metallurgy
Metallurgy (synonymous with metallurgy ) describes the totality of the processes for the extraction and processing of metals and other metallurgically useful elements.
The word metallurgy is made up of the ancient Greek μέταλλον métallon for a mining site and ourgos for those who do an activity. Accordingly, a metallurgist works in mining sites and with their contents. The Latin word metallum is conceptually narrow, it just means metal .
history
Ore deposits establish metallurgical works
Copper, bronze and iron tools, after which historical epochs are named, owe their origin to knowledge that was gained by chance or intentionally, initially only through outcrops (exposed ore veins). The Copper Age with the conspicuous cuprite is exemplary . After the discovery of tin-containing ores ( cassiterite ), the Bronze Age developed from the Copper Age , followed by the Iron Age . All epochs are evidence of targeted metallurgical work. On the basis of this, it is still a long way until the operation of the first blast furnace made the “tapped” pig iron available in quantities for iron casting and, from the 18th century, for steel production. The steel age and the earth metal age that joined it in the 20th century determine many people's living conditions today.
The traditional German deposits have been considered exploited since the end of the 20th century from the point of view of a calculation that takes into account marginal costs - i.e. prime costs at which the yield was just marketable without loss. This concerns the Goslar Rammelsberg , which is rich in zinc ore , the Hessian-Siegerland iron ore and uranium mining in the Saxon Ore Mountains, where uranium ore was mined to a less environmentally friendly extent until 1990. The mining of silver in the German and Slovakian Ore Mountains , which has been practiced for centuries, has so far been considered no longer worthwhile . The same applies to other European ore deposits, of which the “Tauern gold” in the Austrian Rauriser Valley is also worth mentioning because its mining was facilitated and then hindered by proven, long-term temperature changes.
From 2010 onwards, it was not only the sharp rise in the listed silver price that led to considerations of prospecting in the Ore Mountains on the basis of new knowledge about the mining quality and mining technology of silver ores and other valuable mineral resources. Mining permits were sought, the granting of which became known in 2011.
The steadily growing population of the world and industrialization, especially in Asia, have caused a rapidly growing demand for raw materials for metallurgical products since the beginning of the 21st century, not least due to new technical developments (transport, communication electronics). Therefore, new deposits are being explored worldwide with increasing Chinese participation. The auxiliary science of this activity, also known as exploration, is geology, more precisely also called geometallurgy. The development of raw material prices, driven by increased demand, means that some of the aforementioned mining areas, if they are not completely exhausted, cause a shift in marginal costs if demand continues or even increases and can thus be reactivated. Even previously unrecognized deposits, for example in central German Lausitz, are being considered for future exploitation. In particular, the search for deposits of rare earth metals, which are extremely important for future technical developments, is lively. In the Erzgebirge not only are new mines for fluorspar and barite opened, reference is also made to the existence of as yet undeveloped polymetallic deposits for lithium , germanium , indium as well as tungsten , molybdenum and tantalum .
Metallurgy has grown into a technology based on old experiences and constantly renewing knowledge . As early as the 19th century, a distinction was made between ferrous and non-ferrous metallurgy. The state of the art not only safeguards these two main and secondary disciplines for their own research. It is supported by other disciplines that accompany the entire process from raw materials to ready-to-use goods, including metal science , closely linked to materials science , chemistry and furnace , machine and plant engineering .
Timetable
The following chronological table tries to show the development of metallurgy from the Neolithic to the beginning of the modern age . The times given for cultural changes are not always the same for Europe, Asia and Africa. The end of the Mesolithic (approx. 5500 BC) and the beginning of the Neolithic (from 8000, according to other data from 5500 to 2000 BC) overlap. With the ceramic cultures already encountered (cord and ribbon ceramics, bell beakers as grave goods filled with metallic jewelry), the more recent dating extends far back to around 5000 BC. The beginning of the early Bronze Age, also known as the Copper Age and, in the early phase, the Copper Age, was dated backwards.
around 8000 BC Chr. | slow transition to the Neolithic | settled settlement from 7750 BC Proven, agriculture, metal jewelry, first knowledge in metal extraction and processing |
around 4000 BC Chr. | early Copper Age, also Copper Age | Metal mirrors in Knossos, hatchets made of copper, grave goods in the form of copper daggers and gold jewelry, first objects made of iron |
from 2700 BC Chr. | Early bronze age | Advance of bronze from the Caucasus into the Mediterranean region (Cycladic culture) and into Egypt , in Europe the Nebra sky disc is the most important find of the Early Bronze Age |
1700 - 800 v. Chr. | Bronze age | Bronze chariots and weapons, swords, monuments, jewelry (bronze brooches), coins, tools ( axes ), construction (brackets as connectors for marble parts) |
from 1100 BC Chr. | Immigration from the north brings technical progress - not without controversy in terms of type and timing. Doric equestrian warriors, already with iron weapons (from 1200 already with the Hittites), are said to have prevailed against bronze swords and chariots. | |
from 800 BC Chr. | Early Iron Age | Hallstatt culture , dissemination of iron objects in Central Europe |
from 600 BC Chr. | Beginning of the Iron Age in China | |
around 500 BC Chr. | Zenith Hellenic - Roman antiquity | |
from 450 BC Chr. | Younger Iron Age, La Tène culture | advanced use of iron |
Turning point | Roman smelting plants are built in areas close to ore, Siegerland | |
200 AD | Late antiquity | Fabricae ( manufactories ) appear alongside handicrafts in metal processing |
400 - 600 / . 700 AD. | Time of the Germanic Migration Period, end of late antiquity | Further development in the use of iron among the Merovingians and Vikings (weapons, technical equipment), bronze for coins, small portraits, reliefs, monuments |
around 1160 | Beginning of the settlement of the Bohemian-Saxon Ore Mountains | initially only targeted mining of lead ores containing silver for silver extraction ("driving work") |
after 1300 | 1318 first documentary mention of Muldenhütten near Freiberg / Erzgebirge as a "hut location" | The first "high shaft furnaces " are taking the place of previous "low shaft furnaces ", see blast furnace |
after 1400 | increasing early industrial iron extraction and processing. | |
after 1500 | Beginning of the development leading to the present day. | with Georgius Agricola (XII Libri) technical aids for ore extraction and processing take the place of mere manual labor; The first Joachimsthalers were minted from Bohemian silver mining in 1519 |
From the copper ax to the Bronze Age

The history of the development of metallurgy began a little more than 8000 years ago in the end of the Mesolithic and in the transition to the Neolithic (see the table above). More recent research in Asia Minor has even discovered the first metallurgical approaches in early settlements around 12,000 years old. They confirm the view that early metallurgy was decisively determined by the conversion of nomadic hunters and gatherers to arable farmers and settlers with “fixed stoves” instead of changing, open fireplaces. Perhaps at the beginning of metallurgical discoveries there is a chance find, be it of solid (pure) metal such as the shiny river gold from mountain waters, or a metal-rich ore ( red copper ore ) that aroused interest because of its color. It is conceivable that in a fire pit by natural cover with ashes when burning down, charcoal, which consists of 80% carbon, could be produced. If a fire that has become flameless, i.e. apparently dull, after burning the volatile components is refreshed by supplying air (blowing), 1000 ° C and more are reached when the charcoal is burned. Then copper is exuded from red copper ore, from tin gravel, a copper-tin-iron-sulfur ore, a natural alloy of copper and tin. This could have sparked metallurgical considerations. Pictorial representations show the use of blowguns for this technology. The supplied oxygen from the air oxidizes the sulfur content in the ore, as does the carbon, which is a hindrance for the forging processing of iron, if this content in the iron exceeds two percent. Sulfur becomes volatile, because it occurs in gaseous form, sulfur dioxide (SO 2 ), and carbon becomes carbon dioxide (CO 2 ), with additional heat of reaction being generated.
The first purpose-built smelting furnaces have been identified as early as the early Copper Age (4500–3500 BC); research from the 21st century suggests that they (copper axes) were in the area of today's Serbia. Key finds of metallurgical activity are from 3000 BC. The (ceramic) bell beakers as a uniform feature of different cultures in burials ( bell beaker culture ). In addition to the bell-shaped beakers from which they are named, the graves contain various grave goods, including shields and daggers made of copper, as well as gold and ivory. The early was followed by a late Copper Age, which, however, started from 3000-2500 BC. BC already passed into the early Bronze Age. In very long periods of time and in partly overlapping cultures, but with a clear reference to local and regional ore deposits ( Bohemian Ore Mountains), centers of metallurgical development emerged over time, which were linked by trade routes and shipping routes. This happened in Central Europe, in the Aegean ( Uluburun shipwreck ), in southern Spain, in England, in the Carpathian space and on the Balkans . This circle flowed around 3000 BC. BC, at the beginning of the Early Bronze Age, knowledge from the Caucasus and Anatolia, which also reached Greece (beginning of the Early Helladic ), Crete and Egypt and found its way into the already pronounced high cultures for works of art as well as in the everyday world. Representations of the ancient Egyptian metal extraction from the XVIII. Dynasty (middle of the 15th century BC) were about in the grave of the vizier Rechmire . According to the figures, the necessary temperature was achieved by means of bellows attached to the feet. For the Mediterranean area , copper, Greek chalkos ( Chalkidike ), called aes cyprium ("ore from Cyprus ") by the Romans , with rich deposits formed the basis for a now comprehensive metallurgical advancement, which not only made small parts and weapons into trade articles of the Phoenicians , but also produced large bronzes. The Colossus of Rhodes was even then considered one of the wonders of the world. The processing of gold as a store of value was already recognized by Pharaoh Menes from the first dynasty of the old empire, he had small gold bars stamped with a kind of guarantee. Knowledge of smelting and working gold can be traced back to 3000 BC. And are also close because of the almost identical melting points of gold (1063 ° C) and copper (1083 ° C). Driven and cast everyday objects and pieces of jewelry made of gold and silver (melting point 960.5 ° C), as well as numerous parts made of pure copper, were found by Heinrich Schliemann in 1873 during his search for the Homeric Troy and mistakenly called the "treasure of Priam" by a much younger one Associated with culture.
The Scythians , an equestrian people without writing or coinage, in so far not yet a high culture , were already very skillful in making gold jewelry, as the tombs of princes ( Kurgane ) show. The Celts also used gold for jewelry and regalia . Around 600 BC gold was used as a means of controllable store of value for the subjects. BC struck into coins by King Croesus of Lydia (" gold stater "). It also became a means of payment . The Egyptian Ptolemies mined gold in mines leading to gold ore in pre-Christian times , the Romans exploited the Spanish silver ore deposits to produce coins, statues, vessels and other proofs of wealth.
Middle East, India, China, Southeast Asia, Japan
In the Near East there are bronzes, for example that of a king's head, from the time of the Akkadian Empire ( Mesopotamia ) around 2300 BC. BC Although the knowledge was available, the subsequent empires preferred to depict their rulers again in stone or alabaster . In the 2nd and 3rd millennium BC The metals that could be produced were limited to gold, silver, copper, tin and lead, although other metals were found in the artefacts that had been alloyed with the main metals during smelting from ores. In the case of bronzes, two alloys were produced and processed, arsenic bronze and tin bronze . Iron was initially a by-product of the smelting of copper, but was then used from the 1st millennium BC onwards. More and more meaningful.
In parts of the Indian subcontinent, towards the end of the 4th millennium BC, The use of copper and bronze can be proven at the same time as the development of “urban life” ( Indus cultures ). Southeast Asia has known copper and bronze since around 3000 BC. Chr.
From China this only becomes apparent around 1600 BC. Chr. Reported. Easily machinable alloys (with lowered melting points ) such as gold-colored brass are invented. The influence of the 1700 to 1100 BC in this area is documented. Ruling Shang dynasty . The bronze drums ( Dong-Son culture ) are traced back to them, which dates from around 1000 BC. Are numerous in the southern provinces. From the 7th century BC A bronze bell was made for the princes (kings) of Qin. As a result, bronze was used for quite different purposes. From the 3rd century BC During the relatively short-lived Qin Empire, joist cladding for house building, coins and of course weapons were found. In any case, in the kingdom of the princes (kings) of Qin, bronze is no longer used only for cult objects, but in a variety of ways.
Culturally, Japan is first of all under the influence of China and the Mongolian-shamanistic and Shinto cults that are widespread there . Buddhism gained a foothold around 500 AD. The figure of the Daibutsu of Nara, cast from a low-tin bronze, is said to weigh 380 tons. Bronze mirrors from the period between 3000 and 710 BC are evidence of earlier metallurgical activity. But also the Yayoi period from 350 BC. BC is also visible from mirrors, bells and weapons.
Overall, the Asian region with its metallurgical knowledge is not behind the European one, although only since 600 BC. Is spoken of a beginning Iron Age. Caravan routes such as the Silk Road , and perhaps even more so trade by sea, are increasingly promoting the exchange of knowledge and the products that have arisen from such. This includes a 200 BC In Europe still unknown, shiny white copper alloy, which is called " Packfong " in China .
From the early Bronze Age to the beginning of the Early Iron Age
Because of the Greek word chalkos (χαλκὀς), which does not differentiate between copper and bronze , the early Bronze Age is also called the Late Copper Age. The knowledge gained from experience of a targeted improvement of the properties of copper objects by adding tin and zinc to the alloy was established relatively quickly by today's standards. Brass as a copper-zinc alloy is either of Chinese or Persian - Indian origin.
Figurative finds prove the almost simultaneous development of lead . The widespread galena was initially only sought as a silver carrier, and the lead produced during its extraction was considered waste. Once recognized, its low melting point of only 327 ° C encouraged considerations that led to a wide range of uses. Very early figurative objects are known ( Hallstatt finds ), followed by objects of daily use - (Roman times with vessels, tubes, plates). Lead casting achieved a late bloom in monuments of the Baroque period , whereby the toxicity of the lead vapors occurring during melting was not considered for a long time.
Another “historic” metal is nickel . As a component of copper-zinc alloys (brass) it was first found around 200 BC. In China. The nickel-containing nickel silver is still the basic type for cutlery alloys today .
Biblical traditions
Biblical traditions are difficult to classify in terms of time, but they go back to very ancient scriptures.
“It will sit and melt and cleanse the silver; he will cleanse and purify the children of Levi like gold and silver. " Malachi 3, verse 3 ( Old Testament ) |
Melting, refining (cleaning the melt of foreign matter) and driving work (for defleading) are professionally described correctly in various places in the Old Testament Bible . Early metallurgists and their pyrometallurgical techniques are described in Tubal-Cain ( Genesis 4:22 EU ) and Malachi . They differ only slightly from today's basics. Jewelry and utensils made of gold, silver and bronze were manufactured. Iron was not unknown, but - according to the findings - was still used very rarely, so that it was even used as a jewelery.
In Jeremiah 6, verses 27-30, a metallurgist becomes the judge of apostates whom he describes as "rejected silver" in a comparison with inadequately chased silver. In the second book of Genesis , 32: 1-4, it is recorded that the "Golden Calf" from eingeschmolzenem jewelery extending from Yahweh averting Israelites said to have been cast.
The long way to the Iron Age
As early as the Middle Bronze Age (in Central Europe from 1200 BC), the gradual displacement of bronze by iron began , the extraction of which became possible - even if by today's standards in a still quite simple way - after one had learned the necessary basic principles. For reductive production of iron from iron ores to significantly higher temperatures than required for the extraction of copper or bronze. With the available fuel and reducing agent charcoal, this required a special construction of the smelting furnaces with regard to the air supply in order to achieve the necessary temperatures. The iron was only obtained in sintered (not molten) form, as so-called lobes , because the iron's melting temperature of 1538 ° C could not be reached with the available furnaces. In addition, there were still no processing techniques for pig iron that could not be formed using forging. In addition to low-carbon iron, the racing kiln process also produces steel and cast iron in different proportions. While the Celts recognized and processed steel by its properties, cast iron could not be used. Techniques learned later, such as carburizing , hardening and tempering, were able to improve the properties of iron-carbon alloys and thus steel , which gradually replaced copper or bronze.
This became visible in around 700 BC. BC fully developed Hallstatt culture , which is referred to as the early Iron Age. Celts, Slavs , Italians and Illyrians had an equal part in this. From around 450 BC. The Latène period followed as the second stage , an Iron Age epoch that extended to the turn of the century and beyond. Weapons, tools and utensils were made of steel and iron.
From today's point of view, the transition from the Bronze Age to the Iron Age is slow progress, because apart from the time around 5000 BC. Backdated individual finds from Egypt only began in 1600 BC. Chr. ( Hyksos ) repeated incursions of equestrian peoples fighting with iron weapons contributed to the spread of iron. Interesting in this context is the use of the Indo-European word brazen , i.e. of great durability (compare Aera ). North of the Alps it was understood to mean iron, for Italians and Iberians it was bronze.
Iron for weapons came from 660 BC. On trade routes from Asia to North Africa, however, surprisingly, it was not found until 700 years later (100 AD) in southern Africa. The Central American civilizations gave evidence of the use of iron only for the time around 500 AD.
The importance of dominance influences for metallurgical development
The representation of metallurgical development in cultural epochs, which by no means abruptly, but often followed one another with long transition periods, is overlaid by historical periods of rule. The ancient world has made a lasting impression . It begins around 2500 BC. Seen and equated with the early Bronze Age. The influence became clearer with the beginning of the Doric migration, which was disputed in terms of origin and effects, around 1100 BC. During its course, mounted "warriors with iron weapons" coming from the north prevailed against opponents who were still fighting with bronze swords and two-wheeled chariots . But they did not only bring advances in this area (Balkan or "Carpathian technology"). The Cretan- Minoan influence that had prevailed up to then , including places like Mycenae and Tiryns , was finally replaced after many local and regional wars by the Hellenic antiquity ( Magna Graecia ) extending over large parts of the Mediterranean (temple building with the help of bronze brackets and Doric, Ionic and Corinthian capitals ).
Gold and silver were found as solid metals, in particular easily accessible river gold, or as deposits containing silver (gold soaps) and from visibly silver-rich ore veins. As a valuable commodity, gold and silver were not only items of trade but also booty on military campaigns. The regional and supraregional exchange, whether wanted or forced, contributed to the refinement of the craftsmanship handed down from Mycenae and early layers of Troy in the production of ornamental jewelry and cult objects. From 700 BC were of great importance. The first gold or silver coinage. Sparta, as an exception, led around 660 BC. Chr. Iron in ingot form as the "domestic currency".
The Hellenic determined antiquity reached a climax around 500 BC. After that it was dated around 1000 BC. Beginning of the rise of the Etruscans and from 700 BC Determined by that of Rome . It stayed that way for almost a millennium, during which it was considered noble for an upper class to be "Greek" for a long time.
In Roman times, the importance of bronze extended beyond figurative representations (statues) and cult objects. It remained indispensable in the construction industry for joining marble parts (cast or forged bronze brackets), as well as in roofing and in car construction. Iron was still difficult to manufacture because of its very high melting point of 1535 ° C compared to copper, but also to gold and silver. Its use was limited to tools and, above all, weapons until the Merovingian era . Damascus steel was famous at that time , the production of which resulted from the endeavor to turn inhomogeneous racing fire iron into a homogeneous material with predictable properties through frequent folding and fire welding. This forging process, which is called refining when it only uses a base material, was always necessary for cleaning and homogenizing the early iron products, so-called welded composite steel (Damascus steel / welded damask) was created when different alloys were used. It was only in the early Middle Ages (beginning of the Viking Age) that such alloys (additives or different contents of carbon, phosphorus, arsenic, etc.) could be specifically manufactured and processed into a pattern damask (so-called worm-colored blades). This was made visible by etching the metal surface.
The name Damascus steel originally comes from the trading metropolis Damascus, at that time a trading center also for so-called melted or crystallized damask (Wootz), which was made around 300 BC. Came from India and Persia. All so-called Damascus steels have the same properties as their original metals, i.e. are hardened and tempered in this way and do not show any outstanding performance compared to well-processed mono-steel, as it was later brought onto the arms market by the Franks and was widely used. Therefore, the appearance of these high-quality steels initially meant a decline and finally the end of early Damascus steel production.
In the late antiquity , the time was predominantly Germanic barbarian invasions from the 4th to 6th century. BC. Rome was transformed from the time of Emperor Constantine, a Christian kingdom. Not yet completely detached from the bronze culture (monuments), the Western Roman Empire fell in 476, while the Eastern Roman Empire was able to assert itself.
The knowledge of bronze casting was preserved in the religious area, there ( bell casting since 750, church doors made of gunmetal in 1015 in Hildesheim ) and as a symbol of rule ( Brunswick lion from 1166). The invention of gunpowder brought new challenges. "Piece founders" are said to have cast the first cannons from ore - that is, from bronze - in 1372. Foundries were built and again it was the church and the rulers who commissioned tombs and monuments. In addition to the bronze, brass came with the Sebaldus grave in Nuremberg (1519). From 1800 cast iron made of iron became "acceptable" (grave slabs) and in the 19th century large bronzes of modern times, confirming rulers and state, were created again (Bavaria in Munich 1850).
From the medieval blast furnace to blown and electric steel
For a long time, Europe lagged behind China and Egypt in terms of the “industrial” extraction and processing of metals, not just iron. The iron objects found during excavations in Egypt, probably 5000 years old and still well preserved, do not allow any reliable conclusions to be drawn about the type of iron extraction at that time. After all, both old and newer reference works (Meyer, Brockhaus) indicate that as early as 1200 BC. The Philistines (valley dwellers in contrast to the mountain dwelling Israelites ) had knowledge of iron extraction.
