Ruhr mining
The Ruhr mining industry describes the coal and ore mining in the Ruhr area , which can look back on centuries of history.
Currently (2019) only rock salt is promoted on the edge of the Ruhr area.
geology
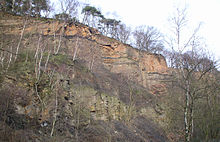
Already at the beginning of the mountain formation ( Variscan orogeny ) 400 to 300 million years ago in the south of today's Ruhr area during the Devonian and Carboniferous periods magma rose from tectonic faults , creating ore deposits.
At the same time, a subsidence set in north of the high mountains. There, over millions of years, the landscape alternated again and again between a flat sea, the formation of river deltas and silting up due to eroded sediments from the high mountains. This resulted in extensive moors in the warm, humid climate of the Carboniferous, which were covered by sediments and thus caused the carbonization of the plant material. Up to the current depth of around 3000 meters, hundreds of coal-bearing layers were created , of which around 75 seams reach minable thicknesses of one to a maximum of three meters. As a result of the subsidence, the seam-bearing layers sink in at around six degrees to the north today. On the southern edge of the Ruhr area near Witten , for example, the coal reaches the surface of the earth, while at Marl, for example, on the northern edge of the Ruhr area, it is around 700 meters deep.
Ore mining
In the ore deposits of the Ruhr area, iron ores such as red iron ore , clay iron stone and lawn iron stone , but above all coal iron stone (so-called black band ) were mined for steel production. Other ores such as pyrites , cobalt , lead , zinc , silver and copper were also extracted in small quantities .
At the Auguste Victoria colliery , lead-zinc ore deposits were discovered in 1938 in the “William-Koehler-Gang” and also mined during the self-sufficiency efforts of the Third Reich. In the 1950s, around 20 percent of German ore production was mined at the Auguste Victoria colliery (1956: 349,000 tons of ore). In 1962 the mining was stopped after it had become uneconomical.
Rock salt
A large salt deposit was found in 1897 in Borth (today part of Rheinberg ) on the edge of today's RVR during test drilling for coal . This has also been mined underground since 1924. The Borth salt mine is now the largest salt mine in Europe and the last mine in the Ruhr area.
Hard coal mining
history
Workforce in Ruhr mining | ||
year | Workforce | Production in million t |
---|---|---|
1820 | 3,556 | 0.41 |
1830 | 4,457 | 0.549 |
1840 | 8,945 | 0.96 |
1850 | 12,741 | 1.96 |
1860 | 28,657 | 4.3 |
1865 | 42,450 | 9.3 |
1870 | 50,749 | 11.8 |
1875 | 83.134 | 17.0 |
1880 | 80,309 | 22.5 |
1885 | 102.292 | 29.0 |
1890 | 127.794 | 35.5 |
1895 | 154,702 | 41.3 |
1900 | 228,593 | 60.1 |
1905 | 273.184 | 66.7 |
1910 | 353,347 | 89.1 |
1912 | 374.041 | 102.8 |
1913 | 444.406 | 114.2 |
1915 | 295.993 | 86.5 |
1918 | 350.282 | 95.7 |
1920 | 473,468 | 88.1 |
1923 | 42 | |
1925 | 459.876 | 104.3 |
1927 | 118.0 | |
1929 | 123.6 | |
1931 | 85.6 | |
1932 | 221.096 | 73.2 |
1934 | 90.4 | |
1936 | 107.5 | |
1938 | 355.084 | 127.2 |
1940 | 355.084 | 129.2 |
1942 | 128.5 | |
1943 | 127.5 | |
1944 | 110.8 | |
1945 | 276.192 | 33.3 |
1948 | 401,671 | 81.1 |
1953 | 480,806 | 115.5 |
1956 | 484.986 | 124.6 |
1957 | 123.2 | |
1960 | 408.049 | 115.4 |
1965 | 316.114 | 90 |
1970 | 198.943 | 91.1 |
1975 | 161.113 | 75.9 |
1980 | 141,808 | 69.1 |
1985 | 125,824 | 64 |
1990 | 100,949 | 54.6 |
1995 | 72,483 | 41.6 |
1997 | 37.2 | |
2000 | 48,679 | 25.9 |
2002 | 26th | |
2008 | 14.5 |



The beginnings
According to legend, a boy in the area of Witten , Sprockhövel or Wetter found glowing black stones in a fireplace while herding pigs . Coal was mined here in simple burial holes ( pinging ) as early as the Middle Ages . The focus of this early coal mining was in the Witten-Sprockhövel- Haßlinghausen area , where the coal seams reach the surface. In the beginning, the farmers mainly used coal for their own needs. The coal mining took place as far as the agricultural activities allowed it.
This free coal trench could be preserved until the landlords recognized the economic use of the raw material. Charlemagne covered his imperial territory with castles and fortresses and deployed service men ( ministrals ) to secure the area. The farmers had to pay the rulers in kind and when the possibilities of economic exploitation of coal were recognized, the farmers were forbidden to use free coal. As part of the Bergregal , the mineral treasure was placed under the ownership of the rulers. The coal mining took place under the direction of the rulers or the peasants were allowed to mine , but a large proportion of the coal extracted had to be delivered to the sovereign.
Due to the proximity to the important customers in Schwelm , Ennepetal , Hagen and the Wupper area , the germ cells of the Ruhr mining industry are to be found in Sprockhövel and Wetter . These pings were operated until the rising groundwater prevented further coal extraction .
The first coal mining for Dortmund is documented in 1296 near Haus Schüren . The coal extracted here was mainly taken from the salt works in Unna (see Königsborn salt works ). In 1439 Adolf II von Berg granted Johann Schüren the coal privilege. The coal was used in forges or as domestic fuel.
The unregulated coal mining resulted in considerable damage to the fields, and the first attempts at regulation were made in the 16th century, but were unsuccessful. In addition to the free trench was already late medieval tunnels mining operation, in which on several soles coal was mined. The soles were connected by shafts with a rectangular cross-section . Mining in Schee near Sprockhövel was first mentioned in a document in 1547 . A tunnel at Schlebusch in Wetter is occupied for around 1552 . In 1566 the first mining cooperative was formed in Bredeney .
By 1700 there was already shooting , blasting with black powder . A list from 1737 recorded 105 collieries with a total of 688 miners in the county of Mark .
Direction principle
On behalf of the "General-Ober-Finanz-Kriegs- und Domainen-Directorium" reports on coal mining in the county of Mark were made in 1734/35. In order to secure tax revenues from coal mining, the policy of the Prussian state aimed to exert extensive influence on coal production. The opening and closing of mines was determined by state authorities. Management and remuneration were set by the state. This form of state regulation is known as the principle of direction . Mining offices were set up for the administration at the mining locations and mining ordinances regulated the operation of the mines. In 1738 the Märkisches Bergamt was opened in Bochum . The first mine separators began their work in the county of Mark. Large-scale maps were made by the Markscheider and Mining Authority Head Johann Friedrich Niemeyer (1759–1814) and Johann Ehrenfried Honigmann (1775–1855).
Shortly before the Seven Years' War , King Friedrich II commissioned Ludwig Philipp Freiherr vom Hagen and Johann Friedrich Heintzmann to inspect the Ruhr mining in 1755 and on April 29, 1766 issued the Revised Mining Regulations for the Duchy of Cleve , the Principality of Meurs and the County of Mark , because he whose importance for the war industry and the mercantilism had recognized.
