Stonemason
The stonemason (plural: stonecutters or stonemasons ; Latin aciscularius or lapicida, lapidarius ) exercises one of the oldest craft professions. Its original material was natural stone . Today, he also edited cast stone or artificial stone and used alongside traditional hand tools and machines . Geometric shapes, profiles, ornaments, writing and other symbols dominate his objects, which are often created based on foreign designs. These are, for example, tombstones or components. In contrast to the stonemason, the stone sculptor , who completes the first two years of training together with the stonemason in Germany, is more creative.
A widespread historical name for stone sculptors and stonemasons was stone cutter , by which one understands today only the worker in the quarry who digs the blanks there and prepares them for the stone mason or stone sculptor. Because this work is mostly done by machine and industrially automated today, the profession of stone cutter can no longer be found in many areas of the world. Excepted from this are some less industrialized countries, in which, due to the tradition and religious integration, there is a lot of ornamental and artistic work for stonemasons and stone sculptors. One example of this is Indonesia, particularly Bali.
Word origin
The Duden dictionary of origin gives the etymology : “ mhd. Steinmetze , ahd. Steinmezzo ; the second part is borrowed from Gallo-Roman ; the vlat ahead. matio , macio "bricklayer, stonemason" [cf. French maçon »bricklayer«] ultimately belongs to the German word group to make in its old meaning. »build, erect« "
Country-specific features
Different developments of the stonemasons in the German-speaking area (Switzerland, Austria and Luxembourg) were and are marginal and can therefore be neglected. Neither the earlier nor the present (2008) stone working techniques and stone material differ. In the Alpine republics, however, the use of natural stone is more extensive due to its regional occurrence.
In the apprenticeship there are minor differences. In the German-speaking countries, training is based on the dual training system . This means that the stonemasons learn the skills in the company and in separate courses in the inter-company training and the theory in the vocational school. In most other European countries, for example in Italy, France and Spain, training only takes place at school and not in companies.
The national development has been different since around 1900 due to country-specific organizational forms in chambers of crafts and chambers of industry and commerce . In Germany and Luxembourg there are chambers of crafts that are responsible for monitoring and handling apprenticeship training and taking the master craftsman's examination . Both employers and employees are represented in the committees of the HWK. The vocational school teachers are also represented in the committees that are exclusively responsible for vocational training . In some cases, HWK delegate the acceptance of the journeyman's exams to the stonemasons' guild.
There are also the Chambers of Commerce and Industry (IHK) in Germany , which are responsible for training industrial stonemasons and natural stone mechanics. Since the number of industrial apprentices is low, the IHK has partly handed over the acceptance of the examination of the stonemason skilled workers to the craft organizations, while the natural stone mechanics take the exams in central locations in front of the IHK examination committees.
In Austria there are the chambers of commerce in which the stone industry and the stonemasonry are combined in one organization. The responsibility for the training lies with the chambers of commerce or with the stonemason specialist organizations commissioned by them.
There are no chambers of crafts in Switzerland. The Steinmetz professional associations are responsible for the training .
Another difference is that in Austria, Luxembourg and Germany only master stone masons and stone sculptors can set up and run a business . In Switzerland, journeymen can also do this.
history
prehistory
The oldest stone carvings are half-relief representations on rocks of the Dordogne from the Paleolithic culture of the Aurignacien (about 40,000 years old), such as the La Ferrassie site . In Solutréen and Magdalenian (about 20,000 to 14,000 years ago) there was a heyday of reliefs on rock faces, such as the aurochs in Abri Fourneau du Diable or the horse fries in Abri Cap Blanc .
The monumentality of stone carvings is first demonstrated in the Middle East with the stone T-pillars from Göbekli Tepe and Nevali Cori around 10,000 to 9,000 BC. Chr. Clearly.
Ancient Egypt
In ancient Egypt , the stones to be extracted were extracted using natural fissures with hand tools. The question of whether the Egyptians used the wedge technique with wood and water remains open according to the current state of knowledge.
The Egyptians mainly used soft stone , such as limestone and sandstone , which were extracted in the immediate vicinity of the structures. Limestone was for all great pyramids of the Old Kingdom, as the Cheops pyramid , the Pyramid of Chephren and Menkaure used in Giza. The great rock temple of Ramses II in Abu Simbel was carved out of sandstone. Only statues for graves and temples , columns , pillars, obelisks and courtyard paving were made from hard stone. For the rough work on soft and hard stone, the Egyptian stonemasons used shaped stone handpieces made of dolerite or granodiorite that were guided with both hands . The Egyptians also used these tools to extract rough blocks from granite , diorite or gabbro . This tool use is documented by finds of these tools and tool remains.
For the finer processing of soft rock were between 1500 and 600 BC. Chr. Knüpfel of wood and chisel from copper and from later Bronze used only after iron tools. The stone surfaces were smoothed with polishing stones ( pumice ) and emery material such as quartz sand. Iron chisels, iron stone splitting tools and wedges made of iron were not used in Egypt until Roman times .
Little is known about the position of Egyptian stonemasons in society, but there are supposed to have been associations of builders. It can be assumed that the stonemasons were completely dependent on the pharaohs and viziers . This went so far that bronze chisels, which were very valuable at the time, had to be returned in the evening and a loss resulted in heavy penalties. It is believed that builders and stonemasons, who had knowledge of the location of the royal tombs, also lost their lives with the death of the Pharaoh.
Ancient Greece

The Greek masons used bronze and iron pointed chisel , possibly two tip or pointed hammers . They used tooth irons and, according to archaeological finds, it is also assumed that the tooth surfaces were used . If parts with radial shapes such as profiles were to be smoothed, the Greeks partially used chisels or round irons, which did not have a straight, but a round cutting edge. From the middle of the 5th century there are traces of stone drills. Metal rasps were mainly used in places where paint was to be applied later. Marbles were primarily processed as natural stones .
