Wind turbine
A wind power plant (abbr .: WKA) or wind energy plant (abbr .: WEA) converts the energy of the wind into electrical energy in order to then feed it into a power grid. The terms wind power plant or wind turbine or wind power converter are also used colloquially . Wind turbines are by far the most important form of using wind energy today. The design that dominates by far is the three-bladed lift rotor with a horizontal axis and rotor on the windward side , the machine house of which is mounted on a tower and the wind direction is actively tracked. A number of other forms of construction, in particular with a different design of the rotor, have not yet become established.
Wind turbines can be used in all climates. They are installed on land (onshore) and in offshore wind farms in the coastal apron of the seas. Today's systems are operated almost exclusively with a grid connection and, in contrast to older systems with asynchronous generators connected directly to the grid, have a very good grid compatibility thanks to feed-in via power electronics . The typical output of current systems (as of 2016) is around 2 to 5 MW for onshore systems and 3.6 to 8 MW for offshore systems. In isolated operation , even small systems in the power range from a few 100 watts to several kW can be economical. They are dealt with under wind generator . Groups of several wind turbines are considered in the article wind farm , further applications and energy policy aspects in the articles wind energy , renewable energies , energy transition and energy transition by country .
History of wind turbines
Wind motors, test facilities and failed major projects
The first documented wind-powered system for generating electricity was built in 1887 by the Scot James Blyth to charge batteries for the lighting of his holiday home. Its simple, robust construction, with a vertical axis ten meters high and four sails arranged in a circle eight meters in diameter, had a modest efficiency. At almost the same time, Charles Francis Brush in Cleveland , Ohio, based a 20 meter high system on the then quite advanced American wind pumps . With pumps, torque is more important than speed; Brush used a two-stage transmission with belt drives to drive a 12 kW generator.
Around 1900, the Dane Poul la Cour came through systematic experiments - including on aerodynamically shaped wing profiles in wind tunnels - to the concept of the high-speed machine , in which only a few rotor blades are sufficient to utilize the energy of the flow over the entire rotor surface. During the First World War over 250 plants of this type were in operation in Denmark. In other countries, too, wind motors were built for decentralized power generation in the early 20th century. With the widespread electrification in the interwar period , many of these systems disappeared again, especially since the wind motors equipped with direct current generators and battery storage systems were not compatible with alternating current power grids .
After the Second World War, wind energy research was promoted in various countries. Countries such as France and Great Britain invested large sums in wind power research until around 1965. The improvement of the profile geometries in the 1950s and 1960s to glide ratios well over 50, driven by aviation, allowed extreme high-speed runners with only one single rotor blade . Rotors with more than two blades were considered backward. With the exception of a few prototypes, hardly any systems were built in view of the low energy prices.
There was a renaissance in the use of wind energy from the 1970s, among other things as a result of the environmental and energy debate and two oil crises . In the 1970s and 1980s, a large number of different designs were tested, with turbines with a horizontal axis ultimately prevailing. In some countries (such as Germany and the USA, among others), they initially relied on demanding large-scale industrial projects such as the two- wing GROWIAN ; but these had major technical problems and proved to be failures. Starting from Denmark, where, in addition to the knowledge of building small systems, there was also an idealistic clientele for such systems, the Danish concept of numerous robust systems of low power, which were initially often produced by small companies and hobbyists with initially simple means , prevailed .
The systems, which were exported by the thousands to the USA in the 1980s, had three rigid rotor blades (rigid = no blade angle adjustment ) and an asynchronous machine with one or two fixed speeds that was connected to the grid without a frequency converter . Performance was limited by intentional stall . The archetype of this very successful concept was the Gedser wind turbine designed by Johannes Juul and commissioned in 1957 . It worked until its temporary shutdown in 1966 and was put back into operation for several years in 1977 for a joint test program by Danish scientists and NASA .
On the basis of these small systems by today's standards, the further development towards large turbines with variable speed and adjustable rotor blades took place in the 1990s and 2000s . Since then, Denmark has been the country with the largest share of wind power in electricity generation.
Technical development since the 1990s until today
With the Electricity Feed Act of 1991, the upswing in wind energy began in Germany too; it continued with the Renewable Energy Sources Act (in force since April 1, 2000). These political framework conditions contributed to the fact that German wind turbine manufacturers are now among the world's technology and world market leaders.
In the endeavor for ever lower electricity production costs , the wind turbines gradually became larger in the course of development. The average nominal output of the wind power plants newly installed in Germany was 164 kW in 1990, in 2000 for the first time over 1 MW , in 2009 for the first time over 2 MW. In 2011 it was over 2.2 MW, with systems with an installed capacity of 2.1 to 2.9 MW dominating with a share of 54%. A further increase in the average nominal output is foreseeable: the 3 MW class will be introduced for onshore wind turbines , while in the increasingly built offshore wind farms , mainly large-scale systems with 3.6 to 6 MW are being built.
To increase performance, u. a. the rotor diameter is larger. According to the circular formula, doubling the rotor blade length results in a quadrupling of the rotor area. Until the end of the 1990s, the diameter of newly constructed systems was mostly less than 50 meters, after around 2003 mostly between 60 and 90 meters. By 2018, the average rotor diameter grew to 118 m, the average hub height to 132 m and the nominal power to 3.233 MW, with significant differences due to regional wind speeds . Worldwide, the average output of newly installed systems exceeded the 2.5 MW mark for the first time in 2017.
Modern light wind turbines now have rotor diameters of over 140 meters and hub heights of over 160 meters. In the offshore sector, new series with rotor diameters of 160 to 170 meters and a nominal output of up to around 9 MW are available. Enercon has been using gearless systems since 1995 and was initially the only manufacturer with direct drive for a long time; Meanwhile, however, significantly more manufacturers use a gearless design, which is now considered the "second standard construction". In 2013, the global market share of gearless systems was 28.1%.
Up until around 2010, wind turbines were manufactured in a stationary manner using dock assembly . Since then, manufacturers have been relying more and more on series production using the assembly line process and on industrialization and standardization of their products for reasons of cost. At the same time - as has long been the standard in automotive engineering - modular platform strategies are becoming established in which system types or variants are developed for different wind classes on the same technical basis , e.g. B. by different rotor sizes with largely identical drive train or different generator concepts with the same rotor diameter.
Not all newly installed systems are in new locations: some old systems are being dismantled and replaced by more powerful ones, which is known as repowering . As a rule, the number of individual systems within wind farms decreases, while the installed capacity and yield increase.
Energy supply and yield
- See also: Wind energy: profitability (for a macroeconomic view; here the calculation of a single system)
Power density of the wind
The density of the kinetic energy of the flow increases quadratically with the wind speed v and depends on the air density ρ :
- .
At a wind speed of 8 m / s (≈ wind force 4 Bft ) it is almost 40 J / m³.
This energy is transported with the wind. The power density of this transport is in the free flow far in front of the rotor of the wind turbine
- ,
in the example 320 W / m².
Because of this strong increase in power density with wind speed, windy locations are particularly interesting. The height of the tower plays a major role, especially inland, where the roughness of the ground (buildings and vegetation ) reduces the wind speed and increases the degree of turbulence .
Lossless performance coefficient
The performance of a wind rotor is usually expressed by relating its power delivered to the shaft to the rotor area and to the power density of the wind. According to Albert Betz, this fraction is referred to as the performance coefficient c P , also known colloquially as the degree of harvest . In 1920 he derived a maximum achievable performance coefficient from basic physical principles. The reason is that the flow speed decreases as a result of the power consumption, the air parcels become shorter in the direction of flow and the streamlines increase their distances from one another, see figure. The more the wind is slowed down, the more unused it flows past the rotor. The optimum of 16/27 = 59.3% would be achieved by a lossless rotor, which slows the flow down to 1/3 of the wind speed with a dynamic pressure of 8/9 the energy density of the wind. The rest of this power is still in the flow: 1/3 = 9/27 in the stream threads that have evaded the rotor, 1/9 of 2/3 = 2/27 in the braked air mass.
Performance limits and losses
Like all machines, real wind turbines do not reach the theoretical maximum either. Aerodynamic losses result from air friction on the blades, from wake vortices at the blade tips and from swirl in the wake of the rotor. In modern systems, these losses reduce the power coefficient from c P, Betz ≈ 0.593 to c P = 0.4 to 0.5. From the above-mentioned 320 W / m², up to 160 W / m² can be expected. A rotor with a diameter of 113 m (10,000 m² area) then delivers 1.6 megawatts to the shaft. To calculate the power at the mains connection, the efficiency of all mechanical and electrical machine parts must also be taken into account.
The performance coefficient of the rotor is often overrated when comparing different designs. A ten percent lower performance coefficient can be compensated for by increasing the rotor diameter by five percent. For economic success it is more important to cover the largest possible rotor area with the given material input. In this regard, today's standard design with a horizontal axis of rotation and a few slim rotor blades is superior to other designs .
Yield
To estimate the annual yield, the so-called mean wind speed is given for the location of the wind turbine . It is an average value of the wind speeds occurring over the year. The lower limit for the economic operation of a system, depending on the feed-in tariff , is at an average wind speed of around 5–6 m / s at hub height. However, there are other factors to consider.
A wind report based on the frequency distribution of the wind speed for a location is used to optimally select the nominal wind speed (usually 1.4 to 2 times the mean wind speed) or, given the system data, to estimate the energy generated per year, specified as full load hours as is customary in the industry . Depending on various factors such as B. Site quality and system design, wind turbines achieve between 1400 and 5000 full load hours. This corresponds to a utilization rate of 16 to 57 percent.
Using computer programs on the Internet, the yield of certain systems can be approximately determined under the conditions to be selected. However, only wind reports based on wind measurements can provide information about the actual yields of a location. The degree of turbulence due to topographical conditions, vegetation, taller buildings or neighboring wind turbines must be taken into account. The reduction in yield due to reduced wind speed and turbulence behind other wind turbines is referred to as wake or lag loss .
Since the range of services increases with the third power of the wind speed, it makes sense to design the system for a significantly higher than the mean wind speed. A wind turbine achieves its rated output , sometimes referred to as installed capacity , at its rated wind speed . In this way, the performance of the system is kept constant in order to avoid overloads. In the event of very high wind speeds ( storms ), the system is completely switched off (for details see below in the section: Control and operational management ).
Given the investment costs, the nominal power can be increased at the expense of the rotor area or vice versa. A system with a higher nominal output uses a larger part of the energy available, a system with a larger rotor feeds more output into the power grid below the nominal wind speed . For onshore plants in Germany, where v. a. Systems with comparatively high nominal outputs are used, an average of around 1640 full load hours have been achieved in recent years, with newly installed wind power systems achieving significantly better results than with older models. Systems built around 2010 achieved almost 2000 full load hours, and systems built in 2013 around 2150 full load hours. It is expected that the full load hours of systems on land will increase to an average of at least 2250 VLS, while offshore 4500 VLS is expected. In other countries the capacity factors are e.g. T. significantly higher. In the USA, where no offshore wind farms were yet in operation in 2015, wind turbines achieve comparatively high capacity factors of 30–40%, corresponding to around 2600–3500 full load hours .
There is a tendency towards higher capacity factors, both onshore and offshore, triggered by greater hub heights and a higher rotor area per kW of installed power. Since around 2010, several manufacturers have also developed so-called low-wind systems with a particularly large specific rotor area (approx. 4.5 - 5 m² / kW) with which significantly more full-load hours than specified above can be achieved even at locations with less wind. The comparatively weaker drive train and generator only lead to minor losses in annual electricity generation, but it reduces the mechanical loads acting on the system, increases the number of full load hours and has a positive effect on the wind power forecast . At the same time, wind power production is stabilizing, the need to expand the power grid is lower and the electricity production costs decrease.
Examples of such low wind systems are the Nordex N131 / 3000 , the GE 2.5-120 or the Gamesa G114-2.0. With hub heights of 130 m and more, such systems achieve over 3500 full load hours under reference conditions; For example, the Nordex N117 / 2400 with a hub height of 141 m is around 3960 full load hours. For the future, it is expected that the trend towards low wind turbines will continue and that the rotor area will continue to increase faster than the generator output. However, even for locations with more windy conditions, it makes sense to increase the rotor area per nominal power in order to increase the full load hours and to reduce costs.
Designs
Depending on the aerodynamic principle that is used to generate the rotary movement, wind turbines are divided into drag and lift rotors.
A drag runner is a type of system whose mode of operation is primarily based on the use of flow resistance , as in the case of the Persian windmill, which can be traced back to the 7th century .
When buoyancy Runner is dynamic lift used. The narrower, profiled rotor blades of these turbines move much faster and across the wind. In this way, a large area can be harvested with less material. In the case of smaller wind generators in particular , this principle has been implemented through various designs, including simple versions of the actual wind turbines discussed in detail in the following chapter, i.e. designs with a star-shaped rotor with a few (usually three) blades that rotate around a horizontal axis in front of a mast or tower . These systems are occasionally referred to in the specialist literature as HAWT d. H. horizontal axis wind turbine (wind turbine with horizontal axis).
The active wind tracking mechanism required for these systems can possibly be omitted in so-called leeward runners, where the rotor runs behind the tower, since the wind can automatically turn the rotor in the correct direction. In practice, however, such concepts are difficult to implement and cause serious problems. This includes in particular the risk of rapid nacelle rotations with the resulting high bending loads on the rotor blades. Successful systems with passive wind direction tracking are only documented in the area of small and medium-sized power, while successful large-scale systems have not been implemented.
Buoyancy rotor can also be with vertical axis of rotation realize ( VAWT according English vertical axis wind turbine ). Among these, Darrieus rotors dominate , which are built up to the medium power range, in the classic 'whisk shape' or as H-Darrieus rotors, the blades of which form a cylinder jacket when rotating. With a vertical axis of rotation, the rotor does not have to track the wind direction. However, in some areas of the circulation the leaves are unfavorable to the flow, the leaf surface must be enlarged accordingly. Cyclical load changes cause vibrations and loads on the entire construction. The additional design effort, together with the performance coefficient of 0.3 on average compared to 0.4 to 0.5 for rotors with a horizontal axis of rotation, explains the low market share.
A design of the H-Darrieus rotor with helically bent blades has a more even torque than the classic H-rotor and therefore does not require any starting aid, as is required for classic Darrieus rotors with a high high-speed speed. Savonius rotors are out of the question for power generation due to their low high speed and low power coefficient, but they are suitable for use as wind pumps .
Design of the rotor
High speed number
A rotor is optimized for the range below the nominal power of the generator. One for the interpretation of any turbomachine important figure is the tip speed ratio (lambda). It indicates the ratio of the circumferential speed of the rotor to the (here) wind speed. With the same high speed, large rotors seem to turn slowly compared to smaller ones. Usual three-blade rotors today have high-speed numbers from 7 to 8. The illustration opposite shows the speed, force and angle relationships for such a high-speed number on a blade cross-section at about 2/3 the radius.
The torque is inversely proportional to , that is, at lower high speeds the torque increases, which necessitates a larger generator or a more powerful gearbox with a higher gear ratio and reduces the efficiency, because the air flow through the rotor is set in rotation. In addition, there are losses due to the flow around the blade tips. This induced drag decreases with the number of sheets and the higher the speed. As the speed increases, fewer blades are required to keep the induced drag at a constantly low level (in principle proportional to , but the number of blades must of course be an integer). Because of the proportionality of the lift to the blade area and to the square of the flow velocity, the higher the speed, the less total blade area (proportional to ) is necessary to harvest the entire rotor area.
A larger blade area than necessary with a lower lift coefficient is avoided because this would lead to increased air resistance. In addition, a smaller area exposed to wind on the turbine, which was shut down in the storm, reduces the mechanical load on the entire structure, from the rotor to the tower to the foundation. However, slender leaves with a small area cause a stability problem. Since the flexural strength and torsional stiffness increase disproportionately with the profile thickness, the entire blade surface is divided into as few blades as possible, taking the above relationships into account.
Without the strength problem, according to what has been said so far, the high speed number would have to be selected very high. However, with a correspondingly flatter angle of attack, an ever smaller proportion of aerodynamic lift becomes effective as propulsion (see figure), while the flow resistance remains roughly the same. At a high speed number that corresponds to the glide ratio of the profile, the profile no longer provides any propulsion (in the outer area of the blades).
Number of rotor blades
For every number of blades and otherwise optimized geometry depending on the high-speed number, there is therefore an optimal high-speed number at which the performance coefficient is maximum. The maximum, however, is quite flat in each case. For one-, two- and three-blade rotors it is 15, 10 and 7 to 8 respectively.
The height of the maximum initially increases with the number of blades, from single to two-blade rotors by around 10%, but only by 3 to 4% for three blades. This small increase alone does not justify a third rotor blade. However, three-blade rotors are quieter and easier to control in terms of vibration than two-blade rotors. The two main reasons for this are:
- Even if, as is common today, the blades are running in front of the tower, the air congestion in front of the tower briefly reduces the angle of attack and thus the lift. An opposite blade is loaded to the maximum at this point in time because there is more wind at the top, so that with a rigid hub a higher alternating load occurs, which must be taken into account when designing the entire system including the foundation.
- The moment of inertia of the rotor around the high axis is twice per orbit very small. Together with any torque around this axis, destructive load peaks can arise. In the proof of safety for the turbine, not only turbulence is considered as the cause of the torque, but also technical failures, such as tracking the wind direction or - even more critical - an error in the control of the pitch adjustment (twisting) in only one of the two rotor blades.
Measures against these load peaks are pendulum hubs , elastic mounting of the entire drive train and an overload-proof drive for wind direction tracking . However, these require higher construction costs and represent a potential source of errors, which can be expressed in greater maintenance and repair costs and thus higher downtimes. After two-winged aircraft played a certain role in the past, nowadays almost exclusively systems with three rotor blades and a rigid hub are built, which are technically easier to control than systems with fewer than three rotor blades and which have therefore emerged as an economically and technically optimal concept in the course of development history.
However, two-winged aircraft have theoretical advantages, especially in offshore use, so that - provided that the problematic dynamic behavior is mastered - there is a possibility that two-winged aircraft will again play a greater role in this area in the future. Noise emissions are less relevant in offshore use, which means that the rotor speed can be increased by dispensing with the third blade and at the same time the necessary gear ratio can be reduced. Simpler logistics and installation would also be possible with two-blade rotors . In offshore use, two-blade systems could therefore have an advantage over three-blade systems for cost reasons, despite the rather negative experience. Drastic cost reductions compared to the standard design, through which the electricity production costs are in a completely different order of magnitude, are considered to be unrealistic. The greater potential for reducing costs lies in larger series and the further optimization of existing concepts. So far, however, there has been no return of the two-winged aircraft, only individual prototypes are being built.
