieces on a lathe first and then process them on a milling machine. With a machining center that masters both processes, there is no need to reclamp or transport the workpiece between the two machines.
Through the development of numerical controls and the material flow and handling technology , the first were flexible manufacturing systems possible. They have several identical or different types of machines connected by transport devices (e.g. the new industrial robots ), which enable an individual path through the system for each workpiece. From now on it was also possible to manufacture medium-sized series inexpensively. The use of robots on production lines also made them more flexible.
In the last decades of the 20th century Germany and Japan as well as the USA were leaders in the world market. In 2013, China was both the largest producer and buyer worldwide, followed by Japan and Germany. While China still imports machine tools net, Japan and Germany have a clear export surplus. Other important manufacturing nations are Italy, Taiwan, South Korea, the USA and Switzerland. The most important customer industries are mechanical engineering with around a third of production and the automotive industry, including suppliers, with a further third.
Classification of machine tools
Machine tools, together with tools , devices , measuring and testing equipment, are part of the operating equipment . They have a wide variety of manifestations and are therefore classified according to different criteria. The first option is single-purpose machines , with which only a very limited range of workpieces is possible (such as hobbing machines for hobbing or gear form grinding machines ), and universal machines , with which different workpiece shapes can be produced. They are usually named after the manufacturing process for which they were mainly designed, such as lathes or milling machines (a milling machine can also be used for drilling). In addition, they are classified according to the number of axes (up to six), the position of the main spindle (horizontal or vertical), the structural design (e.g. cross-bed lathe), the kinematics (parallel or serial), the achievable accuracy ( Standard, precision and ultra-precision machines, different depending on the manufacturing process) and the workpiece class (machines for the production of gears , camshafts or crankshafts ).
The two most common classification options are analogous to the classification of the main groups of manufacturing processes and according to the degree of automation .
Classification according to manufacturing process
According to the narrower view, only the forming , cutting and removing machines are counted as machine tools. According to a broader perspective, the primary forming machines (e.g. casting machines), joining and all separating machines ( dividing , cutting and removing) are also included.
With around two thirds of the production value of all machine tools, metal cutting machines are among the most important. They include in addition to turning and milling machines and drilling machines , planers , shapers , broaching , sawing , grinding , honing and lapping machines (for lapping ).
The forming machines can be further subdivided according to the manufacturing process into bending machines , presses , drawing machines (for pulling through ) and rolling machines . However, several manufacturing processes can be implemented by installing different tools. Therefore, a classification according to the underlying functional principle has proven itself. With energy-bound forming machines, the same amount of energy acts on the workpiece with each stroke. This can be done by always dropping the tool from a certain height like a drop hammer . The top pressure and counter blow hammers as well as screw presses also belong to this group . Path-bound forming machines cover the same path with each stroke. These include eccentric presses , crank presses and toggle presses . Force-bound forces act on the workpiece until a certain force is reached. These include hydraulic presses .
Cutting machines are very similar in construction to the forming machines and are divided into guillotine shears , cutting presses and punching machines . They are mainly used for processing sheet metal .
The ablative machines are divided according to the underlying processes into erosion machines , laser processing machines and water jet cutting machines . Because of the high costs due to the low productivity, they are only used when other machines cannot be used. This is the case, for example, with very hard, brittle or temperature-sensitive materials or for producing undercuts and very small shaped elements.
Classification according to the degree of automation
A conventional machine tool generates the cutting and feed movements via a motor and a gearbox as well as handwheels. An automatic machine, on the other hand, already controls the feed movement. A CNC machine performs an automatic work cycle on a manually clamped workpiece. The tool change is usually carried out automatically. A machining center (BAZ) also integrates the workpiece change and the tool control system. The flexible manufacturing cell includes several machines with their tool magazines, a larger workpiece storage and z. T. integrated measuring devices. Flexible manufacturing systems (FMS) have a cross-machine automatic workpiece flow with connection to a production control or a production planning system. Conventional transfer lines have a very low level of flexibility. Small changes in the product range can only be made through extensive set-up .