Bronze could still be produced in a low- shaft furnace made of clay with a natural draft, but the extraction and processing of iron was easier with the use of a powerful bellows , even if there were self-drawing furnaces in this area. A temperature increase from 1100 ° C, which is sufficient for bronzes, to the more than 1200 ° C required for iron extraction, is only possible with a sufficient supply of atmospheric oxygen. In the early Iron Age, so-called lobes - unformed lumps / sponge iron made of forgeable iron (because it was low in carbon) - were extracted from a mixture of iron-rich ores such as hematite / red iron ore and charcoal and the air supply by means of still very simple bellows (racing freshening) in racing furnaces ( racing fire ) used for weapons , armor and tools. This first step into the Iron Age already produced significant amounts of iron. An improvement in the Middle Ages led to the so-called wolf or piece furnaces , forerunners of today's blast furnace . They delivered liquid pig iron to the bottom (bottom of the furnace) , the "wolf" above it gave off carbon during annealing and freshening and turned into steel or malleable iron.
Although contemporary records of the first high shaft furnaces (blast furnaces in today's parlance) are reported as early as the 14th century and early industrial iron production in the 15th century, one can only speak of an Iron Age, rightly so called in the technical sense, when it was towards the end of the 16th century. In the 19th century, it was possible for the first time to achieve permanent temperatures of more than 1400 ° C with bellows powered by water power . This enabled the first conceptually real blast furnace , which was still based on charcoal from coal piles in the still dense forests, to start, which could produce pig iron in appreciable quantities. Medieval gunsmiths - instead of the earlier "piece casters" - processed it as " castings " into guns and cannonballs , and later into various "cast goods" such as the Siegerland furnace plate casting , which founded an entire industry . With the further development of simple shaft furnaces into small blast furnaces, now called cupolas , larger amounts of cast iron could also be melted. This made iron construction possible, delivering cast segments from the ornate garden pavilion to larger objects ( bridge over the Severn , casting hall of the Sayner Hütte ), which were then assembled into prefabricated structures. The joining of cast and rolled parts led to large buildings ( Frankfurt station hall ) towards the end of the 19th century , until this technology was replaced by pure steel construction.
In parallel to this development, iron casting has been perfecting itself since the first third of the 19th century due to the need for iron castings by mechanical engineers and the railways.
Georgius Agricola (1494–1555), mineralogist , geologist and author of De re metallica libri XII (Twelve Books of Mining and Metallurgy), which is fundamental for ore mining and smelting , gave precise descriptions and engravings of technical facilities and processes, such as, Driving art ”,“ water art ”, tunnel construction, smelting furnace construction, or roasting and driving work, not only valid rules for a“ modern ”metallurgy for his time. The preserved facilities of the "water art", which are indispensable for mining and smelting, were declared a World Heritage Site in 2010 as the Upper Harz water shelf .
A blast furnace no longer run with charcoal but with coke went into operation in England in 1781, and Silesian Gleiwitz followed in 1796 . In 1837 the hot furnace gases were made usable for the first time ( Faber-du-Faur method). Since the early pig iron with a carbon content of up to 10% was neither forgeable nor weldable , various methods of “ freshening ”, i.e. carbon removal, were developed.
The "wind freshening" is coming
From the historical approach "oven fresh" starting on the labor-intensive " puddling furnace " there was a solution to the 1855 by Henry Bessemer invented "Wind Fresh" in which compressed air from below through one with acid ( silicate -lined) mass, large pear-shaped vessel ( Bessemer ) blown has been. In the process, carbon - and with it other undesirable, oxidizable additions of the pig iron, such as silicon (which provides process heat) - were oxidized, in fact burned, to such an extent that the iron treated in this way became malleable.
The Siemens-Martin furnace ("SM furnace") attracted a lot of attention at the 1867 World Exhibition .
In 1878 Sidney Thomas and Percy Gilchrist improved the Bessemer process by adding an alkaline lining to the “pear”, which also reduced the phosphorus content. With this method, were brown iron ore with low iron content (30-55% Fe ), including the very fine-grained funded Lorraine Minette heard (only 20-40% Fe), and German Raseneisenerz ( Salzgitter ) to cast and forged steel to process. The slag , which predominates in the blast furnace process in a ratio of 2: 1, was - ground - as phosphorus-containing " Thomas flour " as the first artificial fertilizer for agriculture , which however remained dependent on iron smelting until the ammonia synthesis according to Haber and Bosch became an alternative in the 20th century . The above-mentioned blow-steel processes were further improved with the LD process (patented December 1950), which introduces pure oxygen for freshening steel production and which, after a good four hundred years of history of the blast furnace (which, however, still retained its technical justification under the appropriate conditions ), is now available the technology was.
The blast furnace is becoming less important
The classic blast furnace lost its unique position as a pig iron supplier for steel production with the introduction of the Siemens-Martin furnace with Martin regenerative combustion. In it, at a temperature of 1700 ° C, pig iron is transformed into low-carbon steel together with scrap containing oxides (scrap recycling as the first recycling process). The electric steel process goes one step beyond the Siemens-Martin process. Scrap and sponge iron (pellets) produced by direct reduction from rich ores are turned into steels or cast iron types in an electric arc furnace .
Another simplification was the use of gas ( shale gas ) to reduce iron oxides to sponge iron, which can be used directly for steel production.
A conventional blast furnace plant designed for maximum throughput is dependent on an advantageous location in order to be economical because of its large demand for input materials. For blast furnace operation, these are local or regional ore or coal deposits, supplemented by the infrastructure. An important German plant in Duisburg, Europe's largest inland port, estimates the advantages of the location so high that after decades a new blast furnace went into operation in 2008. An Austrian plant was built close to its ore deposits ( Steirischer Erzberg ) on the Rhine-Main-Danube major shipping route . Inland and sea ports with sufficient capacity make it possible today to supply the input materials inexpensively by ship and thus to operate a blast furnace even at locations with little ore and coal. The electric steelworks (mini steelworks), for which a transport connection by land or water is sufficient, is increasingly taking its place. It can flexibly adapt to the available quantities of its raw material scrap and, unlike a blast furnace, work discontinuously and with less environmental pollution.
A counter-movement was attempted with the migration of the classic pig iron production in the blast furnace including the attached steelworks to the basic raw materials, primarily deposits with high-quality iron ore (Brazil, Belo Horizonte ). The advantage achieved in this way should favor the globally oriented transport of the products. So far, however, the expectations have not been met.
The return of copper
In the middle of the 19th century and with the onset of industrialization, a kind of new era for copper and copper alloys began in Europe : the bronzes were no longer in the foreground. The return of copper was expressly determined by a new copper-based alloy called "Gun Metal" or "Cannon Bronze" and was a copper-tin-zinc-lead alloy that met the military requirements of the time, mainly for cannons . Later and until today it is called machine bronze or gunmetal and is used especially for fittings .
Equally important for the consumption of copper is the rediscovery of historical brass as a particularly versatile cast and wrought alloy ( cartridge cases , cartridges, sheet metal , wires and wire mesh made from them). Sieves made from fine brass wires for home and trade are called Leonische Waren . Today it is the “ cable harnesses ” manufactured in highly specialized factories that modern electronics require not only for vehicles and large aircraft.
With the introduction of telegraphy and later the telephone, the civilian sector required highly conductive copper wires that could be used to bridge greater distances. The same has been true for the armature winding since Werner von Siemens discovered the dynamo-electric principle in 1866 . The use of electromagnets made possible by this made small, high-speed electric drives ( electric motors ) available for work machines towards the end of the 19th century and gradually replaced steam engines and drive belts . This was followed by the generators for generating electricity in power plants and there was again a need for the overhead lines made of copper that were necessary for the transmission of high-voltage currents .
There is a need for copper pipes for public and individual heating systems and water supply ( fittings ). A tube radiator made of copper ( radiator ) is used for water-cooled internal combustion engines in automobiles . According to the trade press, a car contained around 25 kg of copper in 2008. For electric cars, the same sources calculate with an additional requirement of 40 kg of copper per vehicle.
In shipbuilding , the corrosion-resistant copper, which protects against mussel growth, is used below the waterline ( fouling ), while above it, brass dominates in equipment, fittings and instruments. The proven resistance to weather influences created numerous possible uses in construction and in traffic. The bactericidal property of brass handles and handles has proven to be beneficial in public transport.
The "earth metals" are coming
In addition to the “Iron Age”, which adapted to the requirements of modern times (steel structures, Eiffel Tower ), something completely new in metallurgy has appeared since the end of the 19th century, the “Earth Metal Age”. The elements that determine them are called earth metals because they do not occur as metal-bearing ore, but only in compounds that - for chemical simplicity - are called earth . Usually this is the oxidic form, with aluminum, the best known of all earth metals of group IIIa of the periodic system of elements , this is the bauxite .
Spodumene , a lithium-aluminum-silicate, only brought into focus with the development of the super-light metal, can also be found in Germany in extensive deposits that are awaiting detailed exploration.
Rare earth metals
The periodic table knows 14 rare earth metals , called lanthanoids . Taken are added scandium , yttrium and lanthanum , is so often spoken of 17 elements. A subdivision according to atomic mass distinguishes lighter from heavier elements, whereby the heavier elements that are particularly sought after for a new technology and its subordinate application techniques are inferior to the lighter ones in terms of occurrence and productivity. One of the results of a new electronic communication is the development of ubiquitous information possibilities, which have gained in importance to an extent that could not be expected around the middle of the 20th century. An economic article headlines in this context: "From salt became gold".
The rare earth metals are contained in minerals with different frequencies and predominantly oxidic-silicate character. A scandium-rich mineral is thortveitite found in Norway and Madagascar . Most of the occurrences are known of yttrium, as it is contained in numerous minerals, but few of lutetium. Lanthanum is found in monazite sand (secondary, enriched deposits of cerium phosphate) together with other "light" rare earth metals as a companion. These deposits are also known as cerite earths, as they were used exclusively for the extraction of cerium for a long time.
In order to represent the pure elements, the minerals are mostly processed wet-chemically and converted into chlorides, which are dried and then subjected to a melt flow analysis.
Cerium, a widely used element of this group, was already used industrially in the 19th century, both for the mantles of the still widespread gas lighting, and as the basis for the alloy developed by Carl Auer von Welsbach for the production of flints, etc. a. for pocket lighters.
An alloy of 48–52% cerium, to which other lanthanides and 0.5% iron are added in addition to lanthanum , has been used since the 20th century for nodular graphite cast iron and for alloys of many non-ferrous metals as a "mixed cerium metal" to influence the grain structure (see melt treatment ) is used.
In the field of modern electronics, for flat screens, energy-saving lamps, batteries, hybrid motors and other new products, most of the lanthanoids are sought-after raw materials.
“Rare earth metals” are by no means “rare” in the literal sense of the word, but today it is true that only 30% of the world reserves estimated at 100 million tons are located in China for geological reasons (lithophilic enrichment), but in 2010 with 95% of the production of 135,000 tons that served world consumption. More recent reports put earlier statements into perspective and refer to deposits in all parts of the world that are worth mining if they are processed sustainably, but mainly in Greenland, Vietnam, Canada and the USA. The Storkwitz deposit is located in Saxony-Anhalt. Prospecting stimulated by the scarcity leads to surprising results: "Japan discovers rare earths in its waters", highly concentrated, but at a depth of 5000 meters that is difficult to exploit.
The report continues to report that the recycling rate is too low.
The low-melting elements gallium , indium (F 156.4) and thallium (known as rat poison), which are also traded as "special metals", are not part of the rare earth metals, but are often named together with them because of their area of application resulting from modern technologies , which are obtained electrolytically from their natural compounds.
aluminum
It all started with aluminum . Friedrich Wöhler first reduced it as a gray powder in 1828, although aluminum was discovered as an element by Hans Christian Ørsted as early as 1825 . The production of molten spheres from aluminum did not succeed until 1845. In 1854 Robert Wilhelm Bunsen proposed the fused-salt electrolysis for the recovery of usable quantities . Henri Etienne Sainte-Claire Deville presented it for the first time in a process in 1855 and called it "silver made of clay" because of the cost of its production at the time. In 1886 Charles Martin Hall and Paul Héroult applied for a patent at the same time , which is the basis of aluminum production to this day and opened the way to a utility metal for him. It took another ten years for the world's first aluminum smelter to go into operation in Neuhausen am Rheinfall, Switzerland , with the help of powerful turbines using the hydropower of the Rhine Falls (built by Aluminum Industrie Aktiengesellschaft, AIAG for short, later Alusuisse ). Another ten years later, the AIAG also put the first German aluminum smelter ( Aluminum Rheinfelden ) into operation in Rheinfelden (Baden) on the Upper Rhine , which obtained its energy from the recently built Rheinfelden hydropower station .
In 2014 (according to the note in Economics from issue 1/2015, ERZMETALL) just under five million tonnes of raw aluminum were produced by the five Arab-dominated primary smelters of the GCC alone (energy-rich Russia missed out on RUSAL, which in 2014 only produced 3.6 million tonnes of market leadership with a total demand of 59 million t in 2015). In 2011, Germany cites a consumption of 28 kg aluminum per inhabitant.
The chemically similar scandium with a density of 2.985 g · cm −3 is a light metal that only found interest in the age of space technology. Boron is another non-metal that only occurs in the form of oxidic compounds. In metallurgy it is used in the hardening of steels, as an additive in aluminum alloys and as a neutron brake in nuclear technology.
As earth metals, aluminum in the first place can be assigned to elements that do not belong to the same group of the periodic system, but are metallurgically comparable insofar as they never occur in ore deposits in nature, but only as minerals, in form chemical compounds, mostly chlorides , silicates or carbonates .
Magnesium, titanium
Magnesium , which continues to grow in industrial importance due to its low weight , is obtained from chloride ( Israel , Dead Sea , carnallite as overburden salt in potash mining), but much larger amounts worldwide from the reduction of magnesite .
Titan has an exceptional position . It occurs as ore in the form of rutile , anatase , brookite or ilmenite . The majority of it is obtained from ilmenite and rutile sands and can be put to the side of the earth metals. With a density of only 4.5 g · cm −3, it is still one of the light metals .
The “light metal age” begins with the earth metals and elements related to them. In any case, it must be seen as a metallurgical epoch and is increasingly taking its place alongside the still dominant “Iron Age”. In a foreseeable period of time, the light metals will not displace iron in the same way as it displaced bronze and this previously displaced copper and that in turn the stone ax and hand ax .
State of metallurgy at the beginning of the 21st century
Extraction of the raw materials
Finding “solid”, ie pure, metal has always been an exception. The metal is sought in ore. To the geosciences related economic geology deals with the origin of the deposits. The applied sciences around mining ( prospecting and exploration ) deal with the prospecting, exploration and mining of the most "prospective" deposits, i.e. those that promise good ore exploitation - whereby the technology and further processing strongly depend on the metal content of the deposit is.
It is located underground in the tunnel (historical examples: silver mining on Cerro Rico in the Bolivian Potosí until 1825, today only copper, tin and lead can be found there). The historical gold mining in Austria (" Rauriser Tauerngold") is also known. Other European examples typical of opencast mining can be found in Falun in Sweden (lead, zinc, copper), in Erzberg in Austria (iron) and not far from there in Mittersill ( tungsten ).
In addition to open ore deposits (called “outcrops”), the important deposits include not only ore but also “solid” geologically so-called “sands” and “ soaps ” that are found worldwide . They are differentiated according to the way in which they arise. Most metallurgically significant are the residuals left over after the weathering of surrounding rock (e.g. magnetite or magnetic iron ore) and the alluvial , washed ashore by water going down into the valley (e.g. discovered in California in 1848 very rich in gold on the American River ) and, geologically comparable, those tin-containing, marine, coastal soaps from Malaysia and Indonesia with a share of 30% of world production, as well as the cerium-containing monazite sand of Western Australia and the titanium-containing ilmenite sands (black sands). As " residue rocks ", the "sands" related parties, the nickel are laterite -Erze that are found only in lower geological reasons, equatorial latitudes.
The Central African deposits of tantalum and niobium-containing ores known as coltan (columbite-tantalite) (also found in floating soaps) are exploited for instruments and equipment ( circuits ) , especially because of the corrosion resistance of the tantalum obtained . Due to their high hardness, tantalum , niobium and the related vanadium (vanadium group of the periodic table) are sought-after accompanying metals in stainless steels .
Post-classical, as they are tied to processes that were only developed in modern times, can still be assigned to this metallurgy:
- the electrolytic extraction of alkali metals from the mining of their chlorides and the mining of uranium pechers as a mineral containing uranium;
- the state-of-the-art production of magnesium from the breakdown of magnesite (Australia) via the intermediate stage magnesium chloride , the smaller part of which can still be obtained from its share in seawater;
- the open mining of bauxite , a reddish sedimentary rock , which - converted to pure clay - is the basic material for aluminum production;
- A future task with great metallurgical benefits is the deep-sea mining of manganese nodules with up to 27% manganese and other metals, including up to 1% nickel , which has been prospected for decades and has still not been technically satisfactorily solved . This applies even more to the deposits of minerals, crude oil and natural gas that have been suspected to be under the North Pole at a depth of 4000 m since 2007 .
- The increasing importance of recycling metallurgy, which has set itself the task of using primarily industrial metals, but also scarce, metallurgically important elements in a sustainable manner.
Classification of metals according to their metallurgical importance
A common classification is based on the percentage of the elements in the earth's crust , i.e. without taking into account the nickel-iron earth core. However, this classification says nothing about the metallurgical meaning. Beryllium has a share of only 0.006% and yet the magnesium, which is abundant at 1.95%, cannot be melted and cast without its addition as an oxidation inhibitor.
The practice tends to stick to the distinction between main metals - that is, metals that are widely used as the basis of alloys - and secondary metals. Aluminum has become a main metal; it was only recognized as such in the 20th century because, like silicon , it does not occur in nature as a metal. The clay mineral bauxite (previously often referred to as "aluminum ore") is processed into alumina and has been electrolytically extracted from aluminum since the end of the 19th century . The main metals also include the metallurgically and chemically important alkali and alkaline earth metals sodium , potassium , calcium and magnesium. Since they never occur metallic, but only in the form of non-metallic compounds, as salts, carbonates and silicates, they were assigned to the earth metals at an earlier point (section The "earth metals" ), also because of the approximate comparability of the extraction process. The rare earth metals require a special section (see there).
The “earth metals” also include silicon, which has several functions. It is primarily a semi-metal that occurs naturally only as quartzite or quartz sand (SiO 2 ), from which it can only be extracted “carbothermally” in an electrochemical reduction process in an electric arc furnace with carbon electrodes . When iron scrap is added at the same time , ferrosilicon (FeSi), which is used, among other things, for calming steel after refining , is created " in situ " (in the process ). Like aluminum and manganese, silicon has a deoxidizing (oxygen-removing) effect.
In the case of aluminum-silicon alloys, silicon determines the alloy properties of wrought alloys as well as cast alloys . An additional melt treatment (refinement or refinement) prevents the disadvantageous primary coarse separation of the silicon when the melts slowly solidify, be it in sand casting , such as engine parts (e.g. crankcases , cylinder heads ), but also in heavy mold casting .
With very specialized copper alloys (silicon bronze) it is an alloy companion and in semiconductor technology it has achieved its own position. Manufactured in an elaborate process of “ pure metallurgy” (that is, achieved purity of a metal in the range of 99.999%, so-called “five-nine metal”), it is the basis for chips that are indispensable in computer technology. The German share of world production is considerable (for example chip production in Dresden ). Silicon is also used as a semiconductor in the manufacture of solar cells .
Another possibility of classification separates the heavy metals from the light metals . Heavy metals have a density greater than 5. Osmium with a density of 22.45 g · cm −3 is at the top, followed by the much more popular platinum , which is also used for jewelry, with a density of 21.45 g · cm −3 . Copper (8.93 g cm −3 ), iron (7.86 g cm −3 ) and zinc (7.14 g cm −3 ) follow at a distance. Among the light metals, lithium with 0.54 g · cm −3 is the lightest, followed by magnesium with 1.74 g · cm −3 and aluminum with 2.70 g · cm −3, titanium with a density of 4.5 g · cm −3 is still assigned to light metals.
There is also a widespread division into “base metals” and “alloy companions”, which includes numerous elements that are often only added in traces and are nevertheless important. Copper, iron, lead, tin, zinc, and nickel are considered to be base metals - due to developmental history. However, aluminum, magnesium and titanium are now equated with the historical base metals in terms of their economic and metallurgical importance.
A distinction already mentioned in the introduction sees iron and its metallurgy in the first place. The non-ferrous metals follow at a distance .
Current classifications also differentiate between "bulk metals", such as iron, copper, zinc, etc. and special, rare earth and, as a subgroup, technology metals. The special metals include gold, silver and platinum metals, but also rare earth metals, refractory metals and (so-called) "technology metals, indium, germanium, gallium, rhenium, selenium and tellurium". What they all have in common is their addition to “bulk metals” in only small quantities and an increasing interest in recycling.
Main metals

As the main metal, copper is extracted either by the "dry route" for the richer ores or the "wet route" for the poorer ores. The process leading to pure copper is multi-stage. It begins with the roasting of the ore, which is followed by the crude smelting with further operations, either in the shaft furnace (“German way”) or in the flame furnace (“English way”). The product is now black copper with more than 85% copper. Its further refining is now rarely done in the flame furnace. It is more common to refine black copper plates electrolytically . The pure copper that arises is a hydrogen-containing cathode copper , also known as a blister copper (bubbled copper). It is “conductive copper” (pure copper with defined electrical conductivity) for the electrical industry, being highly pure and free of oxygen .
The bulk of the available refined copper is - mostly alloyed - into kneading or casting material. When rolled into sheet metal, pure copper is particularly noticeable in construction. Very stable against the effects of weathering, copper sheets are increasingly being used for roofing and rain gutters . The patina (green color) that develops over time was valued earlier. Incorrectly referred to as toxic verdigris , it is actually made up of non-toxic copper sulfate and carbonate .