In the beginning, the seams lying on the surface were excavated until the groundwater penetrated into the depressions. In the 17th century there was a change to targeted coal mining in the form of tunnel mining. The tunnels were driven into the mountain in valley cuts, mostly river valleys, in order to be able to mine the coal above the tunnel mouth hole . At the deepest point, a tunnel with a constant gradient to the mouth hole was driven into the mountain, which had the function of draining the pit water at the lowest possible point. These tunnels were called hereditary tunnels ; A certain proportion of the coal that was extracted in the drainage area had to be carried away to the owner of this tunnel. Hereditary tunnels are still preserved on the Ruhr in the area of Witten and Bochum. The mouth holes of these tunnels are only slightly above the level of the river. In the Muttental (Witten), the surface structures of some of the tunnels have been restored ( Muttental mining trail ). In 1754 there were 20 mines in Bochum with a total workforce of 114 people, so that mining was not yet of any significant economic importance at the time.
Freiherr vom Stein , who was appointed director of the Märkisches Bergamt in 1784, had a particular influence on the political framework for mining. He made extensive trips to the domestic and foreign mining districts. The tightening of the management principle by the revised Clever-Märkische Bergordnung went back to his suggestions. It led to a streamlining of the accounting system and a joint management of the companies with senior managers and senior shift masters. Freiherr vom Stein had an influence on the use of the steam engine , the improvement of the marrow separation system and the use of new mining methods.
The Ruhr had several barrages in the 18th century that had been created by mill owners, fishermen and manufacturers. In 1735/36 Bergrat Decker recommended making the river navigable and using it to transport coal. In 1749 the Prussian government issued a license that allowed shipping. This only applied to the Prussian state area. The different interests of the states in the course of the Ruhr initially prevented a targeted implementation of the plans. The cargo bags had to be reloaded at the barrages, which was a laborious process. In 1776 the aim was to make it navigable throughout. In 1780 the last of sixteen Ruhr locks commissioned by Prussia was completed, and the river was navigable from Duisburg to Langschede . The lock chambers were built from stone or wood. The size of the locks was standardized and was 45 × 5 meters, with the length of the Ruhraaken mostly not exceeding 35 meters. The 74 kilometer journey down the river took two days; the ships were hauled upstream . The hard coal mining in the Grafschaft Mark and in the Essen-Werdener Revier profited most from the canalization of the Ruhr. The Ruhr Marine served until the late 19th century, especially the coal transportation to the Rhineland and was adjusted with increasing expansion of the railway network gradually.
The coal was extracted with a wedge hoe . The tunnels were 1.2 meters wide and 2.2 meters high; Main conveyor lines had a cross-section of around 1.5 × 2.5 meters. The expansion initially consisted of brushwood with inserted wooden poles; later one went over to the wooden door frame . Mouth holes and critical tunnel sections were secured by vaults. The gezähe the miner consisted of the wedge pick, Schramhacke and shovel. For centuries, the coal was transported from the longwall with single-wheeled carts and sledges or towing trays , which were then replaced in the 18th century by hunte ( trolleys ) of various designs. Later, the Hunt design prevailed with four equal-sized running wheels that were pushed on wooden planks. Tugs had to push the Hunte to the shaft or mouth hole. Reels were set up at seigeren shafts with which the coal buckets were brought to light. The use of explosives in the 17th century was a major innovation that streamlined the construction of the tunnels.
From 1785 horses were used in horse pegs to mine shafts ( Trappe colliery , Silschede ). The shafts had a rectangular cross-section and were built with squared timber and boards. The shafts were divided; one strand served to drive and one to promote.
Around 1787, surface transport by rail ( Rauendahler Schiebeweg ) was introduced, and in the 18th and early 19th centuries, the coal was often transported by horse-drawn tram to the loading points on the Ruhr. From mines that were not connected to the water network, the coal could only be transported over poor roads in ox- or horse-drawn wagons.
In 1804 there were already 229 mines in the Ruhr area with a total annual output of 380,000 tons. The Ruhr mining industry experienced a further boom through the introduction of steam power in dewatering . The first 46 m deep Seiger shaft as part of civil engineering was sunk in 1800 by the Vollmond colliery in Langendreer . The first steam engine was also used here for dewatering. In 1809 a steam engine was used for the first time for coal mining at the United Sälzer & Neuack colliery in Essen . The first coking plant was also built at the United Sälzer & Neuack colliery in 1816. In 1835, a wire rope was used for the first time in shaft extraction . Around 1840, the safety lamp developed by Sir Humphry Davy was introduced in the Ruhr mining industry.
Civil engineering mine
In the middle of the 19th century, the capacities of the tunnels were no longer sufficient to meet the coal requirements of the beginning industrialization . A milestone in Ruhr mining was the overcoming of the marl boundary through civil engineering. In underground mines, the pit water must be lifted and drained away. The first underground excavation shafts were created to complement the existing tunnel pits in order to develop deeper seams. Franz Haniel succeeded in doing this in 1833 with the Franz shaft in Borbeck near Essen and on a large scale in 1840 at the Kronprinz colliery . The hereditary tunnels set up in this area were previously regularly stuck in the marl sludge produced during the tunneling .

The shafts of the first underground mines north of the Ruhr (in the south of the cities of Dortmund, Bochum and Essen) had to be sunk through a marl deck mountains of 30 to 100 m. The shafts were initially built with wood; soon one went to the lining with bricks over, made watertight as possible to the shaft wall and increase the stability.
Dewatering was the major problem of developing civil engineering . Initially, the pit water was led to the surface with simple hand-operated wooden pumps or leather buckets. The overburden above the carbon is permeable to water, so that inevitably water penetrates the mine workings. The steam engine was first used in the Ruhr mining industry for dewatering and slowly gained acceptance in the 1830s. The pit water was collected in the shaft sump . Initially, pumps installed underground were used, which were driven via a linkage that reached to the steam engine installed above ground. The first successes in the dewatering of underground mines could be achieved, although the arrangement was very prone to failure and inefficient and also reduced the usable shaft cross-section. The steam engine was only used later as a hoisting machine . There were then variants in which the steam engine could alternatively be used for dewatering and conveying.
At the beginning of the 19th century, hemp ropes were used for hoisting shafts . From 1836 the Märkische mining authority advocated the use of steel cables . In 1840, all steam-powered hoisting machines were retrofitted with the more resilient and more durable steel cables.
The common method for sinking shafts in the second half of the 19th century was the sinkhole method . A cast steel shoe was lowered into the borehole. The clinker shaft wall was built onto this steel ring. While the soil on the bottom of the shaft was loosened and conveyed in buckets for days, the shaft sank due to the weight of the walled up shaft. But in several cases water ingress made the work of the sink more difficult. The discharge of the penetrated water with the help of the bucket or with the failure-prone rod pumps was often inadequate, so that the sinking work had to be postponed in several shafts. In the case of shafts that were sunk in more northerly areas with a higher marl deck, several sinks sometimes had to be built into one another if the friction between the shaft wall and the ground had become too great and the sump did not sink any further.
In the middle of the 19th century, coal was often extracted using the pillar dismantling method . A sloping section was driven from a higher level to the mining operation, which served as a brake mountain . The loaded heavy coal wagons were filled on the face and braked and lowered to the lower level . At the same time, with the heavier weight of the loaded wagons, empty wagons were pulled up the Bremsberg. From the Bremsberg, narrow horizontal stretches were laid into the longwall every ten to twelve meters until the department border was reached. The coal was conveyed over the route in carts ( Hunte ) that were pulled either by tugs or by pit horses .