Machine tool assemblies
Machine tools are usually assembled from modular assemblies. This simplifies the construction and enables higher quantities and thus lower production costs for the individual components. The individual assemblies are often put together according to customer requirements. The most important of these include the frame , drive , control and the guides , which allow the tool only certain possibilities of movement and prevent others. Other assemblies include foundations , tool stores and changers , tool holders , workpiece changers , measuring systems and supply and disposal facilities .
frame
The machine frame absorbs the machining forces and secures the position of all assemblies in relation to one another. It largely determines the static and dynamic rigidity of the machine tool . In the case of smaller machines, the frames are designed as a table. For heavier machines, bed designs in open (column or C-construction) or closed (portal) construction are used.
Designs made of cast iron , steel , light metals , mineral cast (polymer concrete) or fiber-reinforced plastics are typical . Granite frame components can also be found in ultra-precision machines . Foamed light metals are now also used. For small quantities, welded or screwed structures are preferred, for larger quantities cast frames.
Important properties of the frame materials are the modulus of elasticity , the density , the coefficient of thermal expansion , the thermal conductivity , the yield point and the material damping that dampens the frame's vibrations . Mineral casting is distinguished from metallic materials by its low density and very high damping. Because of the low load-bearing capacity, the frames have to be very massive. Of the metallic materials, cast iron is characterized by good damping, which is why it is used particularly frequently.
steel | Cast iron with nodular graphite |
Cast iron with flake graphite |
Mineral cast | aluminum | |
---|---|---|---|---|---|
Young's modulus [10 5 N / mm²] | 2.1 | 1.6 ... 1.85 | 0.8 ... 1.4 | 0.4 | 0.67 ... 0.76 |
Specific weight [N / dm 3 ] | 78.5 | 74 | 72 | 23 | |
Thermal expansion coefficient [10 −6 / K] | 11.1 | 9.5 | 9 | 10… 20 | 21 ... 24 |
Specific heat capacity [J / (g · K)] | 0.45 | 0.63 | 0.46 | 0.9 ... 1.1 | 0.88 ... 0.92 |
Thermal conductivity [W / (m · K)] | 14… 52 | 29 | 54 | 1.5 | 117… 211 |
Yield point [N / mm²] | 400… 1300 | 400 ... 700 | 100 ... 300 | 10 ... 18 | |
Material damping [dimensionless] | 0.0023 | 0.0045 | 0.02 |
foundation
Special foundations are particularly important for large machines , usually made of concrete with 70 to 90 percent of the total mass of a machine poured into a floor form, because they guarantee a high overall torsional stiffness due to their high inertia and enable the necessary accuracy through quiet machine operation. Especially with heavy workpieces and / or with a correspondingly high workforce or with shock loads, a correspondingly massive design of the machine foundation is important, because otherwise the machine will inevitably be partially lowered, which means that the geometric accuracies customary today can no longer be achieved in the entire work area.
Guides and bearings
Guides and bearings limit the number of degrees of freedom of machine components. Straight guides allow movement in a linear ( translational ) axis, round guides or bearings allow rotation and, in the case of shaft guides, additional linear movement. They are differentiated according to their cross-sectional shape (e.g. dovetail or V-guide) and according to the type of guide surface separation into magnetic bearings , roller guides and sliding guides , which in turn are divided into hydrodynamic, hydro- and aerostatic bearings. Guides and bearings are possible small coefficients of friction , have a low wear subject, a good damping have to vibrations to be avoided, be protected against falling chips and other parts as possible without play and little maintenance and be a high rigidity have.