Although all alloys with the main component copper are referred to as copper alloys , there are significant differences in appearance and mechanical properties between bronzes and special bronzes (compare beryllium bronze ) and brass (alpha or beta brass with 63–58% zinc). One example is the “ nickel silver ”, which is completely different in color from the reddish copper tone , formerly also known as white copper and even more recently with the term “Packfong”, which originated in China.
Pure copper is more numerous than the “master alloy” in non-ferrous metallurgical processes of added elements. In cast iron, copper is an alloying element that has positive properties.
Tin has been themost important metal accompanying coppersince the Bronze Age . As pure tin, it is not processed very well because it is too soft. For more details see under "Tin."
Because of the frequency of its occurrence and its low melting point, lead (lead sulphide) falls before copper, around 6000 BC. BC, as metallurgically usable (see also under literature: 5000 years of casting metals ) Historically ( Roman times ) it appears as a widely used, easy-to-work main metal. Since the 20th century, insofar as it is late, it has no longer been used because of its toxicity for systems carrying drinking water (lead pipes). Lead is believed to be one of the causes of the fall of the Roman Empire for the same reason. Paints made on the basis of lead oxide (" white lead ", red lead ) and children's toys on or in which it is contained are also toxic .
As a result of modern printing technology, lead- antimony alloys as font metals have become largely insignificant. For the time being, lead is still indispensable for accumulators and as a component of lead-containing bearing metals. Here it is especially lead bronze, a copper-lead-tin alloy with up to 26% lead, which is used for highly stressed slide bearings in automobile engines.
With wrought brass alloys, lead is an additive that promotes machining (maximum 3%). With up to 7% it is an alloy companion to copper-tin-zinc cast alloys ( machine bronze ).
Iron becomes cast iron or steel solely through its accompanying elements (iron companions), which, although indispensable in steel production , remain minor metals in terms of quantity. For hard steel, manganese is added, which is contained in the fried iron with 50%. Ferromanganese is a manganese carrier with 75–85% manganese. Chromium , nickel, molybdenum , vanadium , cobalt (see also metals used in industry ), titanium , the semimetal silicon (added as ferrosilicon / FeSi) and the non-metals carbon , phosphorus and sulfur are also used in steel production, such as cast iron .
Zinc is pure zinc alloyed with 0.5% copper when galvanizing steel and used in large quantities as protection against corrosion . Zinc sheets and strips made from very “low-alloy pure zinc or titanium zinc” with 0.1% copper or titanium are used in construction . Zinc is also the base metal for fine zinc casting alloys with copper and aluminum components. Zinc is an important companion in copper alloys (see above), especially in brass for more than two millennia.
Aluminum is available as standardized primary aluminum (purity 99.5–99.9%), as pure aluminum with a degree of purity of 99.99% ("four-o'clock metal") and even as pure metal (> 99.9999%). Its actual importance as a wrought and cast material is determined by numerous alloy-forming accompanying elements, including the base metal copper. In 1909, Alfred Wilm developed the patented Duraluminium (brand name DURAL), the first hardenable alloy consisting of aluminum, copper and magnesium ( AlCu 4Mg1). This alloy is mainly used in aircraft construction, first at Junkers / Dessau . Aladár PACZ 1920 manages the structure -influencing "refinement" of the eutectic aluminum-silicon - binary alloy (legally protected as "Alpax" and " Silumin ") by means of addition of less than 150 ppm sodium. In the range of 7–13% silicon, this becomes the group ofalloys most processedas castings today. A little later, aluminum-magnesium alloys follow(legally protected as seawater-resistant hydronalium and, in a variant with a titanium addition, "particularly seawater-resistant"). The alloy AlMgSi with 0.5% silicon and magnesium each canbe used as a rolling and kneading material. In addition to it, there are alloys with copper, titanium, zinc, manganese, iron, nickel, chromium and other elements, whereby the increasingly more specified properties required of the alloys determine the type and quantity of accompanying elements. If they are not available as a finished alloy, they can be added to a base melt of pure aluminum as an “alloying agent” or “master alloy based on aluminum”.
Accompanying metals
In addition to the term "accompanying metals" (synonym: "alloy companion") there is the more comprehensive term "accompanying elements". These are regularly used to manufacture alloys. The proportion of these accompanying elements starts at tenths of a percent and less and goes up to the double-digit percentage range. Examples: AlCuTi with 0.15-0.30% titanium; AlSi 12 with 10.5-13.5% silicon. Materials development now only knows a few elements, for example radioactive ones , which are not suitable for potentially improving the properties of newly developed alloys. Particularly in the area of "rare earths" are in addition to the already long known cerium (see for cerium mixed metal ) and the associated him lanthanum (Greek: "the unseen") other related elements such as neodymium (for strong permanent magnets) or praseodymium (in its connections for colored glasses with UV absorption).
Examples of further important accompanying elements are the non-metal phosphorus in eutectic AlSi piston alloys , or beryllium , a light metal with a density of 1.84 g · cm −3 , which is toxic in the form of its vapors. Beryllium is used for hardenable bronzes ( beryllium bronze ), for spark-free tools in mining, as a deoxidation additive for conductive copper (here via a five percent master alloy) and in the ppm range (also dosed via master alloy) in aluminum alloys to improve quality and to reduce oxidation of the melt, a measure that is essential when melting and casting magnesium alloys. The annual world production of beryllium - from whose rare, transparent crystal form beryl our word glasses is derived - is given as 364 t.
Basic metallurgical processes
After this first process stage, the elements described in the section “Extraction of the raw materials” with regard to occurrence and extraction go through a further process stage, that of processing, before they become pure or alloyed usable metals and semi-metals through smelting.
A first divorce or sighting is still assigned to the mining area, which can be both tunnels and opencast mining. The subsequent processing stage is already considered "metallurgical" work. The necessary measures are as diverse as the raw materials themselves. A basic distinction is made between dry and wet processes, each with the aim of “enrichment”. "Heap" mined in tunnels requires the separation of valuable, ore-rich, from worthless, ore-poor, "deaf" material, which is referred to as "gangue". For the separation, the rock is crushed further by grinding, followed by sieving, sifting and, if necessary, magnetic separation . When mining in opencast mines, overburden of different thicknesses must usually be removed beforehand.
The further processing of the prepared substances is carried out using the basic techniques described below.
Pyrometallurgy
Pyrometallurgy is the thermal further processing of ores or already extracted metal, be it oxidizing, i.e. heated with oxygen supply ( roasting ), or reducing in an oxygen-free furnace atmosphere. Fire refining (oxidizing and slagging of undesired elements) and segregation , which refers to the segregation of a melt using differences in density in the melt material (example: above its solubility limit in copper, lead segregates from a copper alloy melt, drops to the Bottom of the melting vessel). The situation is similar with distillation, which uses different vapor pressures of the substances at a given temperature to separate them into fractions (example zinc extraction from roasted zinc ore in muffle furnaces ).
The latest state of the art is a two-step process for removing impurities such as arsenic, antimony and carbon from copper and gold concentrates by roasting.
Hydrometallurgy
Hydrometallurgy originally means the preparation of ores for smelting using cold or warm separation processes (cold or hot extraction) using water. The historical flotation , further developed for sink-float separation, makes it possible to enrich the ore extracted during the mining. Leaching and boiling serve the same purposes. Extraction using acids , alkalis , organic solutions and bacteria is also part of hydrometallurgy. If bacteria are involved, one speaks of bioleaching . Chemical precipitation processes or electrolysis are also used to extract the elements contained in less than one percent concentration from poor ores, for example precious metals. In these cases hydrometallurgy is referred to as “electrometallurgy by the wet route”.
Electrometallurgy
Electrometallurgy includes electrothermal and carbothermal (see silicon production ) as well as electrolytic process technologies. Modern steel production, which replaces the blast furnace with the induction furnace charged with scrap rich in oxides, can also be described as an electrometallurgical process ( electric steel )
By means of fused-salt electrolysis , aluminum is released at the cathode from an alumina - cryolite mixture ( Hall - Héroult process). A coal pan is used for the mixture, which also functions as a cathode , and current-carrying anodes that are fed in from above . The Bayer process , which is generally used today, extracts aluminum in a continuous process of removing metal and adding a mixture of alumina, as the bauxite that is processed and dried in special alumina factories is called. Continuous production of the electrolysis of the alumina-cryolite mixture includes the ongoing replacement of used anodes. The Söderberg anode technology , which has been the standard for several decades, is increasingly being replaced by the Pechiney process , which has been significantly improved in terms of energy consumption, anode maintenance and yield ; existing old systems are shut down or converted.
All alkali metals can be obtained from their salt solutions according to the principle of fused-salt electrolysis of a chloride mixture (because the required reaction temperature is always lowered with mixtures) .
As early as 1852 , Bunsen proposed electrolysis mixed with fluorspar for the increasingly important alkaline earth metal magnesium . Today it is basically still presented in the same way, be it directly from natural magnesium chloride ( bischofite ), or after separation from mixed salts containing magnesium chloride ( carnallite ), or from the magnesium chloride content (up to 0.4%) in seawater. Technically more important is the already mentioned conversion of magnesite MgCO 3 or bitter spar (large deposits in Australia, among others) in a chemical process first to magnesium chloride . A subsequent electrolysis, which since Bunsen's knowledge has practically resembled the process of aluminum production (pioneer in this field: G. Pistor , 1920), leads to pure magnesium. The first volume production took place in the Elektron-Griesheim plant of IG Farbenindustrie (protected trademark "Elektronmetall")
Electrolytically obtained magnesium has become a product of electrometallurgy that is not inferior to aluminum in terms of its industrial importance due to constantly growing areas of application. It was used early on, for example to influence the structure of cast iron, in lightweight aircraft construction ( zeppelin ), in civil and military pyrotechnics (rockets, flares, stick bombs). The Second World War meant a development boost for magnesium and its alloys, because it was a material that was independent of imports. In the 21st century, its use meets the increasing trend towards lightweight construction, especially in vehicles, and not only the methods of its extraction are expanded, but also those of its use. Mostly these are parts manufactured using the die-casting process, in some cases it is “ hybrid casting ”.
Powder metallurgy
Although the term powder metallurgy is widely used in specialist literature and practice, it is not a separate metallurgy, but a - latently potentially explosive - technique of spraying molten metals and alloys either in the liquid state into powder or converting them from the solid state into fine granules. The majority of useful metals - from aluminum to zinc - can be ground in powder mills into powders with grain sizes from 0.1 to 500 µm . Because of the risk of explosion in contact with atmospheric oxygen emanating from all metal powders with different hazard potential, an inertization or phlegmatization is carried out. Stabilizers, ranging from wax to phthalates , reduce the sensitivity to explosion. Magnesium powder is a special case because of its highly pyrophoric behavior. It cannot be obtained by grinding, but only by "rubbing" the block metal.
Metal powders, correctly called “inorganic pigments ” in this case , are important as a component of metallic paints for automobiles. A completely different area of application is pressing in steel molds under very high pressure (2000 bar and more). From pure metal powders pressed in this way, often alloy-like mixtures, metallic molded parts can be produced (MIM process, SLM process). With hot isostatic pressing, which is preceded by the heating of the powder up to the softening limit, the properties of cast parts are achieved.
Another approach is taken in the manufacture of parts that are difficult to cast or that are complex to manufacture from solid by using the 3D printing process. This technology, which has been known for years, is now so advanced that metallic series parts for technically demanding use are built up (injected) layer by layer on 3D printers to the shape specified by the computer.
In the mold and model comes powder flame spraying is used. The metal powder is softened by a flame or by plasma ( plasma spraying ). The advantage lies in the short-term production of tools - molds - for pilot projects in machine and tool construction ( automotive industry ).
Secondary metallurgy
The term secondary metallurgy was originally only used in steelworks, but is also used for the desulphurisation process of cast iron. However, it does not designate a separate metallurgy, but rather various, alternatively or sequentially applicable, the molten steel desulphurizing, deoxidizing or "calming" measures, which serve as "ladle metallurgy" to increase the steel quality. The addition of aluminum granulate , calcium silicide and a number of other electrometallurgically obtained products is common. In addition to these techniques based on chemical reactions, there are also those that have a purely physical or physico-chemical effect. This includes applying a vacuum to the melt (with the resulting degassing effect). The CLU process , more commonly known as the “Uddeholm process”, introduces inert or reactive gases into the molten steel through nozzles at the bottom of a ladle.
Overall , they are special forms of melt treatment , as they are common in a comparable manner with other metals (for example in primary aluminum production).
In addition, the term secondary metallurgy is increasingly used by non-ferrous metal smelters, which, after exhaustion of ore mining areas close to the site, instead of primary production of metal, in accordance with the demand for sustainability in the handling of raw materials, with their recovery from scrap and waste, such as Deal with sludge and dust, i.e. set up a secondary cycle.
Nuclear metallurgy
The nuclear metallurgy deals with the radioactive elements whose best known today uranium is. It is obtained from the uranium-containing mineral pitchblende using hydrometallurgical processes . Long neglected compared to radium , which was already used for medical purposes in the early 20th century ( nuclear medicine ), it only gained its current importance during the course of the Second World War. In the USA, the “ Hanford Works ”, which were built for this purpose alone, operated nuclear metallurgy on a large scale in order to produce enough plutonium for the construction of the atomic bomb . Today, civil nuclear metallurgy is geared towards not only extracting fuel elements for nuclear power plants, but also dealing with the processing of the remaining residues and the so-called "safe disposal" (see also " Uranium "). An important secondary field of nuclear metallurgy are the radionuclides for medical purposes, such as technetium -99m and iodine 131 (e.g. for scintigraphy ) , which are produced in only a few nuclear reactors worldwide .
Smelting and processing technology
Metallurgy and metallurgy are still synonymous today and the extraction and processing of ores is seen as a process that precedes “smelting”.
A different structure made possible by advances in technology and science sees metallurgy as a superordinate science conveyed as metallurgy , which uses extraction and processing technology, which in turn uses chemistry . From the more narrowly understood metallurgy - a term that is primarily based on thermal processes - the development leads in the sequence already described from the pretreated input materials to usable metals and alloys, semi-finished and finished products. The workflow in a smelter that processes ores, whether ferrous or non-ferrous metals, usually consists of the following steps:
- Charging (compilation of the material to be smelted) of the input , also taking into account the desired properties of the output
- One-off (discontinuous, tied to the furnace socket) or continuous (continuous) charging, i.e. charging of a furnace, with equally continuous metal removal (examples: blast furnace with daily output of up to 5000 t of pig iron or the melt-flow electrolysis that continuously supplies raw aluminum )
- Reduction of the use, again either in batches and with batch properties (see below ) or by means of continuous recharging and collection of the recovered metal in a mixer that only compensates for the batch character (see ibid ).
- Treatment of the melt by means of an oxidizing or reducing refining (see secondary metallurgy ), including alloying or alloy corrections
- Potting : simple ingot casting or further processing (example: steelworks that processes pig iron either into simple cast steel or continuously cast formats for a downstream rolling , drawing and pressing plant ).
"Industrial Metals"
"Industrial metals" are used when a metal has established its own industry because of its importance . This is at least the case with iron, copper, nickel, lead, zinc and aluminum. The term “metals used in industry” is broader and includes all elements used in metallurgy, regardless of whether they appear independently, i.e. unalloyed, or as alloy components.
iron
The range of “smelting” is particularly evident when using iron as an example. Iron ore smelting is based on the iron-carbon diagram , on which iron technology is based as a science and then developed its techniques.
The classic ironworks only produces pig iron in the blast furnace. The blast furnace to a charge make- charged mixture mentioned, the ore portion has previously been prepared. A roasting process oxidizes the sulfides . The associated heating removes other volatile constituents, such as too high a water content, as is the case with the Lorraine minette (minette means “small ore” because the iron content is relatively low, around 20–40%). Oxide, hydrated oxide or carbonate ores ( magnetite , hematite , limonite ( Salzgitter ), siderite (Austria), and also the pyrite (pyrites) burn-off from sulfuric acid production) are prepared for the blast furnace process by adding aggregates ( Möller ) from the river - and slag-forming limestone ( flux ) and coke are added. In historical blast furnaces, charcoal produced in the vicinity was used instead of coke .
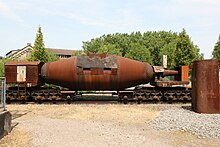
The tapping (discharge of the molten pig iron) takes place in continuous operation, that is, the furnace never cools down; As long as its lining allows, it is continuously fed via the "gout", the upper end of the furnace, and tapped at the bottom of the sole. The tapping has so-called “batch properties”, whereby batch is understood to mean, for example, a shipload of Brazilian iron ore with properties determined by the extraction location. These determine the assignment to a specific pig iron quality. Both a hematite iron with more than 0.1% phosphorus or a foundry iron with up to 0.9% phosphorus could be tapped. In addition to the batch to which it belongs, the properties of the tapping are determined by the type of solidification. Slow cooling ( ingot casting ) produces gray cast iron , differentiated according to the type of graphite precipitation (lamellar, vermicular, spheroidal). With rapid solidification, white cast iron containing manganese is formed; a transition form is mottled cast iron. Pig iron not intended for use as cast iron is discharged from the blast furnace into a mixer which is used for equalization and from there passed on to the steelworks. For the first time, liquid metal was transported over a greater distance towards the middle of the 20th century in the standard gauge 200 t and more holding and at the same time acting as a mixer " torpedo ladle ". The term “batch” can also be used here, namely the loading of a vessel, pan or oven with an amount determined by the respective capacity. In the further processing, which in this case is referred to as discontinuous, each batch can be assigned characteristic batch properties. “Batch work” is particularly important for the recycling of mostly very mixed scrap.
Even in the 21st century, the production of pig iron is still the purpose of an "ironworks". However, primary production in the blast furnace has lost its unique position in iron production since the invention of the Siemens-Martin furnace with regenerative combustion and especially since the introduction of the electric furnace. In the direct reduction process, a low-carbon sponge iron can be produced from pelletized iron ore in a classic shaft furnace or a state-of-the-art fluidized bed reactor. This is then melted in the electric arc furnace. The process leads to reduced carbon dioxide emissions. Nevertheless, the “linked ironworks” - also known as the “ironworks”, in Eastern Europe (1936 Magnitogorsk ) referred to as the combine - continues to be the leader in the production of pig iron, types of cast iron and steels.
Cast iron materials are obtained from carbon-rich pig iron. It is fed from the blast furnace into a bed of ingots and the cooled and transportable ingots are melted down again in the cupola furnace of an iron foundry or in an electric furnace and processed into cast parts. As a rule, defined scrap, own foundry return and alloy additives are added there in order to obtain cast iron types with defined properties (see also above). High strength provides, according to E. Bain named bainitic ductile iron . As Austempered Ductile Iron, or ADI for short, it enables “lightweight iron construction”; this has been a response to the rapid increase in cast aluminum in automobile engines since the beginning of the century. A newly developed cast iron material with aluminum as an alloy component even allows it to be used in automobile engines with high operating temperatures, such as those that occur with turbocharging.

Malleable cast iron is a special form of cast iron that occurs as "white" low-carbon or black high-carbon malleable cast iron. Its mechanical properties, which are better than those of gray cast iron , are obtained from annealing the cast parts wrapped in tempered carbon in adjustable, gas-heated tempering furnaces. The residence time under the given oxidizing conditions depends on the part. It starts in a controlled manner at 900 ° C and is lowered to 750 ° C by the end of the tempering time. Examples of malleable cast iron are fittings , keys or gears .
A special form related to malleable cast iron is chilled cast iron (white cast iron, low graphitized iron), which is economically important as roll cast iron (for cold and hot rolling mills, among others ).
Pig iron which has been melted for the first time cannot yet be used for steel production. Steel must be weldable or forgeable and therefore lower in carbon. It is therefore “ refined ”, that is, treated with the aid of compressed air or oxygen in an oxidizing manner until the unwanted carbon is burned and its share is less than two percent. There were several processes for freshening: At the beginning of industrialization the puddling process , in which the plastic pig iron was manually milled with bars, later production in a crucible furnace . In the middle of the 19th century, the freshness in the Bessemer pear and the Thomas process - the blown steel process in the converter - lead to an extreme increase in productivity. The Siemens-Martin process spreads at the end of the 19th century, and finally the electrical process (electric arc or induction furnace) is industrialized at the beginning of the 20th century, before the LD process (oxygen freshening) spreads in the middle of the century . The carbon-oxidizing (burning) freshening is followed by the removal of excess oxygen already bound to iron (deoxidation, "calming") by adding easily oxidizable elements. Common are aluminum or silicon , this as ferrosilicon (FeSi), which is obtained during the carbothermic silicon production (see above). Oxidation and deoxidation are measures determined by thermodynamics and reaction kinetics , in which chemistry and metallurgy - not just those of iron - interact.
Siemens-VAI has brought a special 150 t electric arc furnace for slag-free and energy-saving direct reduction to operational readiness.
As soon as the treated molten steel has settled down, it can be adjusted for future use as steel by adding alloying elements. The variety is considerable because a distinction is made according to origin ( Thomasstahl , Siemens-Martin steel , electrical steel ) as well as use and properties, for example high and low alloyed steel, alloyed cold or hot work steel , stainless steel (NIROSTA with more than 12% chromium ), magnetic, soft magnetic and "non-magnetic" steel and others (complete list, for example, under "steel" in "foundry glossary").
The bulk of the steels, hence also “bulk steel ”, is fed to the rolling mill . Earlier starting material of the Verwalzens were Großkokillen produced rolling slab , wherein are cavity (caused by solidification shrinkage cavities) made by means of an exothermic (heat releasing) the lining of the mold and directed solidification slowed possible. Today the continuous casting process has largely replaced this technology.