The stone surface was initially not polished, it remained rough and was given a velvety surface through the use of pointed iron. The stone sculptures were colored. It was only in later times that the marble was always smoothed and polished by the Greek stone sculptors from 350 onwards . This can be proven, for example, by traces of processing on the Parthenon .
The stonemasons and especially the stone sculptors were highly respected personalities in Greek society. You can also recognize their position from the fact that, for example, the stone sculptor Phidias was such an influential politician that he prevailed in the people's assembly of Athens with a program he developed for the construction of the Parthenon .
Ancient Rome
The Romans essentially adopted the stone-working technique of the Greeks. Pieces of stone were removed from Greek buildings on a large scale and transported to Rome. The Roman stonemasons mainly worked soft stone, such as Roman travertine from Tivoli and volcanic tuffs from the Orvieto area ; until the 2nd century they mainly obtained marble from the island of Paros and only later used Carrara marble for more valuable work . There was a difference in stone processing compared to the Greeks: the closer they got to the end surface of the marble, the more they worked with the pointed iron at a shallow angle and finally used chisels for smoothing. In this workflow, the marble surface was not bruised as badly and consequently did not receive any undesired light individual spots, called bounces . In a final step, the marble surface of the valuable decorative and architectural sculptures could be perfectly ground and polished and shimmered transparently. Stone carving was of great importance. The Romans often copied stone busts of their emperors and other sculptures and brought them to the conquered lands as a demonstration of their power, which is why many copies of imperial portraits were made, which are now often exhibited in museums.
A society of builders already existed in the Roman Empire. These collegia fabrorum were run by an aedili , a building expert with the rank of a high official. All members had to prove a scientific and artistic education as well as virtue and righteousness. The stonemasons played an important role in Roman society as an important building participant and in 334 Emperor Constantine was so important to the building industry that he ordered all provincial prefects to set up schools in which the knowledge of architecture should be taught.
Pre-Romanesque and Romanesque

Roman soldiers brought stone architecture to Germania. The pre-Romanesque stone masons were monks or lay brothers and there were construction workers from the surrounding area.
They built monasteries, were closely tied to the weal and woe of the monasteries and were members of the monastery brotherhoods.
The Comacini from the Lombard Kingdom (568-774), who were referred to as Baurotten , played a special role during this period . They are considered to be the first construction workers who were involved in groups not only in Italy, but above all between 1050 and 1150 in numerous buildings in what is now Germany with their wickerwork and knotted columns, such as B. at the Romanesque domes of Freising , Königslutter , Mainz , Quedlinburg and Speyer .
In the Romanesque era , with the monastery brotherhoods, there were monks wandering from monastery to monastery as stone masons in groups for the first time. Romanesque builders are generally little known, although Günther Binding names a few in his standard work Baubetrieb in the Middle Ages . The Romanesque stonemasons invented a new stonemason tool, the surface .
Gothic
The Gothic articulated structure required a high level of accuracy in the fit of all the stones, so qualified stonemasons were needed to build the dome. In the Gothic there were three stonemason organizations: the so-called building huts on the domes, the traveling stonemason brotherhoods and the guilds . Only masters were organized in the stonemasons' guilds , in contrast to the huts and stonemason brotherhoods, which had their own stonemason regulations .
In addition to the bishops, who previously appeared as builders, cathedral chapters and city councils were added from the 13th century. The Gothic stonemasons were highly respected personalities; for the first time in history, craftsmen were able to freely change their jobs. Another feature of the enormous self-confidence of the Gothic stonemasons was that they stamped their personal stonemason marks into the Gothic stone . They were the highest paid craftsmen of the time.
The Gothic builders were stone masons, stone sculptors and at the same time planners and architects. The client made a first draft for a building. This was then made ready for implementation either by the responsible builder or together with another planner.
It was part of the self-image of the builders that they B. depicted with their stone portraits in the buildings. They are known by name and were able to design buildings according to their ideas with relatively great freedom from their clients.
The Gothic stonemasons converted the surface into a stone ax with a working width of approx. Three centimeters, which they mastered with virtuosity and which was called the pill . They also used the tooth iron for the first time in Germany . The typical stonemasonry tool of the Gothic, the chisel iron probably imported from France , was not used until the middle of the 15th century.
Renaissance
The bourgeoisie and the nobility had mainly secular buildings built in accordance with their interests , such as utility buildings for the citizens, castles and other representative buildings of the nobility.
The stonemasons of the Renaissance were entrepreneurs as masters or contract workers as journeymen. The relationship between client and foreman changed little. For example, Elias Holl could not resign as Stadtwerkmeister in Augsburg, while the city council could resign him at any time. On the one hand, the construction huts experienced an enormous loss of importance, on the other hand, stonemasons had the chance to pursue a career as city builder or at the royal courts with the increasing number of secular buildings.
During the Renaissance, a new type of master builder had developed who was trained in the craft and at the same time, in addition to his function as an architect, was also an entrepreneur. Master builder Elias Holl was the first to be a bricklayer and no longer a stonemason. In the Renaissance stonemasons invented a new soft stone tool, the crown .
Baroque and Rococo
The baroque style of construction introduced a fundamental change for natural stone. In some cases, pillars made of stucco marble and vaults as well as profiles made of gypsum stucco and, depending on the financial situation of the builder, stone parts were replaced by masonry or plaster.
Clients were princes and commoners. "Construction contracts were based on the cost estimate and construction plans, in which the client sometimes took a considerable part". Construction errors of the executing trades were punished up to the executing builder. Most of the builders in the Baroque and Rococo periods were bricklayers or stone masons, but there were exceptions, such as Balthasar Neumann , who was a gun and bell founder. For the first time there was a master builder training in France at state building schools. There was no such specialization in German-speaking countries, the builders learned from practical experience and from the master craftsman's books , in which the art of building was written down. The so-called Vorarlberg Building School, which dealt exclusively with sacred buildings, was an exception. The builders were craftsmen according to their training, but their main tasks were planners and organizers.