Type class (wind class)
Wind turbines can be approved for different wind classes. Internationally, the IEC 61400 standard is the most common. In Germany there is also the division of the German Institute for Building Technology ( DIBt ) into wind zones. The IEC wind classes reflect the layout of the system for areas with strong or weak winds. Large rotor diameters with the same nominal output are characteristic of light wind turbines. In the meantime, there are systems with a rotor area of 4–5 m² per kW of nominal output, while common strong wind systems are 1.5–2.5 m² per kW of nominal output. Low wind turbines often have an adapted blade profile and a larger hub height.
The reference values are the average wind speed at hub height and an extreme value of the 10-minute average, which statistically occurs only once within 50 years.
IEC wind class | I. | II | III | IV |
---|---|---|---|---|
50-year extreme value | 50 m / s | 42.5 m / s | 37.5 m / s | 30 m / s |
average wind speed | 10 m / s | 8.5 m / s | 7.5 m / s | 6 m / s |
Components and technology of wind turbines
A wind turbine essentially consists of a rotor with a hub and rotor blades as well as a nacelle that houses the generator and often a gearbox. There are also gearless systems. The gondola is rotatably mounted on a tower , the foundation of which provides the necessary stability. In addition there are the monitoring, regulation and control systems as well as the network connection technology in the machine nacelle and in the base or outside of the tower.
- Assembly cycle of a wind turbine
Rotor blades


Today's wind turbines almost without exception have three rotor blades. These are an elementary and defining component of a wind turbine. With them, energy is taken from the flow and fed to the generator. They are responsible for a significant part of the operating noise and are therefore not only optimized for high efficiency, but also for noise reduction, especially near the blade tips (see e.g. trailing edge comb ). As of 2013, the maximum blade length of current wind turbines was around 65 meters in the onshore and 85 meters in the offshore area. The weight of such sheets is about 25 tons. So-called rotor blade adapters are increasingly being used for easier transport , with which the blades can be swiveled upwards on the last transport section when passing narrow roads or when passing through rough terrain. Rotor blades are usually made of fiberglass-reinforced plastic and are mostly made in half-shell sandwich construction with stiffening bars or webs inside. Carbon fibers are increasingly being used in long rotor blades , especially in strong winds and offshore systems exposed to high loads, but also in light wind systems with large rotor diameters. The longitudinal forces are absorbed by belts made of glass or carbon fibers. These belts consist either of continuous fibers, so-called rovings , or scrims .
Since lightning strikes on large wind turbines cannot be avoided, the rotor blades are equipped with a lightning protection system. Near the blade tip there are one or more points made of metal (the so-called receptors) on the surface of the rotor blade. Lightning tends to strike at these. Alternatively, blade tips made of aluminum are used. From there, the currents are derived integrated in the sheet metal conductors on the nacelle and the tower into the ground, wherein the bridging of bearings ( journal bearing , main bearing rotor, the tower head bearing) by radio links or slip rings is realized. Statistically, a wind turbine is struck by lightning every ten years, and much more frequently in exposed low mountain ranges.
With a slight sickle shape in the outer area of the rotor blades, the blade tips give way to leeward in gusts. The resulting twisting of the blades reduces the angle of attack and thus the wind load. Accordingly, material can be saved. In addition, rotor blades can be equipped with turbulators such as vortex generators and serrated bands. A relatively new trend in the design of rotor blades are tubercles on the surface and ridges on the wing trailing edge. These measures enable both an increase in yield by a few percent and a reduction in noise during operation.
One possible phenomenon on the leaves is ice formation . It reduces the efficiency as it changes the shape and thus the aerodynamic profile of the blades. Also imbalance of the rotor can be a consequence. Ice chunks that fall or are thrown away by the rotating movement represent a danger below the rotor blades and in the immediate vicinity. 1.5 times the sum of the tower height and rotor diameter is therefore recommended as a safety distance. The systems switch off automatically when ice forms, which is usually determined by changing the internally recorded power curve (power and wind no longer match due to poor aerodynamics) and by observing the temperature or imbalance on the rotor. Some companies' rotor blades can be equipped with a rotor blade de-icing system. This is intended to reduce the accumulation of ice on the leaves or accelerate defrosting. The heating has an output in the one to two-digit kilowatt range per rotor blade, which is little compared to the power fed in (several hundred to several thousand kilowatts). In some systems, the exhaust air from the nacelle (the generator house on the tower) is pumped through the rotor blades to heat the blades, so that the waste heat from the generator and current transformer is used. Ice breakage has already been documented several times, but no personal injury or damage to property, as it only occurs at low speed or in spin mode after the ice has been switched off due to the deteriorated aerodynamics.
Machine house
In the nacelle, also known as the nacelle, the drive train, part of the electrical equipment, the wind direction tracking , the rotor head bearing and auxiliary equipment such as B. cooling systems, electronics, etc. housed. Although this makes the assembly of the nacelle and the accessibility and maintenance of the units in the nacelle more complicated than with other concepts, this design has established itself as the standard solution due to its advantages (short mechanical transmission paths, few dynamic problems). In older systems, the drive train components are usually arranged one behind the other on a supporting base plate. In newer systems, more and more cast machine carriers are spreading in the front part of the nacelle, directing the rotor loads and the weight of the nacelle directly into the tower, while the generator and auxiliary units in the rear area of the nacelle rest on a lighter sheet steel construction. Oil and hydraulic supply , heating, data acquisition and processing systems, fire alarm and, if necessary, fire extinguishing systems are also installed in the machine house. In many plants there are crane systems with which individual system components can be serviced or replaced without the use of an expensive mobile crane. Environmental sensors are usually mounted on the machine house, and on some offshore systems there is also a helicopter platform.
Machine train
The mechanical drive train includes all rotating parts, i.e. H. Hub, rotor shaft and possibly gearbox. For a long time, systems with mostly three-stage gears and asynchronous generators as well as gearless systems with externally excited synchronous generators were used (the latter almost exclusively by the Enercon company ). Since the end of the 2000s, however, a strong differentiation of the drive trains and a trend towards directly driven wind turbines with permanent magnet generators can be observed. There is a trend towards gearless wind farms, especially with offshore systems.
hub
Although it is also part of the rotor, the rotor hub is the first component of the mechanical drive train. In wind turbines with pitch control (blade adjustment), as they are now standard, the components for blade adjustment are housed in the rotor hub. These include B. the electric or hydraulic servomotors and their emergency power supply, so that the system can be safely braked and switched off even in the event of a power failure. Since the rotor hub is one of the mechanically highly stressed parts of a wind turbine, its manufacture is of particular importance. The rotor hubs of large systems are mostly made of cast steel, especially nodular cast iron, but in the past, designs made of sheet steel or forged parts were also common.
Nowadays, almost exclusively rigid hubs are used in larger series machines. Previously, experiments were carried out with flapping hinge and pendulum hub in order to be able to reduce the mechanical load on the entire system. The disadvantages are the complexity, higher costs and susceptibility to failure. A distinction is therefore usually only made between hubs with permanently installed rotor blades and hubs with a blade adjustment mechanism.
transmission
A transmission gear is used to increase the speed. The faster a generator runs, the smaller it can be designed. Gearboxes are common, but technically not absolutely necessary: Gearless designs were not very widespread until around 2005, since then they have been gaining market share. In the meantime, the gearbox has become a supplier component that, with certain adjustments, is taken over from series production by the manufacturer. In the past, transmission problems often resulted from under-dimensioned transmissions. According to Hau (2014), modern systems are appropriately designed.
Wind power transmissions are usually designed in several stages; the bandwidth ranges from one to four gear stages. While in small systems up to approx. 100 kW pure spur gears are often used, in larger systems due to the high bearing reaction forces in spur gears, planetary gears are used at least for the first gear stage . In systems over 2.5 MW, a planetary gear is also used in the second stage. These usually have three to five planets and thus several points of engagement, whereby the individual components are relieved by the distribution of the torque and at the same time the transmission can be made more compact. A power split can also be achieved in this way.
The last gear stage is usually designed as a spur gear stage so that an axial offset is achieved between the input and output shaft. A hollow shaft enables the power supply and control cables for the pitch motors located in the hub to be easily passed through the gearbox without them having to be passed through the generator.
brake
The drive train also includes a brake , the type of which depends on the choice of rotor blade control. In systems with stall control, the brake must be able to absorb the entire kinetic energy of the rotor and the generator in an emergency. It must therefore be very efficient. Sometimes it is also used as a service brake to keep the rotor speed within the tolerances in gusts of wind . Large disc brakes are usually used for this. Systems with active stall control and pitch control can turn the rotor blades out of the wind and brake them aerodynamically. A mechanical brake system is then smaller or can even be omitted entirely. All systems must be equipped with two independent brake systems. These include independently adjustable rotor blades.
Certification companies such as B. Germanischer Lloyd set specifications for the parts of the drive train with regard to noise, vibration behavior and load profiles. This is of great importance as these parts are subject to extraordinary stresses.
generator
Three-phase asynchronous or synchronous generators are used to convert mechanical power into electrical power . The generator is optimized for service life, weight, size, maintenance effort, costs and efficiency, with interactions with the gearbox and the grid connection. The speed of the generator (and thus of the rotor) can be constant, two-stage (for low and high wind speed) or continuously adjustable. Synchronous generators are required for low speeds, such as those found in gearless systems (so-called direct drive).
Asynchronous generator

Early powertrain concepts
The simplest type of asynchronous generator is one with a squirrel cage rotor . If it is not pole-changing, it can only be operated directly on the mains at one speed: with a number of pole pairs of e.g. B. 2 (i.e. four poles) with the mains frequency of 50 Hertz a synchronous speed of 1500 rpm results . In generator mode, the rotor speed (speed of the generator shaft) is higher than the synchronous speed (lower in motor mode, hence the name asynchronous machine).
With pole-changing asynchronous generators, there is the option of operating the wind turbine at two fixed speeds. The generator accordingly has separate windings, e.g. B. with two or three pole pairs. This means that the synchronous speeds are 1500 and 1000 rpm. The advantage is that the generator can work with high efficiency at both low and high wind speeds. These simple variants with asynchronous generators are generally no longer used today.
Systems with gearbox and double-fed asynchronous generator
Despite increasing competition from gearless system concepts and systems with full converters, wind turbines with gears, double-fed asynchronous machines with slip ring rotors and rotor-side frequency converters are still the most common type of wind turbine Adjustable speed range and thus show a high degree of efficiency. In relation to the generator output, the power that the frequency converter must deliver corresponds only to the relative deviation of the speed from the synchronous speed, usually approx. 30% of the generator power. Since the asynchronous generator requires a high speed, a gearbox is required for this type of construction. Although the stator delivers its power synchronously with the mains in both cases, the reactive power requirement can be regulated via the excitation phase, which means that such drive trains offer advantages similar to those with synchronous generators and full converters.
Synchronous generator
Directly driven systems with separately excited synchronous generator
The use of synchronous generators with frequency converters , due to their significantly higher number of pole pairs of up to 36, means that an additional gear unit can be dispensed with - they can be operated at the speed of the rotor. The advantages of this concept with an externally excited generator are higher reliability and lower maintenance costs. This concept, which quickly established and proved itself on the market, was introduced in the early 1990s with the Enercon E-40 . However, this is also bought with disadvantages: in addition to higher investment costs and the like. a. with an enlarged generator diameter (depending on the rated power between three and twelve meters, the latter for the Enercon E-126 ) and a consequently higher generator weight. Although the higher tower head weight in the power range between 2 and 3 MW does not yet have too great an impact, the high tower head mass and thus the costs for raw materials, construction and logistics are becoming increasingly problematic in multi-MW systems over 5 MW.
As with all synchronous generators operated with variable speed, the frequency of the generated voltage , which fluctuates with the speed of the rotor, must first be rectified into direct current and then converted back into alternating current with a grid- commutated inverter in order to feed the grid with the desired values of voltage, frequency and phase angle to get. The converter must process the full generator power; However, by decoupling the generator and the feed, these systems achieve a high level of efficiency and, given the current state of power electronics, very good grid compatibility .
Systems with permanently excited synchronous generator
Permanent magnet generators (PMG) use permanent magnets and have some advantages over separately excited generators. In addition to a slightly higher degree of efficiency due to the lack of excitation power , their higher field strength allows them to be built more compact and lighter, which benefits in particular gearless concepts with large generators (e.g. from Siemens Wind Power , Vensys , Goldwind ). The use of permanent magnet generators has advantages above all in gearless offshore wind turbines of the multi-MW class, while several other proven generator concepts exist for onshore systems. PMGs are also used in gear systems with compact generators (e.g. from General Electric and Vestas ). The permanent magnets required usually consist of rare earth magnets such as neodymium-iron-boron . Dysprosium can also be added to ensure long-term field strength at high temperatures . Neodymium and dysprosium are rare earth metals and are subject to price fluctuations. The market price risk for manufacturers and the environmental problems associated with the mining and extraction of rare earths are detrimental. The poor controllability that existed in the past has been put into perspective by technical advances in frequency converters .
Fully hydrostatic drive train
At RWTH Aachen University , a fully hydrostatic drive train for wind turbines was examined on a test bench at the Institute for Fluid Power Drives and Controls . With this drive concept, radial piston pumps of different sizes are directly connected to the rotor shaft and the high torque of the rotor blades is converted directly into hydraulic energy. Volume-regulated hydraulic motors drive a synchronous generator running at constant speed, so that no frequency converters are required for grid adaptation. The direct feed-in via a synchronous generator running at mains frequency increases the quality of the fed-in current by means of a pure sinusoidal shape; at the same time, the drive concept as a whole offers the advantage of very good damping properties against high torque surges such as those caused by gusts of wind, which protects the system structure.
Wind direction tracking
The wind direction tracking is done with servomotors (also called azimuth drive or yaw motors ). The wind direction is determined by sensors, so-called wind direction transmitters . The tracking takes place slowly in order to avoid high gyroscopic torques . In order to avoid vibrations of the systems around the tower axis, the servomotors (usually there are several) are braced against each other, or the entire bearing is locked with a brake when it is not in motion. The natural damping of plain bearings is also used.
The electrical connection of the nacelle for control signals and the electricity generated on the inside of the tower is made via freely hanging, torsionally flexible cables. With the high electrical currents, sliding contact rings are too maintenance-intensive. In order not to twist these cables too much, the number of revolutions of the gondola in each direction is limited by the central position. Usual twist angles are 500 to 600 °, which is controlled by twist counters. If the maximum permissible twist is reached, the nacelle rotates a few times around the vertical axis in the opposite direction with the rotor stationary to relax the cable.
Electrics / feed
The electrical equipment can be subdivided into the generator , the system for power supply and the control and monitoring system for the plant operation.
In the older, fixed-speed systems, the generator, partly with an intermediate transformer for voltage adjustment, is directly coupled to the public power grid - it runs at the grid frequency. In the case of an asynchronous generator with squirrel-cage rotor, a device for reactive power compensation is connected in parallel to the generator. In modern systems, the generator speed is decoupled from the mains frequency by means of an AC converter .
With both generator variants , the voltage is finally transformed to the nominal system voltage customary in the respective medium-voltage networks . The wind power plant is connected to the public power grid via circuit breakers, with transducers used to determine the power transmitted. While small systems can feed into low-voltage networks, normal wind turbines are almost always connected to the medium or high-voltage network and must therefore meet the medium-voltage directive to ensure network stability . Proof of network conformity is required for commissioning: the operator may have to a. prove that the applicable guidelines (e.g. with regard to compliance with the line voltage , flicker , harmonics and grid support in the event of brief voltage drops in the network) are being observed.
Modern wind turbines are able to supply balancing energy and take over other system services for the security of the power grid; an ability that becomes more important as the share of renewable energies increases. In addition, wind turbines must be able to provide so-called short - circuit power in the event of a short circuit without disconnecting directly from the grid in order to ensure grid stability. Newer wind farms can be regulated in their entirety.
Systems with pitch control can be operated in stand-alone grids, in which maximum generation is not sought as in the interconnected grid, in accordance with the power demand in load follow mode. In addition, as with conventional power plants, throttled operation is basically possible, which within certain limits enables constant energy feed when the wind decreases.
In addition to providing negative control power by throttling the power, variable-speed wind turbines with full converters are basically also able to feed positive control power into the grid for a short time (i.e. for a few seconds) by increasing the power. In this way, wind turbines with appropriate system control could contribute to the frequency stability of the power grid in both overfrequency and underfrequency. The energy required for this comes from the stored kinetic energy of the rotor and drive train, the speed of which decreases. As of 2015, the first manufacturers are working on equipping their systems with this boost function in order to be able to provide more system services for grid support.
Another important part is the sensors for system control and monitoring. The wind turbines have permanent monitoring of their mechanical components in order to recognize changes and to be able to prevent damage events by taking timely measures (e.g. by means of vibration diagnosis). The insurers of wind turbines require such remote monitoring or condition monitoring systems if the systems are to be insured cheaply.
The systems are connected to a remote diagnosis network that transmits all values and operating states and any faults to a control center. This coordinates all maintenance work. The most important characteristics of a wind turbine can be made available to the owners in special Internet offers. There are also systems that also inform the owner via SMS when starting up, switching off or in the event of malfunctions .
tower
The tower is exposed to high loads at times, which it must withstand safely under all operating conditions. In gusts, the wind load is greater than the weight of the rotor and machine nacelle, the mass of which together can be up to several hundred tons , and in gusts it causes high bending moments , especially at the base of the tower . The higher the tower - a decisive factor for the yield of the system - the wider the tower base. The tower construction takes into account the transport to the construction site, the erection and, if possible, also the dismantling; the towers are calculated for the intended service life of the system. Existing towers can therefore generally no longer be used as supports for more modern system generations after this service life has expired. With the condition measurement z. B. Twenty-year-old towers there is hardly any experience: today's 20 or 25-year-old towers are usually so low that demolition and new construction ( repowering ) seems more attractive than equipping an old tower with a new gondola or new wings.
In the case of small systems, towers with external access, i.e. a ladder on the outside of the tower, were sometimes used. This allowed a slimmer design of the towers, since then the interior did not have to be accessible. Larger systems, with the exception of lattice masts, are generally climbed inside the tower. Towers over 80 meters high have inside next to a ladder with climbing safety often a car or elevator to facilitate the rise. In addition, there is often a cable winch or an on-board crane for material transport.