The continuous foundry is a processing unit attached to the steelworks, in which the conversion of liquid to solid steel takes place. A distinction can be made between several types of conversion, between "continuous" (strand separation with "flying saw") or discontinuous (due to the maximum strand length specified by the system), furthermore between vertical, horizontal or curved strand casting and finally between "single-strand" or "multi-strand " Investments. The various products are made as solid castings - also profiled - or as hollow castings (tubes). Further processing takes place either after preheating (warm processing) or after cooling (deterrent, cold processing). They are also subjected to natural or artificial aging (transformation of the mixed crystal structure ). Particularly high-quality rolled products can be achieved with heating, followed by quenching hardening and subsequent “ tempering ”, i.e. reheating for the rolling process.
The economically important steel products include structural steels ( T-, double-T, also I-beams , reinforcing steel ), as well as rails , wires that are manufactured in the rolling process or, in the case of small diameters, in the wire drawing shop. Sheet steel, smooth or profiled ( corrugated sheet ), is a versatile rolled product. Tinned on one side, rolled hot strip is called tinplate . In 2007, 1.5 million t of this went into can production. There are numerous steels with special properties, including stainless steels , stainless steel , hard steels (armor plates) for military and civil purposes.
Special steels (including valve steel , shaped steel ) which - starting from continuously cast ingots - are turned into cast parts in a steel foundry, are treated after their solidification - similar to other castings - using heat in order to relax the parts and improve the structure (stress relief annealing, solution annealing ). Additional alloying elements ( chromium , nickel , molybdenum , cobalt ) can be added to such steel melts as master alloys before casting. Friedrich Krupp recognized the influence of strength-increasing additives ( Krupp steel ) as early as 1811 and on this basis introduced cast steel production in Germany ( gun barrels have therefore been made of cast steel since 1859).
Aluminum, magnesium
From a metallurgical point of view, the processing technology of iron and aluminum is not that different. It is demand that gives preference to one or the other. Often it is only determined by the extent to which it is possible to replace “heavy” iron with “lighter” materials such as aluminum, magnesium or lithium. (see also iron ). A head start for aluminum results from the consistent continued development of aluminum foam, also processed in sandwich technology - for lightweight construction and thermal insulation.
In contrast to a connected ironworks, an aluminum smelter gets its raw material alumina from a spatially and economically separate prefabrication, an "alumina factory", which specializes in converting bauxite into calcined alumina. The alumina obtained from there is used in a mixture with cryolite in hundreds of cells in a fused-salt electrolysis and each cell continuously supplies molten raw aluminum, which is regularly removed. Part of the production is refined into pure and ultra-pure aluminum. Pure and high-purity aluminum is the starting point for foil production. Another part becomes cast alloys with additions of magnesium, silicon, copper and other elements. However, the majority of the metal coming from the electrolysis is used in the liquid state as a wrought alloy. The treatment required for this is usually carried out by a foundry ( casthouse ) attached to the primary smelter to which a rolling and pressing plant is attached. In the foundry, the raw liquid aluminum is charged into the mixer and the alloy composition to be cast is adjusted by adding master alloys or scrap , and undesired impurities are removed. The melt is brought from the mixers into casting furnaces. Before the casting process begins, the melt usually passes through a SNIF box to rinse out the last, mostly oxidic, impurities and degassing using forming gas containing a slight amount of chlorine; furthermore, in the pouring channel leading to the continuous casting molds and the distribution system, grain fine wire made of aluminum is digitally controlled -Titanium or an aluminum-titanium- boron alloy supplied.
The finished wrought alloys are cast into rolled or round bars | bolts. The casting takes place either in the continuous vertical continuous casting process, whereby the strand emerging from the mold and cooled with water is cut by a flying saw according to the specifications. Rolling billets are mostly produced as individual pieces using discontinuous vertical continuous casting. They reach weights of up to 40 t.
Given the given dimensions of the casting table and the collar molds embedded in it, the number of round bars cast at the same time increases with their decreasing diameter (up to 16 or more strands, then already known as “laundry stakes”, are possible). The general name is “ semi-finished product ”, with a distinction being made between rolled material, extrusion and tube presses, as well as cold or warm further processing such as forging and drawing. The heat treatment takes place in special ovens, as the basis (more on this in the section on oven technology ) of such different products as sheet metal , foils, profiles and wires , for which there is a rapidly growing demand, because not only the "energy transition" calls for expansion of the transmission networks . The increased use of aluminum sheets in automobile construction is also prompting well-known suppliers to expand their capacities.
A casting technique that has been specially developed for sheet metal and foils and that reduces the number of rolling passes (passes) is strip casting, in which the liquid metal is poured into an adjustable gap between two counter-rotating, cooled rollers. The modern methods of wire production are technically related to strip casting.
All metallurgically to aluminum said can on the even lighter and therefore for both air and space travel as well as generally used in lightweight magnesium are transferred. For a long time , pure magnesium, mainly obtained from the fused-salt electrolysis of anhydrous carnallite or magnesium chloride, now mainly obtained by the thermal pidgeon process, can be alloyed and, like aluminum, can be further processed as a cast or wrought material. Since molten magnesium oxidizes very quickly in air (magnesium fire), it is melted under an inert protective gas and with a beryllium addition of more than ten ppm . In addition to the areas of application already mentioned, magnesium is found in iron foundries as a desulfurizing agent in the manufacture of spheroidal graphite cast iron . As an alloying element, it leads to self-hardening wrought aluminum alloys (see duralumin ).
It has been a property-determining component since the Second World War as a component of seawater-resistant aluminum-magnesium alloys to which titanium is added. (Hydronalium, type SS-Sonderseewasser ).
After 1950, such alloys are increasingly used for anodable cast iron (machines for the food industry, fittings) using both sand and gravity die casting. In the largely automated die-casting technology , mainly aluminum-silicon alloys with a magnesium content are processed, but also magnesium alloys with aluminum and zinc as accompanying elements (the VW Beetle , which was famous at the time, contained magnesium cast parts weighing more than 20 kg in its first concept, including for the gearbox housing ). The use of magnesium, which has been increasing for years in order to save weight, has already been mentioned. The hybrid process for "layered mold filling" from magnesium-free and magnesium-rich alloys, which is based on the thermal and mechanical stress of certain areas of the automobile engine, should be pointed out again.
For lightweight construction technology, especially in automobile construction, not only flat parts (engine hoods, trunk lids), but also parts that are more demanding in terms of casting technology (automobile doors, window frames) are increasingly being manufactured using the die-casting process. Wall thicknesses from 4 mm down to very thin 1.8 mm can be produced.
Joining steel sheets with aluminum and / or magnesium is also easily possible using die-casting technology.
Magnesium is still an important component of all products in civil and military pyrotechnics .
copper
The metallurgical history of copper extraction (see also “ The return of copper ” and copper for main metals ).
Copper is extracted pyro- or hydrometallurgical depending on the ore on which it is based. The so-called copper matte is extracted from sulphide ores in a shaft furnace process and then blown into black or blister copper with 80–96% copper content in a so-called Pierce-Smith converter. Copper sulphide and copper oxide convert to copper, splitting off sulfur dioxide, and iron, the main accompanying element, is slagged. The shaft furnace technology has long been referred to as the “German way”. The "English way" is similar, but takes place in a flame furnace . In the further course of the process, the “ sealing poling ” takes place ; In the past, tree trunks were used to stir the melt; today, natural gas is blown into the melt. This creates what is known as “anode copper”, which is cast into anode plates that are subjected to refining electrolysis. The anode plates in a sulfuric acid copper sulfide solution are connected in series with stainless steel sheets (or in older electrolysis pure copper sheets) as cathodes. The voltage is chosen so that copper goes into solution and is deposited again on the cathodes, while less noble metals remain in solution and noble metals (silver, gold, platinum, palladium, rhodium, ...) settle as so-called anode sludge on the bottom of the electrolysis cell . The precious metals mentioned are extracted from the anode sludge. The refining electrolysis produces electrolytic copper , which has been indispensable for electrical engineering since the 19th century because of its electrical conductivity .
Oxidic ores and poor sulphidic ores, on the other hand, are subjected to extraction electrolysis. For this purpose, oxidic ores are leached with sulfuric acid; a more complicated pressure leaching process must be used for sulfidic ores. The copper-containing solution is enriched by means of solvent extraction before the electrolysis . The product is a very pure, but hydrogen-containing cathode copper with a copper content of 99.90% (electrolysis principle: hydrogen and the metals swim with the current ).
The copper melts, which are finely refined in a flame furnace or electrolytically, are cast into blocks (pigs) made of pure copper or into shapes ( continuous casting ). Is alloyed beforehand, then in order to bring about certain properties, especially of the wrought alloys.
The processing of the refined copper, like iron and aluminum, adapts to the demands of the market in terms of quality and quantity, for which copper is the basis of a large number of technically important alloys. Some have been known since ancient times (see Section 1). Alloy copper is not only the starting material for horizontally or vertically processed shape castings. Both low-alloyed and chromium copper with 0.4–1.2% chromium, it is also a technically important cast (chromium copper for continuous casting molds and other cast parts subject to high thermal loads), as is the bronzes with 12% tin, standardized according to DIN EN 1982.
The bell bronze with the composition 80% copper, 20% tin is one of the most famous copper alloys. Since the first church bells were cast in the 6th to 8th centuries, it has been cast in traditional technology, hardly changed (very realistic description by Friedrich Schiller “ The song of the bell ”). The composition of this bronze - found empirically at the time - is close to the optimum tear strength with a tin content of 18%.
A technique of processing semi-finished products that has been used for copper, brass and aluminum since the 20th century, and has meanwhile also been used for steel, is the manufacture of wires using the proper process and the casting wheel process derived from it .
The copper alloys that became economically important in the 19th century include gunmetal , a copper-tin-zinc-lead alloy (which is closer to brass than to bronzes) and a number of special bronzes, such as aluminum bronze . With 10% aluminum, it is a valuable material for the casting of large ship propellers (unit weight 30 t and more) , because it is cavitation-resistant, but difficult to melt and cast due to the tendency of the aluminum to oxidize .
From a metallurgical point of view , the copper-zinc alloys, collectively referred to as brass , have been just as important as the numerous, purpose-built bronze alloys since the beginning of the industrial age . Due to the yellow coloration characteristic of most alloys of copper with zinc, many brasses are often not perceived as such. An example is gunmetal or red brass (Italian: "ottone rosso").
With its melting point below 1000 ° C, brass is very versatile. With 63% copper, the remainder zinc, it is particularly used for castings (fittings, fittings). With 58% copper, max. 3% lead, the rest zinc, turns into semi-finished products (sheet metal, profiles). A reduction in the zinc content to 36 to 28% favors the drawing process into cartridge or bullet cases of all calibres, which is why these alloys are known as cartridge or cartridge brass .
The demand for brass is only satisfied in special cases with primary alloys (see under recycling metallurgy ); the majority of these are brass scrap (scrap metal) that has been refurbished in a brass smelter ( brass works ), to which fresh production waste from non-cutting and machining is added. Melting takes place predominantly in a channel induction furnace.
Copper-nickel cast alloys with up to 30% nickel are very seawater resistant ( shipbuilding ). With a zinc addition of up to 25% in copper multicomponent alloys with nickel, lead and tin, brass becomes white copper or nickel silver (CuNiZn). They are widely known as cutlery alloys, including alpaca and argentan (see Packfong ).
Constantan and nickeline , a copper-nickel alloy with manganese added, are corrosion-resistant raw material for heating resistors as heating conductor alloys .
zinc
As an “industrial metal”, the importance of zinc is often underestimated. World production in 2014 was at least 13.5 million t. If the amounts of secondary zinc production mentioned in 2010 with 4 million t, u. a. Recycling processes, including iron dezincification and filter dust, add up to a total amount of more than 17 million t (for figures see Erzmetall 3/2016).
Zinc is mined as oxidic ore ( zinc spar , calamine ) or sulfidic ore ( zinc blende ) associated with lead . The carbonate calamine is burned, the sulfur content of the zinc blende is roasted and used for the production of sulfuric acid . The zinc oxide obtained in both ways is either reduced in a dry way together with coal in refractory retorts (also known as muffles) and raw zinc is obtained at 1100–1300 ° C in a distillation process. When using the wet process, zinc oxide is converted into zinc sulfate in a first stage with the addition of sulfuric acid. In the following electrolysis process, electrolytic zinc is deposited on the cathodes as 99.99% pure fine zinc. In terms of quality, a distinction is made between raw zinc, standardized metallurgical zinc and standardized fine zinc.
Zinc is used in many areas. It determines the alloy character in brass and is an alloy companion in gunmetal and many aluminum and magnesium alloys.
The galvanizing of iron or steel parts, such as B. Ribbons and profiles. For belts, mostly in the continuous Sendzimir process . The galvanizing is carried out by dipping and guiding the individual parts to be galvanized - in this case by means of a hanger - or the rolled strips through a tub-shaped zinc bath, whereby a double protective layer is formed. A pure zinc coating is placed on a primarily occurring iron-zinc compound. Both together provide, provided that the coating does not have any open interfaces, lasting protection against corrosion caused by humidity, i.e. rusting or rusting through.
Fine zinc alloys with an aluminum content of mostly 4% are processed for a wide variety of purposes, especially in die casting, where "resource-efficient casting technology" is increasingly replacing parts previously cast in aluminum. World production amounted to 2 million t in 2014, of which 70,000 t or 4% came from Germany.
Fine zinc is also processed into semi-finished products.
Zinc white , originally an undesirable by-product in the production and processing of brass alloys, is nowadays obtained from raw zinc using various processes, or more than 70% of the consumption estimated at> 250,000 t / a when recycling products containing zinc. It is not only traditionally used for pigments and ceramic products, but also for rubber, glass, pharmaceuticals and electronics, provided that it is not returned to the fine zinc production cycle.
The corrosion resistance of zinc coatings on iron and thus its protection against rust results in a constant high demand from the galvanizing plants. A distinction is made between electrolytic galvanizing (with a shorter shelf life) and hot-dip galvanizing , in which the parts to be galvanized are passed through an immersion bath made of molten fine zinc.
nickel
Nickel has established its own industry (for example, the Russian company Norilsk Nikel ). Regardless of its historical use, which was proven for China even before the turn of the century, it did not regain importance until the 19th century.
For nickel recovery serve mainly gravels, so sulfide ic ores are roasted in a first stage and melted in a reverberatory furnace ( "matte"). Freed from copper and iron, it becomes "fine stone" and this is either electrolytically refined ( pure nickel ) or using the moon process ( carbonyl nickel) to make pure nickel.
Nickel is used for high-quality nickel-based cast alloys , but mainly as an alloying element that determines properties (e.g. for chromium-nickel steels) and as a component of bronzes (it shares its role as an alloy companion here with tin).
Nickel is also found in brass and high-strength aluminum alloys. As a coating for cast parts, it guarantees corrosion protection (nickel plating) and, last but not least, it determines the "silver color" of coins , cutlery and household appliances with a share of around 25% . Nickel is not toxic, but its aerosols can be hazardous. Long-term skin contact, for example with glasses frames or jewelry (both manufactured using the die-casting process), can lead to nickel eczema ( nickel dross ).
lead
With a melting point of only 327 ° C, lead is easy to process and can easily be produced in metallic form from lead luster (PbS) by means of oxidation and subsequent reduction . As pure lead, it is mainly processed in the form of soft, flexible material rolled into sheet metal (lead sheathing of cables, roof seals). As a lead pipe, with an alloy of hardening antimony , it is only permitted for sewage pipes. Much used it as a battery lead for starter batteries , as lead shots , as lead die-cast alloy and lead-bronze bearing . For decades, lead has been extremely important as protection against gamma radiation . When handling radioactive material , a lead cover (the radiologist's lead apron ) is essential.
In wrought brass alloys, lead (up to 3%) ensures good machining properties . Lead is desirable as an alloy companion in copper alloys, although it tends to segregate due to its density .
The processing of waste lead ( accumulators ) is carried out in specialized smelters, among other things because apart from problematic sulfuric acid residues in the batteries, the lead vapors that set in above the melting point (vapor pressure) are very toxic (see recycling metallurgy ).
Metals used in industry
lithium
The light metal lithium has a density of only 0.534 g · cm −3 . It ranks 27th on the element's frequency list. The estimated world supply is 2.2 million t. Lithium can be obtained from lithium ores by means of fused-salt electrolysis ( e.g. from amblygonite with a lithium oxide content of up to 9%, which is processed as ore concentrate). Spodumene is used in particular for the production of lithium carbonate ; other minable ores are petalite and lepidolite . Lithium is also obtained through the evaporation of highly saline water ( Dead Sea ). Extraction from seawater (content 0.17 ppm Li) has so far been considered uneconomical.
At the beginning of the 21st century it has not yet been decided whether, according to his presentation, metallic lithium will be used by means of a process run via lithium carbonate, preferably as a component for the production of particularly light and corrosion-resistant alloys based on aluminum or magnesium, or an alloy of both, including itself becomes the base metal of super light alloys, or is used in high-performance accumulators ( lithium-ion accumulator ). According to experience as a battery for mobile telephony, they are seen as the next possible solution for electrically powered road vehicles. The resulting strongly increasing demand can be satisfied for what is known about deposits developed and to be developed worldwide, including in Europe (Noric Alps). On the other hand, it is less favorable that the efforts to promote electromobility are accompanied by an increased demand for cobalt , whose regionally limited extraction, however, remains susceptible to supply bottlenecks. In nuclear technology, the use of lithium has been considered indispensable for the development of a fusion reactor since its contribution to the development of the "hydrogen bomb".
Among the many other uses of lithium or its compounds, the additive is one of up to 5% lithium fluoride in the fused salt electrolysis of aluminum, the use of lithium copper as a deoxidizing agent for heavy metals ( melt treatment ), the addition of lithium chloride and lithium fluoride to aids in welding and brazing of Light metals, also in the form of its stearates in lubricants and as citrates , carbonates and sulfates in pharmacology.
With regard to the range of uses of lithium and its compounds on the one hand, and its not unlimited availability on the other, recycling, especially from batteries and accumulators, is becoming increasingly important.
beryllium
Beryllium (density 1.85 g cm −3 ) is one of the light metals. It is obtained mainly from beryl , an aluminum beryllium silicate. Although classified as toxic (liver damaging, berylliosis ), it is used in a variety of ways. In the case of magnesium casting, an addition of 0.001% to the alloy or to the molding sand reduces the risk of oxidation; as beryllium copper with a beryllium content of 5%, it is used to deoxidize highly conductive copper. Made of a copper-beryllium cast alloy with max. 3% beryllium and 0.5% cobalt can be used to produce spark-free tools, an important property in coal mining.
According to current research, beryllium has great potential for the desired nuclear fusion in fusion reactors, as it can both produce the fuel tritium and is also suitable for cladding the plasma vessel, which is exposed to a temperature of 100 million degrees.
tin
Tin (density 7.29 g · cm −3 ), Latin for "stannum", is obtained from oxidic ores (tin stone, cassiterite) that are smelted in a reducing manner. Until the invention of porcelain, pewter-based eating and drinking vessels ("crockery pewter") were made. A recent development is " Britanniametall ", a Sn90Sb8Cu alloy that is processed into decorative objects (plates, cups). A special area are pewter figures made of a eutectically solidifying alloy Sn63Pb37, the production of which has been handed down over centuries ( pewter foundry ). The term tinfoil for thinly rolled tin foils goes back directly to the Latin “stannum” for tin and is colloquially used on metal foils. Their application forms, which have been well known for a long time, include bottle caps and the tinsel that decorates the Christmas tree .
Today, tin is mainly processed in the die casting process; the alloys used for this are similar to those for bearing metals based on tin. According to DIN 1703, these are standardized alloys with approx. 80% tin and additions of antimony, copper and lead; an outdated term is “white metal”, today “tin bearing metals” have taken its place. Tin is the naming alloying element of all tin bronzes , and also a component of gunmetal that is required for the required alloy properties . Alloyed with lead and curing antimony found it to be a " hot type " in the now historic now writing metals .
Sheet iron , rolled out to fractions of a millimeter and tinned on one side, is called tinplate . The main area of application are cans for permanent tins. One of the world's top German producers reports an annual production of 1.5 million t for 2007/2008.
Tin is also the main component of all soft solders with a melting point of <450 ° C.
titanium
Titan is because of its relatively low density of 4.5 g · cm -3 and thus only half the weight of steel but equally good strength values, also non-magnetic, seawater resistant and resistant to corrosion, especially in the military as early as the first half of the 20th century Sector increasingly used: as an alloy companion for special steels, as a structure-stabilizing additive in cast iron grades, as an important additive to high-strength, seawater-resistant aluminum alloys in shipbuilding.
The development of titanium alloys begins around 1940, a prerequisite for the construction of jet engines for the aerospace industry. In particular, titanium aluminide materials with additions of niobium, boron and molybdenum are suitable for operating temperatures of aircraft turbines, according to the specialist press.
In medical technology, titanium is used for artificial joints ( endoprostheses , implants ).
In the investment casting process ( lost wax process ), not only small to the smallest precision parts are produced from titanium alloys. A patented process also allows the production of larger parts, as required by motorsport. Model production by means of rapid prototyping in laser sintering technology is quick and also enables short-term changes.
AlTi, AlTiC and AlTiB master alloys are used to influence the structure of wrought aluminum and cast alloys (grain refinement).
New titanium deposits are being developed in anticipation of a demand that will increase to more than 100,000 t annually, with titanium being produced in association with cobalt and nickel.
cobalt
Cobalt , a silvery metal (density 8.9 g · cm −3 ) has been known since the 15th century. The targeted mining of cobalt ores began when, towards the end of the 16th century, something was rediscovered by chance, which was already known to the ancient Egyptians: that cobalt colors glass rivers blue. For the iron industry, cobalt is an additive to high-quality steels. Cobalt is gaining new importance due to its suitability as an electrode material in the manufacture of lithium-ion batteries . World production is estimated at 60,000 t in 2007, two thirds of which come from the Congo ( Katanga ) and Zambia . The manganese nodules in the deep sea offer a very large reserve with a cobalt content of approx. 1%.
