paper
Paper (from Latin papyrus , from ancient Greek πάπυρος pápyros , papyrus shrub ) is a flat material that essentially consists of fibers of vegetable origin and is formed by draining a fiber suspension on a sieve. The resulting fiber fleece is compressed and dried.
Paper is made from fiber , which today is mainly obtained from the raw material wood. The most important fibers are cellulose , wood pulp and waste paper pulp . The through paper recycling recycled waste paper has become the most important source of raw materials in Europe. In addition to the pulp or a mixture of fibers, paper often also contains fillers and other additives.
There are around 3,000 types of paper , which can be divided into four main groups according to their intended use: graphic papers (printing and writing papers ), packaging papers and cardboard, hygiene papers (e.g. toilet paper , paper handkerchiefs ) as well as the various technical papers and special papers (e.g. B. filter paper , cigarette paper , banknote paper ).
Demarcation
Paper, cardboard, cardboard
Paper, cardboard and cardboard are differentiated , among other things, on the basis of the area-related mass . DIN 6730 avoids the term cardboard and only differentiates between paper and cardboard, based on the limit value 225 g / m². Colloquially, however , paperboard is a common name for a material in the 150 g / m² to 600 g / m² range, which is typically thicker and stiffer than paper. When assigning the area-related mass, there are overlapping areas between paper and cardboard and between cardboard and cardboard:
designation | area based size |
---|---|
DIN 6730 | |
paper | 7 g / m² to 225 g / m² |
cardboard | from 225 g / m² |
Colloquial (German) | |
paper | 7 g / m² to 225 g / m² |
carton | 150 g / m² to 600 g / m² |
cardboard | from 225 g / m² |
In the case of the colloquial three-way division into paper, cardboard, and cardboard, other limit values are sometimes given for the overlapping areas, for example:
designation | area based size |
---|---|
paper | 7 g / m² to 250 g / m² |
carton | 150 g / m² to 600 g / m² |
cardboard | from 500 g / m² |
The minimum grammage of cardboard is specified differently depending on the source, for example 220 g / m² or 600 g / m². The flowing weight limits are also based on innovations in production technology. The basis weight is therefore today to be regarded as an approximate reference point and one of several differentiation criteria.
Pseudo papers
Pseudo papers (paper-like) such as papyrus , tapa , Amatl and Huun - all of vegetable origin - differ from paper primarily in the technique of production: vegetable fibers are tapped together and formed into a sheet. When making real paper, the fibers are soaked in water and separated from one another. Then the fibers have to be placed on a sieve as a thin layer, drained and dried. The intertwined, matted fibers form the paper.
history
Early writers
Cave drawings are the oldest documents that humans have drawn on a surface with pigment paint. The Sumerians , as the bearers of the oldest known high culture, wrote since about 3200 BC. BC with cuneiform writing on soft clay tablets , some of which have been fired by chance. Writings made of inorganic materials are also known from Egypt , for example the Narmer palette - a splendid palette of King Narmer (3100 BC) made of slate .
Paper-like ones are made from papyrus. This papyrus (paper) consists of the flattened, crossed and pressed stalks of the reed plants growing along the entire lower Nile in quiet bank areas ( real papyrus ), the thin, pressed layers are then glued together (laminated). It was written in black and red. The black ink consisted of soot and a solution of gum arabic , the red color was based on ocher . The writing implement was a brush made of rushes . Papyrus has been used in ancient Egypt since the third millennium BC. Used as writing material. Although papyrus existed in ancient Greece , it was hardly known to have spread beyond Greece. In the 3rd century BC The Greeks replaced the brush with a split reed pen .
In the Roman Empire , both papyrus were and wax used panels. The text was scratched into the latter using a sharpened stylus. After reading out, the wax was smoothed with a scraper and the board could be written on again. Public pronouncements were mostly attached to temples or administrative buildings as permanent inscriptions (stone tablets or metal plates). The Romans called Papyrus bast with Latin liber , later, from which the term "library" ( library developed).
In China, tablets made of bones, shells, ivory and turtle shells were used. Later, writing tablets were also made of bronze , iron, gold, silver, pewter , jade , stone slabs and clay or often made of organic material such as strips of wood, bamboo and silk . Plant leaves and animal skins have not yet been used as writing carriers. Oracle bones were scratched with pens or inscribed with ink with lamp soot or cinnabar as a pigment.
In India and Ceylon , the leaves of the Talipot palm have been around since 500 BC. Chr. Used → palm leaf manuscript , as well as birch bark, wood blocks, chalkboard and cotton cloth, as well as stone tablets, blocks.
In the advanced cultures of the ancient Orient and the Mediterranean area , leather was used as a writing material from time immemorial. Like leather, parchment is made from animal skins. Due to the advantages of parchment, other writing materials were displaced in medieval Europe. The animal hides are stained with potash or lime , thoroughly cleaned and stretched and dried, followed by scraping and surface treatment.
In the New World, Huun, Amatl, a paper-like writing material, was made by the Maya as early as the 5th century . However, in terms of its production method, this material is more closely related to papyrus, because it is made from cross-pressed bast strands , but not from opened individual fibers . The dehydration process, which is essential for defining the paper, also takes place neither on a screen nor by mechanical dehydration. In this respect it would be wrong to speak of an invention of paper in America. The actual and independent original production of paper can only be proven for Asia and Europe.
Invention of paper
Although there are finds from China that date back to around 140 BC. And although Xu Shen described the manufacture of paper from silk waste as early as 100 AD, the invention of paper is officially attributed to Ts'ai Lun , who around 105 AD (document date of the first mention of the Chinese Paper-making method ) was an official of the authority for the manufacture of instruments and weapons at the Chinese imperial court and was the first to describe the process known today of making paper . In his day there was a paper-like writing material made from silk waste (chi) . The early papermakers mixed this primarily with hemp , old rags and fishing nets and supplemented the material with tree bark or bast of the mulberry tree . The Chinese invention consisted primarily of the new preparation: the cleaned fibers and fiber residues were mashed, boiled and soaked. Then individual layers were skimmed off with a sieve, dried, pressed and smoothed. When scooping the paper, there was a “beautiful side” that was on the side facing away from the sieve, and a “sieve side” that was against the sieve. The resulting pulp made of plant fibers was deposited as a fleece and formed a relatively homogeneous sheet of paper. This was a technique that was probably used in Korea in a separate form since the 2nd century AD and has been celebrating its renaissance for many years under the name Hanji ( 한지 ).
- Papermaking depicted on a Chinese woodcut ( Ming Dynasty )
Since raffia is a material that has longer fibers compared to the wood used and therefore a long service life, Ts'ai Lun's paper could not only be used for writing, but also for room decorations, e.g. in the form of wallpaper and clothing. The use of mulberry bast was obvious, as the silk moth fed on the leaves of the mulberry tree and this material was therefore an already existing by-product of silk production. How old is the use of bast is proven by the glacier mummy Ötzi (approx. 3300 BC), who wears clothes made of linden bast .
East asia

As early as the 2nd century, China had paper handkerchiefs, in the 3rd century sizing agents were added (starch), from the invention resulted the sizing (thin coating to paper smoother and to make less absorbent, the ink or ink runs less) as well as the coloring of paper. The first newspaper (Dibao) may have already been published. In the 6th century, toilet paper was made from the cheapest rice paper. In Beijing alone , ten million packages with 1,000 to 10,000 sheets were produced annually. The waste of straw and lime soon formed large hills, called "Elephant Mountains". The imperial workshop produced 720,000 sheets of toilet paper for the purposes of the Chinese imperial court. For the imperial family it was another 15,000 sheets of light yellow, soft and perfumed paper.
It is known that around the year 300 the Thais used the technique of the floating screen to make paper. The bottom grille of the sieve was firmly attached to the frame. Each scooped leaf had to dry in the sieve and could only then be removed. A corresponding number of sieves were necessary.
Around the year 600 the further developed technique of scooping with the scoop came to Korea and was used in Japan around 625 . The freshly scooped leaf can be removed while damp and laid out to dry. This technique is still used with handmade paper. From this it follows that the ladle sieve was invented between 300 and 600.
In Japan the technique was improved by adding plant slimes to the pulp, e.g. B. was upgraded by Abelmoschus manihot . The fibers were more evenly distributed and there were no lumps. This paper is called Japanese paper . The official robe of the Japanese Shinto priests, which goes back to the aristocratic costume of the Heian period , consists of white paper (washi), which is mainly made of mulberry tree bast.
In the Tang Dynasty , paper production was further improved, it was waxed ( china wax , beeswax ), painted , dyed and calendered . In order to meet the increasing demand for paper among the seaweed, the bamboo fibers were introduced for paper production. The Chinese emperor Gaozong (650 to 683) issued paper money for the first time . The trigger was a lack of copper for coinage. Since the 10th century, banknotes had prevailed in the Song Dynasty . From around 1300 they were in circulation in Japan, Persia and India and from 1396 in Vietnam under Emperor Tran Thuan Tong (1388-1398). In 1298 Marco Polo reported in his travelogue ( Il Milione ) about the widespread use of paper money in China, where there was an inflation at that time that caused the value to drop to around one percent of the original value. In 1425, however, paper money was abolished to end inflation. In order to make it more difficult to bring counterfeit money into circulation, paper money was temporarily made from a special paper that contained additives such as silk fibers, insecticides and dyes.
Arab world
When exactly the first paper was produced in the Arab world is controversial. The date 750 or 751 is mentioned, when Chinese people who were probably captured during a border dispute are said to have brought the technology of paper production to Samarkand . On the other hand, there are findings that lead to the assumption that paper was known and also manufactured in Samarkand 100 years earlier. Flax and hemp ( hemp paper ) were used as paper raw materials. Soon the Arabs had built a thriving paper industry.
In Baghdad , the paper-making was taken by 795, 870 there appeared the first paper Codex . Paper shops were scientific and literary centers run by teachers and writers. It was not by chance that the House of Wisdom was built in Baghdad at that time. In the offices of Caliph Hārūn ar-Raschīd , writing was done on paper. Paper mills followed in Damascus , Cairo , in North African provinces as far as the west. The Arabs further developed the manufacturing technique by introducing surface sizing. Rags and ropes were mixed, these were frayed and combed, then soaked in lime water, then mashed and bleached. This pulp was smeared on a wall to dry. Then it was rubbed smooth with a starch mixture and dipped in rice water to close the pores. Standardized surface dimensions were introduced, 500 sheets were a bundle (rizma), from which the term Ries , which is still used in the paper industry, goes back. The heyday of the Islamic empire lasted from the 8th to the 13th century . As a cultural center, Baghdad attracted artists, philosophers and scientists, especially Christians and Jews from Syria .
India
In India , paper was introduced under Islamic influence from the 13th century and began to replace the previously predominant palm leaf as a writing material in northern India . The Indian paper manuscripts are influenced by the example of the palm leaf manuscripts. The landscape format (which in palm leaf manuscripts is given by the natural dimensions of the palm leaves) was retained. In place of the holes for the string that holds the individual leaves together in palm leaf manuscripts, purely ornamental circles are used in paper manuscripts. In western northern India, paper completely replaced the palm leaf by the 15th century. The palm leaf remained in use in the East Indies until the 17th century. In contrast, paper could not prevail in South India. Here the palm leaf remained the preferred writing material until the advent of printing in the 19th century.
Europe

The writing material reached Europe from the 11th century onwards through the cultural contact between the Christian West and the Arab East and Islamic Spain . A significant part of the raw materials for early European paper production consisted of hemp fibers, flax fibers (linen) and nettle cloth ; the paper mills bought the rags they needed from the rag collectors who worked for them. According to a travel report by Al-Idrisi, there was already a flourishing paper industry in Xàtiva near Valencia in the middle of the 12th century, which also exported high-quality products to neighboring countries. Even after the expulsion of the Arabs from Spain , the area around Valencia remained important for the paper industry, because a lot of flax ( linen ) was grown there, which is an excellent raw material for paper production.