While relatively small towers are sufficient at coastal locations, around 0.7% additional yield per meter height is expected in the north German inland, whereby the value can fluctuate between 0.5 and 1% depending on the location. The manufacturers therefore offer different tower heights and variants for the same rotor size. A high tower is usually placed on top of one another in individual parts, as it cannot be transported to the construction site in one piece. The individual parts are as large as possible. This applies to both towers made of steel tubes, steel frameworks (see mast section ) and those made of wood (see below), because assembly work on the ground or even in the factory is faster and safer than with suspended loads.
The higher the tower height, the more uneconomical the use of mobile cranes for erecting the tower and assembling the nacelle and rotor. Top-slewing tower cranes with anchoring to the growing tower weigh less, have to be brought to the construction site via narrower access routes and find space and support there on the foundation of the tower, an advantage especially in forest areas.
In some wind turbines, the towers are also used as a location for transmitting antennas for radio services with low power in the ultra-short wave range, such as mobile communications .
Steel towers
A distinction is made between tubular steel towers and steel shell towers . Tubular steel towers are today's standard construction for wind turbine towers. They have a conical shape and usually consist of two to five parts that are screwed together with flange connections . With conventional construction, hub heights of up to a maximum of 120 m can be achieved with them (as of 2014), with wall thicknesses of 10 to 50 millimeters. Pipe sections that are not too large can be manufactured in the factory and then transported by road. The optimal diameter of the tower base is more than 6 m, as larger diameters can save material compared to towers with a narrower base, but conventional construction methods only allow diameters of up to approx. 4.5 m.
However, it is possible to enlarge the base of the tower by screwing together several longitudinal plates instead of rolled towers and thus to achieve greater hub heights. With some manufacturers such as Vestas or Siemens, contrary to the industry trend, an increased use of steel towers can be observed. For example, in 2015 Vestas presented a steel tower consisting of three 120 ° segments with a tower base diameter of more than 6 m and a hub height of 149 m, with which the wall thickness could be roughly halved compared to standard towers.
In these so-called steel shell towers, the tower shells do not consist of a single sheet of metal, but rather several bent and tangentially screwed sheets, so that a polygon is the cross-section. Although this tower variant has a significantly higher number of screw connections compared to tubular steel towers, the folded sheets of the individual tower segments can be transported with relatively little effort. In addition, a large tower base diameter can be implemented so that sheets of less thickness can be used than would be required for a tubular steel tower with a given tower base diameter. Steel shell towers are used as prototypes both as pure steel shell towers and as hybrid towers. Lagerwey builds this steel shell tower with a base diameter of up to 12.70 m for the type L 136 and is testing the construction of this wind turbine with a climbing crane.
Hybrid towers
In the case of high towers, hybrid constructions have so far almost always been used, the lower part of which is made of concrete, whereby in- situ concrete can be used or, which is the usual construction, prefabricated parts that can be connected to rings quickly and cheaply on site. In inland areas, where high towers are required, hybrid towers are the standard tower variant, as conventionally manufactured neither pure steel nor pure concrete towers are economical alternatives. The concrete rings, which are composed of one to three circular segments depending on their position in the tower and are each almost four meters high, are layered on top of one another until the transition to the steel part, whereby the tower tapers with increasing height. In any case, a concrete tower with tendons bias. They can run in ducts inside the concrete shell or on the inside of the wall. The latter has the advantage of being accessible for the purpose of control or even replacement and makes it easier to dismantle the tower. In the hybrid towers, an intermediate piece transfers the tensile and compressive forces from the upper steel section of the tower to the tendons or to the concrete.
Lattice masts

Another tower variant is the lattice mast , which used to be v. a. was built many times in Denmark. Advantages are the lower material requirements and the higher internal damping compared to tubular steel towers. The production is relatively labor-intensive because there are few possibilities for automation. That is why lattice towers are today (2013) v. a. common in countries with low labor costs . The use of guyed masts is also possible.
Wooden towers
Wood is seen as a promising construction material of the future . The spruce wood used for this purpose is readily available and, unlike other building materials, its manufacture does not release any carbon dioxide . In addition, it has a high fatigue strength and therefore has a service life of 40 years, according to the manufacturer, if properly processed. In addition, in contrast to existing towers, it is very easy to transport in 40-foot containers and is completely recyclable . It is expected that wooden towers will be cheaper to manufacture than conventional tower concepts, especially with large hub heights.
With the Hannover-Marienwerder wind power plant , a first prototype was built in October 2012 and put into operation in December 2012. A system of the type Vensys 77 with 1.5 MW is used on a 100 meter high wooden tower from Timbertower GmbH . The wooden tower consists of 28 floors and has a stable octagonal outer wall of approx. 30 cm wall thickness made of plywood. About 1000 trees were felled to produce this tower (approx. 400 m³ of wood = approx. 200 t). The machine house and rotor of the wind power plant weigh around 100 t on the tower. About 70 wire tips protrude from the tower wall to divert lightning. A UV-stable PVC film forms the protective outer skin of the tower.
foundation
The wind turbine must have a high level of stability. On land, a shallow foundation is most often chosen for reasons of cost . In the case of inhomogeneous soil conditions, it may be necessary to replace the soil before the foundation is built to improve the load-bearing capacity. If there are only very soft soils in the foundation level, piles are drilled or rammed into more stable layers and their capped heads are intertwined with the foundation reinforcement ( pile foundation or deep foundation ). Since the piles can transfer compressive and tensile forces, pile head foundations are usually smaller than shallow foundation foundations. However, the significantly higher costs compared to a standard flat foundation are negative.
Since systems with stall control are exposed to significantly higher loads during storm phases than systems with pitch control, which can turn their rotor blades out of the wind, the foundations of stall-controlled systems must be larger with the same output. Therefore, the costs for such systems are up to 50% higher than systems with a blade adjustment mechanism.
There are various procedures for setting up plants in offshore wind farms . Hollow steel piles are often driven in. Small wind turbines can be mounted on individual piles ( monopiles ), three or four are common for larger ones ( tripod / tripile or jacket ). Instead of piles, bucket foundations are increasingly being used, which are introduced by negative pressure instead of noisy ramming. The heavyweight foundation is a flat foundation with a precast concrete part.
There are concepts for wind turbines with floating bodies anchored on the seabed, which differ mainly in how heeling is counteracted. Some prototypes of such floating wind turbines are already being tested (as of 2018). They can be installed on steeper sloping coasts, such as the American west coast or in Japan, but are more expensive.
Offshore equipment

Like all offshore installations , wind turbines in the open sea are at great risk of corrosion from the aggressive, salty sea air . Additional protective measures are therefore taken. This includes the use of seawater-resistant materials, the improvement of corrosion protection , the complete encapsulation of certain assemblies and the use of machine houses and towers equipped with overpressure ventilation .
The offshore conditions must be taken into account when setting up, replacing components and performing on-site maintenance. The system is designed for higher average wind speeds (other wind class). B. makes a corresponding construction of the rotor and its coordination with the generator necessary. Another problem with the location is the vibrations to which a wind turbine can be excited by the sea (waves and water currents). Under unfavorable conditions they can have a self-reinforcing effect, so that their occurrence must also be taken into account in the design and operational management.
Where, as in Germany, most offshore wind farms are not planned near the coast, but usually in the exclusive economic zone at a relatively large distance from the coast in deep water ( see also Law of the Sea ), special consideration must be given to access to the systems . Some concepts also provide for helicopter platforms. The transport of the generated electrical energy to the feed point on the coast also requires special measures. There are high-voltage lines as submarine cables laid, and at greater distances to the feeding especially the direct-current transmission high voltage in the form of offshore HVDC systems is used.
Regulation and management
There are various concepts for regulating the systems, some of which have an impact on the system design and its components. The technical availability of wind turbines has been in the range of 98% and above for about a decade (as of 2014).
Start-up and shutdown wind speed
The wind turbines are started up by the control electronics at promising wind speeds (start-up wind speed) and switched off again at too high wind speeds (cut-off wind speed). The wind speed can be determined by the controller via the anemometer or derived from the speed of the rotor and the output power.
If the wind speed is too low for economical operation, the system is put into idle or spin mode. In systems with pitch control, the blades are turned into the sail position, systems with stall control as a whole (rotor with nacelle) are turned out of the wind. A seizure of the rotor would put more stress on the bearings than spinning with a slight movement. The generator or the inverter is disconnected from the power grid. The control electronics and the actuators for rotor blade adjustment and wind direction tracking then draw their energy from the grid. An emergency power supply allows a safe shutdown (turn blades in the feathered position or brake) in the event of a power failure.
When the wind speed is typically 3–4 m / s ( wind force 2–3 Bft), the control switches the wind turbine on, since only then can significant amounts of energy be released into the power grid. In normal operation, the system is then operated in accordance with the design speed control concepts (see the following paragraphs).
Starting wind speed | 2.5 - 4.5 m / s |
Design wind speed (only relevant for older, fixed-speed systems) |
6 - 10 m / s |
Nominal wind speed | 10 - 16 m / s |
Cut-off wind speed | 20 - 34 m / s |
Survival wind speed | 50 - 70 m / s |
Older systems were switched off suddenly at high wind speeds in order to avoid damage from mechanical overload, which, however, had a negative impact on the safety of the power grid. Pitch-regulated systems turned their blades into the sail position and went into spin mode, stall -regulated systems were turned out of the wind and locked by the brake. Newer systems, on the other hand, are equipped with control mechanisms that gradually turn the blades out of the wind when they are switched off and thus enable gentle shutdown by continuously lowering the feed. Another advantage of this regulation is that both switch-off and start-up times are reduced, which increases electricity yield and grid stability. In addition, some manufacturers equip their systems with so-called storm controls , which prevent rapid shutdown by continuously reducing the speed. In such systems, switching off is therefore only necessary at very high wind speeds in the range of over 30-35 m / s, which are very rare.
Apart from wind speeds that are too high or too low, other reasons can lead to a wind turbine having to be taken off the grid. These include:
- Malfunctions and technical defects
- Maintenance and repair work on the wind turbine or in the distribution network
- Shadows
- icing
- (Temporary) inadequate capacity of the distribution network .
Speed control
A wind turbine works optimally when the rotor speed is matched to the wind speed. The combination of the control concepts for rotor ( stall , active stall or pitch) and generator (constant speed, two-stage or variable) must be taken into account.
Control concepts
In the non-adjustable rotor blade nominal wind speed is by using a "passive stall regulation" above the stall limits the speed. "Stall control" means that the rotor blades are operated well above the angle of attack for maximum lift (angle of attack approx. + 15 °) (see wing profile ). Because of its major disadvantages, this “regulation” is no longer used in wind turbines (WKA) with an output of over 500 kW. With the "active stall control" (adjustable rotor blades), which is no longer up to date, it was easier to keep the speed constant. Today only active pitch control is practically used. This means that the rotor blades are only controlled in the angle of attack range from zero to maximum lift (angle of attack approx. −5 ° to + 15 °). Active servomotors change the angle of attack of the rotor blade depending on the wind speed and generator load. The generator applies a counter-torque to the rotor. If there is more feed into the grid, it slows down more.
- WKA with double-fed asynchronous generators or Dahlander gears or gears with two gears switch the possible rotor speeds to the desired generator speed.
- Wind turbines with a DC converter generate, independently of the speed, "artificially" using thyristors, a three-phase three-phase current of constant frequency. With the pitch control, the aim is not a constant speed, but the optimal speed for maximum aerodynamic efficiency.
- Wind power plants with grid-synchronous generators keep the rotational speed with the pitch control in order to be able to feed a constant frequency into the grid.
- Wind turbines with variable gears (torque converters) keep the speed of the generator constant at different rotor speeds and do not need a power converter.
Variable speed pitch controlled systems
Variable-speed, pitch-regulated systems represent the state of the art in wind turbine construction today. They combine a number of advantages: a .:
- the variable rotor speed, so that the rotor can always be operated at the aerodynamically optimal speed below the nominal power
- lower loads on the transmission due to lower torque fluctuations, especially at high powers
- lower noise emissions during times of weak wind conditions due to low rotor speeds
- Lower torque fluctuations due to the possibility of using the rotor as a flywheel during gusts
On the other hand, the disadvantage is the need for inverters, including their disadvantages, and the greater complexity compared to simpler designs.
A distinction is made between two operating modes: speed control in partial load operation (torque control) and speed control in full load operation (pitch control).
- Torque control
- In partial load operation, it is important to maximize performance. To this end, the blade angle and high speed are optimized. The speed is roughly proportional to the wind speed and is influenced by the counter torque on the generator.
- Pitch regulation
- If the nominal output is reached at the nominal wind speed, the harvest is reduced by turning the leaves with the nose into the wind. This is called pitching . The aerodynamically generated torque is adapted on average to the generator torque. Short-term deviations due to gusts are absorbed by fluctuations in the rotor speed, which in this design is independent of the mains frequency.
These wind turbines do not have a mechanical service brake, but are stopped when switched off via the pitch control and only set for maintenance work.
Grid-synchronous systems with house control
This type of system became known as the “Danish Concept” and was used until the 1990s in the construction of wind turbines with a nominal output of around 500 kilowatts. It consists of a three-blade rotor with non-adjustable rotor blades, the speed of which is coupled to that of the generator in a fixed ratio via the gearbox. The generator runs synchronously with the mains, so the rotor runs at a constant speed. Therefore, the angle of attack of the blades increases with the wind speed and thus the lift. An increasing proportion of the lift becomes effective as propulsion, so that torque and power increase roughly quadratic with the wind speed. Stall control now means that the systems were designed in such a way that, before the maximum permissible torque is reached, the angle of attack becomes so large that the flow stops , i.e. a stall occurs. However, this brought with it a lot of noise.
By using the Dahlander pole changeover on the generator, two speeds in a ratio of 1: 2 can be operated in order to cover the partial load and full load range.
This type of turbine is largely responsible for the wind turbine’s bad reputation in terms of grid compatibility. It is only possible to keep the rotor speed constant within a tolerance range. Gusts of wind can cause short-term feed-in peaks, which lead to voltage fluctuations, voltage and current harmonics in the power grid. This shortcoming could be remedied by variable-speed systems with an inverter . Many of these systems have a mechanical service brake, a large disc brake between the gearbox and the generator, which is used in the event of overspeed to bring the rotor back up to its nominal speed. For safety reasons, an aerodynamic brake, often a so-called blade tip brake, is usually installed. If the rotor over-revs, the end of the rotor blade is pulled out of the blade by the centrifugal force on a helical shaft and placed across the flow, which causes a stall.
Without blade angle adjustment, these systems were often not able to start up independently when there was little wind. Therefore, when the wind speed was insufficient, the generator was used briefly as a motor to set the rotor in rotation.
Grid-synchronous systems with active house control
Wind turbines with active stall control are the attempt to transfer the concept of stall control and grid-synchronous operation without expensive rectifiers and inverters to larger systems up to the megawatt range. In these systems, the stall on the rotor blades can also be controlled by adjusting the blades. Fluctuations in the wind (gusts) can be compensated better than with passive stall control. The blade adjustment works opposite to the pitch control and increases the angle of attack until it comes to a stall. In the event of a storm, the leaves can be turned with the rear edge forward. The system then does not have to be swiveled out of the wind.
own use
For control and regulation, wind power plants require electrical energy, the so-called power plant's own demand . In the case of wind power plants, this own requirement is in the range of 0.35–0.5% of the electrical energy produced. With two 500 kW Enercon E-40 / 5.40 plants built in Eberschwang , with a joint annual production of around 1.45 million kWh, a total of 8000 kWh was determined, which corresponds to approx. 0.55%. A conventional thermal power plant , on the other hand, has an internal requirement of approx. 5% at nominal output.
Lifespan and recycling
Traditionally, most wind turbines are designed for a service life of 20 years. This corresponds to the standards set by the IEC and the DIBt as the lower limit for the certification of wind turbines. In view of the experience with existing systems, however, a service life of 30 years is estimated to be more realistic. A number of new systems are now designed and certified for 25 years; In 2014, Enercon announced a new product platform with a certified service life of 30 years.
With repowering , old systems are replaced by larger, modern new systems. As a result of technical progress, new systems are quieter and more efficient, at the same time they enable higher yields with specifically lower maintenance costs and relief of the landscape through a few large instead of a large number of small systems. Repowering usually only makes sense after an operating period of around 20 years, but in individual cases even considerably earlier.
Wind turbines can continue to be operated over the originally certified design life, provided that proof of operational safety can be provided by independent experts. In Germany, the criteria to be met by the operator for this are laid down in the “Guideline for the continued operation of wind turbines”. Turbine upgrades are offered by several manufacturers in order to simplify the continued technical operation of plants or to enable them at all. Extending the operating time - both the design service life and the continued operation beyond the originally planned service life - is seen as having great potential for reducing the electricity production costs of wind energy.
In a study, the Federal Environment Agency Germany examined whether the reserves to be set up by the wind power companies for dismantling and whether the recycling capacities are sufficient and came to the conclusion that there is not enough recycling capacity, especially for the up to 70,000 tons of fiber composite materials expected per year, while components how concrete, steel and other metals were not a problem. For the year 2038, the study forecast a gap in the dismantling financing of over 300 million euros.
Impact on the environment
Like other structures and systems for energy generation, wind turbines interact with the environment. This includes effects on the animal world, sound emissions , shadows and influencing the appearance of the landscape . In general, wind energy is viewed by nature conservation associations as the most space-efficient and energy-efficient form of regenerative energy generation and its further expansion is welcomed.
Space requirement
The area required by wind turbines is low, the surface sealing is very low in comparison with other regenerative as well as fossil generation types. The vast majority of wind turbines installed today are located on agricultural areas that can continue to be used with almost no restrictions. Around 99% of the area used by a wind farm is still available for arable farming , etc. Only the standing area of the wind turbine and an access path for assembly and maintenance are required. For a current wind turbine of the three megawatt class, a paved but unsealed area of around 2,500 m² must remain free and accessible for maintenance. In addition, some alternative land uses are excluded within a certain radius. The BImSchG does not require a meter distance, but a sound distance: At night, no more than 40 dB (A) may be reached on the next busy house wall. This allows (designation of new residential and industrial areas) are adversely affected by a wind turbine, the municipal development, as approved plants grandfathered enjoy.
A 3 MW system has a foundation area of approx. 300 m². With an annual standard energy capacity of around 6.4 million kWh, this results in an annual production of around 21 MWh / m² of foundation area. This is above the value of a 750 MW hard coal power plant with 4000 full load hours, which, taking into account the outbuildings and coal storage (but without mining areas), reaches values of 15 to 20 MWh / m². With increasing system size, the relative space requirement of wind turbines becomes smaller.