Refractory metals
molybdenum
In terms of volume consumption, this element is at the top of the so-called "refractory metals". This group also includes tungsten, vanadium, niobium and tantalum. The name is due to the high melting point of these elements, which is one reason why they could be produced in the necessary purity for the first time around the middle of the 20th century using modern melting techniques such as the vacuum melting process, a prerequisite for the specific uses intended for them beyond steel refinement .
More than 50% of the world production of almost 200,000 t p. a. (2008) of molybdenum (density 10.2) are used as a steel refiner and for cast iron with increasing consumption rates. The electrical industry needs it for catalysts, and pigment manufacturers also use it. It is widely obtained from sulphidic molybdenum luster.
Vanadium, tungsten, tantalum and niobium are obtained from oxidic ores such as vanadinite, wolframite, tantalite, niobite (also known as mixed ore with tantalite as columbite after the main locations) for a steadily increasing demand in microelectronics. 90% of the world's demand for niobium comes from Brazil.
A by-product of molybdenum extraction is the rare noble metal rhenium (density 21.04 g · cm −3 ).
tungsten
The refractory metal tungsten (density 19.3 g · cm −3 ) is obtained from the mining of scheelite and wolframite ores. It is an alloying element for tool steels, for example for twist drills. When the - powder metallurgy - processing of tungsten with its extremely high melting point of 3387 ° C into fine wires succeeded, it was able to replace osmium or tantalum as material for filaments. This made classic lightbulbs relatively durable and cheap to buy.
Also, halogen lamps and more efficient and longer-lasting bulbs fluorescent and compact fluorescent lamps ( energy saving lamp ) have yet to tungsten filament - the latter being the spiral require only before the start of preheating. Only light-emitting diodes can do without. In X-ray tubes , tungsten is used to heat the cathode (filament), but mainly as an anode material.
The compound tungsten carbide , chemically WC, is one of the hardest materials with a Mohs hardness of 9.5 and is therefore used as a coating for cutting tools or directly as a cutting material in hard metals . Tungsten becomes brittle under special loads (in power plants). Promising investigations into reinforcement by embedded tungsten fibers are in progress.
selenium
Selenium named after the Greek word "Selene" for the moon, closely related to tellurium ("earth"), belongs to the VI. Main group of the periodic table of the elements. The world extraction of 2000 t in 2007 - mainly from the anode sludge from copper electrolysis - is used, among other things, for the production of colored glasses, as semiconductors in xerography, as a component of lubricants and pharmaceuticals.
silver
In 2007, 30% of silver was extracted in silver mines, a third of the demand is a by-product of lead and zinc extraction, 27% of copper refining and another 10% of gold extraction.
After the almost complete demonetization , its industrial use predominates, which is based on the thermal and electrical conductivity that surpasses all other metals and is stated for 2007 as 55% of the total requirement. With a density of 10.5 g · cm −3 and a melting point of 960 ° C, silver is very versatile. After its “bactericidal” effect, similar to brass, was discovered in the 19th century, silver is not only processed into everyday objects; the silver coating of handles, handles and other frequently touched metal parts in public spaces is becoming a silver consumer. For the same reason it is used for surgical instruments as well as for apparatus in the food industry. Silver consumers can also be found in electronics and electrical engineering (silver wire). Silver-zinc batteries are under development, the energy density should be 40% higher than that of lithium-ion batteries (see also under "Recycling").
According to reports in the business and trade press, jewelry and cutlery still take up 25% of silver consumption. Jewelry and silver tableware are traditionally made partly by hand (silversmith), partly industrially (foundries specializing in silver).
The use in photo technology has decreased to 15%. 5% of the silver supply is minted into commemorative coins and medals.
Up to 0.25% silver is an alloy component of wrought copper alloys known as "silver bronze". Silver brazing alloys based on copper or manganese can contain up to 87% silver. High-strength aluminum alloys are also manufactured with the addition of silver.
In the history of coinage, silver has long played an important role (see silver currency ). The owners of the coin shelf , now exclusively the states and their national banks , mint silver coins only on special occasions and are happy to use rising silver prices as an opportunity to reduce the silver content of the coins.
uranium
Uranium is a poisonous, radioactive (radiating) heavy metal with a very high density of 19.1 g · cm −3 that belongs to the group of actinides . Discoveredby Martin Klaproth towards the end of the 18th centuryand referred to as pitchblende , it has been mined ever since. German deposits of uranium ore were exploited to a considerable extent until 1990 (Schlema-Alberoda).
In 1898, AH Becquerel observed the radiation from the pitchblende, but without recognizing its harmful effects on human tissue. Pierre and Marie Curie then isolated the highly radiating elements polonium and radium it contained . It is not the small proportions of these two elements in uranium that make it a radioactive alpha emitter , but the content of the isotopes 234, 235 and 238.
All radioactive elements, especially the transuranic elements discovered after 1945, such as fermium, berkelium, Einsteinium, with atomic numbers from 93 onwards, are more or less unstable. Some actinides disintegrate after seconds, others only after millions of years, the yardstick is the so - called half - life . For uranium-238 4.5 billion years are given, for the isotope 235 it is 704 million years and for "weapons-grade" plutonium "only" 24000 years. The final stage of this atomic decay , which also allows the age of elements to be determined, is always lead.
The annual uranium production worldwide for 2007 is given as 40,000 t, the consumption as 60,000 t. The gap is closed by the liquidation of stocks that were hoarded for military reasons. Views on the global supply of uranium ore are debatable, 10% of the reserves are believed to be in Western Australia but have yet to be developed. With the technology of the breeder reactor , the world's stocks could be put to more sustainable use.
The further processing of the extracted uranium ore is based on chemical-metallurgical principles of leaching , precipitation and filtration with the intermediate product yellowcake . The metallic uranium obtained is still radioactive and can only be used to a limited extent without further treatment. Isolated radium (also the isotopes) was used earlier in radiation medicine.
Depleted (that is, in its non- fissile form), uranium is used very differently. Due to its hardness, it is used in the armaments industry for armor plates as well as for armor-piercing ammunition. It is also found as a radiation protection material, as a steel additive and in the aviation industry.
On the other hand, uranium is called enriched when the proportion of isotope 235 has been increased from natural 0.711% to at least 3.5% in a complex process (centrifuge technology). This makes it the raw material for generating nuclear energy in the nuclear power plant . Plutonium is produced there as a by-product, it can be reprocessed into fuel elements or used to manufacture nuclear explosive devices.
Pure metals
A range of metals that are used with the highest purity of> 99.9999% and in extremely thin layers as compound semiconductors in electronics and power generation (e.g. for solar cells ). They consist of compounds of aluminum, gallium and indium (3rd main group) with nitrogen, phosphorus, arsenic and antimony (5th main group of the periodic table). Germanium, for which China covers 75% of the demand, is necessary for fiberglass cables.
Technology metals
This term is increasingly used for elements that are used in the area of so-called "high technology" (high-tech), insofar as a priori encompasses the "rare earth metals". However, it is also used for other classifications, such as “precious metals”, “special metals” and even “industrial metals” and “industrially used metals”, provided that elements that can be assigned there are used in the high-tech area.
Precious metals
The extraction of gold , since the year 600 BC. First used as a minted means of payment ( gold stater ), it is first mentioned in historiography for the profitable mines of the mythical Queen of Sheba . In Germany she started with the discovery of river gold (Rheingold). According to a contemporary report from the 12th century, it was washed out of the river using the gold washing technique that is still used today .
Like copper, silver is one of the oldest metals used by humans. Starting with unminted silver, there was monetization , silver became a means of payment. Silver staters have been around since 600 BC. Known from Macedonia , China raised the cast silver tael to the standard.
In the 14th century, the mining and smelting of silver ore in the Muldenhütten in the Saxon Ore Mountains as well as the industrially operated silver mining in the Austrian Tyrol with its center in Schwaz , where 30 tons of silver were extracted annually in the 15th and 16th centuries, were economically important for Europe . These locations were favored by an abundant supply of wood as fuel and water power to operate the bellows. European silver mining only became less important when, in the 16th century, after the subjugation of Central American cultures, countless shiploads of gold and silver reached Europe. Between 1494 and 1850 some 4,700 tons of gold are said to have come from the Spanish possessions alone. The quantities of silver imported were so large that they allowed monetization. Sovereign mints minted silver thaler (including the Maria Theresa thaler ) as a silver currency . The issue of paper money to make it easier to deal with larger amounts of money was only possible because it could be exchanged for gold ( gold currency ) or silver at any time . Above all, the gold backing of a currency guaranteed the particular solidity of a state. During this time, the nation-state coins emerged as industrial operations.
During the First World War and in the years that followed, the large economies, overindebted due to warfare, had to give up , one after the other, the gold standard of their currency - i.e. the guarantee that paper money could be exchanged for gold at any time. Only the USA undertook again after the Second World War to exchange paper dollars for gold at any time, but had to give up this guarantee again in 1971. With the exception of special issues such as the Krugerrand , there were no more gold coins in circulation . In some countries (including Switzerland) silver coins were still in circulation; but these were withdrawn long before the end of the 20th century. Paper money and coins made of nickel or copper took the place of gold and silver, according to the economic axiom ( Gresham's law ): "Bad money displaces good money in circulation."
On the other hand, the need for hoarding on the part of governments and private investors has not only remained but has increased. In addition, there is a growing demand for precious metals for partly completely new industrial productions. Both ensure the operation of the gold mines and the further processing of the steelworks. For 2007 a world gold production of approx. 2500 t is assumed. Two thirds of this is processed into jewelry, which is made using the methods of classic semi-finished product manufacture (ingot casting and rolling). Only ten percent go into special mints of coinage metals, for which the blanks are first punched out of the gold sheets rolled to the appropriate thickness and then stamped with stamps and dies under high pressure. A few hundred tons go to the electrical industry, glass coating and dental technology.
For comparison, statistics for 1999 give a world silver production of 17,300 t. The electronics industry is processing increasing quantities.
The precious metals that are increasingly being used metallurgically in the 21st century in electronic communication (“mobile phones”, PC) include not only platinum , which has been known since the 19th century , valued higher than gold as a jewelery metal, valued in the course of technical developments for its catalytic properties. but with it the entire “group of platinum metals”, which also includes osmium , which has become important for incandescent filaments , as well as rhodium, ruthenium and iridium . According to recent reports in the business press (including Frankfurter Allgemeine Zeitung ), there are abundant deposits of all platinum metals in the Siberian Yenisei region , in which, for tectonic reasons - so the reports - almost all future-oriented raw materials (including natural gas and crude oil) are, so to speak, "bundled" can be found. In 2007, the same sources say this for the first time in the north polar region. At a depth of 4000 m, the problem of exploitation is no less than that of the long-known undersea manganese nodules.
However, this has been offset by a platinum production deficit since 2007, which is attributed to increasing demand in the fields of jewelry and catalytic converters. Rhodium , which is also used for catalysts and belongs to the group of platinum metals , is therefore increasingly in demand. Palladium, a related product, is finding growing interest as a substitute for platinum, a by-product in Russian nickel mines, little valued as a jewelry and coin metal, but ideally suited for catalysts.
Gold mines are now regarded as worthy of exploitation even if they contain only a few grams of gold per tonne of mined material. In mining operations (bottom depth 900 to 4000 m) South Africa achieves up to 20 g gold / ton in some cases. A common, environmentally harmful processing method is still the cyanide leaching of the gold-bearing ore. In 2007, regardless of the resulting environmental hazard, it is still operated in the “Red Mountain” district ( Roșia Montană ), which is located north of the Romanian / Transylvanian city of Alba Iulia and was already used by the Romans. For the next 20 years, at least one million ounces are to be extracted annually (as of 2007).
A deposit of approx. 550 t in the Chilean Andes (Pascua Lama) is to be newly developed.
Silver ores with a silver content of more than 50% are subjected to a wet amalgamation process after processing , but are also treated electrolytically - insofar as they are comparable to copper, which is related in many ways. In the case of poorer ores, where silver is often a by-product, the usual methods of roasting , leaching , chlorination and separation are used . Classic processes of separating silver from its companion lead are "Parkesians" and "Pattinsonians", the "Reichschaum" obtained in the process is followed by the driving work. With a world production of less than 20,000 t per year, silver and gold with a significant percentage also arise during the refining of copper ( see there ).
Refineries are versatile in recycling precious metals. In line with market requirements, they separate materials containing precious metals, whether solid or liquid, into their individual components. Electroplated gold coatings made of precious metal, as they are required for the upgrading of decorative objects, but much more often for contacts in electronic devices, lead to precious metal sludge that is worth refurbishing. The recovery of platinum and the separation of gold from accompanying silver are economically important. The pure metals produced in the cutting process are either processed by the companies themselves into intermediate and end products, from jewelry chains to gold solders, or they are sold to special consumers. Banks buy fine gold bars (24 carat ) and offer them as a store of value. Alloyed bars and semi-finished products (chains, wires, strips, sheets) are required by the jewelry industry, distributed as 14-carat gold with a gold content of 585 ‰.
A well-known German company in the precious metals sector mentions a sharp increase in “product sales” of 4.1 billion euros and a separately determined precious metal sales of 9.3 billion euros.
The value of the various precious metals achieved through recycling bears the costs of material recovery in all cases.
Alchemy, a digression
Alchemy , also alchemy, or (since it comes from Arabic) alchemy, began around 200 AD in Greek-speaking countries at the beginning of a serious preoccupation with the nature of chemical substances. Since important metallurgical techniques were already well developed at this time, alchemy is to be seen as an offshoot, not as the founder, of metallurgy. The four-element theory of Empedocles (fire, water, earth, air), as well as the Aristotelian theory of hylemorphism , the possible transformation of matter through the removal of ignoble properties, resulted in the search for the " philosopher's stone ", whose possession the transformation is ignoble Metals in gold should ensure. Gold was important to the rulers of the late Middle Ages and at the beginning of the new era, because it could fill war coffers that served to expand power. The historically best-known by-product of alchemical endeavors was not a new metal, but in 1708 the reinvention of the white hard-paste porcelain , known to the Chinese since 700 AD, by JF Böttger , the assistant to EW von Tschiernhaus who was originally employed as a gold maker . Already in the 16th century Paracelsus (1493–1541), in the 17th century R. Boyle (1627–1692) and in the 18th century AL de Lavoisier (1743–1794) transferred alchemy into scientific chemistry , from then on is gaining importance in the history of the development of metallurgy.
Recycling metallurgy
A “metal smelter” and a “ (rem) smelting plant ” originally differed very clearly from each other, but today this usage often blurs and is supported by technical developments.
Disambiguation
Iron, copper, zinc or other industrial metals are presented for the first time in a metalworks, while metal that has been released from previous use is refurbished or reworked in the remelting plant (remelting plant). From this difference - based on the terminology of examples from other areas - on the one hand the metal smelter becomes the “primary smelter”, which operates a “primary production”. Your products are "primary metal" and accordingly also "primary alloys".
The remelting smelter, on the other hand, becomes a “secondary smelter”, which operates a “secondary production” by using scrap metal and scrap. It produces "secondary metal" and from it also "secondary alloys". In this way, it fulfills the requirement for resource conservation. This is not a recently discovered procedure because scrap has always been remelted. The return to the metal cycle is now widely referred to as recycling . If the re-used metal has better properties than the old materials to be processed, the term “upcycling” is also used; the opposite of this would be “downcycling”, i.e. a reduction that cannot be ruled out when recycling plastics.
The reuse of scrap metals is not without problems, because it comes to alloying or contamination with a large number of metallic elements from the scrap, which would only be removed again with great effort. The properties of the raw metals produced in this way (here steel) are therefore different from those of primary metal. This applies to physical criteria (ductility, formability, toughness, etc.) as well as chemical criteria, which can be expressed in corrosion resistance.
Task and its economic and technical limits
“Sustainability” and “extended life cycle” are other time-related expressions for the economical use of valuable raw materials. For this purpose, an optimized product design that includes material consumption and life cycle is on a par with material recovery.
For a century, the beginning of economic recycling metallurgy has been the sorting of so-called collective scrap, i.e., from a metallurgical point of view, materials that are not homogeneous. What began with the sorting of scrap with acquired knowledge is now being perfected by “sensor-based sorting”. It should not be overlooked, however, that all metallic raw materials that go into end products are only released for recycling after their service life has expired, which is also increasingly being extended as a result of modern technologies. Only shown using the example of aluminum, this means that currently only just under a quarter of demand can be covered by recycling and this ratio will worsen in the near future.
copper
Two wars and increasing technical progress, as well as population growth in many countries and the resulting shortage of primary metal have not only pushed the secondary production forward in terms of quantity, but rather have made it qualitatively equivalent to the primary. This is particularly evident not only with aluminum, but also with copper, which can be recycled indefinitely, regardless of the type of waste and the copper content. The “energy turnaround” with the associated need for new line networks, as well as the accelerated “electromobility” will further increase the need for primary and recycled copper. The recycling rate for Europe is (2012) close to 45%, resp. real 2.25 million tons
From a “North German copper smelter”, a European group of works has emerged that operates both divisions and whose areas of responsibility are interlinked. Where there is no single-type separation of copper scrap and simple remelting, i.e. direct recycling, for which an annual capacity of 350,000 t was named in 2011 after extensions, steps will be taken in 2017 with options oriented towards ore processing and new technical methods. It is no longer normal for the accompanying elements of the scrap to be "blown", ie oxidized, by supplying oxygen in order to recover pure copper. in order to reduce the resulting oxides, if they are considered economically valuable, to become pure metals again, which can then be used like the primary metal. This process is now to be improved economically in order to also satisfy the increasing demand for copper companions (see :).
Electrolytic copper refining also produces anode sludge that also contains copper, silver and gold, as well as selenium and tellurium, which is referred to as "precious metal recovery". Since these sludges are a by-product, their processing can either be assigned to the primary process or to recycling.
aluminum
The importance of targeted research to optimize the recycling of aluminum results from the fact that in 2008, according to the General Association of the German Aluminum Industry (GDA), of a total of 1.3 million tons of aluminum produced in Germany, only 43% were primary aluminum and 750,900 t on recycled aluminum, both figures by no means reflecting domestic production, but being supported by significant imports. This development is triggered by the constantly rising electricity prices under the Renewable Energy Sources Act (EEG), which turn primary generation into phasing out production, especially in Germany. A German company that both produces and recycles primary metal and is also active in further processing names a total of 500,000 t for the 2011/12 financial year. Another German primary producer with an annual capacity of 115,000 t went bankrupt in 2013 and will shut down the electrolysis at the end of 2014.
Other aluminum producers, in particular international corporations active in primary production, have also been operating primary and secondary production in parallel for years and are thus looking for a certain level of cost compensation. This means that they not only extract raw aluminum from electrolysis, but also produce "secondary alloys" from their own return material and sorted waste and scrap and are gradually building their own network of recycling huts.
Beverage cans play a key role in the recycling of aluminum around the world. In the USA, significantly more than half of the cans dispensed came back in 2009; 57.4% or almost 750,000 tons of aluminum are reported. Each additional percent returned corresponds to approx. 15,000 t of additional remelted aluminum with only 5% of the energy consumption required for new metal. The can return rate is now 98%. In June 2014, the production of rolling ingots made exclusively from can scrap began in a plant built especially for this purpose in Central Germany. With an annual capacity of 400,000 t, which is processed further in the existing rolling mill, the aim is to become the world's largest recycling center for aluminum.
A task that includes the processing of can scrap is the processing of composite and organically contaminated scrap. The development towards exothermic, heat-generating processes instead of endothermic, heat-consuming processes would significantly improve the energy balance.
The majority of the secondary alloys today are qualitatively comparable to the primary alloys, the need for extraction energy, which has been reduced to one twentieth, is a factor that is being considered worldwide from the point of view of reduced energy consumption that is beneficial to the climate.
The relationship between the use of primary metal and recycled metal will shift even further for the time being, as even medium-sized aluminum foundries no longer put their production waste (mainly machining chips) on the market, but instead remelt it themselves. Chip melting furnaces with an innovative agitator and side channel pump enable economical recycling in-house even on this scale.
This applies to the recycling of process-related return material, but collective scrap, waste and metal-containing dross can also be melted down in the rotary drum furnace, with the addition of 50% of a salt mixture of alkali chlorides and fluorspar, which serves as a flux, regenerated back into secondary metal. With regard to the resulting low-metal, oxide-containing salt slags, their landfilling was ecologically controversial and also economically unsatisfactory. According to press releases from the market leader (ALSA), state-of-the-art technology is now a fully residue-free recycling process, the importance of which arises from the fact that every ton of secondary aluminum also produces 500 kg of salt slag. The world's largest salt slag processor, AGOR AG, with 450,000 tons per year, reports the worldwide annual accumulation of salt slag at 4.5 million tons.
In reversal of the original conditions, the former remelting smelters that have become “recyclers” can not only bring secondary alloys to the market today, but can also cast rolling ingots of the same quality as the primary production from pure wrought alloy waste. With purchased, primary pure aluminum, they even produce alloys that can be referred to as "primary alloys". German and Austrian remelting companies are particularly characterized by their activity in the development of a ductile AlMgSi casting alloy.
steel
In steel production, scrap is now mainly recycled in electric arc furnaces . The share of recycled steel in total crude steel production is given as 45% in 2011. A Siemens process promises a reduction in electricity consumption and a reduction in carbon dioxide emissions through the formation and use of automatically controlled foamy slag formation.
The recycling of the electric furnace dust has been a special task for over thirty years. The Wälz rotary kiln process, which has long been regarded as the achievable optimum, must be compared with the rotary hearth furnace.