The so-called Missal from Silos is the oldest surviving Christian book made of handmade paper. It dates from 1151 and is kept in the library of the Santo Domingo de Silos monastery in the province of Burgos (Spain).
The mass machine production of paper began in medieval Europe; European papermakers succeeded in a short time in optimizing the work process by introducing numerous innovations - unknown to the Chinese and Arabs: the operation of water-powered paper mills mechanized the shredding process, which until then had only been done by hand or with animals in the pan . Such water mills , iron-reinforced rag tampering works, are first attested from 1282. Tearing the rags with a scythe blade replaced the cumbersome practice of tearing by hand or cutting with a knife or scissors. Paper presses , designed based on ancient wine presses , dried the paper using screw pressure.
The construction of the ladle strainer was also completely new, with a metal mesh replacing the older bamboo or reed strainers. The rigid ladle made of metal wire was the technical prerequisite for attaching the watermark used for identification , an Italian invention. A short time later, the refinement of paper quality at affordable prices contributed significantly to the success of modern letterpress, invented by Johannes Gutenberg .
With the spread of writing in more and more areas of culture (economy, law, administration and others), paper began its triumphal march over parchment from the 14th century. From the middle of the 15th century, with letterpress printing on cheaper paper, parchment began to take a back seat as a writing material. However, it was not until the 17th century that it was largely superseded by paper. As a result, parchment only played a role as a luxury writing material.
Spread of paper production in Europe
1056 | Europe's first reliably attested water-powered paper mill in Xàtiva (Spain). |
1109 | Sicily's oldest document written on paper. |
1151 | Missal from Silos - oldest surviving Christian book on paper. |
1225 | France's oldest paper document. |
1228 | From Barletta, Emperor Friedrich II sends the oldest paper document still available on German-speaking soil to the Göss nunnery in Austria. The mandate is in the house, court and state archives in Vienna. |
before 1231 | Paper production in Amalfi , Naples , Sorrento . |
1231 | Emperor Frederick II forbids the use of paper for documents in the Kingdom of Sicily because it is less durable than vellum and parchment. |
1236 | According to Padua's statutes , paper documents have no legal force. |
1246 | The register book of Passau cathedral dean Albert Behaim, written in Lyon on Italian paper, is the oldest paper manuscript preserved in Germany. |
1268 | Paper is made in Italy . |
1282 | Invention of the watermark in Bologna |
1294 | Animal sizing is introduced (Fabriano). |
Other fundamental innovations in this period: scythe blade, paper press, wire mesh screen | |
1381 | Toscolano-Maderno in Italy. |
1390 | Germany's first paper mill, the Gleismühl , was founded by Ulman Stromer in Nuremberg (see below). |
from 1393 | Other paper mills in Germany followed: 1393 Ravensburg, 1398 Chemnitz , 1407 Augsburg, 1415 Strasbourg, 1420 Lübeck , 1460 Wartenfels, 1477 Kempten (Allgäu) , 1478 Memmingen. By the end of the 16th century there were around 190 paper mills in Germany. |
1411 | Marly paper mill , Marly FR in Switzerland |
1469 | St. Pölten in Austria |
1494 | Stevenage in England |
1541 | The papermaker Hans Frey from Altenberg ( Moravia ) invents the smoothing hammer (ramming hammer) for mechanically smoothing the sheets of paper. |
1573 | Klippan in Sweden |
1576 | Moscow in Russia |
1586 | Dordrecht in Holland |
1588 | The first regular magazine in Germany appears in Cologne, the Messrelation . |
around 1605 | First newspapers in Germany by Johann Carolus . |
around 1670 | Invention of the Dutchman for the manufacture of paper. |
1690 | Germantown in Pennsylvania , USA by the German papermaker William Rittenhouse . |
The first German paper mill was built near Nuremberg in 1389/1390. Gleismühl was founded by councilor and export merchant Ulman Stromer . Stromer went on business trips, including to Lombardy , and came into contact with paper production there. Stromer had his employees and heirs take an oath to keep the art of papermaking secret. The track mill consisted of two plant units powered by water power. The smaller mill had two water wheels, the larger one had three. A total of 18 ramps were driven.
From 1389 to 1394 Stromer managed the paper mill himself and then leased it to Jörg Tirman, his colleague, for a lease of "30 reams of paper". The Schedelsche Weltchronik from 1493 shows it as the earliest depiction of a paper mill on the depiction of the city of Nuremberg. The track mill later burned down.
From 1393 the paper production in Ravensburg is proven. In the late Middle Ages and early modern times, the Upper Swabian imperial city developed into the largest paper manufacturing center in the southwest. For the 15th and 16th centuries, production in up to seven paper mills is estimated at around 9,000 reams (around 4.5 million sheets) annually.
The first paper mills only appeared east of the Elbe in the middle of the 17th century. Francois Feureton from Grenoble first founded a paper mill in Burg and then in Prenzlau with the support of Friedrich Wilhelm .
Technical development up to the 19th century in Europe
Until the second half of the 19th century, the cellulose fibers required were obtained from rags, i.e. from rags and worn linen textiles . Rag collectors and dealers supplied the paper mills with the raw material. At times rags were so popular and rare that they were subject to an export ban, which was also enforced by force of arms. In the paper mills, the rags were cut into shreds, sometimes washed, subjected to a digestion process and finally shredded in a tamper. The ramming plant was powered by water power.
The processing of raw materials still took place in the 17th century in artisanal businesses and in some cases in larger factories with a higher degree of division of labor. In the early 18th century, semi-mechanical rag cutters were introduced which initially worked according to the “guillotine principle” and later according to the “scissors principle”. In the first half of the 19th century, instead of rotting and cleaning rags, the transition was made to bleach with chlorine . The loss of fibers was less, and colored fabrics could also be made into white paper. The typical archive order in colored files, for example, dates back to the time when real colored blue and red rags could only be made into pink or light blue paper. Only in the 19th century were folders of different colors added (such as yellow).
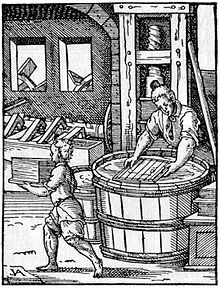
From the thin stock (fuel) in the vat (= vat , hence the name of the hand-made paper of the papermaking scooped up) the sheet by means of a very fine mesh, flat, rectangular suction screen made of copper by hand. The ladle is characterized by a removable rim, the lid. The size of the paper sheet was determined by the size of the screen. Now the Gautscher pressed the fresh sheet from the sieve onto a felt, while the maker scooped the next sheet. After couching, the arches were hung up to dry in large dry rooms, primarily in storerooms and attics. The paper was then pressed again, smoothed, sorted and packaged (one package corresponds to 181 sheets of paper). If it was writing paper, it was glued. To do this, it was dipped in glue , pressed and dried. The glue prevents the ink from running. In manual work, which is only used with fibers - and thus paper - of high quality, the fibers do not take a preferred direction ( isotropy ).
The modern technical breakthrough began with the invention of the "Holländers" around 1670. It is a machine that the pulp ( pulp no longer digests) pure by impacts, but through a combined cutting and impact. Due to the high speed of rotation, the Dutchman offered faster fiber passage than the rammer. This increased the productivity of fiber preparation. Usually, Dutch were initially used where there was only little water power available (low drive torque , but high speeds possible) and / or where a fine tool preparation was to be connected downstream of a large ramming plant. The time ratio for 1 kg of stock is around 12: 1 (tamping time / Dutch time), with gentle tamping clearly producing the better pulp . The Dutchman was used extensively in German paper mills from around 1710. Due to the higher possible entry in the Hollander (approx. 15 kg of fabric as opposed to 2–5 kg in the ramming plant) and the lower manpower required, the device spread quickly. The Dutch also requires less maintenance than a stamping mill, which has a significant impact on the reinvestment costs. Later directly from the Dutch process, the first continuous Mahler constructions (Jordan Mill were then taper fabric mill , disc refiner) developed.
Papermaker
A papermaker is a craftsman who makes paper. At present he works in a paper mill with corresponding production facilities (industrial paper mill). Since 2005 the profession has been called paper technologist according to the classification in Germany .
In the greatest number of cases, every senior paper miller used a watermark that was typical of the time he was at work. Since papermaking was a profession with a strong professional tradition within certain families, genealogical and watermark research complement each other. For this reason, the German Museum of Books and Writing in the Deutsche Bücherei in Leipzig is also the location of a papermaking index (see map ), in which the data of over 8,000 papermakers, paper mill owners, rag collectors and paper dealers, including their families, are recorded, and an index Paper mills with the papermakers that have ever been mentioned on them.
industrialization
The lack of rags, rags, which were necessary for paper production, became the bottleneck of paper production. Therefore, as early as 1700, alternatives for the rags were sought.
The French physicist René-Antoine Ferchault de Réaumur wrote in 1719 to the French Academy of Sciences in Paris :
“The American wasps make a very fine paper, similar to ours. They teach us that it is possible to make paper from vegetable fibers without the need for rag or linen; they seem to be asking us to try to make fine and good paper from certain woods. If we had types of wood similar to those used by American wasps to make paper, we could make the whitest paper. "
The doctor Franz Ernst Brückmann zu Wolfenbüttel made a contribution that seems bizarre today , dealing primarily with "earth plants and minerals". Accordingly, he proposed asbestos paper to solve the raw material problem and had some copies of his work "Historiam naturalem curiosam lapidis ..." or "Historia naturalis de asbesto" printed on asbestos paper in 1727 in Braunschweig . The book also contained his own portrait on this incombustible sheet - in order to become “immortal”.
Early and forward-looking attempts, and immediately on a commercial scale, were undertaken by the versatile and brilliant Brunswick chief hunter Johann Georg von Langen , because in June 1753 - with reference to older reports - he gave an account to his sovereign ( Carl I ) about an am "Holzminder Bach built a grater mill with the idea of using such a mill in the future." To grind “porcelain mass” on this mill had just failed, which is why v. Langen suggested that “this mill could be used at little cost to produce the packing and other paper that Holtz is made of.” Accordingly, he asked for the ducal license and noted that “such ('Holtz- Papier-Mühle ') would not only interest us "(because of the novelty of this technology) by manufacturing such a publicly useful Kauffmanns commodity, but would also pay for it in full over time. Because he had "invented a new kind of paper from Holtz Materie", so that around 1760/61 there was the prospect that the need for rags would be noticeably reduced over time. Unfortunately, there is still more to come. Von Langen had also dealt with other vegetable materials such as the use of "cane for wrapping paper" in 1756.
But more extensive experiments were carried out by Jacob Christian Schäffer in order to obtain paper from plant fibers or wood; He described this in six volumes "Experiments and patterns, without all rags or at least with a small amount of the same to make paper" between 1765 and 1771. His process for making paper from poplar wool , moss, lichen , hops, vines, thistles, field moss Atriplex campestris , mugwort , corn, nettle, aloe, straw, bulrush , blue carbon drunk, grass wool, lily of the valley, silk plants , broom , hemp shives , potato plants, peat, forest vines , pine cones, willow and aspen but as soon as sawdust and roof shingles were not good quality paper and were therefore not used by the paper garbage collectors.
Nevertheless, inspired by Schäffer's experiments, they found their new edition in Räbke near Helmstedt in Brunswick . Here in 1767, under the guidance of the Brunswick professor Justus Friedrich Wilhelm Zachariae , experiments were carried out with other "vegetable" fabrics than the previously indispensable white linen rags. Experts (paper manufacturers) carried out tests with very promising materials such as wild cardoon (weaver thistle), flax, hemp, cotton and finally even with “poplar willow” or the “common willow tree”, i.e. also with pioneering types of wood.
- 1756 In the countries belonging to Prussia , the rag export ban is issued and rag collectors are required to carry a rag pass.
- 1774 The use of waste paper as a raw material for new is initiated by the publication of the Göttingen professor Justus Claproth "An invention to make new paper out of printed paper and to wash out the printing ink completely". ( Deinking process)
- 1784 The French chemist Claude Louis Graf Berthellet uses chlorine bleach in the manufacture of paper.