During the pillar dismantling process, coal piers remain that will carry the mountain for a certain time. However, the charred cavities are soon compressed by the rock pressure and the result is subsidence that extends to the surface of the surface. Another danger is the spontaneous combustion of the remaining coal pillars. Despite the disadvantages, this mining method prevailed until around 1880. During the dismantling, the roof was secured with timber construction. Then the cavities were filled with mountains (manual backfilling). In this way the subsidence of the surface was reduced.
Sinking a shaft in the middle of the 19th century was a long-term and also a speculative investment, as the sinking could take years and the course of the seams and the faults were only insufficiently known. Therefore, when the carbon fiber was reached, two levels ( weather level and mining level) were driven. For the time being, they were satisfied with a shaft that was given a partition to use one side for fresh weather and the other side for bad weather . The fumes were connected to the chimney of the boiler house in order to use the chimney draft for the outflow of the fumes. With the further expansion of the mine buildings and the weather short-circuits that occurred in the shaft, this type of ventilation was no longer sufficient. There were momentous firedamp explosions , often in connection with coal dust explosions , which caused many deaths. In the 1880s, the mining authorities therefore required that every shaft system had to maintain at least two shafts, one of which was to be used as a fresh weather and the other as a weather shaft. The chimney vacuum of the steam boiler combustion turned out to be no longer sufficient to dissipate sufficient weather. Pit fans were therefore installed with a radial fan wheel driven by a steam engine. From 1893, electric motors were also used to drive pit fans, with which the axial fans could then be driven in the 20th century.
From around 1850 pit horses were used to transport routes underground. The Bischoff Hauderei from Gelsenkirchen alone rented up to 6,000 horses in the Ruhr mining industry. With the introduction of compressed air, diesel and electric locomotives at the beginning of the 20th century, the pit horse was displaced. The last pit horse named Seppel was brought to light in August 1966 from the Lothringen colliery in Bochum.
The first Malakov towers were built around 1850 . By 1857 the number of mines increased to 296 and the production to 3.6 million tons. Child labor was banned in 1854, and the mining authority's ban applied to young people under the age of 16.
Coal mining also reached the Emscher zone around 1850 . Mines were built in Gelsenkirchen, Herne , Castrop , Oberhausen and Bottrop . For the shaft structure in 1855 was put on the bill Hibernia in the English style for the first time in the Ruhr mining tubbing one. In 1865 the first compressed air drills were used for coal mining. The end of the 19th century was accompanied by rapid technical development: in 1865 the first pneumatic drill was used to make blast holes, and from 1866 dynamite was used. The first cutting machine was tested in 1875 .
This economic development required an increasing number of workers in the mining industry. The shortage of qualified miners led from 1855 to the construction of the mines 'own housing and the establishment of workers' settlements . With the provision of cheap housing, workers should be recruited and tied to the bill.
The association for mining interests in the Dortmund Oberbergamts district , or mining association for short, was founded in 1858 as a business association. With the General Mining Act for the Prussian States of June 24, 1865 , mining went from state-run to private-run.
The construction of a railroad network was a decisive step forward in order to be able to transport goods cheaply over medium and long distances, and this was taken advantage of early on by the mining industry. The first railway line in the Ruhr area was the Cologne – Duisburg line , which began operating in 1846 and was extended the following year via Dortmund and Hamm to Minden. As a result, new shafts were built as close as possible to this route, for example the first shafts of the Zollverein colliery , the Hibernia mine or the Von der Heydt colliery , which were located directly on the railway line, or branch lines to the mines were created. By the end of the 19th century, the route network in the Ruhr area was already well developed thanks to supra-regional connections and connecting railways. The opening up of Germany by rail during the industrial revolution not only improved the infrastructure of the Ruhr mining industry, but also increased the demand for coal and steel.
In the underground mines, mine gas escapes from the coal seams and can form an explosive mixture if there is insufficient ventilation. Firedamp explosions increased, whirling up coal dust in the routes and subsequently triggering even more devastating coal dust explosions, which cost the lives of many miners. The open light from the time of the tunnel construction was often the ignition source of the explosions. In 1881 the Prussian Firedamp Commission was set up to work out causes and measures to avoid firedamp explosions. As a measure, the gasoline safety lamp was introduced, the flame of which was surrounded by a fine-meshed grid that prevented ignition from the flame to the outside and acted as a flame arrester . Further measures included the order to lay water pipes in the pit to moisten coal dust and the ban on the use of black powder (1898).
After the Franco-Prussian War 1870–71, the contributions led to a large investment in the Ruhr area. After the constitution of the empire in 1873 there was also the first great depression (“ Gründerkrach ”), as a result of which coal sales fell and the price fell. This led to wage cuts, layoffs of miners and social tensions. The social problems and the struggle for fairer wages, better working hours, accident, health and pension insurance were expressed in the first major miners' strike in 1872 .
The golden years of the Ruhr mining were in the epoch from 1880 to 1914, which are characterized by a steep increase in production and a considerable increase in population. By 1885 there were already over 100,000 miners in the area. The great miners 'strike of 1889 eventually led to the formation of miners' unions . These played an important role in the great strikes of 1905 and 1912 .
Around 1880 the mining method changed from the pillar dismantling process to impact mining and then to longwall mining with partial or full offset . The mined area, the old man , was filled with crushed rock, which z. B. comes from the wash mountains . The crushed rock was mixed with water at the beginning of the 20th century and conveyed through a pipe system for mining. In 1908 a total of 35 spray batching systems were in operation, but the method did not prove itself due to blockages. The mountain displacement could at least reduce damage to the mountain.
In addition to the expansion of the railway network, the construction of a canal network for the inexpensive transport of bulk goods was tackled at the end of the 19th century . The Dortmund-Ems Canal was completed in 1899. Since then, it has connected Dortmund with the Ems near Meppen for around 230 km . In the continuation across the river, the connection between the Ruhr area and the Emden seaport was established for around 270 km. The canal had 16 locks and was initially designed for ships with a load capacity of up to 800 t. A branch canal branched off below the Henrichenburg ship lift in Waltrop to the Friedrich der Große colliery in Herne. The canal was further connected to the Rhine in 1914 with the expansion of the Rhine-Herne Canal from this branch canal. It runs parallel to the Emscher through the Ruhr area from east to west and connects Dortmund with the Rhine near Duisburg over around 50 km along the entire route with the Dortmund-Ems Canal. There were many mines on the canal that had their own factory ports for loading coal and coke. Another branch canal of the Dortmund-Ems Canal was the Datteln-Hamm Canal parallel to the Lippe in the northern Ruhr area since 1915 . In 1928, as a continuation of this, the Wesel-Datteln Canal was built , now referred to as the Lippe Lateral Canal in the unit .
In 1893 the Rheinisch-Westfälische Kohlen-Syndikat was founded. In the 19th century and at the beginning of the 20th century, serious accidents occurred time and again, often with many injuries and deaths. The main causes were explosions from firedamp and coal dust, the collapse of tracks and struts, or accidents with the use of explosives. A firedamp explosion with serious consequences occurred on November 12, 1908 at the Radbod colliery in Hamm. As a result of a firedamp explosion, which was probably caused by a defective gasoline safety lamp, 348 miners died from fire and toxic gases. As a consequence, the electric safety lamp was introduced at the colliery.