Classicism and Historicism
In the course of industrialization, the building of train stations, factories and villas of the rich bourgeoisie was in the foreground. Housing was needed in the cities for the workers and their families and rental housing was built. The advancing mechanization increasingly replaced manual labor with machines. Steam and water power as well as electrical energy completely transformed the manufacturing process.
A part of the manual work with natural stone could be replaced by machines in the time of classicism and historicism . Electrically driven stone saws and stone grinding machines made it possible to manufacture large quantities of ashlar from hard stone, which was very expensive until then. The manual individual production was replaced by series production with mechanical support.
In addition to the traditional builders from the urban, state and church sectors, there were industrialists and corporations. The builders were trained at state schools and no longer came from the craft. With the development of hard rock processing , the mallet was increasingly used.
Founding period
The industrial and residential construction for the wealthy citizens was in the foreground in the early days. Inhumane and unsanitary quarters were set up for industrial workers in back buildings and courtyards, which among other things led to social tensions. Both employer organizations and trade unions were founded . On June 18, 1870, after a strike in Berlin, the first collective agreement on wages and overtime was signed between the employers organized in a stonemasons 'guild and the Organization of Stone Workers ' union .
During the founding period , large stone industries with hundreds of employees were formed in German-speaking countries. For the first time, natural stones were divided with diamond-set saw blades stone saws ; In 1896 a plant in the Odenwald in Germany called sawmills, grinding and polishing machines with steam and water power advertised and offered as the largest specialty shop in Germany tombs and slabs made of granite and syenite .
How dynamic the economic development was not only in Germany can be seen in one of the largest natural stone factories in Austria today (2008) . The Poschacher natural stone plant, which opened a granite plant and a quarry in the Mühlviertel in Mauthausen in 1839 , already had 1,059 employees in 1872, who in 1890, for example, shipped 2700 m² granite ashlar stones 1800 kilometers on the Danube to Černá Voda in today's Czech Republic.
The economic development of Switzerland in the early days was closely linked to the development of the railway network, which was expanded from 1850. Huge quantities of stone were required for walls, bridges and tunnel cladding to build the route. Towards the end of the 19th century, there were over 700 stone quarries in operation in Switzerland. The economic upswing and industrialization, population and urban growth as well as the development of tourism and transport resulted in the construction of countless public and private buildings made of natural stone. Because of the strong demand, larger quantities of ashlar were also imported from abroad.
In the course of industrialization and the introduction of freedom of trade in 1871, there were stonemasons in the German-speaking countries that continued to see themselves as handicrafts, but also larger ones that were looking for industrial forms of organization. In an appeal in 1896, this problem was clearly formulated in Germany: "In addition to the purely craft-based businesses, as the master stonemason still represents, we have the factory with its machines, in which only a small proportion of the work is done by hand" .
In 1885, the Association of German Quarry and Stonemason Shops was founded in Berlin , in which 750 industrial and craft businesses with 40,000 employees were organized.
Nevertheless, the majority of the stonemasons remained handcrafted. Further industrial associations such as the Association of Granite Industrialists of the Fichtelgebirge with ten and in 1906 the Association of German Granite Grinding with 30 member companies were founded. The industrial association system was not only fragmented in Germany by individual interests, but there were similar association developments in Austria, Luxembourg and Switzerland.
In contrast to the technical advances of the Wilhelminian era, natural stone as a building material in its massive form was threatened with retreat for the first time in history for two reasons: firstly because of the use of steel structures and secondly because of the invention of reinforced concrete by Joseph Monier . As the dominant material, solid natural stone could be almost completely replaced by other materials.
20th century
Before 1933
In order to adapt to technical progress, the first state stonemason schools in German areas with large deposits of stone for training master stonemasons and stone carvers, stone technicians and apprentices, the state school for stone processing in Friedeberg (1886), the state school for stone processing in Saubsdorf ( 1886), the state college for stone processing in Wunsiedel (1901) and the stone cutting school in Demitz-Thumitz (1908) founded.
Some of the large industrial companies operated internationally around the turn of the century, such as Marmor-Kiefer AG, which, in addition to the types of marble that the company extracted in its own quarries, also used natural stones from "Austria-Hungary, Italy, Belgium, France, Spain, Greece, Sweden, England and Africa ”acted.
In 1913, the Association of German Quarry and Stonemason Businesses, which is now the Association of German Granite Works e. V. (VDG) called for a comprehensive organizational reform of the stone industry associations, which initially did not advance due to the beginning of the First World War . It was completed in 1916 with the establishment of the German Stone Industry Association , which was subdivided into five specialist groups according to stone , road construction , tombs , marble and granite .
After the end of the war (1918) the economic situation of the handicraft businesses was difficult, sales stagnated or fell. Individual stone industries were doing better, they were able to partially compensate for losses in domestic sales with foreign orders. Despite the generally unfavorable economic situation, they prospered, bought up factories and quarries, and increased their workforce.
The Art Nouveau with architectural decorations, ornamentation and plastic meant an increase in orders in the natural stone sector, the New Objectivity of the Dessau Building School , the development of artificial stone and the cemetery reforms, which resulted in fewer and fewer tombstones being sold, led to a drop in sales of 20 to 30 percent. Bases, casings of doors and windows and cornices on buildings made of natural stone were no longer built in or they were made of concrete. In 1929, buildings were faced with natural stone slabs for the first time as an alternative to using solid natural stone.
After the consequences of the Versailles Peace Treaty had been mitigated, domestic demand for natural stone rose in the Roaring Twenties (1924–1929), but with inflation and hyperinflation it fell again into the abyss. The world economic crisis, the rise of the National Socialists between 1929 and 1933 and the fall of the Weimar Republic resulted in agony.