- In 1798, the French Nicholas-Louis Robert received a patent for a longitudinal screen machine that enabled the paper to be manufactured by machine. In this paper shaking machine, the scooping of the paper pulp was replaced by pouring it onto a rotating metal sieve.
- 1804 The Englishman Bryan Donkin perfects the Fourdrinier paper machine.
- 1805 The first cylinder mold machine is patented to the English mechanic Joseph Bramah .
- 1806 The resin sizing of the paper already in the paper pulp, i.e. in the manufacturing process, is invented by the watchmaker Moritz Friedrich Illig from Erbach im Odenwald.
- 1820 The Englishman Th. B. Crompton registers a patent for drying the paper web.
At the beginning of December 1843, Friedrich Gottlob Keller invented the process of making paper from groundwood , using a grindstone to process wood in the cross-grain direction with water to make groundwood, which was suitable for the production of good quality paper. He refined the process by the summer of 1846 by designing three wood grinders. On October 11, 1845, he had a series of copies of the "number 41" of the intelligence and weekly newspaper for Frankenberg with Sachsenburg and the surrounding area printed on his wood pulp paper.
The industrial evaluation of his invention was denied to Friedrich Gottlob Keller because he lacked the funds for technical testing and the patenting of the process was refused by the Saxon Ministry of the Interior. On June 20, 1846, he transferred the rights to use the process for a small fee to the wealthy paper manufacturer Heinrich Voelter , who further developed the cellar wood grinding process, introduced it into practice and brought it to industrial use by developing auxiliary machines. From 1848 Voelter worked with the Heidenheim paper manufacturer Johann Matthäus Voith with the aim of making paper mass-produced. Voith developed the process further and, in 1859, invented the refiner , a machine that refines the chunky coarse material of the ground wood, thereby significantly improving the paper quality.
The wood grinder has been in use since around 1850, making it possible to manufacture paper from the inexpensive raw material wood on an industrial scale; around 1879 there were around 340 such wood grinding shops working in Germany alone. The greatest shortage of raw materials was alleviated through the use of wood pulp, but rags could not be completely dispensed with.
The oldest surviving wood grinding shop is the Verla cardboard factory in Finland , which was built in 1882. The factory, which was closed in 1964, was added to the UNESCO World Heritage List in 1996 .
The wood pulp papers proved to be problematic because of the residual proportions of various acidic substances contained in the pulp . These acid components originate from the chemical digestion process , which is inevitably required for the treatment of the shredded wood pulp ( lignocellulose ) in the industrially widespread sulphite process . From the sulfur dioxide and its salts are formed by air oxidation and hydrolysis reaction relevant amounts of sulfuric acid . Due to the constant exposure to air and humidity, organic, chemically very active substances continue to form in the paper. Other digestion processes work with chlorine compounds and acetic acid . These complex mechanisms of action lead to yellowing and to a considerable reduction in tear strength , wet strength and flexural rigidity in the end product, which is noticeable as the “brittleness” of the paper. The reduced stability in the paper is a consequence of the acid- catalyzed splitting of the cellulose molecule, which takes place in the form of a progressive chain shortening. The main cause of the yellowing of the wood pulp paper is the lignin and its decomposition products (mainly aromatic compounds ).
The wood pulp paper is often mistakenly equated with acidic paper. The acidic paper is a result of the manufacturing process and some chemical additives in its sizing. Wood pulp paper yellows particularly badly and quickly loses its elasticity. Inexpensive wood pulp and saponified resin sizing, invented in 1806, were used en masse, so that paper products (books, graphics, newspapers, maps) in particular have been used since the invention of wood pulp technology by Friedrich Gottlob Keller after 1846 and in the first half of the 20th century due to both causes subject to internal harmful effects in a special way. The restoration is complicated and, if the cellulose disintegrates at high rates, it is only possible through mass deacidification and subsequent stabilization processes such as the paper splitting process.
The wood pulp paper not only brought benefits for the inexpensive production of paper, but also caused great damage to the written records of the 19th and 20th centuries.
- 1850 Invention of the cone pulp mill (Jordan mill).
- 1854–1857 The Englishmen Watt, Burgess and Houghton produce wood pulp using a soda process .
- 1866–1878 The American Benjamin Chew Tilghman and the German Alexander Mitscherlich develop sulphite pulp through the chemical decomposition of wood on the basis of the Ritter- Kellner process.
- around 1870 Straw as a raw material for paper can be bleached.
- 1872 The brown sanding of paper, invented by Moritz Behrend (Varzin, Pomerania) in 1869, is introduced by the paper maker Oswald Mayh in Zwickau . The system was successfully presented at the Vienna World Exhibition in 1873 .
- 1872 The Prussian states lift the rag export ban.
- 1884 Invention of the sulphate pulp process by C. F. Dahl.
- 1909 William H. Millspaugh invents the suction roll.
- 1919 The first papers made from semi-synthetic fibers ( regenerated cellulose ) are manufactured by F. H. Osborne.
- 1921 Start of chlorine dioxide bleaching.
- 1945 Continuous stock preparation ( pulpers and refiners displace pan mill and Holländer).
- 1948 First magnesium bisulfite plant with chemical recovery.
- 1955 The first paper made from fully synthetic fibers ( polyamide ) is manufactured by J. K. Hubbard.
- from 1980 development of chlorine-free bleach
Since the 1980s, "non-aging paper" or "acid-free paper" has predominantly been used for printing high-quality publications and graphics. Thanks to suitable chemical additives, it is free from free acids and free chlorides and is standardized in DIN EN ISO 9706.
Technical development in the 21st century
- 2017 First production of paper coated with nanoparticles that can be reprinted up to 80 times in combination with UV light printing, provided that it has been heated to 120 ° C before each new UV print.
Industrial manufacture
Regardless of the type of fiber, paper can be made by hand or by machine. For machine production, the paper industry (“production of paper, cardboard and cardboard”) has established itself.
Paper consists mainly of cellulose fibers that are a few millimeters to a few centimeters long. The cellulose is initially largely exposed, i.e. separated from hemicelluloses , resins and other plant components. The pulp obtained in this way is mixed with a lot of water and shredded. The papermaker calls this thin pulp "stuff" or "stuff". If this is put in a thin layer on a fine sieve, it has a water content of over 99% (paper machine casserole) or about 97% in the case of handcrafting . Much of the water drips off. The sieve has to be moved so that the fibers lay as close together as possible and form a fleece , the paper sheet. When the paper is dry, the surface can be closed with the help of starch, modified cellulose ( e.g. carboxymethyl cellulose ) or polyvinyl alcohol . This process is known as gluing , although the term impregnation would be the correct one. Sizing takes place with resin soaps or alkyl ketene dimers within the fabric (glue sizing in the paper machine or vat ).
If a pattern made of wire is applied to the hand scoop or cylinder mold, fewer fibers are deposited at this point, and the pattern can be seen as a watermark on the finished paper, at least in the backlight . Watermarks are almost exclusively made on the paper machine as dandy watermarks .
raw materials
The most important raw materials for industrial paper production are wood and waste paper . In addition, certain annual plants are also used as a source of raw materials. All cellulose-containing substances are basically suitable for paper production, for example apple peel.
The fibrous materials ( pulp ) are produced from the paper raw materials. The primary fibers that are used only once or for the first time in production include wood pulp , semi-pulp and cellulose . The waste paper produced from waste paper is a secondary fiber (recycling material).
Wood
Almost 95% of paper is made from wood (in the form of wood pulp, semi-cellulose, cellulose or waste paper). The fiber formation and hardness of the wood play a role in the selection of the paper raw material, not every wood is equally suitable for every type of paper. Frequently, softwoods such as spruce, fir, pine and larch used. Due to the longer fibers compared to hardwood , these fibers felt more easily and the paper is stronger. But hardwoods such as beech, poplar, birch and eucalyptus are also used mixed with softwood pulp. The use of very short-fiber hardwoods is limited to highly finished special papers.
Availability and regional conditions mainly determine which type of wood is used as the primary raw material, although large quantities of wood for paper production have been shipped worldwide with so-called wood chip transporters since the 1960s . However, it must also be noted that the properties of the recoverable pulp correlate with the desired paper quality. Fast-growing woods such as poplar meet the great demand, but are only suitable for voluminous, soft and less tear-resistant papers. Pulps from hardwoods have shorter and thinner fibers than those from conifers. According to the later requirements on the paper, different mixtures of these short fiber and long fiber pulps or hard and soft fiber materials are used. The control of the properties can be varied slightly via the digestion process and the subsequent grinding. A spruce pulp can be boiled hard with caustic soda as well as long-fiber and softer using the sulfate process.
Waste paper
The importance of waste paper as a secondary raw material is increasing. Up to 100% of paper waste is used for less valuable types of paper. With fine papers, modern deinking material is gaining ever greater proportions. LWC papers sometimes contain up to 70% recycled paper without any significant loss of usability. In the 2010s, waste paper made up 61% of the raw materials used in Germany for the production of paper, cardboard and cardboard.
Since waste paper has already been processed into paper once, it contains many additives and has already been ground. The fibers are further damaged by being reprocessed into paper, and the proportion of additives in relation to the fibers increases. In practice, paper fibers are only recycled five to six times on average.
Annual plants
In Europe and America, wheat and rye are occasionally used for straw fiber production. North African grass varieties such as alfa and esparto grass can be used. Rice straw is still used in Japan, while in India it is fast growing bamboo. In terms of quantity, these fibrous materials do not play a major role worldwide compared to pulp made from wood. Cellulose from annual plants mostly shows properties like the typical softwood cellulose and is therefore also used as surrogates for this ( e.g. esparto instead of spruce). Hemp is also suitable for making paper.
Rags
Until the 19th century, rags were the most important paper raw material in Europe. Today rag is still used for special and heavily used papers, especially for security papers (for example papers for banknotes, securities, postage stamps).
Cellulose
The cellulose is the real, high-quality fiber base of each paper. Cellulose is a polysaccharide with the approximate chemical formula (C 6 H 10 O 5 ) n , from which almost all cell walls of plants and woods are made. Cellulose can be obtained from wood, waste paper, annual plants (e.g. straw) and rag.
Cellulose consists of many glucose residues linked together in a chain . The individual cellulose molecules are chain-like macromolecules , the smallest links of which are glucose units. The glucose molecule (C 6 H 12 O 6 ), the monomer of cellulose, forms a cellobiose with another glucose molecule by dissolving a water molecule . The stringing together of such cellobiose to a chain forms a cellulose molecule (a polymer is formed ).
The chain molecules form micelles with one another , which are bundles of molecules from which the fibrils are built. The visible cellulose fiber only forms a larger number of fibrils. The molecule bundles consist of crystalline areas (regular molecule guidance) and amorphous areas (irregular molecule guidance ). The crystalline areas are responsible for the strength and stiffness, the amorphous areas for the flexibility and elasticity of the paper. The length of the chain, i.e. the number of monomers, varies depending on the paper raw material and is of great importance for the quality and resistance to aging.
Preparation of pulp
Mechanical processing
White wood pulp
White sanding is made from sanded logs. For this purpose, peeled pieces of wood are ground with plenty of water in press grinders or continuous grinders . (Compare also wood grinder ) In the same company the heavily diluted fiber mass is processed into paper or made into cardboard for dispatch. This is done with dewatering machines.
Brown wood pulp
Brown grinding occurs when trunk sections are first steamed in large kettles and then sanded.
Thermomechanical wood pulp
Thermomechanical pulp (TMP) is made from chopped wood waste and wood chips from sawmills. These are steamed at 130 ° C in the TMP process (thermo-mechanical pulp process). This loosens the lignin connections between the fibers. The pieces of wood are then ground in refiners (pressure grinding machines with fluted grinding disks) and water is added. Thermomechanical wood pulp has a coarser fiber structure compared to ground wood. If chemicals are also added, the chemo-thermomechanical process (CTMP) is used. Wood pulp (RMP) obtained through purely mechanical processes does not consist of the actual fibers, but of ground and abraded fiber compounds, these are called lignified fibers . In order to obtain the elementary fibers, a chemical treatment of the wood is necessary.