Rationalization at the beginning of the 20th century
Until the beginning of the 20th century, the seams were removed by hand with the classic tools of mallets and irons , which were quickly replaced by compressed air hammer from 1910 onwards. As a result, the negative effects of this mining process on the health of the miners became apparent, which was significantly affected by vibration, noise pollution and exposure to dust. Shaking chutes were mainly used for coal removal . These consisted of sheet metal tubs that were slowly pulled back and forth in order to transport the extracted coal to the conveyor line. The longwall to be mined was made accessible by the mountain supply route and the coal conveyor route. At the coal conveyor line, the end of the vibrating chute was arranged in such a way that the coals could be filled directly into the carts. The coal conveying was increasingly done mechanically. Catenary locomotives and gasoline locomotives were used on routes not endangered by firedamp; accumulator locomotives, compressed air-powered locomotives and later increasingly firedamp-protected diesel locomotives were used in endangered areas. A bottleneck in the transport of coal from the seam to the surface was the shaft extraction, especially with the increasing depth of the extraction floors. The Malakow towers from the middle of the 19th century were replaced by steel headframes around 1880 . The higher scaffolding allowed the installation of conveyor baskets with several levels . Better hoisting ropes and more powerful hoisting machines increased the shaft hoisting rate. The hoist ropes are no longer on the drum wound, but was used the Koepeförderung , wherein the rope in a rope groove on the traction sheave is running and at both cable ends, a conveyor basket is struck respectively. In this way, empty or filled with offset mountains can be transported underground and full coal wagons above ground at the same time.
The first electric hoisting machines were used at the beginning of the 20th century. The first plants of this type in Ruhr mining were the machines from the Zollern 2/4 sample mine . As far as a steam supply was available at the mining site, steam hoisting machines were still installed after the Second World War and operated at the Lohberg and Fürst Leopold collieries until the 1990s. At the beginning of the 20th century, the progress made in coal mining and mining made a significant contribution to the increase in mining at the Ruhrzechen.
When the underground construction shafts were sunk by the Emscher marl in the middle of the 19th century, there were extraordinary difficulties due to water penetrating into the shaft to be sunk. In some cases, the sinking of shafts took decades (e.g. Rhine Prussia 1 shaft ). From 1910 onwards, the ground was cooled down before the shaft was sunk, so that the water contained in the surrounding soil froze. For this purpose, a ring with double pipes was driven into the ground around the planned shaft cross-section. Cold brine (e.g. a chlorine magnesium solution ) at approx. −30 ° C was pumped through the inner pipe, which could then flow out through the outer pipe. After the ground had frozen, the shaft could be sunk without water intake or earth moving.
A miners' strike across the Ruhr area in 1905 limited the daily working hours to 8½ hours. As a result, the Zechenverband was founded on January 22, 1908 as an association of employers in the Ruhr mining industry, which represented the common interests of the mining companies towards the workers and employees.
In the 20th century, the demand for coal and coke continued to grow. This led to another mining migration to the north. The new collieries advanced to Dorsten , Selm and Werne north of the Lippe. The eastern area to Hamm and Ahlen and the Lower Rhine to Kamp-Lintfort were also developed by mining. After the introduction of the freeze shaft method, the increasing overburden could also be penetrated with a thickness of 200 to 400 meters. At the turn of the century, the day facilities were designed lavishly and representative, especially since the economy was flourishing. The buildings were often erected in the classic historicist style, which corresponded to the zeitgeist of the empire and the need for recognition of the mining industry (see Zeche Zollern 2/4; expanded in 1902).
The drafting of miners for military service resulted in a decline in production at the beginning of the First World War . The amount of hard coal produced fell from 114 million tons in 1913 to 70 million tons in the last year of the war. The developed and easily accessible deposits were dismantled haphazardly, while the alignment (driving new routes) largely came to a standstill. As a result, the coal was mined in the most accessible seams and less productive seams were not mined. The essentials were restricted for the maintenance of the technical systems. In particular, the compressed air supply and steam boiler systems were run down, so that mechanization declined again during the First World War. For the drafted soldiers, prisoners of war were used, most of whom were foreign to the mountains. In 1917, more experienced miners were ordered back from the front to increase production. During this time women had to work in mining, even underground.
Weimar Republic
The man-shift work had declined in the course of the war and reached its low point in 1920, apart from the year the Ruhr was occupied in 1923. After the war, the remaining less productive seams were also dismantled, and a lot of working time had to be invested in the neglected extension and equipment. After the war, labor was cheap due to the increasing inflation, so investments were made in expanding the mines. The period up to 1925 was marked by social misery and inflation. The occupation of the Ruhr area by French troops in 1923 led to a targeted decline in production with an absolute decrease to 40 million tonnes per year. Stabilization took place in early 1924.
In 1920, the Ruhr coal district settlement association (today the Ruhr Regional Association ) was founded in order to settle an additional 150,000 miners and around 600,000 other people in the Ruhr area against the background of the reparations claims from the Versailles Treaty . In 1922 the highest number of employees in the Ruhr mining industry was reached with 576,644 employees.
The golden years of the Weimar Republic from 1925 to 1929 also resulted in a significant economic boom in industry. In the mining sector, after ten years of stagnation, this resulted in the modernization and expansion of the pits. After the First World War, the pits were expanded against the background of low labor costs. Specifically, the following rationalization measures were taken: Driving up routes with greater distance and larger route cross-section, drastic reduction of operating points and concentration of the dismantling on longer struts, expansion of the energy supply (steam, compressed air, power station), illumination of operating points underground with electric lighting, almost exclusive dismantling with the pneumatic hammer after the compressed air supply has stabilized. From 1927 to 1934 the number of operating points decreased by 75 percent and at the same time the weather management could be simplified.
While the coal was previously extracted from several shafts in a mine, the production began to be concentrated in one shaft. This rationalization measure had the consequence that more powerful hoisting machines were used, the carriage circulation at the shaft was optimized and the coal processing was further mechanized. Many completely new pits were built in the existing coal fields. The architecture of the time broke away from the classical influences of the imperial era. A special development were the so-called hammer head towers built in the 1920s , which consisted of a steel frame. The hoisting machine was set up in a clinkered, closed room on the head of the steel scaffolding, which protruded beyond the scaffolding (examples: mines minister stone 2 and 4, Hannibal 1). They were the forerunners of the reinforced concrete towers built later.
Modernity, the Bauhaus style and functional design also shaped the new mine buildings; an outstanding example is the Zollverein colliery . The production of shaft 12, which was built in 1928, with 12,000 tons per day was well above the average of other mines. This mining rate of a mine was no longer exceeded in Ruhr mining, so that the development in terms of centralization had already reached an end point. While filigree riveted strut frames were still being built in the 1920s (see conveyor shaft 9 of the Consolidation colliery ), the scaffolding of the Zollverein shaft 12 was designed as a fully riveted double-headed conveyor frame.
In 1926 coal production in England collapsed almost completely as a result of a miners' strike (May to November 1926). The failure was compensated for by German hard coal. The export of hard coal in 1926 was doubled compared to the previous year and the continental markets in north-western Europe were served. These exports, especially to Scandinavia, could be sustained until the beginning of the Second World War. As a result of the rationalization measures, less well-trained miners were laid off after 1922. The rationalization measures, the retention of better trained miners and the high utilization of the mines led to a drastic increase in productivity (doubling between 1924 and 1931). The achieved shift performance of approx. 2 t per underground worker could only be increased significantly in the 1970s.