The simplest version is a hydrodynamic bearing in which the two contact surfaces are wetted with lubricating oil . The friction-reducing effect of the lubricating oil only starts at a certain minimum speed (so-called stick-slip effect ). In a hydrostatic bearing , oil pressure is built up by means of a pump , which separates the contact surfaces even when they are at rest. With aerostatic guides, the upper component slides on an air cushion . Most guides are designed as roller guides in which the contact surfaces are separated by round bodies (mostly balls).
Leadership type | Coefficient of friction |
Starting coefficient of friction |
static stiffness |
damping |
---|---|---|---|---|
hydrodynamic | 0.05 ... 0.2 | Well | very good | |
hydrostatic | 0.001… 0.0001 | good ... high | very good | |
aerostatic | 0.00001 | good ... high | bad | |
Rolling guide | 0.01 ... 0.00001 | high | bad |
Drives
The drive units include the main drive, which is responsible for the work movement, and the feed drives for positioning the tool. Drives for all other tasks such as cooling lubricant transport , chip conveyors or for generating hydraulic pressure are called power take-offs. The demands on drives are high dynamics (especially accelerations), as they have a strong influence on economic efficiency, high maximum speeds and a large and continuously adjustable speed range.
Main drive
The main drive usually consists of a motor , a gearbox , a safety clutch (in the simplest case a V-belt that slips in the event of an overload) and the main spindle as the carrier of the tool or workpiece. Other machine tools have a direct drive in which the rotor of the electric motor sits directly on the main spindle ( motor spindle ). In view of the high power of the drives, especially when using motor spindles, it is important to dissipate the heat loss in a targeted manner in order to avoid inaccuracies in the machine due to the thermal expansion of the frame.
AC motors are mostly used as motors (synchronous or asynchronous). Occasionally, DC motors or hydraulic or pneumatic motors are also used. Gearboxes for torque-speed conversion are often continuously variable gearboxes such as envelope gearboxes or friction gearboxes . Gear units for converting the rotary motor movement into a translatory movement are rack-and-pinion systems, ball screws , crank gears or helical gears .
Power take-offs
Today all moving axes generally have their own feed drives . They are decisive for the working accuracy of the machine and should therefore run quickly and uniformly and have a high level of positioning accuracy. They are divided into linear direct drives , which directly generate a translatory movement, and rotary drives, the movement of which is only converted by a gear unit. Basically, the same gear units are used as for the main drives. Power take-offs are almost exclusively electric; Hydraulic motors are rarely used.
control
Controls are used to automate machine tools. The first controls for machine tools were still implemented mechanically, for example with cams . Today they are operated electrically, e.g. B. with relays or semiconductor components . The numerical controls are special controls for machine tools . Today they enable the production of workpieces of almost any shape. This requires good path controls that guide the tool along a programmed path of any shape.
Electrical controls
The electrical controls read in all signals (e.g. via buttons or switches operated by the operator and via temperature, pressure or displacement sensors), process them and send signals to the actuators to be controlled (e.g. motors or display displays). On the one hand, they are divided into connection-programmed controls (VPS) and programmable logic controls (PLC) according to the type of implementation, and on the other hand, according to the control principle, into logic and sequence controls . With a VPS, the function is determined by the connection between the individual assemblies (relays). They are used in particular in safety-critical applications. In the case of a PLC, on the other hand, the function is determined by software that is stored in a memory. They make up the majority of the electrical controls and mostly control the drives directly, but they can also communicate with other machines (e.g. on transfer lines ) and offer interfaces to the CNC controls. In the case of logic control, the output signals are determined by a logic combination (logic AND gate , OR gate , non-gate ...) of the input signals. They are used, for example, to select the direction of rotation of a motor or to control a feed drive. Sequence controls, on the other hand, necessarily have a step-by-step sequence and are much more important in machine tools than pure logic controls. You care e.g. B. to change the tools.