In Germany this problem is tackled with a land use plan and in Austria with a land use plan , so that a "wild growth" of individual plants is avoided. If so-called priority areas for wind energy have been defined in a zoning plan, erection at another location within the municipality or district is not permitted.
Bird and bat rash
In connection with the occurrence of particularly affected large bird species such as red kite , sea eagle , Montagu's harrier , eagle owl and black stork , wind energy poses problems. In order to avoid collisions of birds and bats with wind turbines, it is crucial to include the ecological requirements of the animal species concerned when choosing a location. Monitoring and, if necessary, the use of shutdown algorithms during certain times or other control measures are helpful in reducing the risk of collision.
Birds
Europe
As early as the early 1980s, discussions at the German Growian test facility were held as to whether more birds could be harmed by rotating wings. While it is generally undisputed that birds are killed by wind turbines, the extent of the bird strike is controversial.
In 140 wind parks in northern Spain with a total of 4,083 wind turbines, a total of 732 griffon vultures were found between 2000 and 2006 . However, it was difficult to determine whether the wind farms were directly responsible for the birds found. The additional annual risk of death for griffon vultures breeding in the vicinity (15 km radius) of wind farms was therefore around 1.5%.
The effectiveness of warning systems was evaluated in Switzerland. A bat system with ultrasonic microphones recognized the animals well, in contrast to the optical system for birds with 70 percent false alarms also from insects. Birds are warned acoustically that switching off the turbine would be too slow in both systems.
In 2016, the PROGRESS study Determining the collision rates of (birds of prey) and creating planning-related bases for the prognosis and assessment of the collision risk from wind turbines was published . In this study, a large-scale quantitative study of the collision rates of birds on wind turbines was carried out for the first time in Germany, namely in the north German lowlands, with parallel recording of flight activity through visual observations. The study comes to the conclusion that for most of the species examined no threat to the population could be identified, but for some species the sharp rise in the number of wind turbines in Germany can already have a negative impact on bird populations due to collision-related mortality. Strong regional population declines in the population of buzzards be attributed in part to the use of wind power, a risk of the stock was not apparent. If the use of wind power continues to expand, populations may also decline in other species. The study calls for the effects of bird collisions with wind turbines to be investigated in more detail through further population studies and measures to be developed to avoid conflicts caused by collisions and to support populations of affected bird species through species protection measures.
A comparison of the population development of the red kite carried out in 2019 by the umbrella association of German Avifaunists from 2005 to 2014 with the density of wind turbines in 2015 shows regional differences. There were significant increases in stocks in southwest and western Germany only in areas where there were almost no wind turbines up to now. Significant inventory declines, however, were noted in districts with a high density of wind turbines, for example in Saxony-Anhalt and East Westphalia. On average, there was a highly significant negative correlation between the change in the red kite population and the density of wind turbines at the district level, which means that the number of red kites decreases as the density of wind turbines increases.
A study by the Norwegian Institute for Nature Research carried out on the island of Smøla for over 11 years showed that the number of birds killed was reduced by 72% after one of three white rotor blades was painted black. Large birds and birds of prey, especially eagles and vultures, have benefited the most. The birds can hardly see rotating, pure white rotor blades due to motion blur- like effects. The interspersed black rotor blades alleviate this problem significantly.
North America
In a 2013 meta- study that evaluated hundreds of other studies, it was estimated that wind turbines pose lower threats to bird life in the United States than other forms of energy generation. It has been estimated that wind turbines are responsible for around 0.27 birds killed per GWh of electrical energy due to bird strikes , while coal-fired power stations and the like a. cause an almost 20 times higher loss of birds through mining and pollutant emissions of 5.2 birds per GWh. A study conducted in Canada estimates the number of birds killed annually by wind turbines at approximately 20,000 to 28,300, while in Canada a total of 270 million birds are killed by human activities, 200 million by cats and 25 million by collisions with buildings.
According to a study published in the journal Nature , the number of birds killed by wind turbines in the USA is generally considered to be negligible. Wind turbines would only kill a few thousand birds. However, there is for some birds of prey populations in critical passage areas significant risk. While in the USA at locations used very early on, such as For example, there was a relatively high risk of birds colliding with wind turbines at the Altamont Pass (e.g. due to the construction in regions with a large number of birds and the use of small, very fast rotating systems), the cases of bird strikes at newer wind farms have declined significantly, according to a review published in 2015 Study revealed. There, the deaths are given as 0.02 to 7.36 birds per facility and year, with 20.53 birds cited as the extreme value. Birds of prey were more endangered than other species.
Bats
Bats can also crash on wind turbines. Initially, this phenomenon was observed in the USA as well as in Australia. Later, some investigations were also carried out in Europe to determine the scope and background. Three nationwide research projects deal with methods for investigating and reducing the collision risk of bats on onshore wind turbines (Renebat I to III). The aim of the Renebat I research project was to validate the existing investigation methodology for the occurrence of bats on wind turbines. The aim of Renebat II was the further development of the methods, in particular the test of bat-friendly operating algorithms. The aim of Renebat III is to reduce the amount of data required to determine the risk of bats being hit. The authors of another study estimate that in Germany more than 250,000 bats could be killed by wind turbines every year if no preventive measures such as adapted operating modes are taken.
All species of the species of bats (Microchiroptera) are specially protected species according to the Federal Nature Conservation Act . They are so-called Appendix IV species of the Fauna-Flora-Habitat Directive . With regard to the endangerment of bat species by wind turbines, it is particularly important whether the affected areas are preferred hunting areas or whether the main flight routes run through them.
In Germany, up to April 2013, 17 accident bat species were found on the facilities. This mainly affects the noctule that Pipistrelle and the common pipistrelle . More striking are the victims endangered species Serotine , the lesser noctule , the soprano pipistrelle , the Northern bat and the parti-colored bat . What all species have in common is that they also hunt in open air and at great heights. In addition, collisions seem to occur more frequently during the migration between noctule swifts and rough-skin bats between winter and summer roosts. The exploration and swarming phase that takes place after the nursery has been closed, probably also plays a role, as a result of which the pipistrelle is likely to have accidents at wind power plants more often. Some locations, for example in or near the forest, are considered to be particularly effective. During the migration period in August and September there are more collisions, and certain weather conditions - temperature, wind speed - also favor the bat.
Various strategies can be pursued to avoid collisions with bats. This includes avoiding particularly dangerous locations and switching off the systems at certain times of the year and night at low wind speeds, when the activity of bats is high. Therefore, by increasing the start-up speed, the bat accidents can be drastically reduced with only a small loss of income for the operator. Investigations in 2008 showed that no direct contact between bat and wind turbine is necessary as a cause of death, but that many animals suffer barotrauma , which is triggered by pressure differences, especially at the ends of the rotor blades. Wind turbines are particularly dangerous for both female and young bats.
In a research project on the Baltic coast of Latvia, it was found that bats are probably attracted by the lights that flash red at night on wind turbines. In order to minimize this risk, the authors suggest needs-based lighting .
A British study from 2010 suggests that the light gray that wind turbines are usually painted with is attractive to flying insects, while other colors are less attractive to insects. Since high insect activity attracts insectivores such as birds or bats, birds and bats could be protected by a different coat of paint.
Insect death
A DLR study from 2017 to 2018 came to the conclusion that wind turbines could be a cause of insect death in Germany. The report points out that, due to a lack of research, no statement can be made about the proportion of wind turbines in the decline in insects in addition to other causes such as the use of insecticides and herbicides , monocultures, traffic, contamination, climate change and urbanization and what the main causes are . However, it has been found that wind turbines are responsible for the loss of over a thousand tons of flying insects each year . The researchers attached particular importance to the statement that if the insect population recovered of any kind, the German wind farms would have a significant, negative impact on this recovery. So z. If, for example, the flying insect population recovers to the insect density per cubic meter of air from 2003, the destruction of insects by wind farms will also increase to over 3500 tons per year, according to their estimates.
Against the background of these results, the researchers urge further research in this area and the immediate development of countermeasures for wind turbines and their implementation.
Entomologists rate the DLR calculations inconsistently. Lars Krogmann from the State Museum for Natural History in Stuttgart notes that the insect groups recorded by the Red Lists hardly occur at such heights and that the consequences of habitat loss , monocultures and overfertilization are "much more conclusive and relatively clearly documented". Thomas Schmitt, Director at the Senckenberg German Entomological Institute , suggests (like the study itself) the use of genetic methods in order to be able to determine the species concerned. Professor Johannes Steidle, animal ecologist at the University of Hohenheim , also warns against neglecting the aspect of habitat loss: "The decisive factor for the size of insect populations is not so much whether animals die somewhere but whether they find the right habitat to reproduce." If insects avoid the open sea, insect death rarely occurs with the offshore wind force.
Effects on the local climate
With their rotors, wind turbines mix higher and lower layers of air. This increases the ground temperature on the leeward side of a wind farm, especially at night and in the morning hours. During the day, the ground warmed by the sun generates thermals so that the lower layers of air are mixed even without wind turbines. This warming is limited to the area around the wind farm within a few kilometers. Solar cells also warm their surroundings by absorbing more sunlight on the surface they cover. The increase in ground temperature caused by wind power plants is roughly ten times greater than that of solar parks with the same electrical output.
It was proposed to install very large offshore wind farms, closely spaced up to 100 km from the coast, in order to protect them from cyclones . In addition to the wind speed, the height of the storm surge would also decrease.
Effects at locations in the sea
Offshore wind farms are being planned and built in Europe in order to be able to use the considerably stronger winds at sea . Germany , Denmark , Sweden and Great Britain have already built numerous nearshore wind farms. For example, there are concerns about collisions with off-course ships and adverse effects on marine ecology. The effects of offshore wind farms on marine mammals such as dolphins and porpoises are uncertain. Possible nature conservation concerns are taken into account when planning the location of the parks. The laying of cables from the offshore wind farms to the land could lead to construction measures in the Wadden Sea , which in Germany is almost completely designated as a biosphere reserve and national park (important law here: intervention regulation ).
The concrete effects of large-scale use of offshore wind energy on marine ecology are currently the subject of research; the findings obtained so far indicate that offshore wind farms tend to cause less environmental pollution than onshore plants.
In an investigation of the Egmond aan Zee offshore wind farm , Dutch scientists came to the conclusion that the completed wind farm had a largely positive effect on wildlife . Marine animals could find resting places and protection in the wind farm; the biodiversity within the wind farm is greater than in the North Sea. Although some birds hunting by sight would avoid the wind farm, other bird species did not feel disturbed by the wind farm. However, there were negative effects during construction. However, the noisy hammering in of piles is increasingly giving way to the suction of bucket foundations .
Use of materials and energy balance
Use of resources
In addition to a variety of other raw materials such as For example, copper for the electrical system or GRP or CFRP for the rotor blades, wind turbines are largely made of concrete and steel. The use of resources in the use of wind energy is considered to have been well investigated by a large number of studies and lifetime analyzes (see also table of energy payback time). A systematic summary for the existing German infrastructure, in which wind energy was also examined, was published by the Wuppertal Institute for Climate, Environment, Energy 2011 in the study "Material inventory and material flows in infrastructures".
According to this, the material inventory of wind power plants in Germany in 2009 was approx. 14.5 million tons, with concrete making up the lion's share with approx. 9.9 million tons. This was followed by steel with 3.6 million t, GRP with 0.37 million t and cast iron with 0.36 million t. The assumed recycling rates for complete turbines vary between 80% and 100%. Compared to other types of power plants, the use of energy-intensive metal in the production of wind turbines is 28.5% above average. For example, the stock of materials in German coal-fired power plants was 17.0 million t, with 14.5 million t being made up of concrete. In this comparison, however, neither the fossil fuel requirements of the thermal power plants are taken into account, nor that lignite power plants produced around three times as much electrical energy as wind power plants in 2012 .
The recycling of wind turbines is a statutory duty for the owners and should be guaranteed by mandatory reserves. In an extensive study in 2019 , the German Federal Environment Agency came to the conclusion that Germany was not adequately prepared for the increased dismantling from 2021. For the year 2038, it forecast a funding gap of 300 million euros.
Energy payback time
The energy payback time (energetic amortization time) describes the time it takes for a power plant to generate as much energy as was required for its production, transport, construction, operation, etc. The energy payback time for wind turbines is around three to seven months and, even according to conservative estimates, is well under a year. The electrical energy produced is usually compared with the primary energy saved . One kWh of electrical energy is about three times as valuable as one kWh of thermal energy , since the conversion efficiency is around 0.3 to 0.4. Due to the conversion efficiency of 0.8 to 0.9, the thermal energy can be roughly equated to the primary energy. In terms of energy, only power plants that use renewable energy sources can amortize , since power plants using fossil fuels constantly consume non-renewable energy supplies.
While initial investigations from the pioneering days of wind energy use (1970s and early 1980s), based on immature test systems with only a few operating hours, definitely led to the conclusion that energetic amortization is hardly possible, numerous studies from the late 1980s to in the present that today's mature series systems amortize energetically in a few months. However, there are certain differences in the results of the various studies. On the one hand, this is related to the widely differing, location-dependent energy yields of wind turbines, and on the other hand, to the life cycle considered. In addition, the accounting methods often differ. So was z. B. in old studies only considered the manufacture of the system. In modern life cycle analyzes , on the other hand, the energy required for transport, maintenance over the lifetime and dismantling are included.
In the literature, the information on the harvest factor fluctuates between a factor of 20 and 50. The harvest factor results from the operating time of the system divided by the energetic amortization time. Ardente u. a. determined in their work for an Italian wind farm a primary energy-weighted harvest factor of 40-80 and stated that even under the worst conditions the energy payback time is less than one year. From these values they conclude that wind farms - also compared to other regenerative energies - are among the most environmentally friendly forms of energy generation. A systematic review article published in 2017 in the specialist journal Renewable Energy , which evaluated 17 studies published since 2000, came to the conclusion that the energy payback time of wind turbines is mostly less than a year. For onshore plants, the energy payback time was between 3.1 and 12 months, on average 6.8 months, for offshore plants 4.7 and 11.1 months, with average values of 7.8 months.
Hau gives detailed data for a system with a nominal output of 1 MW and a rotor diameter of 53 m. The manufacture of such a system therefore requires a primary energy input of around 2 million kWh, with around 1.6 million kWh being used for steel production. The annual standard energy capacity of this system is 2.4 million kWh electrical , corresponding to 6.85 million kWh of primary energy . The energetic amortization time is therefore 3.4 months, the harvest factor for an operating time of 20 years is 70.
Type | Energy payback time |
---|---|
Offshore wind farm 2010; 200 MW (40 × REpower 5M ) recording of entire life cycle, including grid connection | 5 months |
Wind turbine Enercon E-66; 1500 kW, 66 m rotor diameter; Mixed analysis of manufacture, assembly and dismantling, maintenance | 3.7-6.1 months |
Gamesa G80 / 2MW wind turbine with 2000 kW, 80 m rotor diameter and 70 m tower; full life cycle | 0.58 years (approx. 7 months) |
Wind power plant Enercon E-82 E2 with 2300 kW, 82 m rotor diameter and 97 m concrete tower; full life cycle | 4.7-6.8 months |
Wind power plant Enercon E-82 E2 with 2300 kW, 82 m rotor diameter and 107 m hybrid tower; full life cycle | 4.4-8 months |
Wind power plant 2 MW, 90 m rotor diameter; (Transmission); Manufacturing, operation and dismantling | 7.2 months |
Wind power plant 1.8 MW, 70 m rotor diameter; (Gearless); Manufacturing, operation and dismantling | 7.2 months |
Wind power plant 2 MW, 78 m rotor diameter, manufacture, operation and recycling | 5.2 months |
Wind power plant 2 MW, 80 m rotor diameter, manufacture, operation and recycling | 6.4 months |
Use of rare earth magnets
According to estimates from 2011, synchronous generators with permanent magnets made of neodymium-iron-boron are used in around one sixth of wind turbines . Also dysprosium can be added. The elements neodymium and dysprosium are among the so-called rare earths , 90 to 97% of which, depending on the study, are mined and processed in China with considerable stress on the environment and the health of residents.
In 2007 around 62,000 tons of neodymium were in circulation, of which around 10,000 tons were installed in wind turbines. However, their large magnets are easy to recycle, while recovery from products in which neodymium is distributed in small pieces and very diluted, such as computers, cell phones and audio systems, is problematic. Nevertheless, some wind turbine manufacturers such as Senvion and Enercon expressly point out that no neodymium is used in their generators. After price spikes in 2011, other manufacturers such as Vestas and General Electric , who previously used rare earth magnets in their systems at times , returned to double-fed asynchronous generators in many of their systems . In 2013, as part of an increase in output, Vestas also presented new system types that use (neodymium-free) asynchronous generators with full converters. Permanent magnets are still used for attachments to the steel tower. To reduce the proportion of dysprosium in the generators to below 1%, z. B. Siemens Wind Power on a special cooling.
Accident risks
The use of wind energy is a very safe technology, both in terms of the frequency of occurrence and the severity of accidents , especially in comparison to other types of energy generation. Accidents also occur with wind turbines, but since they are mostly far away from settlements and accidents occur mainly during phases of storms, apart from work accidents during installation and maintenance, there are usually no personal injuries. In addition to lightning strikes and defective rotor blades, tower contacts in extreme gusts are reasons for accidents. A system can overturn or parts of the rotor blades can be lost. In Central Europe, around 40,000 wind turbines have so far registered around 15 broken blades (as of early 2014). The effects of accidents are limited and only local, for example the surrounding vegetation can be damaged by breaking off rotor blade parts.
Systems can also catch fire, although fires can usually only be fought by the fire brigade in the lower tower area. A fire protection system is now installed as standard in many systems in order to be able to fight fires in the mechanics and electronics. As a result of fires, substances can be released locally, as is also possible with other energy technologies. In order to avoid environmental pollution from oil leaks , wind turbines with oil-lubricated gears are equipped with collecting trays. Typically stronger winds prevail at locations, which can fan the resulting fires. As of October 2013, at least 100 of the 28,000 wind turbines installed in Germany were completely lost due to fire.