Chemical processing

Wood chips are chemically treated in a cooking process. By boiling for twelve to fifteen hours , the fibers are separated from the incrustations , the unwanted wood components and accompanying substances from cellulose. From a chemical point of view, wood consists of:
- 40% to 50% cellulose
- 10% to 15% hemicellulose
- 20% to 30% lignin
- 6% to 12% other organic substances
- 0.3% to 0.8% inorganic substances
There is the sulfate process , the sulfite process and the soda process , which are differentiated according to the cooking chemicals used. The Organocell process is a new development. Residual lignin in particular gives the pulp a yellowish to brown color after boiling, so it must be cleaned and bleached . Residual lignin and other undesirable substances are removed during bleaching, chemical whitening removes discoloration. The bleached pulp is drained. It is now either processed directly into paper or wound up into rolls.
The yield in pulp production is lower than in wood pulp production. Cellulose fibers, however, have the advantage that they are longer, stronger and more supple. Pulp fibers obtained from softwood are approx. 2.5 mm to 4 mm long, those obtained from hardwood are approx. 1 mm long. The largest part, approx. 85% of the pulp required, especially sulphate pulp , is imported from the Scandinavian countries, the USA and Canada. Compared to sulphite pulp, sulphate pulp has longer fibers and is more tear-resistant, so it is mainly used for the production of bright white writing and printing paper. Sulphite pulp is mainly used in the manufacture of soft tissue paper.
Pulp bleach
The fiber material has to be bleached so that it can be made into white paper. Traditionally, the pulp was bleached with chlorine . However, this leads to high pollution of the waste water with organic chlorine compounds ( AOX ). More modern processes replace chlorine with chlorine dioxide for ECF pulps ( elemental chlorine free , without elemental chlorine). Due to the higher oxidation effect and the better selectivity of chlorine dioxide, the AOX load is reduced by 60 to 80%. If chlorine compounds are completely dispensed with and oxygen, ozone , peroxyacetic acid and hydrogen peroxide are used, the pulp is designated with TCF ( totally chlorine free ). Paper made from ECF cellulose is called low in chlorine (there are still chlorine compounds present). Low-chlorine printing papers can be produced in high-white quality from a weight per unit area of 51 g / m², chlorine-free only from 80 g / m².
TCF pulp has a lower fiber strength than chlorine-bleached or ECF. Paper made predominantly from wood pulp is called wood-containing , in the trade it is called medium-fine . Since lignin, resins, fats and tannins remain in the pulp, they are of lower quality than wood-free papers .
Organocell process
The organocell process, once implemented on an industrial scale and world-leading in the Lower Bavarian town of Kelheim, is used for sulfur-free and therefore more environmentally friendly pulp production. In several cooking stages, the wood chips are digested in an ethanol - water mixture with the addition of caustic soda at temperatures of up to 190 ° C under pressure. Lignin and hemicellulose dissolve in the process. This is followed by various washing stages in which the pulp is freed from the cooking liquid, as well as bleaching and dewatering.
The pulp is bleached in three stages:
- in an alkaline medium with oxygen using hydrogen peroxide
- with hydrogen peroxide or chlorine dioxide
- with hydrogen peroxide
Ethanol and caustic soda, the cooking chemicals, are recovered in a recycling process that runs parallel to pulp production. Sulfur-free lignin and sulfur-free hemicellulose are obtained, which can be used by the chemical industry.
Straw pulp
By crushing and boiling in caustic soda, straw is turned into pulp or, with other processing, yellow raw material .
Pellet cooker and pulper
Rags are cooked in the ball cooker. To do this, they are first sorted and cleaned in the rag harvester . The rags are boiled with lime liquor and soda under steam pressure of 3 bar to 5 bar in a spherical cooker. This destroys dyes, saponifies grease and loosens dirt. During the several hours of cooking, the tissue of the rags loosens and they can then easily be shredded into pulp.
The pulper is a vat with a rotating propeller. In it, waste paper that is sorted according to quality class and compressed into bales is shredded with plenty of water and mechanically broken down. This protects the fibers of the waste paper. In the past, this operation was often carried out with the pan mill . The pumpable pulp is still contaminated. In the pulper it enters a cylinder and is shredded by a rotor. Then the coarse solute is pressed through a sieve. Coarse impurities are separated out as a result of the centrifugal force. The light dirt collects on the cylinder axis. Other foreign substances such as wax and printing inks are removed in special systems.
Discoloration of waste paper
During deinking , the printing inks are detached from the fibers of the waste paper with the help of chemicals ( soaps and sodium silicate ). By blowing air at the surface of the formed pulp foam , in which to collect the paint components and can be skimmed off. This separation process is called flotation .
Pulp milling
During pulp grinding , the pulp is further defibrated in refiners (cone pulp mill ). The semi-finished product flows as a thick pulp in the refiner between a knife roller and base knives attached to the side. The fibers are cut ( crispy grinding ) or crushed ( greasy grinding ), depending on the setting of the knife. The ends of the crushed fibers are fibrillated (frayed), which leads to a better connection of the fibers when the sheet is formed.
- Soft, voluminous, absorbent and velvety types of paper are made from crispy ground fibers such as blotting paper.
- Greasy ground fibers lead to firm, hard papers with low absorbency and cloudy or even transparency as for transparent drawing paper, but also paper for documents, banknotes and typewriters.
In addition, the fibers can be kept long or short during the grinding, with the long fibers felting more than the short ones. There are four different ways of grinding. Fiber length and type of grind determine the fiber and paper quality. Usual combinations are “rösch and long” or “greasy and short”. The refiner's knives are very close to each other during short fiber grinding, so that there is almost no space between them.
Processing to the pulp
The manufacture of the stock includes mixing the various pulps and adding fillers, dyes and other auxiliaries.
Fillers
In addition to the fibers, up to 30% fillers are added to the pulp . These can be:
- Kaolin ( China clay ): In the past, kaolin was the most widely used pigment in papermaking. Kaolin remains chemically inert over a wide pH range and can therefore be used not only in acidic but also in alkaline production processes. However, since around 1990 the proportion of kaolin in paper production has decreased significantly, as it has been gradually replaced by calcium carbonate both as a filler and as a coating pigment . Kaolin is the preferred material in acidic papermaking. The use of calcium carbonate in acidic paper production is not very widespread, as it is destroyed due to chemical reactions with the acid and therefore no longer fulfills its intended function. In the past decade there has been a trend in the paper industry from the use of kaolin to calcium carbonate. This trend has been caused by several factors: On the one hand, the increasing demand for whiter paper and the further development of precipitated calcium carbonate (PCC), which made it possible to use it in coating applications for paper and in mechanical printing processes, and on the other hand, the increasing use of Recycled paper that requires stronger and whiter pigments, the carbonates .
- Talc : Talc reduces the porosity of paper and is therefore used to improve the printability of uncoated papers. However, its properties differ considerably from those of calcium carbonate. The use of high-priced talc to influence the wood fiber grain improves the running properties of the paper. However, the gloss and the light scattering achieved are below those of calcium carbonate.
- Titanium White (Titanium Dioxide): Titanium dioxide can provide high opacity, good light scattering and excellent gloss, but this material is many times more expensive than calcium carbonate and is therefore not used in standard filling or painting applications. It is used for the production of high quality paper in small quantities, such as for Bibles.
- Strength
- Barium sulfate: Blanc fix
- Calcium carbonate
- a) Ground calcium carbonate (GCC): The chemical formula CaCO 3 describes a raw material of which there are natural occurrences all over the world. Despite the large number of deposits, only a few are of such high quality that the raw material can also be used in industry and agriculture in addition to the construction sector and road construction . The most important CaCO 3 -containing materials used for the production of GCC are sedimentary rocks (limestone or chalk) and the metamorphic rock marble, which are mined both in open-cast mining and underground. Then sludge and impurities such as colored silicates , graphite and pyrite are removed in a screening process . After sieving, the raw material is further crushed and ground until the required grain size for the application in question is reached. Marble chippings from high-quality deposits can also be delivered directly to the GCC works without further processing. GCC is obtained from various sources (limestone, chalk, marble) and has a wide range of brightness. When a high level of lightness is required, the paper industry usually prefers marble. Limestone and chalk can also be used, but have a lower level of brightness. As a filler, GCC contains 40 to 75% grains with a size of less than 2 µm. With the switch from acidic to alkaline / neutral paper production, GCC has replaced kaolin as the leading filler pigment. While GCC is an important paper filler, in Europe it is primarily used as a paper coating pigment.
- b) Precipitated calcium carbonate (PCC): PCC is a synthetic industrial mineral made from quicklime or its raw material, limestone. In the paper industry, which is the largest consumer of PCC, the material is used as a filler and as a coating pigment. Unlike other industrial materials, PCC is a synthetic product that can be shaped and modified to give different properties to the paper being made. The physical form of the PCC can change significantly in the reactor. Variable factors include the reaction temperature, the rate at which carbon dioxide gas is added, and the speed of movement. These variables influence the grain size and shape of the PCC, its surface size and surface chemistry as well as the grain size distribution. Although there are many advantages to using PCC to control the properties of the paper (greater brightness, opacity and thickness than GCC), PCC cannot be used indefinitely as a filler because it reduces fiber strength. PCC is also used as a paper coating pigment, but the amounts used are small compared to the amounts of PCC used as a paper filler.
- Other fillers: Numerous other minerals are used in various applications with small application quantities. These include plaster of paris, bentonite , aluminum hydroxide and silicates. However, these minerals are only used to a very limited extent and only make up 3% of the pigments used in the paper industry.
By filling in the spaces between the fibers, the fillers make the paper softer and more pliable and give it a smooth surface. The mass fraction of the fillers is expressed in the "ash number". In the case of special papers, which, as in the case of “theater program paper”, should be rustle-free, a high ash content is combined with long fibers. Cigarette paper is also heavily filled so that it glows and does not burn off.
The composition and crystal structure of the fillers determine the transparency and opacity of a paper as well as the acceptance of the ink when printing with striking colors. On the other hand, glue is necessary for ink resistance. Fillers can partly also take over the properties of the dyes. Many pigment dyes are also effective fillers.
Dyes
White papers also sometimes contain dyes, which are added in different amounts, because optical brighteners are also among the dyes. Synthetic dyes are mainly used for colored colors . When dyeing paper, it is important to match the color system to the fiber properties and the sizing system used. Basically, acidic (substantial, self-absorbing) dyes and alkaline or acidic developing dyes, i.e. laking dyes, are used. The former are easy to use, but are sensitive to fluctuations in the pH value with inadequate fixation. The latter tend, because of the necessary precipitation reaction, to lye beyond the fiber, so that a large part of the liquor shows ineffective color loss. Dyes react preferentially to cellulose or wood components, rarely to both. It is important to choose the right system for the pulp to be dyed. A special group are the natural or pigment dyes (body colors). Both are only effective to a limited extent, as they are usually held in the leaf by storage in the lumen and by capillary retention . Intensive tints are only possible with vat coloring ( indigo ) or red pigments (red lacquer, cochineal ).
Sizing agents
Glue makes the paper writable because it becomes less absorbent and less hygroscopic . Sizing is the hydrophobization of the fibers in papermaking . The adhesives are chemically modified ( saponified ) tree resins in combination with acidic salts such as potassium alum or aluminum sulfate . Polymers based on acrylates or polyurethanes are also used.
In addition to various resins, ASA (Alkenyl Succinic Acids = increasingly alkenylsuccinic anhydrides ) and Alkylated ketene dimers (AKD, Ketenleimung) used for sizing paper. The acidic sizing with resin acids and alum , which was frequently used in the past, is the main reason that papers sized in this way are destroyed during archiving. The aluminum sulphate used instead of the alum can form sulfuric acid through excess residual ions , which in turn destroys the cellulose. Sizing is usually carried out in a neutral or slightly alkaline pH range . However, some paper dyes require acidic sizing, whereby the classification acidic or alkaline only refers to the process-related pH value of the vat, not to the finished end product. The choice of paper sizing is also influenced by the following work steps. After printing, the binding agent of the printing ink can penetrate the paper, lower the degree of glue and significantly reduce the writability of the printed paper.