Numerical controls
Numerical controls (NC) are special controls for machine tools that are much more flexible than electrical ones. They are part of the sequence controls and indicate the individual sequence steps in the form of alphanumeric characters. Originally punched tapes were used for data entry, but soon they were converted to microprocessor technology (computerized numerical control, CNC). Today both terms are practically the same. Its main task is to move the tool along any shape of path. With NC controls it is possible to control two or more axes at the same time and to use the tool e.g. B. to lead on a circular path. To do this, the control divides the path into small sections and moves to points on these sections one after the other. The paths between these points are interpolated . From this, nominal position values are calculated for the axes, which are passed on to the drives.
The programming can be carried out in the office by the work preparation department , or directly in the workshop by the operator ( workshop-oriented programming , WOP). Simulation programs help to avoid collisions of the tool in the work area and automatically calculate the required travel paths and the production time from CAD data. This data can then be passed on to a higher-level production planning and control system. The CNC programs can also be stored on a central master computer, which supplies the individual machines with the required programs if necessary ( Distributed Numerical Control , DNC). It is also possible to monitor the cutting force in order to calculate the tool wear and to partially compensate for the deformation of the machine. Modern CNC controls can also take care of order , pallet, tool and tool life management.
Tool storage and changer
Machine tools are often equipped with tool stores from which tools can be exchanged in the work spindle or tool holder either directly or via a fully automatic tool changer, as required. Lathes often have turrets that do not change the required tool, but rather rotate it into the working plane. In modern machine tools, a replacement tool is increasingly being exchanged independently after a programmed service life has expired or after the actual tool wear ( cutting force measured by the spindle motors ), so that such machines can then process workpieces largely unattended in combination with automatic workpiece changers.
Measuring systems
Modern machine tools have measuring systems that are used to record the position of e.g. B. serve the tool or an axle slide. The angle and length measurements required for this are mainly carried out optoelectronically , e.g. B. with incremental encoders or absolute encoders on rotating shafts and glass scales that measure the position directly . Furthermore, ohmic, inductive, capacitive, magnetic or electromagnetic active principles of the transducers are common.
A distinction is made between direct and indirect position measuring systems for measuring devices . With both measuring systems, the scale segments covered are counted via sensors , and the distance covered is then calculated from this number. In indirect position measuring systems, the scale is arranged in a circle so that the system measures the change in angle of the threaded spindle and then calculates the change in distance using the pitch of the thread . With the more precise direct distance measuring systems, the scale is attached parallel to the direction of movement, so that the length of the sections (multiplied by the number of sections counted) corresponds directly to the distance covered.
Tool holders
In order to ensure a quick tool change with high accuracy at the same time, the tool holders (tool-spindle interface) are standardized. In the past, so-called steep taper (SK), even earlier so-called Morse taper (MK), were predominantly used for rotating tools . Today, due to their technological advantages, hollow shank taper mounts are increasingly used. In the case of HSK recordings, among other things, clamping on the inner contour, which makes the system suitable for higher speeds. For all mounting systems there are adapters to the other systems in order to enable efficient tool use in the often mixed machine parks.
Workpiece changer
Modern milling machines and drilling machines often have two or more pallets for clamping the workpieces, which can be brought into the work area alternately. This allows clamping operations to be carried out outside the work area, while machining can take place on the previous pallet. If the workpieces are exchanged together with the pallet as described, one speaks of a pallet changer . Larger workpieces can be swapped in and out with robots .
Supply and disposal facilities
Nowadays, machine tools used in metal-cutting production are predominantly equipped with cooling and lubrication devices. These usually convey a water-oil emulsion into the work area of the tool, be it via spray nozzles on the machine, on the spindle head or through nozzles in the respective tool. The cooling lubricant is filtered in circulation. In the course of environmentally and workplace-friendly production, however, the so-called minimum quantity lubrication (MQL or MQL) is increasingly being used nowadays . A very small amount of cooling lubricant is atomized with air and sprayed onto the active site. The supply and disposal facilities also include the chip conveyor , which conveys the separated chips from the work area into a container.