The rotor blades of old turbines without ice detection can accumulate ice in appropriate weather conditions, which can peel off in the event of a thaw when the turbine is stationary and as an ice throw when the turbine is approaching. The probability of being damaged by ice throwing a wind turbine is largely negligible and roughly corresponds to the probability of being struck by lightning. All modern systems have ice detection based on temperature, wind sensor status, wind speed and performance data, so that they switch off automatically when icing up. When the system is free of ice again (outside temperatures above freezing point), the system starts up again automatically in automatic mode. In manual mode, it must be put back into operation by the windmill operator or service personnel on site (if necessary after a visual inspection ). With rotor blade heating, defrosting can be accelerated after an ice build-up after a standstill. In corresponding climatic zones, the yield can be increased significantly by heating the rotor blades during operation.
Ice shedding can be observed more often (with hoar frost, less often freezing rain), but no personal injury or property damage has yet been documented. The throwing distance (system goes into spin position when icing up) is usually small, whereby the following applies: the more compact the pieces of ice, the closer to the system (e.g. after freezing rain), the lighter, the further they are carried by any gusts of wind - as relevant Distance, the rotor tip height can be assumed (= approx. 45 ° angle of fall). In icy weather or thawing weather, staying under wind turbines as well as under other tall buildings or structures - for example overhead line masts - should be avoided. Usually signs on the access routes warn of the danger.
The accidents described can endanger infrastructure objects that are in the immediate vicinity of wind turbines. With regard to this hazard, the authorities or operators of these infrastructure objects require minimum distances, which are usually determined from the maximum distances from the theoretical effects of these accidents. Alternatively, the risk can be assessed using probabilistic considerations. The result of these considerations is the assessment of the hazard or the specification of minimum distances for normal cases in specific projects.
In January 2019, the Association of Technical Monitoring Associations (VdTÜV) described wind turbines as ticking time bombs and called for a nationwide uniform test for all systems. Due to the age of the wind turbines, personal injury was feared in the future. The VdTÜV currently assumes around 50 serious accidents, such as kinking towers, breaking rotor blades and burning nacelles per year in Germany. The Federal Wind Energy Association, on the other hand, speaks of an average of seven accidents per year since 2013. Data on accidents have not yet been documented in Germany.
Impact on society
social acceptance

A survey carried out in a total of 24 countries worldwide in 2011 showed that 93% of those questioned supported the expansion of wind turbines.
Germany
In Germany, too, there is a broad consensus among the population that renewable energies should play the leading role in a future energy system. The third annual Forsa survey on the acceptance of renewable energies in Germany was carried out in 2009. It was representative and resulted in, among other things:
- The acceptance of wind turbines is also high in one's own neighborhood
- the more experience the population has already gained with wind turbines, the greater the acceptance of new systems
- Those who already know renewable energies from their own environment rate it above average: 55 percent of the total population have a positive opinion of wind power plants; in the group that have wind turbines in the neighborhood, the approval rate is 74 percent
These results have been largely confirmed by further surveys since then. However, especially when building wind turbines in advance, in view of the feared disadvantages, there is often local resistance, which is often referred to as the Nimby phenomenon. In the meantime, this concept has been clearly criticized in the scientific debate, as a number of studies have come to the conclusion that a core element of this thesis, the so-called “proximity hypothesis”, does not apply. This assumes that the closer the residents live to the wind turbines, the greater the resistance. In reality, however, the exact opposite is often observed, i.e. that the support from wind turbines increases with increasing proximity. In addition, further studies suggest that the support increases after the systems are installed. The possibility of participation also has an influence on the approval. If municipal participation in the systems is possible, this leads to significantly higher acceptance values among the population.
Nevertheless, citizens' groups are formed in some places . In addition to initiatives that generally reject the use of wind energy, there are initiatives that only reject specific systems in the vicinity, but in principle support the use of wind energy. Criticisms are z. B. the distance between the systems and residential development, a change in the landscape that is perceived as disadvantageous and the impairment of animals such as birds and bats.
Some citizens' groups claim that the World Health Organization would require a minimum distance of 2000 meters to residential developments. When asked, the organization said it had not issued a wind turbine noise policy. It merely referred to a recommendation by the Canadian Ministry of the Environment and the general noise guidelines of the WHO.
Switzerland
A study by the University of St. Gallen published in November 2015 found a clear majority of those surveyed in Eastern Switzerland who accepted the development of wind power both nationally and in their own area.
health
A meta study by the Federal Environment Agency in Germany came to the conclusion in 2016 that the health hazards of wind turbines are to be assessed as "very low" and that technical regulations ensure this today. The study examined the effects of audible sound, inaudible sound, shadows and strobe effects, light emissions, ice throw and subjective perceptions. According to the Federal Immission Control Act (see also Technical Instructions for Noise ), the noise immission caused by a technical system in Germany in purely residential areas must not exceed an A-weighted continuous sound pressure level of 35 dB at night (general residential area 40 dB, village and mixed area 45 dB, commercial area 50 dB). The values are higher during the day. For areas not stipulated by building law (e.g. single farmsteads in the outdoor area), the values for mixed areas are used according to current case law. When applying for a building application for a wind power plant, as part of the approval procedure, in addition to a mathematical prediction of the expected noise emissions, a consideration of the possible effects of the shadow cast must be submitted.
Shadows
The shadow cast is perceived as uncomfortable because the shadow of a wind turbine, in contrast to the shadow of immobile objects, causes periodic fluctuations in brightness at the immission location. The cause is the rotating rotor. The shadow of a standing wind turbine, on the other hand, is no different to the shadow of a normal building. The occurrence of shadows depends on the location and size of the wind turbine, the location of the immission point, the nacelle orientation and the proportion of direct radiation in the global radiation .
According to the Federal Immission Control Act , shadows (also called hard shadows) by wind turbines in Germany may not be more than 30 hours per year and 30 minutes per day on (existing) residential buildings. These limit values apply regardless of the number and size of the system. The annual limit value is a theoretical value that results from the assumption of constant wind, operation, sunshine and maximum shadow projection. In Germany, the ratio of real to geometric shadows is around 1 to 4, so that there are real loads of around eight hours per year per immission point. These must be adhered to via measuring and control devices in the systems (shadow impact shutdown module).
In particular, the flickering shadow of the rotating rotor is often perceived as annoying. Systems in which expert reports for approval show that the limit values have been exceeded are now equipped with a sunshine and weather-dependent shadow control system, which ensures compliance with the limit values through the automatic temporary shutdown of the systems.
The "disco effect" describes periodic light reflections by the rotor blades, it is often confused with the appearance of shadows cast by the rotor. It mainly occurred in systems from the early days of wind energy use, when glossy paintwork was still used on the rotor blades. The surfaces of the systems have long been provided with matt (non-directionally reflective) paintwork. Therefore, the disco effect no longer plays a role in the immission assessment by modern wind turbines.
sound
The sound of wind turbines is mainly the wind noise of the rotor blades turning in the wind. The A-weighted sound power level is determined by means of acoustic measurements using standardized methods. Typical values are around 95 dB for small wind turbines up to 100 kW and 105 to 107 dB for multi-megawatt systems with a rotor diameter of up to 130 m. Older two-bladed rotors reached z. Sometimes significantly higher values. If the system is assumed to be a point source of sound for the purpose of predicting the sound immission at distant locations and the sound propagation in all directions is assumed to be uniform, the sound level at the immission location drops by 6 dB when the distance is doubled. However, this is an idealized idea. In reality, the value is significantly influenced by the wind direction and can therefore be higher or lower.
The greatest perceptibility is assumed at 95 percent of the nominal power, i.e. at wind speeds between around 10 and 12 m / s at hub height. At lower wind speeds, the sound power levels are lower; at higher wind speeds, they are overlaid by the ambient noise, which continues to increase in volume .
Variable speed wind turbines can be brought into a noise-reducing operating state in order to take into account the residential areas in the vicinity at certain noise-sensitive times, usually at night. Such operating modes are offered by almost all manufacturers for their systems. Since the noise emission is particularly dependent on the blade tip speed and - if available - the gearbox, the system is operated at a suboptimal speed. The reduction of noise emissions is one of the main objectives in the further development of the systems, and great progress has been made in this area in recent years. By dispensing with a gearbox, better structure-borne noise decoupling through the installation of elastomers at support points, soundproofing of ventilation shafts and aerodynamics, noise emissions can be greatly reduced. Individual tones, for example caused by locking frequencies in the gearbox, and impulsiveness, which justify a surcharge of up to 6 dB (A), no longer occur in modern systems due to structural measures.
Low-frequency vibrations such as infrasound occur primarily in systems with house control, which are no longer built today. To a small extent, they can also be demonstrated in modern systems with pitch control . This infrasound is no longer perceptible even at a short distance from the systems. The distances between wind turbines and buildings required by the TA Lärm in Germany do not pose any danger to residents. Wind generates much more intense infrasound in your own house than a wind turbine or a wind park at a legally prescribed distance.
A special feature is the phenomenon of amplitude modulation , for which the first measurement results are now available. This phenomenon was investigated at mean levels between 46.2 and 29.7 dB and distances between 550 and 1000 meters at several wind farms.
Subject to reliable scientific bases, the World Health Organization (WHO) recommends that the noise immission from wind turbines on a 24-hour average should not exceed 45 dB.
Obstacle marking
The obstacle signs required for wind turbines with a height of more than 100 meters serve the safety of air traffic. The daytime identification consists of two red stripes on the rotor blade tips, the nighttime identification consists of red lamps on the roof of the nacelle. These beacons work with fluorescent tubes in old systems, with light emitting diodes (LED) or flash lamps in newer systems . With their characteristic flashing pattern, they can have a disruptive effect on residents, especially when there are large groups of systems. Recently, the warning lights can be dimmed when visibility is good.
There are now radar-based lighting systems that only switch on when an aircraft is nearby. Tests with such a system, which was jointly developed by Enertrag and Airbus , began in 2012, and in 2015 it was approved by the German authorities. At least four radars must be installed per wind farm. Their transmission power of 4 watts is only about twice that of a cell phone . This means that obstruction lights do not need to be used for approx. 98% of the time. First major projects to retrofit the system in existing wind farms are ongoing; For example, around 90% of all wind turbines in the Uckermark district are to be converted from permanent lighting to demand-controlled lighting in 2017 [out of date] . Since March 2017, a total of 23 wind turbines in Schleswig-Holstein have been equipped with the airspex system. As an incentive for equipping with such a system, a discount on the replacement payment for the landscape image intervention is possible for old and new systems.
Landscape image
When it comes to the aesthetic evaluation of wind turbines, subjective perception, habituation and social attitudes, especially landscape ideals, play an important role. The aesthetic assessment of wind turbines is extremely controversial: some see them as an enrichment of the landscape, others as an impairment, especially the uniqueness and naturalness of landscapes. Is criticized u. a. a mechanization / industrialization of the landscape. Because of the mostly slender towers of the wind turbines, in this context one speaks disparagingly of an asparagus of the landscape.
Wind turbines in the vicinity of stationary radars are subject to additional construction restrictions. Air traffic control in civil air traffic control is impaired by its moderate angular resolution in elevation for objects above wind turbines. The protected area of the systems is up to 15 km. Military airspace surveillance, which is also interested in low-flying objects, can be impaired in terms of range, target detection and location by shading and diffraction on wind turbines. Within the 50 km area of interest, the plant planning is subjected to an examination by the Federal Office for Infrastructure, Environmental Protection and Services of the Bundeswehr.
The aircraft systems for terrestrial radio navigation are easier to irritate. The German air traffic control defends an area of 15 km radius around (D) VOR radio beacon .
Real estate prices
Citizens' groups often fear a permanent decrease in the value of real estate due to the construction of wind turbines. 2003 was z. For example, the Association of German Brokers has reported long-term losses in value: “Numerous properties in the vicinity of WKA are practically unsaleable.” Furthermore, in Lower Saxony and Schleswig-Holstein it is complained that “some houses have been offered for years at discounts of up to 40 percent. “There aren't even any interested parties for these properties. The real estate economists Philippe Thalmann from the University of Lausanne and Günter Vornholz from the EBZ Business School in Bochum contradict this representation . According to Thalmann, however, this fear of a price decline often only triggers the actual price decline in the form of a self-fulfilling prophecy. In particular, there was a temporary collapse in property prices where there was great resistance to wind turbines. However, according to Vornholz, this price drop will only last for a short time, as the debate would initially deter potential investors. However, once the wind turbines have been installed, when people have got used to them, the value of the property will stabilize again at the previous level.
However, reference is also made to the methodological difficulties in differentiating the influence of wind turbines from other factors such as economic or demographic development. In addition, knowledge deficits are pointed out, for example in 2015 by an employee of the environmental agency of the city of Dortmund.
tourism

Particularly in regions that are important for tourism, there are often fears that they will have a negative impact on tourism and that the number of overnight stays will fall. However, such effects have not yet been scientifically proven.
In 2005, the Bremerhaven University of Applied Sciences, under the project management of Michael Vogel, on behalf of WAB 840, interviewed randomly selected people in eleven tourist-relevant North Sea communities with wind turbines in the vicinity. In doing so, 20 hypotheses should be verified or falsified that were previously specified by the WAB. The study came to the conclusion that wind turbines were not without controversy, but on average they were not perceived as annoying. T. would be seen as characteristic of the North Sea coast. Wind turbines were seen as more useful for future energy supply, and people were more positive about wind turbines the younger they were or the further away they lived from the turbines. The main reason for rejection was feared noise pollution for optical reasons, and a few large systems were more widely accepted than many small systems. Employees in the tourism industry or people with acquaintances in this industry saw wind farms more positively than the average of the respondents. They also do not fear rejection from tourists and thus falling overnight stays.
In 2012, the Institute for Regional Management carried out a representative study on behalf of the Hohes Venn-Eifel Nature Park , in which 1326 people were interviewed, 159 of them residing within the Nature Park. According to this, 59% of the respondents found the wind turbines not to be disruptive, 28% as disruptive but acceptable. 8% found them annoying and 4% very annoying. 91% of those questioned stated that they would come back if there were any additional wind turbines built, 6% found this so annoying that they would forego another visit. 53% favored a concentration of plants, while 37% preferred a broader distribution across the country. In addition, wind turbines were judged to be important for Germany's future energy supply. 63% found wind energy to be very important, 32% to be of average importance and 4% to be unimportant. In this study, too, a correlation could be established between the age of the respondents and the acceptance of wind energy: while of the respondents under 20 years of age almost 80% rated wind turbines as non-disruptive and almost no one as disruptive or very disruptive, the respondents were over 59 years old the proportion of respondents who did not find wind turbines to be a nuisance was only between 40 and 50%. Approx. 30% of the respondents rated wind turbines in this age group as annoying but acceptable; the number of those who found wind turbines very annoying remained below 10% in all age groups.
In certain regions the use of wind energy is consciously integrated into the local tourism offer. In some places there are z. B. tourism trails, wind hiking trails, wind energy cycle paths or the like. There are also a few wind turbines with viewing platforms that tourists can climb and are often combined with a visitor information center. In Pfaffenschlag near Waidhofen an der Thaya , Lower Austria , a local wind turbine operator installed a machine house (nacelle and hub) of a wind turbine on the ground for inspection from the inside.
Framework
Basis for approval
In Germany, the approval of wind turbines is usually carried out in two separate administrative procedures . First of all, areas are identified where the use of wind energy is suitable and desired. In the second step, the approval for the construction and operation of the plant takes place.
Planning law in Germany
In national development programs of the provinces expansion targets can be set. The regulations of state planning in Germany apply . In the regional planning, the expansion targets are specified and areas for onshore wind power use are specified. If such determinations have been made, the use of wind power outside these areas is not permitted. The spatial control of the use of wind power can also be carried out in smaller parts at the municipal level. Then the municipalities define areas for wind power in the zoning plan . In order to avoid contradictions in state and land use planning, the countercurrent principle applies (spatial planning law) . The federal states of Schleswig-Holstein , Lower Saxony and Mecklenburg-Western Pomerania can also define marine areas for offshore wind farms in the coastal sea . If spatial control has not taken place in a planning area or has become ineffective, the use of wind power is permitted everywhere. Because the use of wind power is a privileged construction project .
The spatial control of the offshore wind farms in the EEZ of the North and Baltic Seas was carried out using two spatial plans that the Federal Ministry of Transport, Building and Urban Development decreed in 2009. Since 2012, the plans have been supplemented by the Federal Offshore Plan of the Federal Maritime and Hydrographic Agency ( BSH ). Since 2017, the BSH has been responsible for the overall planning process for the areas, including development and preliminary studies.
Approval law in Germany
Every single wind turbine on land with a total height of more than 50 m requires a permit. The construction and operation of a wind turbine therefore require a permit . The approval process has been based on the Federal Immission Control Act since July 1, 2005 . Older wind turbines have been approved in accordance with building regulations . Offshore wind farms in the territorial sea are also approved under immission control law. Offshore wind farms in the EEZ of the North and Baltic Seas are subject to marine facility law and the responsibility of the BSH.
Small wind turbines
The approval of wind turbines with a height of less than 50 meters is not based on the Federal Immission Control Act, but on state law. In each federal state there are different regulations for building permits for small wind turbines. Some federal states have switched to foregoing a permit requirement for small systems up to 10 meters in height.
Electricity production costs and funding
The electricity production costs of wind turbines depend on the quality of the location. However, they are on a similar level to thermal power plants , the costs of which will continue to rise in the future due to increasing fuel costs . According to Fraunhofer ISE , wind power plants with LCOE of up to 4.5 ct / kWh are already able to produce more cheaply than most conventional power plants (as of 2013) at very good onshore locations . As the quality of the location decreases, the levelized costs rise, so that wind power plants in very poor locations are even more expensive than coal and gas power plants at up to 10.7 cents / kWh . Offshore plants are z. Sometimes well above these values.
Similar values can be found in the literature. Gasch u. a. call z. E.g. for an exemplary wind farm, electricity generation costs of 6.5 ct / kWh, which can drop to 5 ct / kWh with 10% better wind conditions. In their work, published in 2009, Kaltschmitt and Streicher indicate between 6 and 9 cents / kWh for Austria. At the best locations, the electricity production costs of wind turbines are now around 40–50 US dollars / MWh (33.9–42.4 euros / MWh), although these are also heavily dependent on the quality of the location and the financing conditions; in the USA, onshore wind power plants are already the second cheapest power plants after gas-fired combined cycle plants. In the long term, it is assumed that wind energy will develop into the cheapest form of electricity production worldwide.
Since investments in wind turbines and other alternative energy sources have been and are being promoted in many countries, the annual new installed capacity has been increasing for decades. While research funding dominated in the early days, feed-in tariffs are widespread today , for example in the German Renewable Energy Sources Act . Other funding mechanisms are tax breaks and minimum quotas for electricity from renewable sources.