After 1933
After taking power in 1933, Albert Speer planned gigantic stone structures as the leading Nazi architect and from 1937 as general building inspector for the Reich capital , including the world capital Germania (Berlin). This was linked to the hope of an increase in the demand for natural stone and an improvement in the economic situation, but also the adjustment to the political conditions, which in some reports about company anniversaries of the large stone processing companies of that time in the use of the National Socialist vocabulary and in illustrations of Stone work with swastikas was expressed. In anticipation of major stone construction projects, part of the stone industry formed a working group, the so-called ARGE Nürnberg. 1934 came through the so-called. Gleichschaltung of organizations by the National Socialist government to complete organizational separation of stonemasonry and stone industry, which was associated with the compulsory membership in professional organizations. Failure to attend meetings of the compulsory organizations was fined. A certain increase in construction activity and the 1937 model cemetery ordinance initially helped to improve the situation of the stone processing companies.
After the beginning of the Second World War it became clear that the stone processing companies and their products were not important to the war effort. The companies had to hand over personnel as soldiers, who were often deployed in engineer units, and also machines. Other machines and buildings were destroyed by the effects of the war. Individual stonemasons and companies were employed in the construction of traffic routes or behind the front lines as part of the Todt Organization , a military construction organization.
After 1945
After the end of the war in 1945, the economies of Germany and Austria fell into disrepair. The German stonemasonry and the stone industry were particularly affected. In the east, dominant industrial companies were expropriated and reorganized into new structures; the stonemason trade remained private and almost exclusively marketed tombs. The largest German stone industry company Zeidler & Wimmel lost 80 percent of its works and quarries in the east.
After the currency reform in 1948 , the situation of the economy and also of the stone processing companies in western Germany visibly improved. The regional guilds of the stonemasonry trade with the umbrella association Federal Guild Association of the German stonemasons, stone and wood sculptors and the industrial German natural stone association e. V. resumed their association work at the end of the 1950s. Today (2008) both associations work together in the Central Association of the Natural Stone Industry (ZDNW) . In the east of Germany, the stonemason trade was organized in 16 district specialist groups and in large stone industrial units, such as VEB Elbe-Naturstein . After reunification, the stonemasons of the east formed handicraft organizations based on the German model and the stone industries joined the Deutscher Naturwerkstein-Verband e. V. at.
The economic development in Austria was not as slow after the war as in Germany, because the war damage was less. As in Germany, the stonemasons' associations were divided into a craft organization, the federal guild of stonemasons , and the industrially oriented Association of Austrian Natural Stone Companies (VÖN) .
The development in Switzerland with the Association of Swiss Master Sculptors and Stonemasons (VSBS) and the Industry Association of Swiss Natural Stone Producers (SNP) was similar .
Today's fields of activity
The material that stonemasons work today is mainly natural stone.
Since the 1950s, the profession of stone mason and stone sculptor has been divided into the following fields of activity:
Tombstones
An essential field of activity of the stonemasons and stone sculptors is the production and moving of gravestones . In the last few decades a differentiation has developed among customers: There are customers who mainly order personal tombstones, and others who have industrially mass-produced gravestones inscribed and erected.
There is more industrially manufactured demand in rural areas and more personal demand in large cities. Industrially manufactured tombs are mainly imported from abroad (India, China).
When inscribing both forms of tombs, the design eye and the skilled hand of the stonemasons are of great importance. Here, however, the computer-aided writing has found its way. Ornamental design plays a major role in both forms of tombs .
The tomb culture and thus the number of newly erected stone tombs has undergone major changes in recent years (anonymous burials, cemetery , cremations, etc.). The number of newly erected stone tombs is declining. From 1991 to 2006 it fell in the Federal Republic of Germany from approx. 400,000 to 200,000.
buildings
Natural stone is also in demand in the construction industry as an essential area of this trade.
- Natural stone stairs are produced and moved as decking, bolted and solid stairs. In the production of coiled stairs and staircases software is used that is not only designed but also stone saws controls that saw out the polygonal stairs stone tranches.
- The demand for natural stone floor coverings has increased significantly in recent years. The stone floor coverings enjoy increasing demand as natural stone slabs with a thickness of 1.5 to 2 cm or as natural stone tiles with 1.0 cm, since sustainability (low energy consumption in the extraction and manufacture of natural stone) in addition to cost reduction (with granite cost reduction of around 40 percent in recent years through imports) of natural stone stimulated customer demand.
- Window sills made of natural stone are particularly preferred by private builders for interior design.
- Kitchen worktops , bathrooms and washbasins made of natural stone are in high demand in the upscale interior design of private households.
- Façades made of natural stone, which are ventilated, convince with sustainability and diverse colors, especially in large building projects. The advantage of the facade design with natural stone lies above all in the positive energy balance with the appropriate construction. The natural stone slabs are attached to the construction substrate using stainless steel anchors. There is a layer of air between the thermal insulation and the facade panels.
- Open fireplaces made of natural stone in interior construction serve as decoration and contribute to comfort.
- Natural stone walls as road structures as well as house and boundary walls have recently been built frequently.
Monument preservation and stone restoration
The restoration of historical buildings with modern or stone conservation methods (e.g. Frauenkirche Dresden ) is a third field of activity of the stonemasons and stone sculptors. Mainly stonemasons with a specially qualified workforce have specialized in this work.
Garden design with natural stone
An increasing demand for the design, especially by owners of private gardens, for garden walls , sculptures , fountains and bird baths made of natural stone can be observed.
Stone carving
Both free stone carving and reconstruction in the context of monument preservation are a field in which companies and individual stone sculptors have specialized.
band Aid
Paving stone, offered by individual stonemasons' businesses, are a marginal field of stonemasons. The paver is a separate apprenticeship.
Road, path and bridge construction
Natural stone has been used here since time immemorial. Granite sideboards last longer than concrete. Facing of bridges and street walls are also made of natural stone, mostly regional stone deposits are used. This work is mostly carried out by road construction companies.
Peripheral areas
There are so-called sandstone wallpapers in millimeter thickness, high-quality fittings made of natural stone in luxury cars, natural stone foils behind glass (partially transparent), natural stone as a measuring table base, etc.