Machine housing and safety devices
Machine tools today usually have a machine housing. This serves to protect the operator from flying chips, from cooling lubricant and from the resulting noise pollution, as well as protection against injuries to the moving parts and protection against bursting (e.g. if a tool breaks). Larger machines and systems are protected by light barriers and grids.
Properties of machine tools
In addition to properties that affect the profitability of machine tools, such as performance, travel speed, tool change time, etc., there are also properties that affect the quality of the product to be manufactured. These are:
Geometric accuracy
The geometric accuracy indicates the manufacturing quality of the unloaded machine, i.e. without loading by machining forces. The geometrical accuracy that can be achieved essentially results from the manufacturing quality of the machine tool, the play and the design. A distinction is made between deviations in shape and position .
Static stiffness
The static rigidity or rigidity results from the geometric statics (wall thickness, cross-sections) and the properties of the materials used. Furthermore, the position, shape and number of joints and guides (fixed and movable connections of machine elements) are particularly decisive for the attainable rigidity. Static deformations can be compensated for by the CNC control.
Dynamic stiffness
The dynamic rigidity of a machine results from its deformations when forces change over time and often cause vibrations. They have a negative influence on the workpieces (especially surface roughness) and the service life of the machine and are therefore fundamentally undesirable. Since the dynamic deformations, in contrast to the static ones, also depend on the frequency of the excitation, they cannot be corrected so easily. A distinction is made between self-excited and externally excited vibrations, which in turn are divided into free and forced vibrations.
A single excitation leads to a free oscillation with a natural frequency that slowly decays.
In the case of periodically recurring excitations, there is a forced oscillation with the frequency of the excitation. These can be introduced into the machine via the foundation, caused by imbalances (e.g. of the motor), tooth meshing errors in the gears, bearing errors or worn tools.
Self-excited vibrations arise from the manufacturing process itself. The machine then also vibrates at its natural frequency, but more and more over time. This can be caused by built- up edges , regenerative effects or a falling cutting speed - cutting force characteristic.
Thermal behavior
The thermal behavior of a machine tool describes the reaction to temperature changes, especially the change in position of the tool relative to the workpiece. It is significantly influenced by the action of heat sources and sinks, depending on the amount of heat and its location or arrangement. In terms of thermal stress, a distinction is made between internal and external influences. Internal influences are z. B. exerted by drive losses in drive motors, pumps, bearings, guides and in the hydraulic system or caused by deformation or machining heat in the tool, workpiece, chips and cooling lubricant. External influences are caused by the indoor climate (temperature distribution, temperature fluctuations, air currents), by direct (one-sided) heat radiation (sun, heating systems, neighboring systems) or by heat sinks (foundations, fresh air flows through doors and windows).
To increase the accuracy and despite the effort to keep temperature fluctuations low, it is advantageous to build machines thermosymmetrically. Thermosymmetry means that expansions cancel each other out. The expected temperature distribution in the components has an influence, as well as the length and the expansion coefficient. With the knowledge of the temperature behavior of the machine tool, the thermal expansion in the CNC control can be partially compensated.
Requirements and economic assessment
Different requirements are placed on machine tools from the customer and user perspective. The machine should maintain the required working accuracy, which results from the geometric accuracy and the static, dynamic and thermal rigidity. The work accuracy is described in the context of quality management systems by the machine capability. In principle, it must be better than the required manufacturing accuracy, which results from the design documents.
The profitability of a machine tool is largely a result of its productivity . It can be increased by reducing idle times, main times and set-up times . Machining centers and production cells can, for example, prepare additional tools and workpieces at the same time as machining, thus saving set-up and non-productive times. The main time is reduced by increasing the cutting speed (with cutting machines). Since the life cycles of many products are shorter than the service life of the machines, they should be able to process a wider range of workpieces. This includes differences in the geometry and the materials used. When it comes to costs , not only the procurement costs are important, but also the operating and disposal costs. The total costs can be estimated using the total cost of ownership approach. The operating costs result from the specific energy, tool and auxiliary material consumption. In business administration, the Gutenberg production function is a model for optimizing specific consumption. Minimum requirements for occupational safety and environmental protection are regulated by law.