The slag produced in steel production has always been subject to economic considerations simply because of the amount produced, whereby a distinction must be made between the utilization of the demetallized slag and the methods of demetallization. The dry processing of metal-containing slag is given preference. The fractions remaining after all metallic components have been separated off are widely used in the building materials industry.
Zinc, lead and other recyclable metals
Raw zinc is recovered from oxidic arc furnace dust, final sludge from hydrometallurgical processing, as well as all kinds of secondary materials containing zinc, such as galvanized scrap. Zinc scrap with the main component zinc can be reprocessed into a zinc alloy. If galvanized iron scrap is produced, its zinc coating is released by heating it beyond the evaporation temperature of the zinc (907 ° C). The evaporated zinc is precipitated as raw zinc by cooling, as in the dry way of zinc extraction. However, the zinc vapor can also become zinc oxide by blowing in oxygen and this can either serve as the basis for paints ( paints ) as “zinc gray” and “zinc white” , or it can be converted to zinc sulphate in the electrolysis process and leave it as fine zinc.
The "Ausmelt-Technology" not only allows zinc to be recovered from residues and waste that were previously barely recyclable, by evaporating them and then condensing the metals from the steam.
A branch of industry that is growing in parallel with the increasing globalization of motorization is the reprocessing of lead-acid batteries, which are used as starter batteries in automobiles to supply and store energy at the same time. "Old batteries" are therefore produced in large quantities and, due to international legislation in the country and in compliance with numerous requirements that protect people and the environment, must be subjected to the recycling process. It begins with a pretreatment by means of which the old batteries are freed from sulfur-containing residues and deposits, such as the recyclable lead sludge.
The melted down and refined old accumulators are converted into secondary lead, which in terms of quantity already exceeds the primary production. The high-quality polypropylene housings are shredded. The chips produced - with further PP additives - are mainly sent to the automotive industry, which uses them to make plastic parts. In the recycling process, when the number of old batteries containing sulfur increases, the sodium sulphate that is produced during desulphurisation using sodium salts and that is increasingly difficult to market is proving to be an obstacle. A modern method uses ammonium salts, and as an output stage of the refining as a fertilizer ( Fertilizer ) searched ammonium sulfate.
At the same time as the accumulation of old batteries and non-rechargeable batteries, the recovery of the zinc content is becoming increasingly important. The DK blast furnace process, which has already been introduced for the processing of old batteries, now enables zinc to be separated in the form of zinc concentrate from old batteries of all kinds via a downstream treatment of its exhaust gases.
In terms of quality, the old lead from the batteries is first turned into secondary or factory lead , which is further refined and re-alloyed using segregation technology or electrolysis. The (poisonous) colors of basic lead carbonate and lead tetraoxide can be obtained via black lead ( PbO ) . State-of-the-art technology now enables almost one hundred percent recyclability of all parts and contents of such batteries.
Lead and zinc are also found as oxides in the rolling slag from steelworks that absorb the flue dust . The possibility of chlorinating removal of the lead content from the oxides is being investigated.
Should the lithium-ion battery as a drive for road vehicles overcome its current disadvantage of insufficient power for long-distance travel, a completely different recycling task will arise, namely the recovery of lithium from lithium-containing battery slag.
The processing of so-called "electronic scrap", which not only records personal computers, but also portable telephones, electrically operated and controllable household appliances, radio and tube television receivers, and also device batteries because of their content, is more complex than the reconditioning of conventional vehicle batteries and the subject of constant research Lithium , nickel , cadmium , precious metals, and rare earth metals. Depending on the system, these batteries can have a metallic content of 35 to 85%. According to information published in the specialist and business press, the development of silver-zinc batteries is being promoted because, unlike lithium-ion batteries, they are complete and relatively easy to recycle.
The subject of current research is also the field of processing valuable scrap from refractory metals by means of oxidizing salt melts, especially of tungsten from the return of tungsten carbide, which has so far only been developed individually. A first hydrometallurgical plant with an annual capacity of 500 tons of molybdenum oxide went into operation in 2012 for the extraction of molybdenum oxide and some oxidic accompanying elements from used catalysts, such as those used in petrochemical processes.
The progressive development of flat screens that can be assigned to electronic waste and displace picture tubes initiates a special branch of research which deals with the recovery of indium in the form of an indium tin oxide.
This also applies to the continuously refined, practical investigations that have been carried out since 1990 on the “non-ferrous metal potential in bottom ashes of waste incineration plants”.
In the case of rare earth metals, a demand that increasingly exceeds the supply requires an increase in the previously low recycling rate. A research contract has even set itself the goal of recovering process water from the metal and mining industries.
Furnace technology

The furnace technology initially serves to fulfill all metallurgical tasks that arise in the course of the smelting of metallic raw materials in the context of thermal processes. It begins with the extraction of metal from ores. Sulphidic ores such as pyrite (pyrites) are treated with oxidizing agents (roasting). Oxidic ores such as hematite are melted by reducing and deoxidizing them. This is done through appropriate additions and reducing (air deficit) flame or furnace guidance. This is followed by further processing of the extracted metals. It starts with the standardization of batches produced discontinuously in the mixer. This is followed by refining and alloying, casting (holding or casting furnace) and heat treatment, which is the after-treatment of the cast depending on the alloy and type of casting. The latter is carried out with the help of pusher furnaces, tempering furnaces (block preheating ), annealing furnaces (stress relief annealing , artificial aging, austenitizing cast steel) and tempering furnaces (decarburizing cast part hardening in hot carbon).
Historically, this development started only with the open hearth, which lets liquid metal escape from a mixture of ore and fuel. This is followed by the closed hearth with a natural draft or with a higher temperature bringing air supply by means of bellows or blowpipe (pictorial representations from ancient Egyptian times). Already around 1500 BC It is reported from the Egyptian city of Thebes about large two-stroke (blowing - sucking) leather bellows operated with human strength as an aid in melting metal.
It continues with the prehistoric low-shaft furnace , which, with ever better blower wind feed to the high-shaft furnace ( blast furnace ), has an ever-increasing frame diameter (11 m in the 60 m high furnace B from Salzgitter Flachstahl GmbH) and the resulting charge quantities of up to ten thousand tons further developed. The limit of economic efficiency is now considered to have been reached and technology is increasingly turning to the Siemens-Martin furnace and electric furnaces, especially since they offer the possibility of producing steel not only from pig iron, but also from scrap. You regenerate them at the same time (see also recycling metallurgy ) and use the oxygen from the rust components of the scrap for “freshening”, i.e. the combustion of the carbon (rust as Fe 2 O 3 contains oxygen and thus replaces the blower air). The electric low- shaft furnace, designed as an electric arc furnace , supplies electric pig iron from ore pellets and carbon as a reducing addition in the direct reduction process. The electric arc furnace has also proven itself when recycling steel scrap to crude steel under a foamed slag.
The cupola furnace (derived from the Latin cupola, dome) is derived from the high shaft furnace as a foundry shaft furnace for the production of cast iron ( gray cast iron ). The fuel-heated hot-blast cupola represents a sideline because, as a “small high-shaft furnace”, it can satisfy the needs of iron foundries for a quick change between the types of cast iron to be processed. By means of an attached ORC system ( Organic Rankine Cycle ), the high-energy exhaust gases from the furnace, etc. a. to generate electricity.
All the systems mentioned - whether hearth, low-shaft or high-shaft furnace - have in common that the melt material, slag-forming agent ( limestone ) and fuel are in direct contact. A further development leads to furnaces in which a hot flame, which can be set to oxidize or reduce ( flame furnace ), brushes over the fuel-free melting material or no flame at all, but only hot combustion gases act on it. Other systems use heat radiated from the furnace ceiling (also through heating resistors embedded in this ) to heat the melted material ("ceiling radiant heating"). In this case, the furnace space is a closed, fixed tub (tub furnace ) or a rotatable cylinder, which is also known as a drum furnace due to its shape, with a front loading and unloading opening. In a shortened form, it is also used as a short drum furnace. A development step that was carried out very early on was to direct the hot combustion gases through a recuperator ( heat exchanger ) that preheats the fan air instead of outside ; Examples are the cowper -called wind heaters in blast furnaces and the Siemens-Martin furnace with Martin system. The preheating of the combustion air using waste heat, which was first introduced there on a technical scale, has long been considered state of the art. The exhaust gas combustion as an additional heat source and the optimized, heat-retaining insulation of the melting tank are further steps to improve the efficiency of the furnace. A furnace manufacturer states an achievable increase in output of 20-30% with the same energy consumption.
The representation of the "furnace technology" differentiates between fuel-heated furnaces (wood, coal / coke, oil, gas) and electrically heated furnaces, such as resistance furnaces equipped with heat conductor elements, induction furnaces with and without channels, with mains (NF) or medium frequency (MF) operated, or electric arc furnaces (direct or indirect heating) with graphite electrode. The capacity of the different systems is adapted to the production task.

Environmental protection requirements favor the electrically heated ovens. In modern electric furnaces, the melt is either inductively heated only in a certain area of the furnace - the "channel" - or the melt itself becomes a secondary coil, which is also inductively heated by an external, widespread low-frequency (LF) primary circuit. Induction furnaces of this type can be used as melting, storage or holding furnaces. The furnace , which works with direct current , is now considered to be the latest state of the art in steel production . The development of heat conductor alloys and heat conductors made of silicon carbide , including molybdenum disulphide , as a third variant of electrical heating, has favored the development from small to medium-sized resistance-heated crucible furnaces to large-capacity furnaces for melting and keeping aluminum warm, especially when recycling uniform and "clean" materials.
In the case of fuel-heated stoves, the burner technology was further developed for the same reasons, namely better fuel efficiency and a reduction in the amount of exhaust gas. Instead of three-quarters of the air, which consists of nitrogen that is useless in the process, either oxygen is fed exclusively to the burner or this is also fed into the burner to improve the furnace performance.
For smaller amounts of metal (up to 750 kg), fuel- heated or resistance- heated crucible furnaces with lids are still widely used in the manufacture of castings. Heating elements inside the furnace, (heating) coils protected by ceramic sheathing, which are inserted into the furnace walls and surround the crucible, provide the heat required for melting and keeping warm.
In such crucible furnaces, exclusively hand-made, "Hessian" crucibles have been used as melting vessels for a very long time, which were originally even shaped as a three-sided prism with three pouring openings until they were replaced by those in the form of a truncated cone. The crucible material consisted of Großalmer or clay mixed with quartz sand. This ensured fire resistance, but the very rough interior of the crucible was disadvantageous because of the metal deposits that it caused. With an addition of high-quality Hauzenberg graphite , the fire resistance was further improved, the inside of the crucible was smoothed and the historical “Passau crucible”, which always contained graphite, was replaced by using only Großalmer or clay mixed with graphite. Around the middle of the 20th century, isostatically pressed silicon carbide masses proved to be even more durable and also saved the previous manual labor on the turntable, known as “splashing”.
When magnesium melts, there is a special feature: Due to the oxidative reaction with iron are sized , ie with a silicate interior painting provided iron crucible admitted.
A special feature are the retorts made from clay in which zinc is extracted.
Today's state of the art is provided by the larger non-ferrous metal foundries. The metal quantities you need in two to three-digit tons per day are held ready as liquid metal by an in-house melting or remelting unit upstream of the casting or ladle furnaces and delivered on demand to the manually or automatically operated ladle and holding furnaces using a transport pan. When loaded in this way, it doesn't always have to be crucible furnaces; crucible-free systems are also used. If a company decides on a central melting plant with regard to the quantities that arise, it can choose a (rotary) drum furnace, a low-shaft furnace with a smelting bridge and a sufficiently large tank, or an induction furnace that has a needs-based hourly capacity of liquid metal (3 t is for example for Aluminum foundries a common size).
As far as the furnaces are concerned, the manufacturers of alloys hardly differentiate between the primary producers as those who themselves obtain raw aluminum electrolytically and the secondary producers, which are called remelting smelters or works (see also above). Both use mixers to compensate for batch differences (with a capacity of up to 30 t), which allow the necessary refining and alloying. The liquid metal is then either passed on to a connected foundry (cast-house) or in a molten state, thus saving energy and thus avoiding unnecessary emissions of air pollutants, by special vehicles to casting foundries. An additional simplification results from using the transport ladle in the supplied foundry directly as a casting or ladle furnace and exchanging it for a full ladle after it has been emptied. A separate melting plant, which always has to observe environmental protection regulations, is largely not necessary for the operation, the energy saving is quite considerable in the environmental sense, since the remelting necessary after an intermediate solidification is not necessary. Further cost savings result from the fact that a company exclusively processing liquid metal no longer has to comply with the requirements applicable to smelting companies.
A special feature characterizes the melting systems intended for recycling: After sorting and processing, for example by means of magnetic separators , it is necessary to melt down the scrap that comes from different sources, either bare, but often oily, or varnished scrap. According to the current state of the art, the melting material is passed over a melting bridge upstream of the melting furnace, on which all higher melting points, mainly iron parts, remain and can be removed before the melt is contaminated, for example by excessive iron content. The latest processes provide for multi-chamber furnaces that turn all the organic-based, energy-containing adhesions of the scrap into smoldering gases, the combustion of which contributes to the process heat required for melting down.
The melts, including those made from recycled material, are subject to a treatment when remelting, taking into account the existing furnace technology, comparable to that in primary production, whereby only the alloying can often be limited to mere corrections in view of the already existing alloying elements that are worth preserving (see also " Recycling Metallurgy ").
Significance of metallurgy as an industry
Since metals are always extracted for the purpose of further processing, even if they were and still are temporarily, like precious metals, but also copper and tin , the economic importance of metallurgy is growing steadily. The reasons are new tasks, such as in electronics, as well as a demand for metallurgical products that is linked to population growth and level of education.
Some figures, arranged in tabular form, refer to a reference year and show metallurgy as an important economic complex. In addition, there are figures for some areas that relate to the most recently announced status. There is also a current press release according to which the non-ferrous metal industry in Germany produced and processed 8 million tons in 2014.
metal | World annual production 2006 (in million t) |
Remarks | DIW forecast 2015 [outdated] (in million t) |
---|---|---|---|
Steel (updated information) | for 2012: 1548 | European steel production 2012: 169.4 million t. | 1366 t. |
copper | 15th | Consumption BRD 1.7 million t | > 22 |
zinc | 7th | Consumption BRD 2000 724,000 t, with 367,000 t own generation | |
lead | 6-7 | BRD 2000 395,000 t, of which 100,000 t from battery recycling | |
tin | 0.25 | ||
nickel | 1.3 | to SUCDEN (UK) | |
uranium | 0.03 | ||
platinum | 6.35 million ounces | ||
aluminum | > 20 | 41 million t (possibly primary aluminum + recycling) according to | 33 |
magnesium | 0.7 |
If metallurgy is addressed as an economic factor, its benefit for the raw material countries comes first, especially since the tendency to process the ores on site and also to set up at least primary stages of processing (steel works) is increasing and creating jobs in the country.
In operations close to end use, many metal-producing and metalworking processes are increasingly tending towards automation and the use of robots . This means that the total number of employees does not increase at the same time as the growth in production, but rather stagnates and can tend to decline slightly. The labor productivity is increased thereby, the unit labor costs are declining. Wage increases made possible by this not only increase the purchasing power of the recipients, the state also receives its share from increased tax revenue.
Some figures try to give an impression of the production performance in the metallurgical sector:
steel
The crude steel production of then still 25 EU countries was given for 2006 with 198 million tons, that was 15.9% of the world production of 1242 million tons. The German share within the EU 25 was 23.6%, making it 6th among the world's steel-producing countries with 46.7 million t. The largest German producer at the time was ThyssenKrupp with 17 million tons, including the loss-making site in Brazil, where a second blast furnace for crude steel slabs was started up at the end of 2010, which, after being sold, is now being processed in US plants in Alabama (USA), but also in Duisburg become. European growth in the longer term is seen at just one percent per year. In the opinion of the German steel industry, stronger growth is not only inhibiting production in China, which accounts for two thirds of the global overproduction of rolled steel (FAZ report of November 8, 2016).
The steel production of China was given in 2012 with 716.5 million tons, which accounts for 46.3% of the world production. The EU share of this is slightly down to 169.4 million t (10.9%). The same applies to Germany with a share of 3.7%.
According to earlier information, 31.07 million t of pig iron were produced in Germany in 2007, adding the use of scrap that resulted in 48.55 million t of crude steel. Of this, 45.5 million t were continuously cast for hot rolling into flat and long steels, including 14.6 million t of stainless steel. The 2008/2009 economic crisis brought about a significant decline. For 2011, the German steel industry reported an increase in crude steel production to 44.3 million tons, which meant 7th place in world steel production (Japan took second place with 107.6 million tons). A crude steel production of 42.5 million tons is expected for 2015. The decrease compared to 2011 is due to the reduction in capacity. A moderate upward development in the course of 2016 gives reason to hope for stabilization (FAZ of September 14, 2016 /). Two factors are supporting this. China wants to reduce its overproduction and the development of high-strength lightweight steels is increasing consumption. (Press report FAZ of September 21, 2016, p. V6 “Steel in high performance mode”).
molding
The world cast production (only mold casting) is given for 2016 in all its divisions with 104.379 million t. The German foundries reported a production of 5.168 million t from the companies recorded in 2016 and thus occupied 4th place in the world rankings based on the production quantities. China remains the front runner with 47.2 million t, which includes 7.95 million t of metal casting, a quantity that is well above the total German cast production.
aluminum
For castings made of aluminum and magnesium, which continues to be indispensable for the automotive industry in particular, global production of 18,195 million t is stated for 2016. Germany's share is around 1,114 million t.
Germany's own production of aluminum in 2011 amounted to 1.067 million t of raw aluminum. Germany's demand for aluminum, which far exceeds these quantities - 2.44 million t of semi-finished products were manufactured in 2011 alone and an additional 993.9 thousand t of cast aluminum for 2014 - is covered by imports and the high recycling rate.
According to a press release (HYDRO in FAZ of August 22, 2016), Germany now recycles 99% of all beverage cans.
Global overcapacity continues to be reported in the 2014 financial year. South America is affected by a series of hut closings (ALUMAR, ALBRAS). The reason for this is the expansion of aluminum production, which has been operated by state corporations in Russia (RUSAL), China (CHALCO) and the Arab Emirates (DUBAL, ALBA) over the past decade. China alone accounted for 60% of the world's raw aluminum production in 2014/15. Against this background, smaller plants around the world that also still work with the outdated Söderberg technology will be closed. Modern systems consume significantly less electricity. Further closures are also reported for 2016 (e.g. at ALCOA, according to FAZ article from January 9, 2016, p. 23). Persistent overcapacities and price-depressing exports from China are given as reasons.
In the case of non-ferrous metals in particular, the responsible associations warn of “the economic consequences of forced climate policy and a break in the value chain in the metal industry due to a lack of primary and secondary raw materials”. World production continues to show an upward trend. The London Metal Exchange (LME) explains that the world's bauxite reserves will extend well into the 21st century. A report on the global capacities for the production of alumina, which is not the same as the actual production, comes to a total of 95 million t for 2007/2008.
Availability of rare earth metals
The progressively increasing demand for “rare earths”, which are more correctly referred to as “rare earth metals”, has made them - significantly more and more since 2007 - an economic factor in a key position. In the periodic table they form the long neglected group of lanthanides . Since 2000, they have been increasingly indispensable for modern communication technology, lighting and electric mobility. For some elements, such as lanthanum and europium , the strong demand has already led to the market prices multiplying. Consuming industries are particularly concerned about China's position, which continues to be regarded as almost monopoly. The situation is somewhat relaxed by statements from Australian authorities that refer to large deposits on the continent and at least promise to supply Japan with its needs. The global demand in 2014 is estimated by Australia at 190,000 t and is undercutting at 20,000 t, although China will bring 114,000 t and Australia 22,000 t into the market only with the development of the Mount Weld mine. Canada also wants to extract up to 5000 t annually.
Copper economy
In the copper sector, Germany's largest copper smelter in 2005/2006 with 3200 employees produced 551,000 t of cathode copper, 423,000 t of copper wire, 450,000 t of semi-finished products and a further 67,000 t for affiliated companies. In the year under review, 985 t of silver and 35 t of gold were extracted as by-products of the smelter, which is dependent on secure energy supplies ( refining ).
This must be contrasted with the fact that in Mongolia, with 2.5 million inhabitants on four times the area of Germany, a single mine not far from Ulan Bator could have an annual capacity of 440,000 t of copper and 320,000 ounces of gold.
Synopsis
At the end of 2006, the German non-ferrous metal industry reported over 110,000 employees in 632 association companies, which achieved a total turnover of 44 billion euros. With a German gross domestic product of more than two trillion euros, the figures mentioned are respectable, but they could lead to an underestimation of the economic importance of metallurgy (metal industry). Some figures from Austria seem realistic: If the production values of metal extraction and manufacture, mechanical engineering , automotive engineering and manufacture of metal products are summarized, the Austrian metal industry achieved a share of 42% in the country's material goods production in 2006. A similar value can apply to Germany. In addition, a figure for the year 2014, which indicates a produced and processed quantity of 8 million tons for the German non-ferrous metal industry.
Supporting Sciences and Techniques
Modern metallurgy would be inconceivable without chemistry , in contrast to the historical beginnings, where the “ trial and error ” method was often used. It is not only thanks to the efforts of chemists such as de Lavoisier , Wöhler or Berzelius that metallurgy was able to develop into a science . Analytical chemistry, with its increasingly precise methods since the beginning of the 19th century , came to their aid . The laboratories continued to work with labor-intensive and time-consuming wet analysis (dissolving, electrolyzing or precipitating, filtering, drying, weighing) until around the middle of the 20th century this was replaced by spectrometry , flame photometry and process gas chromatography , modern analytical methods that the practiced metallurgy enable a quick assessment of the input material as well as the output. The results of the analysis together with the properties of metals and their alloys as wrought and cast materials, which are physically determined by metallurgy, become the starting point for further auxiliary sciences, among which materials science and deposit science are to be emphasized.