Stonemason training in Germany, Austria and Switzerland
The apprentices' stonemason training takes place in Germany as well as in Switzerland, Austria and Luxembourg in the dual system. This means that the skills are taught in the company and in inter-company training, the theory in the vocational school.
What is remarkable for one of the so-called “male professions” is that the proportion of women in the Federal Republic of Germany in 2011 was 13.9 percent. In 2008 it was 15.0 percent. An estimated 10 and 12 percent of apprentices in Germany today are female. There are probably significantly fewer female stonemasons who work in the profession, as some of the female apprentices go other ways after completing their vocational qualifications or, for example, take up a degree (architecture, art, etc.). In addition, women more often choose stone sculptors and not stone masons before the start of their third year of training. You will then find work primarily in companies that deal with design topics such as font design and ornaments or that pursue a handicraft orientation.
Germany
Apprenticeship training
Stonemason is a skilled tradesman in Germany . The training lasts three years and ends with the production of a journeyman's piece as well as a theoretical and practical exam. In 2007 there were around 1400 apprentices at around 5000 artisanal stonemasons.
In the profession, a distinction is made between the two fields of stonemasonry and stone sculptor . In the first two years of training, stonemason and stone sculptor have the same training content. In the third year of training, the specialization takes place, which is then subject-related in a journeyman's piece (today called "examination piece 1", which the examinee can freely choose) and in a work sample (today "examination piece 2", which is thematically given to the examinee by the examination committee) as Final exam ends. Simplified one can say that the sculptor plastic pieces of stone (stone figures, free art of stone) formed the measurement tools like angle and folding rule escape, the stonemason worked workpieces (massive chocks, grave times) that can be measured.
There is also the apprenticeship as a natural stone mechanic with approx. 60 trainees in approx. 130 stone industries. This industrial occupation is divided into three areas. The skilled worker examination includes the grinding technology, the stonemason technology and the machine technology area. There is a similar training path in Switzerland.
Further training to become a stonemason in monument preservation
In a one-month training course, apprentice stonemasons and stone sculptors can train to become journeyman in monument conservation . This course is only available in Germany.
Master training
Immediately after passing the journeyman's examination, a journeyman can train himself further in the craft and visit training facilities that conclude with a master craftsman's examination before an examination committee of the Chamber of Crafts. In Germany there are the following training courses for master stonemasons and stone sculptors (listed here from north to south): Königslutter (Lower Saxony), Demitz-Thumitz (Saxony), Soest and Düsseldorf (North Rhine-Westphalia), Mainz and Kaiserslautern (Rhineland-Palatinate), Wunsiedel , Aschaffenburg and Munich (Bavaria) and Freiburg (Baden-Württemberg). In Germany, these two professions, the stonemason and the stone sculptor, can be taken in a master craftsman's examination. It doesn't exist in other countries.
With a master's degree, access to university studies in the federal states of Hesse and Lower Saxony is possible; also to study at a university of applied sciences in North Rhine-Westphalia.
After completing an apprenticeship as a state-certified stone technician, the master's examination can be taken in parallel at the above-mentioned locations .
Stone restoration training
After successfully completing the master's degree in stone masonry and stone carving, there is the opportunity to train as a restorer in stone masonry and stone carving in courses recognized by the German Association of Stone Masons and Stone Carvers in Wunsiedel or in Königslutter. This title is protected, it is neither offered nor recognized in Austria or Switzerland.
Switzerland
Apprenticeship training
The practical apprenticeship training to become a stonemason takes place in a recognized training company. It is supplemented by attending the vocational school - one day a week. There are also inter-company courses . There is also the possibility of attending the vocational school. In Switzerland there are four professional disciplines, stonemason , stone sculptor , stoneworker and marbleist .
This is an essential difference to the German training system with three-year apprenticeship training; After an identical two-year basic training course for stonemasons and stone sculptors, a two-year specialization follows, separated by the two disciplines. Training in these two fields in Switzerland therefore takes four years.
There is also the apprenticeship as a marble and stone worker. While the marbleists mainly machine design elements from natural stone, the stone workers mainly machine work pieces for buildings. Both training courses last three years. The apprenticeship as a stonemason corresponds roughly to the industrial natural stone mechanic in Germany.
Master training
The following are required for the master stonemason or master stone sculptor examination: a completed apprenticeship as a stone mason, stone sculptor or an equivalent qualification as well as four years of professional experience, whereby the attendance of technical schools is counted towards the practical activity. A higher technical examination (HFP) is connected with the master’s examination . With this degree, the right to study architecture or engineering is acquired.
Special preparation courses for the master craftsman's examination, separated by stonemason and stone sculptor, are set up in St. Gallen, for example, as required.
Austria
Apprenticeship training
In Austria, stonemason is a three-year apprenticeship with dual training. The training to become a stone sculptor is carried out according to the job description of stone and wood sculptors . There is also a four-year technical college education with the option of completing an additional two-year advanced course with a Matura as a skilled worker and natural stone technician or structural engineer.
Master training
The preparation for the master craftsman examination in Austria can take place in special courses. With the completion of this examination, the qualification as a terrazzo and artificial stone manufacturer is connected. With a master's degree, students can begin studying at universities in Austria.
Project: European Master of Craft
In a European project, ten apprentice stone masons and stone sculptors have been sent on a European tour since mid-2006, after which they will receive the title of European Master of Craft . The training locations are cathedral huts in Switzerland, Germany and Austria, as well as stone technical schools in South Tyrol (Italy), Hallein (Austria), Brač (Croatia). Furthermore, specialist companies from the extraction and processing of natural stone in Slovenia, Croatia and Austria are involved as training centers.
Occupational diseases and preventive occupational health care
Stonemasons are subject to the following health hazards in the exercise of their occupation, which can be identified by occupational health check-ups (every three years) or by the company doctors or can be excluded by taking appropriate operational measures:
- Exposure to silicogenic (quartz-containing) fine dust can lead to silicosis or silico-tuberculosis and is minimized through the use of suction devices.