A large part of a company's capital is tied up in machine tools . The investment calculation offers a tried and tested set of instruments for procurement . In the cost accounting , the utilization of the machines by production is calculated with machine hourly rates. During which asset management to the procurement, maintenance busy and sale of the machine, it goes into the machine scheduling to the optimum operation.
kinematics
The kinematics of a machine tool or a robot is the name given to the organization and technical execution of the movements of the tool and workpiece. The directions of movement are broken down into axes of movement depending on the structure of the machine.
Serial kinematics
The serial kinematics refers to the classical configuration of a kinematic chain : A module that is responsible only for the drive in a movement axis, sets a second with another axis of motion in motion, and it may be followed by further, until the desired overall movement achieved. So-called Cartesian kinematics represents a special case of this kinematics . Here, all feed axes are arranged perpendicular to one another in order to achieve the coordinates in a Cartesian coordinate system in a mechanically simple manner. In most cases, each feed axis is named after the corresponding coordinate axis (in three dimensions, for example, X , Y and Z ).
Example console Milling: on the machine column, the spindle housing is moved, with a front-mounted swivel head as the support of the milling tool, in a guide back and forth in the machine axis Y . The clamping table moves on the console to the left and right of the machine axis X . The console moves with the clamping table rests on the machine frame up and down, and the machine axis is Z .
Parallel kinematics
A parallel kinematics designates a kinematics with parallel switched axes of movement. This avoids one drive having to move the next. Parallel rod kinematics are often used here.
The implementation of this kinematic principle in machine tools has been the focus of research projects for machine tools for over 20 years because of the promising geometric properties. To date, however, there has been no significant use in production, which is traditionally dominated by machines with serial kinematics. The advantage of parallel kinematics is usually higher dynamics due to the low mass of the guide elements, which - in contrast to serial kinematics - distribute the loads evenly (more) on all guide elements.
(Parallel) parallel kinematics
In contrast to serial kinematics, (parallel) rod kinematics work by changing the distances from points of a moving object (tool) to predefined fixed points in space. The spatial position (and location) of a moving object is not described using a vector-based coordinate system (i.e. a zero point and N non-parallel vectors to encode movements in N dimensions), but rather using the distances between object-space-point pairs.
Typically, for example, for a pure position specification (without rotation axes) in a space with N dimensions, N + 1 distance specifications to N + 1 distinct spatial points are necessary. In practice, however, the machine design often excludes parts of the theoretically achievable space, so that often only N distance information to N points is necessary for an ambiguity-free position information . For example, a so-called tripod with only three arms can easily reach a predefined area of a three-dimensional space.
Precise positioning is achieved by changing the length of several telescopic arms, which are all anchored at one end in a mutually immovable position and at their other end with the object to be positioned.
Example: hexapods
With so-called hexapods (hexa Greek numbers : six , pod Greek : foot ), all feed drives work in parallel with one another in order to generate the desired movement of a tool in space and at the same time a desired inclination of the tool holder or the tool.
See also
Web links
- VDW (Association of German Machine Tool Manufacturers)
- Machine tool laboratory WZL of the RWTH Aachen
- IMU industry study machine tool construction 2017
- Lathes: 4000 years of development
literature
Specialist literature
- Klaus-Jörg Conrad: Pocket book of machine tools. Fachbuchverlag Leipzig, Munich / Vienna 2002, ISBN 3-446-21859-9 .
- Andreas Hirsch : Machine tools: basics, design, examples. 2nd Edition. Springer-Vieweg, Wiesbaden 2012, ISBN 978-3-8348-0823-3 .
- Reimund Neugebauer (Ed.): Machine tools: Structure, function and application of cutting and removing machine tools. Springer, Berlin / Heidelberg 2012, ISBN 978-3-642-30077-6 .