Prices
The prices for wind turbines are subject to normal market fluctuations. On the one hand, the providers keep a low profile, on the other hand, individual framework conditions must be taken into account. These include, for example, the building site , the infrastructure (access to the construction site, distance to the power grid), regulations on power quality and noise emissions, etc. and, depending on this, the technology used (type of foundation, type of feed, etc.). Gearless systems are generally more expensive to install than conventional wind turbines with gear, but they are more reliable, require less maintenance and are quieter.
Hau named exemplary values for two onshore wind turbines, each with a nominal output of 3 MW, a rotor diameter of 100 m and a hub height of 100 m, but with different technical concepts: According to this, the imputed sales price of a variable-speed gear unit with a double-fed asynchronous generator and partial converter is 3,058 .500 euros or 1,019 euros / kW A variable speed gear -less system with permanent magnet generator and full with otherwise identical specifications costs approximately 3,305,250 euros and 1,102 euros / kW. In addition, there are costs for the construction of access roads, foundations, grid connection, project planning , environmental reports, ecological compensation measures, etc .; so that the installed costs, i. H. the cost of erecting a ready-to-use wind power plant is around 125–135% of the plant price ex works. Offshore wind power plants are more expensive than onshore plants, in particular the ancillary installation costs are significantly higher offshore than onshore.
Research and Development
Since wind energy technology is still relatively new and, accordingly, great technical advances still have to be made, wind turbine manufacturers invest a relatively high proportion of their sales in research and further development. Since wind turbines have been manufactured in large numbers, state research in universities and research institutes has also increased. In Germany z. Examples include the German Wind Energy Institute (DEWI) , founded in 1990, as well as the Fraunhofer Institute for Wind Energy and Energy System Technology , which deals with application-oriented research. Examples of internationally important research institutes in the field of wind energy are the US National Renewable Energy Laboratory and the Danish Risø DTU . Important international scientific journals in which research work on wind turbines is published are e.g. B. Wind Energy , Renewable Energy, and Renewable and Sustainable Energy Reviews .
The central starting point for the further development of wind power plants is the further reduction of the electricity production costs in order to achieve full competitiveness with fossil power plants. According to a review study published in 2015, this goal should be achieved in the near future. The technical advancement includes above all cost reductions through more efficient series production and greater use of machines, especially for the Some of the rotor blades made by hand. In the case of rotor blades, there is a trend towards ever larger wing lengths, which are intended to increase the yield per turbine and reduce the cost of electricity. In order to keep the loads due to the increasing dead weight low, this is u. a. researched the use of lighter and more stable materials such as CFRP, which, however, have different technical properties than the more widely used sheets based on GFRP. In addition, new profiles, divisible wings for easier transport and “intelligent” blades are a research goal. In addition, the development of less windy regions with special low-wind systems is moving into the focus of manufacturers and research.
New drive train and generator concepts are also being developed. Generators with excitation by high-temperature superconductors and a correspondingly high energy density are particularly promising for offshore systems with high outputs . Compared to conventional construction methods, significantly smaller and lighter generators can be built with high-temperature superconductors, which promise cost savings.
Another focus of research is offshore wind power plants, which in Germany was accompanied by the installation of the FINO research platforms . Is examined z. B. their influence on the ecosystems off the coast. There are increasing considerations for offshore wind turbines with only two rotor blades, since it would be much easier to set up such systems at sea. With floating wind turbines , waters of more than 50 m depth are to be developed, with which much larger areas of the oceans could be opened up for wind power use. Several prototypes already exist, but commercial projects have not yet been implemented. The challenges are economic efficiency due to the expensive floating foundation structures and the complex dynamic behavior in rough seas.
Flying wind power plants, so-called air wind power plants, are also the subject of current research.
International records reached

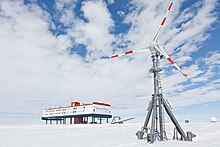
- The oldest windmills in the world are in Nashtifan in Iran and are listed as World Heritage. They are so-called " Persian windmills " (Asbads).
- The oldest modern wind turbine Tvind has been operating since 1975 and is located in Denmark
- The most powerful wind turbine type is the Haliade-X from GE Wind Energy with a nominal output of 12 MW .
- The tallest wind turbine is also the Haliade-X. This type of turbine has a rotor diameter of 220 m and was built in Rotterdam with a hub height of 150 m, giving it a total height of 260 m.
- The Haliade-X also has the largest rotor diameter at 220 meters.
- The world's most powerful wind power plant with a two-blade rotor has an output of 6.5 MW and a rotor diameter of 130 m. It was developed by the German company Aerodyn Energiesysteme and built by Ming Yang at the end of 2014. There is also a variant with 6 MW and 140 m rotor diameter.
- With a total height of 110 m, the largest wind turbine with a vertical axis was the Éole, built in 1988 in Le Nordais , Cap-Chat, Canada. Its Darrieus rotor is 64 m in diameter and 96 m high. Until its closure in 1992, Éole had produced a total of 12 GWh of electrical energy, which corresponds to a nominal output of just under 20 weeks (3.8 MW).
- The highest wind turbines were installed in 2013 in a wind farm in the Tibetan administrative district of Nagqu . The wind farm, which in the final stage will consist of 33 1.5 MW turbines from the Chinese manufacturer Guodian , is located at an altitude of approx. 4,900 meters. In August 2013, five systems were set up.
- The northernmost wind farm (built in 2002) consists of 16 Nordex N80s, each with a nominal output of 2.5 MW, in the Havøygavlen wind farm near Hammerfest in northern Norway, with an annual production of up to 120 GWh.
- The southernmost wind turbines are three Enercon E-33s at 77 ° 51′S , which together with diesel generators supply the Scott Base in Antarctica with electrical energy. The now abandoned Neumayer Station II at 70 ° 38′S had a Darrieus H rotor from Heidelberg Motors from 1991 to 2008 , which was replaced by an Enercon E-10 for Neumayer Station III .
Wind turbines in German-speaking countries
Germany
Lists of wind turbines in Germany were compiled by federal state:
Baden-Württemberg , Bavaria , Berlin and Brandenburg , Bremen, Hamburg and Lower Saxony , Hesse , Mecklenburg-Western Pomerania , North Rhine-Westphalia , Rhineland-Palatinate , Saarland , Saxony , Saxony-Anhalt , Schleswig-Holstein , Thuringia .
Austria
The largest plants are listed in a list of Austrian wind power plants .
See also the list of Lower Austrian wind power plants , wind energy in Upper Austria # locations and wind energy in Styria # locations .
Two particularly powerful wind turbines of the type E-126 (manufacturer Enercon ) were built near Potzneusiedl by the BEWAG subsidiary Austrian Wind Power (AWP) and put into operation at the beginning of 2012. They each have a nominal output of 7.5 MW, a hub height of around 135 m and a rotor tip height of around 198.5 m.
Switzerland
There are around 55 wind turbines in Switzerland (as of mid-2014). 16 of them are in the Mont Crosin wind farm at the top of the Mont Crosin pass.
The Calandawind wind turbine built in 2012/13 (hub height 119 meters) is the first 3 MW wind turbine in Switzerland.
The highest wind farm in Europe is the Gries wind farm with four wind turbines between the Nufenen Pass and the Gries Pass .
See also:
- List of wind turbines in Switzerland
- Wind energy # Switzerland
- Swiss energy policy
- Energy consumption in Switzerland
Wind turbine manufacturer
The largest manufacturer by installed capacity in 2015 was Goldwind , followed by Vestas , General Electric and Siemens .
Direction of rotation, rotor and blade arrangement
Of the predominant type of wind turbines with an essentially horizontal rotor axis, left and right turning were installed in the early years . In the meantime - from the point of view of the incoming wind - the clockwise direction of rotation prevailed. The rotor is usually in front of the mast, as this swirls the wind flow and a rotor behind the mast would regularly guide its blades through this wake, which would lead to noise, blade loads and a reduction in efficiency.
The wind resistance of the imaginary rotor surface allows the wind to gradually evade to the side. Furthermore, the blades bend in the strong wind flow in the direction of the wind. So that, despite both effects, the blades are more at right angles to the local wind flow, they are arranged in a (very flat) cone with the base facing the wind. This also helps prevent a leaf from grazing the mast. In order to create sufficient clearance between the blade and the mast and also the air jam that protrudes from it, the rotor axis is typically designed to be raised slightly against the wind.
In 2020, a working group at DLR came to the conclusion, using computer simulation, that in wind farms in the northern hemisphere, the wind turbines in at least the second row could generate up to 23 percent more energy if they were designed to rotate counterclockwise instead of clockwise, while clockwise wind turbines in the southern hemisphere were optimal Direction of rotation. This effect, which can be traced back to the Coriolis force , mainly arises at night.
literature
- Albert Betz : Wind energy and its use by windmills. Ökobuch, Kassel 1982, ISBN 3-922964-11-7 . (Reprint of the Göttingen edition 1926).
- Robert Gasch , Jochen Twele (Hrsg.): Wind power plants. Basics, design, planning and operation. 9th, updated edition. Springer, Wiesbaden 2016, ISBN 978-3-658-12360-4 .
- Erich Hau: Wind turbines - basics, technology, use, economy. 5th edition. Springer, Berlin / Heidelberg 2014, ISBN 978-3-642-28876-0 . limited preview in Google Book search
- Siegfried Heier : Use of wind energy. 7th edition. Fraunhofer IRB Verlag, Stuttgart 2016, ISBN 978-3-8167-9587-2 .
- Siegfried Heier: Wind power plants: system design, grid integration and control. 5th edition. Vieweg / Teubner, Wiesbaden 2009, ISBN 978-3-8351-0142-5 .
- Matthias Heymann : History of the use of wind energy: 1890–1990 . Campus Verlag, Frankfurt am Main 1995, ISBN 3-593-35278-8 .
- Peter Jamieson: Innovation in Wind Turbine Design . Wiley, 2011, ISBN 978-0-470-69981-2 . limited preview in Google Book search
- Germanischer Lloyd: Guideline for the Certification of Wind Turbines , 2010 (PDF file; 3.7 MB).
- Martin Kaltschmitt , Wolfgang Streicher, Andreas Wiese (eds.): Renewable energies. System technology, economy, environmental aspects . Springer / Vieweg, 5th edition Berlin / Heidelberg 2013, ISBN 978-3-642-03248-6 .
- Volker Quaschning : Regenerative Energy Systems. Technology - calculation - simulation. 9th edition. Hanser, Munich 2015, ISBN 978-3-446-44267-2 .
- Alois Schaffarczyk (Ed.): Introduction to wind energy technology. 2nd Edition. Hanser, Munich 2016, ISBN 978-3-446-44982-4 .
- Hermann-Josef Wagner , Jyotirmay Mathur: Introduction to wind energy systems. Basics, technology and operation . Springer, Berlin / Heidelberg 2013, ISBN 978-3-642-32975-3 .
- Viktor Wesselak , Thomas Schabbach , Thomas Link, Joachim Fischer: Handbuch Regenerative Energietechnik. 3rd, updated and expanded edition. Berlin / Heidelberg 2017, ISBN 978-3-662-53072-6 .
- Matthias Heymann : Technical knowledge, mentalities and ideologies: Background to the failure history of wind energy technology in the 20th century . In: Technikgeschichte, Vol. 63 (1996), H. 3, pp. 237-254.
- Vaughn Nelson: Innovative Wind Turbines: An Illustrated Guidebook. CRC, Boca Raton 2019, ISBN 9780367819316 .
Web links
- www.wwindea.org/technology - Website on the technology of wind turbines.
- wkaero.calcing.de - Design of wind turbines and map calculation
- www.windindustrie-in-deutschland.de - database with characteristics of wind turbines
- www.offshore-wind.de - Information portal of the German Energy Agency for offshore wind energy
- www.transparency.eex.com - regularly updated yield data for German wind turbines from the European Energy Exchange
- Slide show of the picture category "Wind turbines in Germany"
- Spektrum .de: What the wind turbines of the future will look like January 8, 2019
Individual evidence
- ↑ Trevor J. Price: Blyth, James (1839-1906). In: Henry Colin Gray Matthew, Brian Harrison (Eds.): Oxford Dictionary of National Biography , from the earliest times to the year 2000 (ODNB). Oxford University Press, Oxford 2004, ISBN 0-19-861411-X , ( oxforddnb.com ), as of 2004
- ↑ Robert Gasch , Jochen Twele (Ed.): Wind power plants. Basics, design, planning and operation . Springer, Wiesbaden 2013, p. 30.
- ^ Matthias Heymann : The history of the use of wind energy 1890-1990. Frankfurt am Main / New York 1995, p. 107.
- ^ Matthias Heymann: The history of the use of wind energy 1890-1990. Frankfurt am Main / New York 1995, p. 302.
- ↑ Omar Ellabban, Haitham Abu-Rub, Frede Blaabjerg: Renewable energy resources: Current status, future prospects and Their enabling technology . Renewable and Sustainable Energy Reviews 39, (2014), 748–764, p. 755, doi: 10.1016 / j.rser.2014.07.113 .
- ↑ Cf. Matthias Heymann: The history of the use of wind energy 1890–1990. Frankfurt am Main / New York 1995, p. 409.
- ↑ Alois Schaffarczyk (Ed.): Introduction to wind energy technology. Munich 2012, p. 37.
- ↑ Erich Hau: Wind power plants: Basics, technology, use, economy . Berlin / Heidelberg 2014, p. 40.
- ↑ Chehouri et al., Review of performance optimization techniques applied to wind turbines . In: Applied Energy 142, (2015), 361-388, p. 363, doi: 10.1016 / j.apenergy.2014.12.043 .
- ↑ Status of wind energy use in Germany 2011 ( Memento from November 12, 2013 in the Internet Archive ) (PDF; 2.4 MB). DEWI. Retrieved January 28, 2012.
- ↑ status of wind energy development on land in Germany, 2018 . Website of the Deutsche Windguard. Retrieved June 21, 2019.
- ↑ Average turbine size reaches 2.5MW . In: Windpower Monthly , April 6, 2018. Retrieved April 6, 2018.
- ↑ Erich Hau: Wind turbines - basics, technology, use, economy. 5th edition. Springer, Berlin / Heidelberg 2014, p. 333f.
- ↑ Vestas returns to number one in BTM survey . In: Windpower Monthly . March 26, 2014, accessed March 27, 2014.
- ↑ Platform sharing becoming norm for turbine manufacturers . In: Windpower Monthly . May 1, 2013, accessed May 10, 2013.
- ↑ See Erich Hau: Wind power plants - basics, technology, use, economy. 5th edition. Springer, Berlin / Heidelberg 2014, p. 86.
- ↑ Heiner Dörner: Efficiency and economic comparison of different WEC - (wind energy converter) rotor systems. In: Appropriate technologies for semiarid areas: Wind and solar energy for water supply. Conference Report, Berlin 1975.
- ↑ Martin Kaltschmitt , Wolfgang Streicher, Andreas Wiese (ed.): Renewable energies. System technology, economy, environmental aspects . Berlin / Heidelberg 2013, p. 819.
- ↑ Yield calculator . http://www.wind-data.ch/ Retrieved on March 17, 2012.
- ↑ Robert Gasch, Jochen Twele (Ed.): Wind power plants. Basics, design, planning and operation . Springer, Wiesbaden 2013, p. 507.
- ↑ a b Berthold Hahn et al, The limits of growth have not yet been reached . Wind industry in Germany. Retrieved November 19, 2015.
- ↑ Andrew Mills, Ryan Wisera, Kevin Porter: The cost of transmission for wind energy in the United States: A review of transmission planning studies . In: Renewable and Sustainable Energy Reviews 16, Edition 1, (2012), 1–19, p. 2, doi: 10.1016 / j.rser.2011.07.131 .
- ↑ Lorenz Jarass , Gustav M. Obermair, Wilfried Voigt, Windenergie. Reliable integration into the energy supply , Berlin Heidelberg 2009, p. XIX.
- ↑ Cf. Lorenz Jarass, Gustav M. Obermair: What grid conversion does the energy transition require? Taking into account the network development plan 2012. Münster 2012, p. 159.
- ^ Lowering the CoE, a must in the wind industry . ( Memento of October 29, 2012 in the Internet Archive ) In: notonlywindenergy.com . June 12, 2012, Retrieved July 3, 2012.
- ↑ Philip Tafarte et al .: Small adaptations, big impacts: Options for an optimized mix of variable renewable energy sources . In: Energy . tape 72 , 2014, p. 80-92 , doi : 10.1016 / j.energy.2014.04.094 .
- ↑ McKenna et al., Key challenges and prospects for large wind turbines . In: Renewable and Sustainable Energy Reviews 53, (2016), 1212–1221, p. 1220, doi: 10.1016 / j.rser.2015.09.080 .
- ↑ See Erich Hau: Wind power plants - basics, technology, use, economy. 5th edition. Springer, Berlin / Heidelberg 2014, pp. 157–160.
- ↑ Erich Hau: Wind turbines - basics, technology, use, economy. 5th edition. Springer, Berlin / Heidelberg 2014, p. 71.
- ↑ Erich Hau: Wind turbines - basics, technology, use, economy. 5th edition. Springer, Berlin / Heidelberg 2014, p. 153.
- ↑ Erich Hau: Wind turbines - basics, technology, use, economy. 5th edition. Springer, Berlin / Heidelberg 2014, p. 141.
- ↑ See Erich Hau: Wind power plants - basics, technology, use, economy. 5th edition. Springer, Berlin / Heidelberg 2014, p. 209.
- ↑ Martin Kaltschmitt, Wolfgang Streicher, Andreas Wiese (eds.): Renewable energies. System technology, economic efficiency, environmental aspects , Berlin / Heidelberg 2013, p. 478.
- ↑ Robert Gasch, Jochen Twele (Ed.): Wind power plants. Basics, design, planning and operation . Springer, Wiesbaden 2013, p. 557.
- ↑ Erich Hau: Wind turbines - basics, technology, use, economy. 5th edition. Springer, Berlin Heidelberg 2014, pp. 879f.
- ↑ Ming Yang completes 6.5 MW wind turbine . Wind Energy and Electric Vehicle Review. Retrieved November 7, 2013.
- ↑ ENERCON wind turbines trailing edge ridge. In: Technical Description. ENERCON GmbH, October 21, 2014, accessed on April 30, 2018 .
- ↑ Exhibition monument for Windenergy. Giant wing in Hamburg . In: Renewable Energies. Das Magazin , September 19, 2014, accessed December 15, 2014.