- Exposure to noise is avoided by soundproofing tools and equipment and by wearing personal protective equipment. Otherwise hearing damage can occur.
- The load caused by recoil vibrations from hand-held vibration tools ( pneumatic hammers, percussion and hammer drills ) is minimized by special vibration-minimizing chisel protection attachments and vibration-insulated pneumatic tools. If no precautions are taken, the result can be what is known as white finger disease , which manifests itself in circulatory disorders in the hands.
- The load on the hands with cements , to cement scabies can lead is limited by wearing rubber gloves
- The wear of the teeth during the most intensive processing of hard stone, especially in quarries with a lot of dust, can be prevented by wearing a face mask.
- The wear and tear of the spine in the case of incorrect posture and excessive stress when manually setting up the stone can be minimized by using lifting equipment.
The above diseases are recognized as occupational diseases by the professional associations .
Modern and traditional craft
The stonemasonry and stone carving trade is now a modern craft that is aware of its traditions.
The manufacture and design of the stone surfaces that are visible is of great importance for the stonemasonry.
Use of modern technology
Computer and CNC- controlled machines have found their way into the factories . These include circular stone saws with saw blades up to four meters in diameter, which are used to cut stones, and gang saws , which use up to 80 saw blades to cut large blocks of stone into slabs. So-called disks, pieces of metal with small diamonds in them, can be soldered onto the edges of the saw blades. So-called bridge saws form workpieces that are installed as facade, kitchen worktop and floor panels as well as window sills and washbasins. The bridge saws are computer controlled; the drafts of the stones to be produced are made with CAD support . Filigree stone inlays are made with water jet cutting machines that are connected to computers and work with pressures of up to 4000 bar. In stone processing companies, wire saws are used, which cut contours into stones or saw stone fragments out of raw blocks.
Automatic or semi-automatic stone grinders do monotonous work. Using laser technology , natural stone floor panels are made non-slip.
Since the stones have a considerable weight, there are special equipment for stone transport in addition to cranes and forklifts for natural stones .
Use of traditional hand tools

Before stonemasons work on a workpiece, they use the sound test to check whether it is suitable for the work. The sound test is a historical stone processing method that has been used for centuries.
The tools of the stonemason and stone sculptor for processing the raw stone are either made of tool steel or they have hard metals soldered into their cutting edges or tips, which are called widia irons . The tool equipment that stonemasons use for manual surface and profile work is what they call crockery . They are mostly traditional hand tools.
- The stone blocks extracted in the quarry used to be roughly worked. This processing is called bossing . On the work place, the stone made of soft or hard stone was further processed by hand with stone cutting tools . Nowadays (2008) mostly hand-operated machines or equipment are used instead of hand tools.
- Air hammers are mainly used to hammer in writing and to create stone surfaces or profiles. Basically, all work steps carried out with tools operated by compressed air can also be carried out by hand. The time required is usually greater for manual work. Certain work steps, such as the production of scratched surfaces , can only be carried out optimally with hand tools.
- Hand machines are used to facilitate manual labor. These are electric or pneumatic or oil-hydraulic hand grinders and electric or pneumatic angle grinders , which are also called Flex.
Stonemason tradition and its care
Stonemason tradition
Many of the stonemason's traditions go back to the construction huts and stonemason brotherhoods of the Middle Ages. The Bauhütte was the major church construction site on site and the stonemason brotherhood was the supraregional organization of the Bauhütten stonemasons. Both organizations can be distinguished from the guild , an organization made up only of master craftsmen, and the guild , an organization made up of merchants.
Stonemason tradition care
The stonemasons are one of the few professional groups in today's handicraft who maintain their traditions. There is no uniform guild clothing, but some of the employees attach importance to wearing the blue apron , an old professional identification symbol of the stonemasons and stone carvers.
Traditional rudiments from the Middle Ages can be found in the stonemasonry: a stonemason is asked to cooperate with colleagues according to the traditional tradition with "addressed". After the end of the help, he is said goodbye with a "thank you".
As in the Middle Ages, stonemasons call a stone that was unsuccessful in its work a Bernhard or Totenbernhard , who in the Middle Ages was ritualized buried in a funeral procession in the churchyard. Today there is the mockery of work colleagues for unsuccessful workpieces. In addition to masonry huts, such as B. next to the Dombauhütte Regensburg, there are often strangely overgrown corners in which half-buried stones protrude from the earth.
Some young stonemasons practice a special form of cultivating tradition. As they used to be, they are wanderers in Europe and recently also overseas.
Stonemason patronage
The patron saints of the stonemasons are Roman stonemasons called Quattuor Coronati (Four Crowned) who refused to make a statue of a Roman deity, Aesculapius , in the time of Emperor Diocletian in Dalmatia in 302 . They were tortured and had a crown of thorns pressed onto their skulls, only to be drowned in lead coffins in the Sava. The patronage festival of the four crowned guilds and stonemasons is sometimes celebrated on November 8th.
Stonemason's mark
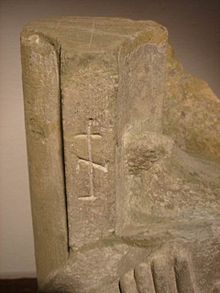
The Steinmetz mark is a generally geometric or ornamental, predominantly mono grammatical characters as personal Signum a masons, which facilitated the settlement of stonework in the Middle Ages, or as a personal label was used.
Stonemason's marks appeared in advanced civilizations and in antiquity , but did not become generally used until the late Romanesque period. In the Gothic period , every stonemason, as a member of a construction hut, had a personal stonemason's mark. These signs are based on the signs of the Bauhütte and differ only slightly from them. The stonemason's marks relate to geometric constructions such as triangulature , three-pass , quadrature and quatrefoil . In late Gothic buildings in particular, a large number of stones, especially complex workpieces, often have a mark. The leading masters put their mark, the so-called master’s mark, on a coat of arms.