- Hans Kurt Tönshoff : Machine tools: Basics. Springer textbook, 1995, ISBN 3-540-58674-1 .
-
Manfred Weck , Christian Brecher : Machine tools .
- Volume 1: Types of machines and areas of application. 6th edition. Springer, Berlin 2005, ISBN 3-540-22504-8 .
- Volume 2: Construction and Calculation. 8th edition. Springer, Berlin / Heidelberg 2005, ISBN 3-540-22502-1 .
- Volume 3: Mechatronic systems, feed drives, process diagnostics. 6th edition. Springer, Berlin / Heidelberg 2006, ISBN 3-540-22506-4 .
- Volume 4: Automation of machines and systems. 6th edition. Springer, Berlin / Heidelberg 2006, ISBN 3-540-22507-2 .
- Volume 5: Metrological examination and assessment. 7th edition. Springer, Berlin / Heidelberg 2006, ISBN 3-540-22505-6 .
Dictionaries
- Henry George Freeman: Cutting machine tools - German-English explanations of terms and comments. Verlag W. Girardet, Essen 1973, ISBN 3-7736-5082-5 .
- Hans-Dieter Junge: Dictionary of machine tools and mechanical engineering: English / German, German / English - Dictionary machine tools and mechanical manufacturing. Weinheim 1992, ISBN 3-527-27993-8 .
Books on the history of machine tools
- Günter Spur : On the change in the industrial world through machine tools - a cultural-historical consideration of manufacturing technology. Carl Hanser Verlag, Munich / Vienna 1991, ISBN 3-446-16242-9 .
- W. Steeds: A history of Machine Tools 1700-1910. Oxford 1969, OCLC 476608011 .
Individual evidence
- ↑ Reimund Neugebauer (Ed.): Machine tools: Structure, function and application of cutting and removing machine tools. Springer, 2012, p. 4.
- ^ HK Tönshoff: Machine tools. Springer, Berlin 1995, p. 2.
- ^ HK Tönshoff: Machine tools. Springer, Berlin 1995, pp. 1f.
- ↑ Andreas Hirsch: Machine tools: Basics, design, exemplary embodiments. 2nd Edition. Springer-Vieweg, Wiesbaden 2012, ISBN 978-3-8348-0823-3 , p. 2.
- ↑ Günter Spur: On the change in the industrial world through machine tools. Carl Hanser Verlag, Munich / Vienna 1991, ISBN 3-446-16242-9 , pp. 25-95.
- ↑ Günter Spur: Production technology in transition. 1979, pp. 116f-118, 64-89.
- ↑ Günter Spur: Production technology in transition. 1979, pp. 116-138.
- ↑ Günter Spur: Production technology in transition. 1979, pp. 140, 176-183.
- ↑ Günter Spur: On the change in the industrial world through machine tools. Carl Hanser Verlag, Munich / Vienna 1991, ISBN 3-446-16242-9 , pp. 313-330, 424-430.
- ↑ Hans-Jürgen Warnecke: The fractal factory. Springer, 1992, ISBN 3-540-55200-6 , pp. 14-19.
- ^ HK Tönshoff: Machine tools. 1995, p. 3.
- ↑ M. Weck, C. Brecher: Machine tools. 5th edition. Volume 1, 1998, p. 3.
- ↑ Tool + machine. January 2015, p. 11. OnlineArchiv ( Memento from June 13, 2015 in the Internet Archive )
- ↑ Reimund Neugebauer (Ed.): Machine tools: Structure, function and application of cutting and removing machine tools. Springer, 2012, p. 18f.
- ↑ M. Weck, C. Brecher: Machine tools. 5th edition. Volume 1, p. 17.
- ↑ M. Weck, C. Brecher: Machine tools. 5th edition. Volume 1, pp. 51-53.