In the 1920s, many unprofitable collieries were shut down, especially in the crisis years of 1925 and 1931. This particularly affected the mines on the southern edge of the mountain, whose supplies were already well exhausted and which were mining hard-to- market edible and lean coal . Due to the geologically unfavorable alignment of the seams, it was not possible to set up efficient, long mining fronts. Some mines in the Lippe-Emscher region were also given up due to unfavorable geological deposits (e.g. Hibernia colliery ).
This concentration could also be observed in the coking plants. Many small, unprofitable coking plants were shut down; instead, central coking plants were built in the late 1920s; Examples are the Hansa coking plant and the Prosper coking plant .
time of the nationalsocialism
At the beginning of the 1930s, underground mining operations were enlarged with longer face lengths. Up to 80 coal miners could work simultaneously on a face length of 200 m. The seam was scored with cutting machines. The excavation was carried out with a hammer and the coals were transported to the excavation section on the vibrating chute. The number of operating points fell from 16,700 to 3,551 between 1927 and 1937. Diesel locomotives were used for the first time in 1927. In 1939 the first shearer loader and chargers were used.
Coal production in the Ruhr area 1943–1945 | |
---|---|
date | t / day |
1943 | 400,000 |
February 1944 | 390,000 |
February 1945 | 190,000 |
Days of occupation | 11 |
Mid-May 1945 | 7,000 |
Late May 1945 | 20,000 |
Mid-June 1945 | 40,000 * |
The rearmament in Nazi Germany and the war economy in World War II resulted in a high demand for coal. The coal was used for steel production (use of coke), as fuel for steam locomotives and for the production of fuel. The coal liquefaction was in the 1930s, several hydrogenation plants in the Ruhr area mainly with the Bergius process , and also the synthesis Fischer-Tropsch constructed. The synthetic fuel was used for road vehicles, tanks and planes. To ensure coal mining, miners were released from military service until 1942. As the war situation worsened, miners were increasingly called up for military service and forced laborers , mostly prisoners of war, replaced them under extremely difficult working conditions and reprisals. Barracks for the forced laborers were built on the colliery premises. In most cases, they were denied a protective position in bombing attacks, so that this group of people was often among the war victims.
The mines of the Ruhr mining were among the special targets of bombing raids on industrial plants, which began as early as 1940 (see also air raids on the Ruhr area ). While inner cities were affected in the first aerial war over the Ruhr area ( Battle of the Ruhr ) and many people died, the damage was mostly repairable until the beginning of 1944, and the effects of the attacks could be reduced by countermeasures ( air defense , fire protection measures , darkening ) . Serious damage to the central facilities of the collieries could mostly be repaired within one to two months or fixed with temporary measures. In the period from mid-1943 to mid-1944, hardly any attacks were carried out on the Ruhr area. It was thus possible to keep coal production in the Ruhr area at the previous level until mid-1944.
The second air battle over the Ruhr area, which ultimately led to the almost complete destruction of the inner cities, took place from March 1944 onwards. The degree of destruction of the industrial plants varied widely. While some mines were almost completely destroyed and the conveyor systems failed, other mines were able to start mining again a short time after the Ruhr area was captured. The near-downtown Zeche President in Bochum was no longer built after the Second World War. B. the largest colliery in the Ruhr area, the Zeche Zollverein , showed only relatively minor damage.
As a result of the direct effects of the war and the failure of the transport infrastructure, the mines stopped mining before the Allied invasion. The war not only resulted in the failure of many surface mining facilities. Although further shafts were sunk by 1944, no investments were made in the technical systems unless they were directly used to increase production. Furthermore, the excavation of new stretches or floors was neglected, so that in addition to the direct destruction, the war economy led to a significant deterioration in the infrastructure of the mining facilities.
Post War and Reconstruction
With the capitulation, coal production collapsed drastically. Many younger men were in captivity and the forced laborers deployed in the Ruhrzechen left the country. The workforce in 1945 amounted to 276,192 men. After the collapse, those able to work had to solve the existential difficulties of the food supply, for example by driving hamsters . In addition, the poor supply situation led to a high level of sick leave among the miners. In the geological areas of the southern Ruhr area, in which the coal seams reach to the surface of the earth, an uncontrolled and undocumented coal mining began in many places, which mostly served the private supply of fuel. The mine management had no influence on the sales price. As a result, most of the mines' coal production was lossy and no capital was invested in modernization. The Allies banned alignment and fixture work. Much of the factory equipment was worn out and outdated, but the lack of capital made major investments impossible.
From August 1945, mining in the Ruhr was managed by the North German Coal Control organization of the British occupying power . The American and later the French occupying forces joined this control authority under the name Combined Coal Control Group . The supply situation for the population deteriorated further in the first years after the war and in April 1947 led to a hunger strike by the colliery workers. As a result, the miners were given special consideration when allocating food, especially the CARE packages . German positions were created from 1947, in particular the German Coal Mining Management (DKBL) was founded by the British and American occupying powers . Through the organization, the mining on the Rhine and Ruhr was divided into districts and the partially orphaned board members of the mining companies were filled.
On February 20, 1946, the greatest mining accident in the Ruhr mining industry occurred: 405 miners lost their lives in a firedamp explosion at the Grimberg colliery in Bergkamen . The colliery was only able to resume operations in 1948.
With the plans to found the Federal Republic of Germany, France renewed its 1946 demand for international control of the arms-relevant Ruhr economy. Via the International Ruhr Authority created in 1949, the participants in the London Six Power Conference (USA, United Kingdom, France, Belgium, Netherlands and Luxembourg) controlled the production and sales of the Ruhr economy, and thus of Ruhr mining, even after the establishment of the Federal Republic. The sovereignty of the young state was thus still severely restricted. This question was so important to the Federal Government that the Marshall Plan Minister Franz Blücher represented Germany at the Ruhr Authority.
During the first economic boom in the Federal Republic of Germany, there was a significant shortage of coal, especially since the use of mineral oil had not yet established itself. The number of employees was therefore increased to increase funding. The high average age of the workforce, the relatively old age of the operating facilities and the increasing mean depth of the mining operations (1936: 665 meters; 1951: 756 meters) had a negative effect on the operating results. Rationalization measures in extraction ( coal plow , tank extraction , stamp-free mining front) and extraction (four-rope extraction at the Hanover colliery ) were tried and tested in practice, but could only slowly gain acceptance. The DKBL tried in particular to repair destroyed and outdated coal processing plants, coking plants and power stations, which met with considerable resistance from the occupying powers. Because of the feared international competition, bans and restrictions were imposed. The coal liquefaction plants built before the war were not put back into operation except for the plant in Bergkamen.
The aim of the occupying powers was to unbundle coal mining and prevent the concentration of economic power. On the basis of Act No. 27 of the Allied High Commission, the DKBL was commissioned to develop proposals for a reorganization. The Allied High Commission finally approved a proposal for unbundling drawn up by the Federal Government on March 14, 1951. In 1951, the co-determination of employees on the boards of the iron and coal industry was passed ( coal and steel co-determination ).