The stonemason's mark is still given today by some traditionally oriented guilds (for example in Hesse) at journeyman's acquittal celebrations.
Personalities with stonemason training
There are a number of well-known personalities who have completed training to become stonemasons. This is mostly not known. Some personalities are named below:
- Socrates : Greek philosopher, son of a stonemason, very likely also received this training
- Parler : Family of cathedral builders in the Gothic period: Peter , Wenzel and Johann the Younger
- Joseph Uphues (1850–1911): apprenticeship as a stonemason in Wiedenbrück
- Günter Grass : (writer, painter and sculptor); 1947–1949 apprenticeship as mason in Düsseldorf
- Ulrich Rückriem : Sculptor, 1957–1959 apprenticeship as a stonemason in Düren
- Franz-Josef Kniola : former interior and building minister of North Rhine-Westphalia; 1981 master mason examination
- Boy Lornsen (1922–1995): writer and master stonemason and stone sculptor (Keitum)
- Emil Cimiotti (professor emeritus at the University of Fine Arts Braunschweig): 1946–1949 apprenticeship as a stonemason
- Gustav Seitz (sculptor): (1922–1924) trained as a stone mason and stone sculptor in Ludwigshafen
- Paul Dierkes : Professor of wood and stone carving at the University of Fine Arts in Berlin
Others
On April 21, 1856, Australian stonemasons successfully struck worldwide for the first time on the construction site of the University of Melbourne for the eight-hour day with full wages, which led to legal recognition.
Natural stone paving used to be made by stone judges .
literature
Technical literature on the history of stone masons
- Max Hasak: Did stonemasons build our medieval cathedrals? Ernst, Berlin 1895.
- Carl von Heideloff (Ed.): The construction works of the Middle Ages in Germany. Nuremberg 1844.
- Ferdinand Janner, The construction huts of the German Middle Ages. Leipzig 1876.
- Louis Schwarz: The German construction huts of the Middle Ages and the explanation of the stonemasons. 1926.
- Eugen Weiß: stonemason and stonemason spirit. Diederichs, Jena 1927.
- Rudolf Wissell : The old craft law and custom. Wasmuth, Berlin 1929.
- Bettina Schmitz : The stones of the pharaohs, from quarry to work of art. Deposits. Materials. Workpieces from ancient Egypt. Information on the subject of "Stone among the ancient Egyptians". Where did they get the material from, how they processed it, what they made from it. In: Information and introductions for museum visitors. Edited by Pelizaeus Museum Hildesheim, Hildesheim 1985.
- Rosemarie Klemm , Dietrich Klemm : The stones of the pharaohs. Edited by the State Collection of Egyptian Art, Munich 1981.
- Egypt's rise to world power. ed. v. Raemer-Pelizaeus-Museum, Zabern, Hildesheim 1987, ISBN 3-8053-0966-X .
- Karl Friederich : Stone processing in its development from the 11th to the 18th century. Augsburg 1932. (Reprint of the original edition, Ulm 1988)
- Gustav Keßler: History of the organization of stone workers in Germany. Posekel, Rixdorf 1897.
- Festschrift: 175 years of Zeidler & Wimmel . 1951.
- Marble Industry Kiefer (Ed.): Marble Industry Kiefer 1883–1908, memorandum on the development of the joint stock company for marble industry Kiefer in Kiefersfelden in the first 25 years of its existence. Bruckmann, Munich.
- Carl Blümel , Greek sculptor at work. 2nd Edition. Walter de Gruyter, Berlin 1941.
- 100 years of associations of the natural stone industry, natural stone, claim and obligation. Edited by German Natural Stone Association V., Marktheidenfeld 2000.
- Anja Sibylle Dollinger: Construction Management and Construction Technology - From Pre-Romanesque to Historicism. In: Natural stone and environmental protection in monument preservation. Edited by the vocational training center for stone masons and sculptors, Ulm 1997, ISBN 3-87188-143-0 .
General and educational specialist literature
- Frieder Bernhard: The stonemason and stone sculptor. Training and practice. Volume 1. Callwey, Munich 2001, ISBN 3-7667-1145-8 .
- Vocational training center for the stonemason and stone sculptor trade (ed.): The work on stone (= The stone mason and stone sculptor. Volume 2). Callwey, Munich 2003, ISBN 3-7667-1330-2 .
- Richard Thiele: Stone carving in architecture. Fachbuchverlag, Leipzig 1957.
- Theodor Krauth, Franz Sales Meyer (Ed.): The Steinhauerbuch. The stone mason's construction and art work. Schäfer, Hannover 2001, ISBN 3-88746-021-9 . (Reprint based on the original from 1896)
- Hans Issel: The stonemason. The construction technician's manual 15, edit. by A. Opderbecke and H. Wittenbecher. (Reprint of the original from 1905)
Trade journals
- Natural stone (Ebner Verlag)
- Stein ( Callwey Verlag )
Popular literature
- Erich Maria Remarque : The black obelisk . Kiepenheuer and Witsch, Cologne 1998, ISBN 3-462-02725-5 . (First published in 1956)
- Siegfried Lenz : The sound test . Hoffmann and Campe, Hamburg 1990, ISBN 3-455-04249-X .
- Ken Follett : The Pillars of the Earth . Lübbe, Bergisch Gladbach 1990, ISBN 3-7857-0577-8 .
Web links
- Federal Association of German Stonemasons, Stone Sculptors and Wood Sculptors
- List and illustrations of German natural stone
- Baumberger Sandstone Museum in Havixbeck
- Steinmetzmuseum Kaisersteinbruch
- Professional and industry information from the Austrian Chamber of Commerce
Individual evidence
- ↑ Duden: The dictionary of origin , 5th edition 2014, p. 816
- ↑ Bettina Schmitz: The stones of the pharaohs. P. 5, see Ref.