When it comes to gluing, a distinction is made between in-situ gluing and surface gluing. In the case of in-situ sizing, the sizing agent is added to the liquor; in the case of surface sizing, the already finished paper is coated. Saponified resins, alkyl ketene dimers and ASA are typical bulk sizing agents, polymeric sizing agents such as gelatin or starch derivatives are used rather than surface sizing agents . Above all, the inherent retention and the technically possible use of retention chemicals are decisive for the possible use as an effective engine-size sizing agent.
Wet strength agent
Untreated paper becomes mechanically unstable when it becomes damp or wet. When the hydrogen bridges are split up when water enters, the fiber fleece loses its inner cohesion. Paper is therefore also called hydroplastic . In order to maintain mechanical strength, albeit limited, when wet, wet strength agents are added to the paper during manufacture . Tear-resistant kitchen paper is probably the best-known paper in this class, but cardboard boxes , map paper or security paper for banknotes also contain large amounts of wet strength agent. Wet strength agents are water-soluble polymers in the processing state , which are primarily made from polyamines and epichlorohydrin derivatives and react with the paper fibers. Water-insoluble cross-links form between the fibers, which stabilize the paper felt. However, the covalent cross-linking prevents successful recycling, so that the increasing use of wet strength agents in the hygiene paper sector has far-reaching consequences for the recycling of waste paper. The incidence of insoluble specks in the normal loosening process is constantly increasing. If wet strength agents (similar to bitumen adhesives ) are broken down chemically, the fiber degrades at an atypical rate. The quality of the recovered paper declines faster than in normal recycling processes. Wet strength agents must not be confused with sizing chemicals (e.g. AKD), as the chemo-physical process is different. For example, wet-strength, unsized paper is still highly capillary , whereas over-sized paper can still be frayed after long exposure to water.
Other auxiliary materials
Other auxiliaries include defoamers , dispersants , retention aids , flocculants and wetting agents .
Paper machine
The paper web is formed on the paper machine . The following machine stations are connected in series:
- Headbox
- Wire section
- Wet press section
- Dryer section
- Winding up
Foliage
In industrial paper production, sheet formation takes place on the paper machine. The purified and deaerated pulp, which consists of about 99% water is in the headbox formed into a thin, uniform as possible beam. In Fourdrinier paper machines, this meets a rotating, endless screen (see also metal cloth ). On the wire, the fibers are increasingly oriented in its direction of movement, which leads to different properties of the paper in the longitudinal and transverse directions (see machine direction ).
In the wire section of the paper machine, a very large part of the water runs off within a few seconds and the paper structure is created. Suction cups placed under the screen and foils that generate pulsations contribute to the dewatering of the pulp. Often attempts are also made to increase the temperature of the suspension (for example using steam blowers), which also promotes drainage via a lower viscosity . If the paper is to contain a watermark , this is incorporated into the screen or is applied from above using a so-called dandy roll.
Paper produced on Fourdrinier paper machines usually has a pronounced two-sidedness due to the one-sided drainage : The top is smoother than the bottom, the fillers are not evenly distributed. In some cases, this can be remedied by dewatering upwards using a second screen (so-called hybrid former), which also increases the overall dewatering performance.
Fourdrinier paper machines reach their physical limits at speeds of approx. 1200 m / min at the latest, as the air turbulence generated above the fourdrinier wire destroys the formation. Modern paper machines, especially for graphic paper and tissue , produce at speeds of up to 2000 m / min with working widths of more than ten meters. For this reason, other headbox concepts have been developed for these machines, so-called gap formers : Here, the paper pulp is injected directly into a gap between two rotating wires. In addition to the higher running speed, gap formers also offer significantly more even drainage and thus reduced bilateralism.
Pressing and drying
At the end of the wire, the soft paper web is transferred to a felt and reaches the press section . Traditional press sections consist of three to four successive presses in which the paper web is dewatered by means of rollers pressed against one another between felts. Since the beginning of the 1990s, however, the concept of the shoe press, in which a roller presses the felt and the paper into a polymer-covered shoe, has become increasingly popular. This results in a significantly greater nip length , which means that more gentle and at the same time stronger drainage can be achieved.
In the dryer section , finally, the final dewatering takes place. Here the paper web runs through a number of steam-heated drying cylinders and is then smoothed and rolled up. In some cases (highly smooth and sharp satin papers), a further smoothing step in before the final rolling calender completed.
Coated paper
Coated paper (also art or picture printing paper) is a paper on which the surface is finished with a coating color ("coating") consisting of pigments, binders and additives . The paper is given a closed, smooth and stable surface, which results in better quality printing .
Standard dimensions for paper
arc | 1 piece (a "sheet") = 8 sheets in the bound book = 16 pages |
---|---|
Book with writing paper | 24 sheets |
Book at printing paper | 25 sheets (A4 paper with 80 g / m² DIN 6730) |
Ries , Rieß | 20 book ("a package") |
Bale | 10 reams |
Formats according to EN ISO 216, DIN 476:
The best-known internationally standardized paper formats are those of the A series according to DIN 476 paper format , which has been partially replaced by EN ISO 216 since 2002. Different formats are used in some countries, such as the United States and Canada .
Paper processing
A number of tools are available for processing paper, especially cutting it to specific formats. From ancient times scissors and paper knives, more recently paper cutting machines:
- Rotary trimmers, primarily for domestic use for trimming one or a few sheets of paper (or photographs); mostly consisting of a cutting board with ruler functions and a cutting stick.
- Lever cutters in various sizes, from domestic use to small commercial use, for example in graphic studios or small copy shops, which can cut several sheets at the same time and be mounted on their own frame, which can have safety measures (protective hoods), fine adjustment and / or locking mechanisms.
- Pile cutters that cut stacks of paper up to 80 mm (approx. 800 sheets), mostly mechanically operated by hand, often weighing 50 kg and more, have an adjustable back stop and press devices to fix the paper. The cut surfaces usually vary between DIN A3 and larger. The drive is mechanical or electromechanical.
- Automatic paper cutting machine for print shops or industrial production, nowadays mostly with electronic tracery, differentiated security systems (two-hand operation, light barriers ) and electromechanical drive.
Paper market
406 million tons of paper, cardboard and cardboard are produced annually worldwide (as of 2014). The largest producers (as of 2014) are China (108 million tons), the USA (73 million tons), Japan (26 million tons) and Germany (22.5 million tons).
One third of the world's paper production capacity is in the European paper industry. Europe is the leader in the manufacture of printing and writing paper, followed by Asia and North America , and has a share of almost 26% of total paper and cardboard production. With the consolidation of the European paper industry over the past decade, the number of companies, paper mills and paper machines in Europe has decreased, but production capacity has increased significantly at the same time. It is estimated that the top 20 paper manufacturers currently account for almost 40% of the world's paper and cardboard production. The turnover of the European paper industry in 2015 was around 79 billion euros. 180,000 people work in the European pulp and paper industry. In addition to large paper manufacturers such as UPM-Kymmene , Stora Enso , International Paper , Svenska Cellulosa Aktiebolaget (SCA), Metsä Board , Sappi or the Smurfit Kappa Group, there are a large number of medium-sized and smaller paper manufacturers such as B. the Palm paper mill or the WEIG cardboard mill .
The German paper industry , whose interests are represented by the Verband Deutscher Papierfabriken (VDP), is number one in Europe with a production volume of 22.6 million tons (2015) of paper, cardboard and cardboard and is behind China, the USA and Japan in fourth place. The around 40,600 employees in the German pulp and paper industry in 162 plants generate sales of 14.4 billion euros (2015), an increase of 0.9% compared to the previous year.
sorts
About 3000 types of paper are known. These result from the wide range of possible combinations for raw materials, production, processing and use.
properties
Source:
General properties
- Hygroscopicity : Adaptation to the humidity of the ambient air through adsorption (absorption of moisture) and desorption (release of moisture).
- Inhomogeneity: fluctuations in the fiber orientation, the distribution of the components, the filler content; possibly recognizable as "cloudiness" of the paper even without a microscope.
- Anisotropy : Dependence of the properties on the direction in the plane of the paper, see below for the direction of travel .
- Two-sidedness (differences in the texture of both sides of the paper): The upper side is rather smooth, dense, with a higher proportion of fines, it is also called the beautiful side or the felt side . The underside, also known as the sieve side , is rather rough, porous, with a higher proportion of coarse material. The cause is the one-sided drainage through the underside during sheet formation in the paper machine. The two-sidedness causes different printability of the pages and often also a tendency of the paper to curl ("curl").
Geometric properties
area based size
The mass (or colloquially also the weight ) of paper is usually specified in relation to the area - specifically in grams per square meter (g / m²). The area-related mass (colloquially also called areal weight or grammage ) is 80 g / m² for normal writing paper. An A4 sheet therefore has a mass of 5 g. Three of these sheets plus the envelope are therefore just below the permitted mass of 20 g for a standard letter . 1000 sheets of A4 paper weighs 5 kg, 200,000 sheets of A4 paper weigh around one ton. Paper, cardboard and paperboard are mainly differentiated on the basis of the area-related mass ( see above ).
In the international paper trade, the mass per unit area (in g / m²) is also referred to as the basis weight . In the USA and in countries that use paper in US formats, on the other hand, the basis weight is the mass of 500 sheets. The specification of the basis weight in the USA depends on the dimensions of the paper sheet.
Papers for the book block of literary or scientific books usually have 80–100 g / m² with 1.0–1.8 times the volume.
Density and thickness
The density of normal writing paper is in the order of magnitude of 800 kg / m³, the thickness of a single sheet is 0.1 millimeters.
Thickness of a single sheet, also called thickness (English caliper , specification in the USA in 1/1000 inch = 25.4 μm). Standards: DIN EN 20534, ISO 534 (paper / cardboard); FEFCO 3 (corrugated cardboard).
Physical Properties
In principle, it should be noted with all measurements that air humidity and temperature have a very large influence on the measured values. For this reason, the measurement always takes place in climatic rooms with a standard climate (23 ° C, 50% humidity) defined in accordance with ISO standards. Usually the paper sample is stored in the room for 24 hours before the measurement in order to acclimate it. Since the measurements depend on the weight per unit area of the paper (also called weight per unit area or grammage ), so-called laboratory sheets with a weight per unit area defined in accordance with the ISO standard are used.
- Porosity: The porosity indicates how much air a paper lets through. The unit of measure for porosity is Gurley . For this purpose, the standard sheet is clamped into the test apparatus and the test apparatus pushes 100 ml of air at 1.23 kPa through a test area of 6.42 cm²> and measures the time required for this. A duration of one second corresponds to a Gurley.
- Smoothness / roughness according to Bekk (in GL (Bekk) s, ISO 5627), Parker Print Surf (PPS surface roughness in μm, DIN ISO 8791-4), Bendtsen (in mPas, ISO 5636-3, DIN 53108), Gurley (in ml / min, ISO 5636-5) or Sheffield (in ml / min, ISO 8791-3); optical laser measurement e.g. B. with UBM microfocus (DIN 4768).
- Water resistance DIN 53122-1: gravimetric, -2 water vapor permeability according to Brugger.
- Cobb test DIN EN 20535, ISO 535
- Weather resistance
- Moisture content / degree DIN EN 20287, ISO 287.
- Equilibrium moisture content
- Oil absorption, oil absorption according to Cobb-Unger; Fat permeability DIN 53116, ISO / DIS 16532-1.
- Absorbency, absorption capacity, degree of sizing (DIN 53126, Zellcheming V / 15/60 ), suction height (DIN ISO 8787, DIN 53106).
- Contact angle
- Conductivity: Paper is generally considered to be a good insulator because when it is dry it usually does not conduct heat well and electricity hardly at all.