- ↑ Erich Hau: Wind turbines - basics, technology, use, economy. 5th edition. Springer, Berlin / Heidelberg 2014, p. 303.
- ↑ Erich Hau: Wind turbines - basics, technology, use, economy. 5th edition. Springer, Berlin / Heidelberg 2014, p. 316f.
- ↑ Robert Gasch, Jochen Twele (Ed.): Wind power plants. Basics, design, planning and operation . Springer, Wiesbaden 2013, p. 98 f.
- ^ Siemens: Air swords for more electricity. Siemens press release, last accessed on September 6, 2014.
- ↑ http://www.iwrpressedienst.de/energie-themen/pm-5368-wirektiven-der-tuberkel-technologie-im-windkanal-bestaetigt
- ↑ Tuning for wind turbines. Extra income through retrofits . In: Renewable Energies. The magazine , November 10, 2013, accessed December 15, 2014.
- ↑ Erich Hau: Wind turbines - basics, technology, use, economy. 5th edition. Springer, Berlin / Heidelberg 2014, p. 841.
- ↑ Erich Hau: Wind turbines - basics, technology, use, economy. 5th edition. Springer, Berlin / Heidelberg 2014, pp. 841f.
- ↑ Erich Hau: Wind turbines - basics, technology, use, economy. 5th edition. Springer, Berlin / Heidelberg 2014, p. 395.
- ↑ Wind Energy Report Germany 2011. ( Memento from December 8, 2015 in the Internet Archive ) (PDF; 6.1 MB). Fraunhofer IWES . Retrieved July 14, 2012, p. 59.
- ↑ Paraic Higgins, Aoife Foley: The evolution of offshore wind power in the United Kingdom . In: Renewable and Sustainable Energy Reviews 37, (2014), 599–612, pp. 604f, doi: 10.1016 / j.rser.2014.05.058 .
- ↑ Erich Hau: Wind turbines - basics, technology, use, economy. 5th edition. Springer, Berlin / Heidelberg 2014, pp. 342–345.
- ↑ Robert Gasch, Jochen Twele (Ed.): Wind power plants. Basics, design, planning and operation . Springer, Wiesbaden 2013, pp. 68f.
- ↑ Erich Hau: Wind turbines - basics, technology, use, economy. 5th edition. Springer, Berlin / Heidelberg 2014, p. 376.
- ↑ Alois Schaffarczyk (Ed.): Introduction to wind energy technology. Munich 2012, p. 243f.
- ↑ Ming Cheng, Ying Zhu: The state of the art of wind energy conversion systems and technologies: A review . In: Energy Conversion and Management 88, (2014), 332–347, doi: 10.1016 / j.enconman.2014.08.037
- ↑ Volker Quaschning : Regenerative Energy Systems, Technology - Calculation - Simulation. Munich 2011, p. 290.
- ↑ Alois Schaffarczyk (Ed.): Introduction to wind energy technology. Munich 2012, p. 251.
- ^ Siegfried Heier : Wind power plants. System design, network integration and regulation , Wiesbaden 2005, p. 13 u. P. 186.
- ↑ Erich Hau: Wind turbines - basics, technology, use, economy. 5th edition. Springer, Berlin / Heidelberg 2014, pp. 444f.
- ↑ Erich Hau: Wind turbines - basics, technology, use, economy. 5th edition. Springer, Berlin / Heidelberg 2014, p. 436f.
- ↑ Mario Mocker et al .: Technology raw materials for renewable energies - availability and ecological aspects . In: Chemie Ingenieur Technik 87, (2015), doi: 10.1002 / cite.201400121 .
- ↑ a b c Bernd Müller: Rare earths - no longer rare? In: Bundesverband Windenergie (Ed.): New energy . March 2017, ISSN 0949-8656 .
- ↑ Erich Hau: Wind turbines - basics, technology, use, economy. 5th edition. Springer, Berlin / Heidelberg 2014, pp. 420f.
- ↑ John Schmitz, Nils Vatheuer: Hydrostatic drive train for wind turbines. (No longer available online.) IFAS at RWTH Aachen University, archived from the original on November 26, 2015 ; Retrieved August 14, 2012 .
- ↑ See Erich Hau: Wind power plants - basics, technology, use, economy. 5th edition. Springer, Berlin / Heidelberg 2014, p. 452.
- ↑ Volker Quaschning: Regenerative Energy Systems. Technology - calculation - simulation . 8th updated edition. Munich 2013, p. 308f.
- ↑ McKenna et al .: Key challenges and prospects for large wind turbines . In: Renewable and Sustainable Energy Reviews 53, (2016), 1212–1221, p. 1219, doi: 10.1016 / j.rser.2015.09.080 .
- ↑ Martin Kaltschmitt, Wolfgang Streicher, Andreas Wiese (ed.): Renewable energies. System technology, economy, environmental aspects . Berlin / Heidelberg 2013, p. 483.
- ^ Anca D. Hansen, Müfit Altin, Ioannis D. Margaris, Florin Iov, Germán C. Tarnowski: Analysis of the short-term overproduction capability of variable speed wind turbines. In: Renewable Energy . 68 (2014) 326–336, p. 326f doi: 10.1016 / j.renene.2014.02.012 .
- ↑ New low wind systems. Large rotor turbines: even more pictures and statements . In: Renewable Energies. The magazine , November 2, 2015, accessed on November 2, 2015.
- ↑ See Erich Hau: Wind power plants - basics, technology, use, economy. 5th edition. Springer, Berlin / Heidelberg 2014, p. 514.
- ↑ See Erich Hau: Wind power plants - basics, technology, use, economy. 5th edition. Springer, Berlin / Heidelberg 2014, p. 531.
- ↑ a b c Stefan Bögl: Hybrid Wind Power Towers - New Generation of Wind Power Plants. ( Memento from June 6, 2012 in the Internet Archive ) 36th Lindau Construction Seminar, January 2011.
- ↑ Erich Hau: Wind turbines - basics, technology, use, economy. 5th edition. Springer, Berlin / Heidelberg 2014, pp. 507-513.
- ↑ a b McKenna et al .: Key challenges and prospects for large wind turbines . In: Renewable and Sustainable Energy Reviews 53, (2016), 1212–1221, p. 1218, doi: 10.1016 / j.rser.2015.09.080 .
- ↑ Erich Hau: Wind turbines - basics, technology, use, economy. 5th edition. Springer, Berlin / Heidelberg 2014, p. 513f.
- ↑ a b Technology 3MW model: Vestas reveals low-wind V136-3.45MW turbine . In: Windpower Monthly , September 30, 2015, accessed October 29, 2015.
- ↑ Bolted Steel Shell Tower. (PDF) Siemens Wind Power, February 18, 2017, accessed on February 18, 2017 (English).
- ↑ Premiere for the new steel tower. Märkische Onlinezeitung, January 13, 2016, accessed on February 18, 2017 .
- ↑ Video: Climbing turbine crane , Lagerwey is testing the construction of a steel tower with a climbing crane
- ↑ Erich Hau: Wind turbines - basics, technology, use, economy. 5th edition. Springer, Berlin / Heidelberg 2014, pp. 524f.
- ↑ Robert Gasch , Jochen Twele (Ed.): Wind power plants. Basics, design, planning and operation . Springer, Wiesbaden 2013, p. 105.
- ↑ a b Erich Hau: Wind power plants - basics, technology, use, economic efficiency. 5th edition. Springer, Berlin / Heidelberg 2014, p. 503.
- ↑ Alois Schaffarczyk (Ed.): Introduction to wind energy technology. Munich 2012, p. 290f.
- ↑ The first multi-megawatt system with a 100 m wooden tower is in place . In: Sonne Wind & Wärme , October 15, 2012, accessed on October 18, 2012.
- ↑ Giant with wooden leg. Heise, November 22, 2012, accessed November 22, 2012 .
- ↑ Robert Gasch, Jochen Twele (Ed.): Wind power plants. Basics, design, planning and operation . Springer, Wiesbaden 2013, p. 521.
- ↑ Erich Hau: Wind turbines - basics, technology, use, economy. 5th edition. Springer, Berlin / Heidelberg 2014, p. 886.
- ↑ Wind Energy Report Germany 2009 Offshore ( Memento from December 8, 2015 in the Internet Archive ) (PDF; 33 MB). Fraunhofer IWES . Retrieved November 21, 2013.
- ↑ Erich Hau: Wind turbines - basics, technology, use, economy. 5th edition. Springer, Berlin / Heidelberg 2014, pp. 628f.
- ↑ Volker Quaschning : Regenerative Energy Systems. Technology - calculation - simulation . 8th updated edition. Munich 2013, p. 275.
- ↑ Cf. Martin Kaltschmitt, Wolfgang Streicher, Andreas Wiese (eds.): Renewable energies. System technology, economic efficiency, environmental aspects , Berlin / Heidelberg 2013, p. 510f.
- ↑ Damir Jelaska et al .: A novel hybrid transmission for variable speed wind turbines . In: Renewable Energy 83, (2015), 78-84, p. 78, doi: 10.1016 / j.renene.2015.04.021 .
- ↑ Robert Gasch , Jochen Twele (Ed.): Wind power plants. Basics, design, planning and operation . Springer, Wiesbaden 2013, p. 61.
- ↑ E. Pick, H.-J. Wagner: Contribution to the cumulative energy consumption of selected wind energy converters. Report of the Chair for Energy Systems and Economics. University of Bochum 1998, p. 20.
- ↑ Scharndorf-West wind farm: detailed information (PDF; 89 kB). Info brochure. Retrieved November 9, 2013.
- ↑ G. Schauer, A. Szeless: Potential - technology and system examples - environmental compatibility - profitability - market development. In: Electrical engineering and information technology. 114, issue 10 (1997), 572-579, pp. 574f, doi: 10.1007 / BF03159081 .
- ^ Klaus Heuck, Klaus-Dieter Dettmann, Detlef Schulz: Electrical energy supply. Generation, transmission and electrical energy for study and practice. 8th revised and updated edition. Wiesbaden 2010, p. 9.
- ↑ Holger Watter, Regenerative Energy Systems. Basics, system technology and application examples from practice , Wiesbaden 2011, p. 70.
- ^ Mark Z. Jacobson : Review of solutions to global warming, air pollution, and energy security . In: Energy and Environmental Science 2, (2009), 148-173, p. 154, doi: 10.1039 / b809990c .
- ↑ a b Enercon launches 4MW turbine platform . In: Windpower Monthly , December 5, 2014, accessed December 17, 2014.
- ↑ Robert Gasch , Jochen Twele (Ed.): Wind power plants. Basics, design, planning and operation . Springer, Wiesbaden 2013, p. 534.
- ↑ Guideline for wind turbines impacts and proof of stability for tower and foundation. Version October 2012 ( Memento from March 4, 2016 in the Internet Archive ). Writings of the German Institute for Building Technology, Series B, Issue 8. Accessed on December 18, 2014.
- ↑ Gamesa ten-year life extension certified . In: Windpower Monthly , December 16, 2014, accessed December 17, 2014.
- ↑ Insufficient recycling capacity for dismantling wind turbines. UBA study looks at the environmental aspects of recycling old wind turbines. 1st November 2019 .
- ↑ a b Lindeiner, A. v. (2014): Wind power and bird protection. - ANLiegen Natur 36 (1): 39–46, running. PDF 0.8 MB
- ↑ Martin Kaltschmitt , Wolfgang Streicher, Andreas Wiese (ed.): Renewable energies. System technology, economy, environmental aspects . Berlin / Heidelberg 2013, p. 539f.
- ^ Ziyad Salameh: Renewable Energy System Design , Academic Press 2014, p. 164.
- ↑ Erich Hau: Wind turbines - basics, technology, use, economy. 5th edition. Springer, Berlin / Heidelberg 2014, p. 671f.
- ↑ Álvaro Camiña: Las Energías Renovables y la Conservacíon de Aves Carroñeras: El Caso del Buitre Leonado (Gyps fulvus) en el Norte de la Península Ibérica . (PDF) 2008.
- ↑ Martina Carrete et al .: Large scale risk assessment of wind farms on population viability of a globally endangered long-lived raptor. Biological Conservation 142, 2009, doi: 10.1016 / j.biocon.2009.07.027 ( online ).
- ↑ BFU: Energeia, 5/2015
- ↑ Determination of the collision rates of (birds of prey) and creation of planning-related bases for the prognosis and assessment of the collision risk from wind turbines . Progress study. Retrieved December 4, 2016.
- ↑ Jakob Katzenberger, Christoph Sudfeldt: Red Kite and Wind Power . Negative relationship between wind turbine density and inventory trends. In: Der Falke - Journal for Bird Watchers . No. 10/2019 . Aula-Verlag , October 2019, ISSN 0323-357X ( falke-journal.de [PDF; accessed December 25, 2019]).
- ↑ Michelle Lewis: EGEB: Singapore solar goes huge - on the water. Singapore solar, Bird-friendly wind turbines, Solar tech breakthrough. In: Electrek. August 21, 2020, accessed August 22, 2020 (American English).
- ↑ Roel May, Torgeir Nygård, Ulla Falkdalen, Jens Åström, Øyvind Hamre, Bård G. Stokke: Paint it black: Efficacy of increased wind turbine rotor blade visibility to reduce avian fatalities. In: Ecology and Evolution. July 26, 2020, doi: 10.1002 / ece3.6592 (English).
- ^ Benjamin K. Sovacool, The avian benefits of wind energy: A 2009 update . Renewable Energy 49, (2013), 19-24, doi: 10.1016 / j.renene.2012.01.074 .
- ↑ Yogesh Kumar et al .: Wind energy: Trends and enabling technologies . In: Renewable and Sustainable Energy Reviews 53, (2016), 209–224, p. 221, doi: 10.1016 / j.rser.2015.07.200 .
- ↑ Emma Marris, Daemon Fairless: Wind farms' deadly reputation hard to shift . Nature 447, 2007, p. 126, doi: 10.1038 / 447126a .
- ↑ Wang et al .: Ecological impacts of wind farms on birds: Questions, hypotheses, and research needs . In: Renewable and Sustainable Energy Reviews 44, (2015), 599–607, pp. 601f, doi: 10.1016 / j.rser.2015.01.031 .
- ↑ WindBat. Friedrich-Alexander-Universität Erlangen-Nürnberg , accessed on July 25, 2019 .
- ↑ a b Robert Brinkmann, Oliver Behr, Ivo Niermann, Michael Reich (eds.): Development of methods for investigating and reducing the collision risk of bats on onshore wind turbines (= environment and space . Volume 4 ). Cuvillier Verlag , Göttingen 2011, ISBN 978-3-86955-753-3 ( cuvillier.de ).
- ↑ a b Oliver Behr, Robert Brinkmann, Fränzi Korner-Nievergelt, Martina Nagy, Ivo Niermann, Michael Reich, Ralph Simon (eds.): Reduction of the collision risk of bats on onshore wind turbines (= environment and space . Volume 7 ). Leibniz University Hannover , Hannover 2016, doi : 10.15488 / 263 .
- ↑ Oliver Behr, Robert Brinkmann, Klaus Hochradel, Jürgen Mages, Fränzi Korner-Nievergelt, Heidje Reinhard, Ralph Simon, Florian Stiller, Natalie Weber, Martina Nagy: Determining the collision risk of bats on onshore wind turbines in planning practice . Erlangen , Freiburg , Ettiswil 2018 ( fau.de [PDF]).
- ^ A b Christian C. Voigt et al .: Wildlife and renewable energy: German politics cross migratory bats . In: European Journal of Wildlife Research . tape 61 , 2015, p. 213-219 , doi : 10.1007 / s10344-015-0903-y (English).
- ↑ Andreas Zahn, Anika Lustig and Matthias Hammer: Potential Effects of Wind Turbines on Bat Populations . In: Nature concerns . tape 36 , no. 1 , 2014, ISBN 978-3-944219-09-7 , pp. 21–35 ( bayern.de [PDF]).
- ↑ Jörg Müller: Bats in the Forest - New Dangers from Wind Power . In: Nature concerns . tape 36 , no. 1 , 2014, ISBN 978-3-944219-09-7 , pp. 36–38 ( bayern.de [PDF]).
- ↑ Erin F. Baerwald u. a .: Barotrauma is a significant cause of bat fatalities at wind turbines. In: Current Biology. 18, No. 16, 2008, pp. R695 – R696, doi: 10.1016 / j.cub.2008.06.029 .
- ^ Linn S. Lehnert, Stephanie Kramer-Schadt, Sophia Schönborn, Oliver Lindecke, Ivo Niermann, Christian C. Voigt: Wind Farm Facilities in Germany Kill Noctule Bats from Near and Far . In: PLOS ONE . tape 9 , no. 8 , August 13, 2014, doi : 10.1371 / journal.pone.0103106 (English, scinexx.de [accessed on August 14, 2014]).
- ↑ Christian C. Voigt, Katharina Rehnig, Oliver Lindecke, Gunārs Pētersons: Migratory bats are attracted by red light but not by warm-white light: Implications for the protection of nocturnal migrants . In: Ecology and Evolution . tape August 8 , 2018, doi : 10.1002 / ece3.4400 (English, researchgate.net [accessed January 18, 2020]).
- ↑ CV Long, JA Flint, PA Lepper: Insect attraction to wind turbines: does color play a role? In: European Journal of Wildlife Research . tape 57 , 2011, p. 323–331 , doi : 10.1007 / s10344-010-0432-7 (English, archives-ouvertes.fr ).
- ^ Franz Trieb: Interference of Flying Insects and Wind Parks . Project report on the DLR website , October 2018
- ^ Daniel Wetzel: Model analysis: Wind energy could be partly responsible for the death of insects . In: Welt Online . 18th March 2019
- ↑ Bernward Janzing : Study on the dangers of wind turbines: Mood making with insect death . In: the daily newspaper . March 24, 2019
- ↑ Jenell M. Walsh-Thomas et al .: Further evidence of impacts of large-scale wind farms on land surface temperature. Renewable and Sustainable Energy Reviews 16, 2012, doi: 10.1016 / j.rser.2012.07.004 ( free full text ).
- ↑ Lee M. Miller, David W. Keith: Climatic Impacts of Wind Power. Joule 2, 2018, doi: 10.1016 / j.joule.2018.09.009 ( free full text ).
- ^ Mark Z. Jacobson et al .: Taming hurricanes with arrays of offshore wind turbines. Nature Climate Change 4, 2014, doi: 10.1038 / NCLIMATE2120 ( free full text ).