- ↑ Rosemarie and Dietrich Klemm: The stones of the pharaohs. P. 34 ff., See Ref.
- ↑ Carl von Heideloff: The Bauhütte. P. 3, cit. n. Alfred Schottner: Das Customs , p. 15, see Lit.
- ↑ Egypt's rise to world power , p. 146, see lit. In the museum catalog two bronze chisels and a wooden club are shown
- ↑ Carl Blümel: Greek sculptor. P. 72, see Ref.
- ↑ Carl Blümel: Greek sculptor. P. 62, see Ref.
- ↑ Ferdinand Janner: The construction huts of the Middle Ages. P. 5f. Carl von Heidloff: Die Bauhütten , p. 3, quoted. n. Alfred Schottner: Das Customs , p. 15, see Lit.
- ↑ Alfred Schottner: The Customs. P. 15, see Ref.
- ↑ a b Alfred Schottner: The Customs. P. 16, see Ref.
- ↑ Karl Friederich, Die Steinverarbeitung , p. 38 ff., See Ref.
- ↑ Alfred Schottner: The Customs. P. 17 ff., See Ref.
- ↑ Alfred Schottner: The Customs. P. 16 ff., See Ref.
- ^ Karl Friederich: The stone processing. P. 36 ff., See Ref.
- ^ Anja Sibylle Dollinger: Construction and construction technology. P. 187 ff., See Ref.
- ^ Karl Friederich: The stone processing. See ref . Fig. 101 is remarkable, as it mentions the toothed iron in the illustration text and also shows toothed iron traces. Amazingly, Friederich does not go into any part of the book about the historical use of the toothed iron in Gothic.
- ^ Karl Friederich: The stone processing. P. 66 ff., See Ref.
- ^ Anja Sibylle Dollinger: Construction and construction technology. P. 211, see Ref.
- ^ Karl Friederich: The stone processing. P. 74, see Ref.
- ^ Anja Sibylle Dollinger: Construction and construction technology. P. 225, see Ref.
- ^ Anja Sibylle Dollinger: Construction and construction technology. P. 228, see Ref.
- ↑ Anja Sybille Dollinger: Construction and construction technology. P. 243, see Ref.
- ↑ Gustav Keßler, History of the Organization of Stone Workers in Germany, p. 92 ff., See Lit.
- ↑ 100 years of associations, p. 7, see Ref.
- ↑ Cultural history of the Mühlviertel
- ↑ Steinmetz , Zeitschrift für Naturstein, 6/1984, p. 52.
- ↑ 100 Years of Associations, p. 4 ff., See Ref .
- ↑ Marble Industry Kiefer, p. 15f, see Ref.
- ↑ Festschrift: 175 years of Zeidler & Wimmel. P. 16, see Ref.
- ↑ 100 years of associations , p. 16, see Ref.
- ↑ Steinmetz + Steinbildhauer , 6/1984, p. 84 ff.
- ↑ Festschrift: 175 years of Zeidler & Wimmel. P. 28, see Ref.
- ↑ Stein, Zeitschrift für Naturstein, 2/2007, p. 2.
- ↑ Frauenkirche Dresden. In: VOGEL Steinmetz- & Bilhauerwerkstätten Vogel GbR. Retrieved on July 2, 2019 (German).
- ^ Gerhard Syben: Further training in the stonemason trade , on bbw-steinmetz.de. Retrieved September 11, 2016
- ↑ Job profile and journeyman's examination regulations for stonemasons and stone sculptors in Germany ( Memento of the original from March 8, 2005 in the Internet Archive ) Info: The archive link was inserted automatically and has not yet been checked. Please check the original and archive link according to the instructions and then remove this notice. (PDF)
- ↑ Job profile and master craftsman examination regulations in the stonemasonry and stone carving trade in Germany ( page no longer available , search in web archives ) Info: The link was automatically marked as defective. Please check the link according to the instructions and then remove this notice. (PDF)
- ↑ Further training examination regulations for restorers in the stonemasonry and stone carving trade in Germany ( page no longer available , search in web archives ) Info: The link was automatically marked as defective. Please check the link according to the instructions and then remove this notice. (PDF)
- ↑ Archive link ( Memento of the original from October 16, 2013 in the Internet Archive ) Info: The archive link was inserted automatically and has not yet been checked. Please check the original and archive link according to the instructions and then remove this notice.
- ↑ Archived copy ( memento of the original from October 16, 2013 in the Internet Archive ) Info: The archive link was inserted automatically and has not yet been checked. Please check the original and archive link according to the instructions and then remove this notice.
- ↑ Archived copy ( memento of the original from October 16, 2013 in the Internet Archive ) Info: The archive link was inserted automatically and has not yet been checked. Please check the original and archive link according to the instructions and then remove this notice.
- ↑ Archive link ( Memento of the original from October 16, 2013 in the Internet Archive ) Info: The archive link was inserted automatically and has not yet been checked. Please check the original and archive link according to the instructions and then remove this notice.
- ↑ vsbs.ch ( page no longer available , search in web archives ) Info: The link was automatically marked as defective. Please check the link according to the instructions and then remove this notice. : Education plan for the regulation on basic vocational training. Occupational field stone processing from October 16, 2009 (as of January 9, 2012) , accessed on July 19, 2012
- ↑ Stone and wood sculptor journeyman's examination regulations in Austria
- ↑ Steinmetzmeister examination regulations in Austria ( page no longer available , search in web archives ) Info: The link was automatically marked as defective. Please check the link according to the instructions and then remove this notice.
- ↑ Our Proud Past ( Memento of the original from September 21, 2013 in the Internet Archive ) Info: The archive link was inserted automatically and has not yet been checked. Please check the original and archive link according to the instructions and then remove this notice. (English). In: cfmeuvic.com.au, accessed April 9, 2015
- ↑ Hans Dietzer Nüdling: Rhönbasalt: Development - Mining - Geotopes , Parzeller, Fulda 2006, p. 117