- ↑ A. Hirsch: Machine tools. Springer Vieweg, Wiesbaden 2000, p. 412.
- ↑ Reimund Neugebauer (Ed.): Machine tools: Structure, function and application of cutting and removing machine tools. Springer, 2012, p. 16f.
- ↑ A. Hirsch: Machine tools. Springer Vieweg, Wiesbaden 2000, p. 83.
- ↑ M. Weck, C. Brecher: Machine tools. Volume 2: Construction and Calculation. 8th edition. Springer, Berlin / Heidelberg 2005, pp. 7-12.
- ↑ A. Hirsch: Machine tools. Springer Vieweg, Wiesbaden 2000, pp. 86-88.
- ↑ Table taken from: R. Neugebauer: Machine tools. 2012, p. 423.
- ↑ M. Weck, C. Brecher: Machine tools. Volume 2, pp. 183-210.
- ↑ W. Bahmann: Machine tools compact - assemblies, use and trends. 21st edition. Springer, Berlin 2013, p. 65.
- ↑ A. Hirsch: Machine tools. Springer Vieweg, Wiesbaden 2000, pp. 97f.
- ↑ Reimund Neugebauer (Ed.): Machine tools: Structure, function and application of cutting and removing machine tools. Springer, 2012, p. 381f.
- ↑ M. Weck, C. Brecher: Machine tools. Volume 2, pp. 234-487.
- ^ J. Milberg: Machine tools - basics. 2nd Edition. Springer, Berlin 1995, pp. 153-226.
- ^ W. Bahmann: Machine tools compact - assemblies, use and trends. 21st edition. Springer, Berlin 2013, p. 36f.
- ^ HK Tönshoff: Machine tools. Springer, Berlin 1995, pp. 125-162.
- ↑ M. Weck, C. Brecher: Machine tools. Volume 3: Mechatronic systems, feed drives, process diagnostics. 5th edition. Springer, Berlin / Heidelberg 2001, pp. 33-57, 113-318.
- ^ J. Milberg: Machine tools - basics. 2nd Edition. Springer, Berlin 1995, pp. 329-370.
- ↑ M. Weck, C. Brecher: Machine tools. 6th edition. Volume 3, pp. 99-110.
- ↑ M. Weck, C. Brecher: Machine tools. 6th edition. Volume 4, pp. 151-182.
- ↑ M. Weck, C. Brecher: Machine tools. 5th edition. Volume 1, Springer, 1998, pp. 494-533.
- ↑ M. Weck, C. Brecher: Machine tools. Volume 3: Mechatronic systems, feed drives, process diagnostics. 5th edition. Springer, Berlin / Heidelberg 2001, pp. 40-88.
- ^ HK Tönshoff: Machine tools. Springer, Berlin 1995, pp. 220-233.
- ^ J. Milberg: Machine tools - basics. 2nd Edition. Springer, Berlin 1995, pp. 318-322.
- ↑ M. Weck, C. Brecher: Machine tools. 5th edition. Volume 1, Springer, 1998, pp. 494-533.
- ↑ M. Weck, C. Brecher: Machine tools. 5th edition. Volume 1, Springer, 1998, pp. 533-569.
- ↑ M. Weck, C. Brecher: Machine tools. Volume 2, pp. 607-631.
- ↑ A. Hirsch: Machine tools. Springer Vieweg, Wiesbaden 2000, p. 56.
- ↑ Rudolf Jürgler: machine dynamics. 3. Edition. Springer, Berlin 2004.
- ^ J. Milberg: Machine tools - basics. 2nd Edition. Springer, Berlin 1995, pp. 79-112.
- ↑ M. Weck, C. Brecher: Machine tools. Volume 2: Construction and Calculation. 8th edition. Springer, Berlin / Heidelberg 2005, pp. 84–95.
- ↑ W. Bahmann: Machine tools compact - assemblies, use and trends. 21st edition. Springer, Berlin 2013, pp. 1–5.