Spectrometry particularly supports secondary metallurgy. The composition of a liquid metal sample is displayed within a few seconds for up to 25 elements. So-called interfering elements such as bismuth in brass , phosphorus in iron or antimony in aluminum are detected, even in the low ppm range. Non-ferrous metal scrap can be scanned and pre-sorted with hand-held devices (spark emission spectrometer ).
As far as the importance of metallurgical research is concerned, especially the implementation of results in practice, ferrous metallurgy is leading in many ways, both for primary production and recycling, as well as for the very innovative foundry industry . Foundry research as an independent, scientific activity benefits all foundries.
The provision of melt “ just in time ” and the associated automation of melting processes, the “robotization” of casting processes, are all inconceivable without controlling electronics , which is why it is an auxiliary science of metallurgy.
With special reference to the foundry industry, mold production, melt treatment by removing undesired and adding desirable properties, and influencing the solidification of the melts in the casting mold, deserve the designation auxiliary science. Another example is the model making technique using erosion , milling and CNC techniques, which make it possible to go directly from the drawing to models that are milled or sprayed in layers by powder metallurgy or molds that can already be cast for prototypes, which are then particularly advantageous for small series. The knowledge that can be gained in this way with little expenditure of time shortens the span from the drawing to the production of the final permanent form and the start of large-scale production.
Another auxiliary industry has developed for parts made of non-ferrous alloys using the die-casting process in permanent molds: Tool steels that are optimized in terms of their strength properties are required , which enable a number of casts in the five-digit range. During the process, the molds are not only exposed to the direct attack of the supplied liquid metal, but also experience a cycle-controlled temperature change of up to 500 ° C during the solidification phase until the part is removed. Specially developed "permanent mold simple " are products which are applied using modern, automated spray as a fine coat and protect the molds. Depending on their composition, they also influence the course of solidification. The basic principle of every permanent form finishing is that black coatings dissipate heat and thus cause rapid solidification and a fine crystalline structure. A white coating has an isolating effect, delays the solidification, promotes the water make-up and leads to higher density, but also to coarser crystallization .
The manufacture of molds for investment casting requires a special technique . The cast models are made of wax or plastic , coated with a ceramic shell. In a second step, the model is melted out or burned out and then the remaining, true-to-model cavity is cast. For alloys with a low melting point ( tin ), permanent molds are made with temperature-resistant chlorinated rubber applied to give shape , a method with which the finest details of the template can be reproduced.
There have been great advances in the production of molds for sand casting , which today for series production, especially in engine construction, only takes place in fully automatic systems. In the here required molding material binders was the resin used croning process 50 years ago, a pacemaker, today set the foundries as binders for molds and cores while still special synthetic resins, but give increasingly more environmentally friendly binder systems preferred, such as those on water glass . This is also assigned to the metallurgy sector in the foundry sector.
The various test methods are among the most frequently used helpers in the broad field of metallurgy - in addition to analytics. Originally, these were purely mechanical. One of the oldest methods here is the elongation test on standardized test bars, so-called tear bars. In addition, notched impact resistance and Brinell hardness were tested.
The thermal analysis (TA) shows the state of the structure and the effects of elements that influence the structure . In the case of aluminum-silicon alloys, these are sodium , strontium , phosphorus , and antimony .
Highly stressed cast parts are now increasingly non-destructive with the help of electronic methods - adopting medical techniques - before delivery to the customer by means of X-rays or, as an extension, by means of computer tomography (CT), two- and three-dimensional checks. This also includes InlineCT (scanning). Cast parts are also checked using sonography and MRI (magnetic resonance). Linear ultrasonic flaw detectors with "phased array technology," stationary or portable, can test 100,000 t of aluminum billets with diameters from 130 mm to 310 mm for homogeneity, but also cast pieces for flaws such as inclusions, pores, cavities, even inaccurate welds. Material testing and the specialty of "damage analysis on metallic components" are intertwined here.
All of the areas mentioned include the activities of the Deutsche Gesellschaft für Materialkunde e. V. (DGM), which with university departments - such as the metal science indispensable for further knowledge - and professional associations [Association of Ironworkers, Association of Foundry Experts (VDG), Society of Metalworkers and Miners (GDMB) and the German Copper Institute (DKI )] Brings together research, training and practice.
Metallurgy and environmental protection
Although it is inconceivable without modern analytics , environmental protection and its demands must be particularly emphasized, because in the environmentally conscious 21st century, both are the position and the solution to the problem at the same time. For a long time, the companies accepted the fact that metallurgical activity can be polluting to a certain extent and that the majority regard it as “hot and dirty” in both literal and figurative terms.
Analysis therefore has to fulfill important additional tasks beyond what is metallurgically required of it, because only it allows the qualitative and quantitative determination of the emissions linked to virtually all metallurgical processes down to the nano and pico range. It thus offers the possibility, whether primarily through process engineering improvements or downstream, to meet the requirements for exhaust gas reduction and air pollution control with the help of a new industrial branch of air technology that is only dedicated to emission control .
Not only the air, but also the wastewater from metallurgical plants must undergo a treatment that eliminates all harmful substances. Primary lead smelters must pay particular attention to this because of the pollutants lead and process-related sulphates.
As long as no adequate, secure energy supply is available for the economic importance of metallurgy - as an important, co-determining basis of our living conditions - the supply of energy decreases and increases in price contrary to demand and the diverse metallurgical services in the construction of a nuclear power plant (nuclear power plant) no longer is recognized, only increasing the efficiency of conventional thermal energies remains as an interim solution. This takes place in the course of ongoing development by increasing the degree of utilization of the fuels used, whether in large heating power plants or individually operated systems and in some cases even using process heat generated by chemical reactions (exothermic process sequence). For industry, this means process-oriented, automated control of the burners , the maximum use of supplied heating energy ( regenerative combustion ) and, last but not least, the reduction of heat losses through improved insulation, as well as the use of waste heat from large systems ( district heating ). Much has already been realized or is approaching realization. Rust-red chimney flue gases (NO X compounds), as they can arise in chemical processes, are a thing of the past.
When recycling plastics (“plastic”) or plastic-coated metal (aluminum cans), all organic components can be recorded in a pyrolytic process. In their gas phase, they either serve as a directly supplied energy carrier (fuel) or they are separated by means of fractional distillation for reuse and, depending on their nature, returned as valuable raw materials to production cycles.
Insofar as such procedures are not (still) possible due to operational circumstances, two areas are consistently recorded today: Gaseous and dusty emissions. Gaseous substances go through at least one setting, neutralizing, mostly alkalizing wet scrubbing ( venturi scrubber or a system related to it, for example the "annular gap scrubbing system" for exhaust gases containing chlorides and phosphides in aluminum foundries), which cannot be precipitated simply by cooling (see smelter ). The precipitated or filtered residues are recycled or disposed of in an orderly manner.
Metallurgical dusts can only be collected cold in fabric filters , which in practice requires an upstream cooler. Hot dusts (cupola furnace dedusting, arc dedusting) are collected dry by electrostatic precipitators or treated by means of upstream wet separation in exhaust air cleaning systems, which are no longer isolated cases with throughputs of 100,000 m³ per hour. The dried filtrate is subject to a legally stipulated recycling obligation, which, however, can often take place at the point where it is produced, reducing initial costs. One example is metallic dusts filtered out of the exhaust gases of cupolas, which can be injected back into the melt.
No less important is the use of appropriately processed, metallurgical dross that has been largely demetallised through special treatment . It is inaccurate to count them as waste products from the production of molten metals, as is slag . All are subject to the REACH regulation . Depending on their composition, however, they can be used again as protection against oxidation (cover) in melting furnaces or as “fillers”, even as paving (“ pavement ”) in road construction. Here, too, precise analysis is a prerequisite for correctly classifying such “waste” and deciding on its usability.
Metallurgy and environmental protection meet in another area. The remediation of the environmental damage caused in the GDR by uranium mining for the Soviet Union (heaps, mud ponds ) is well known. Underground the abandoned tunnels must be secured, either by backfilling or bricking up. If it does not pose any environmental hazards, overburden and slag heaps can also be greened and have a landscape-shaping effect. In lignite opencast mining , recultivation after coaling is the widespread standard; in East Germany it has been done since 1990. Recultivation - and thus at the same time protection against leaching with the consequence of potash overloading of waters - is also being attempted with considerable effort in the piles of the mining of potash and magnesium-containing salts, which are particularly striking in Hesse and Thuringia . In other places nature is able to "heal" the wounds itself. In iron ore mining, some exploited pits were left to their own devices until the 20th century, and only the hilly deforming pings (mine caves), which have now long been reforested, testify to the former ore extraction.
Well-known metallurgists

After only a few historical forerunners, metallurgy has been decisively advanced by several well-known scientists, especially in the last 200 years. Above all, this includes:
Historical
- Gaius Plinius Secundus (approx. 23–79 AD): Naturalis historia
- Georgius Agricola (1494–1555): de re metallica
Iron related
- Adolf Ledebur (1837–1906): "Handbook of Metallurgy"
- Wilhelm Borchers (1856–1925): "Electrometallurgy"
- Eugen Piwowarsky (1891–1953): "The iron and steel casting"; "High quality cast iron"
- Henry Bessemer (1813–1898): inventor of the blown steel process (Bessemer pear, sour)
- Sidney Thomas (1850–1885), Percy Gilchrist (1851–1935): Thomas pear, basic
- Pierre-Émile Martin (1824–1915): Regenerative heating (Siemens-Martin-Stahl)
Non-ferrous metals
- Hans Christian Oersted (1777–1851), Friedrich Wöhler (1800–1882), Robert Bunsen (1811–1899), Henry Saint-Claire Deville (1818–1881): Aluminum representation
- Charles Martin Hall (1863–1914), Paul Héroult (1863–1914): Fused aluminum electrolysis
- Alfred Wilm (1869–1937), Aladár Pácz (1882–1938): Development of aluminum alloys
- Gustav Pistor : Director of Elektronwerk GmbH, Frankfurt-Griesheim, promoter and developer of magnesium metal and its alloys for industrial purposes
- Wilhelm Borchers (1856–1925): Copper
Teachers and researchers
- Adolf Ledebur (1837–1906): Ironworks and foundry customer ( Ledeburit )
- Bernhard Osann (1862–1940): Metallurgy ("Textbook of iron and steel foundry")
- Alfred von Zeerleder (1890–1976): ("Technology of light metals")
- Eugen Piwowarsky (1891–1953): Metallurgy ("high quality cast iron")
- Wilhelm Borchers (1856–1925): Electrometallurgy
- Karl Karsten (1782-1853): Metallurgy
- Eduard Maurer (1886–1969): Metallurgy, inventor of "V2A" and "V4A" steel
- Joachim Krüger (* 1933): Non-ferrous metallurgy
Conferences
European Metallurgical Conference (EMC)
The European Metallurgical Conference (EMC) is the most important metallurgical conference in the field of non-ferrous metals in Germany and Europe. This is where the world's leading metallurgists have met every two years since the start in Friedrichshafen in 2001. In addition to the exchange of experience, it is also about environmental protection, resource efficiency and political and legal matters. The event is organized by the GDMB Society of Metallurgists and Miners e. V aligned.
Literature used
Lexicons
- Meyers Konversations-Lexikon. 5th edition. Bibliographical Institute, Leipzig / Vienna 1897.
- Josef Bersch (Hrsg.): Lexicon of metal technology. A. Hartlebens Verlag, Vienna 1899 (manual for all tradespeople and artists in the metallurgical field).
- Scientific advice of the Duden editorial team (ed.): Günther Drosdowski and others (edit.): The Great Duden in 10 volumes. Vol. 7: Duden Etymology. Dictionary of origin of the German language. Reprint of the 1963 edition, ed. by: Paul Grebe, Bibliographisches Institut / Dudenredaktion, Mannheim 1974, ISBN 3-411-00907-1 (in continuation of the "Etymology of the New High German Language" by Konrad Duden).
- The new Brockhaus: Lexicon and dictionary in 5 volumes and an atlas. 5., completely reworked. Edition. Brockhaus Verlag, Wiesbaden 1975, ISBN 3-7653-0025-X .
- Johannes Klein (arrangement): Herder-Lexikon: Geologie und Mineralogie. 5th edition. Herder Verlag, Freiburg im Breisgau 1980, ISBN 3-451-16452-3 (multi-part work).
- Jürgen Falbe, Manfred Regitz (ed.): Römpp-Chemie-Lexikon. 9th, adult and rework. Edition. Georg Thieme Verlag, Stuttgart 1995–1995, ISBN 3-13-102759-2 (multi-part work, a total of 6 volumes).
- Ernst Brunhuber, Stephan Hasse: Foundry Lexicon. 17., completely reworked Edition. Schiele & Schön Verlag, Berlin 1997, ISBN 3-7949-0606-3 .
- Hermann children, Werner Hilgemann : dtv atlas of world history . From the beginning to the present. Orig.-Ausg., Dtv, Munich 2000, ISBN 3-423-03000-3 (special edition of the dtv atlas world history first published by dtv in two volumes in 1964 and 1966).
- Ekkehard Aner: Great Atlas of World History. 2nd Edition. Extended edition of the standard work from 1956. Westermann Verlag, Braunschweig 2001, ISBN 3-07-509520-6 .
- Microsoft Encarta Encyclopedia Professional 2003 on DVD. Electronic, multimedia encyclopedia.
Specialist literature
- Hermann Ost : Textbook of chemical technology. 21st edition, edited by B. Rassow, Jänecke Verlag, Leipzig 1939 (chapter "Metallurgy").
- Alfred von Zeerleder: About technology of light metals. 2nd Edition. Publishing house of the Academic Machine Engineers Association at the ETH Zurich, 1951.
- Hans Schmidt: The foundry industry in a common representation. 3., reworked. u. exp. Edition. Foundry publishing house, Düsseldorf 1953.
- Hans Riedelbauch: batch and batch production from a business perspective. In: ZfhF - Journal for Commercial Research. Westdeutscher Verlag, Cologne a. a., No. 9, 1959, pp. 532-553.
- Ernst Brunhuber: Melting and alloying technology for copper materials. 2., rework. Edition. Schiele & Schön Verlag, Berlin 1968.
- General Association of German Metal Foundries (Ed.): Castings from copper and copper alloys, technical guidelines. Düsseldorf / Berlin 1982, DNB 821020889 .
- Mervin T. Rowley (Ed.): Cast from copper alloys. Schiele & Schön, Berlin 1986, ISBN 3-7949-0444-3 (English original title: Casting copper base alloys ).
- DKI workshop. Deutsches Kupfer-Institut, Berlin (series of publications; conference volumes - including 1993, 1995).
- AF Holleman , E. Wiberg , N. Wiberg : Textbook of Inorganic Chemistry . 102nd edition. Walter de Gruyter, Berlin 2007, ISBN 978-3-11-017770-1 .
- Hans Joachim Müller: Manual of the melting and alloying practice for light metals. Schiele & Schön, Berlin 1977, ISBN 3-7949-0247-5 .
Other sources
- Association of German foundry specialists (ed.): Foundry calendar. Foundry publishing house, Düsseldorf 1971 a. Subsequent years, ISSN 0340-8175 . (appears annually; from 1999 under the title Giesserei-Jahrbuch ).
- Trade journals: Aluminum, Foundry, Erzmetall / World of Metallurgy, Giesserei-Rundschau.
- Sol & Luna. Degussa self-published, 1973.
- G. Ludwig, G. Wermusch: Silver: from the history of a precious metal. Verlag die Wirtschaft, Berlin 1988, ISBN 3-349-00387-7 .
- On the trail of antiquity. H. Schliemann's reports, Verlag der Nation, Berlin 1974, DNB 750161906 .
- Steel information center, Düsseldorf (ed.): Fascination steel. Issue 13, 2007.
- Google Web Alerts for: "World production of metals". (irregular reports)
- Hans-Gert Bachmann: Early Metallurgy in the Near and Middle East. Chemistry in our time, 17th year 1983, No. 4, ISSN 0009-2851 , pp. 120-128.
further reading
- Wilhelm Weinholz: Technical-chemical handbook for the research, elimination and presentation of the metallic content of mineral bodies, which is common in the arts and trades. Helwing, Hanover 1830, digitized .
- F. Oeters: Metallurgy of steel production. Springer et al., Berlin 1989, ISBN 3-540-51040-0 .
- AF Holleman , E. Wiberg , N. Wiberg : Textbook of Inorganic Chemistry . 102nd edition. Walter de Gruyter, Berlin 2007, ISBN 978-3-11-017770-1 .
- Eugen Piwowarsky: High quality cast iron. Berlin 1951/1961, DNB 453788181 .
- Final report on sustainable metal management NMW. (Discussions, figures, tables using Hamburg as an example).
- V. panel: Textbook of metallurgy. Volumes I – III, S. Hirzel, Leipzig.
- Heinz Wübbenhorst: 5000 years of casting metals. Foundry publishing house, Düsseldorf 1984, ISBN 3-87260-060-5 .
- Silver, from the history of a precious metal. see section “Other Sources”.
- Steel - from iron ore to high-tech product. DVD from www.stahl-info.de.
- Non-ferrous metal recycling basics and current developments. GDMB series of publications, Issue 115, 2008, ISBN 978-3-940276-11-7 .
- Stefan Luidold, Helmut Antrekowitsch: Lithium - raw material extraction, application and recycling. In: Erzmetall. 63, No. 2, 2010, p. 68 (Reprint of a lecture given on the occasion of the 44th Metallurgical Seminar of the Technical Committee for Metallurgical Education and Training of the GDMB.)
- Recycling of copper materials. DKI brochure, www.kupferinstitut.de.
- The chemical elements , Alexander C, Wimmer, SMT-Verlag, Leoben 2011.
- "The world of die-casting": five articles on current die casting technology, Giesserei Rundschau, trade journal of the Austrian Foundry Associations, vol. 60, issue 7/8, 2013.
Web links
- Literature on the keyword metallurgy in the catalog of the German National Library
Institutes
- IME Aachen / Metallurgical process technology and metal recycling.
- Department of Metallurgy and Materials Technology RWTH Aachen.
- IfG Institute for Foundry Technology e. V.
- Montan University Leoben. Department of Metallurgy. Chair of Non-Ferrous Metallurgy.
- Chair of Foundry Science. Montan University Leoben.
- University of Duisburg; Institute for Applied Materials Technology.
- Technological University Bergakademie Freiburg.
- Clausthal University of Technology (Harz).
- Max Planck Institute for Iron Research.
more links
- Montan University Leoben.
- Association of German Foundry Experts VDG.
- GDMB Society of Metallurgists and Miners V.
- Association of German Ironworkers VDEh.
- Information on steel for metallographers.
- Metal trade association.
- General Association of the Aluminum Industry.
- German Copper Institute (DKI), Düsseldorf.
- German Society for Material Science V.
- Raw material prices for industrial metals.
Individual evidence
- ↑ Compare this with a surgeon , one who accomplishes something with his hands.
- ↑ Further information : Zedlersches Lexikon . Vol. 20, 1739/1740, column 1255. Article Metallurgy. Also on the change in the meaning of metal : in Liddell / Scott's dictionary and under metal in Dictionnaire de l'Académie française
- ↑ There is also the seldom used, synonymous term Copper Age for the earliest phase of the Copper Age.
- ↑ Jens Gutzmer: Geometallurgy - why metallurgists should communicate with geoscientists . ERZMETALL 67/2014, ISSN 1613-2394 , GDMB Verlag GmbH, No. 1, p. 54
- ↑ U. a. Business news in FAZ No. 174, 2008.
- ↑ Business news in FAZ No. 214, 2008.
- ↑ citation of the President of the Upper Mountain Office Freiberg as part of a contribution (sgd. PS. Dresden) "ramp blow" for a new mine in the Ore Mountains . FAZ No. 260 of November 8, 2010, p. 16.
- ^ FAS December 18, 2011, p. 71.
- ↑ "Red like blood, green like copper" (Ulf von Rauchhaupt) and "How we have become unequal." (Tilman Spreckelsen), two well-illustrated articles with a map of the expansion of metallurgy in Europe, see details in FAS No. 7 of February 20, 2011, pp. 58/59 and in the FAZ archive.
- ↑ FAZ of May 16, 2013, p. 65, "The Lord of the Clay Armies"
- ↑ Although is Chalkos interchangeably used for bronze and copper discoveries have shown that at least regionally for items that were first made of pure copper (Leitfund: copper hatchets), relatively soon v due to the greater hardness of from about 2500th Bronze was recognized as more useful. Probably the first bronzes were discovered by chance, in that tin ore and copper ore were heated together.
- ^ Timo Habdank; Miriam Kiefer; Klaus Lange; Sabrina Widmann: Topic: Earth and Fire: Pig iron extraction from Bohner ore with the racing furnace. December 10, 2008, State Seminar for Didactics and Teacher Training Reutlingen (Realschulen) Course 25, online
- ↑ "Die Energiepreisschere" by Werner Surbeck in FAZ of August 3, 2013, No. 178, p. 13
- ↑ Erzmetall . tape 61 , no. 3 , 2008.
- ↑ "Solar World receives exploration rights for lithium". in Economics, Technology and Science, ERZMETALL 64/2011, No. 3, p. 181.
- ^ "Economic and ecological consequences of the global market development of rare earths" (original text in English), Karl Nienhaus, Fiona Mavroudis, Mathias Pankert, ERZMETALL 65/2012, No. 2, p. 126.