- Heat conducting properties: see thermal diffusivity
- Electrical conductivity : see electrical conductivity
- Writability
- Printability
- Air permeability DIN 53120-1
- Ash content, residue on ignition DIN 53136, 54370, ISO 2144.
Mechanical properties
tensile strenght
Tests according to DIN EN ISO 1924: quotient (in kN / m) of breaking load and width of a paper strip; derived: tensile index / stiffness (in N / m); Tensile stiffness index (in Nm / kg) as the quotient of tensile strength and grammage.
The tensile strength is one of the key physical values in paper production in kraft paper it is even the most important value. The unit of measurement of the tensile strength based on the width of the paper sample is N / m. Since the tensile strength mainly depends on the mass per unit area, the tensile strength index (ZFI) is also used with the unit Nm / g.
A tensile test is made to determine this value. For this purpose, paper strips of a standardized length and width are mechanically clamped, the so-called “tearing apparatus” pulls the sample apart and records the required force. The force required at the moment of breaking is the tensile strength. To get an average value, ten strips are usually torn, five of which are taken along the machine direction and five across the machine direction. As a by-product of this measurement, the elongation at break and the work at breakage are also determined. The elongation at break is given in percent and indicates the percentage by which the paper strips are elongated at the moment of breakage. The tensile work is given in J / m² and is the applied tensile force per paper surface.
Specific tear resistance
Puncture / further / tear strength, standards: ISO 1974, DIN 53115 (Brecht-Imset), DIN EN 21974 (grammage-related Elmensdorf tear index in mNm³ / g).
The unit of measurement for the specific tear resistance is mN · m² / g. This unit of measurement indicates how easily a paper that has already torn tears on. For this purpose, the paper is provided with a cut and clamped into the tear strength tester (according to Elmendorf). Pressing a button triggers a blocked pendulum, which tears the sample in the course of the pendulum movement and measures the force.
Burst resistance
Pressure (in kPa) that a substrate can no longer withstand; the bursting factor is derived (pressure due to grammage); Burst strength according to Mullen (DIN ISO 2758: paper; DIN 53141-1: cardboard), according to Schopper (DIN 53113), on corrugated cardboard (ISO 2759, DIN / ISO 3689: wet, FEFCO 4).
The bursting resistance indicates the pressure required to cause a paper to burst. The unit of measurement for bursting resistance is k Pa . For this purpose, the standard sheet is clamped in the testing device and a membrane with a standardized surface presses against the paper with increasing force. The pressure required to pierce the paper is called the burst resistance.
Gap resistance / strength
Resistance that paper, cardboard or a composite opposes a vertical stretching ( TAPPI T 541) or a sliding movement (Scott Bond test: TAPPI T 833 pm-94 and T 569, Brecht-Knittweis gap resistance: DIN 54516).
The gap resistance indicates the force to be applied which is required to split the paper web in bulk. This is usually used for multi-ply papers on which several paper webs have been wet (25–35%), for example with folding boxboard (FSK) or particularly voluminous papers (bulk density <1.5) such as beer coasters.
Other mechanical parameters
- Flexural rigidity : ISO 5628, DIN 53121
- Breaking resistance / breaking load: DIN53112
- Elongation at break / at break: DIN EN ISO 1924-2
- Curling, arching: ISO 14968: sheets from a pile DIN 6723-1 / -2: arching inclination, DIN 6023: arching height according to Brecht.
- Puncture resistance, puncture resistance ': ISO 3036, DIN 53142
- Tear resistance
- Modulus of elasticity : DIN 53457 (modulus of elasticity)
- strain
- Seam breaking: DIN 55437
- Number of folds: ISO 5626 (number of double folds according to Schopper)
- Fold resistance: ISO 526
- Edge shrinkage
- Chuck resistance : good correlation between IGT (ISO 3783) and Prüfbau chuck tests
- Cutting edge quality: ISO 22414
- Ring crush resistance: ISO 12192
Optical properties
opacity
Percentage ratio of the reflection factors of a single sheet over a black base and a stack of at least 20 sheets (DIN 53146, ISO 2471), also the radiation transmittance in the UV-vis range (DIN 10050-9).
The degree of opacity of the paper refers to its ability to block light from showing through. Paper is opaque if the incident light is scattered back or absorbed in the paper . The more light is scattered, the more opaque the paper is. Opacity is a desirable quality that will minimize the show through of the print. A sheet that is 100 percent opaque does not allow any light to shine through, and thus also not the print, provided the printing ink does not penetrate. In general, the lower its basis weight, the lower the opacity of the paper. The degree of whiteness and lightness of the filler, its grain structure and size, its refractive index and the filler content are factors that determine the opacity of the paper.
brightness
The brightness is a measure of the light-reflecting properties of the paper, which influence the reproduction of contrasts and halftones . The difference between the brightness level achieved by kaolin (80 to 90 on the ISO brightness scale) and the brightness level achieved by calcium carbonates (GCC over 90 and PCC 90-95) is considerable.
Whiteness
The degree of whiteness is a technical parameter for the reflectivity of the paper for white light . Ideally, it is measured with a spectrophotometer . The numerical value is calculated from the spectral distribution using various formulas. The Berger whiteness is mostly used for paper . With normal copier paper without UV-sensitive brighteners, the degree of whiteness according to Berger is around 160. The measurement results are influenced by optical brighteners and dyes . That is why the degree of whiteness is usually determined under standard light , which has a lower proportion of short-wave UV radiation than daylight . Commercially available white papers are usually lightened. Neutral white papers measured under standard light look more yellowish under incandescent lamp light, but bluish-white in sunny daylight or under fluorescent lamps .
The degree of whiteness only indicates the achromatic proportion of a measured area in relation to an ideally white or ideally black area. In the case of two papers that have the same degree of whiteness in terms of measurement technology, there may be a visible color cast that falsifies the subjective impression of whiteness. People perceive slightly yellow or reddish paper to be less white, i.e. gray compared to a slightly bluish or greenish paper of the same whiteness.
The degree of whiteness is used as a standard test in paper production. In order to avoid unwanted color casts, the user must also consider the color cast of the paper in addition to the whiteness. The effect of the “increase in whiteness” through optical shifting is used, among other things, to “blue” the paper. The yellow tint is reduced by adding blue pigments . With the so-called “pressing”, paper that is too white is broken by adding red or brown pigments. In both cases, the technical degree of whiteness decreases slightly, but the subjective impression of whiteness is increased with blueing and decreased with "pressing".
Other optical properties
- Gloss parameters
- 45 ° DIN gloss
- 75 ° DIN gloss
- 75 ° TAPPI gloss
- Color parameters
- LAB value
- CIE whites
- R457 purity whiteness
-
Kubelka-Munk values: determination of the light scattering and absorption coefficient
- Absorbency
- Throwing power
- opacity
- transparency
- Color cast: Deviation from paper white (ISO 11958, DIN 55980: absolute color cast DIN 55981: relative color cast ISO 11475: tone deviation number from CIE whiteness)
- Hue , coloring: color measures for tinted substrates, e.g. B. CIE L * a * b * or color difference Delta E * (ISO 7724, DIN 5033 or 53140 or with Elrepho DIN 53145), diffuse reflection factor (ISO 2469, for C / 2 ° ISO 5631).
- Lightfastness : DIN EN ISO 105-B02, Xenotest Alpha
- Mottling test: Image analysis method (Mottling Viewer from Only Solutions), with which the cloudiness of papers is assessed
- Transparency: DIN 53147
- Yellowing: DIN 6167
Running direction

While the fibers are laid evenly in all directions in paper production by hand, in machine paper production on an endless screen there is a (partial) alignment of the fibers along the belt. The longitudinal direction of the belt in the paper machine, also called the machine direction, thus corresponds to the preferred direction of the fibers. In the paper this is the direction of travel. The transverse direction is transverse to the direction of travel. The transverse direction is also the direction of the fiber thickness, so that in the transverse direction there is an approximately three-fold swelling and shrinkage of the paper compared to the running direction. The paper is more stretchable in the cross direction than in the machine direction.
In the paper trade and in printing, the machine direction and cross direction are assigned to a format using the terms narrow and short grain :
- Short grain (SG): Sheet of which the short edge is parallel to the machine direction
- Narrow Grain (LG): Sheet with the long edge parallel to the machine direction
This knowledge is important for the format position to be used in various types of machine and further processing processes to be observed (fold positions, later book format). The register can be adjusted in the circumferential direction within the printing machine, but not in the transverse direction. For offset work with a high volume of dampening solution, the first plate in the machine must be set up to be shorter than the last and the paper must run in short grain so that the swelling can be precisely compensated from plant to plant.
In catalogs and on price labels, the dimension across the direction of travel is underlined or in bold or mentioned first. The abbreviations SB (narrow grain) and BB (short grain) or an arrow that marks the direction of travel are also common.
Depending on the prevailing fiber direction, moisture, temperature and aging affect the paper. In the event of an uneven alignment, each map changes its exact scale differently in the two directions over time and with the change in weather or room climate. This effect can only be reduced in machine-produced papers by using special or layered types of paper.
When producing books (and other items made of paper), make sure that the direction of travel of all pages, the book cover and cover material is parallel to the spine , as paper always expands or shrinks across its direction. Otherwise the book will easily break apart at the binding or it will be difficult to leaf through. If the direction of travel of the materials to be combined is ignored when paper and cardboard are glued, this leads to wave-like distortions that are irreversible. There are several practical methods for checking the direction of travel.
By gluing several layers of paper on top of each other in alternating directions, rigid paper is created (comparable to plywood ), as is the case with at least three-ply Bristol board .
Aging resistance
The requirements regarding the resistance to aging of books are set out in the so-called Frankfurt requirements of the German Library and the Society for Books , as well as in the US standard ANSI / NISO Z 39.48–1992 and ISO standard 9706, accelerated aging (simulation: ISO 5630 , DIN 6738).
Today, age-resistant paper should meet the following criteria:
- The natural paper or the base paper must be made from 100% bleached cellulose (without woody fibers),
- have a pH of 7.5 to 9,
- contain a calcium carbonate content of at least 3% as additional protection against harmful environmental influences, calcium carbonate buffer (CaCO 3 buffer),
- have a defined tear resistance lengthways and crossways of 350 mN for papers with a mass per unit area of 70 g / m²,
- have a high resistance to oxidation, expressed in the kappa number .
Lifetime classes have been developed as a guide to the aging resistance of coated and uncoated papers.
- LDK 24 to 85: These papers can be called "non-aging"
- LDK 12 to 80: a service life of several hundred years
- LDK 6 to 70: At least 100 years service life
- LDK 6 to 40: At least 50 years service life
Contrary to standardization, aging-resistant recycled papers are also offered, as research results have shown that ground wood and aging resistance are not mutually exclusive. For example, there are recycled copy papers on the market that meet the requirements of service life class LDK 24 to 85 and also have an alkali reserve in the form of carbonate.
use
Paper is primarily used for writing and printing and, mostly as cardboard or cardboard , for packaging. The share of these two paper groups in paper production in Germany was 38% and 49% respectively in 2015. Hygiene papers follow at a great distance with a share of 6% and technical papers and specialty papers with a share of 6%.
Writing and printing papers
When writing or printing , a dye (for example, ink , toner and printing ink ) is applied to paper with a device. Either by hand with a quill pen , a fountain pen , a pencil , a crayon, a felt-tip pen or a typewriter happened.
Since the invention of the printing press there have been machines that can transfer a text page by page onto paper. With the printing press invented in the 19th century , this is possible a million times over. Different printing processes are used: letterpress , gravure or offset printing . In offices, inkjet printers or laser printers are used for smaller page numbers.
While initially the available raw material only allowed a few different paper properties, paper can now be largely adapted to the various requirements: coated picture printing paper for art prints , newspaper printing as cheap, tear-resistant paper and wood-free uncoated paper as copier paper .
Packaging papers
Cardboard is mainly used as cardboard . With a plastic coating and possibly an aluminum foil as an intermediate layer, it can even pack liquids as a beverage carton. The most common cardboard is corrugated cardboard, which comes in a wide variety of types. Cardboard and cardboard boxes are mainly made from recycled paper. The paper with the greatest relative tensile strength is called Kraft paper . It consists of almost 100% long-fiber cellulose fibers from coniferous woods. It is especially used for paper sacks.