The transition period after the Second World War ended with the dissolution of the International Ruhr Authority in February 1953, after its control function had been transferred to the European Coal and Steel Community , and with the liquidation of the DKBL in mid-1953. The war damage to factories and apartments had largely been eliminated more alignment and fixtures were carried out. Coal extraction and extraction was further mechanized and extraction almost reached the pre-war level in 1952. The production of coke already exceeded the pre-war level with 33 million tons. On May 14, 1952, the Ruhr Mining Association was founded in Essen as an organ of employers .
Under this impression, there was a wave of investment in the 1950s. In addition to the construction of new pits, the existing production sites were extensively modernized and, for example, the production facilities and coal processing were completely renewed. At the old colliery locations, mainly south of the Ruhr, small mines were reopened at abandoned locations . The fields were mostly leased by the old mining companies. The coal removal was mostly carried out with trucks that supplied small and medium-sized businesses in the area.
Until the beginning of the 1950s, electrical energy was used underground for lighting, pump drives and possibly for catenary locomotives. With the mechanized mining, high electrical power was required for the drives, so that the construction of a powerful power supply for the underground operations was necessary. The classic energy compressed air has been partially substituted by electric drives.
The labor shortage in the mining industry led to a wave of rationalization. An essential starting point was coal mining. A prerequisite for mechanized coal extraction was the construction of a stamp-free mining front. As far as the strength of the hanging wall allowed, steel friction punches with a steel cap were used. In 1949 the first tank conveyor was used at the Jacobi colliery in Oberhausen , with which the coal could be transported from the longwall to the mining section. The second step was the commissioning of a mechanized mining machine such as the Löbbehobel at the Jacobi colliery in 1951.
From the number of employees and the funding quota, it can be deduced that funding per employee has not changed from the turn of the century until the 1950s (1900: 263 annual tonnes per employee; 1956: 257 tpy / employee). There were fluctuations, but they can be explained by changes in the shift time, the effects of the war, compulsory special shifts and the occupation of the Ruhr. The rationalization measures were only able to compensate for the mining conditions, which became more difficult over the years, for example due to greater depths and longer distances from the extraction points to the shafts. In particular, the mining in steep storage , which is often found in the southern Ruhr area , could not be thoroughly rationalized. The coal seam was still mined here with a hammer. Until the coal crisis at the end of the 1950s, it was company policy to use the minable coal reserves as much as possible in order to achieve a long service life for the mine. This resulted in a considerable need for personnel for coal production.
In the mid-1950s, many new construction projects from the pre-war period that had been discontinued due to the war continued; Examples are:
- Construction of the Germania central shaft system (started: 1939; completed: 1954, demolition in 1974, headframe is on the site of the German Mining Museum in Bochum),
- Construction of the central shaft 7 of the Ewald colliery (started: 1940; completion: mid-1950s),
- Construction of the Rossenray mine in Kamp-Lintfort (1943: sinking work began; discontinued in 1945; shafts 1 and 2 reached their final depth in 1959, demolition in 2019).
In addition, new production shafts were sunk at other shaft systems to increase capacity and concentrate production on one shaft or existing shafts were equipped with modern conveyor systems. New conveyor systems were designed as four-rope conveyors. In many cases, concrete headframes have been erected with tower hoists. In the 1950s, rack conveying was still predominantly used.
Examples of concrete headframes with tower hoisting machines are:
- Shaft 1 of the Friedrich Heinrich colliery , Kamp-Lintfort, reinforced concrete headframe,
- Central shaft 7 of the Auguste Victoria colliery (sunk 1956/57),
- Central shaft 11 of the Shamrock colliery (Herne, sunk from 1957, reinforced concrete headframe; from 1967 shaft of the General Blumenthal colliery ; demolition 2013)
- Central shaft 3 of the Westerholt colliery in Herten (beginning of Teuf 1956).
In addition, the coal mine power plants were modernized or newly built. In addition, the coke production rate was increased significantly compared to the pre-war level through new coking plants and modernizations. According to an official announcement of July 29, 1958, the coal mining association assumed that the demand for coal from the Ruhr would increase to 180 million tonnes per year over the next 20 years. The increase in capacity should take place through the commissioning of new shafts in previously unexplored fields, the merging of existing shafts and through rationalization measures.
Coal crisis
In 1956, almost 125 million tons of hard coal were mined, the highest level after the Second World War. The wages of the miners were now in the top group and the unions had fought for a strong position. The job of miner was attractive despite the high physical strain. In the post-war period , many expellees came to the Ruhr area; from 1956 came guest workers .
During the boom in the first half of the 1950s, German hard coal production could not completely meet demand, so that coal also had to be imported from the USA, Czechoslovakia and Yugoslavia. In addition, crude oil pushed onto the German market as a new energy source. In addition to its use as fuel for vehicles, heating oil was increasingly used as an industrial fuel. In 1956, Scholven Chemie AG built an oil refinery in Gelsenkirchen-Buer , which went into operation in 1958.
Until 1958, the domestic coal extracted was delivered directly to consumers. In the following years, however, the total production could no longer be fully marketed and coal had to be piled up. In 1958 the stockpiles already amounted to 12.3 million tons, about ten percent of the annual production. As a countermeasure, the first party shifts were put in on February 22, 1958 . The cause of the decline in sales was the substitution of coal by crude oil, the price of which fell as a result of an oversupply on the world market, as more crude oil was extracted in the Arab region. The federal government lifted the tariffs for mineral oil products. Another cause of the drop in sales was the increasing use of imported coal, which in connection with falling freight prices and more favorable geological conditions in the producing countries could be offered more cheaply than domestic coal. On September 30, 1958, the Lieselotte colliery in Bochum was closed and a little later the Friedrich Thyssen colliery . Colliery entrepreneurs and IG Bergbau advocated protectionist measures to curb oil and coal imports; the federal government under Chancellor Adenauer rejected this. After the unchecked rise in coal sales after the Second World War, the extent of the incipient coal crisis was not foreseeable; it proved to be decades-long and grave.
Between February 1958 and June 1959 5 million party shifts had already been processed. On September 26, 1959, IG Bergbau organized a miners' demonstration with 60,000 participants in what was then the federal capital of Bonn. The Friedrich Thyssen 4/8 colliery in Duisburg-Hamborn was the first large mine to be shut down on June 30, 1959; At the beginning of the 1960s it was mainly mines in the southern Ruhr area that were closed. The cities of Dortmund , Bochum and Essen were particularly affected . The coal reserves of the mines there were already well exhausted and the technical systems were old. Due to unfavorable geological conditions, rationalization and cost reductions were not possible. The mainly steep storage and disturbances prevented the mechanization of mining. An attempt was made to compensate for the job losses by setting up new businesses. Well-known examples are the establishment of the Opel plant from 1960 on the site of the recently closed Dannenbaum collieries in Langendreer and Laer and the establishment of the Ruhr University .
The modernization of the productive pits was pushed ahead, since the long-term survival of the coal mining in the Ruhr area was not in question. At the end of the 1950s, which put vessel promotion (Skip promotion), in 1933 on the mine Pattberg had been introduced by at many mines. Instead of the laborious transport of wagons, the coal was temporarily stored underground at the filling location in a bunker and from there it was loaded into the shaft hoist . In this way, continuous and uninterrupted conveyance and a simpler operational process have been ensured since then. The vessels had a capacity of up to 30 t. Examples of the installation of the vessel conveyance were the shaft 1 of the Nordstern colliery (1953), the Walsum colliery, shaft 2 (1954/55), the shaft 12 of the Zollverein colliery (conversion 1957) and the shaft 9 to the Graf Bismarck II colliery , which was built in 1957 / 58 was converted into a central conveyor shaft with two fully automatic container conveyors.