- ↑ FAZ No. 234, October 8, 2011.
- ↑ "Strange Metals", Ulf v. Rauchhaupt, FAZ v. Jan. 27, 2013, p. 51.
- ↑ Elements of Nos. 57–64 of the periodic table.
- ^ AF Holleman , E. Wiberg , N. Wiberg : Textbook of Inorganic Chemistry . 102nd edition. Walter de Gruyter, Berlin 2007, ISBN 978-3-11-017770-1 .
- ↑ “Hidden bull market in rare (sic!) Earths”, especially London in FAZ No. 305/2010, p. 21.
- ↑ "China's policy makes rare earths expensive", FAZ report in No. 144 of June 24, 2011, p. 27.
- ↑ FAZ , July 3, 2011, No. 153, p. 22 Significant discovery of rare earths on the sea floor (near Hawaii); also FAZ , July 20, 2011, No. 166, p. N2: Uta Bilow "Desired metals in deep-sea mud".
- ↑ "Rare earths should become more common", "FAZ" No. 168, July 21, 2012, p. 20.
- ^ "Rare earths confirmed in Germany", Franz Nestler in FAZ No. 27 of February 1, 2013, p. 19
- ↑ FAZ - Economic Report, Issue 70 / wo13, p. 24
- ↑ Judith Lembke: Wasted resources. , In: FAZ No. 27 of September 1, 2011, p. 11.
- ↑ One ton of raw aluminum requires 4 tons of bauxite, 0.5 tons of coal, but 15,000 kWh of electrical energy.
- ↑ Erzmetall 65/2012, No. 2, p. 69, reports on the “Goslar Metallurgy Day”.
- ↑ Michael Stelter gives a very informative comparison of the manufacturing processes for primary magnesium in "ERZMETALL / World of Metallurgie", volume 64/2011, no. 3, p. 151
- ↑ from "Editorial" by Eric Becker, in "Erzmetall, World of Metallurgy", issue 5/2013, p. 245
- ^ At that time (ein periodicum) 9/97, p. 33, Josef Eisinger (physiologist, biophysicist): In ancient Rome, lead was added to wine and caused typical diseases. This was all the more important as from the imperial era onwards, drinking wine was common in all classes.
- ↑ Google alerts - business data service
- ↑ press release of December 27, 2011 in ERZMETALL 65/2012, No. 1, p. 13.
- ↑ Aluminum alloy and magnesium alloy are used in zones in one casting to save weight. In engine casting, one variant uses a so-called “insert” made of eutectic aluminum-silicon alloy, which is sufficient for thermal stress, and then fills the rest of the mold with magnesium to save weight.
- ↑ dpa report in the FAZ of August 14, 2015: Airbus relies on 3D printing • Aircraft parts from the printer
-
↑ Reports on the “Goslar Metallurgy Day”, u. a .:
K. Hanusch: Metallurgy in the transition from the past to the future . tape 61 , no. 2 , 2008, ISSN 1613-2394 , p. 69 (examples lead works Oker, zinc works Harlingerode). - ↑ See "technology" in ERZMETALL, Volume 65/2012, No. 1, P. 12 (press release) from January 19, 2012.
- ↑ a b Stephan Hasse: Foundry Lexicon . 17th edition. Schiele & Schoen, Berlin 2000, ISBN 3-7949-0606-3 .
- ↑ To this in more detail in: Gemeinfassliche representation des Eisenhüttenwesen. Association of German Ironworkers, Düsseldorf.
- ↑ Trimet AG in Essen, 2010 producer of 500,000 t of aluminum, as the primary producer and major recycler, sees this according to a report by the FAZ of September 17, 2011, No. 217, p. 117, TRIMET hopes for a higher demand for aluminum , a requirement of one million tons by 2020.
- ↑ TRIMET reports a production of 640,000 t for 2012/13 after purchasing a plant in France. The Norwegian company HYDRO Aluminum is investing € 150 million in Grevenbroich to increase the capacity of the rolling mill from 50,000 to 200,000 t. Two press releases in ERZMETALL 2/2014, see Economics, pp. 68 and 69.
- ↑ See footnote 17.
- ^ Georg Fischer AG. Retrieved February 18, 2015 .
- ↑ This term, which comes from chemical metallurgy, should not be confused with the historically influenced term of the Copper Age.
- ↑ See low-alloy copper materials, information print i8 of the DKI.
- ↑ Cartridge or cartridge brass is used for bullet cases of all types and sizes that contain the propellant charge in addition to the bullet itself.
- ^ AF Holleman , E. Wiberg , N. Wiberg : Textbook of Inorganic Chemistry . 102nd edition. Walter de Gruyter, Berlin 2007, ISBN 978-3-11-017770-1 , p. 432.
- ↑ Resource-efficient casting techniques in zinc die casting , Sabina Grund, in Giesserei-Rundschau, Vienna, Jhg. 63 issue 11/12 2018
- ↑ See lecture at the International German Die Casting Day 2016, reproduction in Giesserei-Rundschau, Vienna, vol. 63, issue 3/4, also on the subject of GIESSEREI Praxis 6/2012, p. 263, Ulrich Schwab: zinc die casting in automobiles . See also article in ERZMETALL 6/2015 p. 354, Didier Rollez, Annalisa Pola, Frank Prenger: Zinc alloy family for foundry purposes
- ↑ K. Weigel, R. Dreyer: Zinc oxide production, market and areas of application . In: Erzmetall . tape 61 , no. 5 , 2008.
- ↑ Entry on lithium. In: Römpp Online . Georg Thieme Verlag, accessed on June 26, 2014.
- ↑ The information on the world-wide lithium deposits and the possible annual production vary considerably depending on the source. Bolivia is said to have large deposits .
- ↑ See, for more in-depth information, Stefan Luidold, Helmut Antrekowitsch: Lithium - Raw Material Sources , Application and Recycling. In: Erzmetall. 63, No. 2, 2010, p. 68.
- ^ Cobalt from Africa for German electric vehicles. Economic contribution in FAZ of March 8, 2010. No. 56, p. 19.
- ↑ Entry on beryllium. In: Römpp Online . Georg Thieme Verlag, accessed on June 26, 2014. names u. a. even use as a moderator in reactor technology.
- ↑ Lt. Press release of the KTI (Karlsruhe Institute of Technology) from November 13, 2009, reproduced in Erzmetall. 63, No. 1, 2010, p. 45.
- ^ Quote from Loriot , alias Vicco von Bülow : "There used to be more tinsel".
- ^ Rhein-Zeitung of August 22, 2008.
- ↑ Erzmetall . tape 61 , no. 4 , 2008.
- ↑ HERO premium investment casting process, TITAL Bestwig.
- ↑ From Technology. In: Erzmetall. 63, No. 4, 2010, p. 220.
- ↑ WINDOWS Life . In: Focus Africa . No. 1 , 2008.
- ↑ Until 1918, wulfenite or yellow lead ore containing molybdenum and therefore essential for warfare was mined in Germany's highest mine under the Zugspitze until the deposits were exhausted. Quoted from GDMB News in ERZMETALL 2/2011, S. XVI.
- ↑ "World" is not explicitly mentioned in the source but can be concluded. "FAZ November 20, 2010".
- ↑ Refractory metals - key materials for the high tech industry . In: Erzmetall . tape 61 , no. 2 , 2008. , also on the subject of Gerhard Gille, Andreas Meier, in ERZMETALL 3/2011, p. 123, "Refractory Metals - Materials for Key Technologies and High Tech Applications."
- ↑ Erzmetall . tape 61 , no. 4 , 2008. Comment: From 2010, Rio Tinto expects a new molybdenum production facility to produce 4500 kg of rhenium annually.
- ↑ The brand name Osram is an artificial word from the first syllable of Os mium and the last of Wolfram.
- ↑ Isabella Milch: Brittle material gains toughness. (PDF; 187 kB) tungsten fiber reinforced tungsten. (No longer available online.) Max Planck Institute for Plasma Physics, May 27, 2013, archived from the original on July 21, 2013 ; Retrieved October 7, 2013 .
- ↑ Lt. FAZ economic communications . No. 207 , 2008.
- ↑ Lt. FAZ economic communications . No. 193 , 2008.
- ↑ Lt. FAZ economic communications . No. 220 , 2008.
- ↑ Metals - the engine of communication and energy technology . In: Erzmetall . tape 61 , 2008.
- ↑ Hendrik Kafsack: EU in great concern due to scarce raw materials. In: FAZ of November 20, 2010, No. 271, p. 13. Online full text.
- ↑ Michael Stelter: Marktentwicklung von Technologiemetallen , p. 22 in ERZMETALL World of metallurgy, 67/2014, Issue 1, GDMB-Verlag, ISSN 1613-2394 . On the same topic in the series "GDMB Writings", Issue 133, ISBN 978-3-940276-54-4 "Production and Recycling of Technology Metals"
- ↑ This justifies the generally held view that silver today is less to be assigned to precious metals than to metals used in industry. FAZ No. 8, 2008.
- ↑ A “cell phone” contains only 24 mg gold and 9 mg palladium, but in 2006 more than a billion of them were sold, further figures in Ulrich Grillo: NF metal industry - economically and ecologically valuable . In: Erzmetall . tape 61 , no. 3 , 2008, p. 162 ( PDF ).
- ↑ FAZ v. July 18, 2008 reports the deficit for 2007 of 480,000 ounces with further increasing demand and reduced supply.
-
↑ According to the stock exchange listing, the price of an ounce (31.1 g) rose to> 9500 USD
ore metal in the course of 2008 . No. 4 , 2008. - ↑ "Exotic metal palladium gets into the limelight", FAZ No. 28 of February 2, 2013, p. 24
- ↑ According to a note in Erzmetall 63, No. 2, 2010, p. 97 referring to mining-technology 4/2010 , Hungary prohibits cyanide leaching on its national territory and wants to enforce this throughout Europe in the course of its EU Council Presidency.
- ↑ FAZ No. 8, 2008.
- ↑ FAZ economic report of May 10, 2010 No. 108 p. 15.
- ↑ Günther Fleischer: Sustainable product design to promote the use of non-ferrous metals . In: Erzmetall . tape 60 , no. 6 , 2007, ISSN 1613-2394 , pp. 332 f .
- ↑ The RWTH Aachen maintains an "Institute for Processing" that deals with this.
- ↑ Georg Rombusch in "Editorial", ERZMETALL 63/2010.
- ↑ ERZMETALL 4/2012, "economics" press release of June 37, 2012.
- ↑ "Aurubis officially puts KSR Plus systems into operation in Lünen" (according to press release of July 7, 2011), ERZMETALL 64/2011, No. 4, p. 233.
- ↑ "A new process of copper smelting with oxigen enriched bottom blowing technology", Zhisiang Cui, Dianbang Shen, Zhi Wang, Erzmetall 84/2011, No. 5, p. 254.
- ↑ "Kupferhütte AURUBIS is changing into a metal company" - which was once the parent metal company, see p. FAZ of December 28, 2017, number 300, p. 22.
- ↑ James E. Hoffmann: The world's most complex metallurgy revisited . In: Erzmetall . tape 61 , no. 1 , 2008, p. 6th f .
- ↑ A detailed description of the "Recycling of copper materials" is given in a brochure published by the German Copper Institute.
- ↑ A globally active producer of primary aluminum cites an increase in the amount of metal he recovers through recycling in Germany alone by 40% to 280,000 t and is even predicting a million t for 2010. Source: Press interview in FAZ No. 214 of September 15, 2010, p. 14.
- ↑ Press release from TRIMET AG of September 21, 2012 in ERZMETALL 65/2012, No. 6, p. 338.
- ↑ according to alcircle.com, October 15, 2013, in ERZMETALL6 / 2013, p. 318.
- ↑ Also Georg Rombach, Roja Moderesi, Daniel B. Müller "Aluminum Recycling - Raw Material Supply from a Volume to the Quality Constraint System", ERZMETALL - World of Mdtallurgy, 65/2012, No. 3, ISSN 1613-2394 .
- ↑ Press release from November 17, 2015 in ERZMETALL 1/2016
- ↑ ERZMETALL 4/2014, p. 188, s. under "Economics": Press release NOVELIS from June 11, 2014
- ↑ On this article by Michael Schwalbe, "Basics and possibilities of processing highly contaminated aluminum scrap ", lecture before the light metal specialist committee of the GDMB on September 20, 2010, printed in ERZMETALL ISSN 1613-2394 64/2011, No. 3, May / June, P. 157.
- ↑ Lt. FAZ from January 15, 2010, p. 12, reports an economic report “Aluminum scrap is becoming scarce”. It refers to information from the VAR (Association of Aluminum Recyclers), according to which China doubled its scrap imports from Europe in 2009 to 550,000 t.
- ↑ A foundry specializing in automobile wheels has a daily chip volume of 30 t. These are returned to production with three special chip melting furnaces and a combined hourly output of 1500 kg of liquid metal and make up 30% of the total liquid metal requirement. Press release of March 8, 2010 from Erzmetall 63, No. 3, 2010, p. 161 “Technology”.
- ↑ Erzmetall . tape 61 , no. 1 , 2008, p. 46 .
- ↑ Erzmetall . tape 61 , no. 4 , 2008 (press release June 24, 2008).
- ^ Giesserei Rundschau, Vienna, Volume 59, Issue 9/10 from 2012, p. 261.
- ↑ See also under furnace technology with a footnote on the SIMELT FSM foam slag manager.
- ↑ Correspondingly quoted by Norbert E. Piret "EAF Dust Processing: Rotary Hearth a potential substitutes for the Waelz Kiln?" ERZMETALL 65/2012, No. 5, p.306..
- ^ Andreas Jungmann, Andreas Schiffers: Dry processing and High Quality Applications for Steel slag. In: Erzmetall - World of Metallurgy. 63, No. 1, 2010, p. 13 f.
- ↑ Andrzej Chmielarz: Zinc Smelting in Poland - Review of Industrial Operations. Lecture from September 2009, in ERZMETALL 63/2010, No. 3, p. 142.
- ↑ Outotec Ausmelt (R) Technology for Treating Zinc Residues, St. Creedy and others, ERZMETALL 4/2013, p. 230
- ↑ Massimo Mascagni: New Developments in Pb Batteries Recyling: How to Minimize Environmental Impact Reducing Production Costs. ERZMETALL 5/2010 p. 252. Also in ERZMETALL 1/2012, p. 21. “About electrolytic lead extraction from 'paste' (battery sludge)”.
- ^ "Lead A Bright Future for the Gray Metal", David N. Wilson, ERZMETALL 64/2011, No. 4, p. 196.
- ↑ Massimo Maccagni "The new standard for the (patented / brevettato) CX-process: The first CX-Project with ammonium salts based desulphurization", ERZMETALL 6/2013, p. 350
- ^ Carsten Hillmann: Recovery of Zinc from Spent Batteries by the Treatment in a Shaft Furnace. ERZMETALL-World of Metallurgy 4/2014, p. 220
- ↑ BERZELIUS press release of November 16, 2009, reproduced in Erzmetall, 63, No. 1, 2010, p. 40, “the lead battery has a future”. On the same topic, also “Recycling in the lead works” in FAZ No. 19 of January 23, 2012, p. 16, article signed bü'Braubach (location of the BSB). Furthermore: BSB - recycling: secondary lead smelter with compounding system (protected trademark "Seculene") in GDMB - News issue 4/2012. S. XXXIV.
- ↑ "Fundamentals of Chlorination of Lead Oxide using Magnesium Chloride", Christiane Scharf, André Ditze, ERZMETALL 64/2011, No. 4, p. 205.
- ↑ Tobias Elwert, Karl Strauss, Thomas Schirmer, Daniel Goldmann report on related research: "Phase Composition of High Lithium Slags from the Recycling of Lithium Ion Batteries", ERZMETALL - World of Metallurgy, 65/1012, No. 3, ISSN 1613- 2394 .
- ↑ See also Section 3.3 “Precious Metals”.
- ^ E. Rombach et al.: Old batteries as secondary raw material resources for metal extraction. In: Erzmetall.
- ↑ Erzmetall . tape 61 , no. 5 , 2008, p. 335 .
- ^ "Technologies for recycling hard metal scrap" (Parts 1, 2, 3), Th. Angerer, St. Luidold. H. Antrekowitsch, in ERZMETALL (see a.a. O) issue 1/2011, p. 6 f., Ibidem issue 2, p. 62 and issue 6, p. 328.
- ↑ Press release from September 20, 2012, cited in ERZMETALL 65/2012, No. 6, p. 343.
- ↑ "Thermal mechanical enrichment of indium tin oxide from display units of used flat screens". Anika Bihlmayer, Martin Völker in "Erzmetall, World of Metallurgy", 64/2011, No. 2, p. 79.
- ↑ R. Gillner et al. In Erzmetall 64/2011, No. 5, p. 260.
- ↑ ERZMETALL 1/2016, p. 13, press release from November 19, 2015
- ↑ See also Zeerleder, Düsseldorf 1953.
- ↑ Recycling of steel is becoming more environmentally friendly. In: Erzmetall - World of metallurgy. 61, No. 1, 2010, p. 102.
- ↑ ERZMETALL 4/2011, No. 4, p. 239, Franken Guss-Kitzingen BMU funding for a pilot project. (Reproduced from a press release from May 30, 2011).
- ↑ See heat conductor alloys.
- ↑ Erzmetall . tape 61 , no. 5 , 2008, p. 333 .
- ↑ For a detailed description, see the specialist literature, including: Industrial furnace construction. Vulkanverlag, Essen.
- ↑ Rudolf P. Pawlek: Progress in remelting and casting of aluminum . In: Erzmetall . tape 61 , no. 2 , 2008.
- ↑ a b ERZMETALL 5/2015, p. 254 "Economics"
- ^ Reports from the Metalworkers' Association, reports from DIW Berlin, business reports, notices in the specialist press and the Frankfurter Allgemeine Zeitung .
- ↑ Rudolf Pawlek. Editorial Erzmetall 5/2010 “Aluminum in 2010” (with time-related figures on primary production and recycling).
- ↑ Figures for 2000, 2005 and 2006 come from different, not always consistent sources, have become partly obsolete due to the expansive development in some regions of the world (e.g. China), but also the crisis of 2008/2009, but provide at least some information about quantities of important metals produced worldwide as well as production and consumption in the FRG.
- ^ FAZ for 2007.
- ^ Frankfurter Allgemeine Zeitung, October 1, 2007.
- ↑ Figures from "Crude steel production is growing weaker", FAZ Economic Communication in No. 20/2013, p. 11
- ↑ FAZ reports on January 9, 2009 in the economic section on p. 11 under "The end of the steel statistics" for December 2009 a slightly recovered crude steel production of 3.03 million t. At the same time, it is announced that the legal obligation to provide production figures for the entire steel industry expired at the end of 2009.
- ↑ Business note in FAZ No. 208 of September 6, 2012 p. 21. Also comparative statistics on the production of crude steel in Germany since 1950 , November 2, 2011, accessed on January 22, 2012.
- ↑ FAZ No. 276 of November 27, 2013, p. 10, press release from St. Düsseldorf, November 26, 2013 "Steel industry scolds politics".
- ^ "More crude steel melted", press release "st" in FAZ No. 59, p. 20 of March 11, 2014
- ↑ stahl-online.de
- ↑ Figures from the "Statistics of World Casting Production", reproduced in VÖG Giesserei Rundschau, Vol. 65, Issue 01, 2018, p. 68 f.
- ↑ Statistics of world casting production in 2016 from Giesserei-Rundschau, vol. 65, issue 01 2018.
- ↑ The amount of raw aluminum came from primary production with 0.432 million t and from the secondary sector with 0.634 million t.
- ↑ Erzmetall. No. 6, 2007: Rheinische Aluminumhütte increases the total output for rolling billet production by 50,000 to 400,000 t / a with a new recycling furnace.
- ↑ Reports collected under Economics in Erzmetall 4/2013 and 3/2015, ISSN 1613-2394
- ↑ RP Pawlek “The aluminum smelting industry at the end of 2014”, in Erzmetall / World of Metallurgy, issue 2/2015, p. 55, in GDMB-Verlag GmbH
- ^ Bauxite and Alumina Activities in 2007 to 2008, Report by R. Pawlek. In: Erzmetall. 61, No. 5, 2008.
- ↑ The demand has risen since 2000 from 80,000 t to 126,000 t in 2010 (according to BÖRSENMONITOR May 2012).
- ↑ FAZ of November 20, 2010, Hendrik Kafsack: EU because of scarce raw materials in great concern. s. also in FAZ of November 20, 2010, No. 271, p. 13. Online full text .
- ↑ Rüdiger Köhn: On the wrong foot. in FAZ No. 207 of September 6, 2011, p. 22.
- ↑ Christoph Hein: Australia guarantees Japan rare earths. In: FAZ of November 25, 2010, No. 275, p. 12. Online full text .
- ↑ Lt. FAZ economic communications . No. 155 , July 5, 2008.
- ↑ A relevant supplier reports in the press ("Borkener Zeitung") that 2007 sales of € 225 million were achieved.
- ↑ "New ways in computed tomography and component testing", reported by j. Rosc, Th. Pabel, GF Geier, D. Habe, O. Brunke in "Giesserei Rundschau" vol. 58, issue 5/6 - 2011, p. 98.
- ^ I. Stuke, O. Brunke: InlineCT - Fast Computed Tomography in Mass Production. ibidem p. 102.
- ↑ Lt. Ore metal. 61, No. 4 and 5, 2008.
- ↑ Also internships at the RUB (Ruhr University Bochum), Institute for Materials - Materials Testing Department.
- ^ Anja Steckenborn, Urban Meurer: Development of an online sulphide analysis in the wastewater treatment plant of a primary lead smelter. Erzmetall 5/2011, No. 4, p. 282.
- ↑ EMC GDMB homepage.