Sanitary papers
Hygiene papers are fine-pored and absorbent papers that are produced on special paper machines with a single drying or crepe cylinder with a diameter of 4-5 meters. Typical products are single-use toilet paper , paper handkerchiefs , kitchen rolls and paper napkins . These papers can be made from cellulose or from recycled paper.
Technical and special papers
This diverse group of papers includes filter papers (e.g. air filters for vehicles and vacuum cleaners), cable insulation papers, medical papers, cigarette papers and thermal papers . Papers can also be found in metal paper capacitors and electrolytic capacitors , where they serve as an insulator or carrier for the liquid electrolyte .
Visual arts
Paper mache is a mixture of paper, binder, and chalk or clay that was used as a substitute for stucco in interior decoration in the 18th century . There was a factory in which ceiling decorations, busts and even statues that could be set up outdoors for a few months were made from old files for Ludwigslust Palace . Paper can be found in model making , in the Japanese art of origami folding paper, and in collages and assemblages .
As a German contemporary artist, Jutta Barth is recognized with her collages and assemblages. She works object-like with the material paper and makes drawings on handmade recycled paper .
Watercolor paper for watercolors has a weight per unit area of up to 850 g / m². Photo paper must be specially coated so that it is suitable as a carrier for the photo emulsion or for use in inkjet printers .
Luxury papers

This is the name for refined, decorated and decorated, often elaborately processed paper products that were manufactured from around 1820/1860 to 1920/1930, when there was a separate luxury paper industry. A number of processing methods were used for refinement, such as coloring as hand and stencil coloring, color printing as chromolithography, gold and silver printing , embossing ( embossing ) and punching , the application of foreign materials such as mica, silk and the attachment of flaps, flaps and Mechanisms in toys. Luxury paper includes devotional and industrious pictures , lots of view ( leporello ), occasional (congratulatory, Christmas and New Year cards) and picture postcards (motif cards), decorated letterheads , labels , all kinds of paper toys ( paper theater ), advertising stamps and photo cards and much more. Such luxury papers are collectibles.
In Japan and China , paper is used in a variety of ways in interior design, for example the Japanese Shōji , room dividers covered with translucent Washi paper.
Flying with paper
There have been kites made of paper in China since this material has existed. The 1783 built Montgolfière the Montgolfier brothers was a hot air balloon from canvas , which was covered with a thin airtight paper layer. During the Second World War , Japan produced around 10,000 balloon bombs made of paper that were made gas-tight with lacquer and transported incendiary devices and explosives (5 to 15 kilograms) across the Pacific to America.
In aircraft model construction , paper is used as a covering (tensioning paper ) for wings in spar- rib construction and for aircraft fuselages. To do this, it is glued on, soaked with tension varnish and painted over as soon as the necessary surface tension has been achieved through drying.
Furthermore, paper is used to make paper airplanes . To do this, the paper is folded into a shape similar to an airplane.
textiles
Paper can be processed into textiles, on the one hand directly from paper, on the other hand it can be cut into strips, spun and woven into textiles. The "paper dress" that came onto the market in the 1970s was, however, specially manufactured nonwovens that were cheaper than clothing fabrics.
Environmental aspects and recycling

Per capita consumption in Germany and some other industrialized countries is five times higher than the global average. If the wood required to cover German paper consumption were to grow in Germany itself, a third of the land area would have to be planted exclusively with trees for paper production, i.e. the entire area of Bavaria and Baden-Württemberg. Germany is the world's second largest importer of pulp . Primeval forests in Canada, Siberia and even rainforests in Indonesia are therefore still being felled as raw material.
When it comes to paper production, the consumption of wood, water and energy is the main topic of environmental policy discussion. Around 20% of the wood felled worldwide is processed into paper. In Germany, however, so-called residual forest wood , storm wood or industrial waste wood are mainly used. Controversial points of view can be found above all on the subject of sustainable forest management, forest certification and the use of primeval forest . The difficulty of pinpointing the source of paper was declared a neglected news item by the News Enlightenment Initiative in 2015 .
The high water consumption was already problematic before 1900, which necessitated the multiple use of water in order to reduce consumption. In the first paper mills, 1200 liters per kilogram of paper were required, around 1900 it was 100 to 800 liters; better methods have reduced this value to 7 liters. A complete closing of the circuit is usually not possible. Because of the hardness of the water , machine parts clog when calcium carbonate builds up. Only in individual cases, if only waste paper is used, the complete waste water return is currently possible.
The water consumption causes the wastewater. With industrialization at the end of the 19th century and the increasing demand for pulp and chlorine bleach, the amount of wastewater and thus the pollutants it contained increased. The hemicelluloses and the lignin (over 50% of the wood) were initially disposed of in the waters almost untreated. Due to the damage to the environment and health and the loss of cooking chemicals with the waste liquor, the liquors were initially used to generate energy. Modern pulp mills are energy self-sufficient, the cooking chemicals are recovered from the exhaust gas and ash.
German environmental regulations are among the strictest in the world. Wastewater from pulp mills may contain up to 25 kilograms of COD ( chemical oxygen demand ) per ton of pulp; in paper production, two to five kilograms of COD per ton of paper are permitted. Because of this, no pulp at all was produced in Germany for a long time. All the demand was imported from countries with lower environmental protection requirements. Only since 1999 has there been production again in the Thuringian Forest , which covers almost 5% of German demand.
Most paper mills operate their own sewage treatment plants , which clean the water used in up to three stages (mechanical, biological, chemical) and only then discharge it into the receiving water. Other paper mills are indirect dischargers that have their wastewater treated together with municipal wastewater.
The energy consumption for production is around 2.7 kWh per kilogram of paper.
Papers with self-adhesive properties such as post-it notes, self-adhesive envelopes and mailing bags make recycling more difficult. Polymer adhesives have to be replaced in the paper mill because they can lead to the paper web tearing off and contaminate the paper. The pre-sorting or subsequent separation of adhesives and plastics from the paper pulp makes the production process more expensive.
Beverage packaging such as tetrapaks and paper cups, which generally contain more plastic (and aluminum foil) than paper, are disposed of as packaging waste via the dual system . Parcels and mailers should ideally be freed of adhesive strips, stickers and other foils before they are disposed of with the paper waste.
Paper research
Reasons for researching paper arise from very different scientific approaches. In addition to technical issues in the paper industry, these are also complex issues in historical library and archive holdings. This includes, for example, the places of origin of historical papers including their watermarks as well as the aging behavior from a conservation and restoration point of view. Numerous academic libraries and some private institutions are active in this field worldwide.
Industrial paper research in Germany is bundled in the Paper Technology Foundation (PTS), which was founded in 1951 and is funded by companies in the paper industry. Contract research and services are provided for the paper industry and its suppliers. In addition, various suppliers operate their own research facilities.
The technical universities in Darmstadt and Dresden , the Munich University of Applied Sciences and the Baden-Württemberg Cooperative State University in Karlsruhe train paper engineers . The main research areas in Darmstadt are recycling processes and water cycles; research in Dresden focuses primarily on energy efficiency and surface properties.
Another research facility is operated by the largest manufacturer of chemical products for paper production, BASF in Ludwigshafen, partly in partnership with Omya .
literature
Books
- Josep Asunción: The paper craft. Verlag Paul Haupt, Bern / Stuttgart / Vienna 2003, ISBN 978-3-258-06495-6 .
- Jürgen Blechschmidt (Ed. :): Paper processing technology. 2nd edition, Fachbuchverlag, 2013, ISBN 978-3-446-43802-6 .
- Paul Ludger Göbel: Paper as a material in the fine arts. An inventory of modernity and the creative possibilities for art lessons. Dissertation, University of Potsdam 2007 ( full text ).
- Wolfgang Walenski: The paper book. Verlag Beruf + Schule, Itzehoe 1999, ISBN 3-88013-584-3 .
History of paper
- Klaus B. Bartels: Paper manufacture in Germany. From the foundation of the first paper mills in Berlin and Brandenburg until today. be.bra Wissenschaft verlag, Berlin 2011, ISBN 978-3-937233-82-6 .
- Lothar Müller : White Magic. The era of paper. Hanser, Munich 2012, ISBN 978-3-446-23911-1 .
- Érik Orsenna : On the trail of paper: a declaration of love. C. H. Beck, Munich, 2014. ISBN 3-406-66093-2 .
- Armin Renker : The book on paper. Berlin 1929, 4th edition 1951, OCLC 3399822 .
- Wilhelm Sandermann: Paper, a cultural history. 3rd edition Springer, Berlin / Heidelberg 1997 (first 1988), ISBN 3-540-55313-4 .
- Heinz Schmidt-Bachem : Made of paper. A cultural and economic history of the paper processing industry in Germany . De Gruyter, Berlin 2011, ISBN 978-3-11-023607-1 .
- Lore Sporhan-Krempel : Ox head and double tower - the history of papermaking in Ravensburg. Stuttgart 1952.
- Peter F. Tschudin: Fundamentals of the history of paper. Stuttgart 2007, ISBN 978-3-7772-0208-2 .
- Therese Weber: The language of paper. A 2000 year history. Verlag Haupt, Bern / Stuttgart / Vienna 2004, ISBN 3-258-06793-7 .
- Wisso Weiß: Timeline of the history of paper. Fachbuchverlag, Leipzig 1983, OCLC 11783685 .
Magazines
Essays
- Andreas Pingel Keuth: Paper manufacture: From cellulose to filter bags, writing paper, ... In: Chemistry in our time . 39, 6, Wiley-VCH, Weinheim 2005, pp. 403-409. doi: 10.1002 / ciuz.200500234 .
- Klaus Roth : Paper conservation - chemistry versus paper disintegration. In: Chemistry in Our Time. 40, 1, Wiley-VCH, Weinheim 2006, pp. 54-62. doi: 10.1002 / ciuz.200600376 .
History of paper
- Günter Bayerl : Pre-industrial trade and environmental pollution - the example of hand paper-making. In: History of Technology. 48, VDI-Verlag, Düsseldorf 1981, ISSN 0082-2361 , pp. 206-238.
- Robert I. Burns: Paper Comes to the West, 800-1400. In: Uta Lindgren: European technology in the Middle Ages: 800 to 1400; Tradition and innovation. Gebr. Mann, Berlin 1996, ISBN 3-7861-1748-9 , pp. 413-422.
- Michael Reiter: 600 years of paper in Germany. In: Karl H. Pressler (Ed.): From the Antiquariat. Volume 8, 1990 (= Börsenblatt für den Deutschen Buchhandel - Frankfurter Ausgabe. No. 70, August 31, 1990), pp. A 340 - A 344.
- Alfred Schulte: paper press, printing press and wine press. In: Gutenberg yearbook . 1939, pp. 52-56.
- Wolfgang von Stromer : Great innovations in paper manufacture in the late Middle Ages and early modern times. In: History of Technology. Vol. 60, No. 1, 1993, pp. 1-6.
- Susan Thompson: Paper Manufacturing and Early Books. In: Annals of the New York Academy of Sciences . Vol. 314, 1978, pp. 67-176.
- Viktor Thiel: Paper production and paper trade mainly in Germany from the earliest times to the beginning of the 19th century. A draft, In: Archivalische Zeitschrift . Volume 41 (= Archivalische Zeitung 8, 3rd episode), Böhlau, Cologne 1932, pp. 106–151.
- Peter F. Tschudin: Tools and handicraft technology in medieval paper production. In: Uta Lindgren : European technology in the Middle Ages. 800 to 1400. Tradition and innovation. 4th edition, Gebr. Mann, Berlin 1996, ISBN 3-7861-1748-9 , pp. 423-428.
Norms
- German Institute for Standardization V. (Ed.): DIN 6730: 2006-05: Paper and cardboard - terms. Beuth Verlag, Berlin 2006.