By 1963, 33 mines with a production capacity of 10.3 million tons had been closed in the Ruhr area. The mine operators joined forces on September 1, 1963 to form the Rationalization Association of the Coal Mining Industry. The aim was to shut down unprofitable operations and concentrate the subsidies on profitable plants. The promotion should be adapted to the sales situation and competitiveness should be increased. In the following year the Bundestag passed the law to promote rationalization in the coal industry; this resulted in the closure of a further 31 large and 20 small mines with a total annual output of 26 million tons. A brief recovery in coal sales occurred in 1960. It was of the opinion that future sales of 140 million tons of German hard coal could be maintained, with the Ruhr mining industry accounting for a production rate of around 115 million tons per year. The use of mechanical conveyors, coal planers and conveyor belts resulted in a significant increase in performance. From 1957 to 1963, the proportion of fully mechanically extracted coal increased from 13 percent to 65 percent. Due to the rationalization measures between 1958 and 1966, the average shift volume per miner could be increased from 1.7 tons to 2.9 tons.
In 1963, the Wulfen mine planned in the 1950s was completed to open up new, unscratched coal fields. The plan was initially to create new settlements in the cities of the northern Ruhr area with the migration of coal mining to the north. In Wulfen, Marl and Bergkamen, new residential areas with a high density of buildings were built. The low attractiveness of the residential area and the lack of the expected population movement to the northern edge of the Ruhr area later led to social problems in these new building areas. At the state level, in the overall concept for the north migration of the coal mining on the Ruhr in 1986, it was finally determined that "the relationship between settlement and open space in the northern Ruhr area / southern Münsterland should be fundamentally preserved, with the tendency to expand the open space."
Compared to the industrial development of the Emscher zone, the planning changed: No coal was extracted from the new shafts (with the exception of Wulfen until 1981), they were only used for ventilation, material transport and rope travel . The coal was extracted and processed south of the Lippe, partly at the old shaft sites in the Emscher zone, where there was no longer any mining itself.
Coal mining with pneumatic hammers was the predominant mining method until the 1950s. The miners were exposed to considerable physical strain during the mining activity. As a long-term consequence, there was often "pick hammer disease" with a painful change in the arm joints. In the 1960s, mining was increasingly mechanized through the use of peeling (coal planer) and cutting ( cutting machine ) mining machines. The decisive prerequisite was a punch-free excavation front in order to be able to move the extraction machines over the entire length of the face. The first stamp-free face was operated in 1941 at the Zeche Hansa (Dortmund). The timber construction was first removed by friction stamps and caps secured the roof up to the dismantling front. The so-called high-speed planer was first used in 1949/50 and the shearer loader for mining harder coals was introduced in the Ruhr area in 1956. The coal extracted fell on a tank conveyor, which carried them to the aspiring. The armored conveyor consists of a steel channel on which the carriers are moved via chain links guided on the side. The mechanization of mining quickly caught on, especially as productivity could be increased considerably and the very hard work with hammer hammers was replaced. In 1963, 50.6 percent of the coal was extracted by peeling, 18.1 percent by cutting and 20.6 percent by hammers.
In 1964, the Rationalisierungsverband Ruhrbergbau registered 31 large mines for closure. During the economic crisis at the end of Ludwig Erhard's chancellorship in 1966/67, sales collapsed again. The decommissioning premium granted by the federal government meant that high-yield mine systems were decommissioned. An outstanding example was the closure of the Graf Bismarck colliery in Gelsenkirchen-Bismarck . The mine was operated by Deutsche Erdöl-AG (DEA) and 70 million DM had been invested in the modernization of the mine in the 1960s. The closure in 1966 was completely unexpected for the employees, especially since the colliery had reached a high technical standard and high productivity and sufficient coal reserves were available under favorable mining conditions. The closure showed that the federal government's coal policy had failed. The seams in the fields of the Graf Bismarck colliery were mined in the following decades by the adjacent Consolidation and Hugo collieries .
Founding of Ruhrkohle AG (RAG)
On November 27, 1968, Ruhrkohle AG was founded as a consolidation company for German hard coal mining. At the time it was founded, 80 percent of the German hard coal mining companies were combined in the company known for short as RAG . An important basis for business was the smelter contract negotiated with the steelworks in 1969 , which secured part of the coal and coke sales up to the year 2000 with a successor arrangement.
In 1975 the coal pfennig was introduced on top of the electricity tariff, which meant direct subsidization of coal from the Ruhr. In what is known as a “contract of the century ”, an agreement was concluded for the period from 1980 to 1995 on the amount of German hard coal used to generate electricity. This contract was an essential component of the coal priority policy pursued in North Rhine-Westphalia at the time , which was particularly supported by the SPD in the federal government.
The last shaft put into operation in the Ruhr mining industry is the Rheinberg weather shaft of the Walsum colliery. This was put into operation in 1993 and became obsolete in 2008 with the closure of the Walsum colliery. It was demolished in 2017.
When the coal pfennig was abolished at the end of 1995, the necessary funds for the German hard coal mining were made available from the state budget. A coal compromise concluded in 1997 between the federal government, state governments, the RAG and the trade union stipulated that state subsidies for the German hard coal mining industry would be reduced to 2.7 billion euros by 2005 and that subsidies would be limited to 22 million tonnes up to this point , assuming the number of employees from 36,000. These figures were adjusted again in 2003, the annual output in Germany should drop to 16 million tons by 2012. At the beginning of February 2007, the government coalitions of the federal government, the states of North Rhine-Westphalia and Saarland, the RAG and the trade union agreed in a key issues paper to discontinue subsidies for the German coal mining industry at the end of 2018. At the same time, the federal government decided not to receive structural aid for the Ruhr area North Rhine-Westphalian state government to discontinue the state's sales aid for the hard coal mining at the end of 2014. The Hard Coal Financing Act was issued in December 2007 . This stipulates that the Bundestag will review the coal mining industry again by June 2012 at the latest. This clause was not adhered to, but the review was overturned in return for the fact that an EU complaint against the German coal subsidies was dropped.
End of hard coal production
Until 2018, RAG Deutsche Steinkohle AG still operated the Prosper-Haniel mine in Bottrop in the Rhenish-Westphalian coal district . The Auguste Victoria colliery in Marl was closed on December 18, 2015 . In 2018, the hard coal subsidy was ended by the Federal Republic of Germany. The Prosper Haniel colliery ceased regular operations on September 14, 2018. Sporadic production continued until December 2018, among other things to straighten the seam in which it was last mined. The last German hard coal was handed over to Federal President Frank-Walter Steinmeier at a closing event on December 21.
Current situation
The Borth salt mine , which is the only still active mine in the Ruhr area, is not a classic mine for the Ruhr area, but is located on the edge of the Ruhr area.
Environmental impact
The mining of the coal seams resulted in a large-scale lowering of the altitude in the Ruhr area. This also has an impact on the course of the Emscher in particular . In particular during the first years of the mining of seams up to the final settlement, cracks appeared in the masonry of buildings in the areas of the saddles and hollows ( mining damage ). Hollow spaces near the surface, such as unfilled shafts and pits , still pose particular risks today. Only after the introduction of the Prussian Mining Act of 1865 were mine owners obliged to map their mining operations and submit them to the Upper Mining Authority . In the post-war period there was also illegal mining in some places, which left unfilled cavities that are not documented.