- ↑ Martin Kaltschmitt, Wolfgang Streicher, Andreas Wiese (ed.): Renewable energies. System technology, economy, environmental aspects . Berlin / Heidelberg 2013, p. 542.
- ↑ Rest under rotors . Deutschlandradio, October 26, 2011.
- ↑ Three offshore concepts for the future . Renewable energies, April 2014.
- ↑ Material inventory and material flows in infrastructures ( Memento from December 4, 2013 in the Internet Archive ) (PDF; 4.3 MB). Study by the Wuppertal Institute for Climate, Environment and Energy . Retrieved July 20, 2012.
- ↑ Material inventory and material flows in infrastructures ( Memento from December 4, 2013 in the Internet Archive ) (PDF; 4.3 MB). Study by the Wuppertal Institute for Climate, Environment and Energy . Retrieved July 20, 2012, pp. 171–178.
- ↑ Wind turbines eat up material . In: VDI nachrichten , July 20, 2012, accessed on July 20, 2012.
- ↑ Material inventory and material flows in infrastructures ( Memento from December 4, 2013 in the Internet Archive ) (PDF; 4.3 MB). Study by the Wuppertal Institute for Climate, Environment and Energy . Retrieved July 20, 2012, p. 154.
- ↑ Gross electricity generation in Germany from 1990 to 2012 by energy source. (PDF) Arbeitsgemeinschaft Energiebilanzen e. V., August 2, 2013, accessed November 27, 2013 .
- ↑ Wind turbines: Who controls the disposal? , NDR .de, April 3, 2017
- ↑ Impending recycling bottleneck: The problem with the old wind turbines . In: Spiegel Online . November 1, 2019 ( spiegel.de [accessed November 2, 2019]).
- ↑ Erich Hau: Wind turbines - basics, technology, use, economy. 5th edition. Springer, Berlin / Heidelberg 2014, p. 931.
- ↑ Thomas Schabbach, Viktor Wesselak: Energy. The future will be renewable. Berlin / Heidelberg 2012, p. 24.
- ↑ a b Till Zimmermann, Parameterized tool for site specific LCAs of wind energy converters . In: The International Journal of Life Cycle Assessment 18, (2013), 49-60, doi: 10.1007 / s11367-012-0467-y .
- ^ Fulvio Ardente, Marco Beccali, Maurizio Cellura, Valerio Lo Brano: Energy performances and life cycle assessment of an Italian wind farm. In: Renewable and Sustainable Energy Reviews . 12 (2008), 200-217, p. 214. doi: 10.1016 / j.rser.2006.05.013
- ↑ JK Kaldellis, D. Apostolou: Life cycle energy and carbon footprint of offshore wind energy. Comparison with onshore counterpart . In: Renewable Energy . tape 108 , 2017, p. 72-84 , doi : 10.1016 / j.renene.2017.02.039 .
- ↑ Erich Hau: Wind turbines - basics, technology, use, economy. 5th edition. Springer, Berlin / Heidelberg 2014, pp. 931f.
- ↑ Rodoula Tryfonidou, energetic analysis of an offshore wind farm taking grid integration into account. (= Series of publications by the Chair for Energy Systems and Energy Economics. 14). zgl. Diss., Bochum 2007. Online (PDF; 1.2 MB)
- ^ Matthias Geuder: Energetic evaluation of wind turbines. (PDF; 2.1 MB) Würzburg-Schweinfurt University of Applied Sciences, Schweinfurt 2004 (diploma thesis).
- ↑ Eduardo Martinez et al, Life-cycle assessment of a 2-MW rated power wind turbine: CML method . In: The International Journal of Life Cycle Assessment 14, (2009), 52-63, doi: 10.1007 / s11367-008-0033-9 .
- ↑ More wind power on land brings ecology into focus . In: vdi news. September 2, 2011, accessed September 17, 2011.
- ↑ a b Begoña Guezuraga, Rudolf Zauner, Werner Pölz: Life cycle assessment of two different 2 MW class wind turbines. In: Renewable Energy . 37 (2012) 37-44, p. 44. doi: 10.1016 / j.renene.2011.05.008
- ^ A b Karl R. Haapala, Preedanood Prempreeda: Comparative life cycle assessment of 2.0 MW wind turbines. In: International Journal of Sustainable Manufacturing. Vol. 3, No. 2, 2014, pp. 170-185. doi: 10.1504 / IJSM.2014.062496
- ↑ Background paper rare earths (PDF; 136 kB) Öko-Institut, January 2011.
- ↑ a b c Xiaoyue Du, TE Graedel: Global Rare Earth In-Use Stocks in NdFeB Permanent Magnets . In: Journal of Industrial Ecology 16, Issue 6, (2011), 836-843, doi: 10.1111 / j.1530-9290.2011.00362.x .
- ↑ a b Stefania Massari, Marcello Ruberti: Rare earth elements as critical raw materials: Focus on international markets and future strategies . In: Resources Policy 38, (2013), 36–43, doi: 10.1016 / j.resourpol.2012.07.001 .
- ↑ Koen Binnemans et al .: recycling of rare earths: a critical review . In: Journal of Cleaner Production 51, (2013), 1–22, doi: 10.1016 / j.jclepro.2012.12.037 .
- ↑ Wind industry fears damage to image from negative report on neodymium use in wind turbines
- ↑ Markus Mueller, Henk Polinder (eds.): Electrical drives for direct drive renewable energy systems , Woodhead Publishing Limited 2013, p. 147.
- ↑ Technology 3MW model: Vestas reveals low-wind V136-3.45MW turbine . In: Windpower Monthly , September 30, 2015. Retrieved May 8, 2017.
- ↑ Erich Hau: Wind power plants: Basics, technology, use, economy. Berlin / Heidelberg 2014, pp. 651f.
- ↑ RHEINPFALZ.DE: The front part has been removed. January 13, 2014, archived from the original on January 16, 2014 ; accessed on August 15, 2019 .
- ↑ a b Martin Kaltschmitt, Wolfgang Streicher, Andreas Wiese (ed.): Renewable energies. System technology, economy, environmental aspects . Berlin / Heidelberg 2013, p. 543.
- ↑ Oliver Braun: Windrad reports: "Ich brenne" nwzonline.de, October 15, 2013, accessed December 20, 2017.
- ↑ Martin Kaltschmitt, Wolfgang Streicher, Andreas Wiese (ed.): Renewable energies. System technology, economy, environmental aspects . Berlin / Heidelberg 2013, p. 537.
- ↑ Erich Hau: Wind power plants: Basics, technology, use, economy. Berlin / Heidelberg 2014, pp. 842f.
- ↑ VEENKER: Wind turbines in the vicinity of protected objects / determination of minimum distances
- ↑ TÜV: Wind turbines ticking time bombs Westfalenpost dated January 30, 2019, accessed on February 4, 2019.
- ↑ Most opponents of nuclear power in Germany, Italy and Mexico. Ipsos , June 20, 2011; archived from the original on February 9, 2017 ; accessed on March 12, 2019 .
- ^ Hans-Martin Henning, Andreas Palzer: A comprehensive model for the German electricity and heat sector in a future energy system with a dominant contribution from renewable energy technologies — Part I: Methodology. In: Renewable and Sustainable Energy Reviews . 30, (2014), 1003-1018, p. 1003, doi: 10.1016 / j.rser.2013.09.012
- ↑ Forsa survey: The majority of German citizens are in favor of the expansion of renewable energies with undiminished funding. In: Agency for Renewable Energies. December 14, 2009.
- ↑ Clemens Wunderlich, Philipp Vohrer: Acceptance of renewable energies in the German population ( Memento from May 18, 2013 in the Internet Archive ) (PDF; 915 kB), Renews Special, March 2012.
- ↑ a b Fabian David Musall, Onno Kuik: Local acceptance of renewable energy. A case study from southeast Germany. In: Energy Policy . 39, (2011), 3252-3260, pp. 3252f, doi: 10.1016 / j.enpol.2011.03.017 .
- ↑ Fabian David Musall, Onno Kuik: Local acceptance of renewable energy. A case study from southeast Germany . Energy Policy , 39, (2011), 3252-3260, p. 3259, doi: 10.1016 / j.enpol.2011.03.017 .
- ↑ Distances and WHO . LUBW website . Retrieved October 29, 2015.
- ^ Explanatory email from the WHO to the BUND Regional Association Stuttgart ( memento from April 1, 2015 in the Internet Archive ), last accessed on October 29, 2015.
- ↑ Survey of residents of possible wind farms in Eastern Switzerland , Institute for Economics and Ecology at the University of St. Gallen, November 2015
- ↑ UBA: Possible health effects of wind turbines. November 2016. Retrieved August 21, 2017 .
- ↑ Erich Hau: Wind turbines - basics, technology, use, economy. 5th edition. Springer, Berlin / Heidelberg 2014, p. 653.
- ↑ Alois Schaffarczyk (Ed.): Introduction to Windenergietechnik , Munich 2012, p. 129.
- ↑ Cf. Robert Gasch, Jochen Twele (Ed.): Windkraftanlagen. Basics, design, planning and operation . Springer, Wiesbaden 2013, p. 516.
- ^ Bavarian State Office for the Environment / Bavarian State Office for Health and Food Safety : UmweltWissen - Klima & Energie. Wind energy in Bavaria , No. 3.4, p. 9; Wind Energy Decree 2011, No. 5.2.1.3, MBl. NRW. 2011, p. 321ff ( PDF ( Memento from February 28, 2013 in the Internet Archive )); Landesumweltamt (LUA) Nordrhein-Westfalen , materials no.63, wind turbines and immission control, Essen 2002, no.5.2.1, p.25 (PDF) ( Memento from March 10, 2012 in the Internet Archive )
- ↑ a b Erich Hau: Wind power plants - basics, technology, use, economic efficiency. 5th edition. Springer, Berlin / Heidelberg 2014, p. 658.
- ↑ Sound propagation in the open air , explained in a study paper on the subject of machine acoustics , created at the Institute for Mechanical Engineering at Clausthal University of Technology
- ↑ See Erich Hau: Wind power plants - basics, technology, use, economy. 5th edition. Springer, Berlin / Heidelberg 2014, p. 659.
- ↑ Alois Schaffarczyk (Ed.): Introduction to Windenergietechnik , Munich 2012, p. 127.
- ↑ Erich Hau: Wind turbines - basics, technology, use, economy. 5th edition. Springer, Berlin / Heidelberg 2014, p. 654.
- ↑ Martin Kaltschmitt , Wolfgang Streicher, Andreas Wiese (eds.), Renewable Energies. System technology, economic efficiency, environmental aspects , Berlin Heidelberg 2013, p. 536.
- ↑ Wind energy and infrasound (PDF; 3.5 MB), low-frequency noises from wind turbines of the LUBW and the State Health Office of Baden-Württemberg in the Stuttgart regional council
- ↑ amplitude modulation as a special noise characteristics of the wind turbines in noise abatement , 5/2018 page 171-181, accessed online on October 12, 2018
- ^ WHO: Rationale for the guideline levels for wind turbine noise , in: Environmental Noise Guidelines for the European Region , page 77ff.
- ↑ Erich Hau: Wind power plants: Basics, technology, use, economy . Berlin / Heidelberg 2014, pp. 837–839.
- ↑ Earning ends nightly continuous flashing on wind turbines . In: IWR , April 1, 2015, accessed April 1, 2015.
- ↑ Uckermark is switched off . In: Märkische Oderzeitung , December 16, 2016. Accessed January 2, 2017.
- ↑ The output system stops flashing continuously at over 20 wind turbines. iwr.de, March 8, 2017, accessed March 9, 2017 .
- ↑ See on this discussion z. B. Werner Nohl: Landscape aesthetic effects of wind turbines. 2009; Günter Ratzbor: wind turbines and landscape. On the impact of wind turbines on the landscape. ( Memento of March 4, 2016 in the Internet Archive ) Thesis paper of the DNR. 2011; Sören Schöbel: Wind energy and landscape aesthetics: For the landscape-appropriate arrangement of wind farms. Jovis-Verlag, Berlin 2012; Thomas Kirchhoff: Energy transition and landscape aesthetics. Objectification of aesthetic evaluations of energy systems by referring to three intersubjective landscape ideals. In: Nature conservation and landscape planning. 46 (1), 2014, pp. 10-16.
- ↑ Specialist agency onshore wind energy: Air safety radar.
- ^ Specialized agency for wind energy on land: Military air surveillance.
- ^ German air traffic control: air traffic control and the construction of wind energy plants. .
- ↑ Wind power causes turbulence in real estate prices. In: The world . September 22, 2003. Retrieved February 17, 2017 .
- ↑ To the wind turbine, comrades! In: The world . January 21, 2012. Retrieved January 21, 2012 .
- ↑ Vornholz, Günter 2015: Effects of wind turbines on property prices, in: Der ImmobilienBrief, No. 321, pp. 21–23.
- ↑ Printed matter no .: 01749-15. (PDF) In: City of Dortmund . Retrieved on April 26, 2020 : "Mr. Elkmann (Environment Agency) points out that there are no reliable findings on this."
- ↑ An example "Effects of demographic change on tourism and conclusions for tourism policy" ( Memento from April 25, 2014 in the Internet Archive ) (PDF; 1 MB) In 1999/2000, the NIT-Kiel examined the tourist effects of wind turbines
- ↑ Acceptance of wind farms in tourist communities on the German North Sea coast ( memento from July 19, 2007 in the Internet Archive ) (PDF; 389 kB). Website of the Bremerhaven University of Applied Sciences . Retrieved November 11, 2012.
- ↑ Visitor survey on the acceptance of wind turbines in the Eifel (PDF; 6642 kB). Retrieved August 8, 2014.
- ↑ Ulrichstein - Wind Energy Educational Trail . Retrieved November 25, 2012.
- ↑ Hilchenbacher Windwanderweg opened ( memento from April 25, 2014 in the Internet Archive ). rothaarwind.de; Retrieved November 25, 2012.
- ↑ The Wind Turbine Tour . prenzlau-tourismus.de; Retrieved November 25, 2012.
- ↑ https://www.windenergie.at > Info-Service> Events> Maschinenhaus. Detail page , accessed June 23, 2018.
- ↑ Monika Agatz: Wind Energy Handbook. December 2018, accessed June 21, 2019 .
- ↑ Approval for small wind turbines under 50 meters . In: klein-windkraftanlagen.com. Retrieved December 13, 2012.
- ↑ Leopold Böswirth, Sabine Bschorer: Technical Fluid Mechanics. Text and exercise book . Wiesbaden 2014, p. 84.
- ↑ Electricity generation costs of renewable energies, November 2013 . Fraunhofer ISE website . Retrieved January 30, 2014.
- ↑ Robert Gasch, Jochen Twele (Ed.): Wind power plants. Basics, design, planning and operation . Springer, Wiesbaden 2013, p. 539.
- ↑ Martin Kaltschmitt , Wolfgang Streicher (Ed.): Regenerative Energies in Österreich. Basics, system technology, environmental aspects, cost analyzes, potential, use. Wiesbaden 2009, p. 225.
- ^ David Richard Walwyn, Alan Coli Brent: Renewable energy gathers steam in South Africa . Renewable and Sustainable Energy Reviews 41, (2015), 390–401, doi: 10.1016 / j.rser.2014.08.049 .
- ^ Nicola Armaroli , Vincenzo Balzani : Towards an electricity-powered world . In: Energy and Environmental Science 4 , (2011), 3193-3222, p. 3217, doi: 10.1039 / c1ee01249e .
- ↑ 6th edition 2017 p. 891; in the 5th edition in 2014 he named 3,053,000 euros or 1016 euros / kW.
- ↑ Erich Hau: Wind turbines - basics, technology, use, economy. 6th edition. Springer, Berlin / Heidelberg 2017, p. 892 (5th edition. 2014, p. 871f .: 3,276,000 euros or 1092 euros / kW).
- ↑ Erich Hau: Wind turbines - basics, technology, use, economy. 5th edition. Springer, Berlin / Heidelberg 2014, p. 894.
- ↑ Chehouri et al .: Review of performance optimization techniques applied to wind turbines . In: Applied Energy 142, (2015), 361-388, p. 382, doi: 10.1016 / j.apenergy.2014.12.043 .
- ↑ Rotor: Longer blades for more power . In: EE-News , February 7, 2014, accessed on February 9, 2014.
- ^ RH Barnes et al .: Improved methodology for design of low wind speed specific wind turbine blades . In: Composite Structures 119, (2015), 677–684, doi: 10.1016 / j.compstruct.2014.09.034 .
- ↑ J. Lloberas, A. Sumper, M. Sanmarti, X. Granados: A review of high temperature superconductors for offshore wind power synchronous generators . In: Renewable and Sustainable Energy Reviews 38, (2014), 404-414, doi: 10.1016 / j.rser.2014.05.003 .
- ↑ Robert Gasch, Jochen Twele (Ed.): Wind power plants. Basics, design, planning and operation . Springer, Wiesbaden 2013, p. 559.
- ↑ Uwe Ahrens et al .: Airborne wind energy. Springer, Heidelberg 2014, ISBN 978-3-642-39964-0 .
- ↑ Cristina L. Archer et al .: Airborne wind energy: Optimal locations and variability. In: Renewable Energy 64, (2014), 180-186, doi: 10.1016 / j.renene.2013.10.044 .
- ↑ [1] "National Geographic: Iran's Centuries-Old Windmills"
- ↑ "Tvindkraft - the oldest operating wind turbine in the world"
- ↑ World's most powerful wind turbine completely installed! , October 18, 2019, accessed October 31, 2019
- ↑ Ten of the biggest turbines . In: Windpower Monthly , June 30, 2016, accessed July 1, 2016.
- ↑ First turbines at world's highest wind farm . In: Windpower Monthly , August 8, 2013, accessed August 8, 2013.
- ↑ Havøygavlen Wind Farm, Norway (PDF)
- ↑ According to the planning (as of 2007) (PDF; 9 MB)
- ↑ Largest wind turbines officially in operation . ORF-ON, February 22, 2012.
- ↑ wind-data.ch (interactive map) , list
- ↑ The hair dryer ensures a record month . In: Schweizer Radio und Fernsehen , February 19, 2014, accessed on July 24, 2014.
- ↑ Market shares of manufacturers of wind turbines worldwide in 2014. Statista.de. Retrieved October 10, 2016.
- ↑ SWR2 : Why do all the wind turbines turn clockwise? , dated November 6, 2011, accessed on September 8, 2017
- ↑ Otto Wöhrbach: 90 percent of wind turbines turn the wrong way round. In: Der Tagesspiegel. June 11, 2020, accessed June 12, 2020 .