- International Organization for Standardization (ISO) (Ed.): ISO 536: 1995: Paper and board - Determination of grammage. Geneva 1995.
Web links
- Paper school Animated learning portal of the Association of German Paper Mills on the subject of paper
- Paper goes to school Information portal about paper and cardboard
- Paper Encyclopedia of Igepa
- Materials for printing and packaging: glossary, terms, standards kba.com
Paper history
- Martin Börnchen: Handmade paper and what else you wrote on (PDF; 38.4 MB), Freie Universität, Berlin 2002, ISBN 3-929619-29-6 .
- Dieter Freyer: A little paper story - from papyrus to paper of the 20th century
- International Association of Paper Historians (IPH)
- Peter Tschudin: Paper. In: Historical Lexicon of Switzerland .
Industry associations
- Association of German Paper Mills (VDP)
- Main Association for Paper and Plastics Processing (hpv)
- Austropapier - Association of the Austrian Paper Industry
- Confederation of European Paper Industries
Individual evidence
- ↑ DIN 6730: 2017-09 Paper, cardboard and pulp - terms, p. 45.
- ↑ Jürgen Blechschmidt (Ed.): Taschenbuch der Papiertechnik , Fachbuchverlag Leipzig in Carl Hanser Verlag, 2nd, updated edition 2013, p. 37.
- ↑ Jürgen Blechschmidt (Ed.): Taschenbuch der Papiertechnik , Fachbuchverlag Leipzig in Carl Hanser Verlag, 2nd, updated edition 2013, p. 30 f.
- ↑ Erwin Bachmaier ( bvdm ): Materials and auxiliary materials: paper, cardboard, cardboard (PDF), p. 1 f.
- ↑ Solid board harzerkartonagen.de
- ↑ basis weight papyrus.com
- ↑ Use of paper wellpappe-wissen.de
- ^ Dard Hunter: Papermaking: The History and Technique of an Ancient Craft. 2nd Edition, Dover Publication, 1978, ISBN 0-486-23619-6 (Reprint), p. 5.
- ^ Rudolf Frankenberger, Klaus Haller (Ed.): The modern library. De Gruyter, 2004, ISBN 978-3-598-11447-2 , p. 11.
- ↑ a b Jialu Fan, Qi Han, Zhaochun Wang and Nianzu Dai: The Four Great Inventions. In: Yongxiang Lu: A History of Chinese Science and Technology. Volume 2, Springer, 2015, ISBN 978-3-662-44165-7 , pp. 161-238, online (PDF; 5.9 MB), at springer.com, accessed on July 26, 2017.
- ↑ Mukhtar Ahmed: Ancient Pakistan - An Archaeological History. Volume IV, Foursome Group, 2014, ISBN 978-1-4960-8208-4 , p. 316.
- ↑ Omar Faruk, Mohini Sain: Biofiber Reinforcements in Composite Materials. Woodhead, 2015, ISBN 978-1-78242-122-1 , p. 273.
- ^ The Construction of the Codex In Classic- and Postclassic-Period Maya Civilization. Maya Codex and Paper Making.
- ↑ In his dictionary Shuowen Jiezi (after Gerhard Pommeranz-Liedtke: The wisdom of art. Chinese stone rubs. Leipzig 1963, p. 6.)
- ↑ Dieter Pothmann: Impressions from the IPH China expedition.
- ^ Dagmar Lorenz: Paper and writing culture. Fourth episode in the series: Chinoiseries, February 12, 1999, on SWR2. (No longer available online.) Archived from the original on March 13, 2007 ; accessed on January 21, 2017 .
- ↑ Hyejung Yum: Traditional Korean Paper Making . In: Scientific Research on the Pictorial Art of Asia . Archetype Publication Ltd. , London 2005, ISBN 1-873132-74-3 , pp. 75-80 (English).
- ^ Joseph Needham : Science and Civilization in China: Volume 5 Chemistry and chemical technology. Cambridge University Press, 1985, ISBN 0-521-08690-6 , pp. 73 f.
- ^ Rudolf G. Wagner: Joining the Global Public: State University of New York Press, 2007, ISBN 978-0-7914-7118-0 , p. 30.
- ↑ Alexander Monro: Paper: How a Chinese Invention Revolutionized the World. Bertelsmann, 2015, ISBN 978-3-570-10010-3 .
- ↑ Jeremiah P. Losty: The Art of the Book in India. The British Library, London 1982, ISBN 978-0-904654-78-3 , pp. 5-12.
- ↑ Thompson 1978, p. 169; Burns 1996, p. 414 f.
- ↑ Burns 1996, p. 417 f.
- ^ A b Peter F. Tschudin: Tools and handicraft technology in medieval paper production. In: Uta Lindgren: European technology in the Middle Ages. 800 to 1400. Tradition and innovation. 4th edition. Berlin 1996, pp. 423-428, here: p. 424.
- ↑ Schulte 1939, pp. 52–56.
- ^ A b Peter F. Tschudin: Tools and handicraft technology in medieval paper production. In: Uta Lindgren: European technology in the Middle Ages. 800 to 1400. Tradition and innovation. 4th edition, Berlin 1996, pp. 423-428, here: pp. 424 f.
- ^ Peter F. Tschudin: Tools and craft technology in medieval paper production. In: Uta Lindgren: European technology in the Middle Ages. 800 to 1400. Tradition and innovation. 4th edition, Berlin 1996, pp. 423-428, here: pp. 424-426.
- ↑ Stromer 1993, p. 14 f.
- ^ Michael Reiter: 600 years of paper in Germany. Frankfurt am Main 1990 (= Börsenblatt für den Deutschen Buchhandel 70, 1990, supplement: Aus dem Antiquariat , 8, ISBN 0-00-343186-X , pp. A340-A344).
- ^ Richard Leslie Hills: Papermaking in Britain 1488-1988: A Short History. Bloomsbury Publishing, 2015, ISBN 978-1-4742-4127-4 (Reprint), p. 2.
- ↑ Filipe Duarte Santos: Humans on Earth: From Origins to Possible Futures. Springer, 2012, ISBN 978-3-642-05359-7 , p. 116.
- ↑ AT-HHStA> SbgE> AUR 1228 IV 18 : "18. April 1228, Barletta: Emperor Friedrich II orders the Archbishop of Salzburg and the Duke of Austria Leopold VI. according to the complaint of the abbess of the monastery Göß, over which the emperor is entitled to the bailiwick, to interrogate and decide her dispute with Duke Bernhard over the heirless estate of the monastery ministries in the latter country. "
- ↑ Schulte 1939, pp. 52–56
- ^ Fritz Funke: Book customer. 6th edition, Saur, 1999, ISBN 3-598-11390-0 , p. 58.
- ↑ Short biography of Wilhelm Rettinghaus on the city of Mülheim's internet portal.
- ^ Peter Eitel: Ravensburg - an early center of papermaking. In: J. Franzke, W. v. Stromer (Ed.): The magic substance paper - six centuries of paper in Germany. Munich 1990, pp. 46-52. See Michael Reiter: 600 Years of Paper in Germany. In: Karl H. Pressler (Ed.): From the Antiquariat. Volume 8, 1990 (= Börsenblatt für den Deutschen Buchhandel - Frankfurter Ausgabe. No. 70, August 31, 1990), pp. A 340 - A 344, here (for an exhibition from mid-May to mid-August): p. A 340 - A 324: “The magic of paper” in Stein near Nuremberg .
- ^ Eugène Arnaut (1826–1905): Histoire des protestants du Dauphiné aux XVIe, XVIIe et XVIIIe siècles. Grassart, Paris 1876, p. 23, archive.org .
- ^ A b Joachim Lehrmann : The early history of the book trade and publishing in the old university town of Helmstedt and the history of the once important paper mills at Räbke am Elm and Salzdahlum / Helmstedter and Räbker book and paper history . Ed .: Joachim Lehrmann. Lehrte 1994, ISBN 978-3-9803642-0-1 , pp. 282-285 .
- ↑ Eberhard Tacke: The invention of a "new kind of paper made from wood material" by Joh. Georg v. Langen around 1760 . In: IPH-Info . tape 11 , no. 2 , 1977, DNB 1036038408 , p. 41 .
- ↑ Manfred Anders, Peter Bartsch, Karl Bredereck, Anna Haberditzl: For the chemical strengthening of paper in connection with paper deacidification . In: IADA Preprints 1995 , pp. 81–85 (PDF; 4.4 MB)
- ↑ Kurt Hess: The chemistry of cellulose and its companions. Akademische Verlagsgesellschaft, Leipzig 1928, OCLC 609584207 , pp. 139-165.
- ^ Max Zieger: Paper Science. Leipzig (Fachbuchverlag) 1952, OCLC 7686101 , pp. 18-27.
- ↑ Günter Engelhardt, Klaus Granich, Klaus Ritter: The sizing of paper. Fachbuchverlag, Leipzig 1972, pp. 12-14, DNB 730155331 .
- ↑ Otto Wurz: Paper manufacture based on modern knowledge. Graz u. a. 1951, OCLC 71100773 , pp. 46-65.
- ↑ L. Âkesson (ed.), H. Everling and M. Flückiger: Lexicon of the paper industry. 2nd edition, Techn. Bureau Zürich, 1905, p. 586, archive.org .
- ^ Johann Zeman: Zeman, Notes from the Vienna World Exhibition. In: Polytechnisches Journal . 214, 1874, pp. 1-8.
- ↑ “Magic” Reusable Paper Uses UV Light in Place of Ink. Accessed June 8, 2020 (English).
- ↑ The first book made from apple paper. Penguin Random House , October 13, 2015, accessed January 12, 2018 .
- ↑ Oliver Recklies: Sustainability continues - notebooks made of apple paper. September 6, 2016, accessed January 12, 2018 .
- ↑ J. Herer, M. Bröckers: The rediscovery of the useful plant cannabis marihuana hemp . German Orig.-edition, 41st edition Nachtschatten-Verl, Solothurn 2008, ISBN 978-3-03788-181-1 .
- ↑ a b c d e f g Decision of the European Commission in Case No. COMP / M.3796 - OMYA / HUBER PCC (PDF; 777 kB), on ec.europa.eu.
- ↑ The information on the properties is based on: Paper: Properties and Use , Slides for the lecture “Introduction to Printing and Media Technology” at the Institute for Printing Machines and Printing Processes (IDD) of the TU Darmstadt, pp. 2–6.
- ↑ See felt page and screen page in the paper lexicon , gmund.com.
- ↑ DIN 6730: 2017-09 Paper, cardboard and fibrous material - terms, p. 14
- ↑ DIN 6730: 2017-09 Paper, cardboard and fibrous material - terms, p. 51
- ↑ A. Haberditzl: How do I recognize aging-resistant paper? A replica. In: The archivist. Volume 58, Issue 4, (November 2005), p. 327, online (PDF; 866 kB).
- ↑ Ursula Rautenberg (Hrsg.): Reclams Sachlexikon des Buch: From manuscripts to e-books. 3rd edition, Reclam, 2015, ISBN 978-3-15-011022-5 .
- ^ Rainer Hofmann, Hans-Jörg Wiesner: Preservation in archives and libraries. 5th edition, Beuth, 2015, ISBN 978-3-410-25411-9 .
- ↑ my way of working. at j-barth-berlin.de.
- ↑ Elke Gottschalk: paper antiquities. Luxury papers from 1820 to 1920. Battenberg Verlag, Augsburg 1996, ISBN 3-89441-216-X .
- ↑ The future belongs to certified paper. Brochure, WWF Germany , May 2008.
- ↑ 2015: Top 5 - White paper, dirty business. Intelligence initiative , accessed on October 23, 2019 (German).
- ↑ BMU : Wastewater Ordinance. ( Memento of January 13, 2009 in the Internet Archive ) Appendices 19 and 28.
- ^ High energy costs slow down the paper industry, WirtschaftsWoche, March 11, 2006.
- ↑ Berliner Stadtreinigungsbetriebe (ed.): Waste avoidance in the office (PDF), 2002, p. 6 ff.