Even today, mine water is pumped out on a large scale, so that the groundwater level in the Ruhr area has largely decreased.
The consequences of backfilling the cavities in shaft mining with slag are controversial.
Former colliery sites are usually contaminated with various substances ( contaminated sites ), such as hydraulic oils in the machine shop area or polycyclic aromatic hydrocarbons (PAH) and benzene in the coking plant area .
See also
- Mining area
- History of the Ruhr area
- List of mines in North Rhine-Westphalia
- List of mining accidents
- Halden in the Ruhr area
literature
- Werner Abelshauser : The Ruhr coal mining since 1945. Reconstruction, crisis, adjustment . CH Beck, Munich 1984, ISBN 3-406-30308-0 .
- Karl Heinz Bader, Karl Röttgert: 250 years of hard coal mining, a contribution to the history of mining, the mining administration and the city of Bochum. Study publisher Dr. N. Brockhaus, 1987, ISBN 3-88339-590-0 .
- Uwe Burghardt: The mechanization of the Ruhr mining industry 1890-1930. CH Beck, Munich 1995, ISBN 3-406-39370-5 .
- Wilhelm Cleff: "Zeche Rheinpreussen" A German hard coal mine. Wider-Verlag Berlin, 1932.
- Eichholz, Klaus: Mining historical maps of the county of Mark as unknown sources of local and regional history. In: Märkisches Jahrbuch für Geschichte. 105, 2005, pp. 148-191.
- Gerhard Gebhardt: Ruhr mining. History, structure and interdependence of its societies and organizations. Glückauf Verlag, Essen 1957
- Bodo Harenberger: Chronicle of the Ruhr area. WAZ, 1987, ISBN 3-88379-089-3 .
- Wilhelm Hermann, Gertrude Hermann: The old mines on the Ruhr. 6th edition, Langewiesche Verlag, Königstein 2008, ISBN 978-3-7845-6994-9 .
- Joachim Huske : The coal mines in the Ruhr area. Data and facts from the beginnings to 1997. Bochum 1998, ISBN 3-921533-62-7 .
- Evelyn Kroker : The miner's workplace, Vol. 2: The way to full mechanization . German Mining Museum, Bochum 1986, ISBN 3-921533-36-8
- Holger Menne, Michael Farrenkopf (arr.): Forced labor in the Ruhr mining industry during the Second World War. Special inventory of the sources in archives in North Rhine-Westphalia. Bochum 2004 vfkk.de ( Memento from June 22, 2007 in the Internet Archive ) - (PDF; 463 kB).
- Kurt Pfläging : The cradle of Ruhr coal mining. ISBN 3-7739-0490-8 .
- Kurt Pfläging: Stein's journeys through coal mining on the Ruhr. ISBN 3-89570-529-2 .
- Kai Rawe: "... we will bring you to work!" Foreign employment and forced labor in the Ruhr coal mining during the First World War. Klartext, Essen 2005, ISBN 978-3-89861-460-3 .
- Hans-Christoph Seidel: The Ruhr mining in the Second World War. Collieries - miners - forced laborers. (= Publications of the Institute for Social Movements. - Series C: Labor and Forced Labor in Mining. Volume 7). Klartext, Essen 2010, ISBN 978-3-8375-0017-2 .
- Hans Spethmann : Twelve years of mining in the Ruhr. From its history from the beginning of the war to the French march 1914–1925. 5 volumes. Publisher R. Hobbing, Berlin 1928–1931.
- Günter Streich, Corneel Voigt : Mines, dominants in the area. History, present, future. With the Ruhr, Saar, Ibbenbüren districts. 9 Nobel Verlag, 1999, ISBN 3-922785-58-1 .
- Klaus Tenfelde : Social history of the miners on the Ruhr in the 19th century. Bonn 1981
- Gustav Adolf Wüstenfeld: On the trail of coal mining. Pictures and documents on the history of Ruhr mining in the 18th and 19th centuries. Wüstenfeld, Wetter -Wengern 1985 ISBN 3-922014-04-6
Web links
- Witten tourist office: A brief history of mining in the Ruhr - a red thread through nine centuries. ( Memento from February 2, 2003 in the Internet Archive )
- North Rhine-Westphalian State Archives Münster (ed.): Administration of mines, smelters and salt works in Prussian Westphalia ( Memento from January 24, 2003 in the Internet Archive ) (PDF).
- Claudia Köhler: Geology of Economically Significant Hard Coal Deposits in Germany ( Memento from September 29, 2007 in the Internet Archive ) (PDF; 536 kB).
- Early mining on the Ruhr - dates and references to historical traces
- Michael Tiedt: The origins of the mines in chronological order
- Mining in the Ruhr area
- Overview map with numerous mine sites (Action Schachtzeichen) ( Memento from May 17, 2010 in the Internet Archive )
- Overview of former colliery locations in the Ruhr area - numerous maps and information
- Image galleries and information on various mines in the Ruhr area
- Federal Center for Political Education (Ed.): Ruhr area. From Politics and Contemporary History 1-3 / 2019 ( Memento from December 17, 2019 in the Internet Archive ) (PDF).
Individual evidence
- ^ Gerhard Gebhardt: Ruhr mining . History, structure and interdependence of its societies and organizations. With the participation of the Ruhr mining companies. Glückauf GmbH, Essen 1957, p. 492 ff .
- ^ Klaus-Dietmar Henke : The American occupation of Germany . Oldenbourg R. Verlag, 1995, ISBN 978-3-486-54141-0 , p. 444 .
- ↑ “The Cabinet Protocols of the Federal Government” online (Federal Archives), 30th cabinet meeting on Tuesday, December 13, 1949, A. Meeting of the Federal Chancellor with the AHK, http://www.bundesarchiv.de/cocoon/barch/1010/k /k1949k/kap1_2/kap2_30/para3_22.html
- ^ Fritz Pamp: Zeche Jacobi, The story of a mine . M-Design-Verlag, Düsseldorf 1996, ISBN 3-9805259-0-2 , p. 46 .
- ↑ The Minister for the Environment, Spatial Planning and Agriculture of the State of North Rhine-Westphalia: Overall concept for the north migration of the coal mining on the Ruhr . Düsseldorf 1986.
- ^ Federal Center for Political Education: State of North Rhine-Westphalia
- ^ German Bundestag: Motion of the SPD parliamentary group of October 14, 1987
- ↑ J. Flauger, T. Wiede, HJ Schürmann: RAG must close half of the mines . In: Handelsblatt . July 17, 2003, ISSN 0017-7296 .
- ↑ State Parliament internal . No. 3/2007 , ISSN 0934-9154 , p. 6-9 .
- ↑ Hard Coal Financing Act (SteinkohleFinG). From December 20, 2007, § 1 Paragraph 2.
- ↑ Spiegel Online from December 18, 2015: Closure of the Auguste Victoria colliery - last shift start
- ↑ The Prosper-Haniel mine has ceased regular operations . Westdeutsche Allgemeine Zeitung, September 14, 2018
- ^ Shift in the shaft: the last mine closes in the Ruhr area . Neue Westfälische, September 22, 2018